新型刀具论文
刀具材料论文

金属切削刀具的发展历史与现状前言刀具是机械制造中用于切削加工的工具,又称切削工具。
广义的切削工具既包括刀具,还包括磨具。
刀具技术的进步,体现在刀具材料、刀具结构、刀具几何形状和刀具系统四个方面,刀具材料新产品更是琳琅满目。
当代正在应用的刀具材料有高速钢、硬质合金、陶瓷、立方氮化硼和金刚石。
其中,高速钢和硬质合金是用得最多的两种刀具材料,分别约占刀具总量的30%~40%和50%~60%。
本文将介绍刀具的发展历程,发展现状,并对未来刀具的发展法相作出分析。
刀具的发展历史刀具的发展在人类进步的历史上占有重要的地位。
中国早在公元前28~前20世纪,就已出现黄铜锥和紫铜的锥、钻、刀等铜质刀具。
战国后期(公元前三世纪),由于掌握了渗碳技术,制成了铜质刀具。
当时的钻头和锯,与现代的扁钻和锯已有些相似之处。
然而,刀具的快速发展是在18世纪后期,伴随蒸汽机等机器的发展而来的。
1783年,法国的勒内首先制出铣刀。
1792年,英国的莫兹利制出丝锥和板牙。
有关麻花钻的发明最早的文献记载是在1822年,但直到1864年才作为商品生产。
那时的刀具是用整体高碳工具钢制造的,许用的切削速度约为5米/分。
1868年,英国的穆舍特制成含钨的合金工具钢。
1898年,美国的泰勒和.怀特发明高速钢。
1923年,德国的施勒特尔发明硬质合金。
在采用合金工具钢时,刀具的切削速度提高到约8米/分,采用高速钢时,又提高两倍以上,到采用硬质合金时,又比用高速钢提高两倍以上,切削加工出的工件表面质量和尺寸精度也大大提高。
由于高速钢和硬质合金的价格比较昂贵,刀具出现焊接和机械夹固式结构。
1949~1950年间,美国开始在车刀上采用可转位刀片,不久即应用在铣刀和其他刀具上。
1938年,德国德古萨公司取得关于陶瓷刀具的专利。
1972年,美国通用电气公司生产了聚晶人造金刚石和聚晶立方氮化硼刀片。
这些非金属刀具材料可使刀具以更高的速度切削。
1969年,瑞典山特维克钢厂取得用化学气相沉积法,生产碳化钛涂层硬质合金刀片的专利。
机加工中刀具使用和发展情况论文

机加工中刀具的使用和发展情况摘要:随着材料工业及精密机械工业的发展,精密切削、超精密切削和难切削材料使用的增多,超硬刀具材料的应用日益广泛。
本文通过分析超硬刀具材料的发展状况,对主要品种的应用进行探讨。
关键词:超硬刀具刀具材料金刚石一、超硬刀具材料发展概况超硬刀具材料是指天然金刚石及硬度、性能与之相近的人造金刚石和cbn(立方氮化硼)。
由于天然金刚石价格比较昂贵,所以生产上大多采用人造聚晶金刚石(pcd)、聚晶立方氮化硼(pcbn)以及它们的复合材料。
早在20世纪50年代,美国就利用人造金刚石微粉和cbn微粉在高温、高压、触媒和结合剂的作用下烧结成尺寸较大的聚晶块作为刀具材料。
之后,南非戴比尔斯(debeem)公司、前苏联和日本也相继研制成功。
20世纪70年代初又推出了金刚石或cbn和硬质合金的复合片,它们是在硬质合金基体上烧结或压制一层0.5mm~1mm 的pcd或pcbn而成,从而解决了超硬刀具材料抗弯强度低、镶焊困难等问题,使超硬刀具的应用进入实用阶段。
我国超硬刀具材料的研究与应用开始于上个世纪70年代,并于1970年在贵阳建造了我国第一座超硬材料及制品的专业生产厂第六砂轮厂,从1970—1990年整整20年中,超硬材料年产量从仅46万克拉增至3500万克拉。
上个世纪90年代前后,不少超硬材料生产专业厂从国外引进成套的超硬材料合成设备及技术,使产量得以迅速提高,至1997年,我国人造金刚石年产量就已达到5亿克拉左右,cbn年产量达800万克拉,跃居世界超硬材料生产大国之首。
金刚石具有极高的硬度和耐磨性,其显微硬度可达10000hv,是刀具材料中最硬的材料。
同时它的摩擦系数小,与非铁金属无亲和力,切屑易流出,热导率高,切削时不易产生积屑瘤,加工表面质量好,能有效地加工非铁金属材料和非金属材料,如铜、铝等有色金属及其合金、陶瓷、末烧结的硬质合金、各种纤维和颗粒加强的复合材料、塑料、橡胶、石墨、玻璃和各种耐磨的木材(尤其是实心木和胶合板等复合材料)。
一种新型刨床刀具的设计和仿真

De s i g n a nd S i mu l a t i o n f o r a Ne w Ty pe o f Pl ne a r To o l
2 0 1 3年 8月
机床与液压
MACHI NE T OOL & HYDRAUL I CS
Au g . 2 01 3
第4 1卷 第 1 6期
V0 1 . 41 No .1 6
D OI :1 0 . 3 9 6 9 / j . i s s n . 1 0 0 1—3 8 8 1 . 2 0 1 3 . 1 6 . 0 2 1
首先 ,人们认识 到 ,通过采用高效刀具提高劳动 生产率来降低成本 ,比单 纯节省 刀具费 用更加 有利 。 所 以 ,在现代 刀具 的制 造和使用 领域 , “ 效率优 先 ” 已经代 替 了传 统 的 “ 性 能价 格 比” 老 概 念 。其 次 , 近年来生产资料价格的不断升高 ,迫使工业制造企业 减少加工成本 ,以保证经济收益 。
XI E Xi l i n g , W AN G Ra n , W ANG J u n l i a n g ,Z HE NG We i g a n g
( 1 . L o g i s t i c s E n i g n e e r i n g C o l l e g e ,Wu h a n U n i v e r s i t y o f T e c h n o l o g y ,Wu h a n H u b e i 4 3 0 0 6 3 ,C h i n a ; 2 . E n in g e e r i n g T r a i n i n g C e n t e r ,Wu h a n U n i v e r s i y t o f T e c h n o l o y ,Wu g h a n H u b e i 4 3 0 0 6 3 ,C h i n a )
刀具材料论文

金属切削刀具的发展历史与现状前言刀具是机械制造中用于切削加工的工具,又称切削工具。
广义的切削工具既包括刀具,还包括磨具。
刀具技术的进步,体现在刀具材料、刀具结构、刀具几何形状和刀具系统四个方面,刀具材料新产品更是琳琅满目。
当代正在应用的刀具材料有高速钢、硬质合金、陶瓷、立方氮化硼和金刚石。
其中,高速钢和硬质合金是用得最多的两种刀具材料,分别约占刀具总量的30%~40%和50%~60%。
本文将介绍刀具的发展历程,发展现状,并对未来刀具的发展法相作出分析。
刀具的发展历史刀具的发展在人类进步的历史上占有重要的地位。
中国早在公元前28~前20世纪,就已出现黄铜锥和紫铜的锥、钻、刀等铜质刀具。
战国后期(公元前三世纪),由于掌握了渗碳技术,制成了铜质刀具。
当时的钻头和锯,与现代的扁钻和锯已有些相似之处。
然而,刀具的快速发展是在18世纪后期,伴随蒸汽机等机器的发展而来的。
1783年,法国的勒内首先制出铣刀。
1792年,英国的莫兹利制出丝锥和板牙。
有关麻花钻的发明最早的文献记载是在1822年,但直到1864年才作为商品生产。
那时的刀具是用整体高碳工具钢制造的,许用的切削速度约为5米/分。
1868年,英国的穆舍特制成含钨的合金工具钢。
1898年,美国的泰勒和.怀特发明高速钢。
1923年,德国的施勒特尔发明硬质合金。
在采用合金工具钢时,刀具的切削速度提高到约8米/分,采用高速钢时,又提高两倍以上,到采用硬质合金时,又比用高速钢提高两倍以上,切削加工出的工件表面质量和尺寸精度也大大提高。
由于高速钢和硬质合金的价格比较昂贵,刀具出现焊接和机械夹固式结构。
1949~1950年间,美国开始在车刀上采用可转位刀片,不久即应用在铣刀和其他刀具上。
1938年,德国德古萨公司取得关于陶瓷刀具的专利。
1972年,美国通用电气公司生产了聚晶人造金刚石和聚晶立方氮化硼刀片。
这些非金属刀具材料可使刀具以更高的速度切削。
1969年,瑞典山特维克钢厂取得用化学气相沉积法,生产碳化钛涂层硬质合金刀片的专利。
高速切削刀具在数控加工应用论文
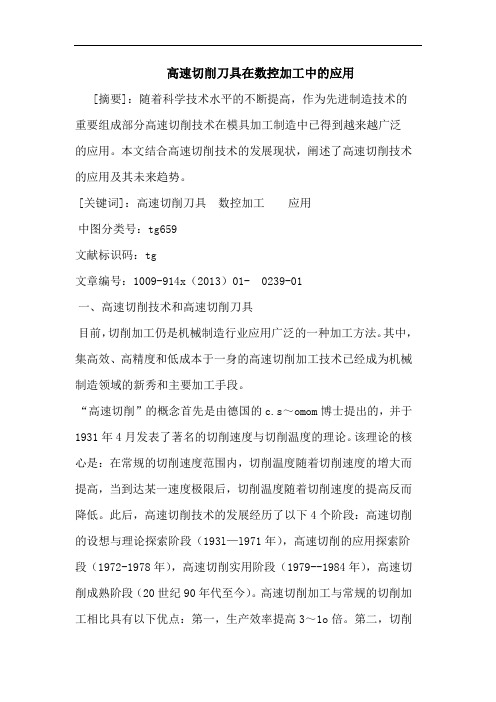
高速切削刀具在数控加工中的应用[摘要]:随着科学技术水平的不断提高,作为先进制造技术的重要组成部分高速切削技术在模具加工制造中已得到越来越广泛的应用。
本文结合高速切削技术的发展现状,阐述了高速切削技术的应用及其未来趋势。
[关键词]:高速切削刀具数控加工应用中图分类号:tg659文献标识码:tg文章编号:1009-914x(2013)01- 0239-01一、高速切削技术和高速切削刀具目前,切削加工仍是机械制造行业应用广泛的一种加工方法。
其中,集高效、高精度和低成本于一身的高速切削加工技术已经成为机械制造领域的新秀和主要加工手段。
“高速切削”的概念首先是由德国的c.s~omom博士提出的,并于1931年4月发表了著名的切削速度与切削温度的理论。
该理论的核心是:在常规的切削速度范围内,切削温度随着切削速度的增大而提高,当到达某一速度极限后,切削温度随着切削速度的提高反而降低。
此后,高速切削技术的发展经历了以下4个阶段:高速切削的设想与理论探索阶段(193l—l971年),高速切削的应用探索阶段(1972-1978年),高速切削实用阶段(1979--1984年),高速切削成熟阶段(20世纪90年代至今)。
高速切削加工与常规的切削加工相比具有以下优点:第一,生产效率提高3~1o倍。
第二,切削力降低30%以上,尤其是径向切削分力大幅度减少,特别有利于提高薄壁件、细长件等刚性差的零件的加工精度。
第三,切削热95%被切屑带走,特别适合加工容易热变形的零件。
第四,高速切削时,机床的激振频率远离工艺系统的固有频率,工作平稳,振动较小,适合加工精密零件。
高速切削刀具是实现高速加工技术的关键。
刀具技术是实现高速切削加工的关键技术之一,不合适的刀具会使复杂、昂贵的机床或加工系统形同虚设,完全不起作用。
由于高速切削的切削速度快,而高速加工线速度主要受刀具限制,因为在目前机床所能达到的高速范围内,速度越高,刀具的磨损越快。
先进刀具使用现状及未来发展方向

先进刀具使用现状和未来发展方向摘要:制造业开始致力于发展适用于各种特定加工条件的现代高效刀具,来代替传统的千篇一律的标准刀具。
这种新的发展战略首先在汽车行业取得了巨大效果,并迅速推广到各行各业。
20多年来,“高精度、高效率、高可靠性和专用化”的现代高效刀具取代传统的标准刀具,成为发达国家工具工业发展的主流。
关键词:高效刀具;现代刀具;发展趋势1 现代高效刀具和工具工业的发展特点1.1 现代高效刀具的内涵现代高效刀具是相对传统标准刀具而言的。
传统的工具工业以生产供应标准化、通用化的刀具为基本特点。
长期以来,制造业有一种共识:除了少量特殊需要,尽量选用标准刀具。
标准刀具虽然性能不是最优,但因经济实用而被广泛接受。
但到20多年前,这种观念在发达国家开始发生变化。
产生这种变化的背景:第一,经济全球化的发展使制造业面临日益剧烈的竞争,提高效率、降低成本的压力空前加大;第二,全球性的资源、能源短缺和环境问题迫使制造业走上一条“高效、低耗、节能、环保”的发展道路;第三,信息技术推动了数字化制造技术的发展,为提高生产效率提供了物质基础。
在这种背景下,全球制造业都在千方百计地为“降低成本、提高效率”进行不懈的努力。
在这个过程中,人们愈来愈认识到,尽管传统的标准化刀具价格很低,采购和管理也十分简单,但它的通用性却使加工效率大大降低,这是一个致命的缺点。
于是制造业开始致力于发展适用于各种特定加工条件的现代高效刀具,来代替传统的千篇一律的标准刀具。
这种新的发展战略首先在汽车行业取得了巨大效果,并迅速推广到各行各业。
20 多年来,“高精度、高效率、高可靠性和专用化”的现代高效刀具取代传统的标准刀具,成为发达国家工具工业发展的主流。
从字面上来理解,现代高效刀具就是性能好、效率高、质量过硬的刀具,但是这种理解是不够全面的。
可将现代高效刀具归纳为“高精度、高效率、高可靠性和专用化”,关键是“专用化”。
“专用化”就是针对用户特定需要,提供一整套高效率的加工方案。
新型陶瓷刀具在不锈钢切削加工中的应用研究
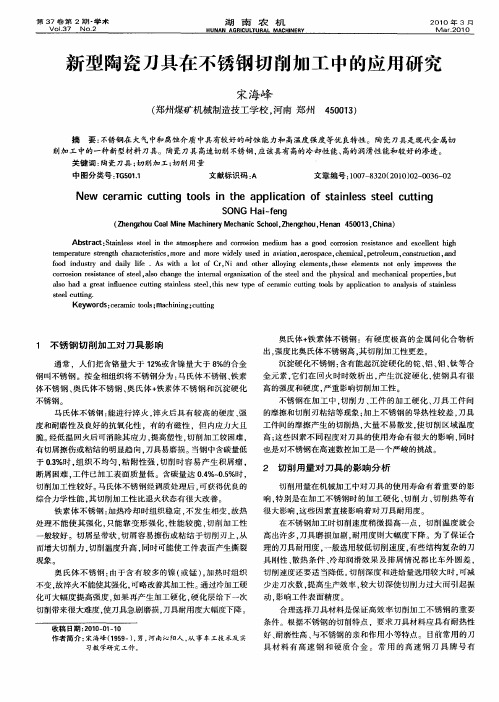
摘 要: 不锈钢在 大 气中和腐蚀介质 中具有较好 的耐蚀 能 力和高温度 强度等优良特性。 陶瓷刀具是现代金属切 削加 工 中的一种新型材料 刀具。陶瓷 刀具 高速切削不锈钢 , 应该具有 高的冷却性能、 高的润滑性 能和较好 的渗透。
关键词 : 陶瓷 刀 具 ; 削加 工 ; 削 用量 切 切
fo idusr a d al lf . As t a o o , a ohe lo ig ee e t ,h s lm e t n t n y m p o e he od n ty n d iy i e wi h lt f Cr Ni nd t r al yn lm n s t e e e e ns o o l i r v s t c ro in r ssa c fse l as h n e t e i e n  ̄anz to ft e se la d t hy ia nd me h nia r p r e bu o r so e itn e o te ,lo c a g h ntr a o l ia in o h te n he p sc la c a c lp o t s, t e i as a r a n u nc ut n t ne s se l t i e tp fc rm i utng to s b p lc i n t nay i fs il s lo h d a g e tif e e c t g sails t e ,hs n w y e o ea c c t l i i o l y a piato o a lss o t n e s a se lc t . te ut ng i
Ke wo d :e a c to ; c ii g c t n y r s c r mi l ma hn n ; u t g os i
新型金属陶瓷刀具在干切削中的应用

质 合 金 刀 片 基 本 类 似 , 采 用 液 相 烧 结 法 。 中 混 合 粉 都 其
末 的 均 匀 混 合 与 刀 坯 烧 结 是 其 中 两 个 最 为 关 键 的 步
骤 。
( ) 米 TN 对 TC 基 金 属 陶 瓷 微 观 组 织 的 影 响 3纳 i i 经 上 述 工 艺 制 作 而 成 的 纳 米 金 属 陶 瓷 刀 片 与 未 加 纳 米 Ti 的 金 属 陶 瓷 刀 片 的 显 微 结 构 的 扫 描 电 镜 照 片 分 N
TC基 金 属 陶 瓷 是 ห้องสมุดไป่ตู้ 世 纪 7 i 0年 代 在 W C —C o基 硬
⑦ 在 真 空 炉 中将 刀 坯 烧 结 成 金 属 陶 瓷 刀 具 。 结 烧
刀 坯 是 整 个 制 作 过 程 的 关 键 , 空 炉 中 的 真 空 度 、 结 真 烧
质 合 金 基 础 上 发 展 起 来 的 新 型 硬 质 合 金 , 常 把 Ni 通 粘 结 的 Ti 基 硬 质 合 金 称 为 金 属 陶 瓷 。 晶 粒 结 构 是 保 C 细 证 金 属 陶 瓷 材 料 高 强 度 与 优 良 力 学 性 能 的 基 础 , 以 所 在 纳 米 材 料 制 造 技 术 有 了 一 定 发 展 的 前 提 下 , 用 纳 采 米 级 细粉 制造 高性 能 材 料成 为材 料 研究 的方 向之一 。 ( ) 米金 属 陶 瓷 刀具 成 分 1纳 纳 米 金 属 陶 瓷 刀 具 成 分 为 : 3 I 一 1 Ti n 5 TC 0 N( m)一 1 Mo一 1 Ni 1 ,T N 8 8 一 C i 纳 米 粉 粒 度 为 3 ~5 n 。 验 研 究 表 明 , 力 学 性 能 0 0m 实 各 的 峰 值 分 别 对 应 一 定 的 纳 米 TN 的 添 加 量 。 添 加 量 i 当
- 1、下载文档前请自行甄别文档内容的完整性,平台不提供额外的编辑、内容补充、找答案等附加服务。
- 2、"仅部分预览"的文档,不可在线预览部分如存在完整性等问题,可反馈申请退款(可完整预览的文档不适用该条件!)。
- 3、如文档侵犯您的权益,请联系客服反馈,我们会尽快为您处理(人工客服工作时间:9:00-18:30)。
1 论文题目 新型数控刀具材料的创新设计对提高企业效益的影响
所在学院 机电工程学院 专 业 机械电子工程 年 级 10级 学生姓名 邓方兴 学 号 102261013005
2011年11 月11日 2
新型数控刀具材料的创新设计对提高企业效益的影响 [摘 要] 刀具材料的进步极大的推动着人类社会文化和物质文明的发展。就世界范围来看,数控机床的应用越来越广,数控加工技术代表了现代切削加工技术的发展方向,而切削加工技术的进步与数控机床刀具材料的发展和应用密不可分,只有把数控机床和数控刀具材料结合起来,才能充分发挥数控加工技术的潜力,也是推动企业技术进步及提高市场竞争实力的有效手段。 [关键词] 数控机床 刀具 材料 创新设计 效益
数控刀具是指与先进高效的数控机床相配套使用的各种刀具的总称,是数控机床不可缺少的关键配套产品。数控加工刀具以其高效、高速、耐磨、长寿命和良好的综合切削性能取代了传统的刀具,已逐步标准化和系列化。近年来,快速发展的数控加工促进了数控刀具的发展。每当一种新型数控刀具产品问世,都会使数控加工技术跃上一个新台阶,产生巨大的经济和社会效益。世界各国都十分重视数控刀具的研究开发。
一、数控刀具材料的新发展 进入21世纪以来,随着制造技术的全球化趋势,制造业的竞争更加激烈,对制造技术必然带来巨大的挑战,首当其冲的是切削刀具的变化,为了适应高精化、高速化、自动化、多功能化、高生产率化,缩短交货期等要求,要求切削刀具材料的强度和韧性要高,具有寿命长、高可靠、耐高温、耐破损、抗氧化和抗冲击等特点。特别为了适应当前对环境保护的要求,提出了条件苛刻的干式切削。切削刀具的设计和制造等方面日新月异,不断推陈出新。数控刀具材料的发展主要体现在刀具的切削性能大幅度提高以适应各项切削技术要求。数控刀具的分类有多种方法,按刀具材料分类有金刚石刀具、立方氮化硼刀具、陶瓷刀具、硬质合金刀具、涂层刀具。超细晶粒硬质合金、粉末冶金高速钢刀具等。 1.超硬刀具 超硬材料是指人造金刚石和立方氮化硼(简称CBN),以及用这些粉末与结合剂烧结而成的聚晶金刚石(简称PCD)和聚晶立方氮化硼(简称PCBN)等。超硬材料的出现,不仅在高速切削上起到了突破性的作用,更重要的是能够适应了较难加工材料的切削需要。 (1)聚晶金刚石(PCD)刀具 聚晶金刚石(PCD)刀具是通过金属结合剂等金刚石微粉末聚合而成的多晶体材料,在烧结过程中由于结合剂的加入,使PCD晶体间形成以Co、Mo、W、WC和Ni等为主要成分的结合桥,其作用是牢固的把持金刚石,并且使PCD硬度和韧性大幅度提高,增加耐性、提高切削效率。由于天然金刚石价格昂贵、在很多场合下天然金刚石刀具已经被人造聚晶金刚石刀具所代替。PCD刀具是精密加工有色金属及其合金、陶瓷、玻璃材料、石墨等非金属材料的最佳刀具。目前铝合金等产品零件已经无法离开这类刀具。 (2)CVD金刚石渡膜涂层刀具 CVD金刚石是指用化学气相沉积法在异质基体上合成金刚石膜,基体材料可以是硬质合金或陶瓷等。CVD金刚石具有与天然金刚石完全相同的结构和特性。具有超硬耐磨性和良好的韧性。目前,CVD金刚石渡膜涂层数控刀具多用于航空、航天、汽车及电子信息技术行业。对于高强度铝合金、纤维金属层板、镁合金、石墨、陶瓷等零部件进行加工,达到了高速、高寿命、干式加工技术要求。 (3)立方氮化硼(CBN)刀具与聚晶立方氮化硼(PCBN)刀具 3
立方氮化硼(CBN)是自然界中不存在的物质,有单晶体和多晶体之分,既CBN单晶和聚晶立方氮化硼(PCBN)。CBN是氮化硼(BN)的同素异构体之一,由于CBN与金刚石在晶体结构上的相似性,决定了它与金刚石相近的硬度,又具有高于金刚石的热稳定性和对铁元素的高化学稳定性。PCBN是在高温下将微细的CBN材料通过TiC、TiN、AL、Ti等结合相烧结在一起的多晶体材料,是目前利用人工合成的硬度仅次于金刚石刀具材料,它与金刚石统称为超硬刀具材料。不同CBN含量的PCBN数控刀具,可用于车、镗、铣、铰、复合孔等加工过程以及某些较难加工材料,被加工材料的硬度越高越能体现PCBN刀具的优越性。 2.新型陶瓷刀具材料 陶瓷刀具是最具有发展潜力的数控刀具之一。 (1)梯度功能陶瓷刀具 梯度功能陶瓷刀具是指组分、结构和物理力学性能呈合理梯度变化的陶瓷刀具,其主要目的是缓解陶瓷刀具在切削过程中刀具内的机械应力、热应力,提高抗震性和可靠性。梯度功能陶瓷刀具的物理力学性能和可靠性比普通均质陶瓷刀具有大幅度的提高,而且速度越高提高越显著。山东大学采用湿法工艺分散混料、粉末叠层填充、轴向热压烧结工艺,研究开发成功两种梯度功能陶瓷刀具材料FG-1和FG-2。切削试验结果表明:FG-1抗磨损和破损能力比组分相同的均质陶瓷刀具提高30%~50%。FG-2在切削淬硬工具钢T10A时刀具寿命比组分相同的均匀陶瓷刀具提高50%~100%。 (2)陶瓷—硬质合金复合刀片 陶瓷—硬质合金复合刀片是指将陶瓷和硬质合金通过烧结的方法结合在一起而得到的新型刀具材料,复合刀片的表层为陶瓷材料,下层或中层为硬质合金。它将陶瓷和硬质合金的优良性能结合起来,陶瓷—硬质合金复合刀片能承受更大的弯曲载荷。利用底层硬质合金与刀杆焊接,可以解决陶瓷刀具难焊接的问题。研究表明:复合刀片接口结合类型为化合物型和扩散型的混合,界面附近硬质合金中Co和W向陶瓷材料中扩散,陶瓷中的Ti向硬质合金中扩散,界面附近形成了Co3W3C、Al18B4O3和TiC几种新相,提高了界面结合强度。陶瓷—硬质合金复合刀片的抗弯强度可达800~1000Mpa,其抗破损能力比普通陶瓷刀具提高30%以上。 (3)粉末表面涂层陶瓷刀具 粉末表面涂层陶瓷刀具是指在硬质合金粉末表面涂层陶瓷制成复合粉末,然后将复合粉末热压制备成新型刀具。粉末表面涂层陶瓷刀具突破在刀具表面进行涂层的传统方法,变宏观涂层为微观涂层,解决了宏观涂层存在的易剥落崩碎等缺陷。这种涂层刀具既发挥了传统涂层刀具的优点又克服了其缺点,成为“新生代”涂层陶瓷刀具,其切削可靠性大大优于陶瓷刀具和刀片表面涂层刀具。 3.涂层刀具 涂层技术是将传统刀具涂覆一层或多层薄模,使刀具性能发生很大改变。涂层材料主要有:TiC、TiN、TiAlN、AlTiN、Al2O3、CrN、CrC、MoS2、WS2等。目前常用的刀具涂层方法有化学气相沉积(CVD)、物理气相沉积(PVD)、等离子体化学气相沉积(PCVD)、等离子喷涂及化学涂覆法等。涂层方式有:单涂层、多涂层、梯度涂层、软/硬复合涂层、纳米涂层、超硬薄膜涂层等。其中CVD和PVD被工业界广泛应用。刀具表面涂层技术极大地改善了数控刀具的切削性能,提高了切削效率,具有成本低见效快的特点。根据涂层刀具基本材料的不同,涂层刀具分为硬质合金涂层刀具、高速钢涂层刀具以及在陶瓷和超硬材料(金刚石和立方氮化硼)上的涂层刀具等。 目前各厂商在不断提高涂层工艺技术,各种新的涂层方法和涂层材料在不断出现,如纳米级超薄、超多层涂层等涂层材料,目的在于不断提高涂层结合牢度、耐磨性、耐热性和抗冲击韧性等。涂层将成为改善刀具性能的重要途径。 4
4.硬质合金刀具 硬质合金刀具是由硬度和熔点很高的碳化物:WC、TiC、TaC或NbC等和金属结构剂(Co、Mo、Ni等)经粉末冶金方法而制成的,其硬度远高于高速钢。金属结合剂含量越高,则抗弯强度越高。其中TiC(N)基硬质合金,其硬度接近陶瓷刀具的硬度水平,硬度一般达91-94HRA,抗弯强度比陶瓷刀具材料高得多,故将其称为金属陶瓷。硬质合金是脆性材料,常温下其冲击韧性仅为高速钢的1/30~1/8。晶粒细化后,细和超细硬质合金刀具,不但可以提高其硬度、耐磨性、抗弯强度和抗崩刃性,其高温硬度也将提高。我国一些硬质合金企业对超细硬质合金已实现了批量生产,可以大幅度提高切削速度,用于难加工材料的加工。
5.高速钢刀具 高速钢是一种加入了较多W、Mo、Cr、V等合金元素的高合金工具钢。其刀具在强度、韧性及工艺性等方面具有优良的综合性能,在复杂刀具,尤其是制造孔加工刀具、铣刀,螺纹刀具等一些刃形复杂刀具,高速钢仍占据主要地位。由于高速钢刀具中W、Co等主要元素资源紧缺,在世界范围内日益枯竭,所以在所有刀具材料中的比重逐渐下降。那么高速钢刀具的发展方向是:发展各种少W的通用型高速钢,扩大使用各种元素无Co、少Co的高性能高速钢。扩大使用各种粉末冶金高速钢和涂层高速钢刀具。 尽管高速钢刀具在全世界的销售量以每年约5%的数量在减少,但是高性能高速钢和粉末冶金高速钢的使用在不断增加。由于表面涂层技术的发展,在高速钢刀具表面PVD涂层TiN、TiCN、TiAIN后,切削速度可以进一步提高。随着人们对切削加工效率的追求和观念的转变,涂层高速钢刀具大量应用于轿车、摩托车、航空发动机、汽轮机等制造行业。在复杂数控刀具领域将会进一步发展而占有重要地位。 二、数控刀具材料的发展前景 随着科学技术的发展,对工程材料提出了越来越高的要求,各种新型航空航天材料、核能材料、复合材料、生物材料、功能材料、纳米材料、稀土材料、先进金属或非金属材料的应用日益广泛,工件材料的品种成倍增长。如此种类繁多,工件材料和刀具材料双方交替进展,相互促进。 涂层刀具材料在数控加工领域有着巨大的潜力,预计今后涂层刀具的应用将会进一步扩大。当前涂层发展的另一个特点是,各厂商都根据产品功能的需要,综合各种涂层的特点开发专用涂层牌号,涂层已成为刀具新产品开发的重要内容;从资源、价格和性能等方面看,陶瓷刀具具有很大优势,尤其是其资源优势。陶瓷刀具材料的主要成分在自然界是用之不竭的,因此,新型陶瓷刀具材料将会得到更大的发展;PCD刀具将继续在有色金属及其合金、非金属材料加工中占有主要地位;PCBN刀具将在黑色金属及其合金加工中占有主要地位,其应用会越来越广泛;超细晶粒的硬质合金和粉末高速钢在小尺寸整体复杂加工领域还将占主导地位;超强、超硬纳米刀具材料是最诱人的数控加工刀具材料、加速研究发展,很快有可能成为现实。同时针对工件材料品种成倍增长的趋势开发通用性好、适应性强,能够在多种条件下均能正常工作的刀具也是刀具业的发展方向。 环境污染已成为全世界共同关注的焦点,保护环境节约资源是人类发展的必然趋势。欧美等工业发达国家已清醒地认识到切削液对环境的危害,相继制定出严格的工业排放标准,进一步限制了切削液的使用。因此,开发具有高温自润滑功能的刀具材料进行高速干切削是一种环境效益和经济效益俱全的工艺选择。研发适应硬切削、干式切削和高速切削的高性能刀具材料是当前研究的热点。 三、结语 1.具有高速、高精度和高可靠性“三高”刀具的研究开发将是今后数控刀具材料研究开发的重点。