[优质文档]高精度轧制实际及技巧
轧制总结范文

轧制总结引言轧制是金属材料加工中常用的一种工艺,通过连续压下金属坯料,使其发生塑性变形,以获得所需的形状和尺寸。
本文将对轧制工艺进行总结和分析,并探讨其应用领域和发展趋势。
轧制工艺概述轧制是利用轧机将金属坯料进行塑性变形的过程。
在轧机中,金属坯料被一对或多对辊轮挤压,使其发生塑性变形,最终得到所需要的形状和尺寸。
轧制工艺通常可以分为热轧和冷轧两种方式。
热轧是指在高温下进行的轧制工艺,通常用于钢材等金属材料的加工。
冷轧则是在室温下进行的轧制工艺,常用于铝、铜等金属材料的加工。
轧制工艺的优点轧制工艺具有许多优点,使其成为金属材料加工中常用的一种工艺。
1.高效性:轧制工艺可以实现连续生产,大大提高了生产效率。
2.精度高:轧制工艺可以控制金属材料的形状和尺寸,使得成品精度高。
3.降低生产成本:相比于其他加工工艺,轧制可以大幅降低生产成本,提高经济效益。
4.改善材料性能:轧制可以对金属材料进行塑性变形,优化其晶粒结构,提高材料的强度和硬度。
轧制工艺的应用领域轧制工艺广泛应用于金属材料的加工领域,包括但不限于以下几个方面:1.钢铁行业:轧制在钢铁行业中是一种常见的加工工艺,用于生产钢材。
2.铝合金加工:轧制可以对铝合金材料进行加工,以获得所需的形状和尺寸。
3.有色金属加工:轧制也被广泛应用于铜、铅、锌等有色金属的加工过程中。
4.汽车制造:轧制在汽车制造中起到重要作用,用于加工汽车零部件。
轧制工艺的发展趋势随着科技的不断进步和需求的不断增长,轧制工艺也在不断发展和改进。
以下是轧制工艺的一些发展趋势:1.数字化:随着计算机技术的发展,轧制工艺正向数字化方向迈进,实现智能化生产和控制。
2.绿色环保:轧制工艺的绿色环保要求也越来越高,发展低能耗、低排放的工艺和设备。
3.超微细加工:轧制工艺正向超微细加工方向发展,以适应微电子、光电子等领域对材料精度的要求。
4.多功能化:轧制工艺正越来越多地融入其他技术,实现多种功能的一体化加工,提高加工效率。
提高热连轧厚度精度的最优控制方法探讨

车辆工程技术213机械电子提高热连轧厚度精度的最优控制方法探讨王 瑞(安钢集团国际贸易有限责任公司贸易部,河南 安阳 455004)摘 要:众所周知,热连轧轧机轧制宽幅越大,意味着轧制难度越大。
如何提高热连轧轧制厚度与精度,提供整套热连轧电气和自动化,并通过人机界面管理工艺控制模型、过程控制、电机及配套传动、制造执行系统等非常重要。
关键词:热连轧轧机;厚度;精度;控制1 热连轧轧制厚度精度工艺流程及效率提高方法 第一,热连轧轧制厚度在生产的过程中对精度十分看重,加工工艺方面不仅要求点多面广,同时对区域分散和工艺复杂程度也有非常高的要求,因此需要各类型的钢铁企业进行整合,按照流程逐步进行,在进行轧钢线后部工序整合工作的时候,材料可能会被做成精品或者是成品等,这些都可以采用扁平式的管理方式。
第二,热连轧轧制厚度精度在进行处理的时候,每一个工艺流程在制作精品的过程中,尽量的精简了加工的流程,按照要求完成交接程序,按照设备操作的要求,进行优化生产工作,使工作能够更加顺利的开展下去,信息的反馈速度更快质量更高,使产品的生产效率得到明显的提升。
第三,采用热连轧轧制厚度精度加工工艺流程的产线,需要经历四个不同的流程,这四个流程分别是1.精饰、2.探伤、3.银亮、4.退火,经过整合之后的产线完成了精饰加工阶段,后续的工序工作流程能够变得更加明朗、生产加工经营过程中的责任也能得到进一步明确,产品的制作效率得到显著提升。
第四,伴随着我国钢铁市场的发展态势开始走下坡路,很多钢材客户对于钢材的质量要求也越来越严格,为了满足客户们的更多要求,有关的钢铁企业按照企业客户提出的标准进行技术改进,并聘请具有相关资质的质量工程师进行生产产品质量的检查,并将检查结果汇总成检查报告进行反馈,保证生产出来的产品质量过硬,产品质量得到明显提升。
第五,根据热连轧轧制厚度精度要求的不同,不同钢材表面的硬化组织也有区别,因此产品的质量可能会受到一定程度的影响。
粗轧阶段的轧制方法

粗轧阶段的轧制方法粗轧是金属加工中的一个重要工序,用于将金属坯料经过轧制设备的多道次轧制,将其变形成为所需的中间截面形状和尺寸,为下一道加工工序提供必要的条件。
下面将详细介绍粗轧阶段的轧制方法。
1.粗轧设备粗轧阶段主要采用的轧制设备有酸洗轧机、立式轧机、斜轧机和辊床等。
其中,酸洗轧机常用于去除坯料表面的氧化皮和锈蚀,提高轧制效果和质量。
立式轧机可用于实现多通道轧制,将坯料逐步压延至所需尺寸。
斜轧机主要用于轧制较大尺寸的坯料,具有轻巧灵活的特点。
辊床是一种水平加工设备,可以对坯料进行横轧,具有较大的轧制强度。
2.轧制方法(1)单道轧制法:即将完整坯料一次性通过一套轧制辊,使坯料厚度得到一次减小。
这种方法的优点是轧制过程简单快捷,适用于一些要求较低的加工工序。
缺点是轧制力较大,轧制效果较差,易产生轧制缺陷,一般用于轧制坯料中较低的轧制强度。
(2)多道次轧制法:即将坯料通过多套不同粗糙度的轧制辊,逐个轧制,使坯料逐步减小厚度和增加宽度。
这种方法的优点是轧制力分散,轧制效果好,能够轧制出高精度的金属材料。
缺点是轧制过程时间较长,设备复杂,成本较高。
适用于对轧制质量要求较高的工件。
(3)反复轧制法:即在多次轧制中,将坯料的轧制方向依次改变,增加坯料内部的位错,使坯料的晶粒得到更细小的变形。
这种方法的优点是能够显著提高金属的塑性和韧性,减少金属材料的断裂和表面缺陷。
缺点是轧制过程复杂,轧制力较大,适用于轧制要求高强度和塑性的金属材料。
(4)硬轧法:即在轧制过程中,通过调整轧制温度、轧制速度以及轧制辊的间距,使坯料在轧制过程中发生较大的变形,改变金属材料的原子结构和晶格排列,提高金属材料的机械性能和强度。
这种方法适用于轧制高强度和高硬度的金属材料。
3.操作要点(1)轧制温度:粗轧一般在金属材料的再结晶温度以下进行。
再结晶温度是金属在轧制过程中的一种热敏性温度,轧制温度低于再结晶温度能够使金属材料保持塑性和变形能力。
承钢无孔型轧制的工艺实践

承钢无孔型轧制的工艺实践承钢无孔型轧制是一种指针钢的轧制方法,具有高速度和高效率的特点。
该方法以无缝钢管为原材料,采用连续轧制和多点轧制的方式,用较小的力来实现更高的变形率。
工艺实践过程如下:1.原材料准备。
首先,选择与要生产的产品相匹配的钢板。
在选择钢板时,应考虑其化学成分、热处理和检测的特性。
然后,将钢板送往切割机或切割线,切割成适当大小的块。
2.炉前处理。
为了保证材料质量,需要对块状原材料进行炉前处理。
炉前处理步骤包括碳化、卸料、预热、预切、表面清洁、钎焊和热处理等。
3.轧制准备。
在轧制准备过程中,需要对轧辊进行清洗、安装和调整。
然后,安装并连接电气和水液系统。
4.连续轧制。
连接好设备后,开始进行连续轧制。
生产过程中,需要监测轧制力、变形率和温度等参数,以确保轧制质量。
一般情况下,连续轧制的变形率达到20%~30%,轧制速度在15~20m/s左右。
5.多点轧制。
完成一段连续轧制后,需要进行多点轧制。
多点轧制是指在轧制过程中,用多个轧辊同时对原材料进行加工。
这样可以使轧制过程更加平稳、更加高效。
在多点轧制中,轧制力、变形率和温度等参数都需要定期监测。
6.测量和切割。
完成轧制后,需要将轧制好的产品进行测量和切割。
在这个过程中,需要采用适当的设备和技术,以确保产品尺寸和质量的一致性。
7.熟化和包装。
最后,需要将生产好的产品进行熟化和包装。
钢板应该经过一个特殊的熟化期,以确保其质量。
然后,将钢板包装好,存储在恰当的温度和湿度条件下。
上述是承钢无孔型轧制的工艺实践过程,通过以上步骤能够生产出高质量的无孔型指针钢。
钢材的轧制操作
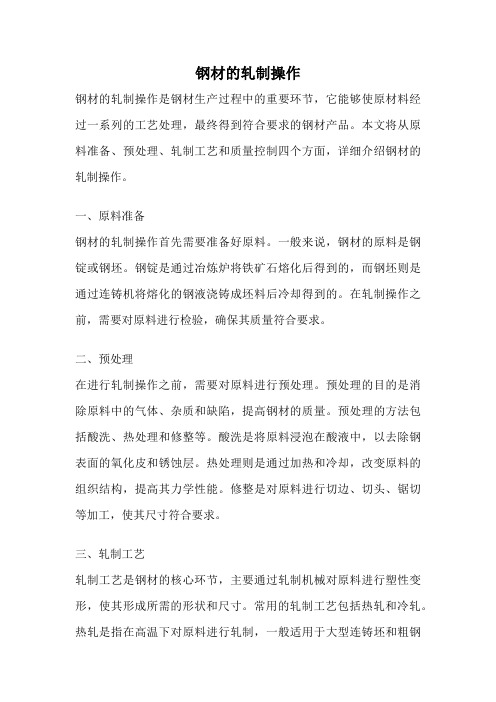
钢材的轧制操作钢材的轧制操作是钢材生产过程中的重要环节,它能够使原材料经过一系列的工艺处理,最终得到符合要求的钢材产品。
本文将从原料准备、预处理、轧制工艺和质量控制四个方面,详细介绍钢材的轧制操作。
一、原料准备钢材的轧制操作首先需要准备好原料。
一般来说,钢材的原料是钢锭或钢坯。
钢锭是通过冶炼炉将铁矿石熔化后得到的,而钢坯则是通过连铸机将熔化的钢液浇铸成坯料后冷却得到的。
在轧制操作之前,需要对原料进行检验,确保其质量符合要求。
二、预处理在进行轧制操作之前,需要对原料进行预处理。
预处理的目的是消除原料中的气体、杂质和缺陷,提高钢材的质量。
预处理的方法包括酸洗、热处理和修整等。
酸洗是将原料浸泡在酸液中,以去除钢表面的氧化皮和锈蚀层。
热处理则是通过加热和冷却,改变原料的组织结构,提高其力学性能。
修整是对原料进行切边、切头、锯切等加工,使其尺寸符合要求。
三、轧制工艺轧制工艺是钢材的核心环节,主要通过轧制机械对原料进行塑性变形,使其形成所需的形状和尺寸。
常用的轧制工艺包括热轧和冷轧。
热轧是指在高温下对原料进行轧制,一般适用于大型连铸坯和粗钢坯的加工。
冷轧是指在常温下对原料进行轧制,适用于薄板、线材和型材等细长产品的加工。
轧制工艺中需要控制轧制力、轧制温度和轧制速度等参数,以确保钢材的质量。
四、质量控制钢材的质量控制是轧制操作中至关重要的一环。
在轧制过程中,需要对钢材的尺寸、形状、表面质量和力学性能进行检测和控制。
常用的质量控制方法包括在线检测和离线检测。
在线检测是指在轧制过程中对钢材进行实时监测,通过传感器和控制系统对轧制参数进行调整,以保证产品质量。
离线检测是指在轧制后对钢材进行取样和试验,通过实验室分析和测试,评估钢材的质量。
总结起来,钢材的轧制操作是一个复杂的过程,需要经过原料准备、预处理、轧制工艺和质量控制等多个环节。
只有严格按照规程操作,并进行有效的质量控制,才能确保钢材的质量达到要求。
钢材的轧制操作不仅关系到钢材生产企业的经济效益,也直接影响到钢材产品的使用性能和安全性。
棒材直接轧制

棒材直接轧制1. 引言棒材直接轧制是一种常见的金属加工方法,用于将金属坯料通过轧制工艺加工成具有特定形状和尺寸的棒材产品。
这种加工方法广泛应用于钢铁、铝合金、铜合金等金属材料的生产中,具有高效、经济、灵活等优点。
本文将对棒材直接轧制的工艺流程、设备和应用领域进行详细介绍。
2. 工艺流程棒材直接轧制的工艺流程通常包括原料准备、预轧制、精轧制、冷却和整形等步骤。
2.1 原料准备原料准备是棒材直接轧制的第一步,主要包括选择合适的金属材料、切割成适当的坯料尺寸和加热处理等操作。
金属材料的选择应根据产品的要求和生产成本进行综合考虑,常见的金属材料有碳钢、不锈钢、铝合金等。
切割成适当尺寸的坯料可以提高轧制效率和产品质量。
加热处理可以改善金属的塑性和可加工性。
2.2 预轧制预轧制是棒材直接轧制的第二步,主要目的是通过辊道的压力和摩擦力将坯料逐渐塑性变形成较小的截面尺寸。
预轧制可以提高轧制效率、减少轧制力和改善产品表面质量。
预轧制通常采用多道次的轧制,每道次的辊道间隙逐渐减小,使坯料逐渐变形。
2.3 精轧制精轧制是棒材直接轧制的第三步,主要目的是进一步减小截面尺寸、提高产品的表面质量和机械性能。
精轧制通常采用单道次的轧制,辊道间隙较小,轧制力较大。
精轧制过程中需要控制轧制温度、轧制速度和轧制力等参数,以保证产品的质量和尺寸精度。
2.4 冷却和整形冷却和整形是棒材直接轧制的最后一步,主要目的是通过冷却和整形工艺使产品获得所需的形状和尺寸。
冷却可以改善产品的力学性能和表面质量,通常采用水冷或空冷方式。
整形包括切割、修直、打标等操作,以满足产品的需求。
3. 设备棒材直接轧制需要使用一系列专用设备,包括轧机、辊道、传动系统、冷却系统和控制系统等。
3.1 轧机轧机是棒材直接轧制的核心设备,用于通过辊道的压力和摩擦力将金属坯料塑性变形成棒材产品。
轧机通常由上辊和下辊组成,辊道间隙可以调节,以适应不同的轧制需求。
轧机的类型和规格根据产品的要求和生产能力确定。
热轧流向硅钢高精度钢同板差控制技术

热轧流向硅钢高精度钢同板差控制技术咱今儿个就来说说这热轧流向硅钢高精度钢同板差控制技术。
嘿,你可别小瞧了这玩意儿,它就像是一个神奇的魔法,能让钢材变得更加出色呢!想象一下,一块钢材,如果同板差控制不好,那会是啥样?就好比一件衣服,这儿皱一块,那儿鼓一块,多难看呀!而且还会影响它的性能和使用呢。
所以呀,这个同板差控制技术可太重要啦!那要怎么实现高精度的控制呢?这可得好好琢磨琢磨。
就好像厨师做菜,得掌握好火候、调料的搭配一样,我们控制同板差也得有一系列的妙招。
首先呢,得从原材料抓起。
就像盖房子得有好的砖头一样,钢材的原材料得质量过硬。
要仔细挑选,不能有丝毫马虎。
然后在热轧的过程中,就像是一场激烈的战斗,温度啦、压力啦、速度啦,都得把握得恰到好处。
温度高了不行,低了也不行,这就像是烤面包,火候得刚刚好,面包才能香喷喷的。
还有啊,设备也得给力呀!要是设备不给力,就像战士上战场拿了把坏枪,那怎么能打胜仗呢?所以设备得经常维护、保养,让它时刻保持最佳状态。
在实际操作中,工人们就像是一群技艺高超的艺术家,精心雕琢着每一块钢材。
他们凭借着丰富的经验和精湛的技术,一点点地调整参数,一点点地改善工艺。
这可不是一朝一夕能练成的功夫,得经过长时间的积累和磨练呢!你说,要是没有这个控制技术,那我们的硅钢能有那么好的质量吗?那肯定不行呀!这就好比没有了方向盘的汽车,还不得乱跑呀!所以呀,这个技术可真是我们钢材行业的宝贝呢!咱再想想,要是同板差控制不好,那造出来的东西能用吗?比如说汽车的零部件,要是同板差大了,那装起来能合适吗?肯定不行呀,说不定还会出大问题呢!所以呀,这个控制技术真的是关乎到很多方面呢。
总之呢,热轧流向硅钢高精度钢同板差控制技术是一项非常重要、非常神奇的技术。
它让我们的钢材变得更加完美,为我们的生活和工业生产提供了坚实的保障。
让我们一起为这项技术点赞,也为那些默默付出的工人们点赞!他们就像是幕后的英雄,虽然不被大家所熟知,但却为我们的生活做出了巨大的贡献!难道不是吗?。
高线精轧机知识

高线精轧机知识一、高线精轧机概述高线精轧机是一种用于轧制金属线材的设备,广泛应用于钢铁、有色金属等行业。
其主要作用是通过连续轧制和塑性变形,将粗线材逐步压制成细线材,并达到一定的尺寸精度和表面质量要求。
高线精轧机通常由多个轧机组成,每个轧机都具有一对辊子,通过转动辊子来完成轧制过程。
二、高线精轧机的工作原理高线精轧机的工作原理是通过辊子的转动和线材的通过,使得线材在辊子之间受到挤压和塑性变形,从而达到减小线材直径和提高线材表面质量的目的。
整个过程中,线材在不同轧机之间经过多次轧制,逐渐减小直径,直至达到目标尺寸。
三、高线精轧机的主要部件1. 轧机辊子:是高线精轧机的核心部件,承担着线材的挤压和塑性变形任务。
辊子通常由优质的合金钢制成,具有高强度和耐磨性能。
辊子的表面经过精细抛光和硬化处理,以确保线材的表面质量。
2. 传动系统:用于驱动辊子的转动。
传动系统通常采用电机和减速器的组合,通过齿轮传动或皮带传动将动力传递给辊子。
3. 卷取系统:用于将轧制好的线材卷取起来。
卷取系统通常由卷取机构和张力控制系统组成,能够保证线材卷取的紧密度和稳定性。
4. 控制系统:用于对高线精轧机进行全面的控制和监测。
控制系统通常包括电气控制系统和液压控制系统,能够实现轧机的启停、速度调节、张力控制等功能,并对轧制过程进行实时监测和数据记录。
四、高线精轧机的应用领域高线精轧机广泛应用于钢铁、有色金属等行业。
在钢铁行业中,高线精轧机主要用于生产各种钢丝、钢绞线、钢绞线等产品。
在有色金属行业中,高线精轧机主要用于生产铝线、铜线等产品。
这些产品在建筑、交通、电力、通信等领域中都有广泛的应用。
五、高线精轧机的优势和发展趋势1. 高线精轧机能够实现线材直径的精确控制,提供高精度的线材产品,满足不同行业的需求。
2. 高线精轧机具有高效率和高自动化程度,能够实现连续生产和自动化控制,提高生产效率和产品质量。
3. 高线精轧机具有较小的占地面积和能耗,能够节约生产成本,提高经济效益。