直廓环面蜗杆传动几何计算
蜗杆传动

H1 1000P 1 (1 )
W
式中:P1—蜗杆传动的功率,KW
—蜗杆传动的总效率
单位时间由箱体外壁散发到空气中的热量为
H 2 aW A(t1 t0 )
式中 aw—表面散热系数 A—箱体的散热面积
W
t1—箱体的工作温度,在800以内
t0—周围空气温度, t0=200
根据热平衡条件H1=H2可求得箱体的工作温度和应满 足的要求为
式中 px 蜗杆轴向齿距;z1-蜗杆头数; u-齿数比,导程角大,传动效率高; 导程角小,传动效率低。
普通蜗杆传动的m与d1搭配值 (注:d1与m的比值称为蜗杆直径系数q)
3 、传动比i、蜗杆头数Z1和蜗轮齿数Z2
n1 Z 2 i n2 Z1
蜗杆头数Z1通常取为:1,2,3,4,或6
确定圆周力Ft及径向力Fr的方向的方法同外啮合圆柱齿轮 传动,也可按照主动件左右手定则来判断。而轴向力Fa的方向 则可根据相应的圆周力Ft的方向来判定,即Fa1与 Ft2方向相反, Ft1与 Fa2的方向相反。
力的方向判断例题
2. 蜗杆传动的计算载荷
计算载荷=K*名义载荷
K K A K K
1000 P 1 (1 ) t1 t0 80C C aW A
在既定工作条件下,保持正常油温所需要的散热面积, 对于散热肋布置良好的固定式蜗杆减速器,其散热面 积可用下式估算:
A 9 105 a1.88 m2 式中a为传动中心距,mm
若t>80℃或有效的散热面积不足时,则必须 采取措施,以提高其散热能力
1
d1n1
m/s
式中:
d1--蜗杆分度圆直径,mm
n1--蜗杆的转速,r/min
(完整版)蜗轮蜗杆-齿轮-齿条的计算及参数汇总

蜗轮蜗杆-齿轮-齿条的计算及参数汇总渐开线齿轮有五个基本参数,它们分别是:名称符号意义标准化数值齿数(teeth number)Z 在齿轮整个圆周上轮齿的总数称为齿数模数(module)m齿距分度圆齿距p与π的比值模数决定了齿轮的大小及齿轮的承载能力。
我国规定标准化模数压力角(特指分度圆压力角)(pressure angle)决定渐开线齿形和齿轮啮合性能的重要参数我国规定标准化压力角为20度齿顶高系数齿顶高计算系数:我国规定标准化齿顶高系数为1顶隙系数顶隙(clearance)计算系数我国规定标准化顶隙系数为0.25标准齿轮:模数、压力角、齿顶高系数、顶隙系数为标准值,且分度圆上的齿厚等于齿槽宽的渐开线齿轮。
我国规定的标准模数系列表第一系列0.10.120.150.20.250.30.40.50.60.81 1.25 1.52 2.534568 10121620253240 50第二系列0.350.70.9 1.75 2.25 2.75(3.25) 3.5(3.75) 4.5 5.5 (6.5)78(11)14182228(30)3645注:选用模数时,应优先采用第一系列,其次是第二系列,括号内的模数尽可能不用.系列(1)渐开线圆柱齿轮模数(GB/T 1357-1987)第一系列0.1 0.12 0.15 0.2 0.25 0.3 0.4 0.5 0.6 0.8 11.25 1.5 22.5 3 4 5 6 8 10 12 16 20 25 32 40 50第二系列0.35 0.7 0.9 0.75 2.25 2.75 (3.25)3.5 (3.75) 4.55.5 (6.5)7 9 (11)14 18 22 28 (30)36 45(2)锥齿轮模数(GB/T 12368-1990)0.4 0.5 0.6 0.7 0.8 0.9 1 1.125 1.25 1.375 1.5 1.75 2 2.25 2.5 2.75 3 3.25 3.5 3.75 4 4.5 5 5.5 6 6.5 7 8 910 11 12 14 16 18 20 22 25 28 30 32 36 40 45 50注: 1.对于渐开线圆柱斜齿轮是指法向模数。
蜗轮蜗杆的传动比计算公式
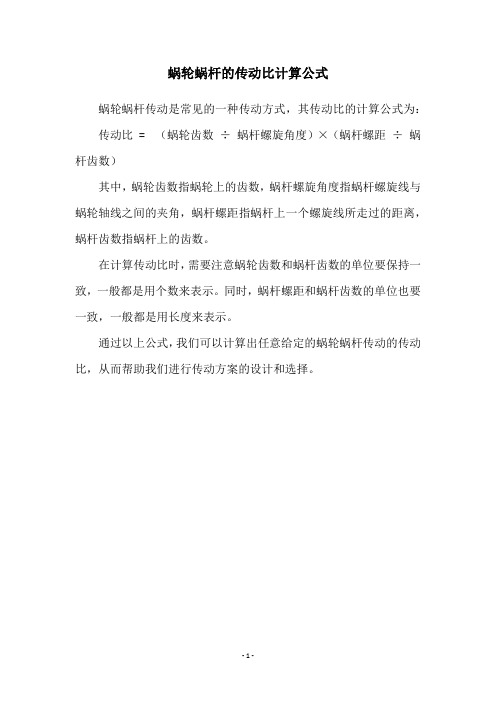
蜗轮蜗杆的传动比计算公式
蜗轮蜗杆传动是常见的一种传动方式,其传动比的计算公式为:传动比 = (蜗轮齿数÷蜗杆螺旋角度)×(蜗杆螺距÷蜗杆齿数)
其中,蜗轮齿数指蜗轮上的齿数,蜗杆螺旋角度指蜗杆螺旋线与蜗轮轴线之间的夹角,蜗杆螺距指蜗杆上一个螺旋线所走过的距离,蜗杆齿数指蜗杆上的齿数。
在计算传动比时,需要注意蜗轮齿数和蜗杆齿数的单位要保持一致,一般都是用个数来表示。
同时,蜗杆螺距和蜗杆齿数的单位也要一致,一般都是用长度来表示。
通过以上公式,我们可以计算出任意给定的蜗轮蜗杆传动的传动比,从而帮助我们进行传动方案的设计和选择。
- 1 -。
涡轮传动
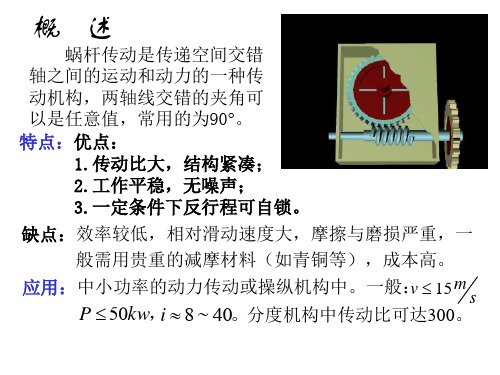
弹性系数,铜或铸铁蜗轮与 钢蜗杆组合时ZE 160 MPa
接触线长度,mm
利用赫兹公式、考虑蜗杆传动特点
将Fn T 2、d2;再L0、、d2 a得:
接触系数,查P253图11-18
校核式:
H ZEZ
KT2 a3
[ H ] MPa
蜗轮齿面的许用接触应力,查P253 [ ]H KHN [ ]H
方向相同 径向力:啮合点指向轴线
轴向力:轴向指向工作齿 廓侧
轴向力亦可视主动轮的螺旋线旋向采用左手或右手定则: 左旋蜗杆用左手法则 右旋蜗杆用右手法则
弯曲四指为转动方向、大拇指指向为 Fa1 方向
例:力的方向判断
Ft1 Fr1
Ft2
Fa1
Fa2 注意:
Fr2
一对啮合的蜗杆蜗轮的旋向相同
三
四. 圆柱蜗杆传动的强度计算
vs小时,蜗杆下置
有利于润滑
蜗杆线速度 v1 4m / s 时,蜗杆上置由蜗轮 带油润滑。
避免过大的搅油损失
• 相对速度高 vs 5 ~ 10m / s ,采用压力喷油润滑。 润滑油量:蜗杆下置时,浸油深度为蜗杆的一个齿高。
蜗杆上置时,浸油深度约为蜗轮外径的1/3。
三. 蜗杆传动的热平衡计算
载荷变化较大或有冲击、
振动时:K 1.3 ~ 1.6
设计式 :
a
3
KT2
(
ZE
[
Z
H
]
)2
mm
说明
设计出a 后,根据传动比按表11-2标准化, 并确定相应的蜗杆、蜗轮参数。
蜗轮齿根弯曲疲劳强度 由于齿形的原因,通常蜗轮轮齿的弯曲强度比
接触强度大得多,所以只是在受强烈冲击、z2较多 (z290)或开式传动中计算弯曲强度才有意义。
蜗轮蜗杆尺寸计算公式
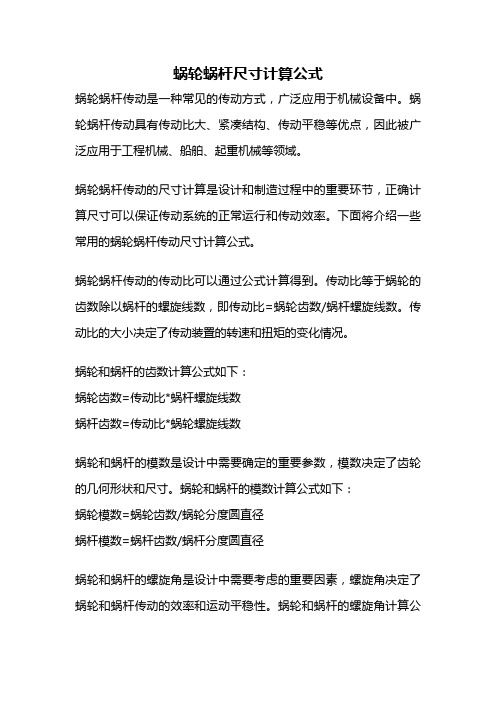
蜗轮蜗杆尺寸计算公式蜗轮蜗杆传动是一种常见的传动方式,广泛应用于机械设备中。
蜗轮蜗杆传动具有传动比大、紧凑结构、传动平稳等优点,因此被广泛应用于工程机械、船舶、起重机械等领域。
蜗轮蜗杆传动的尺寸计算是设计和制造过程中的重要环节,正确计算尺寸可以保证传动系统的正常运行和传动效率。
下面将介绍一些常用的蜗轮蜗杆传动尺寸计算公式。
蜗轮蜗杆传动的传动比可以通过公式计算得到。
传动比等于蜗轮的齿数除以蜗杆的螺旋线数,即传动比=蜗轮齿数/蜗杆螺旋线数。
传动比的大小决定了传动装置的转速和扭矩的变化情况。
蜗轮和蜗杆的齿数计算公式如下:蜗轮齿数=传动比*蜗杆螺旋线数蜗杆齿数=传动比*蜗轮螺旋线数蜗轮和蜗杆的模数是设计中需要确定的重要参数,模数决定了齿轮的几何形状和尺寸。
蜗轮和蜗杆的模数计算公式如下:蜗轮模数=蜗轮齿数/蜗轮分度圆直径蜗杆模数=蜗杆齿数/蜗杆分度圆直径蜗轮和蜗杆的螺旋角是设计中需要考虑的重要因素,螺旋角决定了蜗轮和蜗杆传动的效率和运动平稳性。
蜗轮和蜗杆的螺旋角计算公式如下:蜗轮螺旋角=tan(蜗轮摩擦角)蜗杆螺旋角=arctan(tan(蜗轮摩擦角)/传动比)蜗轮和蜗杆的分度圆直径是设计中需要确定的重要参数,分度圆直径决定了蜗轮和蜗杆齿轮的尺寸。
蜗轮和蜗杆的分度圆直径计算公式如下:蜗轮分度圆直径=蜗轮模数*蜗轮齿数蜗杆分度圆直径=蜗杆模数*蜗杆齿数蜗轮和蜗杆的齿顶圆直径、齿根圆直径、齿宽等尺寸也需要进行计算。
这些尺寸的计算公式可以根据具体的设计要求和传动装置的工作条件来确定。
蜗轮蜗杆传动的尺寸计算是设计和制造过程中的关键环节。
通过合理的尺寸计算,可以确保传动装置的正常运行和传动效率。
在实际应用中,还需要考虑材料的选择、加工工艺的确定等因素,以确保传动装置的质量和可靠性。
蜗杆蜗轮分度圆计算公式

蜗杆蜗轮分度圆计算公式蜗杆蜗轮传动是一种常见的传动形式,它具有传动比大、传动平稳、噪音小等优点,在工业生产中得到了广泛的应用。
蜗杆蜗轮的设计与计算是蜗杆蜗轮传动的关键,其中蜗杆蜗轮的分度圆计算是设计中的重要环节。
本文将介绍蜗杆蜗轮分度圆的计算公式及其相关知识。
蜗杆蜗轮的分度圆是指蜗轮上的分度圆,它决定了蜗轮的齿数、齿廓等重要参数。
蜗杆蜗轮的分度圆计算公式主要包括蜗杆分度圆的计算和蜗轮分度圆的计算两部分。
首先是蜗杆分度圆的计算。
蜗杆的分度圆直径可以通过以下公式计算:d = m z。
其中,d为蜗杆分度圆直径,m为模数,z为蜗杆的齿数。
模数是蜗杆蜗轮传动中的重要参数,它是齿轮的模型参数,表示齿轮齿数与分度圆直径的比值。
通过选择合适的模数,可以满足传动的强度、精度和传动比等要求。
接下来是蜗轮分度圆的计算。
蜗轮的分度圆直径可以通过以下公式计算:D = m z。
其中,D为蜗轮分度圆直径,m为模数,z为蜗轮的齿数。
与蜗杆分度圆类似,蜗轮的分度圆直径也是通过模数和齿数来计算的。
在实际设计中,需要根据传动比、工作条件等因素来选择合适的模数和齿数,以满足设计要求。
除了分度圆直径的计算公式外,还需要考虑蜗杆蜗轮的齿廓参数。
蜗杆蜗轮的齿廓是蜗杆蜗轮传动中的重要参数,它直接影响着传动的效率和精度。
在实际设计中,需要根据蜗杆蜗轮的齿廓参数来确定蜗杆和蜗轮的齿形,以保证传动的平稳性和精度。
总之,蜗杆蜗轮的分度圆计算是蜗杆蜗轮传动设计中的重要环节,它直接影响着传动的性能和可靠性。
通过合理的计算公式和参数选择,可以设计出性能优良的蜗杆蜗轮传动装置,满足工程应用的要求。
希望本文介绍的蜗杆蜗轮分度圆计算公式及相关知识能够对蜗杆蜗轮传动的设计和应用有所帮助。
蜗轮蜗杆的设计及其参数计算

7 蜗轮蜗杆的设计及其参数计算5.1 传动参数蜗杆输入功率P=5.3 kW ,蜗杆转速min /r 960n 1=,蜗轮转速m i n /r 5.56n 2=,理论传动比i=16.75,实际传动比i=17,蜗杆头数2Z 1=,蜗轮齿数为34217 Z i Z 12=⨯==,蜗轮转速min /r 5.5617960i n n 12=== 5.2 蜗轮蜗杆材料及强度计算减速器的为闭式传动,蜗杆选用材料45钢经表面淬火,齿面硬度 >45 HRC,蜗轮缘选用材料ZCuSn10Pb1,砂型铸造。
蜗轮材料的许用接触应力,由《机械设计基础》表4-5可知,[]H σ=180MPa. 估取啮合效率: 10.8η= 蜗轮轴转矩:6651122 5.250.89.55109.55107.110mm n 56.5P T N η⨯=⨯=⨯⨯=⨯⋅ 载荷系数:载荷平稳,蜗轮转速不高,取K=1.1.计算21m d 值 []22122480m d HKT Z σ⎛⎫≥⎪ ⎪⎝⎭=2534801.17.110mm 34180⎛⎫⨯⨯⨯ ⎪⨯⎝⎭=34804mm模数及蜗杆分度圆直径由《机械设计基础》表4-1取标准值,分别为: 模数 m=8 mm蜗杆分度圆直径 1d 80m m = 5.3 计算相对滑动速度与传动效率蜗杆导程角11mz 82=arctanarctan 11.31d 80γ⨯==蜗杆分度圆的圆周速度111d n 80960m /s 4.02m /s 601000601000ππυ⨯⨯===⨯⨯相对活动速度1s 4.024.098m/s cos cos11.31υυγ===当量摩擦角 取v 230 2.5ρ== 验算啮合效率()()1v tan tan11.31081tan tan 11.31 2.5γηγρ===++(与初取值相近)。
传动总效率10.960.960.810.78ηη==⨯=总 (在表4-4所列范围内)。
蜗杆传动的失效形式和计算准则

第一讲一、教学目标(一)能力目标1.能计算蜗杆传动的几何尺寸2.掌握蜗杆传动的失效形式和设计准则(二)知识目标1.了解蜗杆传动特点、类型及主要参数2.掌握蜗杆传动几何尺寸的计算3.掌握蜗杆传动的失效形式和设计准则二、教学内容1.蜗杆传动的类型及特点2.蜗杆传动的失效形式、材料和结构3.普通圆柱蜗杆传动的主要参数和几何尺寸计算三、教学的重点与难点重点:蜗杆传动的失效形式和设计准则。
难点:蜗杆传动的主要参数。
四、教学方法与手段采用多媒体教学(动画演示运动),结合教具,提高学生的学习兴趣。
11.1 蜗杆传动的类型和特点蜗杆传动由蜗杆和蜗轮组成。
用于传递空间交错的两轴间运动和功率,一般交错角为90º,蜗杆为从动件。
11.1.1 蜗杆传动的类型按蜗杆形状分:圆柱蜗杆机构——普通、圆弧环面蜗杆机构锥蜗杆机构按蜗杆齿廓曲线的形状阿基米德圆柱蜗杆(最常用)渐开线圆柱蜗杆(梯形部分为渐开线)延伸渐开线蜗杆锥面包络圆柱蜗杆11.1.2 蜗杆传动的特点1、传动平稳由于蜗杆的齿是连续的螺旋形齿,传动平稳,噪声也小;2、传动比大在一般传动中,i=10~80,在分度机构中可达1000,故结构紧凑;3、能够自锁当蜗杆的导程角小于当量摩擦角时,蜗杆能带动蜗轮,而蜗轮不能带动蜗杆,即自锁。
可用于需要自锁的起重设备,如手动葫芦等;4、效率低蜗杆传动中,蜗轮齿沿蜗杆齿的螺旋线方向滑动速度大,摩擦剧烈,效率=0.7~0.9;低,一般蜗杆传动的效率5、为减少蜗杆传动中的摩擦,蜗轮常用减摩性好但较贵的青铜制造,成本较高。
11.2 蜗杆传动的主要参数和几何尺寸的计算在蜗杆传动中,规定通过蜗杆轴线并与蜗轮轴线垂直的平面,称为中间平面。
对于阿基米德蜗杆蜗轮,在主平面内蜗杆传动相当于齿轮齿条传动。
11.2.1 蜗杆传动的主要参数及其选择1、蜗杆头数z1、蜗轮齿数z2和传动比i传动比i=n1/n2=z1/z2蜗杆头数z1=1、2、4、6(单头,i大,易自锁,效率低,但精度好;多头杆,η↑,但加工困难,精度↓)蜗轮齿数z2=iz1,Z2=27~802、模数和压力角为了保证蜗杆轮齿与蜗轮轮齿的正确啮合,蜗杆的轴向模数1a m 和轴向压力角1a α,应分别等于蜗轮的端面模数2t m 和端面压力角2t α,且均等于标准值,同时蜗杆分度圆上的导程角λ应等于蜗轮分度圆上的螺旋角β。
- 1、下载文档前请自行甄别文档内容的完整性,平台不提供额外的编辑、内容补充、找答案等附加服务。
- 2、"仅部分预览"的文档,不可在线预览部分如存在完整性等问题,可反馈申请退款(可完整预览的文档不适用该条件!)。
- 3、如文档侵犯您的权益,请联系客服反馈,我们会尽快为您处理(人工客服工作时间:9:00-18:30)。
*****直廓环面蜗杆传动几何计算*****
--------------------------------------------------------------
蜗杆类型: 不等齿厚
中心距(mm) A= 250.0
蜗轮端面模数(mm) mt= 12.6875
蜗杆头数 z1= 2
蜗轮齿数 z2= 32
蜗杆包围蜗轮齿数 zk= 3
速比 i= 16.0
分度圆压力角 (度) α= 24.7538
齿顶高系数 ha*= 0.7
顶隙系数 cn*= 0.2
齿顶间隙(mm) c= 2.5375
--------------------------------------------------------------
蜗杆分度圆导程角 γ= 15° 6′ 24″
蜗杆成形圆直径(mm) db1= 170.0
蜗杆分度圆直径(mm) d1= 94.0
蜗轮分度圆直径(mm) d2= 406.0
蜗杆齿顶圆直径(mm) da1= 111.7625
蜗轮齿顶圆直径(mm) da2= 423.7625
蜗杆齿根圆直径(mm) df1= 71.1625
蜗轮齿根圆直径(mm) df2= 383.1625
齿顶高(mm) ha= 8.8813
齿全高(mm) h = 20.3
蜗轮齿宽(mm) b2= 70.0
蜗杆齿顶圆弧半径(mm) ra1= 194.1188
蜗杆齿根圆弧半径(mm) rf1= 214.4188
蜗杆外圆最大直径(mm) de1= 125.0178
蜗杆根圆最大直径(mm) di1= 95.2675
齿距角(度) px-ang= 11.25
蜗杆工作包容半角(度) faw= 14.3438
蜗杆工作长度(mm) lw= 100.582
齿根圆角半径(mm) pf= 2.5375
齿顶倒角尺寸(mm) ca= 1.5225
蜗杆齿厚半角(度) gama1= 2.5313
蜗轮齿厚半角(度) gama2= 3.0938
蜗杆轴向平面齿形半角(度) a1= 27.285
蜗轮齿形半角(度) a2= 21.6854
端面齿侧间隙半角(度) anj= 0.0254
蜗杆螺纹全长(mm) l= 112.0
蜗杆法向弦齿厚测齿高(mm) hn1= 8.6367
蜗轮法向弦齿厚测齿高(mm) hn2= 9.1258
蜗杆中间平面法向弦齿厚 sn1= 17.2984
蜗轮中间平面法向弦齿厚 sn2= 21.1545
--------------------------------------------------------------
蜗杆螺纹入口修形量(mm) △f= 0.4
中心角(度) γk= 19.125
原始齿形入口角(度) γ'k= 6.3113
原始齿形出口角(度) γ''k= 12.8138
入口倒坡角(度) γa= 8.0325
出口倒坡角(度) γb= 7.155