半水煤气脱硫技术知识分享
脱硫问题

半水煤气脱硫存在的问题、原因分析及措施1.脱硫工段存在的主要问题1.1脱硫效率低1.2脱硫辅料消耗高(特别是碱耗高)1.3脱硫塔堵塔1.4副盐高(NaCNS、Na2S2O3、Na2SO4)1.5脱硫中悬浮硫含量高2.原因分析2.1脱硫效率低的原因:2.1.1脱硫液成分不合格,碱含量低、脱硫催化剂加入量不够、催化剂效率低。
2.1.2脱硫液中悬浮硫高、副盐高。
2.1.3脱硫设备偏小,或脱硫设备设计不合理,如:液气比不够,喷淋密度不够。
2.1.4脱硫塔堵塔,液体偏流,液体分布不均。
2.2堵塔的原因:2.2.1脱硫液中悬浮硫高(堵塔的主要原因之一)2.2.2脱硫液中副盐高(堵塔的主要原因)2.2.3操作不当,循环量偏小,液体偏流,填料层局部形成干区,慢慢由于硫泡沫、副盐或煤气中的杂质而结住,并逐渐扩大了板结面积。
2.3脱硫辅料消耗高,特别是碱耗高的原因:2.3.1脱硫液温度控制太低,再生时间短,或者自吸空气量小造成NaHCO3/Na2CO3比太高。
(正常情况下NaHCO3/Na2CO3比小于6)2.3.2副盐增长太快。
2.3.3煤气中焦油、苯、酚类含量高,造成飞泡冒槽。
2.3.4跑、冒、滴、漏。
2.4悬浮硫高的原因2.4.1再生温度高,硫颗粒不易聚结,难浮选。
2.4.2再生吸入空气量太小,得不到再生,或者空气量太大,再生槽内脱硫液翻滚,碰撞,硫泡沫破碎难浮选。
2.4.3泡沫层的厚度太薄或者太厚。
2.5副盐高的原因2.5.1.脱硫温度高,脱硫液温度达到45℃,副盐生成快,50℃以上副盐会急剧上升。
(这是副盐高的主要原因之一)2.5.2高温熔硫时,硫与碱反应迅速(这是副盐高的主要原因),这同时也是碱耗高的原因。
2.5.3溶液中悬浮硫高也是副反应发生的原因之一,而且反应速度会随硫颗粒的细小、颗粒数量的增加以及脱硫液温度的升高而加快。
2.5.4脱硫液中溶解氧过高,接触时间过长,副盐会增加(这个同时要满足温度过高,PH>9),这个发生的可能性不大,正常再生槽吹风强度是60m3/m2.h,我们目前为56m3/m2.h。
半水煤气脱硫

前言1.1 合成氨工业在国民经济中的地位合成氨工业是基础化学工业之一。
其产量居各种化工产品的首位。
氨本身是重要的氮素肥料,除石灰氮外,其它氮素肥料都是先合成氨,然后加工成各种铵盐或尿素。
将氨氧化制成硝酸,不仅可用来制造肥料(硝酸铵、硝酸磷肥等),亦是重要的化工原料,可制成各种炸药。
氨、尿素和硝酸又是氨基树脂、聚酰胺树脂、硝化纤维素等高分子化合物的原料。
以其为原料可制得塑料、合成纤维、油漆、感光材料等产品。
作为生产氨的原料一氧化碳、氢气合成气,可进行综合利用,以联产甲醇及羰基合成甲酸、醋酸、醋酐等一系列碳一化工产品。
以做到物尽其用,减少排放物对环境的污染,提高企业生产的经济效益。
已成为当今合成氨工业生产技术发展的方向。
国际上对合成氨的需求,随着人口的增长而对农作物增产的需求和环境绿化面积的扩大而不断增加。
据资料统计:1997年世界合成氨年产量达103.9Mt。
预计2000年产量将达111.8Mt。
其化肥用氨分别占氨产量的81.7%和82.6%。
我国1996年合成氨产量已达30.64Mt,专家预测2000年将达36Mt,2020年将增加至45Mt。
即今后20年间将增加到现在的1.5倍。
因而合成氨的持续健康发展还有相当长的路要走。
未来我国合成氨氮肥的实物产量将会超过石油和钢铁。
合成氨工业在国民经济中举足轻重。
农业生产,“有收无收在于水,收多收少在于肥”。
所以,合成氨工业是农业的基础。
它的发展将对国民经济的发展产生重大影响。
因此,我国现有众多的化肥生产装置应成为改造扩建增产的基础。
我国七十至九十年代先后重复引进30多套大化肥装置,耗费巨额资金,在提高了化肥生产技术水平的同时,也受到国外的制约。
今后应利用国内开发和消化吸收引进的工艺技术,自力更生,立足国内,走出一条具有中国特色的社会主义民族工业的发展道路。
过去引进建设一套大型化肥装置,耗资数十亿元。
当今走老厂改造扩建的道路,可使投资节省1/2—2/3。
节省的巨额资金,用作农田水利建设和农产品深加工,将在加速农村经济发展,提高农民生活水平,缩小城乡差距起着重要作用。
半水煤气脱硫技术

工艺特点 该工艺优点: 1) 脱硫效率高,一般可大于 99%,能将 H2S 从 6g/m3,脱至 2ppm,只需一次脱 硫即可达到城市煤气标准。 2) 该工艺技术成熟,操作稳定,设备和材料均可在国内解决,是一种比较理想的 脱硫脱氰工艺。 该工艺缺点: 1) 磺、硫代硫酸钠和硫氰酸钠产品品位不高,操作环境较差,因此综合效益较差; 2) 改良 ADA 脱硫装置位于煤气净化处理末端,腐蚀性较强,对前端设备和管道材 质要求较高;
目前,在发生炉煤气的湿法脱硫技术中, 应用较为广泛的是栲胶脱硫法
它是以纯碱作为吸收剂,以栲胶为载氧体,以NaVO2为氧化剂。其脱硫及再生反应过 程如下: (1)吸收: 在吸收塔内原料气与脱硫液逆流接触硫化氢与溶液中碱作用被吸收: H2S+Na2CO2=NaHS+NaHCO2 (2)析硫: 在反应槽内硫氢根被高价金属离子氧化生成单质硫: NaHS+NaHCO2+2NaVO2======S↓+Na2V2O2+Na2CO2+H2O (3)再生氧化 在喷射再生槽内空气将酚态物氧化为醌态: 2HQ+1/2O2====2Q+H2O 以上过程按顺序连续进行从而完成气体脱硫净化。另有资料和实验证实,在酚被 氧化为醌的同时有双氧水生成,故再生氧化也可按下式表达: 2HQ+O2====2Q+H2O2生成双氧水 H2O2+V+4====V+5+H2O HS_+V+5====S0↓+V+4
经济效益
栲胶法根据碱源不同分为碱性 栲胶(以橡椀栲胶和偏钒酸钠 为催化剂)脱硫和 氨法栲胶(以氨代替碱)脱硫。 栲胶法适用于焦炉气脱硫,焦 炉气与半水煤气的区 别在于其含萘及煤焦油、HCN 较多,而 C02 较少。因此,只 要前工序(静电除尘除 焦、脱萘等)正常,使用栲胶法 是可行的。栲胶法和改良的 ADA 法工艺流程完全相 同。
半水煤气脱硫系统硫堵浅析
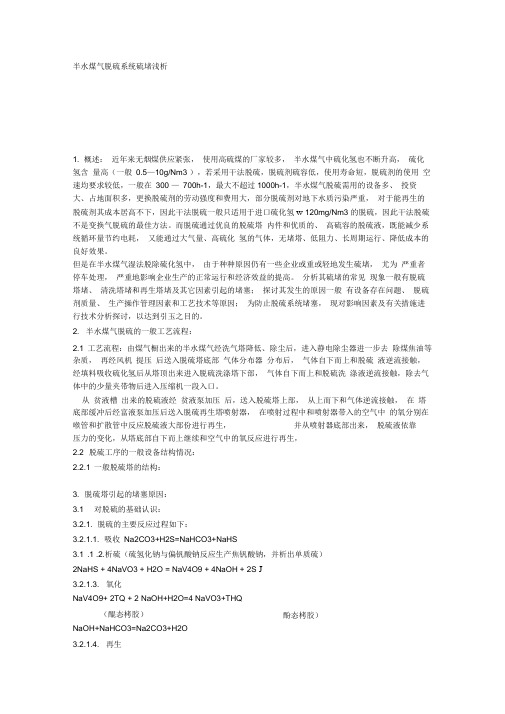
半水煤气脱硫系统硫堵浅析1. 概述:近年来无烟煤供应紧张,使用高硫煤的厂家较多,半水煤气中硫化氢也不断升高,硫化氢含量高(一般0.5—10g/Nm3 ),若采用干法脱硫,脱硫剂硫容低,使用寿命短,脱硫剂的使用空速均要求较低,一般在300 —700h-1,最大不超过1000h-1,半水煤气脱硫需用的设备多、投资大、占地面积多,更换脱硫剂的劳动强度和费用大,部分脱硫剂对地下水质污染严重,对于能再生的脱硫剂其成本居高不下,因此干法脱硫一般只适用于进口硫化氢w 120mg/Nm3 的脱硫,因此干法脱硫不是变换气脱硫的最佳方法。
而脱硫通过优良的脱硫塔内件和优质的、高硫容的脱硫液,既能减少系统循环量节约电耗,又能通过大气量、高硫化氢的气体,无堵塔、低阻力、长周期运行、降低成本的良好效果。
但是在半水煤气湿法脱除硫化氢中,由于种种原因仍有一些企业或重或轻地发生硫堵,尤为严重者停车处理,严重地影响企业生产的正常运行和经济效益的提高。
分析其硫堵的常见现象一般有脱硫塔堵、清洗塔堵和再生塔堵及其它因素引起的堵塞;探讨其发生的原因一般有设备存在问题、脱硫剂质量、生产操作管理因素和工艺技术等原因;为防止脱硫系统堵塞,现对影响因素及有关措施进行技术分析探讨,以达到引玉之目的。
2. 半水煤气脱硫的一般工艺流程:2.1 工艺流程:由煤气橱出来的半水煤气经洗气塔降低、除尘后,进入静电除尘器进一步去除煤焦油等杂质,再经风机提压后送入脱硫塔底部气体分布器分布后,气体自下而上和脱硫液逆流接触,经填料吸收硫化氢后从塔顶出来进入脱硫洗涤塔下部,气体自下而上和脱硫洗涤液逆流接触,除去气体中的少量夹带物后进入压缩机一段入口。
从贫液槽出来的脱硫液经贫液泵加压后,送入脱硫塔上部,从上而下和气体逆流接触,在塔底部缓冲后经富液泵加压后送入脱硫再生塔喷射器,在喷射过程中和喷射器带入的空气中的氧分别在喉管和扩散管中反应脱硫液大部份进行再生,并从喷射器底部出来,脱硫液依靠压力的变化,从塔底部自下而上继续和空气中的氧反应进行再生,2.2 脱硫工序的一般设备结构情况:2.2.1 一般脱硫塔的结构:3. 脱硫塔引起的堵塞原因:3.1 对脱硫的基础认识:3.2.1. 脱硫的主要反应过程如下:3.2.1.1. 吸收Na2CO3+H2S=NaHCO3+NaHS3.1 .1 .2.析硫(硫氢化钠与偏钒酸钠反应生产焦钒酸钠,并析出单质硫)2NaHS + 4NaVO3 + H2O = NaV4O9 + 4NaOH + 2S J3.2.1.3. 氧化NaV4O9+ 2TQ + 2 NaOH+H2O=4 NaVO3+THQ(醌态栲胶)酚态栲胶)NaOH+NaHCO3=Na2CO3+H2O3.2.1.4. 再生2 THQ+1/2O2=2TQ+H2O3.1.1.5. 副反应2NaHS+2O2=NaS2O3 +H2O Na2CO3+CO2+H2O=2NaHCO3 Na2CO3+HCN=NaCHS2NaCN+5 O2=Na2SO4+CO2 f +S02 f + N2 f副反应消耗了Na2CO3,降低了溶液脱硫的能力,使溶液的活性下降,因此生产中应严格控制副反应。
半水煤气脱硫技改总结

l 系统喷淋预脱硫 塔与后 面的填料塔 串联运 行 ,分别 用各 自独 立 的溶 液 再 生 系统 。预 脱 硫 塔 与 填 料塔脱 硫效率 分别 达 50% 左 右 ,可保 证 系统 半水 煤 气 中的 H S在 4000mg/Nm 时稳 定 运行 ,提 高半 水 煤气 中 H S的控 制指 标 ,基本 消 除对原 料 煤 种 的 限制 。
胶 、888、DDS、PDS、MSQ等 各 种 脱硫 技 术 ,如何 在 高 塔 喷淋 +填料 塔两 段 串联 脱 硫 系统 ,喷淋 塔 主要 部
H s的情况下保证脱硫系统 的连续稳定运行 ,防止 件由武汉利德流体技术有限公 司的设计,溶液再生 或减少 脱硫堵 塔现 象 的发 生 ,成 为 脱硫 系统 运 行 正 系统 分别独 立 运 行 。填 料 塔 部分 维 持 现状 不 变 ,主
改 造成 喷淋塔 ,新增 一 台脱硫 泵 、一 台再 生槽等 。 3 投 资分析
项 目建 议 书 预计 投 资 213.78万 元 (其 中利 息 14.08万 元 ),实 际投 资 188.0536万元 (其 中利息估 l5万元 )。具 体项 目见 表 1。
表 1 实 际投资费用一 览表 (一 车间 1 系统)
统 H s都将长期在 4000 mg/Nm 左右运行 ,现有装 产试运 行 。刚开 始利 用 原 来 的 五 台旧泵 (其 中脱 硫
置 不能 满足长周 期运 行要 求 。
泵三 台、再 生 泵 二 台 )运 行 ,脱 硫 效 果 还可 以 ,由于
半水煤气脱硫

成氨工艺有很大的危害, 常见的有: 对催化剂的危害; 对产品质量的危害; 对碳酸丙烯酯脱碳操作的危害; 对铜洗操作的危害;对金属腐蚀; 对人体的危害。
合成氨厂半水煤气中硫化物的种类较多。
其主要是硫化氢, 约占硫化物总量的90%。
另外还含有少量的有机硫化物, 主要是二硫化碳、羰基硫、硫醇等。
硫化氢分子式为H 2 S, 是无色气体, 有类似腐烂鸡蛋的恶臭味。
性剧毒, 易溶于水, 其水溶液呈酸性, 能与碱生成盐。
可用碱溶液来吸收它以除去气体中的硫化氢。
硫化氢有很强的还原能力, 易被氧化成硫磺和水, 这一性质被广泛的用于脱除硫化氢并副产硫磺的工艺上。
硫化氢还容易与金属、金属氧化物或金属的盐类生产金属硫化物。
由于在生产过程中的H2 S会对生产造成很大的危害, 同时硫化氢为有毒有害气体, 为了减少生产的损失、保护环境必须除掉H2 S 气体。
脱硫的方法很多, 可分为干法和湿法两大类, 其中湿式氧化法脱硫多用于半水煤气和变换气的一次脱硫, 而干法脱硫多用于变换气脱硫和碳化气的精脱硫。
干法脱硫具有流程短, 设备结构简单, 气体净化度高, 操作平稳的优点。
但此法经常采用固定层反应器, 需要定期更换脱硫剂, 不能连续。
由于受脱硫剂硫容量( 单位质量脱硫剂能脱除硫的最大含量) 的限制, 干法脱硫一般用于含硫量较低的情况。
湿式氧化法脱硫不仅具有吸收速度快,生产强度大等特点,而且具有脱硫过程连续,溶液易再生,副产硫磺等特点,因而被合成氨厂广泛采用;湿式氧化法脱硫的不足之处是不能有效脱除有机硫化物,没有干法脱硫净化度高。
脱硫技术在合成氨厂中常采用湿式氧化法脱硫, 目前中小型合成氨厂常用的湿式氧化脱硫法有: 氨水催化法、栲胶法、改良ADA法、PDS法、M SQ 法, KCA 法, 888法。
1.氨水催化法氨水催化法系采用8~ 25滴度的氨水, 其中加0. 2~ 0. 3 g /L对苯二酚作催化剂, 使溶解于液相的硫化氢氧化为元素硫; 本法有氨损失较大的缺点, 此外, 溶液的硫容量较低, 仅为0. 1~ 0. 15g /L。
半水煤气湿法脱硫工艺设计
15万吨/年合成氨原料气净化脱硫工段设计1总论1.1概述氮肥尿素1.2文献综述1.2.1合成氨原料气净化的现状合成氨原料气(半水煤气)的净化就是清除原料气中对合成氨无用或有害的物质的过程..原料气的净化大致可以分为“热法净化”和“冷法净化”两种类型..原料气的净化有脱硫..脱碳..铜洗和甲烷化除杂质等..在此进行的气体净化主要是半水煤气的脱硫的净化。
煤气的脱硫方法从总体上来分有两种:热煤气脱硫和冷煤气脱硫。
在我国..热煤气脱硫现在仍处于试验研究阶段..还有待于进一步完善..而冷煤气脱硫是比较成熟的技术..其脱硫方法也很多。
冷煤气脱硫大体上可分为干法脱硫和湿法脱硫两种方法..干法脱硫以氧化铁法和活性炭法应用较广..而湿法脱硫以砷碱法、ADA、改良ADA和栲胶法颇具代表性。
煤气干法脱硫技术应用较早..最早应用于煤气的干法脱硫技术是以沼铁矿为脱硫剂的氧化铁脱硫技术..之后..随着煤气脱硫活性炭的研究成功及其生产成本的相对降低..活性炭脱硫技术也开始被广泛应用。
干法脱硫既可以脱除无机硫..又可以脱除有机硫..而且能脱至极精细的程度..但脱硫剂再生较困难..需周期性生产..设备庞大..不宜用于含硫较高的煤气..一般与湿法脱硫相配合..作为第二级脱硫使用。
湿法脱硫可以处理含硫量高的煤气..脱硫剂是便于输送的液体物料..可以再生..且可以回收有价值的元素硫..从而构成一个连续脱硫循环系统。
现在工艺上应用较多的湿法脱硫有氨水催化法、蒽醌二磺酸法(A.D.A法)及有机胺法。
其中蒽醌二磺酸法的脱除效率高..应用更为广泛。
改良ADA法相比以前合成氨生产中采用毒性很大的三氧化二砷脱硫..它彻底的消除了砷的危害。
基于此..在合成氨脱硫工艺的设计中我采用改良ADA法工艺。
1.2.2改良ADA的简述ADA 法是英国西北煤公司与克莱顿胺公司共同开发的, 于1959 年在英国建立了第一套处理焦炉气的中间试验装置, 1961 年初用于工业生产。
半水煤气脱硫岗位操作要点
半水煤气脱硫岗位操作要点一、任务用贫液吸收来自造气工段半水煤气中的硫化氢,使半水煤气得到净化。
吸收硫化氢的富液在催化剂的作用下,经氧化再生后循环使用,根据全厂的生产情况,调节罗茨机气量,以均衡生产负荷。
三、工艺流程流程简述:来自静电除焦器除去煤焦油等杂质的半水煤气,由罗茨机加压后送入脱硫塔,进入脱硫塔和塔顶喷淋下来的脱硫液逆向接触,半水煤气中的硫化氢被脱硫液吸收,脱硫后的半水煤气经清洗塔进一步降温至30~50℃以下,去压缩机一段进口总气水分离器。
吸收了硫化氢的富液,由富液泵打入喷射再生器,喷嘴向下喷射与喷射器吸入的空气进行氧化还原反应而得到再生,液体再进入再生槽继续氧化再生,再生后的贫液经液位调节器流入贫液槽再由贫液泵打入脱硫塔循环使用。
富液在再生槽中氧化再生所析出的泡沫,由槽顶溢流入硫泡槽贮罐,再进入熔硫釜,回收液体后由地池泵直接打到贫液槽回收使用,制得的硫磺作为成品售出。
脱硫过程中消耗的栲胶液,由定期制备的栲胶液补充。
四、主要设备一览表表2-6 湿法脱硫设备一览表序号设备名称详细规格数量/台1 脱硫清洗塔Φ4000×30000脱硫段:海尔环上层Φ50mm,H=4000下层Φ76mm,H=4000(100m)清洗塔:海尔环上层Φ50mm,H=500mm下层Φ50mm,H=4000mm(44.0m) 12 罗茨鼓风机2Q=346m3/min,△P=5000mmH2O柱 43 富液泵Q=280m3/min,H=63m 34 贫液泵Q=288m3/min,H=41.3m 35 清洗塔水封Φ600mm×6500mm,V=1.84m3 16 再生槽Φ6300mm/5000mm×6500mm 17 贫液槽Φ5000mm×5000mm 18 液位调节器Φ1200mm×2200mm 19 喷射器Φ250mm/Φ100mm×780mm16五、操作要点(一)保证脱硫液质量①根据脱硫液成分及时制备栲胶液,保证脱硫液成分符合工艺指标。
半水煤气脱硫
置:主页> 大气治理技术> ?正文水煤气,水煤气,半水煤气系统脱硫综合分析2011-11-21 15:55湖南环保网-湖南第一环保门户网站,绿色,低碳点击: 302 次天然气,焦炉气,煤气,石油裂解气等气体中都含有一定数量的硫化氢和有机硫化物(主要有羰基硫,二硫化碳,硫醇,硫醚等),原料气中的硫化物能导致甲醇,合成氨生产中催化剂中毒,增加液态溶剂的黏度,腐蚀,堵塞设备和管道,影响产品质量。
燃烧物和工业装置排放的气体进入大气,造成环境污染,危害人体健康。
笔者主要针对合成氨,甲醇工业原料气中的硫化氢脱除工艺进行简单介绍。
1 小型氮肥企业脱硫工艺状况1.1 工艺条件的选择气体中硫化物的脱除方法主要有吸收,吸附,膜渗透,化学转化,凝缩等,根据原料气的种类,处理量大小和硫化物的种类,含量,可选用不同的脱除方法和工艺条件。
一般在1套系统中采用2种以上脱硫方法。
国内大型氮肥企业采取的脱硫工艺一般为低温甲醇洗,小型氮肥企业一般采取碱性溶液加催化剂吸收以及吸附或膜渗透等方法。
碱性溶液加催化剂吸收方法工艺路线基本相同,区别在于不同企业根据自身情况而选用不同的脱硫催化剂。
1.2 水煤气,半水煤气脱硫湿法脱硫一般的工艺路线水煤气,半水煤气由气柜经洗气塔,静电除焦器,罗茨风机和降温塔后,进入脱硫塔,在脱硫塔填料层中与脱硫液逆流接触,气体中的无机硫和部分有机硫被溶液吸收后,进入分离器和清洗冷却器,冷却分离后的气体经静电除焦器进入气体压缩机。
脱硫泵从贫液槽抽取"贫液"进入塔内,吸收后的"富液"进入富液槽经泵加压后送入再生槽,经喷射器吸收空气氧化再生后,单质硫以泡沫的形式从再生槽中浮选出来,"富液"转化为"贫液""贫液"经液位调节器进入贫液槽,循环使用。
1.3 变换气脱硫变换气脱硫工序的工艺和设备基本与半水煤气脱硫相同,各企业根据自身的情况选择不同的操作压力.一般的工艺路线为:来自变换或其他工段的气体进入脱硫塔,在脱硫塔填料层中与脱硫液逆流接触,气体中的H2S被溶液吸收后,进入分离器,分离后的气体进入后续工段.脱硫泵从贫液槽抽取"贫液"进入塔内,吸收后的"富液"进入再生槽,在催化剂的作用下经喷射器吸收空气氧化再生后,单质硫以泡沫的形式从再生槽中浮选出来,"富液"转化为"贫液""贫液"经液位调节器进入贫液槽,循环使用,由于干法脱硫剂存在饱和硫容,故干法脱硫虽然在水煤气,半水煤气系统无泵的动力消耗,但企业一般并不采用。
半水煤气脱硫技术
DS碱法脱硫包括气体进入液体的扩散过程, 也包括化学反应过程。影响扩散的因素有 温度、液气比、传质面积、脱硫液浓度等; 影响化学反应的因素包括脱硫液组成、温 度、化学反应种类、反应进行程度等。
: 1) 适用范同广,能够脱除高含量硫; 2) 脱硫脱氰效率高,H2S 脱除率可达 96%以上,HCN 脱除率可达 95%以
湿式栲胶法脱硫缺点 设备较多,工艺操作也较复杂,设备投资较大。
湿式栲胶法脱硫优点 湿式栲胶法脱硫整个脱硫和再生过程为连续在线过程, 脱硫与再生同时进行,不需要设置备用脱硫塔;煤气 脱硫净化程度可以根据企业需要,通过调整溶液配比 调整,适时加以控制,净化后煤气中H2S含量稳定。 运行费用低,经济效益好。
工艺特点 该工艺优点: 1) 脱硫效率高,一般可大于 99%,能将 H2S 从 6g/m3,脱至 2ppm,只需一次
脱 硫即可达到城市煤气标准。 2) 该工艺技术成熟,操作稳定,设备和材料均可在国内解决,是一种比较理想的 脱硫脱氰工艺。 该工艺缺点: 1) 磺、硫代硫酸钠和硫氰酸钠产品品位不高,操作环境较差,因此综合效益较差; 2) 改良 ADA 脱硫装置位于煤气净化处理末端,腐蚀性较强,对前端设备和管道材 质要求较高;
3) 废液处理流程较长,能耗高,致使装置投资费用较高。
PDS
01
PDS 工艺主要应用于煤气、焦炉气、合成氨厂、半
水煤气、炼厂气等,一般是与
02
ADA 法和栲胶法配合使用。只需要在原脱硫液中
加微量的 PDS 即可,消耗费用较Fra bibliotek03 低。
泡塔的位离循沫底压调心在来环从靠部缩节后P自泵2液D,空器的台粗将S位N与气流硫催脱苯脱aN差塔接回膏化硫H的a硫自S2顶触脱外剂塔温+液S2流喷使硫运的 底度xNH分+入脱aC淋脱塔,作排为1别H硫N硫/的硫循离用出3C2送+泡0液OO脱液环心下的NN~入沫32吸硫再使液,脱aa3++222槽2收5液生用经可硫台(HCCNxN℃,HOO2-逆。,过脱液再aa的O2H33用PH1向再浮低除经生S+DS煤)→SN←泵的SH2+接生于位无液塔+Sa气H→2将←法过221H触后再槽机封底SO2N依/硫C→脱程H(22S,的生返硫槽部2aO次NON2泡N硫还C→气→脱脱塔回与进,3Sa2a进Na沫的伴进,)OC除硫顶脱有入与2N←+N入NHS连原随一其←aC煤液部硫机溶再a→x++2HO续2理+以步基→气 从 扩 系硫液生台SxSSN2CS送及下参本+H2→中塔大统,循塔串+O程↓aON2往工副加V反HO2的上部,同环底联见S3NaD+2H离艺反反应(+H大部分工时槽部的a图OuH+H心CC流应应为液T部经的艺促,鼓脱2.x1LO2NOS机程::。:)#8O分液硫流使用入硫3S↓,
- 1、下载文档前请自行甄别文档内容的完整性,平台不提供额外的编辑、内容补充、找答案等附加服务。
- 2、"仅部分预览"的文档,不可在线预览部分如存在完整性等问题,可反馈申请退款(可完整预览的文档不适用该条件!)。
- 3、如文档侵犯您的权益,请联系客服反馈,我们会尽快为您处理(人工客服工作时间:9:00-18:30)。
3) 废液处理流程较长,能耗高,致使装置投资费用较高。
PDS
PDS 工艺主要应用于煤气、焦炉气、合成 氨厂、半水煤气、炼厂气等,一般是与
ADA 法和栲胶法配合使用。只需要在原脱 硫液中加微量的 PDS 即可,消耗费用较
低。
PDS法脱硫的原理及工艺流程 来自粗苯的温度为30~35℃的煤气依次进入2台串联的脱硫塔底部,与塔顶
也较复杂,设备投资较大。
经济效益
栲胶法根据碱源不同分为碱性 栲胶(以橡椀栲胶和偏钒酸钠 为催化剂)脱硫和
氨法栲胶(以氨代替碱)脱硫。 栲胶法适用于焦炉气脱硫,焦 炉气与半水煤气的区
别在于其含萘及煤焦油、HCN 较多,而 C02 较少。因此,只 要前工序(静电除尘除
焦、脱萘等)正常,使用栲胶法 是可行的。栲胶法和改良的 ADA 法工艺流程完全相
离心后的硫膏外运,离心液经过低位槽返回脱硫系统,工艺流程见图1。
PDS碱法脱硫包括气体进入液体的扩散过 程,也包括化学反应过程。影响扩散的因 素有温度、液气比、传质面积、脱硫液浓 度等;影响化学反应的因素包括脱硫液组 成、温度、化学反应种类、反应进行程度 等。
该工艺优点
: 1) 适用范同广,能够脱除高含量硫; 2) 脱硫脱氰效率高,H2S 脱除率可达 96%以上,HCN 脱除率可达 95%以上。
Na2SO4≥40g/L 时,设备开始腐蚀,Na2SO4≥80g/L 时设备腐蚀相当严重。
ADA
我公司甲醇系统改良ADA法脱硫流程: 一、气体8 n) F, C) @. I0 _& Z 中变气脱硫塔底部,与塔顶进入的Na2CO3溶液逆向接触,脱除H2S,使出塔 气体中H2S含量<10PPm,COS含量<5PPm,再分别进入脱硫塔后分离器 分离夹带溶液,气体温度约50℃,压力2.4 MPa(G)送至脱碳工序。" v2 Y6 ~) u+ y9 w+ Y 二、溶液 脱硫塔底部排出的含硫富液进入氧化再生塔底部,来自空气压缩机J0502约 0.5Mpa(G)的压缩空气分别经U型管液封进入氧化再生塔底部空气分配器, 在塔内充分鼓泡混合、反应,使硫化物氧化,析出元素硫。形成的硫泡沫由 塔顶部溢流至硫泡沫槽F0201。经氧化再生后的贫液,由再生塔中上部扩大部 分自流到脱硫溶液循环槽,贫液再经脱硫泵J0203a,b升压后送入脱硫塔,继 续吸收中变气中的硫化物,并循环使用。硫泡沫槽内的硫泡沫液,经硫泡沫 泵J0201a,b送至转鼓真空过滤机L0201,过滤出单质硫,该硫膏液经下料斗流 到熔硫釜ⅠF0203,沉积到釜内的硫量不断增多,当釜内硫膏充满度达80%时, 进行间歇熔硫操作,利用0.4MPa(G)蒸汽通入熔硫釜夹套加热釜内硫膏, 使釜底部硫层的温度在120~130℃保持4h,硫变成熔融状态,易于流动的液 体硫,顺利地从釜内放出,到硫铸模内自然冷却成型。 Na2CO3 53g/l ADA 2g/l NaVO3 2g/l3 C" j/ S7 K- @. `0 L* ] PH值 8.0-8.5 总碱度(N)0.5-0.6
NaHS+1/2O2 ←→ NaOH+xS↓ 脱硫液吸收H2S的过程还伴随以下副反应:
2NaHS+2O2 → Na2S2O3+H2O
2HCN+Na2CO3 → 2NaCN+CO2+H2OT #
NaCN+S → NaCNS 从2台脱硫塔底排出的脱硫液经液封槽进入溶液循环槽,用循环泵将脱硫液 分别送入2台再生塔底部,与再生塔底部鼓入的压缩空气接触使脱硫液再生。 再生后的脱硫液从塔上部经液位调节器流回脱硫塔循环使用,浮于再生塔顶部 扩大部分的硫泡沫靠液位差自流入硫泡沫槽,用泵将硫泡沫连续送往离心机,
工艺特点 该工艺优点: 1) 脱硫效率高,一般可大于 99%,能将 H2S 从 6g/m3,脱至 2ppm,只需一次脱 硫即可达到城市煤气标准。 2) 该工艺技术成熟,操作稳定,设备和材料均可在国内解决,是一种比较理想的 脱硫脱氰工艺。 该工艺缺点: 1) 磺、硫代硫酸钠和硫氰酸钠产品品位不高,操作环境较差,因此综合效益较差; 2) 改良 ADA 脱硫装置位于煤气净化处理末端,腐蚀性较强,对前端设备和管道材 质要求较高;
对有 机硫的脱除率可达 50%以上: 3) 生成的单质硫颗粒大,易分离; 4) 可脱除部分有机硫; 该工艺缺点: 1) 有时脱硫效率不稳定; 2) 需要其它成分配合使用。 3) 根据国内应用情况来看,该技术用于无机硫脱效果较理想,用于有机硫脱
除的
效果不理想。
此课件下载可自行编辑修改,仅供参考! 感谢您的支持,我们努力做得更好!谢谢
同。
. 工艺特点 1) 该工艺优点: 2) 原料为野生植物,资源丰富、价格低廉。 3) 无堵塔问题。 4) 栲胶既是氧化剂又是钒的配合剂,脱硫液组成简单。 5) 脱硫液腐蚀性小。 该工艺缺点: 1) 管道容易淤积硫。 2) 没有脱除有机硫。 3) 栲胶需要预处理才能添加到系统中,否则会引起严重的溶液发泡。 4) 溶液本身的胶体功能和发泡性对脱硫操作和硫回收不利。 5) 脱高硫气体其脱硫效率更低,尤其是有含高挥发组份原料值得的高硫气体。 6) 随着副反应生成物增多和其他杂质增加,溶液腐蚀性增大。当溶液中
半水煤气脱硫技术ห้องสมุดไป่ตู้
湿式栲胶法脱
湿式栲胶法脱硫优点 湿式栲胶法脱硫整个
脱硫和再生过程为连续在 线过程,脱硫与再生同时 进行,不需要设置备用脱 硫塔;煤气脱硫净化程度 可以根据企业需要,通过 调整溶液配比调整,适时 加以控制,净化后煤气中 H2S含量稳定。运行费用 低,经济效益好。
湿式栲胶法脱硫缺点 设备较多,工艺操作
喷淋的脱硫液逆向接触,脱除煤气中的大部分H2S,其基本反应为: H2S(气)←→H2S(液)
Na2CO3+2H2S → NaHS+NaHCO3 在PDS催化剂的作用下,可脱除无机硫与有机硫,同时促使NaHCO3进一步
参加反应: NaHS+NaHCO3+(x-1)S ←→Na2Sx+CO2+H2O
Na2Sx+1/2O2+H2O ←→ 2NaOH+xS↓VDu .L8