渗碳 渗氮、氮碳共渗标准
渗碳处理国标
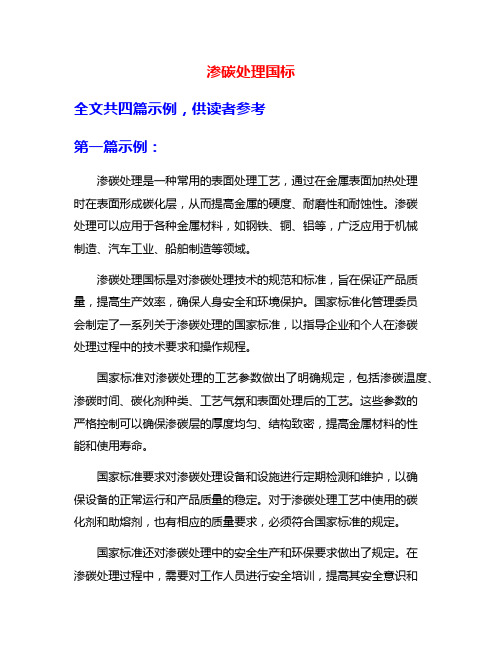
渗碳处理国标全文共四篇示例,供读者参考第一篇示例:渗碳处理是一种常用的表面处理工艺,通过在金属表面加热处理时在表面形成碳化层,从而提高金属的硬度、耐磨性和耐蚀性。
渗碳处理可以应用于各种金属材料,如钢铁、铜、铝等,广泛应用于机械制造、汽车工业、船舶制造等领域。
渗碳处理国标是对渗碳处理技术的规范和标准,旨在保证产品质量,提高生产效率,确保人身安全和环境保护。
国家标准化管理委员会制定了一系列关于渗碳处理的国家标准,以指导企业和个人在渗碳处理过程中的技术要求和操作规程。
国家标准对渗碳处理的工艺参数做出了明确规定,包括渗碳温度、渗碳时间、碳化剂种类、工艺气氛和表面处理后的工艺。
这些参数的严格控制可以确保渗碳层的厚度均匀、结构致密,提高金属材料的性能和使用寿命。
国家标准要求对渗碳处理设备和设施进行定期检测和维护,以确保设备的正常运行和产品质量的稳定。
对于渗碳处理工艺中使用的碳化剂和助熔剂,也有相应的质量要求,必须符合国家标准的规定。
国家标准还对渗碳处理中的安全生产和环保要求做出了规定。
在渗碳处理过程中,需要对工作人员进行安全培训,提高其安全意识和操作技能,减少事故发生的可能性。
对渗碳处理过程中产生的废气、废水和废渣要进行有效处理,确保不对环境造成污染。
渗碳处理国标的制定和执行,可以提高渗碳处理技术的规范化和标准化水平,促进行业的健康发展,保障产品质量和人身安全,实现节能减排和可持续发展。
企业和个人在进行渗碳处理过程中,应严格遵守国家标准的要求,确保生产操作的合法性和规范性,为行业的发展做出积极贡献。
【2000字】第二篇示例:渗碳处理是一种提高金属表面硬度和耐磨性的热处理工艺,主要应用于各种金属制品的表面加工。
为了规范和统一渗碳处理的技术要求及工艺流程,中国自主制定了《渗碳处理国家标准》(GB/T 18932-2003),以下将对该标准进行详细介绍。
渗碳处理国家标准的适用范围包括了碳化处理、渗氮处理和碳氮共渗处理三种方法的金属工件。
碳氮共渗深度和硬度

碳氮共渗深度和硬度
碳氮共渗的深度和硬度取决于多个因素,包括温度、时间、合金成分等。
以下是一些常见的碳氮共渗深度和硬度标准:
1.在常规条件下,碳氮共渗的深度约为0.5至
2.5毫米,硬度范围为500至700
HV。
2.如果采用较高的温度和较长的处理时间,碳氮共渗的深度和硬度范围可能会更高。
例如,在580℃至620℃的温度下处理2至6小时,硬度范围可达到800至1000
HV,深度约为1至3毫米。
3.合金成分也会对碳氮共渗的深度和硬度产生影响。
通常,较高含量的氮含量可以提
高硬度和深度,而较高含量的碳含量可以提高硬度和降低深度。
需要注意的是,这些标准仅供参考,实际碳氮共渗的深度和硬度会因具体条件而有所不同。
如果您需要具体的碳氮共渗深度和硬度标准,建议咨询相关的材料科学家或工程师。
渗氮 渗碳 碳氮共渗

渗氮渗碳碳氮共渗碳氮共渗是一种常见的表面处理技术,通过渗碳和渗氮来改善材料的硬度和耐磨性。
本文将对渗氮、渗碳和碳氮共渗的原理、应用和工艺进行详细介绍。
一、渗氮渗氮是将氮原子渗入材料表面形成氮化物层的过程。
氮原子通过高温处理和氮气氛的作用,渗透到材料表面并与材料中的元素反应,形成硬质氮化物层。
这一薄层氮化物层不仅能提高材料的硬度和抗磨损性能,还能改善材料的耐腐蚀性。
渗氮的主要应用领域包括机械制造、汽车工业、航空航天等。
在机械制造中,渗氮可以增加零件的硬度和耐磨性,延长使用寿命;在汽车工业中,渗氮可以提高引擎零件的耐磨性和抗腐蚀性能;在航空航天领域,渗氮可以增强航空发动机部件的耐高温和耐磨性能。
渗氮的工艺流程一般包括清洗件表面、装配件和炉内预处理、渗氮和回火处理等步骤。
渗氮一般采用封闭式和开放式两种方式进行,根据具体应用需求可以选择合适的渗氮工艺。
二、渗碳渗碳是将碳原子渗入材料表面形成碳化物层的过程。
碳原子通过高温处理和含有碳气体的氛围,渗透到材料表面并在表面与材料中的元素反应,形成硬质碳化物层。
渗碳技术不仅能提升材料的硬度和耐磨性,还可以改善材料的断裂韧性和抗腐蚀性。
渗碳广泛应用于机械零件、钢铁制品等领域。
渗碳后的材料表面硬度高、耐磨性好,适用于制作耐磨零件,如轴承、齿轮等;同时碳化层的外表面与空气隔绝,降低了材料的腐蚀速率,提高了零件的使用寿命。
渗碳的工艺流程包括预处理、渗碳、淬火和回火等。
渗碳一般采用气体渗碳和液体渗碳两种方式进行,具体工艺参数可以根据材料的要求进行选择。
三、碳氮共渗碳氮共渗是将碳原子和氮原子同时渗入材料表面形成碳氮共渗层的过程。
碳氮共渗通过碳氮共渗剂和高温处理,使碳原子和氮原子分别与材料中的元素发生反应,形成硬质碳氮化物层。
碳氮共渗能够同时获得渗碳和渗氮的特性,提高材料的硬度、耐磨性和抗腐蚀性。
碳氮共渗广泛应用于汽车工业、航空航天等领域。
在汽车工业中,碳氮共渗可以提高零部件的硬度和耐磨性,同时还可以提高零部件的抗磨损能力和抗腐蚀性;在航空航天领域,碳氮共渗可以增强发动机部件的抗高温性能和抗腐蚀能力。
金属热处理中渗氮工艺常识

金属热处理中渗氮工艺常识金属热处理中的各种渗氮工艺使氮原子渗入钢铁工件表层内的化学热处理工艺;传统的气体渗氮是把工件放入密封容器中﹐通以流动的氨气并加热﹐保温较长时间后﹐氨气热分解產生活性氮原子﹐不断吸附到工件表面﹐并扩散渗入工件表层内﹐从而改变表层的化学成分和组织﹐获得优良的表面性能。
如果在渗氮过程中同时渗入碳以促进氮的扩散﹐则称为氮碳共渗。
钢铁渗氮的研究始於20世纪初﹐20年代以后获得工业应用。
最初的气体渗氮﹐仅限於含铬﹑铝的钢﹐后来才扩大到其他钢种。
从70年{BANNED}始﹐渗氮从理论到工艺都得到迅速发展并日趋完善﹐适用的材料和工件也日益扩大﹐成为重要的化学热处理工艺之一。
渗入钢中的氮一方面由表及裡与铁形成不同含氮量的氮化铁﹐一方面与钢中的合金元素结合形成各种合金氮化物﹐特别是氮化铝﹑氮化铬。
这些氮化物具有很高的硬度﹑热稳定性和很高的弥散度﹐因而可使渗氮后的钢件得到高的表面硬度﹑耐磨性﹑疲劳强度﹑抗咬合性﹑抗大气和过热蒸汽腐蚀能力﹑抗回火软化能力﹐并降低缺口敏感性。
与渗碳工艺相比﹐渗氮温度比较低﹐因而畸变小﹐但由於心部硬度较低﹐渗层也较浅﹐一般只能满足承受轻﹑中等载荷的耐磨﹑耐疲劳要求﹐或有一定耐热﹑耐腐蚀要求的机器零件﹐以及各种切削刀具﹑冷作和热作模具等。
渗氮有多种方法﹐常用的是气体渗氮和离子渗氮。
气体渗氮:一般以提高金属的耐磨性为主要目的﹐因此需要获得高的表面硬度。
它适用於38CrMnAc等渗氮钢。
渗氮后工件表面硬度可达HV850~1200。
渗氮温度低﹐工件畸变小﹐可用於精度要求高﹑又有耐磨要求的零件﹐如鏜床鏜杆和主轴﹑磨床主轴﹑气缸套筒等。
但由於渗氮层较薄﹐不适於承受重载的耐磨零件。
气体参氮可採用一般渗氮法(即等温渗氮)或多段(二段﹑三段)渗氮法。
前者是在整个渗氮过程中渗氮温度和氨气分解率保持不变。
温度一般在480~520℃之间﹐氨气分解率为15~30%﹐保温时间近80小时。
这种工艺适用於渗层浅﹑畸变要求严﹑硬度要求高的零件﹐但处理时间过长。
零件热处理技术要求的提出及标注

零件热处理技术要求的正确提出及正确标注零件设计在确定了材料后,还要正确提出热处理技术要求,并在图样上正确地标注出来。
热处理技术要求,是指热处理质量的检验指标,除硬度和其它力学性能指标外,还有对组织、变形量以及局部热处理要求,对表面硬化零件有硬化层深度和渗层组织及脆性要求等等。
热处理技术要求的正确提出和正确标注,是一个合格热处理工作者的基本素质,也是在设计会审环节发表专业意见的基本依据。
1热处理技术要求的确定1.1硬度和其它力学性能的要求由于硬度试验简便快捷,又不破坏零件,而且硬度与强度等其它力学性能有一定对应关系,可以间接反映其他力学性能,因此,硬度成为热处理质量检验最重要的指标,不少零件还是唯一的技术要求。
对于重要受力件,除有硬度要求外,还有强度极限、屈服强度或断裂韧度等要求。
在较高温度下工作的重要受力件,还有持久强度和蠕变极限等要求。
在有腐蚀介质条件下工作的重要受力件,还有应力腐蚀、临界应力强度因子等要求。
在确定硬度以及力学性能指标时,要注意强度与韧性的合理配合,避免忽视韧性或过分追求韧性指标的偏向;注意组合件强度或硬度的合理匹配,提高零部件使用寿命。
例如,轴承滚珠一般要比套圈硬度高2-3HRC,汽车后桥主动齿轮的表面硬度一般要比被动齿轮高2-5HRC;处理好表面硬化零件(如渗碳淬火、渗氮、表面淬火等)的硬化层深度与表面、心部硬度的关系,使心部与表面达到最优匹配,适合零件的工作条件;由于材料强度、结构强度和系统强度三者不完全一致,所以设计中要处理好这三者的关系,对于某些重要零件,应根据模拟试验确定所需要的力学性能指标。
1.2表面硬化层深度选择需要表面硬化的零件,硬化层深度多少合适?这个指标的选择要考虑零件的工作条件、对性能的要求、失效形式和表面硬化工艺的特点。
首先要知道不同表面硬化工艺都有什么样工艺的效果?设备造价、变形开裂倾向、实用范围等有设么不同?下面分述以供参考:1.2.1 【渗碳淬火】表层状态是:层深0.2-2.0mm,表层硬化、压应力高,硬化层组织为马氏体+碳化物+残奥,层深均匀;性能特点是:硬度650~850HV(56~64HRC),耐磨性高,接触、弯曲疲劳强度高,抗咬合性好;变形开裂倾向性是:变形较大,不易开裂;设备造价:中等;适用范例:低碳钢、低碳合金钢等齿轮、轴、活塞销。
最全的渗碳和渗氮区别整理表格
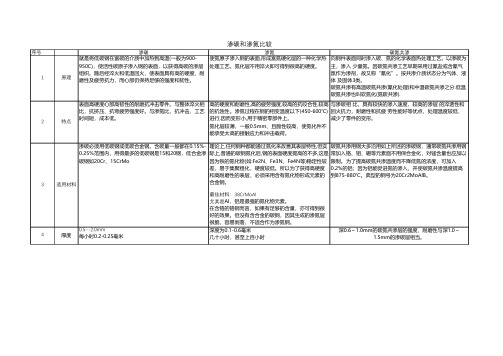
序号渗碳和渗氮比较12特点表面高硬度心部高韧性的耐磨抗冲击零件。
与整体淬火相比,抗挤压、抗弯疲劳强度好。
与渗氮比,抗冲击,工艺时间短,成本低。
高的硬度和耐磨性,高的疲劳强度,较高的抗咬合性,较高的抗蚀性。
渗氮过程在钢的相变温度以下(450-600℃)进行,因而变形小,用于精密零部件上。
氮化层较薄,一般0.5mm、且脆性较高,使氮化件不能承受太高的接触应力和冲击载荷。
渗碳渗氮就是将低碳钢在富碳的介质中加热到高温(一般为900-950C),使活性碳原子渗入钢的表面,以获得高碳的渗层组织。
随后经淬火和低温回火,使表面具有高的硬度、耐磨性及疲劳抗力,而心部仍保持足够的强度和韧性。
使氮原子渗入钢的表面,形成富氮硬化层的一种化学热处理工艺。
氮化层不用淬火即可得到很高的硬度。
原理碳氮共渗向钢件表面同时渗入碳、氮的化学表面热处理工艺。
以渗碳为主,渗入 少量氮。
因碳氮共渗工艺早期采用过氰盐或含氰气氛作为渗剂,故又称“氰化”。
按共渗介质状态分为气体、液体 及固体3类。
碳氮共渗有高温碳氮共渗(氰化处理)和中温碳氮共渗之分.低温碳氮共渗也叫软氮化(氮碳共渗).与渗碳相 比,具有较快的渗入速度,较高的渗层 的淬透性和回火抗力,耐磨性和抗疲 劳性能好等优点,处理温度较低,减少了零件的变形。
3适用材料渗碳必须用低碳钢或低碳合金钢。
含碳量一般都在0.15%-0.25%范围内,用得最多的低碳钢是15和20钢,低合金渗碳钢如20Cr、15CrMo理论上,任何钢种都能通过氮化来改善其表层特性,但实际上,普通的碳钢氮化后,钢的表面硬度提高的不多,这是因为铁的氮化物(如:Fe2N、Fe3N、Fe4N等)稳定性较差,易于集聚粗化,硬度较低。
所以为了获得高硬度和高耐磨性的表层,必须采用含有氮化物形成元素的合金钢。
最佳材料:38CrMoAl尤其是AI,铝是最强的氮化物元素。
在含铬的铬钢而言,如果有足够的含量,亦可得到很好的效果。
但没有含合金的碳钢,因其生成的渗氮层很脆,容易剥落,不适合作为渗氮钢。
钢的化学热处理

渗剂
吸收: 析出的活性原子克服表面能垒进入金属表面, 形成固溶体或化合物。
Fe〃[C]吸附 → Fe〃C溶
溶解
3Fe〃[C]吸附 → Fe3C
化合
吸收必须进行得足够快,否则会因发生其它反应而失去活性 。 吸收能力与钢的表面活性有关,表面缺陷多(位错、晶界露 头)、粗糙、干净无污染则表面活性高,吸附力强,可促进化 学热处理。
常用的气体介质:天然气、煤气、液化石油气。
使用时,直接通入炉罐里。 CH4→2H2+[C]
2CO→CO2+[C]
CO+H2→H2O+[C]
良好的渗碳介质应具备下列条件:
价格低廉,安全卫生,易于获取; 具有较好的活性,既保证能获得较高的渗碳速度,同时不致使
渗碳层碳浓度过高,而造成大量的过剩碳化物;
5)化学催渗:渗剂中加入一定的化学药剂或触媒剂以加速分解或吸收过程
6)物理催渗:eg:高频电场下的扩散。
化学热处理进行的条件:
1. 渗入元素的原子必须是活性原子, 而且具有较大的扩散能力 2. 零件本身具有吸收渗入原子的能力, 即对渗入原子有一定的 溶解度或能与之化合, 形成化合物。
分解、吸收、扩散三者的协调进行是确保化学热处理成功进行的关键。
产生的“碳黑”“焦炭”少。 渗碳剂分解产物中如果含有较多的不饱和碳氢化合物易形成过
多的碳黑附着在零件表面,使渗碳不均匀;附着在炉壁上,使
炉罐导热性差,从而使渗碳速度降低,同时也增加清理时的麻 烦。 含硫量低。
举例:
18CrMnTi钢汽车后桥主动伞齿轮渗碳工艺
固体渗碳:
液相等离子体电解渗碳_渗氮及其碳氮共渗技术

收稿日期 : 2005 - 07 - 14 修回日期 : 2005 - 08 - 26 作者简介 :田占军 (1971 - ) ,男 ,河北衡水人 ,工程师 ,主要从事金 属材料表面强化外理研究 。 作者联系方式 :李杰 , ( Email) ljysu@263. net。
1 前言
离子渗碳 、渗氮 、碳氮共渗技术 [1 ]是从 20世纪 60 年代中期迅速发展起来的 ,经过 40多年的时间 ,已经 成为离子热处理技术中比较普及的工艺 ,但是具有处 理温度高、时间太长 、工件容易变形等缺点 ,而且离子 渗碳、渗氮 、碳氮共渗反应需要在低真空条件下的真空 室 [1 ]内进行 。液相等离子体电解渗碳 、渗氮 、碳氮共渗 技术解决了这些问题 ,它是在一个开放的大气环境下、 特定的电解液中进行 ,整体工件受热轻微 ,且可以在完 成渗透处理后直接淬火 ,在几分钟的时间内即可获得 高硬耐磨、耐蚀的渗透层 。等离子电解渗碳 /氮技术属 于等离子体电解沉积的范畴 [2 ] 。等离子体电解沉积 (p lasma electrolytic deposition, PED)是一种利用等离子 体电解进行材料表面处理的新兴技术 。由于放电 ,在 电解液中会产生有别于固态 、液态 、气态的物质第四态 “等离子体 ”。等离子体电解沉积 [ 2]包括等离子体电解 氧化和等离子体电解渗透 2种技术 ,其划分是根据被 处理工件材料的不同而定义的。对于 A l、Mg、Ti等轻 金属及其合金材料的处理 ,应用的是等离子体电解氧 化 [ 3 - 6 ] (又称微弧氧化技术 [ 7 - 17 ] ) ;对于钢铁材料的处 理 ,应用的是等离子体电解渗透技术 [18 ] 。等离子体电 解渗透技术根据电解液体系选择的不同可以分为阴极 和阳极等离子体渗透技术。该技术有处理时间短 、处 理工艺简单 、试用范围广等优点 ,但目前对这项技术的 研究并不是很多 ,进行的研究也主要集中在阴极等离 子 体 电 解 渗 透 技 术 上 : 聂 学 渊 [19 ] 和 A. L. Yerokhin [ 20 ]等人进行的研究是在尿素电解液体系下对不锈钢进 行等离子体碳氮共渗处理 ; M. Tarakci[21 ]等人是在甘油 电解液体系下对纯铁进行等离子体电解渗碳处理 ;本 课题组 [22 ]目前研究在甲酰胺 - 乙醇胺体系下对低碳钢 (Q235)进行等离子体电解碳氮共渗处理和在甲酰胺体 系下进行等离子体电解渗氮研究 ,最近笔者在试验中 处理试样 30 s就得到了超过 40μm的渗透层。工件作
- 1、下载文档前请自行甄别文档内容的完整性,平台不提供额外的编辑、内容补充、找答案等附加服务。
- 2、"仅部分预览"的文档,不可在线预览部分如存在完整性等问题,可反馈申请退款(可完整预览的文档不适用该条件!)。
- 3、如文档侵犯您的权益,请联系客服反馈,我们会尽快为您处理(人工客服工作时间:9:00-18:30)。
渗碳渗氮、氮碳共渗标准
通俗地说,不锈钢就是不容易生锈的钢,实际上一部分不锈钢,既有不锈性,又有耐酸性(耐蚀性)。
不锈钢的不锈性和耐蚀性是由于其表面上富铬氧化膜(钝化膜)的形成。
这种不锈性和耐蚀性是相对的。
试验表明,钢在大气、水等弱介质中和硝酸等氧化性介质中,其耐蚀性随钢中铬含水量的增加而提高,当铬含量达到一定的百分比时,钢的耐蚀性发生突变,即从易生锈到不易生锈,从不耐蚀到耐腐蚀。
不锈钢的分类方法很多。
按室温下的组织结构分类,有马氏体型、奥氏体型、铁素体和双相不锈钢;按主要化学成分分类,基本上可分为铬不锈钢和铬镍不锈钢两大系统;按用途分则有耐硝酸不锈钢、耐硫酸不锈钢、耐海水不锈钢等等,按耐蚀类型分可分为耐点蚀不锈钢、耐应力腐蚀不锈钢、耐晶间腐蚀不锈钢等;按功能特点分类又可分为无磁不锈钢、易切削不锈钢、低温不锈钢、高强度不锈钢等等。
由于不锈钢材具有优异的耐蚀性、成型性、相容性以及在很宽温度范围内的强韧性等系列特点,所以在重工业、轻工业、生活用品行业以及建筑装饰等行业中获取得广泛的应用。
奥氏体不锈钢在常温下具有奥氏体组织的不锈钢。
钢中含Cr约18%、Ni 8%~10%、C约0.1%时,具有稳定的奥氏体组织。
奥氏体铬镍不锈钢包括著名的18Cr-8Ni钢和在此基础上增加Cr、Ni含量并加入Mo、Cu、Si、Nb、Ti等元素发展起来的高Cr-Ni 系列钢。
奥氏体不锈钢无磁性而且具有高韧性和塑性,但强度较低,不可能通过相变使之强化,仅能通过冷加工进行强化。
如加入S,Ca,Se,Te等元素,则具有良好的易切削性。
此类钢除耐氧化性酸介质腐蚀外,如果含有Mo、Cu等元素还能耐硫酸、磷酸以及甲酸、醋酸、尿素等的腐蚀。
此类钢中的含碳量若低于0.03%或含Ti、Ni,就可显著提高其耐晶间腐蚀性能。
高硅的奥氏体不锈钢浓硝酸肯有良好的耐蚀性。
由于奥氏体不锈钢具有全面的和良好的综合性能,在各行各业中获得了广泛的应用。
铁素体不锈钢
在使用状态下以铁素体组织为主的不锈钢。
含铬量在11%~30%,具有体心立方晶体结构。
这类钢一般不含镍,有时还含有少量的Mo、Ti、Nb等到元素,这类钢具导热系数大,膨胀系数小、抗氧化性好、抗应力腐蚀优良等特点,多用于制造耐大气、水蒸气、水及氧化性酸腐蚀的零部件。
这类钢存在塑性差、焊后塑性和耐蚀性明显降低等缺点,因而限制了它的应用。
炉外精炼技术(AOD或VOD)的应用可使碳、氮等间隙元素大大降低,因此使这类钢获得广泛应用。
奥氏体--铁素体双相不锈钢
是奥氏体和铁素体组织各约占一半的不锈钢。
在含C较低的情况下,Cr含量在18%~28%,Ni含量在3%~10%。
有些钢还含有Mo、Cu、Si、Nb、Ti,N等合金元素。
该类钢兼有奥氏体和铁素体不锈钢的特点,与铁素体相比,塑性、韧性更高,无室温脆性,耐晶间腐蚀性能和焊接性能均显著提高,同时还保持有铁素体不锈钢的475℃脆性以及导热系数高,具有超塑性等特点。
与奥氏体不锈钢相比,强度高且耐晶间腐蚀和耐氯化物应力腐蚀有明显提高。
双相不锈钢具有优良的耐孔蚀性能,也是一种节镍不锈钢。
马氏体不锈钢
通过热处理可以调整其力学性能的不锈钢,通俗地说,是一类可硬化的不锈钢。
典型牌号为Cr13型,如2Cr13 ,3Cr13 ,4Cr13等。
粹火后硬度较高,不同回火温度具有不同强韧性组合,主要用于蒸汽轮机叶片、餐具、外科手术器械。
根据化学成分的差异,马氏体不锈钢可分为马氏体铬钢和马氏体铬镍钢两类。
根据组织和强化机理的不同,还可分为马氏体不锈钢、马氏体和半奥氏体(或半马氏体)沉淀硬化不锈钢以及马氏体时效不锈钢等。
不锈钢具有良好的耐腐蚀能,抗高温氧化性,较好的低温性能及优良的机械与加工性能。
因此广泛用于化工、石油、动力、核工程、航天航空、海洋、医药、轻工、纺织等部门。
其主要目的在于防腐防锈。
不锈钢的耐腐蚀主要依靠表面钝化膜,如果膜不完整或有缺陷,不锈钢仍会被腐蚀。
工程上通常进行酸洗钝化处理,使不锈钢的耐蚀潜力发挥得更大。
在不锈钢设备与部件在成形、组装、焊接、焊缝检查(如探伤、耐压试验)及施工标记等过程中带来表油污、铁锈、非金属脏物、油漆、焊渣与飞溅物等,这些物质影响了不锈钢设备与部件表面质量,破坏了其表面的氧化膜,降低了钢的抗全面腐蚀性能(包括点蚀、缝隙腐蚀),甚至会导致应力腐蚀破裂。
1.腐蚀的种类和定义
在众多的工业用途中,不锈钢都能提供今人满意的耐蚀性能。
根据使用的经验来看,除机械失效外,不锈钢的腐蚀主要表现在:不锈钢的一种严重的腐蚀形式是局部腐蚀(亦即应力腐蚀开裂、点腐蚀、晶间腐蚀、腐蚀疲劳以及缝隙腐蚀)。
这些局部腐蚀所导致的失效事例几乎占失效事例的一半以上。
事实上,很多失效事故是可以通过合理的选材而予以避免的。
应力腐蚀开裂(SCC):是指承受应力的合金在腐蚀性环境中由于烈纹的扩展而互生失效的一种通用术语。
应力腐蚀开裂具有脆性断口形貌,但它也可能发生于韧性高的材料中。
发生应力腐蚀开裂的必要条件是要有拉应力(不论是残余应力还是外加应力,或者两者兼而有之)和特定的腐蚀介质存在。
型纹的形成和扩展大致与拉应力方向垂直。
这个导致应力腐蚀开裂的应力值,要比没有腐蚀介质存在时材料断裂所需要的应力值小得多。
在微观上,穿过晶粒的裂纹称为穿晶裂纹,而沿晶界扩图的裂纹称为沿晶裂纹,当应力腐蚀开裂扩展至其一深度时(此处,承受载荷的材料断面上的应力达到它在空气中的断裂应力),则材料就按正常的裂纹(在韧性材料中,通常是通过显微缺陷的聚合)而断开。
因此,由于应力腐蚀开裂而失效的零件的断面,将包含有应力腐蚀开裂的特征区域以及与已微缺陷的聚合相联系的“韧窝”区域。
点腐蚀:是一种导致腐蚀的局部腐蚀形式。
晶间腐蚀:晶粒间界是结晶学取向不同的晶粒间紊乱错合的界城,因而,它们是钢中各种溶质元素偏析或金属化合物(如碳化物和δ相)沉淀析出的有利区城。
因此,在某些腐蚀介质中,晶粒间界可能先行被腐蚀乃是不足为奇的。
这种类型的腐蚀被称为晶间腐蚀,大多数的金属和合金在特定的腐蚀介质中都可能呈现晶间腐蚀。
缝隙腐蚀:是局部腐蚀的一种形式,它可能发全于溶液停滞的缝隙之中或屏蔽的表面内。
这样的缝隙可以在金属与金属或金属与非金属的接合处形成,例如,在与铆钉、螺栓、垫片、阀座、松动的表面沉积物以及海生物相接烛之处形成。
全面腐蚀:是用来描述在整个合金表面上以比较均勺的方式所发生的腐蚀现象的术语。
当发生全面腐蚀时,村料由于腐蚀而逐渐变薄,甚至材料腐蚀失效。
不锈钢在强酸和强碱中可能呈现全面腐蚀。
全面腐蚀所引起的失效问题并不怎么令人担心,因为,这种腐蚀通常可以通过简单的浸泡试验或查阅腐蚀方面的文献资料而预测它。
2.各种不锈钢的耐腐蚀性能
304 是一种通用性的不锈钢,它广泛地用于制作要求良好综合性能(耐腐蚀和成型性)的设备和机件。
301 不锈钢在形变时呈现出明显的加工硬化现象,被用于要求较高强度的各种场合。
302 不锈钢实质上就是含碳量更高的304不锈钢的变种,通过冷轧可使其获得较高的强度。
302B 是一种含硅量较高的不锈钢,它具有较高的抗高温氧化性能。
303和303Se 是分别含有硫和硒的易切削不锈钢,用于主要要求易切削和表而光浩度高的场合。
303Se不锈钢也用于制作需要热镦的机件,因为在这类条件下,这种不锈钢具有良好的可热加工性。
304L 是碳含量较低的304不锈钢的变种,用于需要焊接的场合。
较低的碳含量使得在靠近焊缝的热影响区中所析出的碳化物减至最少,而碳化物的析出可能导致不锈钢在某些环境中产生晶间腐蚀(焊接侵蚀)。
304N 是一种含氮的不锈钢,加氮是为了提高钢的强度。
305和384 不锈钢含有较高的镍,其加工硬化率低,适用于对冷成型性要求高的各种场合。
308 不锈钢用于制作焊条。
309、310、314及330 不锈钢的镍、铬含量都比较高,为的是提高钢在高温下的抗氧化性能和蠕变强度。
而30S5和310S乃是309和310不锈钢的变种,所不同者只是碳含量较低,为的是使焊缝附近所析出的碳化物减至最少。
330
不锈钢有着特别高的抗渗碳能力和抗热震性.
316和317 型不锈钢含有铝,因而在海洋和化学工业环境中的抗点腐蚀能力大大地优于304不锈钢。
其中,316型不锈钢由变种包括低碳不锈钢316L、含氮的高强度不锈钢316N以及合硫量较高的易切削不锈钢316F。
321、347及348 是分别以钛,铌加钽、铌稳定化的不锈钢,适宜作高温下使用的焊接构件。
348是一种适用于核动力工业的不锈钢,对钽和钻的合量有着一定的限制。
在空气中或化学腐蚀介质中能够抵抗腐蚀的一种高合金钢,不锈钢是具有美观的表面和耐腐蚀性能好,不必经过镀色等表面处理,而发挥不锈钢所固有的表面性能,使用于多方面的钢铁的一种,通常称为不锈钢。
代表性能的有13铬钢,18-铬镍钢等高合金钢。
从金相学角度分析,因为不锈钢含有铬而使表面形成很薄的铬膜,这个膜隔离开与钢内侵入的氧气起耐腐蚀的作用。
为了保持不锈钢所固有的耐腐蚀性,钢必须含有12%以上的铬。