文献翻译—汽车转向系统的发展
汽车电动助力转向系统的发展

汽车电动助力转向系统的发展汽车电动助力转向系统是一种利用电动机辅助车辆转向的技术。
随着科技的进步和人们对驾驶体验的要求不断提高,汽车电动助力转向系统在近年来得到了快速发展。
汽车电动助力转向系统的发展可以追溯到20世纪60年代,当时一些高档车型开始使用液压助力转向系统,通过液压泵和转向助力器来提供转向的辅助力。
这种系统存在液压泄漏、能效低下等问题,而且在高速行驶时往往会感受到转向过重的现象。
为了解决这些问题,汽车电动助力转向系统逐渐取代了液压助力转向系统。
这种系统利用电动机代替了液压泵,通过转向助力器将电动机提供的力量传递给转向装置,实现转向的辅助作用。
相比于液压助力转向系统,电动助力转向系统具有体积小、重量轻、响应速度快、能耗低等优点,大大提高了转向的精度和舒适性。
随着电动助力转向系统的发展,一种新型的系统被引入,即电动助力转向系统。
这种系统将电动助力转向系统与机械助力转向系统相结合,通过电动机和传统的转向齿轮机构相互协调工作,实现最佳的转向效果。
电动机可以在低速行驶时提供更大的助力,而在高速行驶时逐渐减小助力,以保证转向的稳定性和安全性。
近年来,一些车辆制造商开始使用电子控制系统来进一步提升汽车电动助力转向系统的功能。
通过与车辆的其他系统相连接,电子控制系统可以实现自动驾驶、路径规划、防抱死制动等高级功能,大大提高了驾驶的便利性和安全性。
除了在传统的内燃机汽车上使用,电动助力转向系统在电动汽车和混合动力汽车上也得到了广泛应用。
由于电动汽车和混合动力汽车通常具有较高的动力输出,因此需要更强的转向辅助力来应对不同的驾驶条件。
汽车电动助力转向系统通过与电动机和电池系统相连接,可以提供更大的辅助力,满足车辆的转向需求。
汽车转向系统的发展

1-方向盘 2-转向轴 3-转向中间轴 4-转向油 管 5-转向油泵 6-转向油罐 7-转向节臂 8转向横拉杆 9-转 向 摇 臂 10-整 体 式 转 向 器 (包 括 转 向 控 制 阀 、液 压 油 缸 、机 械 转 向 器 ) 11-转 向 直拉杆 12-转向减振器
图 1 液压助力转向系统构成
在此过程中,微处理器以 0.004s/次 的 频 率 持 续 不 断 地 反 复 进 行转向角度的计算和转向系统故障 自检,一旦四轮转向系统出现异常或 传感器出现错误时,后轴转向执行电 机立即自动驱动后轴回正,同时系统 由 4WS 模式切换至 2WS (传统的两 前轮转向)的安全转向模式。即便在 转向过程中 ECU 出现灾难性故障, 后轴转向齿条机构内部的回位弹簧 也能够使后轴慢慢回复至中立位置, 并同时使后轴转向电机关闭,以阻止 后轮的转向动作。
min 的发动机转速限制。 空调高压端:检测仪范围为 0~
459kPa,显示电压为 0~5V,所代表的 是空调制冷剂压力传感器的信号,压 力的数值表明安装在发动机上的空 调(A/C)压缩机的负荷,PCM 利用这 个信息来调整怠速并控制冷却风扇。
节气门全开(WOT)时 A/C 关闭 (OFF):检 测 仪 显 示“ 是 ”或“ 否 ”,显 示“是”表明 PCM 已使 A/C 压缩机离 合器继电器关闭,因为节气门位置 (TP)已超过 A/C 压缩机正常工作的
电子控制液压助力转向系也靠 液压力帮助驾驶员转向,但其液压泵 (齿轮泵)是通过电动机驱动的,与发 动机在机械上毫无关系,其助力效果 只与方向盘速度和车辆的行驶速度 有关。
1.系统结构和工作原理 电子控制助力转向系统
向系统。因为液压泵的供油量主要是 由方向盘转角变化量和车速决定的, 其共有特性更符合转向系统对助力 作用的实际要求,因此节省能量,并 能够获得更加理想的转向助力特性。 但是,它在不转向时仍然存在能量损 失,而且液压系统的固有缺陷仍然存
文献翻译-马自达公司的速度感应四轮转向系统

英文全文The Mazda Speed Sensing Computerised 4-Wheel Steering System.the Mazda Speed Sensing Computerised 4-Wheel SteeringThe Mazda Speed SensingComputerised 4-Wheel Steering System.Three and a half decades ago,well-calculated conclusion that presentation Conference,at the October 26,two young Mazda designers arrived at a far-sighted and was quite revolutionary for the time. In their technical 1962 Japanese Automotive Engineers' Society Technical Dr Tadashi Okada concerning vehicle dynamics as and engineer Toshiaki summarised their arduous research follows.1 The basic difference in the characteristics of oversteer and understeer lies in themagnitude of time delay and response.2.a vehicle that is stable under high speed must possess understeer characteristics3.the rear wheel tyre reflects heavily on the stability and a major improvement on control and stability may be anticipated by means of the automatic rear wheel steering system.The conclusions and formulations presented by these two engineers established thefoundation for Mazda's present-day reputed suspension technology. Over years of dedicatedresearch and development expertise, their original discoveries and theories have contributed to some of the most significant achievements within the recent history of automotive chassis engineering, incorporated by Mazda within its series production products. These developments include the twin trapezoidal link rear suspension, first employed in the originalfront-wheel driveMazda 323 (1980) and the Mazda 626 (1982}, and then perfected within the updated Mazd 626; the award winning Dynamic Tracking Suspension System of the second generation Mazda RX-7 (1985); and the elaborate E-link rear suspension of the new Mazda 929 (1987).While various external forces and loads are exerted to the rear wheels of a vehicle as itcombats the elements of the law of motion as defined by Sir Isaac Newton, these new suspension systems convert those forces into "4WS effects" which positively aid in vehicle stability and agility.the Mazda designers' and engineers' ultimate goal was still a positive measure to generateforces for positive controls; a Four-Wheel Steering system.In 1983, Mazda astonished the automotive world with the introduction of an engineeringconcept car, the MX-02, exhibited at the Tokyo Motor Show. This four-door Sedan, withgenerous passenger accommodation on an unusually long wheelbase, incorporated among itsnumerous advanced features a true 4WS system that aided high-speed stability as well as itslow-speed manoeuvring. The degree of rear wheel steering was determined by themeasurement of both front wheel steering angle and vehicle speed, by means of a centralcomputer unit.The MX-02 was followed by another exciting concept car; the MX-03, first exhibited at theFrankfurt Motor Show in September 1985. This sleek four seat futuristic coupe of the 1990scombined a refined electronically-controlled 4WS system with a continually varying torque-split, four-wheeldrive system and a powerful three-rotary engine.Mazda Electronically一Controlled Four-Wheel Steering System:A Beneficial TechnologyMazda's electronically-controlled, vehicle-speed-sensing Four-Wheel Steering System (4WS}steers the rear wheels in a direction and to a degree most suited to a corresponding vehicle speed range. The system is mechanically and hydraulically actuated, producing greatly enhanced stability, and within certain parameters, agility.The driver of a Mazda 4W5-equipped car derives five strategic benefits, over and above the conventional vehicle chassis.1.Superior cornering stability2.Improved steering responsiveness and precision3.High-speed straightline stability4.Notable improvement in rapid lane-changing manoeuvres5.Smaller turning radius and tight-space manoeuvrability at low vehicle speed rangeThe most outstanding advantage of the Mazda 4WS is that it contributes to a notable reduction in driver fatigue over high-speed and extended travelling. This is achieved by optimally:1 .reducing the response delay to steering input and action and2. eliminating the vehicle's excessive reaction to steering inputIn essence, by providing the optimum solution to the phenomena researched by the two youngMazda engineers in the early sixties一by the method advocated by them一the 4WS system has emerged as a fully beneficial technology. Strategic ConstructionThe Mazda 4WS consists of a rack-and-pinion front steering system that is hydraulically assisted by atwin-tandem pump main power source, with an overall steering ratio of 14.2:1.The rear wheel steering mechanism is also hydraulically assisted by the main pump andelectronically controlled一according to the front steering angle and vehicle speed. The rearsteering shaft extends from the rack bar of the front steering gear assembly to the rearsteering-phase control unit.The rear steering system is comprised of the input end of the rear steering shaft, vehicle speed sensors, a steering-phase control unit {determining direction and degree), a power cylinder andan output rod. A centering lock spring is incorporated, which locks the rear system in a neutral (straightforward} position in the event of hydraulic failure. Additionally, a solenoid valve that disengages hydraulic assist (thereby activating the centering lock spring} in case of anelectrical failure is ineluded.The 4WS system varies the phase and ratio of the rear-wheel steering to the front wheels,according to the vehicle speed. It steers the rear wheels toward the opposite phase (direction}of the front wheel during speeds less than 35kmlh (22mph} for a tighter turn and "neutralizes"them (to a straightforward direction, as in a conventional two-wheel steering principle} at35kmlh (22mph}. Above that speed, the system steers toward the same phase-direction as thefront wheels, thereby generating an increased cornering force for stability. The maximunsteering angle of the rear wheels extends 5 degrees to either left or right, a measurement th敏Mazda has determined to be optimally effective and natural to human sensitivity.Primary Components1. Vehicle speed sensors Interpret speedometer shelf revolutions and send signal to theelectronic computer unit. two sensors, one within the speedometer and the other atthe transmission output, are used to crosscheck the other for accuracy and failsafemeasures.2. Steering phase control unit Conveys to the power steering cylinder booster valve the direction and stroke of rear wheel steering by the combined movement of the control yoke angle and bevel gear revolutions.3.Electric stepper motor Performs altering of the yoke angle and bevel gear phasing4.Rear steering shaft Transmits front wheel steering angle by turning the small bevelgear in the steering phase control unit, which rotates the main bevel gear in the assembly.5.Control valve Feeds hydraulic pressure to the steering actuator, according to thephase and stroke required for appropriate rear wheel steering.6.Hydraulic power cylinder Operates the output rod by hydraulic pressure and steersthe rear wheels. It locks the rear wheels in a "neutral" (straightforward) position withthe centering lock spring, which is activated by a solenoid valve in case of failure toensure a normal 2WS function for the vehicle.7.Hydraulic pump. Provides hydraulic pressure to both the front and rear steering Systems.Details of Steering Phase Control UnitThe steering phase control unit alters the direction and degree of rear wheel steering. It consists of a stepper motor that controls the rear steering ratio, a control yoke, a swing arm, a main bevel gear engaged to the rear steering shaft via a small bevel gear, and a control rod connected to the control valve. It operates:a. Opposite phase (direction) steering under 35kmlh (22mph)1.Control Yoke is at an angle activated by the stepper motor2.Front wheels are steered to the right. The small bevel gear is rotated in direction X bythe rotation of the rear steering shaft. The small bevel gear, in turn, rotates the mainbevel gear.3.Rotation of the main bevel gear causes movement of the control rod toward the control valve.4.Input rod of the control valve is pushed to the right, according to the degree of the control rod's movement (determined by the disposition of the swing arm}, which is positioned to move in an upward direction, to the right. The rear wheels are thus steered to the left, in an opposite direction to the front wheels5.As the angle of the control yoke is increased in direction A as vehicle speed decreases, the rear-to-front steering ratio proportionately increases and the vehicle'ssteering lock tightens.b. Same phase (direction} over 35kmlh (22mph)The operation of this phase is the reverse of the opposite phase one, because the control yoke is angled toward "positive" in this vehicle speed range, as illustrated. The phasing of the swing arm, yoke rod and bevel gear steers the rear wheels toward the right-the same direction as the front wheels.c. Neutral phase, at 35kmlh (22mph} The control yoke's angle is horizontal (neutral). Thus, theinput rod is not affected, even if the control rod is moved with the rotation of the bevel gear unit As a result, the rear wheels are not steered in this mode.Power CylinderThe movement of the input rod of the control valve unit is transmitted to the power cylinder'sspool. The spool's displacement to the sleeve causes a pressure difference between the right and left side chambers in the hydraulic power cylinder. The pressure difference overcomes the output shaft load and initiates sleeve movement. The sleeve-power rod assembly is moved in the direction of the input rod by a proportionate degree. The output rod transmits steering action to the tie rod on either end of the rear wheel steering control-mechanism unit, thereby steering the rear wheels.Fai-Safe MeasuresThe system automatically counteracts possible causes of failure, both electronic and hydraulic. In either case, the centering lock spring housed in the steering system unit returns the output rods in the "neutral" straightforward position, essentially alternating the entire steering systemto a conventional 2WS principle.Specifically, if a hydraulic defect should render a reduction in pressure level (by a movement malfunction or a broken driving belt), the rear wheel steering mechanism is automatically locked in a neutral position, activating a low-level warning light.In the event of an electrical failure, such would be detected by a self-diagnostic circuit integrated within the 4WS control unit, which stimulates a solenoid valve and then neutralizes hydraulic pressure and return lines, thereby alternating the system again to that of a 2WS principle. Henceforth, the warning light referencing the 4WS system within the main instrument display is activated, indicating a system failure.中文译文马自达公司的速度感应四轮转向系统三十五年前,两个马自达设计师提出了个远见的、有计算认为是相当革命性的结论。
汽车助力转向文献综述

文献综述汽车转向是通过驾驶者转动方向盘,经过转向系统提供的操纵力以改变车轮角度来实现。
助力转向是一种为了减轻驾驶员的操纵力而设有主力机构的转向装置。
为方便驾驶员易于操纵转向系,动力转向已经成为汽车的标准装备。
黄蓉清认为:汽车汽车转向系统大致经历了无助力的纯机械转向(MS)、有液压助力的液压助力转向(HPS)、随车速改变助力大小的电控液压助力转向(ECHPS)、由电动机直接驱动转向油泵的电动液压助力转向(EHPS)、纯粹靠电动机提供助力的电动助力转向(EPS)、可变传动比转向系统(VGRS)等发展历程。
专家们预测,未来汽车转向系统的发展趋势是线控转向(SBW),即取消方向盘与转向车轮之间原有的机械连接,而改用控制信号代替的一种电动转向系统。
(电动助力转向的原理和发展,华南理工大学汽车工程学院,广东广州510640,黄蓉清,向铁明,许迎东)。
电子助力转向系统的发展是朝着EPS的方向发展的,未来汽车配置中将必不可少的拥有电子助力转向系统,对司机的安全驾驶起到协助作用。
李国洪(电动助力系统控制单元的设计,天津理工大学,天津市复杂系统控制理论及应用重点实验室,天津300384)做出论断:在电动助力转向系统中,电子控制单元是整个系统的控制核心,也是驾驶系统的主要工作,电子控制单元设计要实现的主要功能如下:(1)采集方向盘扭矩信号和车速信号,并将其转化为DSP可以接收、处理的信号。
(2)根据控制要求,确定助力特性,将扭矩值换算成为电机提供的目标电流值。
(3)设计合适的驱动电路,将DSP的输出信号提供给直流助力电机。
(4)跟踪目标电流形成闭环控制,保证实际电流和目标电流的误差不超过允许范围.(5)对系统进行监控和保护,保证系统正常工作。
电动助力系统控制单元的设计是重中之重,对于控制单元的设计,我会尽力于老师沟通,毕竟控制单元一步错步步错,对于控制单元我细心加谨慎,来认真完成。
郝金魁认为(电动助力转向系统驱动电路的设计,石家庄铁道学院机械工程分院,2006-09-11,郝金魁,张超风):电动助力转向系统的硬件电路主要包括以下模块:MC9S12DP256 微控制器、电源电路、信号处理电路、直流电机功率驱动模块、故障诊断模块与显示模块、车速传感器、扭矩传感器、发动机点火信号、电流及电流传感器等接人处理电路, 另外还有电磁离合器等。
(完整版)汽车转向系统最新毕业论文设计

优秀论文审核通过未经允许切勿外传开题报告一、背景、现状及发展趋势转向系统:用来改变或保持汽车行驶方向的机构称为汽车转向系统(steering system)。
汽车转向系统的功能就是按照驾驶员的意愿控制汽车的行驶方向。
汽车转向系统对汽车的行驶安全至关重要,因此汽车转向系统的零件都称为保安件。
汽车转向系统分为两大类:机械转向系统和动力转向系统。
完全靠驾驶员手力操纵的转向系统称为机械转向系统。
借助动力来操纵的转向系统称为动力转向系统。
动力转向系统又可分为液压动力转向系统和电动助力动力转向系统。
随着产业布局、产品结构的调整,就业结构也将发生变化。
企业对较高层次的第一线应用型人才的需求将明显增加,培养相当数量的具有高等文化水平的职业人才,成为迫切要求。
据统计,目前,我国技术工人中,高级技工占 3.5℅,中级工占35℅,初级工占60℅。
而发达国家技术工人中,高级技工占35℅,中级工占50℅,初级工占15℅。
这表明,我们的高级技工在未来5—10年内仍会有大量的人才缺口。
因此熟悉汽车转向系统,熟练掌握现代化汽车转向系统的设计、操作和维护的应用型高级技术人才成为社会较紧缺、企业最需要的人才。
随着汽车工业的迅速发展,转向装置的结构也有很大变化。
现代汽车转向装置的设计趋势主要向适应汽车高速行驶的需要、充分考虑安全性、轻便性、低成本、低油耗、大批量专业化生产发展。
通过本次毕业论文对转向系统进行进一步的了解,并且结合通过实习了解的知识对转向系统的可能出现的问题进行分析和解决方法,从而提高自身对转向系统的深入认识二、设计目的通过本次毕业设计使自己对汽车转向系统在故障诊断和维修方面有更为充分、细致的理解,进一步掌握转向系统的原理、应用和CADCAM软件应用。
三、设计工作1、概述2、转向系统现阶段的主要类型3、汽车转向系统可能出现的问题和分析4、汽车转向系统的新发展---整体式、半分置式及联阀式动力转向结构四、时间安排项目时间截点备注论文题目确定2011年2月25日开题报告2011年3月4日论文初稿2011年4月15日论文定稿2011年5月7日论文答辩2011年5月15日二次答辩2011年5月22日目录浅析汽车转向系统常见故障诊断与维修 (2)摘要 (2)绪论 (3)1 概述 (4)1.1 什么是汽车转向系统 (4)1.2 汽车转向系统概述 (4)1.3 转向系统简介及工作原理 (4)2 汽车转向系统的故障诊断 (10)2.1 机械转向系故障诊断 (10)2.2 动力转向系故障诊断 (12)2.3 转向系仪器检测 (14)3对汽车转向系统的故障进行维修 (16)3.1机械转向系的维修 (16)3.2动力转向系的维修 (19)4结论……………………………………………………………………………………………22谢辞 (23)参考文献 (24)英文资料 (25)中文翻译 (30)浅析汽车转向系统常见故障诊断与维修摘要:本文阐述了汽车转向系统各个部分的作用、组成、主要构造、工作原理、及可能出现的故障,同时提出了对出现的故障进行维修的可行方案;采用了理论与实际相结合的方法,对每个问题都有良好的认识,对所学内容进行了良好的总结归纳,以此进一步熟悉掌握汽车转向系统的各方面知识,深化巩固所学知识,做到理论与实际相结合,在理论学习的前提下,用实际更好的理解所学内容。
汽车转向系统综述

汽车转向系统概述摘要本文简述了汽车转向系统在国内外的发展,经历了机械转向、液压助力转向、电控液压助力转向、电动助力转向系统四个阶段的发展的汽车转向系统已经相对成熟,探讨了汽车转向系统的发展趋势。
提出了通过控制信号解决方向盘与转向轴之间的联系问题,省略去方向盘与转向轴的机械连接装置,使汽车转向有更好的灵活性,更好的稳定性,轻便省力,并发现了系统中不够成熟和有待解决的问题。
关键词:助力转向;液压助力转向;电动助力转向AbstractThis article describes the steering system's development at home and abroad. The steering system experienced a mechanical steering, hydraulic power steering, electric hydraulic power steering and electric power steering four stages. Automotive steering system has been relatively mature. And the article explores the steering system trends. It proposed by the steering wheel and shift control signals to resolve the linkage between the axes, omitted to steering wheel and steering shaft of the mechanical connection device. It can make the car turn better flexibility, better stability. And I found that the system is not mature enough and the problems to be solved.Key Words: power steering; hydraulic power steering;electric power steering引言汽车转向系统的发展经历了传统的机械转向、液压助力转向、电控液压助力转向、电动助力转向系统四个阶段。
汽车电动助力转向系统的发展
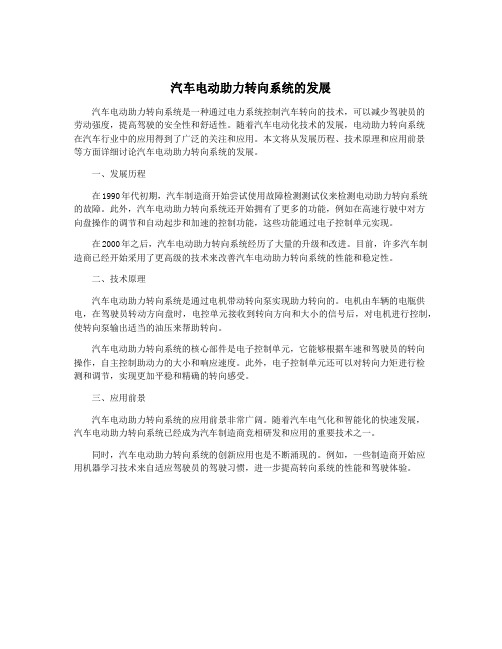
汽车电动助力转向系统的发展汽车电动助力转向系统是一种通过电力系统控制汽车转向的技术,可以减少驾驶员的劳动强度,提高驾驶的安全性和舒适性。
随着汽车电动化技术的发展,电动助力转向系统在汽车行业中的应用得到了广泛的关注和应用。
本文将从发展历程、技术原理和应用前景等方面详细讨论汽车电动助力转向系统的发展。
一、发展历程在1990年代初期,汽车制造商开始尝试使用故障检测测试仪来检测电动助力转向系统的故障。
此外,汽车电动助力转向系统还开始拥有了更多的功能,例如在高速行驶中对方向盘操作的调节和自动起步和加速的控制功能,这些功能通过电子控制单元实现。
在2000年之后,汽车电动助力转向系统经历了大量的升级和改进。
目前,许多汽车制造商已经开始采用了更高级的技术来改善汽车电动助力转向系统的性能和稳定性。
二、技术原理汽车电动助力转向系统是通过电机带动转向泵实现助力转向的。
电机由车辆的电瓶供电,在驾驶员转动方向盘时,电控单元接收到转向方向和大小的信号后,对电机进行控制,使转向泵输出适当的油压来帮助转向。
汽车电动助力转向系统的核心部件是电子控制单元,它能够根据车速和驾驶员的转向操作,自主控制助动力的大小和响应速度。
此外,电子控制单元还可以对转向力矩进行检测和调节,实现更加平稳和精确的转向感受。
三、应用前景汽车电动助力转向系统的应用前景非常广阔。
随着汽车电气化和智能化的快速发展,汽车电动助力转向系统已经成为汽车制造商竞相研发和应用的重要技术之一。
同时,汽车电动助力转向系统的创新应用也是不断涌现的。
例如,一些制造商开始应用机器学习技术来自适应驾驶员的驾驶习惯,进一步提高转向系统的性能和驾驶体验。
汽车电动助力转向系统的发展
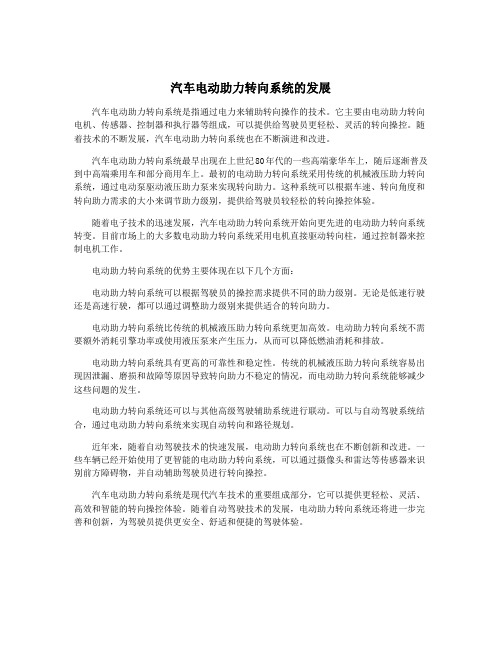
汽车电动助力转向系统的发展汽车电动助力转向系统是指通过电力来辅助转向操作的技术。
它主要由电动助力转向电机、传感器、控制器和执行器等组成,可以提供给驾驶员更轻松、灵活的转向操控。
随着技术的不断发展,汽车电动助力转向系统也在不断演进和改进。
汽车电动助力转向系统最早出现在上世纪80年代的一些高端豪华车上,随后逐渐普及到中高端乘用车和部分商用车上。
最初的电动助力转向系统采用传统的机械液压助力转向系统,通过电动泵驱动液压助力泵来实现转向助力。
这种系统可以根据车速、转向角度和转向助力需求的大小来调节助力级别,提供给驾驶员较轻松的转向操控体验。
随着电子技术的迅速发展,汽车电动助力转向系统开始向更先进的电动助力转向系统转变。
目前市场上的大多数电动助力转向系统采用电机直接驱动转向柱,通过控制器来控制电机工作。
电动助力转向系统的优势主要体现在以下几个方面:电动助力转向系统可以根据驾驶员的操控需求提供不同的助力级别。
无论是低速行驶还是高速行驶,都可以通过调整助力级别来提供适合的转向助力。
电动助力转向系统比传统的机械液压助力转向系统更加高效。
电动助力转向系统不需要额外消耗引擎功率或使用液压泵来产生压力,从而可以降低燃油消耗和排放。
电动助力转向系统具有更高的可靠性和稳定性。
传统的机械液压助力转向系统容易出现因泄漏、磨损和故障等原因导致转向助力不稳定的情况,而电动助力转向系统能够减少这些问题的发生。
电动助力转向系统还可以与其他高级驾驶辅助系统进行联动。
可以与自动驾驶系统结合,通过电动助力转向系统来实现自动转向和路径规划。
近年来,随着自动驾驶技术的快速发展,电动助力转向系统也在不断创新和改进。
一些车辆已经开始使用了更智能的电动助力转向系统,可以通过摄像头和雷达等传感器来识别前方障碍物,并自动辅助驾驶员进行转向操控。
汽车电动助力转向系统是现代汽车技术的重要组成部分,它可以提供更轻松、灵活、高效和智能的转向操控体验。
随着自动驾驶技术的发展,电动助力转向系统还将进一步完善和创新,为驾驶员提供更安全、舒适和便捷的驾驶体验。
- 1、下载文档前请自行甄别文档内容的完整性,平台不提供额外的编辑、内容补充、找答案等附加服务。
- 2、"仅部分预览"的文档,不可在线预览部分如存在完整性等问题,可反馈申请退款(可完整预览的文档不适用该条件!)。
- 3、如文档侵犯您的权益,请联系客服反馈,我们会尽快为您处理(人工客服工作时间:9:00-18:30)。
附录附录A 英文文献Along with automobile electronic technology swift and violent development, the people also day by day enhance to the motor turning handling quality request. The motor turning system changed, the hydraulic pressure boost from the traditional machinery changes (Hydraulic Power Steering, is called HPS), the electrically controlled hydraulic pressure boost changes (Elect ric Hydraulic Power Steering, is called EHPS), develops the electrically operated boost steering system (Elect ric Power Steering, is called EPS), finally also will transit to the line controls the steering system (Steer By Wire, will be called SBW).The machinery steering system is refers by pilot's physical strength achievement changes the energy, in which all power transmission all is mechanical, the automobile changes the movement is operates the steering wheel by the pilot, transmits through the diverter and a series of members changes the wheel to realize. The mechanical steering system by changes the control mechanism, the diverter and major part changes the gearing 3 to be composed.Usually may divide into according to the mechanical diverter form: The gear rack type, follows round the world -like, the worm bearing adjuster hoop type, the worm bearing adjuster refers sells the type. Is the gear rack type and follows using the broadest two kinds round the world -like (uses in needing time big steering force).In follows round the world -like in the diverter, the input changes the circle and the output steering arm pivot angle is proportional; In the gear rack type diverter, the input changes the turn and the output rack displacement is proportional. Follows round the world -like the diverter because is the rolling friction form, thus the transmission efficiency is very high, the ease of operation also the service life are long, moreover bearing capacity, therefore widely applies on the truck. The gear rack type diverter with follows round the world -like compares, the most major characteristic is the rigidity is big, the structure compact weight is light, also the cost is low. Because this way passes on easily by the wheel the reacting force to the steering wheel, therefore has to the pavement behavior response keen merit, but simultaneously also easy to have phenomena and so on goon and oscillation, also its load bearing efficiency relativeweak, therefore mainly applies on the compact car and the pickup truck, at present the majority of low end passenger vehicle uses is the gear rack type machinery steering system.Along with the vehicles carrying capacity increase as well as the people to the vehicles handling quality request enhancement, the simple mechanical type steering system were already unable to meet the needs, the power steering system arise at the historic moment, it could rotate the steering wheel while the pilot to provide the boost, the power steering system divides into the hydraulic pressure steering system and the electrically operated steering system 2 kinds.Hydraulic pressure steering system is at present uses the most widespread steering system.The hydraulic pressure steering system increased the hydraulic system in the mechanical system foundation, including hydraulic pump, V shape band pulley, drill tubing, feed installment, boost installment and control valve. It with the aid of in the motor car engine power actuation hydraulic pump, the air compressor and the generator and so on, by the fluid strength, the physical strength or the electric power increases the pilot to operate the strength which the front wheel changes, enables the pilot to be possible nimbly to operate motor turning facilely, reduced the labor intensity, enhanced the travel security.The hydraulic pressure boost steering system from invented already had about half century history to the present, might say was one kind of more perfect system, because its work reliable, the technology mature still widely is applied until now. It takes the power supply by the hydraulic pump, after oil pipe-line control valves to power hydraulic cylinder feed, through the connecting rod impetus rotation gear movement, may changes the boost through the change cylinder bore and the flowing tubing head pressure size the size, from this achieved changes the boost the function. The traditional hydraulic pressure type power steering system may divide into generally according to the liquid flow form: Ordinary flow type and atmospheric pressure type 2 kind of types, also may divide into according to the control valve form transfers the valve type and the slide-valve type.Along with hydraulic pressure power steering system on automobile daily popularization, the people to operates when the portability and the road feeling request also day by day enhance, however the hydraulic pressure power steering system has many shortcomings actually: ①Because its itself structure had decided it is unable to guarantee vehicles rotates the steering wheel when any operating mode, all has the ideal operation stability, namely is unable simultaneously to guarantee time the low speed changes theportability and the high speed time operation stability;②The automobile changes the characteristic to drive the pilot technical the influence to be serious; ③The steering ratio is fixed, causes the motor turning response characteristic along with changes and so on vehicle speed, transverse acceleration to change, the pilot must aim at the motor turning characteristic peak-to-peak value and the phase change ahead of time carries on certain operation compensation, thus controls the automobile according to its wish travel. Like this increased pilot's operation burden, also causes in the motor turning travel not to have the security hidden danger; But hereafter appeared the electrically controlled hydraulic booster system, it increases the velocity generator in the traditional hydraulic pressure power steering system foundation, enables the automobile along with the vehicle speed change automatic control force size, has to a certain extent relaxed the traditional hydraulic pressure steering system existence question.At present our country produces on the commercial vehicle and the passenger vehicle uses mostly is the electrically controlled hydraulic pressure boost steering system, it is quite mature and the application widespread steering system. Although the electrically controlled hydraulic servo alleviated the traditional hydraulic pressure from certain degree to change between the portability and the road feeling contradiction, however it did not have fundamentally to solve the HPS system existence insufficiency, along with automobile microelectronic technology development, automobile fuel oil energy conservation request as well as global initiative environmental protection, it in aspect and so on arrangement, installment, leak-proof quality, control sensitivity, energy consumption, attrition and noise insufficiencies already more and more obvious, the steering system turned towards the electrically operated boost steering system development.The electrically operated boost steering system is the present mo tor turning system development direction, its principle of work is: EPS system ECU after comes from the steering wheel torque sensor and the vehicle speed sensor signal carries on analysis processing, controls the electrical machinery to have the suitable boost torque, assists the pilot to complete changes the operation. In the last few years, along with the electronic technology development, reduces EPS the cost to become large scale possibly, Japan sends the car company, Mitsubishi Car company, this field car company, US's Delphi automobile system company, TRW Corporation and Germany's ZF Corporation greatly all one after another develops EPS.Mercedes2Benz and Siemens Automotive two big companiesinvested 65,000,000 pounds to use in developing EPS, the goal are together load a car to 2002, yearly produce 300 ten thousand sets, became the global EPS manufacturer. So far, the EPS system in the slight passenger vehicle, on the theater box type vehicle obtains the widespread application, and every year by three million speed development.Steering is the term applied to the collection of components, linkages, etc. which allow for a vessel (ship, boat) or vehicle (car) to follow the desired course. An exception is the case of rail transport by which rail tracks combined together with railroad switches provide the steering function.The most conventional steering arrangement is to turn the front wheels using a hand–operated steering wheel which is positioned in front of the driver, via the steering column, which may contain universal joints to allow it to deviate somewhat from a straight line. Other arrangements are sometimes found on different types of vehicles, for example, a tiller or rear–wheel steering. Tracked vehicles such as tanks usually employ differential steering —that is, the tracks are made to move at different speeds or even in opposite directions to bring about a change of course.Many modern cars use rack and pinion steering mechanisms, where the steering wheel turns the pinion gear; the pinion moves the rack, which is a sort of linear gear which meshes with the pinion, from side to side. This motion applies steering torque to the kingpins of the steered wheels via tie rods and a short lever arm called the steering arm.Older designs often use the recirculating ball mechanism, which is still found on trucks and utility vehicles. This is a variation on the older worm and sector design; the steering column turns a large screw (the "worm gear") which meshes with a sector of a gear, causing it to rotate about its axis as the worm gear is turned; an arm attached to the axis of the sector moves the pitman arm, which is connected to the steering linkage and thus steers the wheels. The recirculating ball version of this apparatus reduces the considerable friction by placing large ball bearings between the teeth of the worm and those of the screw; at either end of the apparatus the balls exit from between the two pieces into a channel internal to the box which connects them with the other end of the apparatus, thus they are "recirculated".The rack and pinion design has the advantages of a large degree of feedback and direct steering "feel"; it also does not normally have any backlash, or slack. A disadvantage is that it is not adjustable, so that when it does wear and develop lash, the only cure is replacement.The recirculating ball mechanism has the advantage of a much greater mechanical advantage, so that it was found on larger, heavier vehicles while the rack and pinion was originally limited to smaller and lighter ones; due to the almost universal adoption of power steering, however, this is no longer an important advantage, leading to the increasing use of rack and pinion on newer cars. The recirculating ball design also has a perceptible lash, or "dead spot" on center, where a minute turn of the steering wheel in either direction does not move the steering apparatus; this is easily adjustable via a screw on the end of the steering box to account for wear, but it cannot be entirely eliminated or the mechanism begins to wear very rapidly. This design is still in use in trucks and other large vehicles, where rapidity of steering and direct feel are less important than robustness, maintainability, and mechanical advantage. The much smaller degree of feedback with this design can also sometimes be an advantage; drivers of vehicles with rack and pinion steering can have their thumbs broken when a front wheel hits a bump, causing the steering wheel to kick to one side suddenly (leading to driving instructors telling students to keep their thumbs on the front of the steering wheel, rather than wrapping around the inside of the rim). This effect is even stronger with a heavy vehicle like a truck; recirculating ball steering prevents this degree of feedback, just as it prevents desirable feedback under normal circumstances.The steering linkage connecting the steering box and the wheels usually conforms to a variation of Ackermann steering geometry, to account for the fact that in a turn, the inner wheel is actually traveling a path of smaller radius than the outer wheel, so that the degree of toe suitable for driving in a straight path is not suitable for turns.As vehicles have become heavier and switched to front wheel drive, the effort to turn the steering wheel manually has increased - often to the point where major physical exertion is required. To alleviate this, auto makers have developed power steering systems. There are two types of power steering systems—hydraulic and electric/electronic. There is also a hydraulic-electric hybrid system possible.A hydraulic power steering (HPS) uses hydraulic pressure supplied by an engine-driven pump to assist the motion of turning the steering wheel. Electric power steering (EPS) is more efficient than the hydraulic power steering, since the electric power steering motor only needs to provide assist when the steering wheel is turned, whereas the hydraulic pump must run constantly. In EPS the assist level is easily tunable to the vehicletype, road speed, and even driver preference. An added benefit is the elimination of environmental hazard posed by leakage and disposal of hydraulic power steering fluid.An outgrowth of power steering is speed adjustable steering, where the steering is heavily assisted at low speed and lightly assisted at high speed. The auto makers perceive that motorists might need to make large steering inputs while manoeuvering for parking, but not while traveling at high speed. The first vehicle with this feature was the Citroën SM with its Diravi layout, although rather than altering the amount of assistance as in modern power steering systems, it altered the pressure on a centring cam which made the steering wheel try to "spring" back to the straight-ahead position. Modern speed-adjustable power steering systems reduce the pressure fed to the ram as the speed increases, giving a more direct feel. This feature is gradually becoming commonplace across all new vehicles.Four-wheel steering (or all wheel steering) is a system employed by some vehicles to increase vehicle stability while maneuvering at high speed, or to decrease turning radius at low speed.In most four-wheel steering systems, the rear wheels are steered by a computer and actuators. The rear wheels generally cannot turn as far as the Alternatively, several systems, including Delphi's Quadrasteer and the system in Honda's Prelude line, allow for the rear wheels to be steered in the opposite direction as the front wheels during low speeds. This allows the vehicle to turn in a significantly smaller radius —sometimes critical for large trucks or vehicles with trailers.附录B 文献翻译随着汽车电子技术的迅猛发展,人们对汽车转向操纵性能的要求也日益提高。