涡电流检测工件表面裂纹
涡电流原理及探伤技术介绍

四、涡电流探伤检测技术
(一)涡电流传感器的基本工作原理 1.当把通有交变电流的线圈(激磁线圈)靠近 导电物体时,线圈产生的交变磁场会在导电体中感 应出涡电流,该涡电流的分布及大小除了与激磁条 件有关外,还与导电体本身的电导率、磁导率、导 电体的形状与尺寸、导电体与激磁线圈间的距离、 导电体表面或近表面缺陷的存在或组织变化等都 有密切关系.涡电流本身也要产生交变磁场。
二、涡电流的产生
1.涡电流产生的基本电路
2.交流电的振幅与相位
頻率:f × 106Hz 角頻率:ω=2πf=2π/T 單位時間所繞的徑度 (rad/s) 正弦波的交流電流:i=I0Sinωt i:交流電瞬時值 I0:交流電最大值,即振幅 ωt:表示在時間t,交流電之相位 同理正弦波的交流電壓亦可表示為 υ=V0Sinωt 若正弦波有一相角 i=I0Sin(ωt+θ)
3.涡电流产生机理
1.將载有交流电之激发线圈接近金属物体,使得金 属导体引发交流磁场,感应产生旋涡状电流。 2.产生的感应电流之振幅及相位會随导体特性(如导 电率、导磁系数)差异而变化,这些涡电流亦感应 交变磁场,以改变线圈之磁场。
三、涡电流在检测方面的应用
1、探伤:检测金属表面或次表面之瑕疵。 2、检测物性: (a)检测金属物理性质(如导电率)。 (b)识别、控制热处理及加工条件。 3、测量尺寸及定位: (a) 测量金属薄片及薄管厚度 (b) 测量涂层膜厚 (c) 精密测量微小尺寸变化
涡电流原理及探伤技术
刘国晖
一、什么是涡电流? 在圆柱形铁芯上绕有螺线管,通有交 变电流 I,随着电流的变化,铁芯内磁通 量也在不断改变。我们把铁芯看作由一层 一层的圆筒状薄壳所组成,每层薄壳都相 当于一个回路。由于穿过每层薄壳横截面 的磁通量都在变化着,因此,在相应于每 层薄壳的这些回路中都将激起感应电动势 并形成环形的感应电流。我们把这种电流 叫做涡电流。
列举电涡流式传感器的应用场合

列举电涡流式传感器的应用场合
电涡流式传感器是一种利用涡流效应测量物体表面缺陷、硬度、形态等特性的传感器。
电涡流式传感器应用广泛,以下是其主要应用场合:
1. 金属表面缺陷检测
电涡流式传感器可以检测金属表面的缺陷,如裂纹、孔洞、毛刺等。
应用于机械制造、汽车、航空航天等行业的产品质量检测及生产过程控制中。
2. 金属硬度检测
电涡流式传感器可以检测金属的硬度,主要应用于金属材料的硬度检测和分析。
3. 金属零件尺寸检测
电涡流式传感器可以测量金属零件的尺寸和形状,可以应用于測量有突起和凹陷的零件。
4. 金属疲劳损伤检测
5. 电动机缺陷检测
电涡流式传感器可以检测电动机转子上绝缘缺陷,例如裂痕、孔洞等,用于电动机的
生产质量控制。
6. 地下管道检测
电涡流式传感器可以检测地下管道中的缝隙、裂缝和铸造缺陷,用于管道安全控制和
维护。
总之,电涡流式传感器是一种非常实用的传感器,应用范围广泛,被广泛应用于金属
制造、物流、车辆、电子、电力等各个领域。
涡流检测原理及部件

涡流原理及主要配件上海佳创精工机械有限公司一、概述1.1 涡流检测的原理涡流检测就是运用电磁感应原理,将激励信号加到探头线圈,当探头接近金属表面时,线圈周围的交变磁场在金属表面产生感应电流。
对于平板金属,感应电流的流向是以线圈同心的圆形,形似漩涡,成为涡流。
涡流的大小、相位及流动形式受到试件导电性能的影响。
涡流也会产生一个磁场,这个磁场反过来又会使检测线圈的阻抗发生变化。
因此当导体表面或近表面出现缺陷或测量的金属材料发生变化时,将影响到涡流的强度和分布,涡流的变化又引起了检测线圈电压和阻抗的变化,根据这一变化,就可以间接地知道导体内缺陷的存在及金属材料的性能是否有变化。
1.2 涡流检测技术的特点涡流检测时一种应用较为广泛的无损检测技术,它具有如下技术特点:●检测速度快,且易于实现自动化。
●表面、亚表面缺陷检出灵敏度高。
●能在高温状态下进行检测。
●抑制多种干扰因素。
涡流检测的对象必须是导电材料,且不适用于检测金属材料深层的内部缺陷,这是涡流检测在应用上的局限所在。
其次,涡流检测至今仍处于当量比较阶段,对缺陷作出准确的定性定量判断技术尚待开发研究。
1.3 涡流的探伤及材质分选涡流法可以用来测量非金属表面层的电导率,也可以用来检验与电导率数值有对应关系的性能,如化学成分和组织状态等。
因此,涡流检测可以成功地用于按牌号分选合金,检验材料热处理质量及机械性能等。
涡流探伤不仅对于导电材料表面上或近表面的裂纹、孔洞以及其它类型的缺陷,涡流实验具有良好的检测灵敏度并能提供缺陷深度的信息,还可以发现于薄的油漆层或涂层下的这些缺陷。
涡流检测仪的操作请参考《多频多通道智能数字涡流检测仪操作使用说明书》。
二、主要配置清单。
脉冲涡流热成像裂纹检测机理仿真分析

文运用 电磁 感应原 理及 热传 导理论 , 立感应 加 热数学模 型 , 用 有 限元 法分 析 电磁 激励 热成 建 利 像 检测缺 陷的机理 。利 用 C MS L有 限元 软 件建 模 分 析 了导磁 材 料 和 非 导磁 材 料 中两种 基 O O
本 裂纹 s t nth附近 涡流场和 温度 场 的分 布 情况 , 过分 析裂 纹 附近 涡 流 密度 大小 和温度 l和 o o c 通
场 的变化 曲线 , 出检 测导磁 和 非导磁材 料裂 纹 的最佳观 测 时 间以及 温度 响 应 , 下 一步 的裂 指 为 纹定 量检测 提供 理论 指导 。 关 键词 : 冲 涡流 热成像 ; 应加 热 ; 纹检 测 ; 真分析 脉 感 裂 仿
中图分 类号 :G15 2 T 1.8 文献 标识 码 : A D :0 3 6 /.sn 10 —0 8 2 1 .9 0 8 OI 1 . 9 9 ji . 0 15 7 .0 2 0 . 0 s
第4 2卷 第 9期
21 0 2年 9月
激 光 与 红 外
L ASER & I NFRARED
Vo . 2, . 1 4 No 9 S pe e t mbe 2 2 r, 01
文章编号 : 0- 7 (02 0- 9- 1 1 082 1)9 98 6 0 5 0 0
・红外技 术及 应用 ・
p p r a ma h mai a d lo d cin h ai g i e t bih d wi h lcr ma n t n u t n a d h a rn fr a e , t e t lmo e fi u t e t s sa l e t t e ee t c n o n s h o g e i id ci n e tt se c o a t e r . h i i lme t meh d i u e n lz h c a i o r c ee t n u i g ee t ma n t t l— h oy T e f t e e ns ne t o s s d t a ay et e me h n s fc a k d tci sn lcr o m o o g ei si a c mu td t emo r p y T e d s i u in o d y c re ta d tmp r t r ed n a h rc l ta d n th a e smu ae e h r g a h . h it b t fe d u n n e ea u e f l e r te ca k so n oc r i ltd r o i wi OMS g ei n o - g ei tr l e p ciey T r u h t e a ay i o d y c re td n i e r t C h OL i ma n t a d n n ma n t mae i sr s e t l . h o g h n lss fe d u n e st n a n c c a v y
涡流探伤原理

涡流探伤原理涡流探伤是一种常用的无损检测方法,它通过利用涡流感应原理来检测材料中的缺陷和异物。
涡流探伤原理的核心是利用交变磁场产生涡流,通过检测涡流感应电阻的变化来判断材料是否存在缺陷。
本文将从涡流探伤的基本原理、应用领域和优缺点等方面进行介绍。
涡流探伤的基本原理是利用交变磁场在导体中产生涡流的现象。
当导体材料表面存在缺陷或异物时,其导电性会发生变化,从而影响涡流感应电阻的大小。
通过测量涡流感应电阻的变化,可以判断材料中的缺陷情况。
涡流探伤可以对导电性材料进行检测,如金属、合金等,对于非导电性材料则需要进行表面导电处理后才能进行检测。
涡流探伤在航空航天、汽车制造、铁路运输、核工业等领域有着广泛的应用。
在航空航天领域,涡流探伤常用于飞机发动机叶片、机身结构等零部件的缺陷检测,可以及时发现隐藏在材料内部的裂纹、气孔等缺陷,确保飞机的安全飞行。
在汽车制造领域,涡流探伤可以用于发动机零部件、制动系统等的缺陷检测,提高汽车的质量和安全性。
涡流探伤的优点是检测速度快、无损伤、对表面涂层无影响,可以实现自动化检测,提高工作效率。
然而,涡流探伤也存在一些局限性,如只能检测表面附近的缺陷,不能检测材料内部的缺陷;对于非导电性材料需要进行特殊处理才能进行检测;对材料的形状和尺寸有一定的要求。
总的来说,涡流探伤是一种非常有效的无损检测方法,可以广泛应用于工业生产中,帮助生产企业提高产品质量,确保产品安全。
随着科学技术的不断发展,涡流探伤技术也在不断完善,相信在未来会有更多的应用场景和更高的检测精度。
通过本文的介绍,相信读者对涡流探伤的原理、应用领域和优缺点有了更深入的了解。
涡流探伤作为一种重要的无损检测方法,对于工业生产具有重要的意义,希望能够得到更广泛的应用和进一步的发展。
涡流检测原理
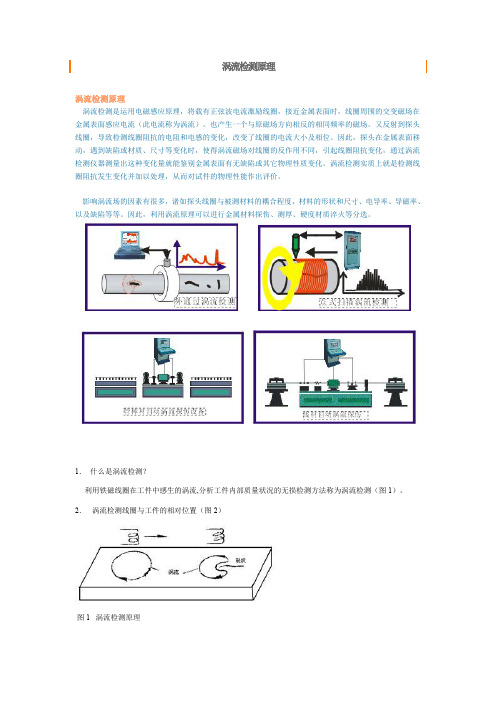
涡流检测原理涡流检测是运用电磁感应原理,将载有正弦波电流激励线圈,接近金属表面时,线圈周围的交变磁场在金属表面感应电流(此电流称为涡流)。
也产生一个与原磁场方向相反的相同频率的磁场。
又反射到探头线圈,导致检测线圈阻抗的电阻和电感的变化,改变了线圈的电流大小及相位。
因此,探头在金属表面移动,遇到缺陷或材质、尺寸等变化时,使得涡流磁场对线圈的反作用不同,引起线圈阻抗变化,通过涡流检测仪器测量出这种变化量就能鉴别金属表面有无缺陷或其它物理性质变化。
涡流检测实质上就是检测线圈阻抗发生变化并加以处理,从而对试件的物理性能作出评价。
影响涡流场的因素有很多,诸如探头线圈与被测材料的耦合程度,材料的形状和尺寸、电导率、导磁率、以及缺陷等等。
因此,利用涡流原理可以进行金属材料探伤、测厚、硬度材质淬火等分选。
1.什么是涡流检测?利用铁磁线圈在工件中感生的涡流,分析工件内部质量状况的无损检测方法称为涡流检测(图1)。
2.涡流检测线圈与工件的相对位置(图2)图1 涡流检测原理图2 涡流线圈与工件的三种位置涡流检测是建立在电磁感应原理基础之上的一种无损检测方法,它适用于导电材料,如果我们把一块导体置于交变磁场之中,在导体中就有感应电流存在,即产生涡流,由于导体自身各种因素(如电导率、磁导率、形状、尺寸和缺陷等)的变化会导致感应电流的变化,利用这种现象而判知导体性质、状态的检测方法,叫做涡流检测方法。
在涡流探伤中,是靠检测线圈来建立交变磁场;把能量传递给被检导体;同时又通过涡流所建立的交变磁场来获得被检测导体中的质量信息。
所以说,检测线圈是一种换能器。
检测线圈的形状、尺寸和技术参数对于最终检测是至关重要的。
在涡流探伤中,往往是根据被检测的形状,尺寸、材质和质量要求(检测标准)等来选定检测线圈的种类。
常用的检测线圈有三类:穿过式线圈; 穿过式线圈是将被检测试样放在线圈内进行检测的线圈,适用于管、棒、线材的探伤。
由于线圈产生的磁场首先作用在试样外壁,因此检出外壁缺陷的效果较好,内壁缺陷的检测是利用的渗透来进行的。
涡流检测技术
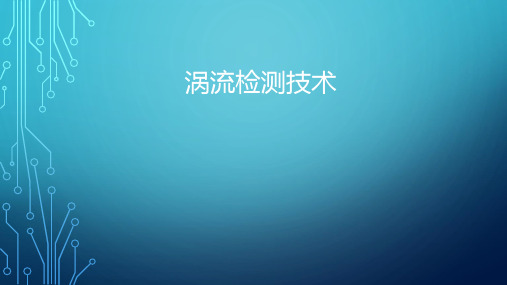
Thank you
涡流检测的主要用途及影响感生涡流的特性的主要因素
目的 探伤
材质试验
厚度及位移 等的测量
检测因素 试件中的裂纹、腐 蚀、凹坑、夹杂、 气泡等
电导率 磁导率
提离效应、厚度效 应、充填效应等
典型应用
管、棒、线、板材等的探伤; 机制件的探伤; 飞机维护及管道系统的维护检查; 疲劳裂纹的监视。
测量金属试件的电磁参数; 金属热处理状态的鉴别; 金属材料的分选; 金属材料成分含量、杂质含量的鉴 别。
金属试件上涂、镀等膜层测量; 板材测厚; 位移、振动测量; 液面位置、压力等的监控; 试件尺寸、形状测量等。
主要应用
• (1)能检测出材料和构件中的缺陷,例如裂纹、折叠、气孔和夹杂等。 • (2)能测量材料的电导率、磁导率、检测晶粒度、热处理状况、材料
的硬度和尺寸等。
• (3)金属材料或零件的混料分选。通过检查其成分、组织和物理性能
当探头从零件的中间部位移动到零件的边缘时,仪器所发生的报警现
象,是由于边缘效应所致,一般不是裂纹信号
当探头扫描移动到局部漆层脱落处,仪器所发出的报警现象,属间隙
效应引起,一般不是裂纹信号
当探头移动到受检部位的形状,或曲率发生变化的区域时,发出的报
警现象,一般不是裂纹信号
在对非磁性材料进行涡流检测过程中,如探头移动到磁性材料附近,
涡流检测的特点
• 优点: • (1)不需耦合剂,对管、棒、线材易于实现自动化。 • (2)对导电材料表面和近表面缺陷的检测灵敏度较高。 • (3)能在高温、高速下进行检测。 • (4)应用范围广,对影响感生涡流特性的各种物理和工艺因素均能实现检测。 • (5)工艺简单、操作容易、检测速度快。
05涡流检测
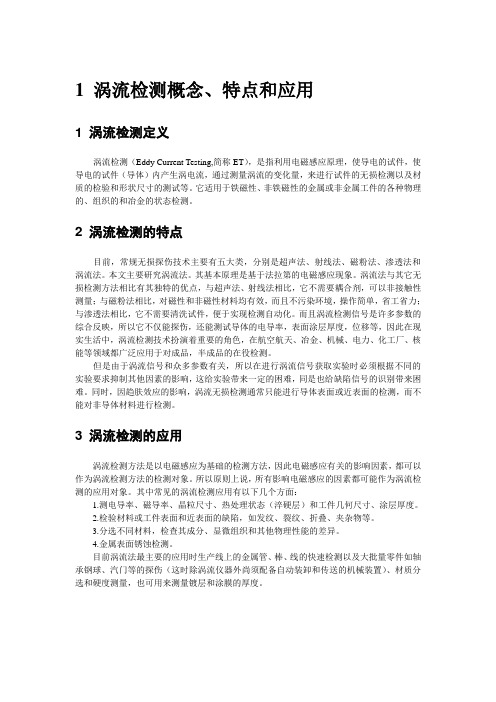
1 涡流检测概念、特点和应用1 涡流检测定义涡流检测(Eddy Current Testing,简称ET),是指利用电磁感应原理,使导电的试件,使导电的试件(导体)内产生涡电流,通过测量涡流的变化量,来进行试件的无损检测以及材质的检验和形状尺寸的测试等。
它适用于铁磁性、非铁磁性的金属或非金属工件的各种物理的、组织的和冶金的状态检测。
2 涡流检测的特点目前,常规无损探伤技术主要有五大类,分别是超声法、射线法、磁粉法、渗透法和涡流法。
本文主要研究涡流法。
其基本原理是基于法拉第的电磁感应现象。
涡流法与其它无损检测方法相比有其独特的优点,与超声法、射线法相比,它不需要耦合剂,可以非接触性测量;与磁粉法相比,对磁性和非磁性材料均有效,而且不污染环境,操作简单,省工省力;与渗透法相比,它不需要清洗试件,便于实现检测自动化。
而且涡流检测信号是许多参数的综合反映,所以它不仅能探伤,还能测试导体的电导率,表面涂层厚度,位移等,因此在现实生活中,涡流检测技术扮演着重要的角色,在航空航天、冶金、机械、电力、化工厂、核能等领域都广泛应用于对成品,半成品的在役检测。
但是由于涡流信号和众多参数有关,所以在进行涡流信号获取实验时必须根据不同的实验要求抑制其他因素的影响,这给实验带来一定的困难,同是也给缺陷信号的识别带来困难。
同时,因趋肤效应的影响,涡流无损检测通常只能进行导体表面或近表面的检测,而不能对非导体材料进行检测。
3 涡流检测的应用涡流检测方法是以电磁感应为基础的检测方法,因此电磁感应有关的影响因素,都可以作为涡流检测方法的检测对象。
所以原则上说,所有影响电磁感应的因素都可能作为涡流检测的应用对象。
其中常见的涡流检测应用有以下几个方面:1.测电导率、磁导率、晶粒尺寸、热处理状态(淬硬层)和工件几何尺寸、涂层厚度。
2.检验材料或工件表面和近表面的缺陷,如发纹、裂纹、折叠、夹杂物等。
3.分选不同材料,检查其成分、显微组织和其他物理性能的差异。
- 1、下载文档前请自行甄别文档内容的完整性,平台不提供额外的编辑、内容补充、找答案等附加服务。
- 2、"仅部分预览"的文档,不可在线预览部分如存在完整性等问题,可反馈申请退款(可完整预览的文档不适用该条件!)。
- 3、如文档侵犯您的权益,请联系客服反馈,我们会尽快为您处理(人工客服工作时间:9:00-18:30)。
涡电流检测工件表面裂纹
在磨削过程中,涡电流传感器用于监测裂纹的发生。
左图为涡电流基础的测量装置。
其用于决定涡轮叶片根部表面在成型研磨过程中裂纹的产生。
对于很难加工的飞行器发动机的组件材料,例如,镍、钴和钛合金,裂纹的产生是一个特殊的问题。
应用的目的是研磨之后,通过移动与地表面相连的传感器电桥,可以确定机床工作空间的裂缝。
右图显示了测量的结果。
裂纹在电子显微镜帮助下研究表明裂纹宽度2μm。
通过接触测量,涡电流传感器能清晰地测定裂纹。
这个尺寸被认为是传感器的最小分辨率。
传感器必须安装在垂直表面方向上,因为任何倾斜都会减小灵敏度。
这样在移动电桥时一个附加的移动选项被引入。
虽然测量速度小于磨削工作台的速度,但由于工件高的安全性,对于磨床而言,这种检测仍是可接受的。
然而由于限制因素的存在,只有研磨工件表面的裂纹能被识别出来,因此,只有有限范围内的材料能参与进去。