助镀剂助镀原理及检测方法
助镀液作用

1.助镀液作用工件浸渍助镀液的目的是保证工件在浸锌时,其表面的铁基体在短时间内与锌液起正常的反应,顺利生成一层Zn-Fe合金相层。
工件在经过脱脂、酸洗、清洗等生产工序处理后,在其表面上仍然会附有残余的铁盐、残酸等(焊接结构件的“存液”现象也不可避免);在工件浸入锌液前,工件洁净的铁基体表面,在这些残余污物的作用下,还可能与空气进行反应生成薄的氧化膜(锈),就必须再一次进行除锈。
为了防止这一现象的发生,酸洗到浸锌工序之间采用助镀液处理,也就是浸(浸渍或者涂覆)助镀液,其作用是:(1)进一步清除工件表面上残留的铁盐及未除掉的氧化铁等杂质。
助镀液对工件的钢铁表面起到清洁的作用,去除酸洗工件经清洗后残留在工件表面的铁盐或氧化物,使工件在浸锌时具有最大的表面活性。
这个作用主要是有氯化铵来完成的。
助镀液在工件表面形成的复盐盐膜中含有结晶水,这种结晶水会产生两种羟基酸,及氢氧化盐类,它们可以分解、破坏工件浸锌时在锌液表面所形成的氧化锌层,有利于生成Zn-Fe合金相层。
这也是一些不设置烘干、而是利用加热助镀液提高其自干特性进行热镀锌工艺的重要原因。
过量的铁盐带入助镀液的影响和盐酸相似,将增加锌灰的产生,另外一个影响需要根据铁的氧化状态而定。
生产中往往在采用双氧水除铁后,紧接着加入苛性钠或氨水来调整PH,并将pH控制在5左右,这种作法是为了保持助镀液工艺性的稳定。
如果提高pH,将使二价铁氧化成三价铁。
原氯化亚铁转换成氢氧化铁,但氢氧化铁在干燥阶段又无法完全被烘干。
生产中,烘干工序一般将工件的干燥温度控制在80℃~100℃,即使是温度达到150℃,包含在氢氧化铁中的水,也无法完全被去除,所以这些残留的水,仍将被带入锌锅与锌液反应产生锌灰,这也是热镀锌生产中,无法避免产生锌灰的原因。
如果提高工件的烘干温度,残留的水和助镀液复盐盐膜中的结晶水,都会被去除,但这样又会导致助镀液失效,因为助镀液复盐盐膜中的结晶水可以形成羟基酸,分解、破坏工件浸锌时在锌液表面所形成的氧化锌层,利于生成Zn-Fe合金相层。
助镀剂助镀原理及检测方法.
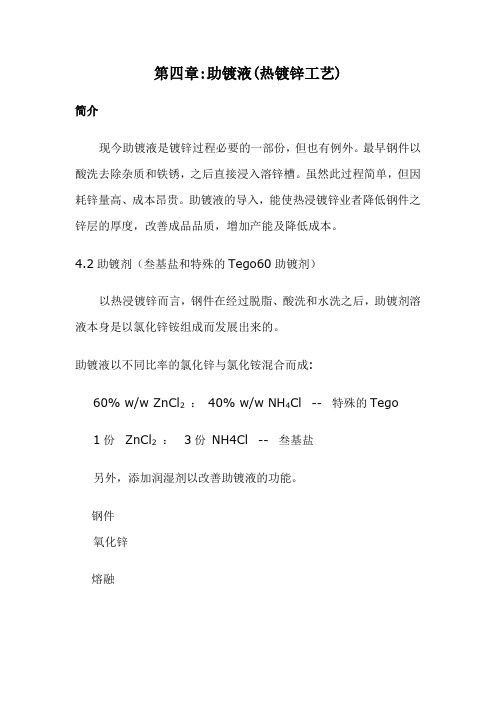
第四章:助镀液(热镀锌工艺)简介现今助镀液是镀锌过程必要的一部份,但也有例外。
最早钢件以酸洗去除杂质和铁锈,之后直接浸入溶锌槽。
虽然此过程简单,但因耗锌量高、成本昂贵。
助镀液的导入,能使热浸镀锌业者降低钢件之锌层的厚度,改善成品品质,增加产能及降低成本。
4.2助镀剂(叁基盐和特殊的Tego60助镀剂)以热浸镀锌而言,钢件在经过脱脂、酸洗和水洗之后,助镀剂溶液本身是以氯化锌铵组成而发展出来的。
助镀液以不同比率的氯化锌与氯化铵混合而成:60% w/w ZnCl2:40% w/w NH4Cl -- 特殊的Tego1份ZnCl2:3份NH4Cl -- 叁基盐另外,添加润湿剂以改善助镀液的功能。
钢件氧化锌熔融锌液功用助镀剂有几点功用:1. 防止烘乾时钢件表面氧化。
2. 分解溶融锌液附着在金属表面的氧化锌层。
氧化锌产生是因为空气中的氧和溶融锌液之反应(450~460℃),当钢件浸入溶融锌时,气化锌层附着其上。
假如:金属表面形成氧化锌,则内层的锌铁反应将受很大的影响,将造成镀件的浸镀时间较原来长,时间加长,最终将增加钢件上锌层厚度。
氯化锌是易受潮所以优先吸收钢件表面水分,因此可防止浸过助镀液的钢件,在烘乾时生锈。
NH4Cl →HCl + NH3ZnCl2.2H2O + HCl →(HCl(OH)2)H2 + ZnCl2Hydroxy Acids ____(ZnCl2(OH)2H2+ HCl氯化铵在锌槽中会分解产生盐酸和氨水,盐酸会和氯化锌吸收的结晶水,结合产生两种Hydroxy酸(HCl(OH)2)H2和(ZnCl2(OH)2)H2 + HCl )。
此两种Hydroxy酸可以分解钢件表面所生之氧化锌层。
操作参数浓度助镀剂浓度决定在处理钢件的种类钢件种类o Be 波美’S.G 比重oTW比重线材7 ~ 13 1.05 ~ 1.10 10 ~ 20薄板13 ~ 19 1.10 ~ 1.15 20 ~ 30管材/一般热镀件19 ~ 24 1.15 ~ 1.26 30 ~ 52超大型钢/锻造件30 ~ 40 1.26 ~ 1.38 52 ~ 76以Be波美浓度28被认为可适用于各种钢件并得到最佳效果’温度助镀液的最适温度是60℃-65℃,温度较低,助熔剂附着会较不均匀且较没效果;温度较高,则助熔剂附着太厚,增加消耗。
无烟助镀剂热浸镀锌的镀件质量和镀层性能研究
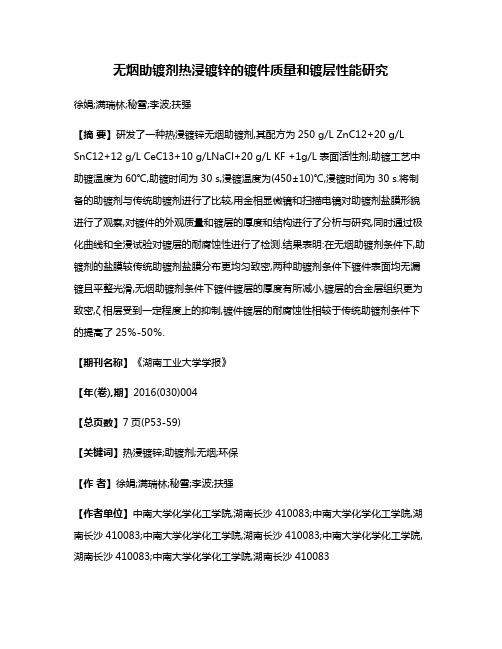
无烟助镀剂热浸镀锌的镀件质量和镀层性能研究徐娟;满瑞林;秘雪;李波;扶强【摘要】研发了一种热浸镀锌无烟助镀剂,其配方为250 g/L ZnC12+20 g/L SnC12+12 g/L CeC13+10 g/LNaCl+20 g/L KF +1g/L表面活性剂;助镀工艺中助镀温度为60℃,助镀时间为30 s,浸镀温度为(450±10)℃,浸镀时间为30 s.将制备的助镀剂与传统助镀剂进行了比较,用金相显微镜和扫描电镜对助镀剂盐膜形貌进行了观察,对镀件的外观质量和镀层的厚度和结构进行了分析与研究,同时通过极化曲线和全浸试验对镀层的耐腐蚀性进行了检测.结果表明:在无烟助镀剂条件下,助镀剂的盐膜较传统助镀剂盐膜分布更均匀致密,两种助镀剂条件下镀件表面均无漏镀且平整光滑,无烟助镀剂条件下镀件镀层的厚度有所减小,镀层的合金层组织更为致密,ζ相层受到一定程度上的抑制,镀件镀层的耐腐蚀性相较于传统助镀剂条件下的提高了25%-50%.【期刊名称】《湖南工业大学学报》【年(卷),期】2016(030)004【总页数】7页(P53-59)【关键词】热浸镀锌;助镀剂;无烟;环保【作者】徐娟;满瑞林;秘雪;李波;扶强【作者单位】中南大学化学化工学院,湖南长沙410083;中南大学化学化工学院,湖南长沙410083;中南大学化学化工学院,湖南长沙410083;中南大学化学化工学院,湖南长沙410083;中南大学化学化工学院,湖南长沙410083【正文语种】中文【中图分类】TQ050钢铁材料是世界上产量最高的金属材料[1-2],但钢材尤其是户外使用的钢材面临的最大问题是腐蚀[3],据统计,全世界每年腐蚀的钢铁材料约占世界钢铁年产量的1/4~1/3[4-5]。
热镀锌技术也称热浸镀锌,是将钢铁构件浸入熔融的锌液中获得金属覆盖层,由于锌层具有机械保护及电化学保护的双重效果[6],已成为钢铁防腐的主要方法之一[7-8]。
热镀锌的助镀理论及相关工序生产注意事项 唐山鑫德 2011

溶剂助镀剂是热浸镀前处理中一道重要处理工序,它不仅可以弥补前面几道工序可能存在的不足,还可以进一步活化钢铁表面,提高镀锌质量。
这是其他钢铁防腐工艺中所没有的。
它不仅直接影响镀层质量,还对锌耗,成本有很大影响。
如不采用溶剂助镀,会容易产生漏镀,而且会产生较多的锌渣,造成锌耗增加,影响镀锌质量。
现在最常用的采用氯化锌和氯化铵混合溶液作为溶剂来助镀。
所谓助镀就是将酸洗后的制件再浸入一定成分的氯化锌铵助镀液中,提出后在制件表面形成一层薄的氯化锌铵盐膜的过程。
一.助镀的作用机理:1助镀的作用㈠对钢铁表面起到清洁的作用,去除酸洗清洗后残留在制件表面的铁盐或氧化物,使钢铁件在进入锌浴时具有更大的表面活性。
㈡在制件表面沉积上一层盐膜,可防止制件从助镀池到进入锌锅这一段时间内在空气中锈蚀。
㈢净化制件使浸入液体锌时能与液体锌快速浸润并反应。
2.制件表面覆盖的氯化锌铵盐膜的活化作用㈠低于200oC时,在制件表面会形成一种复合盐酸,这种强酸保证了在干燥过程中制件表面无法形成氧化膜而保持活化状态。
㈡在200oC以上时,制件表面的助镀液盐膜中的NH4CL会在较高温度下分解成NH3和HCL,此时HCL对钢基体的侵蚀占了主导,使钢基体表面不能形成氧化物,保持钢基体的活化状态。
故在热浸镀锌时正确使用含有NH4CL的助镀剂是很重要的。
二.助镀剂的成分范围及工艺参数对于助镀液,除了对其质量浓度需要控制外,氯化铵和氯化锌的比例,溶液中的二价铁盐含量,PH值,温度以及杂质含量等因素均会对助镀效果产生较大效果。
因此助镀液的成分和工艺参数是衡量其质量和效果的重要因素。
三.助镀剂成份及工艺参数的影响1.助镀剂质量浓度。
助镀液质量浓度的高低对助镀效果影响很大。
当助镀液质量浓度过低(低于80g/L)时,镀件浸锌时容易产生“漏镀”;当助镀液质量浓度偏低(80-150g/L)时,由于制件表面附着的盐膜量少,不能有效活化制件表面,难以获得平滑均匀的镀层;当助镀液质量浓度偏高(300-500g/L)时,由于制件表面盐膜过厚,不易干透,在浸锌时将引起锌的飞溅,产生更多的锌灰,更浓的烟尘,以及更厚的镀层;当助镀液质量浓度过高(超过500g/L)时,制件表面形成的盐膜层将分成内外两层,外层薄而干,内层潮湿且呈糊状。
助镀液铁离子检验

助镀液中铁离子含量检测
取1ml的助镀液,加入3ml的30%的过氧化氢(H2O2)再加入10ml水,加热至沸,冷却后加10ml(1+1)的氨水,过滤,并用10ml的(1+1)氨水洗涤沉淀,弃去滤液,把带有沉淀的漏斗置于一干净的250ml锥形瓶上,用10ml热的(1+1)盐酸洗涤于锥形瓶中,加热至沸。
加入6滴1g/L的甲基橙。
趁热边摇边滴加SnCl2溶液还原Fe3+至溶液变为粉红色,停止加SnCl2溶液,再摇几下至粉色褪去。
然后加入50ml水,15ml硫磷混酸(15+15+75),2-4滴二苯胺磺酸钠(5g/L),立即用K2Cr2O7标准溶液滴定至紫红色为终点。
c(铁离子)=C*V*55.85/a (g/L)
C---K2Cr2O7标准溶液的浓度mol/L。
V---消耗K2Cr2O7标准溶液的体积ml。
a---取样量ml。
镀液性能与镀层质量检验培训课件

04
镀液性能的检测与维护
镀液性能的检测方法
了解镀液性能的检测方法对于保证镀 层质量至关重要。
定期检测镀液性能是维护镀层质量的 重要环节。
通过物理、化学和电化学等方法,对 镀液的成分、浓度、温度、酸碱度等 进行检测,确保其符合工艺要求。
根据不同的镀液类型和工艺要求,制 定合理的检测计划,定期对镀液进行 检测,及时发现并解决潜在问题。
粗糙度
基材表面的粗糙度对镀层的结合 力和外观都有影响,适当的粗糙 度可以提高镀层的附着力和耐磨
性。
材质
不同材质对电镀的适应性不同, 前处理阶段需要考虑基材的材质 和特性,选择合适的电镀工艺和
配方。
03
镀层质量的检验方法
外观检验
通过目视或低倍显微镜检查镀层的外观,评估其表面状态、颜色、光洁度等是否 符合要求。
金属盐浓度
金属盐是构成镀液的主要成分,其浓 度直接影响镀层中金属的含量和覆盖 度,过高或过低都会影响镀层质量。
络合剂
添加剂
添加剂可以改善镀液的电化学行为, 提高镀层的平滑度和结合力,常见的 添加剂包括表面活性剂、稳定剂和光 亮剂等。
络合剂的作用是使金属离子形成可溶 性络合物,控制络合剂的种类和浓度 可以调整镀层的光泽度和硬度。
确保实验室内工具齐全,设备状态良好,如滴定 管、烧杯、搅拌器等。
操作步骤
按照规定的顺序进行实验操作,确保每一步都准 确无误,如溶液的配制、镀层的制备等。
技巧分享
在实验过程中,掌握一些技巧可以提高实验效率, 如快速搅拌、准确滴定等。
安全防护措施
佩戴防护眼镜和实验服
在实验过程中,务必佩戴合适的防护眼镜和实验服,以防止溶液 溅出伤人和化学物质污染。
热镀锌钢管助镀剂的成分分析及影响
热镀锌钢管助镀剂的成分分析及影响作者:陈国强张红田来源:《商品与质量·建筑与发展》2014年第05期【摘要】热镀锌层质量及热镀锌过程中的锌耗成本与热镀锌的助镀工艺密切相关,通过对热镀锌助镀工艺的研究,阐述了热镀锌助镀作用机理,给出了钢铁制件热镀锌时助镀液的有效成分范围及工艺参数为氯化铵和氯化锌的总质量浓度、铵锌比、PH值、温度。
并分析了助镀液浓度、成分配比、铁盐含量、除铁方法、PH值和温度等因素对热镀锌的影响。
结果表明,要获得良好的镀锌质量及较低的生产成本,必须对热镀锌助镀液成分及工艺条件进行严格控制。
【关键词】热镀锌;钢管;助镀剂;成分;除铁【Abstract】 The quality of hot dip galvanized coating and the cost of zinc consumption during the hot galvanizing, are closely connected with the galvanizing fluxing technology. Based on the research about the galvanizing fluxing technology, the present paper has explained the mechanism of hot galvanizing fluxing, indicted the effective composition and technological parameters of the steelwork galvanizing, which including the total mass concentration, An/Zn ratio, pH,temperature of ammonium chloride and zinc chloride. Moreover, this paper also has analyzed the effect on the hot galvanizing by concentration of flux, composition proportion, molysite content,method of removing molysite, pH and temperature, etc. The research results show that, we must strictly controll the composition of flux and technology conditio.,if we expect to obtain the good quality as well as the low output cost of hot dip galvanized coating.【Key Words】 hot-dip galvanizing;Steel pipe;plating auxiliary;composition;Removing ferric ion1 概述熱镀锌钢管生产工艺中助镀剂的应用,在浸锌前处理工序中是非常重要的工序,目前,国内外研究和应用的是溶剂助镀法、盐酸助镀、氧化还原法和热浸渗铝法。
助镀液的测定方法
助镀液的测定方法
助镀液的测定方法可以根据所需要测量的指标不同,采用不同的方法。
1. pH值的测定
采用酸碱滴定法或pH电极法,将助镀液样品加入一定量的标准酸或碱溶液中,记录所需的转移指标,根据相应的计算公式计算出pH值。
2. 氧化还原电位的测定
采用电化学法,使用参比电极和工作电极,将助镀液样品置于电解池中,同时施加一定的电位,根据参比电极和工作电极之间的电位差,计算出氧化还原电位。
3. 密度的测定
使用密度计将助镀液样品的密度进行测量,根据所测量得的数值,参考助镀液的密度标准值,判断助镀液浓度的变化。
4. 含量的测定
使用标准化学分析方法,如滴定法、分光光度法、原子吸收光谱法等,对助镀液中所需要测定的物质进行分析和定量。
5. 黏度的测定
使用黏度计测量助镀液样品的粘度,根据所测得数值,判断助镀液浓度和稠度的变化。
热镀锌工艺助镀剂中除铁工艺对比
热镀锌助镀剂除铁工艺助镀剂除铁主要是除去助镀剂中的二价铁离子。
将二价铁离子氧化成三价铁离子,三价铁离子被水解生成氢氧化铁。
氢氧化铁不溶于水,经沉淀在助镀剂中被分离。
除铁的方法有很多。
有用压缩空气氧化,有用臭氧氧化,有用化学氧化剂氧化等。
在此只介绍化学法氧化除铁的原理和方法。
目前国内大多采用氧化提纯法除铁,其工艺为:调整PH值——氧化除铁——过滤(分离)。
1、调整PH值:助镀剂中的铁离子一般以Fe2+即氯化亚铁状态存在,Fe2+在PH值很大(PH=8.5)时,或锌含量不大而Fe2+很大时才能水解析出沉淀。
因此必须将Fe2+经氧化成为Fe3+,Fe3+在PH=1.7时即可发生水解,形成氢氧化锌沉淀后很容易被除去。
锌水解时PH值为5.0—5.5,因此在除铁工艺中为便于控制PH值,一般将PH值调整在3—4。
若PH值小于3:KClO3+2HCl=KCl+O2↑+H2O+Cl2↑4KMnO4+4HCl=4KCl+4MnO2+3O2↑+2H2O2H2O2=2H2O+O2↑(酸性条件)Ca(ClO)2+4HCl=2Cl2↑+ CaCl2+2H2O这时会使氧化剂与酸反应会造成氧化剂的消耗,可以用氨水、锌、氧化锌调整PH值。
NH4OH+HCl=H2O+NH4ClZn+2HCl=ZnCl2+H2↑ZnO+2HCl=ZnCl2+H2O若PH值大于4:ZnCl2+2H2O=Zn(OH)2↓+2HCl这时会使氯化锌水解生成氢氧化锌沉淀,造成氯化锌浪费,此时可用盐酸调整。
在测试PH值时可采用如下方法:取一份过滤好的助镀剂与同体积的水在试管中混合后摇匀,若产生白色的絮状混合物即为合格;若产生白色的胶状体则说明PH值超过4,需加酸调整;若加水后溶液仍然澄清说明酸度大,需加氨水或锌粉或氧化锌调整。
2、氧化除铁处理在助镀剂中加入氧化剂,将二价铁氧化成三价铁,使之水解沉淀分离。
化学法除铁通常是用高锰酸钾、氯酸钾、氯酸钠、次氯酸钠、次氯酸钙、过氧化氢等作为氧化剂。
助镀液的测定方法
助镀液的测定方法
助镀液的测定方法会根据具体的成分和性质有所不同。
以下是一般常用的助镀液测定方法:
1. 比重测定法:通过测量助镀液与水的比重差异来确定助镀液的浓度。
这种方法通常用于测定含有金属盐类的助镀液。
2. 密度测定法:通过测量助镀液的密度来确定浓度。
这种方法适用于无机盐、有机盐和酸碱性物质的助镀液浓度测定。
3. pH测定法:通过测量助镀液的酸碱度(pH值)来确定助镀液的浓度和性质。
这种方法通常适用于酸碱性助镀液的测定。
4. 离子浓度测定法:通过离子选择电极或离子色谱等方法,测定助镀液中特定离子的浓度,从而确定助镀液的成分和浓度。
5. 过氧化物测定法:对于含有过氧化物的助镀液,可以采用滴定法或者分光光度法来测定过氧化物的浓度。
需要注意的是,助镀液的浓度和成分测定通常需要在实验室或专门设备下进行,操作时应注意安全,并按照具体方法和设备的要求进行。
- 1、下载文档前请自行甄别文档内容的完整性,平台不提供额外的编辑、内容补充、找答案等附加服务。
- 2、"仅部分预览"的文档,不可在线预览部分如存在完整性等问题,可反馈申请退款(可完整预览的文档不适用该条件!)。
- 3、如文档侵犯您的权益,请联系客服反馈,我们会尽快为您处理(人工客服工作时间:9:00-18:30)。
第四章:助镀液(热镀锌工艺)简介现今助镀液是镀锌过程必要的一部份,但也有例外。
最早钢件以酸洗去除杂质和铁锈,之后直接浸入溶锌槽。
虽然此过程简单,但因耗锌量高、成本昂贵。
助镀液的导入,能使热浸镀锌业者降低钢件之锌层的厚度,改善成品品质,增加产能及降低成本。
4.2助镀剂(叁基盐和特殊的Tego60助镀剂)以热浸镀锌而言,钢件在经过脱脂、酸洗和水洗之后,助镀剂溶液本身是以氯化锌铵组成而发展出来的。
助镀液以不同比率的氯化锌与氯化铵混合而成:60% w/w ZnCl2:40% w/w NH4Cl -- 特殊的Tego1份ZnCl2:3份NH4Cl -- 叁基盐另外,添加润湿剂以改善助镀液的功能。
钢件氧化锌熔融锌液功用助镀剂有几点功用:1. 防止烘乾时钢件表面氧化。
2. 分解溶融锌液附着在金属表面的氧化锌层。
氧化锌产生是因为空气中的氧和溶融锌液之反应(450~460℃),当钢件浸入溶融锌时,气化锌层附着其上。
假如:金属表面形成氧化锌,则内层的锌铁反应将受很大的影响,将造成镀件的浸镀时间较原来长,时间加长,最终将增加钢件上锌层厚度。
氯化锌是易受潮所以优先吸收钢件表面水分,因此可防止浸过助镀液的钢件,在烘乾时生锈。
NH4Cl →HCl + NH3ZnCl2.2H2O + HCl →(HCl(OH)2)H2 + ZnCl2Hydroxy Acids ____(ZnCl2(OH)2H2+ HCl氯化铵在锌槽中会分解产生盐酸和氨水,盐酸会和氯化锌吸收的结晶水,结合产生两种Hydroxy酸(HCl(OH)2)H2和(ZnCl2(OH)2)H2 + HCl )。
此两种Hydroxy酸可以分解钢件表面所生之氧化锌层。
操作参数浓度助镀剂浓度决定在处理钢件的种类钢件种类o Be 波美’S.G 比重oTW比重线材7 ~ 13 1.05 ~ 1.10 10 ~ 20薄板13 ~ 19 1.10 ~ 1.15 20 ~ 30管材/一般热镀件19 ~ 24 1.15 ~ 1.26 30 ~ 52超大型钢/锻造件30 ~ 40 1.26 ~ 1.38 52 ~ 76以Be波美浓度28被认为可适用于各种钢件并得到最佳效果’温度助镀液的最适温度是60℃-65℃,温度较低,助熔剂附着会较不均匀且较没效果;温度较高,则助熔剂附着太厚,增加消耗。
当然若附着较厚助熔剂在工件上锌灰产生会降低。
不过太厚时则成反效果。
时间一般需2 ~ 5 分钟即可得到好的助熔剂附层,这也让钢件充分加热以助烘乾。
延长在助镀液浸泡时间,将增加在酸性助熔液中铁的含量。
另外在助熔剂附层会产生FeCl3氯化铁,它将吸收乾躁时残留的水份,导致浸镀时,熔融锌液与铁离子和水反应,增加氧化锌和锌灰之生成。
PH助镀液的PH控制在3 ~5.5 。
当PH降低,更多的铁将被分解入助镀液,导致氯化铁FeCl3含量增加,锌灰产生将增加。
铁Fe助镀液应该控制铁的最大含量10g/1,维持低含量铁是低锌灰产生的关键。
助熔剂的铁含量超过10g/1。
仍可继续操作,但锌灰和锌的耗费将增加。
润湿剂添加0.2 ~ 0.5% v/v 的润湿剂,将有助于增加助镀剂附层的效果和均匀性。
过程分析助镀槽应该依下列变数, 每3至4个月分析一次。
1. 氯化锌2. 氯化铵3. 上两项的比率4. 铁离子5. PH6. 比重热镀锌工艺中的助镀剂的作用是?为什么要用氯化锌和氯化铵的混合液做助镀剂。
最佳答案助镀剂使熔剂正常的助镀作用受到阻碍,导致局部漏镀等缺陷,所以不能将热镀锌的熔剂直接移作热镀Al-Zn合金工艺用。
热浸镀锌助镀剂的化学法除铁工艺及经济性分析吴起鞍山鞍海金属添加剂有限公司通讯地址:辽宁省海城市大屯镇邮政编码:114225 摘要:近几年,许多热浸镀锌企业越来越重视助镀剂的除铁处理,本文叙述了国内热浸镀助镀剂除铁处理的现状、助镀剂的分类、化学法除铁处理工艺及经济性分析。
关键词:热浸镀锌;化学法除铁;经济性1、现状近几年,由于热浸镀行业迅猛发展,原来酸洗之后不浸助镀剂直接镀锌的传统工艺逐渐已被摒弃。
这样已经使用助镀剂的企业越来越多的开始重视助镀剂的除铁工艺。
由于酸洗后铁盐被带到锌锅内,1公斤铁可产生25公斤锌渣,不但造成锌耗增加、镀锌成本增高,而且还会使锌液中氧化物和其他杂质增加,这样会造成锌液老化、锌液黏度增加,使热浸镀锌质量下降。
原来干法镀锌工艺规程要求,助镀剂中铁盐含量不大于30g/l,现在很多企业控制铁盐含量不大于5g/l,甚至有些企业在助镀工序采用连续除铁,连续过滤的方法控制铁盐含量。
然而现在还有的企业不了解助镀剂除铁的有关原理,认为助镀剂直接用过滤泵或压滤机过滤就是除铁了。
还有的企业随便加一些氨水和双氧水经过滤后就认为是除铁了,实际根本达不到除铁的目的。
2、助镀剂的种类。
目前国内热浸镀锌企业采用多种助镀剂配比方式,但广泛使用的助镀剂是氯化锌和氯化铵混合而成的复盐。
基本都是根据企业的实际使用情况进行配比,有的是纯氯化铵溶液,有的是氯化锌和氯化铵混合而成的复合盐。
复合盐有高氯化锌低氯化铵的复合盐,也有低氯化锌高氯化铵的复合盐。
还有些企业为了使用助镀添加剂而特殊制定氯化锌与氯化铵的复合盐的比例,它的比例是氯化锌80-100g/l,氯化铵120-150g/l,这是由于氯化锌吸水性决定的。
如果在高氯化锌配比的溶剂中加入助镀添加剂,而且预镀件存放时间较长时,氯化锌吸水会使助镀添加剂起不到防爆作用。
因此说,氯化铵氯化锌含量高低主要是取决于预镀件存放时间长短和有无烘干来决定的。
氯化锌含量越高形成的助镀膜越厚,储存时间越长,但吸水性越强。
氯化铵含量越高,崩锌虽然减小,但氯化铵分解后烟气增大。
现在大部分企业都采用助镀剂加热的方式,加入助镀添加剂后预镀件可短时间存放,在生产中浸助镀剂后马上进行镀锌作业,取消了干燥工序。
3、助镀剂除铁工艺助镀剂除铁主要是除去助镀剂中的二价铁离子。
将二价铁离子氧化成三价铁离子,三价铁离子被水解生成氢氧化铁。
氢氧化铁不溶于水,经沉淀在助镀剂中被分离。
除铁的方法有很多。
有用压缩空气氧化,有用臭氧氧化,有用化学氧化剂氧化等。
在此只介绍化学法氧化除铁的原理和方法。
目前国内大多采用氧化提纯法除铁,其工艺为:调整PH值——氧化除铁——过滤(分离)。
3.1、调整PH值:助镀剂中的铁离子一般以Fe2+即氯化亚铁状态存在,Fe2+在PH值很大(PH=8.5)时,或锌含量不大而Fe2+很大时才能水解析出沉淀。
因此必须将Fe2+经氧化成为Fe3+,Fe3+在PH=1.7时即可发生水解,形成氢氧化锌沉淀后很容易被除去。
锌水解时PH值为5.0—5.5,因此在除铁工艺中为便于控制PH值,一般将PH值调整在3—4。
●若PH值小于3:KClO3+2HCl=KCl+O2↑+H2O+Cl2↑4KMnO4+4HCl=4KCl+4MnO2+3O2↑+2H2O2H2O2=2H2O+O2↑(酸性条件)Ca(ClO)2+4HCl=2Cl2↑+ CaCl2+2H2O这时会使氧化剂与酸反应会造成氧化剂的消耗,可以用氨水、锌、氧化锌调整PH值。
NH4OH+HCl=H2O+NH4ClZn+2HCl=ZnCl2+H2↑ZnO+2HCl=ZnCl2+H2O●若PH值大于4:ZnCl2+2H2O=Zn(OH)2↓+2HCl这时会使氯化锌水解生成氢氧化锌沉淀,造成氯化锌浪费,此时可用盐酸调整。
在测试PH值时可采用如下方法:取一份过滤好的助镀剂与同体积的水在试管中混合后摇匀,若产生白色的絮状混合物即为合格;若产生白色的胶状体则说明PH值超过4,需加酸调整;若加水后溶液仍然澄清说明酸度大,需加氨水或锌粉或氧化锌调整。
3.2、氧化除铁处理在助镀剂中加入氧化剂,将二价铁氧化成三价铁,使之水解沉淀分离。
化学法除铁通常是用高锰酸钾、氯酸钾、氯酸钠、次氯酸钠、次氯酸钙、过氧化氢等作为氧化剂。
高锰酸钾除铁的反应原理:5FeCl2+KMnO4+8HCl=MnCl2+5FeCl3+4H2O+KClFeCl3+3H2O=Fe(OH)3↓+3HCl氯酸钾(钠)除铁的反应原理:6FeCl2+KClO3+6HCl=6FeCl3+KCl+3H2OFeCl3+3H2O=Fe(OH)3↓+3HCl次氯酸钙除铁的反应原理:4FeCl2+Ca(ClO)2+4HCl=4FeCl3+CaCl2+2H2OFeCl3+3H2O=Fe(OH)3↓+3HCl过氧化氢除铁的反应原理2FeCl2+2H2O2+2HCl=2FeCl3+2H2OFeCl3+3H2O=Fe(OH)3↓+3HCl在除铁过程中,首先根据化验得出的铁盐含量计算出氧化剂的用量,将氧化剂用水制成饱和溶液后放入助镀槽中,这时助镀槽温度应控制在60℃—80℃。
若温度过低则造成反应速度变慢。
在加入氧化剂时特别要注意:要加饱和溶液,不要加固体。
因为加入的固体氧化剂颗粒在溶解时容易被水解后的Fe(OH)3包裹,使之不再继续溶解而沉入底渣中,造成氧化剂大量浪费。
3.3、过滤(分离)目前除铁后分离方式主要有过滤泵过滤、板块压滤机过滤、自然沉降过滤三种方式。
自然沉降过滤所需温度要控制在80℃以上,将已制成饱和溶液的絮凝剂(聚丙烯酰胺)放入助镀槽中均匀搅拌,使Fe(O H)3迅速沉降。
沉降后,上部为清液,下部为底渣。
最后可将混液和底渣排放,而清液可用酸泵抽出使用。
4、经济性分析氧化剂的选择应根据其来源、价格、使用量等条件来确定。
1、高锰酸钾:5FeCl2+KmnO4+8HCl=MnCl2+5FeCl3+4H2O+KCl根据方程式计算得出:除掉1公斤氯化亚铁需使用高锰酸钾0.19公斤。
2、氯酸钾(钠):6FeCl2+KClO3+6HCl=6FeCl3+KCl+3H2O根据方程式计算得出:除掉1公斤氯化亚铁需使用氯酸钾0.16公斤或需氯酸钠0.14公斤。
3、次氯酸钙(钠):4FeCl2+Ca(ClO)2+4HCl=4FeCl3+CaCl2+2H2O根据方程式计算得出:除掉1公斤氯化亚铁需使用次氯酸钙0.57公斤或需次氯酸钠0.29公斤。
4、过氧化氢:2FeCl2+2H2O2+2HCl=2FeCl3+2H2O根据方程式计算得出:除掉1公斤氯化亚铁需使用过氧化氢0.13公斤。
从上表可以看出,每除去1公斤氯化亚铁所需氧化剂的费用从高到低排序为:高锰酸钾——次氯酸钙——次氯酸钠——氯酸钾——过氧化氢——氯酸钠。
因为过氧化氢是最洁净的氧化剂,所以目前很多企业使用过氧化氢除铁。
但由于其为液体,浓度低、体积大,不便于运输和贮存,而且过氧化氢存放一年浓度还会下降约3%,造成了成本加大。
另外过氧化氢在使用过程中对人体危害较大,其蒸汽对眼睛、鼻子、喉咙造成强烈的刺激,最终可能导致慢性呼吸器官疾病,皮肤接触也会造成疼痛及腐蚀,迸入眼睛有可能致盲。