转炉炼钢动态控制技术_全红
电炉炼钢工艺培训课件.ppt

9 .1 0
相对成本* (参考值)
3 .7 3 .2 6 .0 1 .8 0 .5 ~ 0 .6 0 .3 ~ 0 .6
化学反应中各发热元素的来源首先是炉料――废钢和生 铁,还有是由碳枪喷入的碳粉或焦粉。对于普通铁水,每吹入 1m 3 的 氧 气 ,所 含 各 元 素 在 1600 ℃ 时 反 应 理 论 发 热 值 约 为 4kw h。
5 m in
16 1 5 /5
1 5 /5
1 8 /6 3 m in
1 5 /5
4 m in 1 8 /6 8 m in
2 m in
2 m in
2 m in
12
8
4
0
0
5
10
15
20
25
30
35
40
45
50
(一 次 料 ) (加 铁 水 )
(二 次 料 )
(精 炼 )
供 电 时 间 m in
5.4 电炉氧化期操作
废钢熔化过程:从中心向四周、从热区向冷区、 从下向上。
熔化期操作原则:合理供电、合适吹氧、提前 造渣。
吹氧方式:自耗式:可切割、可吹渣钢界面; 水冷式:只能吹渣钢界面。
优化的供电曲线
电 压 级 /电别 流 级 V别 / A
28
24
2 1 /6
2 1 /6
20
5 m in
5 m in 1 9 /6
1 8 /6
5 电炉冶炼工艺
传统冶炼工艺(三段工艺) 熔化期、氧化期、还原期
现代冶炼工艺(二段工艺) 熔化期、氧化期、加炉外处理; 或称熔氧脱磷期、脱碳升温期
操作步骤:补炉、装料(配料)、熔化期、 氧化期、精炼(或还原期)、出钢
炼钢转炉煤气回收及其连锁控制方案技术应用
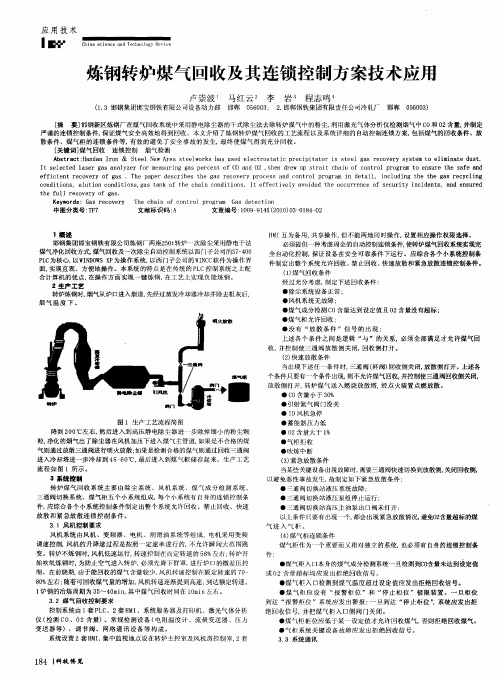
中图 分类号 : F T7
文 献标 识码 : A
文章 编号 :0 9 9 4 (0 0 0 — 1 4 0 10 — 1X2 1) 30 8— 2
1概 述 邯钢 集 团邯宝钢 铁有限 公司炼 钢厂两 座20 转炉~ 次除尘 采用静 电干法 5t 煤气 净化 回收方 式, 煤气 回收及一 次除尘 自动控制系 统 以西 门子公司 的s—0 74 0 PC L 为核 心, ID W P 操作系 统, 以WN O SX 为 以西 门子公 司 的W N C IC 软件为 操作 界 面, 实现直观 、方 便地操 作 。本系统 的特 点 是在传 统 的 P C控制 系统 之上 配 L 合计 算机 的优 点, 在操 作方 面 实现 一键炼 钢 , 工艺上 实 现 负能炼 钢 。 在 2生 产 工艺 转炉炼钢 时, 烟气从 炉 口进入 烟道, 先经过蒸 发冷却器冷 却并除去粗 灰后, 烟气温 度下 。
t e f l r c v r f g s h u 1 eo eyo a . Ky od e w r s: G s e o e y a r c v r T e c a n f c n r lp o r m G s d t c i n h h i o o t o r g a a e e t o
应用 技术
I- ■
炼钢转炉煤气 回收及其连锁控制方 案技术应用
卢 崇波 马红云z 李
(. 邯钢集 团邯 宝钢铁 有 限公司设 备动 力部 13 邯郸
岩 。 程 志呜
邯郸 0 6 0) 5 03
0 60 : 2 邯郸 钢铁 集团有 限责任 公 蟊冷轧厂 50 3 . = 』
[ 要] 摘 邯钢 新区炼钢 厂在 煤气 回收 系统 中采用 静 电除尘器 的干式 除 尘法去 除转 炉煤气 中 的粉尘 , 用激 光气 体分析 仪检 测烟气 中 c 利 O和 O 含 量, 2 并制 定 严 谨的连 锁控制 条件 , 保证 煤气 安全 高效地 得到 回收 。本文介 绍 了炼钢 转炉 煤气 回收 的工艺 流程 以及 系统详 细 的 自动 控制连 锁方 案, 括煤气 的 回收条件 、放 包 散 条件 、煤气 柜 的连 锁条 件等 , 有效 的避 免 了安全 事 故 的发 生, 最终 使 煤气 得 到充 分回 收 。 [ 关键 词] 煤气 回收 连锁 控制 烟气检 测
副枪在转炉自动化控制过程中常见问题及对策

Metallurgical Engineering 冶金工程, 2020, 7(3), 185-194Published Online September 2020 in Hans. /journal/menghttps:///10.12677/meng.2020.73026副枪在转炉自动化控制过程中常见问题及对策张孝兴1,程奎生21铭达科冶金科技(上海)有限公司,上海2达涅利霍高文钢铁技术(上海)有限公司,上海收稿日期:2020年8月28日;录用日期:2020年9月10日;发布日期:2020年9月17日摘要本文阐述了转炉副枪使用过程中影响转炉测温、测样、定碳、取样的主要因素,并逐一提出了对策,通过一系列措施改进,副枪使用成功率在现场稳步提高。
关键词副枪,探头,自动化Common Problems and Countermeasuresin the Operation of Sublancefor the Automatic Controlof ConverterXiaoxing Zhang1, Kuisheng Cheng21MDC Sublance Probe Technology (Shanghai) Co., Ltd., Shanghai2Danieli Hoogovens Steel Technology (Shanghai) Co., Ltd., ShanghaiReceived: Aug. 28th, 2020; accepted: Sep. 10th, 2020; published: Sep. 17th, 2020AbstractThis paper describes the main influence factors of converter temperature measurement, sample measurement, carbon determination and sampling with sublance and puts forward countermea-sures one by one. Through a series of improvements, the success rate of sublance is steadily in-creased on site.张孝兴,程奎生KeywordsSublance, Probe, AutomationCopyright © 2020 by author(s) and Hans Publishers Inc.This work is licensed under the Creative Commons Attribution International License (CC BY 4.0)./licenses/by/4.0/1. 引言近年来随着“中国制造2025”的不断深入,智能制造成为各炼钢企业追求的目标。
转炉炼钢主要过程及特点

脱氧及合金化
脱氧
吹炼终点钢水 [O]=0.02~0.08%, 向 钢 中 加 入一种(或几种)与氧亲和力 比 Fe 大 的 元 素 , 常 用 脱 氧 剂 Fe-Si 、 Fe-Mn 、 Al 、 Si-AlCa、Si-Al-Ba等;
合金化
向钢水中加入合金元素使其 达到成品钢成分要求
❖ 供料系统 ❖ 转炉系统 ❖ 供气系统 ❖ 净化系统 ❖ 辅助设备
炼钢原料
转炉炼钢的原材料分为金属料、非金属料和气 体。金属料包括铁水、废钢、铁合金,非金属料包 括造渣料、熔剂、冷却剂,气体包括氧气、氮气、 氩气、二氧化碳等。非金属料是在转炉炼钢过程 中 为了去除磷、硫等杂质,控制好过程温度而加入的 材料。主要有造渣料(石灰、白云石),熔剂(萤 石、氧化铁皮),冷却剂(铁矿石、石灰石、废 钢),增碳剂和燃料(焦炭、石墨籽、煤块、重 油)。
(3)基建投资和生产费用低 纯氧顶吹转炉的基 建投资相当于同样生产量的平炉车间的60~70%, 生产费用也低于平炉。
温度制度
随铁水中元素氧 化,金属液相线温度升 高,浇注也要求过热度, 升温是炼钢重要任务 之一.
出钢温度T的确定:
T= 浇 注 钢 种 液 相 线 温 度 + 浇 注过热度+钢水镇静及炉 外精炼温度降+出钢温度 降
出钢
出钢过程
先测定[C]、[P]、 [S]及T,判断是否满足 出钢要求,否则补吹;采 用挡渣技术与红包出 钢.
转炉设备
转炉冶炼的基本原理 ----物料平衡及热平衡
纯氧顶吹转炉炼钢优点
(1)生产速度快 因为用纯氧吹炼,会高速降碳, 快速提温,大大缩短冶炼时间。。
(2)品种多、质量好 纯氧顶吹转炉既能炼普通 钢,也能炼普通低碳钢。如首钢采用这种方法成功 地试炼了一百多种钢材。用纯氧吹炼,钢中氮、氢 等有害气体含量较低。
转炉炼钢安全规程
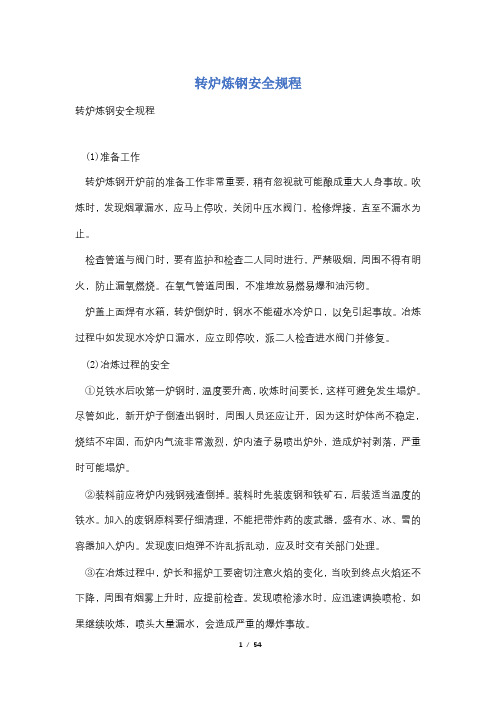
转炉炼钢安全规程转炉炼钢安全规程(1)准备工作转炉炼钢开炉前的准备工作非常重要,稍有忽视就可能酿成重大人身事故。
吹炼时,发现烟罩漏水,应马上停吹,关闭中压水阀门,检修焊接,直至不漏水为止。
检查管道与阀门时,要有监护和检查二人同时进行,严禁吸烟,周围不得有明火,防止漏氧燃烧。
在氧气管道周围,不准堆放易燃易爆和油污物。
炉盖上面焊有水箱,转炉倒炉时,钢水不能碰水冷炉口,以免引起事故。
冶炼过程中如发现水冷炉口漏水,应立即停吹,派二人检查进水阀门并修复。
(2)冶炼过程的安全①兑铁水后吹第一炉钢时,温度要升高,吹炼时间要长,这样可避免发生塌炉。
尽管如此,新开炉子倒渣出钢时,周围人员还应让开,因为这时炉体尚不稳定,烧结不牢固,而炉内气流非常激烈,炉内渣子易喷出炉外,造成炉衬剥落,严重时可能塌炉。
②装料前应将炉内残钢残渣倒掉。
装料时先装废钢和铁矿石,后装适当温度的铁水。
加入的废钢原料要仔细清理,不能把带炸药的废武器,盛有水、冰、雪的容器加入炉内。
发现废旧炮弹不许乱拆乱动,应及时交有关部门处理。
③在冶炼过程中,炉长和摇炉工要密切注意火焰的变化,当吹到终点火焰还不下降,周围有烟雾上升时,应提前检查。
发现喷枪渗水时,应迅速调换喷枪,如果继续吹炼,喷头大量漏水,会造成严重的爆炸事故。
④发生喷溅时,火星冲出氮(或蒸汽)封口,可将氧气皮管烧坏,造成设备事故,如果渣子不化而又采取高枪位的不正常操作,造成连续性的剧烈大喷溅,危害更大。
还有一种是动炉倒渣大喷溅,爆炸威力大,往往会炸坏摇炉房的仪器设备、灼伤人员。
出现这种大喷溅的原因是渣子氧化性过高、氧气截止阀失效,漏氧时间过长等,因而渣子表面氧量高,炉子倾动时,产生大量泡沫喷出炉口。
⑤发生跑钢事故时,首先应搞清跑钢部位,以便采取措施。
窜钢时应从速调整化学成分,快速出炉,以免发生设备和人身事故。
万一发生炉底窜钢时,应立即关闭进水阀门,在着火部位用四氯化碳灭火机灭火。
⑥氧气顶吹转炉炼钢,钢水温度高达1000℃以上,在这种温度下,水的体积将增大5000倍以上。
炼钢安全操作规程

炼钢安全技术操作规程一、一般安全要求1、工程中的隐蔽部分,应经设计单位、建设单位、监理单位和施工单位共同检查合格,方可进行隐蔽.施工完毕,施工单位应将竣工说明书及竣工图交付建设单位。
建设工程的安全设施竣工后,应经验收合格方可投入生产。
2、炼钢厂应建立健全安全管理制度,完善安全生产责任制。
厂长对本厂的安全生产负全面责任,各级主要负责人对本部门的安全生产负责.各级机构对其职能范围的安全生产负责.3、炼钢厂应依法设置安全生产管理机构配备专(兼)职安全生产管理人员,负责管理本厂的安全生产工作.4、炼钢厂应建立健全安全生产岗位责任制和岗位安全技术操作规程,严格执行值班制和交接班制。
5、炼钢厂应认真执行安全检查制度,对查出的问题应提出整改措施,并限期整改。
6、炼钢厂的厂长具备相应安全生产知识和管理能力。
7、炼钢厂应定期对职工进行安全生产和劳动保护教育,普及安全知识和安全法规,加强业务技术培训.职工经考核合格方可上岗。
新工人进厂,应首先接受厂、车间、班组三级安全教育,经考试合格后由熟练工人带领工作,直到熟悉本工程操作技术并经考核合格,方可独立工作。
调换工种和脱岗三个月以上重新上岗的人员,应事先进行岗位安全培训,并经考核合格方可上岗.外来参观或学习的人员,应接受必要的安全教育,并应由专人带领。
8、特种作业人员和要害岗位、重要设备与设施的作业人员,均应经过专门的安全教育和培训,并经考核合格、取得操作资格证,方可上岗。
上述人员的培训、考核、发证及复审,应按国家有关规定执行。
9、炼钢对厂房、机电设备要进行定期检查、维修和清扫。
要害岗位及电气、机械等设备应实行操作牌制度.10、安全装置和防护设施,不得擅自拆除。
11、炼钢厂应建立火灾、爆炸、触电和毒物逸散等重大事故的应急救授预案,并配备必须的器材与设施,定期演练.12、炼钢厂发生伤亡或其他重大事故时,厂长应立即到现场组织指挥抢救,并采取有效措施,防止事故扩大。
发生伤亡事故,应按国家有关规定报告和处理。
炼钢厂转炉工段操作规程
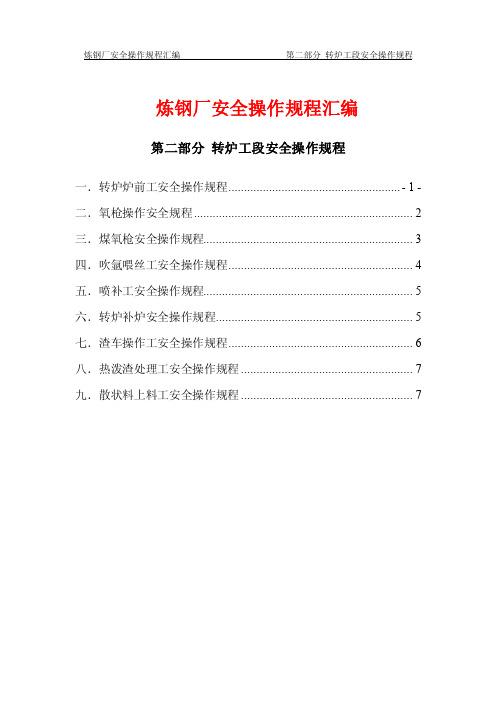
炼钢厂安全操作规程汇编第二部分转炉工段安全操作规程一.转炉炉前工安全操作规程....................................................... - 1 - 二.氧枪操作安全规程 . (2)三.煤氧枪安全操作规程 (3)四.吹氩喂丝工安全操作规程 (4)五.喷补工安全操作规程 (5)六.转炉补炉安全操作规程 (5)七.渣车操作工安全操作规程 (6)八.热泼渣处理工安全操作规程 (7)九.散状料上料工安全操作规程 (7)一.转炉炉前工安全操作规程1.开新炉前的安全准备工作1.1.必须严格按照开新炉方案检查调试,逐项检查、确认设备联锁等所有安全装置均符合工艺条件,调试后签字认可。
1.2.检查透气砖时,必须关氩气或氮气,通空气5分钟后,才能进入炉内作业。
1.3.开炉第一炉倒炉前,先将炉台周围人员及行车喊开后再倒炉,待转炉停稳后再测温取样。
2.复合吹炼时安全规程2.1.指行工指挥兑铁水、加废钢时,铁水包、废钢槽应正对炉口,手势清楚,哨音清晰、准确,站在安全位置指挥,并将周围人员叫开。
加废钢前检查炉内是否有液体渣,有则必须倒掉。
加完废钢后,必须确认槽内是否卡有废钢,否则应进行处理,兑铁前应关好操作室防火门,确认铁包离开炉口后方可动炉。
2.2.下枪吹炼时,必须关好炉前挡火门。
2.3.炼钢工和主摇炉工应随时检查氧枪是否有漏水的现象,发现问题应立即停吹起枪;关闭水和氧气并移枪;漏水时严禁摇炉,待确认炉内水蒸发完后方可缓慢倾动转炉,炉前四周严禁站人,炉前上方行车应叫开。
2.4.加入渣料、废钢必须干燥,严禁易燃易爆品、密闭容器进入转炉,若废钢潮湿,应先加废钢来回摇炉,待水蒸发完后再兑铁。
2.5.副摇炉工应确认渣罐干燥才能倒渣。
2.6.当水冷系统发生泄漏时,炼钢工和主摇炉工必须按程序执行提枪,处理好后才能冶炼。
2.7.炉前工使用的各种工具必须放在规定位置并实行交接班,保证平台畅通干净。
转炉炉气分析技术发展浅析

新 疆钢 铁
总 10 2 期
转 炉炉气分析 技术发展浅析
刘 玉宝 , 郭庆 华
( 新疆八钢南疆钢铁拜城有 限公 司 ) 摘 要: 转 炉炉气分析技术通过 分析转炉炉气成分 , 控制转炉 冶炼 进程 , 能够提高炼钢过程稳定性 和终点命
中率 , 是一种很有发展前途 的转炉 控制技术 。从 发展 历史 、 系统 组成 、 系统功能及存在 的问题 四个 方面对这一
1 前 言
转 炉炼 钢过 程 的复杂性 以及 客户 对钢 的质 量 要
一
段 时间里 发展 缓慢 。 进入 2 O世纪 9 O年代 , 于炉 基
气 分 析 的转 炉 动 态控 制 再 次 引 起 了人 们 的关 注 , 质 谱 仪取 代 红外 分析 仪 用于气 体 成分 分 析 ,响应 时 间 和 精度 都 大 幅度提 高 1 。 迄 今 为止 ,国外许 多 大钢 厂都 采用 了炉气 分 析
a heh t ae o nd nd t i t f r e -pon . it Theh soy, tucur , u t nsa hot g so e h lg r nto c d. itr sr t e f nci nd s ra e ft tc noo a ei r du e o he y Ke wor : c n c r pr c s o tol nd y ds o v  ̄e ; o e sc n r ;e -pon o to;of a n lss itc n r l f-g sa ay i
过程 无 消耗 件 , 不受 炉容 大 小 限制 , 为发展 最 快 且 成 的转 炉 控制 技 术之 一 l 1 ] 。
Pia60 扇 式 质谱 仪用 于 转 炉生 产 ,碳 温 命 中 r 0S磁 m
- 1、下载文档前请自行甄别文档内容的完整性,平台不提供额外的编辑、内容补充、找答案等附加服务。
- 2、"仅部分预览"的文档,不可在线预览部分如存在完整性等问题,可反馈申请退款(可完整预览的文档不适用该条件!)。
- 3、如文档侵犯您的权益,请联系客服反馈,我们会尽快为您处理(人工客服工作时间:9:00-18:30)。
转炉炼钢动态控制技术X全 红(昆明冶金高等专科学校冶金与矿业学院,云南 昆明 650033) 摘 要:介绍了国内外转炉炼钢中用于过程动态控制的副枪和炉气分析系统技术,并对国内大、中型转炉终点采用动态控制技术提出了建议。关键词:转炉;炼钢;动态控制中图分类号:TF711 文献标识码:A 文章编号:1006-0308(2006)03-0031-04
TechnologyofDynamicControllingonConverterSteelmakingQUANHong(MeterageandMetallurgyDepartmentofKunmingMetallurgyCollege,Kunming,Yunnan650033,China)
ABSTRACT:Thispaperintroducesthedomesticandforeigntechnologyofsub-lanceandoff-gasanalysisonconvertersteelmaking,the
suggestionaboutdynamiccontrollingtheprocessoflargeormiddleconvertersteelmakinginourcountryisproposed.KEYWORDS:converter;steelmaking;dynamiccontrol
1 转炉吹炼控制技术的发展及现状自1952年世界上第一座氧气转炉在奥地利Doawitz厂投产以来,由于其生产效率高、产品质量好,得到迅速发展。从20世纪50年代到70年代主要是完善技术和实现大型化,70年代从静态控制向动态控制发展,80年代以来,随着计算机技术的全面推广以及各种检测手段的迅速发展,国外先进钢铁厂逐步研究采用计算机对转炉吹炼进行控制,日本在80年代后开始采用全自动控制技术。国内除宝钢、武钢、首钢等少数转炉采用动态控制外,大多数转炉的装备、控制水平还较低,处于经验控制向自动控制的过渡。转炉吹炼控制技术的发展可分为三个阶段:静态控制、动态控制和转炉全自动吹炼控制。111 静态控制技术静态控制指转炉吹炼前,根据初始条件和终点要求,对转炉吹炼过程进行模型计算,制定出吹炼方案(提供供氧时间和各种辅原料加入量),以达到基本命中目标值,它可以对转炉吹炼过程的熔池温度和成分变化进行预报[1]。静态模型是转炉实现动态控制和全自动控制的基础,转炉要进行动态控制或全自动控制,必须首先建立静态模型。但是,由于静态模型不能根据吹炼情况采集炉内金属液成分和温度变化等炉内信息来调整吹炼参数,因此命中率较低。112 动态控制技术转炉所采用的动态控制技术主要有副枪动态控制和炉气分析动态控制以及副枪+炉气分析动态控制。11211 副枪动态控制技术副枪动态控制技术是在吹炼接近终点时(终点前2~3min),向熔池内插入副枪,检测熔池温度T和碳含量[C]及钢水氧活度,并取出金属样。根据检测数据,修正静态模型的计算结果,计算命中终点所需的供氧量(或供氧时间)和冷却剂加入
31
2006年6月第35卷第3期(总第198期) 云南冶金YUNNANMETALLURGY Jun.2006Vol.35.No.3(Sum198)
X收稿日期:2005-11-15;修回:2006-03-20作者简介:全 红(1963-),女,湖南长沙人,机械工程师。量,调整后2~3min的吹炼参数。副枪安装的组合探头不同,具备的检测功能也不同,终点命中率也不同[2]。1)宝钢炼钢厂。宝钢一炼钢、二炼钢转炉均采用计算机动态炼钢技术,主要依靠所装备的副枪检测吹炼过程中钢液的信息,通过动态控制模型对吹炼终点进行控制。宝钢的转炉动态代数模型是根据副枪快速测定的结晶碳及钢水温度,分别利用指数函数及线性函数来推定吹炼停止时的钢水碳含量和温度,它还具有动态学习功能,即利用吹炼停止时的钢水碳含量和温度信息对动态模型参数进行校正,以提高下一炉的精度。据了解,终点一次命中率为80%~85%(控制精度:[C]?01015%、T?13e),补吹率在10%以下。2)武钢三炼钢。武钢三炼钢是20世纪90年代新建的现代化炼钢厂,转炉静态模型包括四相模型:即中间目标温度计算模型、原料计算模型、熔剂计算模型和静态计算模型。这四个模型决定每炉钢吹炼前的设定值。转炉冶炼在副枪第一次测量(占总氧耗量的85%左右)后进入动态控制,计算出达到目标温度和目标碳所需的吹氧量及冷却剂量,以后每吹氧3s,启动一次动态计算,预测熔池内的碳含量和温度,当温度和碳含量都进入目标范围时,发出提枪停吹指令。从1997年下半年开始,通过对转炉静态模型参数和动态模型参数的优化调整,转炉终点命中率(控制精度:[C]?0101%、T?12e)由开始的4216%提高到2001年的平均9311%,其中2001年11月最高达到96196%。补吹率一般在5%以下,达到了国际先进水平[3]。3)济钢三炼钢。济钢2000年新建投产的120t复吹转炉采用了副枪和两级自动化控制系统,副枪技术由达涅利公司提供,实现炼钢过程的动态控制。所达到的转炉一次命中率见表1。采用副枪测量实现了转炉吹炼的动态控制,其优点在于:1)能完全消除转炉初始条件波动的影响和系统误差;2)基本消除吹炼过程中产生的随机误差;3)对终点进行近程预报,大幅度提高终点命中率。但转炉副枪工艺只能提供吹炼过程中瞬时的碳含量和温度,并不能提供连续的信息,严格来说,副枪仍然是一种静态控制手段,只不过距终点时间很短,实质上转炉生产的大部分时间仍是在静态模型的指导下进行的。另外,副枪所采用的结晶定碳技术对低碳钢的测量精度较高,而对高碳钢的测量误差却较大[4]、[5]、[6]。
表1 济钢三炼钢120t转炉终点命中率Tab.1 End-pointhittingrateofthe120tconverterinthethirdsteelmakingplantofJinanIron&SteelCompanyLtd.
[C]/%控制精度[C]、T同时命中率/%0102~0106[C]?01015%,T?12e880106~0115[C]?0102%,T?12e840115~0124[C]?0103%,T?12e78
11212 炉气分析动态控制技术
图1 炉气分析系统示意图Fig.1 Sketchofthefurnacegasanalysissystem
图2 CO、CO@、O2和N2的气体特征曲线Fig.2 CharacteristiccurveofCO,CO2,O2andN2
炉气分析动态控制技术是通过连续检测炉口逸出的炉气成分数据,推算熔池瞬时脱碳速度和Si、Mn、Fe、P的瞬时氧化量,并对熔池物料平衡和能量平衡进行计算,求出熔池瞬时的升温速度。它可依据前一时刻的检测值,预报下一时刻的成分和温度变化,同时,比较每一时刻的计算值与检测值的误差,不断对结果进行校正,从而提高控制精度和命中率(如图2-1、2-2所示)[7]、[8]。目前,国外如欧洲、日本、韩国等有基于炉气32
2006年6月第35卷第3期(总第198期) 云南冶金YUNNANMETALLURGY Jun.2006Vol.35.No.3(Sum198)分析动态控制的应用实例较多,国内应用较少。据了解,在国内的大型转炉中,目前只有本钢、马钢一炼钢已装备了炉气分析技术,攀钢新建转炉也将引进副枪+炉气分析动态控制技术。1)奥钢联(VAI)炉气分析动态控制技术。奥钢联的转炉炉气分析动态控制系统由两部分组成:¹负责转炉炉气采集、处理和分析的低维护量的LOMAS系统;º转炉二级动态控制模型DYNA-CON。可以分析温度高达1800e、烟尘含量高达100mg/m3的气体成分。LOMAS系统由两个气体采集探头、现场处理柜、气体处理柜、控制柜和分析柜组成。目前国内外钢厂使用的炉气分析技术多数是VAI提供的DYNACON动态控制模型和LOMAS系统。DYNACON的动态分析计算主要包括:¹一次加料计算;º二次加料计算;»转炉液面计算;¼过程动态控制计算(核心部分);½补吹校正计算;¾合金加料计算;¿反馈计算。在普通生产条件下,使用炉气分析动态控制技术,碳的命中率可达到80%。如果能使供氧、底吹搅拌、吹炼方式、加料方式等进一步优化,可使命中率达到95%。同时可提高产品质量,降低生产成本[9]、[10]。2)中国马钢。马钢引进奥钢联的转炉炉气分析动态控制系统已成功应用于一炼钢1座95t、2座120t的顶底复吹转炉上,是国内第一家引进该项技术的中、小型转炉企业。该系统的硬件和软件均从奥钢联引进(包括设计、安装),2004年3月开始投入运行。马钢一炼钢的CSP和圆坯连铸均配有LF炉,具有较强的温度调节功能,因而对转炉终点的钢水温度要求不严(高于1570e即可),再加上转炉冶炼的所有钢种均为低碳出钢,所以在炉气分析系统投入应用后,转炉冶炼CSP所浇钢种及圆坯连铸所浇钢种时,基本可做到不倒炉直接出钢,直接出钢率在80%以上,从而使转炉的冶炼周期由原来的40min缩短至目前的32min。马钢的炉气分析系统应用较成功,所获得的主要冶金效果:¹缩短冶炼时间8min,使影响全连铸节奏的限制性环节得到了解决;º缩短了高氧化性钢水在转炉内的停留时间,减少了炉衬的侵蚀,降低了耐材消耗;»深吹比例减少,钢水、钢渣的氧化性降低,脱氧剂及合金的用量减少。炉气分析动态控制技术的优点是:1)通过不断地动态校正,可实现连续预报,提高控制精度;2)除预报熔池温度和碳含量外,还可预报熔池的磷含量和炉渣成分的变化;3)适用于各种转炉,不受炉口尺寸的限制,且成本低于副枪。炉气分析动态控制技术的不足之处是:1)炉气分析只适用于低碳钢吹炼终点控制。对于普通钢种,采用炉气分析动态控制可以取代或部分取代副枪测试,降低生产成本,但对于特殊钢种或新开发的钢种,为了得到直接和精确的测量结果,通常应该采用副枪;2)炉气分析是通过连续检测转炉的炉气成分来推算冶炼终点,属于间接测量法,其测量精度受诸多因素的影响。比如:炉气分析设备的分析精度、对炉气流量的校正计算准确性、炉气分析系统的响应时间、模型本身的精度等对控制效果影响较大;3)采用质谱仪在控制吹炼温度方面尚没有取得大的突破[11]、[12]、[13]。113 副枪+炉气分析全自动吹炼控制技术炉气分析与副枪是检测转炉吹炼信息的两种手段,以达到优势互补,目前日本和德国的做法是在大型转炉上同时采用副枪和质谱仪检测,计算机采集数据在线计算,将结果指令连续下达给控制系统,实现完全自动控制,吹炼结束直接出钢。1)日本住友金属。住友公司鹿岛厂基于副枪检测+炉气成分分析,开发出具有参数自整定功能的终点控制系统。该系统包括动态控制模型和反馈计算模型,其中反馈模型基于副枪检测结果分析动态模型的误差趋势,并根据相应的规划确定反馈量,从而达到调整动态模型误差的目的。另外,为了避免不正常操作的影响,相应开发出一个专家系统,根据经验调整静态模型。2)日本神户制钢。日本神户钢铁公司加古川钢厂采用全自动吹炼控制240tLD/OTB转炉,取得很好效果。其控制技术的主要特点是:¹根据初始条件和终点目标,用静态模型制定吹炼方案;º采用氧枪加速度仪测量吹炼过程中的炉渣液位,判断化渣情况,动态调整枪位和氧流量,控制吹氧和造渣过程,避免喷溅;»连续检测吹炼过程中的炉气成分,全程在线预报熔池C、Si、Mn、P、S含量和熔池温度;¼接近吹炼终点时,用副枪测温,进行动态校正,确定吹炼终点。采用全自动吹炼技术后,能得到理想的控制效果:¹减少喷溅,冶炼高碳钢喷溅率从40%下降到8%;º减少补吹次数,冶炼高碳钢补吹率从114次/炉下降到111次/炉;»冶炼高碳钢缩短冶33