溅渣护炉技术
溅渣护炉技术 冶金

毕业设计(论文)学校:专业:冶金技术班级:学生:学号:指导教师:摘要溅渣护炉技术作为一项工艺简单、综合经济效益高的新技术,正别外国许多厂家推广、使用,分析了该技术的优势及存在的问题和解决办法,以及该技术的应用现状和应用前景。
转炉溅渣护炉是在出钢后,将转炉内留渣的粘度和氧化镁含量调整到合适的范围,在车间原有的氧枪或另设专用喷枪,向氧化镁含量、高粘度的炉渣喷一定压力和流量的氮气,将粘渣吹溅到炉衬上全面涂挂、冷却、凝固成一层炉渣质的保护层,避免了在冶炼时炉衬和炉渣的直接接触,从而起到减缓耐火材料的蚀损,延长转炉炉龄的作用。
溅渣护炉作为一项实用技术,经过国内外许多钢厂实践后,对提高转炉炉龄和降低耐火材料消耗的效果非常显著。
关键词:溅渣护炉;转炉;应用目录1存在问题及解决办法 (1)2溅渣护炉工艺的冶金因素及其优势 (2)3国外溅渣炉技术的发展 (3)4国内转炉炉龄现状及溅渣护炉技术的发展 (5)5应用现状及应用前景 (6)致谢信 (7)参考文献 (8)1存在问题及解决办法任何一项技术的应用不可能没有缺陷,在一些早期设备上,氧枪结瘤就是一个问题。
溅渣技术使用后,往往使枪结瘤出现次数增加。
实践证明,在溅渣过程中,若炉内残留少量钢水,氧枪结瘤将更加严重。
解决这个问题,有几种方法证明是有效的。
第一,有充足冷却水的炉子不出现结瘤问题;第二,将用于吹炼的热氧枪移走,换上冷枪完成溅渣,氧枪结瘤几乎完全消除。
这表明氧枪结瘤与温度和热量的传递有关。
渣子和冷枪的表面结合并不紧密,如果在溅渣时冷凝钢不出现在氧枪上,那就不会再氧枪上形成粗糙的外壳以使炉渣粘附其上。
溅渣后将氧枪停放在支架上,形成的渣壳将冷却,并与氧枪分离,脱落。
使用底吹搅拌技术的BOF转炉对溅渣技术的应用提出了新的要求。
在溅渣时炼钢工必须小心,不能使炉底的渣太多;氮气的流速必须足够高,以便将炉渣吹离炉底;另外要调整经过透气砖喷吹气体的压力、流量。
最终,随着炉衬寿命的提高,额外的操作需要增加辅助设备的使用寿命,如BoF炉的烟罩、钢包车和轨道等设备。
转炉溅渣护炉系统优化技术基础理论研究
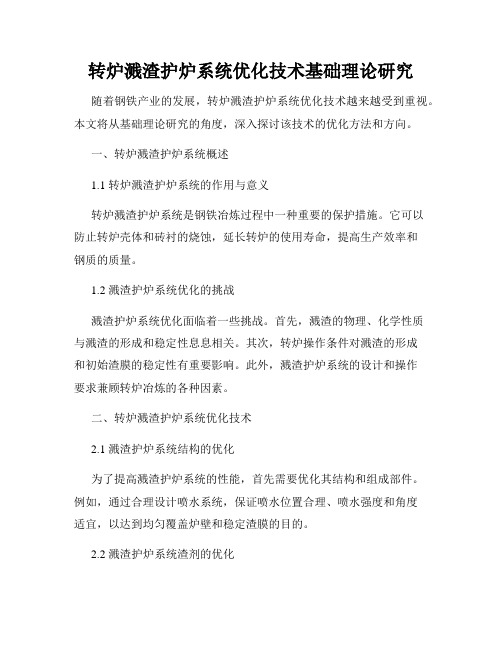
转炉溅渣护炉系统优化技术基础理论研究随着钢铁产业的发展,转炉溅渣护炉系统优化技术越来越受到重视。
本文将从基础理论研究的角度,深入探讨该技术的优化方法和方向。
一、转炉溅渣护炉系统概述1.1 转炉溅渣护炉系统的作用与意义转炉溅渣护炉系统是钢铁冶炼过程中一种重要的保护措施。
它可以防止转炉壳体和砖衬的烧蚀,延长转炉的使用寿命,提高生产效率和钢质的质量。
1.2 溅渣护炉系统优化的挑战溅渣护炉系统优化面临着一些挑战。
首先,溅渣的物理、化学性质与溅渣的形成和稳定性息息相关。
其次,转炉操作条件对溅渣的形成和初始渣膜的稳定性有重要影响。
此外,溅渣护炉系统的设计和操作要求兼顾转炉冶炼的各种因素。
二、转炉溅渣护炉系统优化技术2.1 溅渣护炉系统结构的优化为了提高溅渣护炉系统的性能,首先需要优化其结构和组成部件。
例如,通过合理设计喷水系统,保证喷水位置合理、喷水强度和角度适宜,以达到均匀覆盖炉壁和稳定渣膜的目的。
2.2 溅渣护炉系统渣剂的优化渣剂是溅渣护炉系统中起着关键作用的组成部分。
通过优化渣剂的物理、化学性质,可以改善渣膜的稳定性和降低溅渣对炉壁的侵蚀。
此外,选择合适的渣剂还可以提高转炉冶炼的效率和钢质的质量。
2.3 溅渣护炉系统操作参数的优化转炉冶炼中,操作参数的优化对溅渣护炉系统的性能影响巨大。
如合理控制氧枪的氧浓度和流速,可以影响转炉中的气体组成和温度分布,从而改善渣膜的稳定性和溅渣的产生。
三、转炉溅渣护炉系统优化的基础理论研究3.1 溅渣生成机制研究溅渣的生成机制是转炉溅渣护炉系统优化的基础。
通过研究渣剂的物理、化学性质和与炉壁的相互作用,可以揭示溅渣产生的机理和规律。
3.2 渣膜稳定性研究渣膜的稳定性影响整个溅渣护炉系统的工作效果。
通过研究渣膜在高温、高压环境下的性质和行为,可以为渣膜的稳定性优化提供理论依据。
3.3 操作参数对溅渣的影响研究操作参数对溅渣的形成和稳定性具有重要影响。
通过模拟实验和理论计算,可以探究操作参数对溅渣护炉系统的影响规律,并为优化操作参数提供理论指导。
转炉溅渣护炉技术

转炉溅渣护炉技术的应用方法1.溅渣护炉的基本原理,是在转炉出完钢后加入调渣剂,使其中的Mg与炉渣产生化学反应,生成一系列高熔点物质,被通过氧枪系统喷出的高压氮气喷溅到炉衬的大部分区域或指定区域,粘附于炉衬内壁逐渐冷凝成固态的坚固保护渣层,并成为可消耗的耐材层。
转炉冶炼时,保护层可减轻高温气流及炉渣对炉衬的化学侵蚀和机械冲刷,以维护炉衬、提高炉龄并降低耐材包括喷补料等消耗。
氧气顶吹转炉溅渣护炉是在转炉出钢后将炉体保持直立位置,利用顶吹氧枪向炉内喷射高压氮气(1. 0MPa) ,将炉渣喷溅在炉衬上。
渣粒是以很大冲击力粘附到炉衬上,与炉壁结合的相当牢固,可以有效地阻止炉渣对炉衬的侵蚀。
复吹转炉溅渣护炉是将顶吹和底吹均切换成氮气,从上、下不同方向吹向转炉内炉渣,将炉渣溅起粘结在炉衬上以实现保护炉衬的目的。
溅渣护炉充分利用了转炉终渣并采用氮气作为喷吹动力,在转炉技术上是一个大的进步,它比干法喷补、火焰喷补、人工砌砖等方法更合理,其既能抑制炉衬砖表面的氧化脱碳,又能减轻高温渣对炉砖的侵蚀冲刷,从而保护炉衬砖,降低耐火材料蚀损速度,减少喷补材料消耗,减轻工人劳动强度,提高炉衬使用寿命,提高转炉作业率,减少操作费用,而且不需大量投资,较好地解决了炼钢生产中生产率与生产成本的矛盾。
因此,转炉溅渣护炉技术与复吹炼钢技术被并列为转炉炼钢的2项重大新技术。
2 溅渣护炉主要工艺因素2. 1 合理选择炉渣并进行终渣控制炉渣选择着重是选择合理的渣相熔点。
影响炉渣熔点的物质主要有FeO、MgO和炉渣碱度。
渣相熔点高可提高溅渣层在炉衬的停留时间,提高溅渣效果,减少溅渣频率,实现多炉一溅目标。
由于FeO易与CaO和MnO等形成低熔点物质,并由MgO和FeO的二元系相图可以看出,提高MgO的含量可减少FeO相应产生的低熔点物质数量,有利于炉渣熔点的提高。
从溅渣护炉的角度分析,希望碱度高一点,这样转炉终渣C2 S 及C3 S之和可以达到70%~75%。
炼钢工—简答题 207

1.什么是溅渣护炉技术?答案:溅渣护炉技术是向炉渣中加入含MgO的造渣剂造粘渣补炉技术的基础上, 采用氧枪喷吹高压N2在2-4mm 内将出钢后留在炉内的残余炉渣喷溅涂敷在转炉内衬表面上,生成炉渣保护层的护炉技术。
2.炉渣来源何处?它在炼钢中起什么作用?答案:来源:(1)钢铁料中夹杂氧化的产物。
(2)造渣材料(石灰、白云石、萤石等)。
(3)冷却剂(氧化铁皮、矿石等)。
(4)被浸蚀和冲刷下来的炉衬耐火材料。
(5)各种原料带来的泥沙。
作用:(1)去夹杂(P、S);(2)传氧媒介;(3)清洁钢液;(4)对熔池保温;(5)影响金属损失;(6)影响炉衬浸蚀。
3.脱碳反应对炼钢过程的重要意义是什么?答案:(1)铁水中C氧化到钢种所要求的范围。
(2)氧化产生CO气泡对熔池起着循环搅拌作用,均匀钢液成份、温度, 改变各种化学反应的动力学条件。
(3)CO气泡有利于去除N2、H2等。
(4)利于非金属夹杂物上浮。
(5)提供炼钢的大部分热源。
(6)CO气泡使炉渣形成泡沫渣。
4.造成钢包回磷的原因是什么?如何防止?答案:原因:(1)出钢下渣;(2)脱氧产物SiO2;(3)氧含量降低。
防止措施:(1)挡渣出钢,尽量减少出钢带渣。
(2)采用碱性钢包或渣线部位用碱性材料。
(3)出钢过程中投入钢包中石灰粉。
(4)减少钢水在钢包中停留时间。
5.为什么兑铁时,有时会发生大喷?答案:因为转炉吹炼到终点,钢中氧含量和炉渣氧化性高, 留渣或未倒净的渣子和钢水,兑铁时炉内碳含量急剧增加且铁水温度低及钢水温度骤然下降, 促使碳氧反应剧烈进行在炉内产生强烈沸腾,如果兑铁水过猛且炉内残留钢渣较多就会大喷。
6.为什么转炉炼钢脱硫比脱磷困难?答案:碱性转炉渣中含有较高的(FeO),炉渣脱硫的分配比较低,降低了炉渣的脱硫能力,高(FeO)对脱磷工艺是一个相当有利的因素, 转炉炼钢条件下钢渣间磷的分配比较高, 一般可达100-400,而硫的分配比一般为6-15,此外,脱磷反应速度快,很快可达到平衡,而脱硫速度较慢,一般达不到平衡。
一种溅渣护炉方法
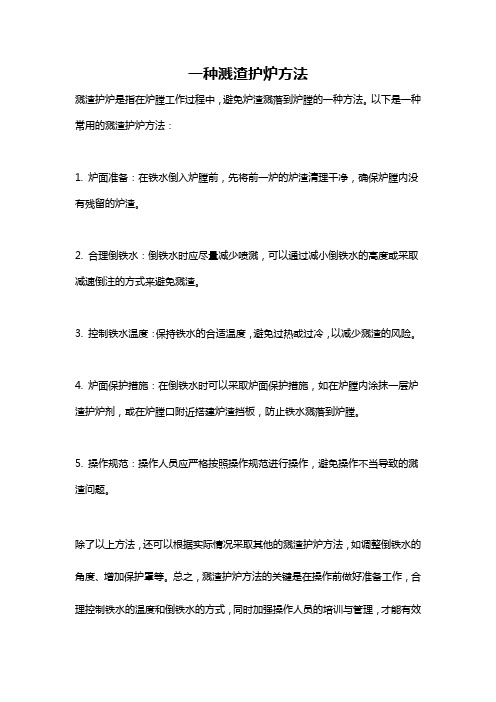
一种溅渣护炉方法
溅渣护炉是指在炉膛工作过程中,避免炉渣溅落到炉膛的一种方法。
以下是一种常用的溅渣护炉方法:
1. 炉面准备:在铁水倒入炉膛前,先将前一炉的炉渣清理干净,确保炉膛内没有残留的炉渣。
2. 合理倒铁水:倒铁水时应尽量减少喷溅,可以通过减小倒铁水的高度或采取减速倒注的方式来避免溅渣。
3. 控制铁水温度:保持铁水的合适温度,避免过热或过冷,以减少溅渣的风险。
4. 炉面保护措施:在倒铁水时可以采取炉面保护措施,如在炉膛内涂抹一层炉渣护炉剂,或在炉膛口附近搭建炉渣挡板,防止铁水溅落到炉膛。
5. 操作规范:操作人员应严格按照操作规范进行操作,避免操作不当导致的溅渣问题。
除了以上方法,还可以根据实际情况采取其他的溅渣护炉方法,如调整倒铁水的角度、增加保护罩等。
总之,溅渣护炉方法的关键是在操作前做好准备工作,合理控制铁水的温度和倒铁水的方式,同时加强操作人员的培训与管理,才能有效
减少溅渣对炉膛的损害。
溅渣护炉的基本原理

溅渣护炉的基本原理溅渣护炉是一种常见的钢铁冶炼过程中的热力学现象。
其基本原理是通过在炉内加入适当的物料,将炉内产生的溅渣与炉壁进行反应,从而保护炉内的炉壁不被腐蚀,延长炉壁的使用寿命。
本文将具体介绍溅渣护炉的基本原理及其应用。
一、溅渣护炉的基本原理在钢铁冶炼过程中,高温下会产生大量的溅渣,这些溅渣不仅会降低冶炼效率,还会对炉壁造成破坏。
为此,需要通过添加适当的物料进行溅渣护炉。
溅渣护炉的基本原理是添加一些特殊的反应剂,使其在高温下与溅渣发生反应,生成一种新的化合物,从而消耗掉大部分的溅渣。
这种化合物可以形成一层保护膜,在钢水和炉壁之间形成一个隔离层,减少溅渣对炉壁的侵蚀,从而有效地延长炉壁的使用寿命。
溅渣护炉的物料有很多种,其选择主要依据于冶炼工艺和物料的性质。
在整个钢铁冶炼过程中,常用的物料有镁球、石灰石、硅石等。
二、溅渣护炉的应用在钢铁冶炼过程中,溅渣护炉是一种常见的技术。
其应用可以有效地提高冶炼效率,降低生产成本,提高冶炼质量。
下面我们将分别介绍其应用在各个环节中的具体情况。
1.高炉在高炉冶炼中,溅渣护炉对炉壁保护尤为重要,可以有效地减少高炉的磨损和锈蚀。
目前,高炉冶炼中主要采用的溅渣护炉物料是镁球和石灰石。
镁球主要用于抑制磷和硫的生成,从而提高炉膛的可控性;石灰石则可以中和酸性物质,减少炉壁的腐蚀。
2.转炉在转炉冶炼中,溅渣护炉主要用于中和氧化物和碱性物质。
其主要物料是硅石和石灰石。
硅石主要用于中和氧化物,而石灰石则可以中和碱性物质,从而减少炉壁的腐蚀。
3.电炉在电炉冶炼中,溅渣护炉主要用于中和酸性物质。
其主要物料是石灰石和麻粉。
石灰石可以中和酸性物质,麻粉则可以降低炉壁的温度,从而减少炉壁的腐蚀。
总之,溅渣护炉在钢铁冶炼过程中起着非常重要的作用。
通过添加适当的物料,可以有效地保护炉壁不受腐蚀,延长炉壁的使用寿命。
转炉溅渣护炉技术9
9.什么是转炉溅渣护炉技术?答:转炉溅渣技术是近年来开发的一种提高炉龄的新技术。
它是在20世纪70年代广泛应用过的、向炉渣中加入含MgO的造渣剂造黏渣挂渣护炉技术的基础上,利用氧枪喷吹高压氮气,在2—4min内将出钢后留在炉内的残余炉渣喷溅涂敷在整个转炉内衬表面上,形成炉渣保护层的护炉技术。
该项技术可以大幅度提高转炉炉龄,且投资少、工艺简单、经济效益显著。
此项技术是由美国Praxair气体公司开发、在美国共和钢公司的GreatLakes(大湖)分厂最先应用,在大湖厂和GraniteCity厂实施后,并没有得到推广。
1991年美国LTV公司的Indiana HaBOr厂用溅渣作为全面护炉的一部分。
1994年9月该厂252t顶底复吹转炉的炉衬寿命达到15658炉,喷补料消耗降到0.37kg /t钢,喷补料成本节省66%,转炉作业率由1987年的78%提高到1994年的97%。
溅渣护炉技术能使炉衬在炉役期中相当长的时间内保持均衡,实现“永久性”炉衬。
10.溅渣护炉技术的基本原理是什么?答:溅渣护炉技术的基本原理,是在转炉出钢后,调整余留终点渣成分,利用MgO含量达到饱和或过饱和的终点渣,通过高压氮气的吹溅,在炉衬表面形成一层与炉衬很好烧结附着的高熔点溅渣层,如图2—1所示。
这个溅渣层耐蚀性较好,并可减轻炼钢过程对炉衬的机械冲刷,从而保护了炉衬砖,减缓其损坏程度,使得炉衬寿命得以提高。
11.溅渣护炉对炉渣的组成与性质有哪些要求?答:炉渣成分是指构成炉渣的各种矿物的成分,它决定了炉渣的基本性质。
一般说来,初期渣的主要成分是SiO2、MnO、CaO、MgO和FeO等,随着吹炼过程进行,石灰熔化、渣量增加,使SiO2、MnO的含量逐渐降低,CaO、MgO的含量逐渐增加。
13.底吹对复吹转炉溅渣的影响有哪些?答:在复吹转炉溅渣过程中,由于底吹射流的介入,熔池中炉渣的搅动增强。
底吹气体涌起熔渣高度与底吹气体射流搅拌能有关:εv. b=2×371KQT1/Vm ln (1+9.8ρL/P)式中εv. b——底吹气体射流的搅拌能,W/m3.s K——喷体体积增加率,%;Q——底吹气体流量(标态),m3/min;TL——底吹气体温度,℃;Vm——熔池体积,m3;ρL——熔池液体(熔渣)密度,m3/min;p——大气压力,Pa理论上分析增加底吹气体量Q,即增大底吹搅拌能εv. b ,有利于溅渣。
转炉溅渣护炉技术(讲座)PPT课件
实际上,溅渣护炉时残留在炉内的 终渣是一种最安全的留渣操作,它有利 于早化初渣,并可促进前期脱P。
首钢三炼钢在前炉溅渣和未溅渣两 种情况下,对吹炼3未溅渣的1.16%提高到1.95%。
(2)中期渣 转炉吹炼中期,铁水中Si、Mn已
转炉溅渣护炉技术
1、 溅渣护炉简介
图1 溅渣护炉示意图
•1991年美国LTV钢铁公司开始采用溅渣护 炉技术,现已有12个钢厂采用,其中内 陆钢厂1998年炉龄达33000次仍在吹炼。
•国内30吨以上转炉绝大部分采用溅渣护 炉技术,炉龄2万炉以上,莱钢30吨转炉 3万炉以上。
•国内部分15吨转炉采用溅渣护炉技术 (三明,安钢等)。 •武钢80吨复吹转炉底吹元件寿命与炉龄
同步,达1万炉以上。
2、溅渣护炉的炉渣控制
2.1溅渣护炉工艺过程
吹炼过程造好渣
出钢后将转炉摇正
降下氧枪吹氮2-3分钟
将多余炉渣倒出
2.2 造渣工艺
转炉采用溅渣护炉技术后, 造渣工艺可简单概括为“初渣早化, 过程渣化透,终渣做粘,溅渣挂 上”。
(1)初渣
在吹炼前期能否迅速形成高碱度的 炉渣,是减轻初渣对溅渣层及炉衬侵蚀 的一个重要环节。
当碱度从1.0提高到2.0时,MgO饱和值相应 由~12%降到~7%,早化初渣尽快提高碱度,MgO饱 和值会显著降低。因而,影响初渣MgO饱和溶解度 的主要因素是碱度。
温度升高,MgO饱和溶解度也相应增 加,大约是温度每提高50℃,MgO饱和 值增加1.0-1.3%。
当终渣碱度为3时,温度由1600℃ 升高到1700℃,MgO饱和值由6%增加到 8.5%。因此,影响终渣MgO饱和溶解度 的主要因素是温度。
在实施溅渣护炉后的造渣实践中,鞍 钢180t转炉使用活性石灰,并在开吹时 加入轻烧镁球、锰矿和复合球团,吹炼 5分钟时的初渣碱度由普通石灰的1.2提 高到2.0。
溅渣护炉
转炉溅渣护炉的效果,决定于溅渣层与炉衬间的结合状态。
溅渣层与炉衬的结合原理包括炉渣如何与炉衬砖有机地相结合,炉渣层如何有效地保护转炉炉衬。
1 溅渣层的成分与结构生产实践证明,采用溅渣护炉在转炉炉衬表面形成的溅渣层,在成分和岩相结构方面,不仅和炉衬砖有明显的差距,而且和转炉终渣(或改质处理后的炉渣)也有区别。
这种区别是由于反复溅渣过程中,炉衬耐火材料与炉渣间经过长时间的高温化学反应扩散渗透与溶解脱熔、熔化与析出、剥落与烧结等复杂的过程逐步形成的。
2 溅渣层成分的变化(1)在溅渣过程中,炉渣成分(指终渣溅后渣和溅在炉壁表面上的炉渣)不会发生明显的变化,喷溅到炉壁上的炉渣(或溅后渣)成分与终渣大致相同。
(2)由于炉衬表面温度不同和炉衬传热热流密度的差别,在溅渣过程中炉渣成分也会发生微小的变化。
这主要是由于溅渣中发生了“异相分流”效应,使渣射到炉衬表面上的一些液态低熔氧化物流失。
这就导致溅渣层表面高熔点化合物浓度稍有增加(如MgO结晶,C2S 和C3S),而低熔点氧化物(如FeO等)减少(溅后渣成分变化的趋势则相反),溅渣中“异相分流”引起的成分变化一般不超过2%。
(3)溅渣层的成分与转炉终渣有明显的区别,高熔点化合物(MgO结晶,C2S和C3S)的浓度明显增加;有一些氧化物(如MnO,P2O5,Al2O3,SiO2等)显著减少。
(4)对于不同的溅渣工艺,溅渣层的成分有明显的区别。
采用高FeO炉渣溅渣,溅渣层中MgO含量很高,达到58.4%;而TFe含量比终渣略有降低,CaO、SiO2等成分显著降低。
这说明高FeO炉渣溅渣形成的溅渣层主要以MgO,(MgO,Fe2O3)为主相。
采用低FeO 炉渣溅渣,溅渣层中CaO和MgO含量富集,SiO2含量略有降低,碱度升高,说明该溅渣层是以C3S为主相,以C2S和MgO结晶为辅相。
根据上述溅渣层与转炉中渣有成分上的明显差异,可以得到进一步推论如下:(1)溅渣层是通过炉渣与炉衬耐火材料间在较长时间内发生化学反应逐渐生成的。
转炉炼钢工艺(溅渣护炉)
溅渣护炉的负面影响
吹炼终点[%C] ·[%O]积随炉龄变化情 吹炼终点 积随炉龄变化情 况
关于经济炉龄的问题
生产率、 生产率、成本与炉龄关系
溅渣护炉的优点
大幅度降低耐材消耗; 大大提高转炉作业率,达到高效增产目的; 投资回报率高; 溅渣护炉综合效益每吨钢约为2~10元。
溅渣护炉的负面影响
底吹透气砖覆盖渣层厚度与吹炼终点[%C] ·[%O]积的关 底吹透气砖覆盖渣层厚度与吹炼终点 积的关 系
溅渣护炉的负面影响
底吹透气砖覆盖渣层厚度与吹炼终点[%C] ·[%O]积的关 底吹透气砖覆盖渣层厚度与吹炼终点 积的关 系
炉渣粘度的控制
过低的炉渣粘度有利溅渣的操作,即易溅起、挂 渣且均匀,但由于渣层过薄,会在摇炉时挂渣流 落; 而粘度过大,溅渣效果差,耳轴!渣线处不易溅到, 且炉底易上涨,炉膛变形,所以粘度需要根据实 际情况合理调整; 炉渣过热度增高,粘度下降。
溅渣操作参数控制
为了在尽可能短的时间内将炉渣均匀喷 敷在整个炉衬表面而形成有足够厚度的 致密溅渣层。必须控制好溅渣操作手段, 即根据炉形尺寸,来控制喷吹N2气压力 和流量、枪位和喷枪结构尺寸等喷溅参 数。
其它参数
喷溅时间:通常为2.5~4min; 喷枪夹角:许多厂家的经验表明采用12 度夹角比较理想。
需要采取的其它措施
炉衬材质不能因实行溅渣护炉技术而降 低,对使用镁碳砖而言,其碳含量应控 制为下限; 控制和降低终渣FeO含量; FeO 合理调整终渣MgO含量; 提高溅渣层熔化性温度,降低炉渣过热 度; 降低出钢温度。
- 1、下载文档前请自行甄别文档内容的完整性,平台不提供额外的编辑、内容补充、找答案等附加服务。
- 2、"仅部分预览"的文档,不可在线预览部分如存在完整性等问题,可反馈申请退款(可完整预览的文档不适用该条件!)。
- 3、如文档侵犯您的权益,请联系客服反馈,我们会尽快为您处理(人工客服工作时间:9:00-18:30)。
溅渣护炉溅渣护炉原理溅渣护炉工艺是把氮气通过氧枪吹入炉膛,高速氮气流股与渣面相遇后把一部分炉渣击碎成尺寸不等的液滴向四周飞溅。
由于流股的能量高,把熔池渣层击穿并形成凹坑,氮气流股遇到炉底后以一定角度形成反射气流,反射气流与渣坑表面的磨擦作用会带起一部分渣滴,使其飞到炉壁上。
通过这样的连续吹氮气,炉渣温度不断下降,渣滴不断黏附在炉衬上,直到溅渣操作结束。
由于炉渣的分熔现象(也叫选择性熔化或异相分流),是指附着于炉衬表面的溅渣层,其矿物组成不均匀,当温度升高时,溅渣层中低熔点物首先熔化,与高熔点相相分离,并缓慢地从溅渣层流淌下来;而残留于炉衬表面的溅渣层为高熔点矿物,反而提高了溅渣层的耐高温性能。
在溅渣层的形成过程中,经过多次“溅渣-熔化-溅渣”的循环和反复使溅渣层表面一些低熔点氧化物发生“分融”现象。
使溅渣层MgO结晶和C2S(2CaO·SiO2)等高熔点矿物逐渐富集,从而提高了溅渣层的抗高温性能,炉衬得到保护。
溅渣层保护炉衬的机理(1)对镁碳砖表面脱碳层的固化作用吹炼过程中镁碳砖表面层碳被氧化,使MgO颗粒失去结合能力,在熔渣和钢液的冲刷下大颗粒MgO松动→脱落→流失,炉衬被蚀损。
溅渣后,熔渣渗入并充填衬砖表面脱碳层的孔隙内,或与周围的MgO颗粒反应,或以镶嵌固溶的方式形成致密的烧结层。
由于烧结层的作用,衬砖表面大颗粒的镁砂不再会松动→脱落→流失,从而防止了炉衬砖的进一步被蚀损。
(2)减轻了熔渣对衬砖表面的直接冲刷蚀损溅渣后在炉衬砖表面形成了以MgO结晶,或C2S和C3S为主体的致密烧结层,这些矿物的熔点明显地高于转炉终点渣,即使在吹炼后期高炉温度下不易软熔,也不易剥落。
因而有效地抵抗高温熔渣的冲刷,大大减轻了对镁碳砖炉衬表面的侵蚀。
(3)抑制了镁碳砖表面的氧化,防止炉村砖体再受到严重的蚀损溅渣后在炉衬砖表面所形成的烧结层和结合层,质地均比炉衬砖脱碳层致密,且熔点高,这就有效地抑制了高温氧化渣,氧化性炉气向砖体内的渗透与扩散,防止镁碳砖体内部碳被进一步氧化,从而起到保护炉衬的作用。
(4)新溅渣层有效地保护了炉衬-溅渣层的结合界面新溅渣层在每炉的吹炼过程中都会不同程度的被熔损,但在下一炉溅渣时又会重新修补起来,如此往复循环地运行,所形成的溅渣层对炉衬起到了保护作用。
溅渣护炉工艺(1)熔渣成分的调整转炉采用溅渣护炉技术后,吹炼过程更要注意调整熔渣成分,要做到“初期渣早化,过程渣化透,终点渣做黏”;出钢后熔渣能“溅得起,粘得住,耐侵蚀”。
为此应控制合理的w(MgO),使终点渣适合于溅渣护炉的要求。
终点渣的成分决定了熔渣的耐火度和黏度。
影响终点渣耐火度的主要组成是MgO、TFe 和碱度w(CaO)/w(SiO2);其中w(TFe)波动较大,一般在10%~30%范围内。
为了溅渣层有足够的耐火度,主要应调整熔渣的w(MgO)。
表4-30为终点渣w(MgO)推荐值。
表1 终点渣w(MgO)推荐值终渣w(TFe)/%8~11 15~22 23~30终渣w(MgO)/%7~8 9~10 11~13根据理论分析与国外溅渣护炉实践来看,在正常情况下,转炉终点渣w(MgO)应控制在表1所示的范围内,以使溅渣层有足够的耐火度。
溅渣护炉对终点渣w(TFe)并无特殊要求,只要把溅渣前熔渣中w(MgO)调整到合适的范围,w(TFe)的高低都可以取得溅渣护炉的效果。
如果终点渣w(TFe)较低,渣中C2F量少,RO 相的熔化温度就高。
在保证足够耐火度情况下,渣中w(MgO)可以降低些。
终点渣w(TFe)低的转炉溅渣护炉的成本低,也容易获得高炉龄。
调整熔渣成分有两种方式:一种是转炉开吹时将调渣剂随同造渣材料一起加入炉内,控制终点渣成分,尤其是w(MgO)达到目标要求,出钢后不必再加调渣剂;倘若终点熔渣成分达不到溅渣护炉要求,则采用另一种方式,出钢后加入调渣剂,调整w(MgO)含量达到溅渣护炉要求的范围。
常用的调渣剂有轻烧白云石、生白云石、轻烧菱镁球、冶金镁砂、菱镁矿渣和高氧化镁石灰等。
调渣剂的作用主要是提高渣中MgO含量,选择调渣剂时,首先考虑MgO的含量多少。
综合考虑提出MgO质量分数的概念,用以比较调渣剂中MgO含量的高低。
MgO质量分数的定义如下:MgO质量分数(%)=w(MgO)/{1-w(CaO)+B×w(SiO2)} (4-26)式中,w(MgO)、w(CaO)、w(SiO2)分别为调渣剂的MgO,CaO,SiO2实际含量;B为炉渣碱度,可取B=3.5。
根据MgO含量选择调渣剂,应以冶金镁砂、轻烧菱镁球、轻烧白云石和含镁石灰为宜(MgO 质量分数不小于50%)。
显然,从成本考虑时,调渣剂应选择价格便宜的;从以上这些材料对比来看,生白云石成本最低;轻烧白云石和菱镁矿渣粒价格比较适中;高氧化镁石灰、冶金镁砂、轻烧菱镁球的价格偏高。
(2)合适的留渣量合适的留渣数量就是指在确保炉衬内表面形成足够厚度溅渣层,还能在溅渣后对装料侧和出钢侧进行摇炉挂渣即可。
形成溅渣层的渣量可根据炉衬内表面积,溅渣层厚度和炉渣密度计算得出。
溅渣护炉所需实际渣量可按溅渣理论渣量的1.1~1.3倍进行估算。
炉渣密度可取3.5t/m3,公称吨位在200t以上的大型转炉,溅渣层厚度可取25~30mm;公称吨位在1OOt以下的小型转炉,溅渣层的厚度可取15~20mm。
留渣量计算公式为:CBAKQ⋅⋅⋅=s(4-27)式中sQ——留渣量,t/炉;K——渣层厚度,m;A——炉衬的内表面积,m2;B——炉渣密度,t/m3;C——系数,一般取1.1~1.3。
不同公称吨位转炉的溅渣层重量如表2所示。
表2 不同吨位转炉溅渣层重量溅渣层重量/t 转炉吨位/t溅渣层厚度/mm10 15 20 25 3040 1.8 2.7 3.680 4.41 5.98140 8.08 10.78 13.48250 13.11 16.39 19.7300 17.12 21.4 25.7根据国内溅渣的生产实践,合理的留渣量也可根据转炉的具体容量按式(4-28)计算:nWQ301.0s=(n=0.583~0.650)(4-28)式中sQ——转炉留渣量,t/炉;W——转炉公称吨位,t。
(3)溅渣工艺①直接溅渣工艺即以炼钢过程中调整炉渣为主,出钢后基本不再调渣,直接进行溅渣操作。
直接溅渣工艺适用大型转炉,要求铁水等原材料条件比较稳定,吹炼平稳,终点控制准确,出钢温度较低。
其操作程序是:a.吹炼开始在加入第一批造渣材料的同时,加入大部分所需的调渣剂;控制初期渣w(MgO)在8%左右,可以降低炉渣熔点,并促进初期渣早化。
b.在炉渣“返干期”之后,根据化渣情况,再分批加入剩余的调渣剂,以确保终点渣w(MgO)达到目标值。
c.出钢时,通过炉口观察炉内熔渣情况,确定是否需要补加少量的调渣剂;在终点碳、温度控制准确的情况下,一般不需再补加调渣剂。
d.根据炉衬实际蚀损情况进行溅渣操作。
并确定是否需要对炉衬上的特殊部位进行喷补,以保证溅渣护炉的效果和控制良好炉型。
宝钢由于采用了复合吹炼工艺和大流量供氧技术,熔池搅拌强烈,终点渣w(TFe)在18%左右,为适应溅渣需要,w(MgO)由6.8%提高到10.3%,出钢温度在1640~1650℃,终点一般不需调渣直接溅渣。
②出钢后调渣工艺即在炼钢结束后,根据炉渣状况适当加入少量调渣剂用以降低炉渣过热度,提高炉渣黏度,然后进行溅渣。
出钢后调渣工艺适用于中小型转炉。
由于中小型转炉的出钢温度偏高,因此熔渣的过热度也高。
再加上原材料条件不够稳定,往往终点后吹,多次倒炉,致使终点渣w(TFe)较高,熔渣较稀;w(MgO)也达不到溅渣的要求,不适于直接溅渣。
只得在出钢后加入调渣剂,改善熔渣的性态,以达到溅渣的要求。
用于出钢后的调渣剂,应具有良好的熔化性和高温反应活性,较高的w(MgO),以及较大的热焓,熔化后能明显、迅速地提高渣中w(MgO)和降低熔渣温度。
其吹炼过程与直接溅渣操作工艺相同;出钢后的调渣操作程序如下:a.终点渣w(MgO)控制在8%~10%。
b.出钢时,根据出钢温度和炉渣状况,决定调渣剂加入的数量,进行炉后调渣。
c.调渣后进行溅渣操作。
出钢后调渣的目的是使熔渣MgO 含量达到饱和值,提高其熔化温度,同时由于加入调渣冷料吸热,从而降低了熔渣的过热度,提高了黏度,以达到溅渣的要求。
若单纯调整终点渣w(MgO),加调渣剂只调整w(MgO)达到过饱和值,同时吸热降温稠化熔渣,达到溅渣要求。
如果同时调整终点渣w(MgO)和w(TFe),除了加入适量的含氧化镁调渣剂外,还要加一定数量的含碳材料,以降低渣中w(TFe),也利于w(MgO)达到饱和。
(4)复吹转炉溅渣工艺在复吹转炉溅渣过程中由于底吹射流的介入,熔池中炉渣的搅动增强,底吹气体射流涌起熔渣高度与底吹气体射流搅拌能有关: ⎥⎦⎤⎢⎣⎡+⨯=p V KQT E l m v.b 8.91ln 3712ρ (4-29) 式中 v.b E ——底吹气体射流的搅拌能,W/(m 3·s);K ——喷吹体积增加率,%;Q ——底吹气体流量(标态),m 3/min ;T ——底吹气体温度,℃;m V ——熔池体积,m 3;l ρ——熔池液体(熔渣)密度,kg/m 3;p ——大气压力,MPa 。
理论上分析增加底吹气体流量Q,即增大底吹搅拌能,有利于溅渣。
水力学模拟实验表明,底气量变化对炉衬各高度溅渣量影响不大。
但工业实验中发现,适当的底气可防止底枪堵塞,有利于保证底枪正常操作。
(5)溅渣时间与溅渣频率①溅渣时间溅渣时间一般为2.5~4min。
溅渣时间过短,炉渣没有得到充分的冷却和混匀,炉渣条件比较差,即使溅到炉壁上,也不能很好地挂上,起不到护炉的作用。
在渣况正常的条件下,溅渣时间越长,炉衬挂渣越多,但也易造成炉底上涨和粘枪。
②溅渣频率a.开始溅渣护炉的时机。
在一个炉役中,什么时间开始溅渣护炉,要根据各厂的具体情况确定。
原则上由操作工根据对炉衬侵蚀情况的观察结果决定,若炉衬有明显的损耗,则应开始溅渣护炉。
一般从炉役的中期开始溅渣护炉,即在起始补炉时就应开始溅渣护炉。
b.溅渣的频率。
溅渣频率,即为合理溅渣的间隔炉数,是溅渣护炉的重要操作工艺参数之一。
在炉役的中期过于频繁溅渣,对炉型产生较大的影响(如炉型变小),并将影响炼钢作业时间,反而不利。
一般应在炉役的前期就开始溅渣,可以两炉一溅,在炉衬厚度为400mm 左右时应保持炉炉溅渣,力争炉衬厚度保持在300~400mm之间,形成动态平衡,有利于形成永久炉衬。
关于溅渣频率,可以概括为“前期不溅、中期两炉一溅、中后期炉炉溅”。
(6)影响溅渣效果的因素炉内溅渣效果的好坏,可从通过溅粘在炉衬表面的总渣量和在炉内不同高度上溅渣量是否均匀来衡量。