循环流化床分离器
循环流化床
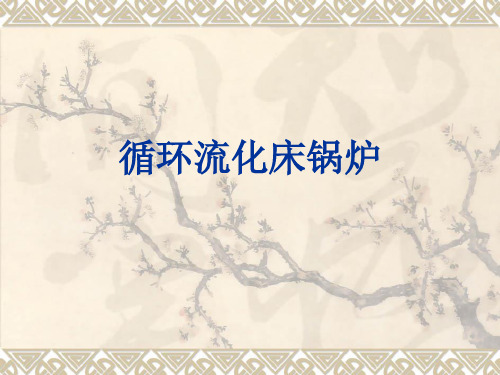
汽水系统流程
给水 省煤器 水 汽包 饱和蒸汽 汽水混合物 水冷壁
包墙
低温过热器
屏式过热器
合格品质的蒸汽
末级过热器
汽水系统
锅炉给水首先被引至尾部烟道省煤器进口集
箱两侧,逆流向上经过水平布置的省煤器管 组进入省煤器出口集箱,通过省煤器引出管 到锅筒。
省 煤 器 图
汽水系统
给水引入锅筒水室间,并通过集中下降管和
给煤系统
循环流化床锅炉的给煤系统和其燃烧系统的
特殊方式有关系,循环流化床锅炉一般都采 用密闭式皮带给煤机或刮板式给煤机。循环 流化床锅炉对入炉煤的粒径要求不太严格, 一般粒径在0~13mm均为合格。
煤仓 驱动电机 输送皮带 电子称
清扫刮板
密封风 落煤口
石灰石系统
为保证循环流化床锅炉的脱硫效 果,必须有专门的脱硫剂添加系 统。一般都采用石灰石脱硫剂。 因此都称为石灰石系统,其大致 流程如下图:
饱和蒸汽从锅筒引出后,由饱和蒸汽连接管引入汽冷式旋风 分离器入口烟道的上集箱,下行冷却烟道后由连接管引入汽 冷式旋风分离器下联箱,上行冷却分离器筒体之后,由连接 管从分离器上集箱引至尾部竖井侧包墙上集箱,下行冷却侧 包墙后进入侧包墙下联箱,由包墙连接管引入前、后包墙下 集箱,由包墙连接管引入前、后包墙下集箱,向上行进入中 间包墙下联箱,即低温过热器进口联箱,逆流向上对后烟道 低温过热器管组进行冷却后,从锅炉两侧连接管引至炉前屏 式过热器进口联箱,流经屏式过热器受热面后,从锅炉两侧 连接管返回到尾部竖井后烟道中的高温过热器,最后合格的 过热蒸汽由高温过热器出口联箱两侧引出。
过热器
低温过热器
烟风系统
从一次风机出来的空气分成三路送入炉膛。第一路,经一次风空气预热 器加热后的热风进入炉膛底部的水冷风室,通过布置在风板上的风帽使 其流化,并行向上通过炉膛的气固两相流;第二路,经过空气预热器的 冷风向冷渣器提供流化风,冷渣器出风作为二次风引到炉内;第三路, 热风经播煤增压风机后,用于炉前气力播煤,二次风机供风分为两路, 第一路经预热器后的二次风直接经炉膛上部的二次风箱分级进入炉膛。 第二路,一部分未经预热的冷二次风作为给煤皮带的密封用风。 烟气及其携带的固体粒子离开炉膛通过布置在水冷壁后墙上的分离器进 口烟道进入旋风分离器,在分离器里绝大部分物料颗粒从烟气中分离出 来,另一部分烟气则通过旋风分离器中心筒引出,由分离器出口烟道引 至尾部竖井烟道,从前包墙及中间包墙上部的烟窗进入前后烟道并向下 流动,冲刷其中的水平对流受热面管组,将热量传递给受热面,而后烟 气流经管式空气预热器进入除尘器,最后由引风机通过烟囱,排入大气。
循环流化床原理及运行

循环流化床原理及运行循环流化床主要由床体、循环器、气固分离器、换热器以及气体和固体的供给与排出系统等组成。
其工作原理是将气体和粗颗粒固体以较高的速度由床体底部引入,通过气固的强烈的接触,将反应所需的物质传递至固体表面,然后通过气体与粗颗粒固体的分离器将固体从气体中分离出来,然后再将固体颗粒经过循环器回流至床底,形成循环。
在循环流化床中,床体内的固体颗粒会被流化空气携带起来,在床体内形成一种类似于流体的状态。
床体中的气体通过气体分布板均匀地从底部引入,在床内形成均匀的气流。
当气体通过床体时,由于流体动力学的特性,固体颗粒被悬浮在气体中,形成浮动着的连续相。
在这种状态下,气体与颗粒之间的传质和传热效率大大提高,从而增加了反应的速率和效率。
循环流化床的运行过程可以分为固体颗粒的循环和气体的循环两个主要步骤。
在固体颗粒的循环过程中,气体通过固体颗粒床体将颗粒携带起来,并从循环器中回流至床底。
循环器中的固体颗粒经过多级分离装置的分离后,被分为两部分,一部分再次回流到床底,一部分从床体上部排出。
这样不断循环地将固体颗粒带到床体中,使床体保持一定的固体浓度。
在气体的循环过程中,气体从床体底部引入床体,通过床体上升,经过一定的高度后,在床上部进入气固分离器。
在气固分离器中,气体与固体颗粒进行分离,固体颗粒沉降至底部,而气体则从顶部排出。
排出的气体可根据需要进行再利用或者进行后续处理。
循环流化床具有很好的传质和传热性能,能够有效地控制反应的温度和反应速率。
由于固体颗粒的循环,床内固体颗粒的平均停留时间较短,减少了固体颗粒的积聚和结焦现象,延长了固体颗粒的寿命。
此外,循环流化床还具有较好的反应均匀性和操作灵活性,可广泛应用于化工、冶金、环保等领域。
总之,循环流化床通过将气体和固体颗粒进行高速流化,形成浮动着的连续相,以此来完成气体固体反应。
其原理是通过气体与固体颗粒之间的强烈接触和传质传热效果,实现反应的高效率和高速率。
循环流化床锅炉结构及工作原理介绍(2.2M)
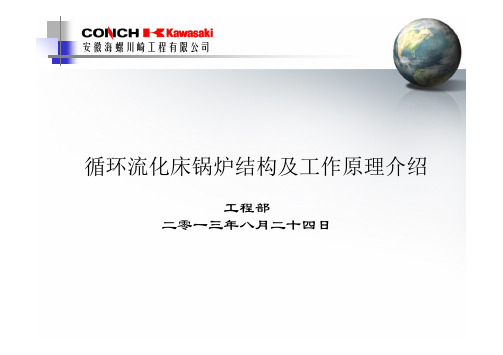
安徽海螺川崎工程有限公司循环流化床锅炉结构及工作原理介绍工程部二零一三年八月二十四日安徽海螺川崎工程有限公司循环流化床锅炉结构及工作原理介绍一前言二循环流化床锅炉的结构三循环流化床锅炉的工作原理四循环流化床锅炉的特点五自备电站项目设计注意事项安徽海螺川崎工程有限公司一、前言循环流化床燃烧技术是二十世纪七十年代末发展起来的高效低污染清洁煤燃烧技术。
循环流化床锅炉具有燃料适应性广、添加石灰石在炉内低成本脱硫、低温燃烧和分级送风有效降低氮的氧化物生成、低温燃烧形成的灰渣便于综合利用的优点,几十年来得到迅速发展。
安徽海螺川崎工程有限公司二、循环流化床锅炉的结构循环流化床锅炉大致可分成两个部分。
第一部分由炉膛(流化床燃烧室)、气固体分离设备(分离器)、固体物料再循环设备(回料器)等构成,上述形成一个固体物料循环回路;第二部分则为尾部对流烟道,布置有过热器/再热器、省煤器、空气预热器等,与常规煤粉炉相近。
安徽海螺川崎工程有限公司循环流化床锅炉的基本结构安徽海螺川崎工程有限公司典型循环流化床锅炉结构如上图所示,其基本流程为:燃烧所需要的一次风和二次风分别由炉膛的底部和侧墙送入,燃料的燃烧主要在炉膛中完成。
煤和脱硫剂送入炉膛后,迅速被大量惰性高温物料包围,着火燃烧,同时进行脱硫反应,并在上升烟气流的作用下向炉膛上部运动,对水冷壁和炉内布置的其他受热面放热。
粗大粒子进入悬浮区域后在重力及外力作用下偏离主气流,从而贴壁下流。
安徽海螺川崎工程有限公司气固混合物离开炉膛后进入高温旋风分离器,炉膛出口水平烟道内装有多级烟灰分离器,分离出的高温灰落入灰斗,由气流带出炉膛的大量固体颗粒(煤粒、脱硫剂)被分离和收集,通过返料装置(回料器)送入炉膛,进行循环燃烧。
未被分离出来的细粒子随烟气进入尾部烟道,以加热过热器、省煤器和空气预热器,经除尘器排至大气。
飞灰通过分离器经尾部烟道受热面进入除尘器经灰沟冲到沉灰池,床体下部已燃尽的灰渣定期排放。
循环流化床锅炉中旋风分离器的设计与探讨

粒, 旋风分离器都可以完全捕集 , 而后者对 d。 5 的颗粒
粒径 刚好 有 5 %被 捕 集 , 程上 常 采 用 d 。 进 行 设 0 工 来
Vo | I 3 No. 4
Oc . 2 07 t 0
循 环 流 化 床 锅 炉 中 旋 风 分 离 器 的 设 计 与 探 讨
黄新章 王永波 郑传 贵 徐 有宁 , , ,
( . 阳工程 学院 动力 工程 系 , 阳 1 0 3 ; . 宁科 林环保 工程 有限 责任公 司 , 阳 10 3 ; 1沈 沈 116 2 辽 沈 10 4
计l. 2 临界 分 离 粒 径 的 大 小 决 定 于 分 离 器 的结 构 尺 ] 寸 , 以应在满 足一 定分离 效率 的条件 下 , 算临 界分 所 计
离粒 径 , 临界分 离粒径 确定 后 , 根据 经验公 式来确 定 再
是 用分离器 的效 率和 压 损来 衡 量 、 中分离 效 率 高 低 其
关键 词 :旋 风 分 离 器 ; 离效 率 ; 分 临界 分 离粒 径 中 图分 类 号 :TO 5 0 文 献 标 识 码 :A 文 章 编 号 :17 —1 0 (0 7 0 6 3 6 3 2 0 )4—0 3 3 3—0 2
旋 风分离 器是 结构 简 单 、 易 制造 和 安装 的 常见 容 的化工设 备 , 在食 品 、 医药 、 日用化 工 以及 冶金 电力 等
为衡 量其好 坏 的最 主要 指标 , 即旋 风 分 离 器处 理 后 的
循环流化床

名词解释1、床料:流化床锅炉启动前,铺设在布风板上的一定厚度和一定粒度的固体颗粒,称作床料,也称点火底料。
床料一般由燃煤、灰渣、石灰石粉等组成,静止床料层厚度一般为350-600mm 。
2、物料:循环流化床锅炉运行中,在炉膛及循环系统(循环灰分离器、立管、送灰器等)内燃烧或载热的固体颗粒,称为物料。
它不仅包含床料成分,还包括新给入的燃料、脱硫剂、经循环灰分离器返送回来的颗粒以及燃料燃烧生成的灰渣等。
3、流化态:这种由于固体颗粒群与气体(或液体)接触时,固体颗粒转变成类似流体的状态称为流态化。
4、床层阻力特性:所谓流化床床层阻力特性,就是指流化气体通过料层的压降p ∆与按床截面计算的冷态流化速度u 0之间的关系,即所谓压降--流速特性曲线。
5、料层阻力:指燃烧空气通过布风板上的料层时的压力损失。
6、燃料筛分:燃料筛分是指燃料颗粒粒径大小的分布范围。
如果颗粒粒径粗细范围较大,即筛分较宽,就称作宽筛分;颗粒粒径粗细范围较小,就称作窄筛分。
循环流化床锅炉一般是宽筛分。
7、物料循环倍率:由循环灰分离器捕捉下来并返送回炉内的物料量(循环物料量)与新给入的燃料量之比,即B G R h=其中R--物料循环倍率;G h --循环物料量,即经循环灰分离器返送回炉内的物料量,kg/h ;B--新给入的燃料量或燃煤量,kg/h 。
用来反映物料循环的量化程度。
8、临界流化速度:将床料从固定床状态转变为流化状态(或鼓泡床状态)时,按布风板通流面积计算的空气流速称为临界流化速度u mf,即所谓的最小流化速度,它是流化床操作的最低气流速度,是描述循环流化床的基本参数之一。
9、燃料份额:指炉内每一燃烧区域中燃料燃烧量占燃料总燃烧量的比例,一般可用燃料在各燃烧区域内所释放的热量占燃料总发热量的百分比表示。
循环流化床锅炉燃烧主要发生在密相区和稀相区,炉膛内这两个燃烧区域的燃烧份额之和接近于1.密相区燃烧份额是一个重要参数。
10、颗粒终端速度:固体颗粒在静止空气中作初速度为零的自由落体运动时,由于重力的作用,下降速度逐渐增大,速度越大,阻力也就越大。
旋风分离器前期设计知识
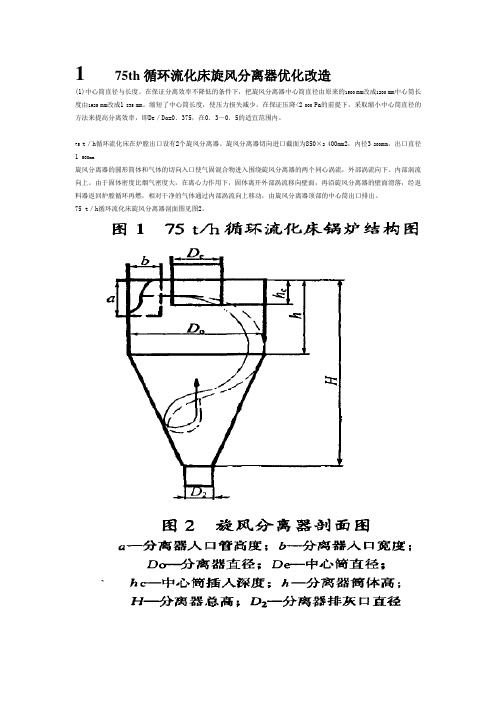
1 75th循环流化床旋风分离器优化改造(1)中心简直径与长度。
在保证分离效率不降低的条件下,把旋风分离器中心简直径由原来的1500 mm改成1200 mm中心筒长度由1925 mm改成1 835 mm。
缩短了中心筒长度,使压力损失减少。
在保证压降<2 000 Pa的前提下,采取缩小中心筒直径的方法来提高分离效率,即De/Do=0.375,在0.3~0.5的适宜范围内。
75 t/h循环流化床在炉膛出口设有2个旋风分离器。
旋风分离器切向进口截面为850×2 400mm2,内径3 200mm,出口直径1 500mm旋风分离器的圆形简体和气体的切向入口使气固混合物进入围绕旋风分离器的两个同心涡流,外部涡流向下。
内部涡流向上。
由于固体密度比烟气密度大,在离心力作用下,固体离开外部涡流移向壁面,再沿旋风分离器的壁面滑落,经返料器返回炉膛循环再燃,相对干净的气体通过内部涡流向上移动,由旋风分离器顶部的中心筒出口排出。
75 t/h循环流化床旋风分离器剖面图见图2。
影响旋风分离器分离特性的因素主要是旋风分离器的结构参数、粉尘的物理性质和分离器的运行参数,如切向进口风速、烟气温度、粒径、进口颗粒浓度、切向进口宽度和进口形式、中心筒长度和直径、固体的再夹带等。
由于旋流在中心筒与壁面之间运动,因此,中心筒的插入深度直接影响旋风分离器性能。
有研究表明,筒长度对分离效率的影响(见图3)是:中心简长度增加,分离效率提高,当中心筒长度大约是人口管高度的0.4~O.5倍时,分离效率最高,随后分离效率随着中心筒长度增加而降低。
因此,中心筒过短或过长都不利于分离,因为中心筒插入过深会缩短其与锥体底部的距离,增加二次夹带机会;而插入过浅,会造成正常旋流核心弯曲,甚至破坏,使其处于不稳定状态,同时也容易造成气体短路而降低分离效率。
另外,中心筒长度对压力损失也有影响(见图4)。
中心筒的压力损失主要是筒内摩擦损失,气体因同时进行旋转运动和直线运动需要消耗更多的能量,筒内气体静压能的损失转化为旋转时的动能。
旋风分离器发展及工作原理

旋风分离器发展及工作原理摘要:综述了旋风分离器的发展概况,并从气体、粉尘运动的工作原理以及分类等方面介绍了。
一、旋风分离器的发展旋风分离器的应用已有近百年的历史,因其结构简单,造价低廉,没有活动部件,可用多种材料制造,操作条件范围宽广,分离效牢较高,所以至今仍是化工、采矿、冶金、机械、轻工等工业部门里最常用的一种除尘、分离设备。
随着工业发展的需要,为使旋风分离器达到高效低阻的目的,自1886年Morse的第一台圆锥形旋风分离器问世以来百余年里,由于分离器的结构、尺寸、流场特性的不同,出现了许多不同用途的旋风分离器,现从两个方面来进行概述。
1.气体、粉尘运动的研究旋风分离器内颗粒流体的流动属于稀浓度颗粒流体力学,故可先分析纯气体流场,再计及颗粒在其中的运动。
在1949年,TerLinden研究得出切向速度轴对称分布,在同一断面随其与轴心的距离减小而增大,达到最大值后又逐渐减小;径向速度在中心区方向朝外,在外围区方向朝内,形成源汇流;轴向速度在外部区域气流向下,在轴心区域气流向上;压力分布是壁面处大于中心处。
1962年,Lewellen把不可压缩流体的连续性方程和Navier-stokes方程在圆柱坐标系和轴对称定常流动下进行了简化,通过引入流函数和环量,得到了强旋转简化层流模型。
1975年Bloor、Ingham运用普朗特提出的混合长理论确定湍流表观粘度,并对水力旋流器流场进行了分析,建立了适合于工程应用的初级湍流模型。
1982年Boysan等人利用Rodi推得的关于雷诺应力的近似代数关系式,得到了高级湍流模型。
用这些模型计算得到的切向速度数值解与实验测定结果较吻合。
2.旋风分离器内气固流况的剖析通过对旋风分离器内气固流况的剖析,针对影响旋风分离器效率的顶部上涡流和下部的二次带尘,影响动力消耗的进口膨胀损失和出口旋转摩擦等因素,人们进行改进。
为了消除因上涡流而引起粉尘从出口管短路逃逸的现象,Cardiff 大学的Biffin等人研制的新型带集涡室的旋风分离器、德国西门子公司顶端带导向叶片的旋流分离器、日本专利多头切向进口的多管分离器,以及国内的倾斜螺旋形进口的CLT/A、CLG、DⅠ型等也都是为了削弱上涡流的带尘。
分宜100MW循环流化床锅炉旋风分离器分离效率的计算

和可靠的计算方法。 江西分宜发电有限责任公 司 10M C B锅 0 W F 炉 由西安热工研究院有限公司与哈尔滨锅炉厂有 限责任公司联合开发 , 国产首 台具有 自主知识 是 产权 的大型 C B锅炉…。该锅炉原设计煤种为 F
收稿 日期 :05 1 3 20 一l —2
作者简介 : 王智微 ( 7 一)清华大学工学硕士, 10 。 9 从事循环流化床 锅炉和 电站控制系统 的研究开发, 发表论文五十余篇。 已
分离器分离效率的工程计 算方 法进行了研究。在热态试验条件下 通过直接测量物料浓度进 行分离器分 离效 率的计算是很 困难的 , 同时该方法还需要辅 以分离器进 出 7物料粒径分布 的测量 , 1 在数据 处理和数据精度 上
都存在 问题 。为此从工程应用 的角度出发 , 通过炉膛压力计算 分离器人 口烟气携 带的物料浓度 , 采用物料 平
出 口的压差可以计算出分离器人 口烟气携带的物 料浓度 , 即:
p = AP | x 1
分宜发 电有限责任公司 1 W F 锅炉机组完 0 M CB 0 成 35 . 亿度发电任 务。2O O4年发 电 5 3 . 亿度 , 累
维普资讯
第1 期 26 3 O 年 月 O
锅
炉
制 造
No. 1 Ma . O 6 r2 0
B ⅡER MA F r R 、 O NU AC U Ⅱ『 G
文章 编号 :N 3 2920 ) 1 0 1 3 C 2 —14 (06 0 —00 —0
维普资讯
-
2・
锅
炉 制
造
总第 19 9 期
分 宜 10 W F 0M C B锅 炉于 20 03年 6月通 过 7 2
- 1、下载文档前请自行甄别文档内容的完整性,平台不提供额外的编辑、内容补充、找答案等附加服务。
- 2、"仅部分预览"的文档,不可在线预览部分如存在完整性等问题,可反馈申请退款(可完整预览的文档不适用该条件!)。
- 3、如文档侵犯您的权益,请联系客服反馈,我们会尽快为您处理(人工客服工作时间:9:00-18:30)。
循环流化床分离装置摘要:气固两相流中的气固分离气固分离器是循环流化床锅炉的关键部件,循环流化床锅炉采用高温气固分离还是中温气固分离是一个复杂的技术经济问题,气固分离器需要满足下述要求才能被循环流化床锅炉采用:(1)能有效地连续工作;(2)适应颗粒浓度变化;(3)具有较低的运行阻力和较高的分离效率。
气固分离器在循环流化床中起着重要作用。
它用在循环流化床锅炉中不同位置,则起着不同作用。
用于循环流化床锅炉主循环回路的气固分离器主要有旋风分离器、惯性分离器两类。
关键字:旋风分离器、高温方形分离器、惯性分离器、组合分离器、分离器的性能指标、分离器的影响因素引言:在循环流化床锅炉里,通常将分离器布置在锅炉炉膛出口,以便将高温烟气流中的热固体物料分离下来进入回料斗,再通过回料阀进人炉膛继续循环,以便保证炉膛内一定的灰浓度同时也提高了锅炉的燃烧效率。
由于旋风筒是装在炉膛出口,烟温较高,锅炉满负荷运行时,炉膛出口温度一般为800~850摄氏度,因此旋风简要求由耐热材料制作这就是常说的高温温旋风分离器。
除在炉膛出口安装旋风筒的布置方式外,也可采用过热器、再热器、省煤器之后布置旋风筒的半塔式布置,此处烟温较低,一般400~450左右摄氏度,这就是常说的中温旋风分离器。
采用中温旋风分离,可以减少分离器体积和避免分离器在高温下的恶劣条件。
旋风分离器的缺点是体积大,造价高。
惯性分离器多采用耐温耐磨的非金属材料作成,组合成特殊烟气通道,安装在循环流化床锅炉出口,烟气流通过分离器各内壁时,固体颗粒被分离下来进入料斗再通过回料阀,将分离下来的固体颗粒返回炉膛进行循环。
与旋风分离器相比,这类分离器体积较小,适合于循环流化床锅炉整体化,但通常分离效率不佳,需要串联一个效率更高的分离器作为性能补偿。
循环流化床燃烧技术兴起之前,气固分离技术广泛应用于化工、冶金、建材、医药等工业领域,在电力行业则着重于煤粉炉或层燃炉的烟气除尘。
与循环流化床锅炉分离器不同的是,前者的目的是净化烟气,尽可能降低粉尘排放,其所处理的流动介质(烟气)一般含尘浓度不高(大多小于0.1kg/m3),温度较低(小于200。
C),粉尘粒度较细微(多在15/tm以下);循环流化床锅炉分离器的目的是分离、收集循环灰,注重物料的顺畅流动与可靠回送,所处理的两相流烟气介质固体成分含量非常高(约为2~5kg/Nm3或更高),温度比较高(一般约为850。
C),固体颗粒粒度分布也很宽(从几近零微米至几百微米)。
所有这些差异使得循环流化床锅炉气固分离技术有自己的独特性。
多年来,借鉴烟气除尘器和化工用分离器的设计、运行经验,众多电力设备生产商开发出了多种多样的循环流化床锅炉气固分离器。
下面按一般习惯对其作分类介绍一、气固分离器的分类用于气固分离的分离器种类非常多,按不同的分离机理、工作环境等有不同的分类方法。
如按工作温度不同可分为高温分离、中温分离、常温分离和低温分离;按排灰的情况可以分成干式和湿式。
最常见的分类是按作用力的情况分成四大类:机械力分离、静电分离、过滤分离和湿法分离。
机械力分离中主要包括重力沉降、惯性力分离、离心分离(主要有旋风分离器、旋转分离器等)。
循环流化床锅炉中最常用的是惯性分离器和旋风分离器。
(一)旋风分离器旋风分离器是目前在循环流化床燃烧技术领域应用最多的气固分离装置。
该装置最常见的型式由圆柱形旋流筒体和圆锥形加速段两部分构成。
两相流气体沿切向引入简体后主体部分以筒壁为边界作螺旋向下运动,此为外旋气流。
旋转产生的离心力使重度大于气体的固体颗粒脱离气体主流汇聚到筒壁,并在进VI动量和重力的作用下沿筒壁下滑至加速段.由其下口排出后经料腿、回灰阀等回送到炉膛。
旋转下降的外旋气流到达锥体后受圆锥形壁面制约而向分离器中心收缩,由于旋转矩不变,故其切向速度不断提高。
当气流到达锥形加速段下端某一位置时,开始以同样的旋转方向反弹上升,继续作螺旋形流动,形成内旋气流。
失去所携固体成分的内旋气流经排气芯管离开分离器,少部分未被捕集的细小颗粒也随之逃逸。
旋风分离器内实现气固分离的气体运动可以分为切向速度和径向速度。
通常测量旋风分离器内部特性时还要包括全压和静压分布。
(1)切向速度口切向速度主导着气固分离。
排气管以下任一截面切向速度沿着半径方向的变化可分为三个区,靠近器壁的I区内切向速度为常数,称为自由旋流区。
该区中:式中Ui——进口速度;Fi——旋风分离器进口截面积;D。
——排气筒直径;De ——分离器直径。
在分离器中心到具有最大切向速度处,v/r=常数vt/r=常数,在这两个区之间,vt/rn=常数式中,r指半径,n称为速度分布指数,一般在0.5~0.9之间。
n=1一(1—0.668Doo 14)(T/283)o·3径向速度理想条件下,平面旋转流可近似看作平面势流与平面点汇组成假设径向速度分布均匀就有: (2—3)式中q——进人分离器的气体流量;H—半径为r的理想圆柱高;分离效率和分离器阻力气固分离器效率定义为分离器捕集的颗粒量与进入分离器颗粒量之比。
为进一步表明分离器的工作能力,引进分级效率的概念。
分级效率是分离器对某一尺寸颗粒的分离效率,两者之间有循环流化床锅炉有一个特殊定义的参数——循环倍率。
在其类型锅炉上,循环倍率是一个工质循环方面的概念,而在循环流化床锅炉上,循环倍率R指的是单位时问经过气固分离器送回炉膛的颗粒量与给煤量的比值。
因此,气固分离器的分离效率是一个与循环倍率紧密关联的参数。
气固分离器分离效率和循环倍率之间的关系可由下式表述分离器效率是一个十分重要的运行参数,它发生变化后,会相继影响到主颗粒循环回路中各处的颗粒尺寸分布、颗粒停留时间、燃尽程度、脱硫效果、运行床温,甚至锅炉负荷。
当一个分离器无法满足分离效率要求时,可以串联一个分离器,此时的分离效率为:分离器工作阻力是衡量分离器性能的重要参数,它取决于分离器结构和运行条件。
通常用离心分离原理经验公式表达用于循环流化床锅炉的旋风分离器处于高温状态工作,可以分为绝热型和冷却型两大类。
绝热型分离器最外层的壳体由钢板卷制而成,内衬由绝热材料和耐磨耐火材料组成,厚度一般为300mm。
分离器本身不吸热。
其特点是制造简单、初投资较低,但可靠性差、运行维修费用高和冷态启动时间长。
冷却型又称为吸热型,分为水冷和汽冷两种。
壳体由蒸汽或水冷却的膜式壁组成,内衬仅为耐磨耐火材料,厚度一般为50mm。
绝热型分离器和冷却型分离器的结构如图所示。
采用水冷时,分离器和炉膛的连接不需膨胀节;采用汽冷时,需要补偿热膨胀量较小的膨胀节。
其特点是制造复杂、造价较高,但运行可靠,冷态启动时间短、效率高,寿命长。
给出了绝热型和冷却型分离器的技术特点比较有人将绝热型分离器称为第一代,冷却型分离器称为第二代,而将方形分离器称为第三代圆筒形高温旋风气固分离器典型的高温气固分离器包括旋风分离器(绝热式和冷却式)和惯性分离器。
旋风分离器是利用离心原理进行气固分离的装置,主要分为高效分离器和大流量分离器两大类。
在结构上主要分为长锥体、圆筒体、扩散式和旁通型。
分离器的主要结构尺寸如图2-3和表2-5所示。
投人运行的循环流化床锅炉的旋风分离器的主要工作特性包括入口颗粒浓度、入口颗粒尺寸及其分布、d50 d90给出了已经投运的典型循环流化床锅炉使用的旋风分离器的定性尺寸和主要性能。
表2-6循环流化床锅炉旋风分离器性能旋风分离器与循环流化床锅炉炉膛匹配是一个重要的几何和锅炉性能要求。
图2—4和表2-7给出了旋风分离器与锅炉炉膛之间的配合。
影响分离器工作性能的因素包括:简体直径、进口风速、烟气温度、颗粒尺寸、颗粒浓度、进口通道结构和尺寸绝热式高温气固分离器存在以下几个问题:一是绝热结构使得未燃可燃物可以在分离器中继续燃烧,通常不希望分离器受到结焦的威胁;二是保温层厚度较厚,要求锅炉的启动时间较长,且保温材料容易脱落,体积庞大,支架的钢材消耗量较大。
为克服这些问题,FosterWheeler公司设计了冷却式旋风分离器(水冷或汽冷)。
冷却式旋风分离器结构复杂、制造困难、成本高,除了大型循环流化床锅炉外采用的比较少。
循环流化床锅炉所使用的主要是旋风分离器。
除此之外,根据结构特点和整体布置的不同,旋风分离器还有其它的型式,如卧式旋风分离器、下排气旋风分离器等等,这些分离器多为专利。
方形高温气固旋风分离器方形高温分离器可以是正方形、矩形或多边形结构。
由于采用较多的是正方形,故称为方形分离器。
采用冷却结构时可以大大降低制造困难和制造成本。
方形分离器有一个单独定义的参数——圆形度,其定义为:方形分离器的结构如图2-5所示,主要结构参数有8个,分别是:人口高度(n)和宽度(b)、特征尺寸(D)、直段高度(h)、总高度(H)、芯筒直径(d)、芯筒插入深度(s)和排灰口宽度(B)。
旋风分离器设计旋风分离器是典型的气固分离设备,应用最多的是低温气固分离。
循环流化床锅炉的旋风分离器在高温条件下工作,按照低温设计的旋风分离器的性能会发生很大变化。
高温工作时,旋风分离器有如下特点:(1)采用较短的涡旋导向管;(2)螺旋人口优于切向人口;(3)雷诺数太高分离效率会下降;(4)为返料方便,分离器直段通常较短。
为满足这些特殊要求,在运行阻力和分离效率适当折中的条件下,可按下述步骤设计循环流化床锅炉的旋风分(1)入口气体速度:(2)按下式计算旋风分离器的直径:式中q——气体流量;N——分离器个数。
(3)按表2-8确定相关尺寸。
(4)计算分离器的下锥角。
(5)校核分离器下部立管直径,保证返料量:返料量=2.29×立管中固体的表观密度×/立管直径(6)计算沉降速度,检查是否有再夹带。
旋风分离器的颗(7)按图选取旋转圈数Ⅳc,用下式计算颗粒的切割直径d引(8)按图选取某一粒径颗粒的分离效率,颗粒浓度的影响按图进行修正。
总的分离效率都是采用经验公式或实验结果确定。
(二)惯性分离器惯性分离器是利用某种特殊的通道使介质流动的路线突然改变,固体颗粒依靠自身惯性脱离气体轨迹从而实现气固分离。
这种特殊通道可以专门设计成型(如S型分离器、U刑外套装、十b可以诵1叶布谢墙丰元件央空瑚f加槽珏!J 分离器、百叶窗分离器)。
型分离器),也可以通过布设撞击元件来实现(如槽型分离器、百叶窗分离器)。
惯性分离器结构简单,布置方便,与锅炉匹配性好,热惯性小,流动阻力一般也不高。
缺点主要是分离效果欠佳,特别是对惯性小、跟踪性好的细微颗粒捕集效果差。
因此,在循环流化床锅炉中几乎不可能利用单独的惯性分离器来满足工程要求。
目前惯性分离器主要作为预分离装置应用于小型循环流化床锅炉,或改进型鼓泡流化床锅炉。
(三)组合分离器组合式分离器不是一个单独的分离装置,它常由二级甚至三级分离器串联(有时还有并联)布置而成。