循环流化床锅炉旋风分离器改造
流化床锅炉旋风分离器施工工法
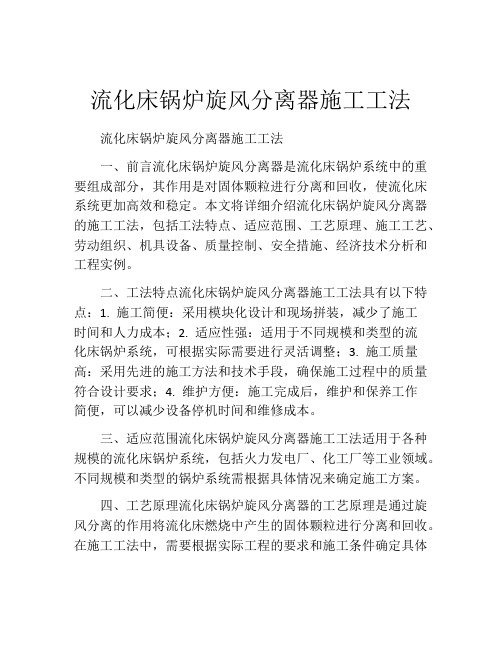
流化床锅炉旋风分离器施工工法流化床锅炉旋风分离器施工工法一、前言流化床锅炉旋风分离器是流化床锅炉系统中的重要组成部分,其作用是对固体颗粒进行分离和回收,使流化床系统更加高效和稳定。
本文将详细介绍流化床锅炉旋风分离器的施工工法,包括工法特点、适应范围、工艺原理、施工工艺、劳动组织、机具设备、质量控制、安全措施、经济技术分析和工程实例。
二、工法特点流化床锅炉旋风分离器施工工法具有以下特点:1. 施工简便:采用模块化设计和现场拼装,减少了施工时间和人力成本;2. 适应性强:适用于不同规模和类型的流化床锅炉系统,可根据实际需要进行灵活调整;3. 施工质量高:采用先进的施工方法和技术手段,确保施工过程中的质量符合设计要求;4. 维护方便:施工完成后,维护和保养工作简便,可以减少设备停机时间和维修成本。
三、适应范围流化床锅炉旋风分离器施工工法适用于各种规模的流化床锅炉系统,包括火力发电厂、化工厂等工业领域。
不同规模和类型的锅炉系统需根据具体情况来确定施工方案。
四、工艺原理流化床锅炉旋风分离器的工艺原理是通过旋风分离的作用将流化床燃烧中产生的固体颗粒进行分离和回收。
在施工工法中,需要根据实际工程的要求和施工条件确定具体的技术措施和施工步骤。
例如,可以采用冷喷射或热喷射的方式对旋风分离器进行喷涂,以提高其耐磨性和防腐性。
五、施工工艺施工工艺包括预处理工序、分离器安装工序、连接管道工序等。
首先,需要进行现场勘察和土建准备工作,如制定施工方案、采购材料和设备等。
然后,根据施工图纸和设计要求,进行分离器的安装和连接管道的铺设。
最后,进行分离器的试运行和调试,以保证其正常工作。
六、劳动组织施工工法需要合理组织施工人员和设备,根据具体工地情况安排人员的工作任务和工作时间。
同时,需要建立施工管理团队,对施工过程进行监督和控制,确保施工质量和进度。
七、机具设备施工工法需要使用一些特定的机具设备,如起重机、焊接设备、喷涂设备等。
循环流化床旋风分离器防变形及结构优化
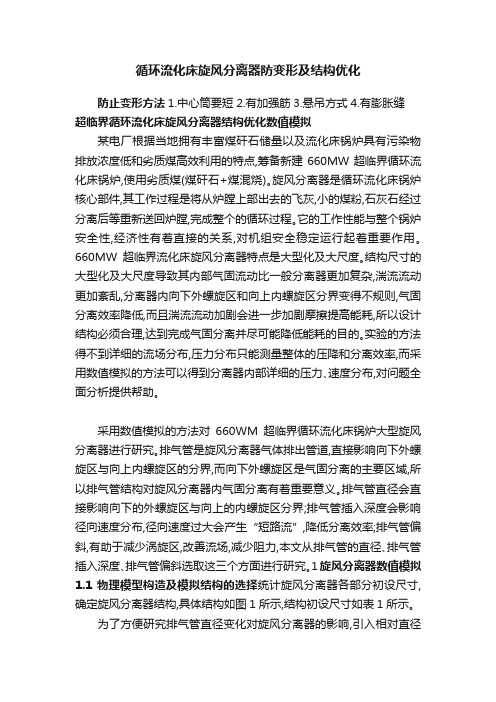
循环流化床旋风分离器防变形及结构优化防止变形方法1.中心筒要短2.有加强筋3.悬吊方式4.有膨胀缝超临界循环流化床旋风分离器结构优化数值模拟某电厂根据当地拥有丰富煤矸石储量以及流化床锅炉具有污染物排放浓度低和劣质煤高效利用的特点,筹备新建660MW超临界循环流化床锅炉,使用劣质煤(煤矸石+煤混烧)。旋风分离器是循环流化床锅炉核心部件,其工作过程是将从炉膛上部出去的飞灰,小的煤粉,石灰石经过分离后等重新送回炉膛,完成整个的循环过程。它的工作性能与整个锅炉安全性,经济性有着直接的关系,对机组安全稳定运行起着重要作用。660MW超临界流化床旋风分离器特点是大型化及大尺度。结构尺寸的大型化及大尺度导致其内部气固流动比一般分离器更加复杂,湍流流动更加紊乱,分离器内向下外螺旋区和向上内螺旋区分界变得不规则,气固分离效率降低,而且湍流流动加剧会进一步加剧摩擦提高能耗,所以设计结构必须合理,达到完成气固分离并尽可能降低能耗的目的。实验的方法得不到详细的流场分布,压力分布只能测量整体的压降和分离效率,而采用数值模拟的方法可以得到分离器内部详细的压力、速度分布,对问题全面分析提供帮助。采用数值模拟的方法对660WM超临界循环流化床锅炉大型旋风分离器进行研究。排气管是旋风分离器气体排出管道,直接影响向下外螺旋区与向上内螺旋区的分界,而向下外螺旋区是气固分离的主要区域,所以排气管结构对旋风分离器内气固分离有着重要意义。排气管直径会直接影响向下的外螺旋区与向上的内螺旋区分界;排气管插入深度会影响径向速度分布,径向速度过大会产生“短路流”,降低分离效率;排气管偏斜,有助于减少涡旋区,改善流场,减少阻力,本文从排气管的直径、排气管插入深度、排气管偏斜选取这三个方面进行研究。1旋风分离器数值模拟1.1 物理模型构造及模拟结构的选择统计旋风分离器各部分初设尺寸,确定旋风分离器结构,具体结构如图1所示,结构初设尺寸如表1所示。为了方便研究排气管直径变化对旋风分离器的影响,引入相对直径比:式中:De———排气管管径,m;D———圆柱分离段直径,m。排气管直径太大会使分离效率急剧降低,而太小会使总压差急剧上升,一般排气管相对直径比选取0.5,对于压差要求不大的可进一步缩小排气管直径来提高分离效率。选取模拟直径范围2.55m~4.25m,模拟尺寸选取2.55m~4.25m范围内典型尺寸2.55m、2.975m、3.4m、3.825m、4.25m,分别对应相对直径比0.3、0.35、0.4、0.45、0.5,其中4.25m是初设值。插入深度为3.6m,8.5m,10.1m分别对应排气管的底端在进气管底板以上,与进气管底板持平,在进气管底板以下这三种典型结构。选取这三个典型插入深度进行模拟,其中插入深度3.6m为初设值。排气管向涡旋区适量偏离,可以优化流场。旋风分离器初设排气管不进行偏置布置,为提高分离效率,降低总压差,对初设排气管结构进行设计优化。据文献,90°~180°方向紧靠排气管外壁会形成离体漩涡区。在偏置0°~180°方向之间选取典型偏置方向0°,45°,90°,145°,180°进行研究。模拟尺寸选取汇总表如表2所示。1.2 网格划分使用网格划分软件对构建好的个体进行网格划分,将旋分分离器分成3个子区域,分别是进气管段,排气管段和其他区域。分别对3个子区域进行网格划分。经过网格无关性检验,最终选取201287个网格个体的模型。具体网格划分如图2所示。其中进气管段与圆柱分离段连接处含有尖端易产生质量较差网格。先采用“撒种子”方法将进气管段上表面进行划分,然后采用cooper 方法对进气管段进行网格划分,剩下的圆柱体段,圆锥体段都是规则几何体,可以直接采用cooper方式进行划分,最终生成高质量网格。图3为进气管段与圆柱体段连接处网格。1.3 湍流模型的选取旋风分离器流体为强旋湍流,湍流模型有k-ε模型,RNG模型和RSM模型。k-ε模型是基于同向性假设,这与旋风分离器的强旋性质不符,RNG模型虽然加入了时均应变率,但仍基于同向性假设,还是不能符合旋风分离器的强旋性质。RSM模型抛弃了各向同性假设,在模拟各向异性湍流方面有显著优势,许多学者采用RSM模型对旋风分离器进行研究并得到了与实际情况相近的结果,所以采用RSM湍流模型来进行模拟。表3为RSM模型控制方程组。1.4 差分格式及算法选取常用的差分格式有一阶差分格式,二阶差分格式和QUICK差分格式。一阶差分格式只有一阶精度的截差,优点在于易于收敛,但是扩散项大,误差较大;二阶差分格式在一阶差分格式基础上优化了精度截差,使模拟更加接近现实但是仍有一定的假扩散;QUICK差分格式不仅保留了稳定性而且具有更高的精度截差,假扩散被进一步减小,为提高模拟准确性采用QUICK差分格式。PRESTO压力插补格式适用于高速旋转流动,符合旋风分离器内流体高旋流动的特点,所以采用PRESTO压力插补格式。SIM-PLEC耦合方式是在SIMPLE 耦合方式基础上进行优化,对于许多问题SIMPLEC耦合方式可以快速得到收敛解,所以采用SIMPLEC压力速度耦合方式。1.5 两相流模型选取择气相湍流流动会对颗粒相产生影响,同样,颗粒相反过来也会对气相产生影响,但是颗粒之间的相互作用可以忽略不计,所以采用相间耦合的随机轨道模型来模拟分离器颗粒运动。颗粒在分离器中主要受重力作用和拽力作用,不考虑其他力。颗粒相在拉格朗日坐标系下的运动方程如式(2)、式(3):1.6边界条件设置设旋风分离器内物质为空气,温度为900℃,气体密度为0.301kg/m3,黏度μ=4.67×10-3Pa·s,并对边界条件进行设置。(1)进口:速度进口(velocityinlet),大小为20m/s;(2)出口:自由出流(outflow),流量为1;(3)颗粒捕集口:壁面(wall),在加入颗粒时设置为trap类型;(4)壁面:标准壁面函数,无滑移壁面。分级效率是评价旋风分离器分离性能的一个重要指标之一。分级效率是指某给定粒径颗粒的分离效率,与进气口颗粒粒径,浓度无关,因此可以看出,用分级效率评价旋风分离器性能更具有意义,不考虑操作条件,单独考虑旋风分离器总效率是无意义的。因为旋风分离器对大颗粒几乎可以完全分离,关键在于对小颗粒的分离,所以主要对小颗粒进行模拟,颗粒直径服从Rosin-Rammler分布,颗粒粒径0.05mm~0.1mm,平均粒径0.075mm,从颗粒质量流中任意选取2000个颗粒来计算分级效率。颗粒初始喷入位置是进气口平面,颗粒速度与进气口空气速度相同。颗粒在分离器中随气流做高旋流动,大颗粒在离心力作用下被甩出,经多次碰撞壁面后落入排尘口平面,认为颗粒被捕集;小颗粒随气相流体流动,被携带从排气管排出,认为颗粒逃逸。设进入旋风分离器颗粒数为n,被捕捉数为ni,分级效率通过式(5)计算:2数值模拟结果与分析2.1 排气管直径对旋风分离器的影响模拟排气管直径2.55m、2.975m、3.4m、3.825m、4.25m,分别对应相对直径比0.3、0.35、0.4、0.45、0.5这5种典型结构。图4为不同直径x=0截面速度等值线分布图。通过数值模拟得到各个直径下总压差变化曲线图5。从图5可知。排气管直径增大,总压差随之降低,直径从2.55m增加到2.975m,压差降低12.1%;从2.975m增加到3.4m,压差降低7.60%;从3.4m增加到3.825m,压差降低7.43%;从3.825m到4.25m,压差降低5.32%,变化幅度逐渐趋于平缓。分析图4,图5可知,排气管直径增大,会导致分离器内高旋湍流速度降低,减弱了流体内部以及流体与排气管壁面和分离器内壁面的摩擦。同时排气管直径的增大可以有效减弱排气管底端入口径缩效应。最终使总压差降低,能耗减少。通过模拟得到各个直径下分级效率变化曲线图6从图6中可以看出,排气管直径增大,分级效率先增后减,但是总体变化幅度不超过2.5%。分析图4,图6发现旋风分离器分级效率最主要是受切向速度影响,排气管直径的增大会导致切向速度的降低。直径在2.55m~3.4m之间变化时,向上内螺旋区域和向下外螺旋区域变化不大,不影响气固分离;但排气管直径增大,排气管底部区域轴向速度会减少,减弱“短路流”的影响,使分级效率得到提升。排气管直径在3.4m~4.25m之间变化时,排气管直径的增大会压缩向下外螺旋区域。向下外螺旋区域是气固分离的主要区域,分离区域被压缩导致分级效率降低。虽然排气管直径增大会进一步降低轴向速度,这对减弱“短路流”是有利的,但是排气管直径的增加,也会加剧旋风分离器分离区域的“甩尾”现象,导致颗粒返混,降低分级效率并且加剧锥形壁面的磨损。综合影响下,分级效率降低。2.2 排气管插入深度对旋风分离器的影响对排气管插入深度为3.6m、8.5m和10.1m的情况进行模拟。图7为不同插入深度的结构简图。图8为不同插入深度x=0截面速度等值线分布图。经模拟得到不同插入深度下的总压差变化折线图9。从图9可以看出,随着插入深度的增加,压差快速地升高,插入深度8.5m比3.6m压差增加42.93%;插入深度10.1m比8.5m压差增加66.39%。分析图8,图9可知这主要是因为排气管插入深度提高,加大了流体与排气管壁面的接触面积从而加大摩擦,流体能量损失增加,流速降低。而总压=静压+动压。流体流速的减小,总压中动压部分减小,使出口总压减小,在入口总压不变条件下,最终总压差增大。通过模拟得到不同插入深度的旋风分离器分级效率变化折线图10。从图10可以看出,插入深度越大,分级效率越大。分析图8,图10可知,这是因为进入旋风分离器的部分气流会直接沿壁面向上流动,到达顶端后继续贴壁流动,汇聚到排气管底部四周后,紧贴排气管内壁而不经过旋风分离器圆柱体段和锥体段部分直接从排气管流出。颗粒相中一些容易被气流携带的小颗粒就会直接从排气管排出,造成“短路流”,降低分级效率。而插入深度增加,排气管贴壁速度减小,减弱“短路流”影响,提高分级效率。2.3 排气管偏心对旋风分离器的影响模拟计算了排气管沿着0°、45°、90°、135°及180°五个偏置方向的总压差和分级效率。为了便于分析,引入相对偏心距。式中:Δx———排气管偏心的距离,mm;R———圆柱段的半径,mm;r———排气管的半径,mm。相对偏心距设为定值10%(偏心距0.425m)。图11为不偏置和偏于180°方向的示意图。图12为不同偏置方向z=18截面的速度分布等值线图。通过模拟得到不同偏置方向的总压差变化曲线图13。从图13中可以看出,当偏置方向角度增加时,总压差先增后减,在偏置于90°方向时达到最大值,比初设结构增加了17.48%。在偏置方向180°时压差最小,比初设结构减少了5.32%。通过模拟得到不同偏置方向分级效率变化曲线图14。从图14中可以看出,偏置于180°方向时分级效率最高,达到77.78%。分析图12,图14可知这是由向心力导致的,因为排气管偏置于180°方向时,正好是速度进口切向方向,切向速度阻力小,可以一直保持较高速度。流体切向速度对颗粒分离起到最主要作用,流体切向速度的高速性,保证了颗粒相可以被有效地分离。3综合性评价及结构优化总压差(Δp)和分级效率(η)是评价旋风分离器重要指标,总压差Δp代表了旋风分离器能耗的多少,分级效率η代表了旋风分离器分离固体颗粒能力,评价旋风分离器的性能必须将两者都考虑进去。而压降Δp与阻力系数ξ关系如式(7)所示:式中:ui———进口气流的速度,m/s; ρg———气体密度,kg/m。阻力系数ξ可以用来表示能耗的相对大小。引进综合性因素Y=η/ξ,因为旋风分离器分级效率越高越好,而能耗越少越好,所以Y最大结构最优。使用综合性因素Y 对某电厂排气管结构进行设计优化。表4为不同直径的综合性因素计算表。从表4中可以看出,直径为4.25m时,Y=3.17最大。表5为不同插入深度的综合性因素计算表。从表5中可以看出,插入深度为3.6m 时,Y=3.17最大。表6为不同偏置方向的综合性因素计算表。从表6中可以看出,偏置方向为180°时,Y=3.38最大,为了进一步提高分离器效率,降低能量损失,某电厂旋风分离器排气管可以偏置方向为180°布置。4结语通过数值模拟的方法对某电厂660MW超临界循环流化床旋风分离器排气管直径,插入深度,偏置方向进行研究并得到这三种结构变化对分离器压差和分级效率的影响规律。引进分析综合因素Y=η/ξ,对某电厂分离器排气管结构进行了评价和设计优化。得到了以下结论:(1)随着排气管直径的增大,总压差逐渐减小,但幅度越来越小,直径4.25m时,压差最小为1461.65Pa。而分级效率是先增加后减小,直径为3.4m时最大,达到79.4%,但是整体变化幅度较小,不超过2.5%。(2)插入深度越小,总压差越小,插入深度3.6m时,总压差最小为1461.65Pa。而对于分级效率,插入深度越大,分级效率越高,插入深度10.1m时,分级效率最高为82.6%。(3)偏置方向在0°~180°变化时,偏置方向的角度增加,压差先增后减,90°时最大,达到1717.09Pa。对于分级效率,偏置方向的角度越大,效率越大,180°时,达到77.78%。(4)通过引进综合因素Y=η/ξ来评价优化排气管初设结构。某电厂旋风分离器排气管直径4.25m,插入深度3.6m的设计是合理的。为进一步提高性能,排气管可以偏置于180°方向布置。文献信息赵立正,原奇鑫,康志忠,郭永红,孙保民. 超临界循环流化床旋风分离器结构优化数值模拟[J]. 锅炉技术,2016,03:31-37+44.来源:循环流化床发电。
流化床锅炉分离器中心筒及其墙体优化改造

【摘要】本文主要分析循环流化床锅炉旋风分离器中心筒及其浇注料墙体多次损坏(筒体开裂、变形、倾斜、脱落、挂钩脱落,浇注料脱落等)的原因,并针对存在缺陷的部位提出了结构性优化改造,经检修改造后,现在该炉一直运行稳定。
【关键词】循环流化床锅炉;旋风分离器;中心筒中心筒;托架;总进气管;环隙承重板;排气管;结构优化改造1 前言循环流化床锅炉是近年来发展起来的新一代高效、低污染清洁燃烧的锅炉。
而高温旋风分离器是循环流化床锅炉的关键部件,其主要由筒体及中心筒组成,中心筒又是高温旋风分离器的关键部件。
国内循环流化床锅炉经过多年的实践运行,也相继暴露出了流化床锅炉存在的一系列问题。
譬如,随着长时间的运行,旋风分离器中心筒常出现了磨损穿孔、脱落、碳化等现象,浇注料脱落,从而影响了整个循环流化床锅炉的安全稳定运行。
在现有技术中,循环流化床锅炉旋风分离器中心筒安装方式主要有焊接吊挂式、螺栓拉杆式、外置的下吊筋吊挂式及自由吊挂式。
自由吊挂式是目前最佳的安装方案,其托架与中心筒不焊接,可以使筒体上下自由膨胀,不发生变形,歪斜和连接板断裂现象,这是人们希望的理想状态。
但实际运行过程中,由于设计、制作、安装、金属材质等因素,以及中心筒处在烟气温度高、烟气流速快、颗粒物浓度大的环境中,至使中心筒在烟气流扰动、振动、重力、高温等综合因素作用下发生变形,导致筒体凹凸不平或者椭圆化甚至坠落;从而使分离效率下降,造成锅炉带负荷能力下降,锅炉飞灰含碳量升高,过热器及尾部烟道内的受热面加速磨损,严重影响着锅炉设备的安全经济运行。
2 损坏原因分析2.1 中心筒设计结构欠佳常用的自由吊挂式是指中心筒通过上部大筋板安放在支架上的安装方式,这种安装方式大筋板与支架间为自由配合(无焊接等任何方式的固定),可以相对滑动,因此中心筒在受热膨胀时或冷却收缩时均不会受到较大的阻力发生变形。
这是人们希望的理想状态。
但是大筋板在中心筒重力及吊架支撑力的共同作用下有一个旋转的趋势,且大筋板固定在中心筒上再加上中心筒工作时处于红热状态,强度降低,极易被扭曲变形,严重时可以从支架上脱出,并且一般大筋板与支架上的配合间隙较小,相互挤压导致墙体局部脱落,影响锅炉正常运行。
循环流化床锅炉旋风分离器及省煤器的技术改造
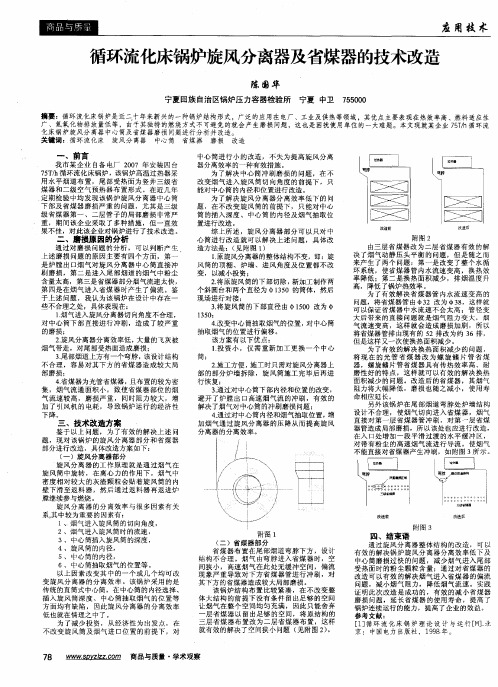
附图 2 由三 层 省 煤 器 改 为二 层 省 煤 器 有 效 的 解
3 . 将旋风 筒的下部直径 由 1 5 0 0改为
1 3 5 0;
三 、技术改造方案
鉴 于以上问题 ,为 了有效的解决上述 问 题 ,现 对 该 锅 炉 的旋 风 分 离 器 部 分 和 省 煤 器 部 分 进 行 改 造 , 具 体 改造 方 案 如 下 : ( 一 )旋 风 分 离 器部 分 旋 风 分 离 器 的 工 作 原 理 就 是 通 过 烟 气 在 旋风筒中旋转 ,在 离心力 的作用下 ,烟气中 密 度 相 对 较 大 的灰 渣颗 粒 会 贴 着 旋 风 筒 的 内 壁 下 滑 至 返 料 器 , 然 后 通 过 返 料 器 再 返 进 炉 膛继 续 参 与 燃 烧 。 旋风分离器 的分 离效率与很 多因素有关 系, 其 中较 为 重 要 的 因素 有 : l、烟气进入旋风筒的切向角度, 2、烟 气 进 入 旋 风 筒 时 的 流速 , 3、中心 筒插入旋风筒 的深度 , 4、旋风 筒的内径 , 5、 中 心 筒 的 内径 , 6、中心筒抽取烟气 的位置等 。 以上 因素 改 变 其 中 的一 个 或 几 个 均 可 改 变旋风分离 器的分离效率 。该锅炉采用 的是 传统的直筒式中心筒 ,在 中心筒的 内径选 择、 插入旋风筒 深度、 中心筒 抽取烟气 的位置等 方面均有 缺陷 ,因此旋 风分离器的分离效 率 低也就在情理之中了。 为 了减 少 投 资 ,从 经 济 性 为 出发 点 , 在 不 改变旋风筒及烟气进 口位置 的前提 下,对
一
磨损 改造
、
前言
我市某 企业 白备 电厂 2 0 0 7年安装 四台 7 5 T / h循环流化床锅炉 ,该锅炉高温过热器采 用水 平烟道布置 ,尾 部受热面为竖井 三级省 煤 器 和 二 级 空 气 预 热 器 布 置 形 式 。在 近 几 年 定期 检验中均发现该 锅炉旋风分离器 中心筒 下部及 省煤器磨损严 重的 问题 ,尤其 是三级 级省煤器第一 、二层 管子的局部磨损 非常严 重,期间该企业采取 了多种措施 ,但 一直效 果 不 佳 ,对 此 该 企 业 对锅 炉 进 行 了技 术 改 造 。
循环流化床锅炉旋风分离器改造及应用效果.
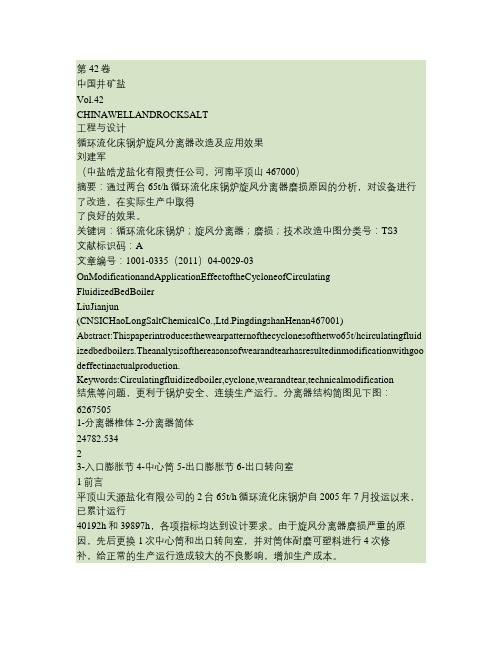
第42卷中国井矿盐Vol.42CHINAWELLANDROCKSALT工程与设计循环流化床锅炉旋风分离器改造及应用效果刘建军(中盐皓龙盐化有限责任公司,河南平顶山467000)摘要:通过两台65t/h循环流化床锅炉旋风分离器磨损原因的分析,对设备进行了改造,在实际生产中取得了良好的效果。
关键词:循环流化床锅炉;旋风分离器;磨损;技术改造中图分类号:TS3文献标识码:A文章编号:1001-0335(2011)04-0029-03 OnModificationandApplicationEffectoftheCycloneofCirculating FluidizedBedBoilerLiuJianjun(CNSICHaoLongSaltChemicalCo.,Ltd.PingdingshanHenan467001)Abstract:Thispaperintroducesthewearpatternofthecyclonesofthetwo65t/hcirculatingfluid izedbedboilers.Theanalysisofthereasonsofwearandtearhasresultedinmodificationwithgoo deffectinactualproduction.Keywords:Circulatingfluidizedboiler,cyclone,wearandtear,technicalmodification结焦等问题,更利于锅炉安全、连续生产运行。
分离器结构简图见下图:62675051-分离器椎体2-分离器简体24782.53423-入口膨胀节4-中心筒5-出口膨胀节6-出口转向室1前言平顶山天源盐化有限公司的2台65t/h循环流化床锅炉自2005年7月投运以来,已累计运行40192h和39897h,各项指标均达到设计要求。
由于旋风分离器磨损严重的原因,先后更换1次中心筒和出口转向室,并对筒体耐磨可塑料进行4次修补,给正常的生产运行造成较大的不良影响,增加生产成本。
循环流化床锅炉改造毕业论文

AGX75-1№17.2 D 左 90
62480m3/h
17000Pa 电动机
型号 功率 转速 电压
Y400-4 450KW 1450rpm 6000V
二次风机
型号
风量 风压
AGX75-2№12.5 D 右 90
41925m3/h
9356Pa 电动机
型号 功率 转速 电压
Y315 L-4 160KW 1450rpm
7
2 峄化公司型锅炉整体情况
2.1 锅炉概况
尾部烟道的前包墙与炉膛后墙水冷壁共用,形成双面水冷壁;低温过热器布置 在尾部烟道内,采用吊管结构;一、二级省煤器支于侧包墙上,并随侧包墙一 同膨胀;空气预热器单独向外拉出,分为一次风及二次风预热器;在炉膛出口, 烟气分为两路分别进入两只旋风分离器,进旋风分离器后的烟气回到炉顶水平 烟道。
(2) 鲁奇(Lurgi)型循环流化床 (3)巴特利(Battelle)的多固体循环流化床锅炉
(4)德国Babcock公司的Cirfluid循环流化床锅炉
4
1.3 国内外循环流化床锅炉的发展
从节约燃料、保护大气环境及回收温室气体CO2这三观点出发, 发展流化床锅炉在以煤为主要能源的国家具有重大意义。
9
设备技术参数
a.锅炉技术规格
表2-1 锅炉主要技术数据
锅筒中心标高 运转层标高 左右柱距 一次风量 锅炉效率
32050mm 8000mm 7200mm 62100m3/h
87%
表2-2 锅炉重要参数表
额定蒸发量 额定蒸汽压力 额定蒸汽温度
连续排污
75t/h 3.82MPa 450℃
2%
操作层标高 烟气量 前后柱距 二次风量
针对该型锅炉在实际运行中存在的问题(带负荷能力不足、水冷壁 管磨损严重、锅炉给煤易堵塞等),我公司结合实际运行经验,通过理论 分析和实践验证,积极采用各类技术和设备先后对一次风风道、风帽、旋 风分离器、给煤机、煤筛分机进行了合理的改造,创造了更好的燃烧条件, 提高了锅炉出力率,有效地延长了锅炉的运行时间。
循环流化床锅炉旋风分离器返料器安装施工探讨

循环流化床锅炉旋风分离器返料器安装施工探讨循环流化床锅炉旋风分离器返料器安装施工探讨谢晓刚(神华神东电力公司郭家湾电厂)摘要:循环流化床(Circulating Fluidized Bed,简称CFB)锅炉效率高,煤种适应性广,洁净燃烧,已被大家所接受。
但由于安装过程的一些问题使得在实际运行中,经常发生返料器引起的各种问题。
现就高温旋风分离器下部的返料器在运行中出现的一些问题,结合理论和实践经验进行探讨。
关键词:循环流化床分离器安装施工前言循环流化床(CFB)锅炉的燃烧特点是节约能源,减少对大气的污染,是我国热能动力发展的方向。
在CFB锅炉中,分离器的效率高的情况下,循环倍率高,可以提高燃烧效率,增强传热效果,但也确定了炉内烟气中固体颗粒的浓度。
流化床锅炉的燃烧方式和性质决定了锅炉内衬的工作状况,要长期地经受带煤粒子的高温烟气高速冲刷,并且要在一定的工作年限内保持正常运转而不损坏。
而实际情况是,分离器反料器在运行中经常存在一些问题,特别是试运初期,很容易发生堵灰等问题,这对整个热力机组不利,造成较大经济损失。
解决好CFB锅炉分离器和反料器的问题,是进一步提高流化床运行的关键。
而这些问题在安装过程就埋下了隐患,为了能更好的保证运行,根据运行经验结合安装施工进行一下探讨:1、分离器中心筒安装(结构参数问题),分离器效率降低,返料量不够分离器的中心同时分离器的关键部件,对于分离器的性能来说是很重要的,中心筒的插入长度、直径都直接影响着分离效率,当插入长度太长时,风力起的效率高,可是当超过一个特定值时,他对后面的影响就又一次增大了,而当插入长度不够时,分离效率偏低,返料量降低,锅炉炉膛出口温度降低,气温偏低,床温偏高,严重时锅炉负荷降低。
在施工时一定要严格按照设计参数进行安装施工,确保分离器的运行效率。
2、浇注料膨胀缝隙不合理,密封效果不好,致使外钢板烧红及漏灰、漏风,破坏压力平衡由于浇注料的膨胀系数与钢材膨胀系数不一致,施工中需科学地设置膨胀缝,防止浇注料在烘炉中发生网状裂纹和贯穿性的裂纹。
循环流化床锅炉旋风分离器事故分析与改造措施

循环流化床锅炉旋风分离器事故分析与改造措施【摘要】旋风分离器效率的提高是循环流化床锅炉经济运行的关键,其设备的长期完好运转是循环流化床锅炉稳定运行的关键。
通过对旋风分离器常见事故的分析、总结、提出并实施改造,为循环流化床锅炉满负荷运行提供保证。
【关键词】旋风分离器中心筒分离效率改造措施1 前言循环流化床锅炉的分离机构是循环流化床锅炉的关键部件之一,其主要作用是将大量高温固体物料从气流中分离出来送回燃烧室,以维持燃烧室的快速流化状态,保证燃料和脱硫剂多次循环,反复燃烧和反应,使锅炉达到理想的燃烧效率和脱硫效率。
黑化集团热电分厂的四台济锅生产的YG-75/3.82-M1型循环流化床锅炉采用高温绝热旋风分离器和悬挂中心筒,在运行中出现大量事故。
近几年在实践中对事故的不断分析总结和对设备的不断改造,使锅炉能够长期安全高效稳定运行。
2 旋风分离器中心筒变形脱落的改造措施2.1 问题的提出锅炉投运初期,运行一年以后,6#炉发现旋风分离器处差压增大,分离效率下降,锅炉负荷骤减。
停炉检查发现锅炉中心筒出口处筒壁变形向内突出,四个吊挂开裂两个,造成筒体倾斜。
如继续运行,中心筒就会落入分离器椎体内。
2.2 原因分析中心筒出口与旋风分离器顶棚直接接触,在锅炉启炉和运行中中心筒和分离器顶棚受热膨胀,相互挤压使筒体变形。
进入旋风分离器的烟气一部分由变形处短路,分离效率降低,筒体变形愈加严重。
中心筒是由四根750×80×8mm材料为1Cr25Ni20Si2钢板悬吊,一侧焊接在中心筒外壁上,另一侧焊接在旋风分离器出口外护板上。
在950℃和高速烟气作用下轻微摆动,焊口氧化开裂,造成倾斜和脱落。
2.3 改造措施(1)改变中心筒的结构和材质。
原中心筒由δ8mm的1Cr25Ni20Si2钢板卷制改为δ10mm的0Cr25Ni20钢板卷制,提高其抗压强度和耐热温度。
在筒体外壁上中下三处分别增加了防变形的加强环,出口加强环内焊有8个三角形的加强板。
- 1、下载文档前请自行甄别文档内容的完整性,平台不提供额外的编辑、内容补充、找答案等附加服务。
- 2、"仅部分预览"的文档,不可在线预览部分如存在完整性等问题,可反馈申请退款(可完整预览的文档不适用该条件!)。
- 3、如文档侵犯您的权益,请联系客服反馈,我们会尽快为您处理(人工客服工作时间:9:00-18:30)。
循环流化床锅炉旋风分离器改造俞信福(宁波热电股份有限公司,浙江宁波315800)[摘要]通过对我公司6#炉主蒸汽流量长期达不到额定出力的分析,首先从运行的角度入手,查阅相关资料分析入口烟速、飞灰浓度和粒径、烟气温度等因素对分离器的影响不致于使其阻力严重偏低;然后从结构上对照设计图纸,实地观察为分离器短路造成其压差偏少,因此有针对性地对旋风分离器进行了改造,取得了较好的效果,为以后类似问题的解决提供了一定的思路。
[关键词]循环流化床锅炉;旋风分离器;中心筒;短路分离器是循环流化床锅炉的主要部件之一,它的分离性能对整个锅炉设计与稳定运行起着至关重要的作用。
旋风分离器是目前循环流化床锅炉中应用最为广泛的一种分离装置,其结构简单,且分离效率较高,问题主要是体积较大。
1设备介绍我公司6#炉为次高压循环流化床锅炉,由杭州锅炉集团有限公司制造生产的,型号为:NG-130/5.3-M7,在炉膛与尾部烟道之间布置有两台蜗壳式旋风分离器。
旋风分离器的上半部分为蜗壳式入口,下半部分为锥形。
烟气出口为圆筒形,由防磨耐热铸件拼接而成。
颗粒和烟气先旋转下流至圆柱体的底部,粗颗粒将被分离,洁净烟气向上流动,离开旋风分离器。
粗颗粒进入回料器。
旋风分离器为膜式包墙过热器结构,其顶部与底部均与环形集箱相连,墙壁管子在顶部向内弯曲,使得在旋风分离器管子和烟气出口圆筒之间形成密封结构。
旋风分离器中心筒由5排筒板构成,每排筒板由24块ZG8Cr26Ni4Mn3Nre 组成,筒体进口内径Φ1470mm ,出口内径1662mm ,中心筒伸出长度1545mm ,并要求满焊,中心筒上部与耐磨浇注料相接并采用密封套结构,密封套用不锈钢丝网将硅酸铝棉板裹住,并用不锈钢丝将其缝牢,不锈钢丝和不锈钢丝网材料均为1Cr18Ni9Ti ,在密封套与耐磨浇注料之间用硅酸铝棉板塞实,以防气流短路。
2问题的提出及分析我公司6#炉2005年1月投入运行以来,流量只能达到110t/h ,再带高就出现主蒸汽超温,减温水每只6t/h 全开主蒸汽温度还在455℃以上。
从运行的角度对影响旋风分离器分离效率的因素进行分析,由于主蒸汽超温,首先想到温度对旋风分离器分离效率的影响,通过查阅资料,烟气温度影响着烟气的粘度,随着温度的升高,烟气的粘度随之增加,因而作用在运动颗粒的粘性阻力也会增加,从而使其分离效率下降。
但是烟气的密度随着温度的增加而减少,从而使粘性阻力减少,因此烟气的温度对旋风分离器分离效率的作用并不明显。
旋风分离器进口烟速对其分离效率的影响,分离器的效率随着进口烟速的增大而增大,虽然当进口烟速过高时,由于紊流增加和尘粒反弹等因素使分离器的效率有所下降,按运行锅炉炉膛出口的压力和高温过热器进口压力比较,进口烟速不可能过高。
最后是灰粒,灰粒的许多物理化学性能都对旋风分离器性能有影响,其中飞灰的浓度和粒径影响较大,分离效率随着飞灰的浓度的增加而增大,同时也随着飞灰的粒径增加而增大,而运行中5#炉和6#炉在用同一种煤时颗粒也一样,既使燃用不同的煤种锅炉负荷还是不会上来。
从结构上分析旋风分离器为锅炉厂整体制造提供,与其进口烟道接口的支吊架位置材料都由锅炉厂提供,现场只是整体拼装,不可能出现大的偏差。
从运行的参数比较分析,主要为分离器阻力偏低,主蒸汽超温,锅炉流量带不上。
运行时分析是否为旋风分离器保温有问题,但保温问题也不应该影响分离器的效率,也考虑筒板少装,但4#炉的中心筒只有4排比三期少一排,也未出现炉膛灰浓度提不上,锅炉流量带不上情况。
因此问题还是出在旋风分离器本身,5月下旬6#炉停炉时,经检查旋风分离器保温完好,从旋风分离器出口烟道处检查发现中心筒上部筒板开裂严重,大的裂缝有20mm ,长度大的为300mm 以上(一块筒板的有效高度为525mm ),中心筒上部耐磨浇注料与密封套之间的硅酸铝棉板已大部分被短路的烟气拉走,因此在中心筒上部第二块筒板处均匀地割了4块,高度为300mm ,塞入用不锈钢丝网将硅酸铝棉板裹住缝牢的密封套,并在密封套与耐磨浇注料之间通过4个孔用硅酸铝棉板塞实,再用原筒板把4个孔补回,用专用焊条(奥407铬26镍21不锈钢焊条)焊接,较大的缝采取耐热钢筋衬,并且满焊。
投入运行的初期,主蒸汽流量曾到过120t/h ,以后一直在100t/h 以内。
经过分析可能为焊缝为表面成形,且从4个孔塞棉的难度较大,中心筒出现裂缝后把部分硅酸铝棉板拉走,重新形成短路。
8月份6#炉停炉后,与有关技术老师傅探讨后,对旋风分离器中心筒与分离器的密封进行了改造,见图1。
图1分离器中心改造图保温层与分离器中心筒之间用硅酸铝棉板塞实后,用4mm 的SUS309密封,密封板外径Φ1770mm 内径Φ1610mm 的圆环分成若干段安装,每隔100mm 加一块4mm 的SUS309尺寸为40mm ×80mm 的筋板,并要求满焊,对旋风分离器中心筒出现的裂缝再次进行满焊,焊条仍为奥407铬26镍21不锈钢焊条。
3分离器改造前后运行参数比较旋风分离器改造前主蒸汽流量长期不超过100t/h ,炉膛顶部P16/P19差压不超过1kPa (一般在0.75kPa 左右),(下转第144页)(上接第134页)分离器的差压在600~700Pa之间,当时与4#炉、5#炉相对较阻力严重偏少。
旋风分离器改造后,负荷(主蒸汽流量)能达到额定出力130t/h,炉膛顶部P16/P19差压1.3kPa甚至更高,分离器的阻力明显增大,在额定负荷下有1.2kPa。
通过最近一次的停炉检查,由于采用了SUS309板密封,密封板未发现有变形及硅酸铝棉板脱落现象,使用情况良好。
4结论循环流化床锅炉的分离器是循环流化床锅炉的关键部件之一,其主要作用是将大量的高温固体物料从烟气中分离出来送回燃烧室,以维持燃烧室的快速流化状态,保证物料多次循环,反复燃烧和反应。
这样才能达到理想的燃烧效率。
因此,分离器机构的性能,直接影响整个循环流化床锅炉的运行效率。
循环流化床的分离器分离效率与运行中的烟速、温度及灰粒有关,当运行无法调整且分离器的阻力偏少时,应从旋风分离器的结构上进行改造,对照设计图纸,现场察看,防止短路,从而以较少的投入解决问题。
龙门煤矿井筒掘砌过三软煤层支护方法袁保玺(洛阳龙门煤业有限公司龙门煤矿,河南洛阳471935)[摘要]管缝式锚杆可以在煤体中以最短的时间发挥最大的锚固力及时对松散煤体进行支护。
[关键词]井筒掘砌;过煤层;管缝式锚杆支护洛阳龙门煤业有限公司龙门煤矿隶属于偃龙煤田,属于“三软”煤层,煤体属于极松散煤体。
龙门煤矿主井井筒掘进至390m处过二2煤层,399m处过二1煤层。
二2煤层厚度3m,在二1煤层厚度4.5m。
掘砌过这两层煤时临时支护采用了普通锚杆支护,规格为¢18×1800m,由于锚固剂在“三软”煤层中无法起到锚固作用,锚固力为0KN,普通锚杆支护支护在过二2煤层、二1煤层无法起到临时支护作用,故普通锚杆支护无法在极松散煤体中发挥作用。
为保证安全通过二2煤层、二1煤层,并针对极松散煤体这一特性,决定采用管缝式锚杆进行支护,管缝式锚杆可以在煤体中以最短的时间发挥最大的锚固力及时对松散煤体进行支护:1管缝式锚杆支护原理管缝式锚杆采用合金钢板经卷压为有缝管而成。
由于管径大于孔径(径差一般在1.5~3mm),此时合金钢板所具有足够大的屈服强度和弹性模量,使安装好的缝管式锚杆与孔壁紧紧挤压,立即在杆体全长产生摩擦锚固力,此锚固力称为初锚力。
随着时间的推移,井巷围岩应力的变化将使岩石产生水平方向错动和垂直方向位移,锚杆锚固力也因此而增大(即长时锚固力大于初锚力)。
2管缝式锚杆支护主要技术性能参数初锚固力≥25KN/m;长时锚固力(15天后)≥50~80KN;杆体拉断力≥90KN;挡圈抗脱力≥70KN;托板抗压力≥60KN。
3管缝式锚杆在井筒过“三软”煤层支护设计3.1支护材料根据井壁揭露出的煤体松散这一特点,选用的管缝式锚杆规格为:长度为2000mm,直径为40mm。
选的钢筋网片规格为:长×宽=2000×1000mm,钢筋直径为6.5mm,网孔规格为:长×宽=100×100mm。
托盘规格:长×宽=140×140mm,托盘高度为25mm,托盘厚度为4mm,孔径为42mm。
3.2支护形式管缝式锚杆孔垂直于井壁打设,锚杆采用矩形布置,为保证煤体支护的及时性,锚杆间排距定为600×600mm。
钢筋网片搭接长度为100mm,采用14#铁丝联接,做到隔孔相联。
4确保缝管式锚杆支护质量1)选用的锚杆产品必须符合国家有关技术标准。
只有合格产品,使用后才能提供足够的初锚力和长久锚固力。
使用前必须对每批产品作初锚力和长时锚固力测试,测试时采取随机抽取总量的0.5%~1%。
测试结果不得低于产品技术性能特征值的90%方可认定该锚杆合格,凡不合格产品严禁使用。
只有选用合格锚杆,才具有足够大的屈服强度和弹性模量,支护过程中才能提供足够的弹性变形恢复从而承受住井巷围岩水平方向错动和垂直方向松动膨胀而引起的变形破坏。
同时,加强对锚杆长时锚固力的测试,是检验锚杆支护是否安全可靠的重要一环。
2)进行锚杆支护时使用适宜的锚杆钻机和与锚杆匹配的孔径。
适宜的锚杆支护施工机具和孔径,可提高锚杆安装合格率、提高支护效率、降低劳动强度。
选用适宜锚杆钻机的原则是:与矿井当前技术装备水平、管理水平、施工人员技术素质、所设计的巷道断面规格大小相适应。
3)编制具有针对性并切实可行的作业规程,及时贯彻到作业人员中。
工作面围岩情况、该井筒用途及服务年限长短等,是制定锚杆支护方式和支护结构参数的主要依据。
必须使施工人员清楚并掌握各类适用的锚杆支护方式,如只锚不喷、锚喷、锚—钢带、锚—网—钢带等支护方式,以及相应的锚杆孔眼间排距规格。
同时还要根据工作面围岩变化情况及时修改补充作业规程。
4)做好对钻头磨损量的检测,确保所钻出的锚杆孔孔径与所选用的缝管式锚杆管径相匹配。
在现场施工中常会出现如下情况:用新钻头打锚杆孔眼时,安装推进往往很顺利,而越往后打出的孔眼安装时推进却越来越困难,直至出现把锚杆尾部挡圈撞脱落而尾部还露出一段在孔外,这时由于托板无法紧贴岩层面而造成该锚杆失效。
这是由于钻头使用一段时间后,因磨损而引起直径变小,故打出的锚杆孔眼直径也必然越来越小。
正确做法:在施工现场建立钻头磨损量检测制度,并根据现场岩性特征(主要是岩层软硬情况)规定当磨损量达到某一数值时必须更换新钻头,现场可采用卡尺、钢环等简易方法进行量测。
如前述,小锚杆∮33mm+0.5-2mm刚好与∮32mm小钻头匹配,二者径差在1.5-3mm,当岩层较硬时径差取小值,较软时径差取大值。