铜精炼渣鼓风炉还原熔炼实践
铜精炼反射炉的生产和实践

铜精炼反射炉的生产和实践一、概述二、铜火法精炼的氧化过程三、铜火法精炼的还原过程四、铜火法精炼炉的结构五、铜火法精炼炉的供热六、铜火法精炼炉的生产实践1.生产作业2.事故处理3.开停炉4.产物5.技术经济指标铜精炼反射炉的生产和实践一、概述铜精炼反射炉的原料为矿石粗铜、再生杂铜、不同渠道获得的各类铜锭等。
入炉原料除含硫、氧外,还含有一些其它杂质。
如砷、锑、铅、锌、锡、铁、钴、镍等,此外尚含有硒、碲、铋、金、银等稀有金属。
通常情况下,将铜料在铜精炼炉中进行火法精炼,产出Cu≥99.8%的阳极板,在进行电解精炼,产出Cu≥99.95%的电解铜。
最后从阳极泥中将稀贵金属提取出来。
铜火法精炼为间歇(周期)作业,分为加料熔化、氧化、还原、铸型五个阶段,每炉作业周期一般小于24小时,最快12小时。
由于各工厂所处理的原料成分差异很大,所以氧化期的操作方法有不同之处,但基本原理相同。
二、铜火法精炼的氧化过程完成加料、熔化作业,进入氧化阶段。
用氧化管将压缩空气通入铜熔体,铜首先氧化:4Cu(液)+O2(气)=2Cu2O(液)铜氧氧化亚铜生成的氧化亚铜立即溶解在铜熔体中。
氧化亚铜在铜熔体中的溶解液。
随着温度升高而升高,如下表:氧化亚铜在铜熔体中的溶解度温度1150 1200 1250 1300(℃)Cu2O溶8.3 12.4 13.1 13.8解度(%)相当氧0.73 1.38 1.48 1.52含量(%)正常氧化温度约为1200℃,此温度条件下,熔体中Cu2O含量超过12.4%时,熔体将分为两层,下层为饱和Cu2O的铜熔体,上层为析出的Cu2O。
生产控制氧化亚铜不可过量饱和,以防止造成渣含铜增高等恶果。
溶解在铜熔体的氧化亚铜起着氧化剂的作用,去氧化对氧的亲和力大于铜对氧的亲和力的金属杂质Me’被氧化:Cu2O + Me’ = Me’O + 2Cu氧化亚铜金属杂质杂质氧化物铜为使化学反应顺利进行(化学平衡向右移动),氧化过程中如下控制:1、增加Cu2O浓度:适当提高温度,使Cu2O在铜熔体中尽可能的达到饱和。
铜精矿的熔炼反射炉
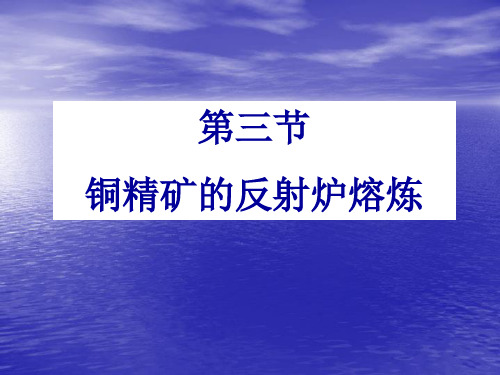
(2)采用预热空气。
(3)采用富氧。
26
单元作业
1、简述反射炉熔炼的缺点。
2、影响反射炉生产率的关键因素是什么?
27
2
一、概述
第一台炼铜反射炉始于1879年,此后,反射炉
炼铜迅速发展,在20世纪60年代达到顶峰,其产量
达到世界铜总产量的70%。但反射炉熔炼有它难以 克服的缺点,如能耗高、环境污染严重等,这些缺 点制约了它的发展。到20世纪70年代,以闪速熔炼 为代表的低能耗、高效率、低污染的现代熔炼方法
迅速崛起,致使反射炉熔炼逐渐被新的炼铜方法取
处理焙烧矿时,大部分铅进入炉渣,少量
进入冰铜,约20%的铅挥发排出。
14
镍和钴的行为与铜相似,均以硫化物形态 进入冰铜中。
大量的As、Sb、Bi、Sn和Te也进入冰铜中,
在冰铜吹炼及粗铜精炼时加以回收。
15
5、反射炉熔炼的产物
反射炉熔炼的产物是冰铜、炉渣、烟尘及
烟气。
反射炉的烟尘量一般为入炉物料量的1.3 ~ 1.5%。 采用空气燃烧时,反射炉熔炼烟气的成分一般 为,%:CO215~18;SO21~2;O20.5~1.2;CO
的表面温度的关系最大。
9
炉气的温度主要取决于燃料的发热量,燃
烧时的过剩空气系数等等。 炉料的温度主要取决于炉料的熔点。 对于一定成分的炉料,熔点是一定的,所 以,炉气温度是决定炉子生产率的关键因素。
反射炉内传热过程是非常复杂的,影响传热的
因素甚多,但是其中最主要的还是燃料燃烧即
炉气温度。
10
2、主要的化学反应
(1)选择合理渣型; (2)使炉渣充分过热,使冰铜、炉渣良好分离; (3)严格控制冰铜面,减少随渣损失; (4)稳定冰铜品位;
冶炼厂鼓风炉炉渣含钙、铜高低研析

The Judgment of Calcium and Copper Content of Blast Furnace Slag of Smelter
SU Fenglai (Zijin Mining Group COMMUS SAS, Kolowezi, Congo (Kinshasa)) Abstract: This paper summarizes the production practice of Zijin Mining Group COMMUS SAS since it was put into operation for three years, and puts forward a method to judge the calcium and copper content of the slag by the physical characteristics of the slag (slag temperature, slag fluidity, slag color, etc.), so as to provide guidance for the closed blast furnace smelting practice of copper oxide concentrate in Congo (Kinshasa). Keywords: copper oxide concentrate; slag type; calcium content; copper content
(CaO • 2SiO2)存在。也就是说,若炉渣中没有游离 的二氧化硅,则炉渣的表面就不会出现光面。 3.2渣含铜的判断
在正常的操作条件下,人们可以根据水淬渣的 颜色来判断炉渣含铜的高低。炉渣含铜由高到低的颜 色变化如下:黑红(V 0.6% )—暗红(0.6% ~ 1.0%) -艳红(> 1.0%)。人们可以根据炉渣的颜色恰当
铜密闭鼓风炉熔炼技术操作条件
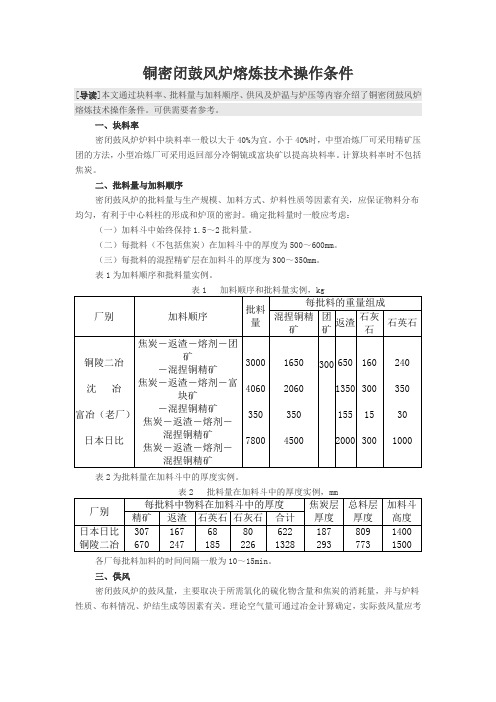
密闭鼓风炉的批料量与生产规模、加料方式、炉料性质等因素有关,应保证物料分布均匀,有利于中心料柱的形成和炉顶的密封。确定批料量时一般应考虑:
(一)加料斗中始终保持1.5~2批料量。
(二)每批料(不包括焦炭)在加料斗中的厚度为500~600mm。
(三)每批料的混捏精矿层在加料斗的厚度为300~350mm。
铜密闭鼓风炉熔炼技术操作条件
[导读]本文通过块料率、批料量与加料顺序、供风及炉温与炉压等内容介绍了铜密闭鼓风炉熔炼技术操作条件。可供需要者参考。
一、块料率
密闭鼓风炉炉料中块料率一般以大于40%为宜。小于40%时,中型冶炼厂可采用精矿压团的方法,小型冶炼厂可采用返回部分冷铜锍或富块矿以提高块料率。计算块料率时不包括焦炭。
340
420
470
烟气单体硫含量,g/m³0.78
0.35
密闭鼓风炉炉顶负压过高,漏入空气量增加,降低了烟气中二氧化硫浓度。但负压过低又会造成炉顶操作条件恶化,一般控制在50~100Pa为宜。表11为炉顶负压与烟气二氧化硫浓度的测定值。
表11 炉顶负压与烟气二氧化硫浓度的测定值
㎡
t/(㎡·d)
m³/min
%
m³/(㎡·d)
m³/t
10.5
38~45
390~400
21
30~38
~1400
10
40~45
330~400
21
33~40
~1240
2
40~45
75~80
21
38~40
~1320
1.5
45~50
50~55
21
33~37
~1060
2、风压 密闭鼓风炉的鼓风压力主要取决于炉内阻力,在一定范围内增加风压对熔炼过程有利。但风压过高会增加烟尘率和料层穿孔而跑空风。目前各厂的鼓风压力一般控制在8~10kPa。表4为鼓风压力实例。
铜矿的熔炼工艺与冶炼设备

感谢您的观看
汇报人:
熔炼设备:包括熔炼炉、鼓风机、冷却塔等设备
熔炼过程中的化学反应:包括氧化还原反应、硫化反应等化学反应
铜矿的熔炼过程
矿石准备:将 铜矿石破碎、 研磨、混合,
制成矿粉
熔炼反应:将 矿粉与熔剂、 燃料等混合, 在高温下进行
熔炼反应
熔融提取:将 熔融后的铜液 与熔渣分离,
提取铜液
精炼提纯:将 提取的铜液进 行精炼提纯,
熔炼炉:用于铜矿的熔炼,提高铜的纯 度
电解槽:用于铜的电解,提高铜的纯度
冷却设备:用于铜的冷却,防止铜的氧 化
净化设备:用于铜的净化,去除铜中的 杂质
铸锭设备:用于铜的铸锭,便于运输和 储存
检测设备:用于铜的质量检测,确保产 品质量
铜矿的冶炼设备发展趋势
节能环保:提高能源利用率,减少废气、废水、废渣等污染物排放
自动化与智能化:采用先进的自动化和智能化技术,提高生产效率和产品质量
提高设备使用寿命:通过改进设备材料和工艺,提高设备的耐腐蚀、耐磨损等性能,延长设备使 用寿命
降低生产成本:通过优化设备设计和生产工艺,降低设备投资和运行成本,提高企业经济效益
铜矿的熔炼工艺 与冶炼设备的比 较与选择
铜矿的熔炼工艺与冶炼设备的比较
得到纯铜
铜矿的熔炼方法
火法熔炼:通过高温加热,使铜矿中 的金属元素与氧、硫等元素发生化学 反应,生成熔融状态的金属和熔渣。
电炉熔炼:利用电能产生高温,使铜 矿中的金属元素与氧、硫等元素发生 化学反应,生成熔融状态的金属和熔 渣。
添加标题
添加标题
添加标题
添加标题
湿法熔炼:利用酸、碱等化学试剂, 将铜矿中的金属元素溶解,然后通 过电解、化学沉淀等方法提取金属。
炼铜炉渣选矿的工艺研究与生产实践

炼铜炉渣选矿的工艺研究与生产实践一.炼铜炉渣的几种主要类型目前进入磨浮法选矿贫化的炉渣,按冶炼方式不同,可分为:熔炼渣(如诺兰达炉)、吹炼渣(如转炉)、还原渣(如电炉)等;按炉渣冷却方式不同,可分为:渣包缓冷渣、铸渣机铸渣、自然冷渣以及水淬急冷渣等,通常情况下,吹炼渣含铜品位较高,其次是熔炼渣,还原贫化渣最低,一般在1%以下。
二.影响渣选指标的主要因素1、炼铜炉渣自身特性的影响1)、相比之下,吹炼渣子高氧势氛围产生,渣中铜呈金属态甚至于氧化态度比例相当较多,金属态度铜难磨细,比重又大,造成浮选困难,影响指标;氧化态的铜与硫化铜相比,可选性变差。
熔炼渣的可选性相对改善。
还原贫化渣,渣保持较好的还原氛围的前提下,可选性会进一步改善。
在冶炼过程中由于操作条件的变化会影响熔炼渣的组成成分和结构,从而影响选别效果。
当熔炼渣过氧化时,会生产大量的氧化亚铜,将会使熔炼渣的铜回收率显著降低。
对过氧化渣的物相和粒度分析表明,其硫化铜含量降低,磁性铁含量增加,铜相对细粒级含量比例增大,这些情况的出现不利于浮选分离。
2)、炉渣成分的影响实践和分析表明,炉渣中铜品位高低,与选铜指标呈很强大正相关系,即炉渣中铜品位越高,其选铜指标相对越好,反之也然。
研究表明,如果冶炼工序采用“高铁渣型”,有益于渣选铜回收率达提高,同时,炉渣中SiO2含量对选铜也有影响,即SiO2越高对选铜指标越不利。
3)、炉渣冷却方式的影响渣包冷却渣可选性最好,铸渣机铸渣和自然冷渣较差,水淬急冷渣最差。
让热液态炉渣充分缓冷,有利于渣中硫化态或金属态铜颗粒凝聚和长大,便于通过磨矿解离和浮选分离。
生产实践中,用渣包缓冷渣入选已经成为趋势。
同样是渣包缓冷渣,但由于缓冷过程控制不同,也会明显影响选别指标,表1列出了不同冷却条件对转炉渣选铜效果的影响。
表1. 不同冷却条件对铜熔炼渣选别效果的影响4)、磨浮工艺控制的影响影响渣选的磨浮工艺控制因素较多,归纳起来主要有:流程方案、磨矿效果、浮选药剂及用量、浮选矿浆浓度及浮选时间等。
关于铜冶炼炉渣处理的研究
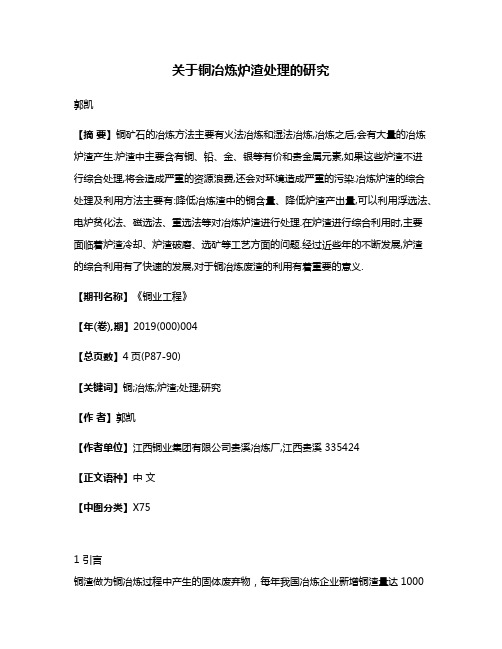
关于铜冶炼炉渣处理的研究郭凯【摘要】铜矿石的冶炼方法主要有火法冶炼和湿法冶炼,冶炼之后,会有大量的冶炼炉渣产生.炉渣中主要含有铜、铅、金、银等有价和贵金属元素,如果这些炉渣不进行综合处理,将会造成严重的资源浪费,还会对环境造成严重的污染.冶炼炉渣的综合处理及利用方法主要有:降低冶炼渣中的铜含量、降低炉渣产出量,可以利用浮选法、电炉贫化法、磁选法、重选法等对冶炼炉渣进行处理.在炉渣进行综合利用时,主要面临着炉渣冷却、炉渣破磨、选矿等工艺方面的问题.经过近些年的不断发展,炉渣的综合利用有了快速的发展,对于铜冶炼废渣的利用有着重要的意义.【期刊名称】《铜业工程》【年(卷),期】2019(000)004【总页数】4页(P87-90)【关键词】铜;冶炼;炉渣;处理;研究【作者】郭凯【作者单位】江西铜业集团有限公司贵溪冶炼厂,江西贵溪 335424【正文语种】中文【中图分类】X751 引言铜渣做为铜冶炼过程中产生的固体废弃物,每年我国冶炼企业新增铜渣量达1000万t左右,显现逐年递增现象。
铜渣的简单堆存不仅占用土地、而且污染周边环境,造成资源的浪费,铜渣中铜含量一般可以达到1.2%左右。
中国属于铜矿石短缺国家,对于铜渣中有价金属回收、并进行综合利用,有着重要的意义[1]。
2 炉渣的成分组成铜冶炼炉渣是指在铜冶炼过程中产生的含铜炉渣,根据冶炼生产工艺的不同可分为熔炼渣、转炉渣和电炉渣等;根据炉渣冷却方式的不同分为水淬渣、自然冷却渣、保温冷却渣等。
铜冶炼渣主要是冰铜熔炼渣和转炉渣,其中转炉渣冰铜是经转吹炉吹炼而产出并由铸渣机缓冷铸出的渣分,其品位高于其他炉渣[2]。
铜冶炼炉渣经铸渣机冷铸后,渣表结构致密,性脆坚硬、易碎难磨,颜色呈现出黑色或者黑中透绿,铜品位约为2%~7%,密度约为4g/cm3左右。
炉渣中的铜及其含铜化合物分布不均,且粒度较细大部分以硫化铜形式存在,还伴随有方辉铜矿、辉铜矿、黄铜矿、斑铜矿、金属铜、氧化铜和铜的含铁硅酸盐等。
1.3 造锍熔炼生产实践

完成造渣和造冰铜过程 本床区 炉渣与冰铜成分相互调整,少量的Cu2O被再硫化
铜精矿的密闭鼓风炉熔炼
——密闭鼓风炉炼铜的基本原理(I) 密闭鼓风炉炼铜的基本原理( ) 密闭鼓风炉炼铜的基本原理
(2) 炉顶温度较高(500~650℃) (3) 炉气穿过料层和炉料不断下移,使传热传质都比反射炉好, 热利用率和脱硫率高 (4)主要氧化反应是铁的硫化物氧化 (5) 鼓风炉的焦炭燃料完全作为加热剂,其燃烧热约占全部热 收入的60%。
闪速熔炼的原理
闪速熔炼的实质是将干精矿与氧气、 闪速熔炼的实质是将干精矿与氧气、预热空气 或二者的混合物一起吹入高温反应炉内, 或二者的混合物一起吹入高温反应炉内,硫化 物颗粒立即与周围的氧化性气体发生反应, 物颗粒立即与周围的氧化性气体发生反应,同 时放出大量的热, 时放出大量的热,利用这个热作为熔炼所需的 大部发生相互反应, 大部发生相互反应,完成造冰铜和造渣的过 然后分别从放冰铜口和放渣口放出。 程,然后分别从放冰铜口和放渣口放出。 目前闪速熔炼法的产铜量占铜总产量的30%以 目前闪速熔炼法的产铜量占铜总产量的 以 上
闪速熔炼的精矿干燥
铜冶炼厂进厂铜精矿含水一般为8%~15%。 。 铜冶炼厂进厂铜精矿含水一般为 冶炼前的配料作业、 冶炼前的配料作业、冶炼过程中及冶炼烟气制酸 都对精矿含水有一定要求。 都对精矿含水有一定要求。 在配料过程中,若含水高,精矿易粘结, 在配料过程中,若含水高,精矿易粘结,会影 响配料精度。因此, 响配料精度。因此,配料前的精矿含水一般控制 以下, 在10%以下,必要时可增加预干燥设备。 以下 必要时可增加预干燥设备。
铜精矿的密闭鼓风炉熔炼
——密闭鼓风炉炼铜的基本原理(I) 密闭鼓风炉炼铜的基本原理( ) 密闭鼓风炉炼铜的基本原理
- 1、下载文档前请自行甄别文档内容的完整性,平台不提供额外的编辑、内容补充、找答案等附加服务。
- 2、"仅部分预览"的文档,不可在线预览部分如存在完整性等问题,可反馈申请退款(可完整预览的文档不适用该条件!)。
- 3、如文档侵犯您的权益,请联系客服反馈,我们会尽快为您处理(人工客服工作时间:9:00-18:30)。
铜精炼渣鼓风炉还原熔炼实践 7· 铜精炼渣鼓风炉还原熔炼实践 西安铜材厂韩瑜瑛 提要本文系统地介绍了鼓风炉处理铜精炼渣的开炉、进料、管理、停炉以及故障排除等经 验,探讨了渣型选择间题。 量压风风 我厂用于还原熔炼铜精炼渣的鼓凤炉为 圆形:风口区截面积0.4m2。炉子下部为4 块轴对称冷却水套,上部铁炉壳内衬耐火 砖,底部为活动式本床。采用罗茨风机供 风。炉料经计量后由加料小车自动_L料人 炉,烟气30%进收尘器回收氧化锌,其余排 空,炉渣水淬后堆放,冷却水循环使用,打 眼放渣出铜‘液体粗铜自流冷却成块,送料 场存放。 我厂鼓风炉主要用千本厂铜阴、阳极炉 所产炉渣的还原熔炼,属间断作业,年处理 渣量800吨左右,开炉时间60多天。经十多 年的反复实践,不断摸素。目前炉子生产情 况良好,工艺日趋完善,炉渣基本定型,各 项指标比较稳定。主要技术经济指标如下: 床能率65吨/米2·日粗铜品位85% 焦率29%弃渣含铜1% 铜直收率95%电耗40度/吨渣 熔剂率23%加工成本10。元/吨渣 300公斤,开风并打开出铜口15分钟,接着 停风炯烧15~20分钟,加入第三批焦炭300 公斤,开风机并再开出铜口15~20分钟,待 出铜口发红,焦炭喷出时停风炯烧15分钟。 炯烧结束后,开风并加人返回渣3~5批,每 批返回料组成为(公斤):焦炭70,鼓风炉渣 160,石灰石5,萤石2。当渣从放铜口流‘出 后,堵住出铜口,加人焦炭150公斤,接着 开始加正规炉料,并准备放渣,加人正规料 10批后,开始放第一次铜。至此开炉已告结 束,接通收尘系统转人正常生产。 (二)正常操作正常作业主要是进 料、排渣、放铜,其工艺操作包括原料、熔 剂、燃料、风口、铜口、渣口、料柱、水套 等的控制。技术条件如下: 料量170公斤/批 焦炭70公斤/批 石灰石40公斤/批 萤石3公斤/批 进料间隔8分钟 放铜间隔10。分钟 放渣间隔 一、鼓风炉还原熔炼的操作 (一)开炉装配炉子各部及配套设 施,检查符合要求后,用木柴生火,加人焦 炭烘烤炉缸24~36小时,并定时清除炉缸内 积灰。 烘烤炉缸结束后,清净余灰,另加木材 引燃,并在缸体上部周围涂好一圈耐火泥, 推进炉底,水平上好四个千斤顶,然后由炉子 上部加入150~200公斤木材,待木材烧旺 时,加人第一批焦炭300公斤,风眼内焦炭 发红时,装上风眼盖头,加入第二批焦炭 料柱高度 水套水温 4分钟 4。米3/分钟 12。毫米汞柱 2一2。5米 40OC 1.进料。炉料入炉前要精心选料,剔 除杂物,捡出大于100毫米块料,筛掉小于 5毫米的碎料,然后按时按量把炉料加人护 内,通常采用分层装料法,装料次序是焦 炭、熔剂、渣料。炉料应装成中间高、四周 低的形状,细料应尽量集中到炉子中间。料 面高
度与炉料的性质有关,一般应低于加料 平面1米左右。 2.凤口照应。在还原熔炼过程中,由 于个别风目常被炉渣或不熔物堵塞,使风目.8, 面积缩小,因此必须按时清除。根据风口状 况的不同,在一定程度上可以判断炉况,炉 况正常时,风口的硅酸窝均匀,并伸进约 100毫米的距离,风口中心温度高,通过凤 口窥视孔可观察到表层有黑色网状渣壳而里 面发亮。当炉况恶化时,则风口硅酸窝不均 匀,风口里外均发红,甚止发黑,风送不进 去。 3.水套管理。水套是鼓风炉比较关键 的设备,.其接触的温度高,易于损坏,在实 际操作中要密切观察水套的进水出水情况, 防止超压或缺水。如遇停泵,立即停风,快 速抢修,防止回水管蒸汽喷射伤人。此外还 要定期排污,经常检查水套、管道有无漏 损,以便及时修补。 4.料柱高度。对于鼓风炉还原熔炼, 保持一定的料柱高度,才能使炉料在炉内有 一定的停留时间和稳定的炉内压力。由于我 厂鼓风炉受炉身长度的限制,在实际生产 中,其高度只能控制在2~2‘.sm,使床能率 不能进,一步提高,且.焦耗较高,同时也是不 、 能连续放渣的主要原因。 5.排渣放铜。放渣口操作是定期排出 炉渣,用耐火泥堵塞,出铜口操作是定期放 出粗铜,用铁棒堵塞,铁棒外可涂少量耐火 泥以免和粗铜粘结时难以抽出,操作时注意 炉缸熔体的高度,防止炉渣倒流风口。 (三)故障及其处理 1.炉结。炉结是鼓风炉还原熔炼的主 要故障。一般随着生产的进行,产生炉结是 不可避免的,问题在于不能让其堆积增长, 以免引起棚料等较大的故障发生。通常防止 炉结生成的方法是:正确配料,减少粉料, 适当降低操作料柱,集中凤口区,发现炉结 应尽早处理(人工敲打铲除),使其逐步熔 化。 2.棚料。棚料现象实际上是高熔点物 质在风口区上方堆积和冻结,从而破坏炉料 正常下降,严重时可迫使停产。产生的原 因:焦炭灰分过高,一般不要超过17%,当 达到20%时就很易产生棚料;铜济原料中含 有大量未燃的粉煤、木炭等引起表面熔化; 炉料难熔成分过多,渣型控制不当。一般在 棚料故障之前是有预兆的,表现在风口温度 低、渣流动性变差。风压升高等。当出现这 种故障时,应立即降低料柱、适当补焦,若 渣型控制不当而产生悬料,则应调整熔剂 量,增加炉渣中硅酸铁的含量,适当加人一 些返料,调整凤管的进风闸口,给温度低的 风管停止进风或减少进风经过调整,可使 棚料消除,恢复正常生产。 3.风口结块。风口结块产生的原因是 渣面太高,或渣的熔点过高,粘度太大。防 止的办法是保持适当的渣面高度,选择熔点 和粘度适当的渣型。如风口已出现结块时, 应及
时用铁钎捣碎。 4.本床结小。本床结小的主要原因是 炉料中5102不足或炉料中金属铁屑过多造成 的,处理办法是适当增大S主02含量,降低用 焦量,控制金属铁屑的含量等来解决。 (四)停炉 1.长期停炉。停止加正规料后,加3~ 5批鼓风炉渣及焦炭洗炉,继续鼓风,直到 出铜口掖体产物极少,并有焦炭吹出时即可 停风。一般炉料全部熔化,渣流流尽约需l~ 2小时。 2.暂时停炉。将料面深度降低0.5米 左右,加300公斤焦炭即可停风,同时关闭 烟道闸门并将液态产物从炉内放出。 二、还原熔炼的渣型探讨 在我厂‘的鼓风炉还原熔炼生产中,炉渣 的好坏直接影响到炉子的正常生产,它决定 了炉子的寿命、焦比和炉温的高低、床能率 的大小和铜的回收率,因此要开好鼓风炉就 必须控制好炉渣渣型。 (下转第24叮矛云., 增加至5.1%左右。 2.随冰镍品位的增加,渣中铁和钙增 加,而冰镍中铁和钙减少,渣和冰镍中的硫 变化都不大.冰镍中的硫稳定在24一25%, 一 渣中的硫在1.5一2%左右‘ 一 3.物相观察表明,冰镍品位愈低,冰 镍与渣相之间的相互溶解愈多,界限愈不清 晰。而品位愈高,两相澄清分离愈好,甚至 照片1冰镍和钙铁氧体渣相放大中间出现断缝。 照片 一 (冰镍品位了0.59%)峨。低冰镍相主要由磁镍铁矿(Fe·Ni) S:,Ni一Fe合金,二者的共晶及渣成分CaO· FeO·Fe20。所构成。高品位冰镍相主 要由Ni3S:,磁镍铁矿,Ni一Fe合金所构成, 并含有少量的渣成分。无论高品位冰镍还是 低品位冰镍,平衡渣相的成分都是由ZCaO· Fe203、CaO·FeO·Fe:05、Fe一Ca一S一O 化合物,及溶解的(Fe·Ni)52,Ni一Fe合金 等冰镍成分所构成。 照片2冰镍和钙铁氧体渣相放大 照片(冰镍品位28.24%) 参考文献 四、结论 1.镍冰铜与钙铁氧体渣之间的平衡研 究表明,随冰镍品位的增加,直到45%,渣 中镍的损失是减少的,从5.2%降至2.6%, 当冰镍品位大于45%时,渣中镍的损失反而 〔1』朴文景、武田要一、矢沉彬,《日本东北 大学选矿制炼研究所学报》,vol.39,1983115. [21CesarAeunaandAkirayazawa,介a一 nsaetionoftheJopanInstituteofMetals,Vol. 27,滩11,1986,P881. 〔3]宇都宫公昭、CesarAcuna、矢汽彬,《日 本东北大学选研所学报,Vol.40,1984,P77. [4]张世波、CosarAeuna、矢派彬,《日本 东北大学选研所学报》,Vo】.40,1984,P144 (上接第8页) 鼓风炉还原熔炼渣是炉料中金属和非金 属氧化物在熔炼过程中形成的复杂共熔体, 510,一cao一Feo是炉渣的基本体系。我厂 鼓风炉还原熔炼渣经反复试验,‘不断总结, 现采用了乳O::CaO=l,l的比例、F,Q不 大于15%的中性渣型,在实践中证明其 技术经济效果是比较好的。同时在还原熔炼 过程中加人一定数量的萤石,改善了渣的
流 动性,在实践第一的基础上摸素蓦结出了我 J一鼓风炉还原熔炼炉渣的基本规律。内容如