甲醇回收塔
甲醇-水体系单塔精馏与双效精馏流程比较

图1 双效并流流程和双效顺流流程甲醇-水体系单塔精馏与双效精馏流程比较樊晶1,张奉波2(1.北京石油化工工程有限公司, 北京 100107)(2.北京低碳清洁能源研究所, 北京 102211)[摘 要] 以11万吨/年二甲醚合成装置中甲醇回收塔为实例,采用Aspen Plus软件研究了甲醇回收塔单塔、并流型、顺流型双效精馏流程,在相同的设计基准及要求下,从设备投资及节能效果两方面,综合分析评价不同方案的优劣。
结果表明,并流双效流程的冷凝器和再沸器负荷分别下降了42.21%和49.63%,每年可节约运行成本252.714万元。
对于本项目中给定的进料,并流双效精馏是最佳的甲醇-水体系分离方案。
[关键词] 甲醇-水;流程模拟;双效精馏;节能作者简介:樊晶(1987—),女,山西永济人,硕士学位,工程师,从事化工工艺设计工作。
精馏是石油化工行业重要的分离操作单元,同时又是一个非常耗能的单元操作过程,为了降低其能耗,可以采用多种措施。
多效精馏就是其中行之有效的措施之一。
多效精馏是将精馏塔分成压力不同的多塔,压力较高塔的塔顶蒸汽向压力较低塔的再沸器供热,同时塔顶蒸汽被冷凝。
因此在多效精馏中只是第一个塔的塔釜需要加入热量,最后一个塔的塔顶蒸汽需要冷却介质进行冷凝,而其余各塔则不需要由外界进行供热和冷却,所以与单塔相比,多效精馏具有非常明显的节能效果[1]。
近年来随着能源紧张和人们环保意识的增强,多效精馏在化工行业逐渐受重视。
工业上广泛使用的是双效精馏,实际节能率大约在40%左右[2,3]。
本文以11万吨/年二甲醚合成装置中的甲醇回收塔为实例,采用Aspen Plus 对甲醇回收塔单塔进行模拟计算和优化,并设计了并流型和顺流型两种甲醇-水双效精馏流程,在相同的设计基准及要求下,对比单塔精馏与双效精馏方案的经济成本,找出不同精馏方案之间的差别,对实际生产和工程设计具有一定的指导作用。
1 多效精馏流程根据进料与压力梯度方向的一致性,多效精馏可以分为:(1)并流结构,即原料分配到各塔进料;(2)顺流结构,进料方向和压力梯度的方向一致,即从高压塔进料;2 模拟方法及过程2.1 设计依据表1 不同组成不同压力下甲醇-水体系泡点温度模拟条件:用Aspen Plus 软件模拟;用NRTL-RK 模型计算气液平衡;按理论板数计算。
甲醇精馏工艺流程
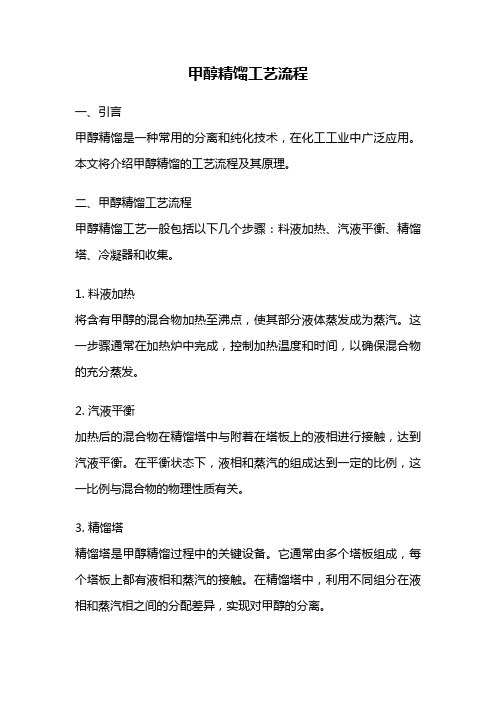
甲醇精馏工艺流程一、引言甲醇精馏是一种常用的分离和纯化技术,在化工工业中广泛应用。
本文将介绍甲醇精馏的工艺流程及其原理。
二、甲醇精馏工艺流程甲醇精馏工艺一般包括以下几个步骤:料液加热、汽液平衡、精馏塔、冷凝器和收集。
1. 料液加热将含有甲醇的混合物加热至沸点,使其部分液体蒸发成为蒸汽。
这一步骤通常在加热炉中完成,控制加热温度和时间,以确保混合物的充分蒸发。
2. 汽液平衡加热后的混合物在精馏塔中与附着在塔板上的液相进行接触,达到汽液平衡。
在平衡状态下,液相和蒸汽的组成达到一定的比例,这一比例与混合物的物理性质有关。
3. 精馏塔精馏塔是甲醇精馏过程中的关键设备。
它通常由多个塔板组成,每个塔板上都有液相和蒸汽的接触。
在精馏塔中,利用不同组分在液相和蒸汽相之间的分配差异,实现对甲醇的分离。
4. 冷凝器精馏塔中的蒸汽进入冷凝器进行冷却,转变为液体。
冷凝器通常采用冷却水循环冷却的方式,使蒸汽迅速冷却,凝结成液体。
冷凝器的效率对甲醇的回收率有重要影响。
5. 收集冷凝后的液体经过收集装置,最终得到纯度较高的甲醇产品。
收集装置通常是一个储存容器,用于收集冷凝后的甲醇液体。
收集后的甲醇可以进一步用于其他工艺或产品的生产。
三、甲醇精馏原理甲醇精馏的原理基于不同组分在液相和蒸汽相之间的分配差异。
在精馏塔中,组分相对挥发性差的物质偏向液相,而相对挥发性较高的物质偏向蒸汽相。
通过不断的汽液平衡和塔板间的传质传热,甲醇与其他组分逐渐分离。
四、总结甲醇精馏是一种常用的分离和纯化技术,其工艺流程包括料液加热、汽液平衡、精馏塔、冷凝器和收集等步骤。
通过控制加热温度和时间,利用精馏塔中的汽液平衡和塔板间的传质传热,可以实现对甲醇的分离和纯化。
甲醇精馏的原理基于不同组分在液相和蒸汽相之间的分配差异。
精馏工艺在化工工业中具有广泛的应用前景。
通过不断改进工艺流程和设备技术,可以提高甲醇精馏的效率和产量,满足不同领域的需求。
日本甲醇精馏塔爆炸事故分析

防范措施
(5) 由于不存在类似的事故案例,要预测 这样的爆炸事故非常困难。但是这起事故 也是由于回收甲醇的前期处理方法、中和 工程的pH计故障、精馏塔的焚烧操作等设 备和操作上的原因而引起的。如果供给精 馏塔的回收甲醇中的过氧化物完全还原, 就不会再发生这样的事故。
事故经过
爆炸发生在精馏塔的上部(从第5层至第26 层约7m),塔顶至第4层落至地下,塔壁 碎片最大飞至1300m,大部分散落在半径 为900m的范围内,第27层以下的塔壁碎片 残留在原地。据推算,爆炸当量相当于 10~50kg TNT。
事故经过
爆炸造成2人死亡,1人重伤,1人中度受伤, 11人轻伤。精馏塔完全破坏,塔周围50m 内的窗户玻璃全部损坏,爆炸碎片和冲击 波使工厂内319个场所遭破坏。
事故经过
α-磺基脂肪酸酯生产设备于1991年1月完成,2月进入正 常运行。6月19日21时35分,磺化反应装置启动,20日2 时46分,回收甲醇开始供给甲醇精馏塔。26日8时9分, 磺化反应装置停车;9时06分,停止向精馏塔供给回收甲 醇,同时减小再沸器的蒸气量,将精制甲醇的馏出量从正 常的350kg/h降至150kg/h,之后保持“待机状态”(回 流比为12);9时55分,为了使甲醇和水更好地分离,停 止精制甲醇的馏出,浓缩甲醇全部返回塔内进行“全回流 操作”;10时05分左右,停止向塔内回流,并增大再沸 器的蒸气量,精馏塔内的甲醇残液全部从塔顶推出进入 “焚烧操作”;10时15分左右,爆炸发生(事故发生前 0.2s,工艺温度和压力没有异常)。
化工安全事故案例
日本甲醇精馏塔爆炸事故分析
1.事故经过 1991年6月26日10时15分左右,日本狮子 株式会社千叶工场,在新型表面活性剂“α磺基脂肪酸酯”生产中,由于甲醇和过氧 化氢反应生成微量的甲基过氧化物,并在 精馏塔停止运转过程中,在局部从0.1%浓 缩到百分之几十而发热,导致精馏塔发生 爆炸,造成2人死亡,13人受伤,塔及周围 设施遭到严重破坏。
甲醇工艺介绍
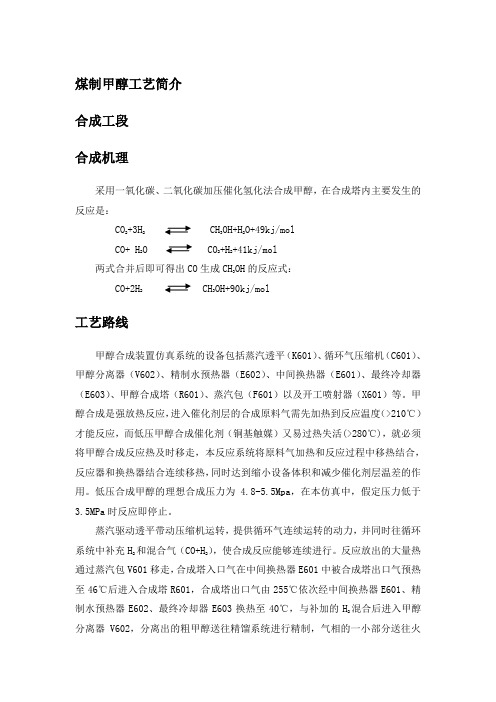
炬,气相的大部分作为循环气被送往压缩机 C601,被压缩的循环气与补加的混 合气混合后经 E601 进入反应器 R601。
合成甲醇流程控制的重点是反应器的温度、系统压力以及合成原料气在反应 器入口处各组分的含量。反应器的温度主要是通过汽包来调节,如果反应器的温 度较高并且升温速度较快,这时应将汽包蒸汽出口开大,增加蒸汽采出量,同时 降低汽包压力,使反应器温度降低或温升速度变小;如果反应器的温度较低并且 升温速度较慢,这时应将汽包蒸汽出口关小,减少蒸汽采出量,慢慢升高汽包压 力,使反应器温度升高或温降速度变小;如果反应器温度仍然偏低或温降速度较 大,可通过开启开工喷射器 X601 来调节。系统压力主要靠混和气入口量 FIC6001、 H2 入口量 FIC6002、放空量 PIC6004 以及甲醇在分离罐中的冷凝量来控制;在原 料气进入反应塔前有一安全阀,当系统压力高于 5.7MPa 时,安全阀会自动打开, 当系统压力降回 5.7MPa 以下时,安全阀自动关闭,从而保证系统压力不至过高。 合成原料气在反应器入口处各组分的含量是通过混和气入口量 FIC6001、H2 入口 量 FIC6002 以及循环量来控制的,冷态开车时,由于循环气的组成没有达到稳态 时的循环气组成,需要慢慢调节才能达到稳态时的循环气的组成。调节组成的方 法是:1.如果增加循环气中 H2 的含量,应开大 FIC6002、增大循环量并减小 FIC6001,经过一段时间后,循环气中 H2 含量会明显增大;2.如果减小循环气中 H2 的含量,应关小 FIC6002、减小循环量并增大 FIC6001,经过一段时间后,循 环气中 H2含量会明显减小;3.如果增加反应塔入口气中 H2的含量,应关小 FIC6002 并增加循环量,经过一段时间后,入口气中 H2 含量会明显增大;4.如果降低反 应塔入口气中 H2 的含量,应开大 FIC6002 并减小循环量,经过一段时间后,入 口气中 H2 含量会明显增大。循环量主要是通过透平来调节。由于循环气组分多, 所以调节起来难度较大,不可能一蹴而就,需要一个缓慢的调节过程。调平衡的 方法是:通过调节循环气量和混和气入口量使反应入口气中 H2/CO(体积比)在 7-8 之间,同时通过调节 FIC6002,使循环气中 H2 的含量尽量保持在 79%左右, 同时逐渐增加入口气的量直至正常(FIC6001 的正常量为 14877NM3/H,FIC6002 的正常量为 13804NM3/H),达到正常后,新鲜气中 H2 与 CO 之比(FFI6002)在 2.05~2.15 之间。
日本甲醇精馏塔爆炸事故分析

日本甲醇精馏塔爆炸事故
一、事故经过
1991年6月26日,日本某工厂在新型表面活性剂“α-磺基脂肪酸酯”生产中,由于甲醇和过氧化氢反应生成微量的甲基过氧化物,并在精馏塔停止运转过程中,在局部从0.1%浓缩到百分之几十而发热,导致精馏塔发生爆炸,造成2人死亡,13人受伤,塔及周围设施遭到严重破坏。
α-磺基脂肪酸酯生产设备于1991年1月完成,2月进入正常运行。
6月19日21时35分,磺化反应装置启动,20日2时46分,回收甲醇开始供给甲醇精馏塔。
26日8时9分,磺化反应装置停车;9时06分,停止向精馏塔供给回收甲醇,同时减小再沸器的蒸气量,将精制甲醇的馏出量从正常的350kg/h降至150kg/h,之后保持“待机状态”;9时55分,为了使甲醇和水更好地分离,停止精制甲醇的馏出,浓缩甲醇全部返回塔内进行“全回流操作”;10时05分左右,停止向塔内回流,并增大再沸器的蒸气量,精馏塔内的甲醇残液全部从塔顶推出进入“焚烧操作”,10时15分左右,爆炸发生(事故发生前0.2s,工艺温度和压力没有异常)。
爆炸发生在精馏塔的上部(从第5层至第26层约7m),塔顶至第4层落至地下,塔壁碎片最大飞至1300m,大部分散落在半径为900m的范围内,第27层以下的塔壁碎片残留在原地。
据推算,爆炸当量相当于10~50kg TNT。
二、事故危害
爆炸造成2人死亡,1人重伤,1人中度受伤,11人轻伤。
精馏塔完全破坏,塔周围50m内的窗户玻璃全部损坏,。
甲醇精馏系统的简介及优化
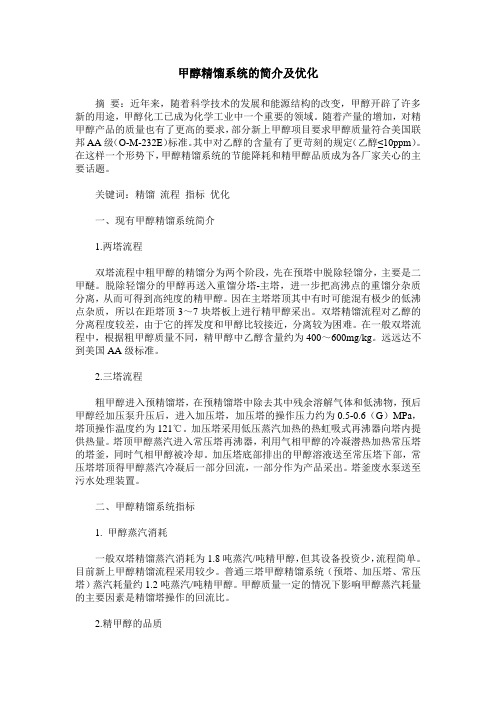
甲醇精馏系统的简介及优化摘要:近年来,随着科学技术的发展和能源结构的改变,甲醇开辟了许多新的用途,甲醇化工已成为化学工业中一个重要的领域。
随着产量的增加,对精甲醇产品的质量也有了更高的要求,部分新上甲醇项目要求甲醇质量符合美国联邦AA级(O-M-232E)标准。
其中对乙醇的含量有了更苛刻的规定(乙醇≤10ppm)。
在这样一个形势下,甲醇精馏系统的节能降耗和精甲醇品质成为各厂家关心的主要话题。
关键词:精馏流程指标优化一、现有甲醇精馏系统简介1.两塔流程双塔流程中粗甲醇的精馏分为两个阶段,先在预塔中脱除轻馏分,主要是二甲醚。
脱除轻馏分的甲醇再送入重馏分塔-主塔,进一步把高沸点的重馏分杂质分离,从而可得到高纯度的精甲醇。
因在主塔塔顶其中有时可能混有极少的低沸点杂质,所以在距塔顶3~7块塔板上进行精甲醇采出。
双塔精馏流程对乙醇的分离程度较差,由于它的挥发度和甲醇比较接近,分离较为困难。
在一般双塔流程中,根据粗甲醇质量不同,精甲醇中乙醇含量约为400~600mg/kg。
远远达不到美国AA级标准。
2.三塔流程粗甲醇进入预精馏塔,在预精馏塔中除去其中残余溶解气体和低沸物,预后甲醇经加压泵升压后,进入加压塔,加压塔的操作压力约为0.5-0.6(G)MPa,塔顶操作温度约为121℃。
加压塔采用低压蒸汽加热的热虹吸式再沸器向塔内提供热量。
塔顶甲醇蒸汽进入常压塔再沸器,利用气相甲醇的冷凝潜热加热常压塔的塔釜,同时气相甲醇被冷却。
加压塔底部排出的甲醇溶液送至常压塔下部,常压塔塔顶得甲醇蒸汽冷凝后一部分回流,一部分作为产品采出。
塔釜废水泵送至污水处理装置。
二、甲醇精馏系统指标1. 甲醇蒸汽消耗一般双塔精馏蒸汽消耗为1.8吨蒸汽/吨精甲醇,但其设备投资少,流程简单。
目前新上甲醇精馏流程采用较少。
普通三塔甲醇精馏系统(预塔、加压塔、常压塔)蒸汽耗量约1.2吨蒸汽/吨精甲醇。
甲醇质量一定的情况下影响甲醇蒸汽耗量的主要因素是精馏塔操作的回流比。
日本甲醇精馏塔爆炸事故分析

事故原因
(1)在漂白过程中,残留的无水硫酸和添 加的甲醇发生副反应生成甲基硫酸,甲基 硫酸只有在酸性条件下,与过氧化氢反应 生成甲基过氧化物。而甲基过氧化物在弱 酸性水溶液中较稳定,几乎不分解,但在 中性和碱性溶液中不稳定,随着温度的升 高而加速分解。
事故原因
(2)在正常运行时(回流比为5),甲基 过氧化物最大浓度不超百分之几,在进行 “全回流操作”时,甲基过氧化物的浓度 被浓缩到百分之几十。
事故经过
爆炸发生在精馏塔的上部(从第5层至第26 层约7m),塔顶至第4层落至地下,塔壁 碎片最大飞至1300m,大部分散落在半径 为900m的范围内,第27层以下的塔壁碎片 残留在原地。据推算,爆炸当量相当于 10~50kg TNT。
事故经过
爆炸造成2人死亡,1人重伤,1人中度受伤, 11人轻伤。精馏塔完全破坏,塔周围50m 内的窗户玻璃全部损坏,爆炸碎片和冲击 波使工厂内319个场所遭破坏。
3.防范措施
(1)设置利用还原剂能够完全除去向精馏 塔供给回收甲醇中所含有的过氧化物的设 备。
3.防范措施
(2)回收甲醇中的过氧化物,应确认其被 还原剂完全还原后,再供给精馏塔。
3.防范措施
(3)精馏塔停止焚烧操作。
防范措施
(4) 再漂白工程中,应抑制甲基过氧化物 的生成,且在中和工程中设置双重pH计。
事故原因
(3)事故发生当日,中和工段的pH计发生 故障,使中和的烧碱量减少,溶液呈酸性, 甲基过氧化物不易分解,导致甲基过氧化 物在塔内的滞留量由正常时的10~20kg上升 至30~40kg。
甲醇多效热泵精馏塔,甲醇蒸馏设备 高效节能
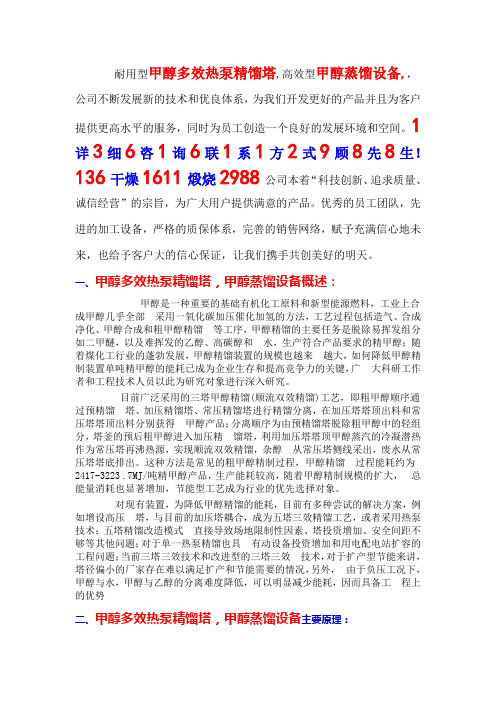
耐用型甲醇多效热泵精馏塔,高效型甲醇蒸馏设备,,公司不断发展新的技术和优良体系,为我们开发更好的产品并且为客户提供更高水平的服务,同时为员工创造一个良好的发展环境和空间。
1详3细6咨1询6联1系1方2式9顾8先8生!136干燥1611煅烧2988公司本着“科技创新、追求质量、诚信经营”的宗旨,为广大用户提供满意的产品。
优秀的员工团队,先进的加工设备,严格的质保体系,完善的销售网络,赋予充满信心地未来,也给予客户大的信心保证,让我们携手共创美好的明天。
一、甲醇多效热泵精馏塔,甲醇蒸馏设备概述:甲醇是一种重要的基础有机化工原料和新型能源燃料,工业上合成甲醇几乎全部采用一氧化碳加压催化加氢的方法,工艺过程包括造气、合成净化、甲醇合成和粗甲醇精馏等工序,甲醇精馏的主要任务是脱除易挥发组分如二甲醚,以及难挥发的乙醇、高碳醇和水,生产符合产品要求的精甲醇;随着煤化工行业的蓬勃发展,甲醇精馏装置的规模也越来越大,如何降低甲醇精制装置单吨精甲醇的能耗已成为企业生存和提高竞争力的关键,广大科研工作者和工程技术人员以此为研究对象进行深入研究。
目前广泛采用的三塔甲醇精馏(顺流双效精馏)工艺,即粗甲醇顺序通过预精馏塔、加压精馏塔、常压精馏塔进行精馏分离,在加压塔塔顶出料和常压塔塔顶出料分别获得甲醇产品;分离顺序为由预精馏塔脱除粗甲醇中的轻组分,塔釜的预后粗甲醇进入加压精馏塔,利用加压塔塔顶甲醇蒸汽的冷凝潜热作为常压塔再沸热源,实现顺流双效精馏,杂醇从常压塔侧线采出,废水从常压塔塔底排出。
这种方法是常见的粗甲醇精制过程,甲醇精馏过程能耗约为2417-3223 .7MJ/吨精甲醇产品,生产能耗较高,随着甲醇精制规模的扩大,总能量消耗也显著增加,节能型工艺成为行业的优先选择对象。
对现有装置,为降低甲醇精馏的能耗,目前有多种尝试的解决方案,例如增设高压塔,与目前的加压塔耦合,成为五塔三效精馏工艺,或者采用热泵技术;五塔精馏改造模式直接导致场地限制性因素、塔投资增加、安全间距不够等其他问题;对于单一热泵精馏也具有动设备投资增加和用电配电站扩容的工程问题;当前三塔三效技术和改进型的三塔三效技术,对于扩产型节能来讲,塔径偏小的厂家存在难以满足扩产和节能需要的情况,另外,由于负压工况下,甲醇与水,甲醇与乙醇的分离难度降低,可以明显减少能耗,因而具备工程上的优势二、甲醇多效热泵精馏塔,甲醇蒸馏设备主要原理:四塔热泵甲醇精馏方法,采用预精馏塔、负压精馏塔、加压精馏塔、杂醇回收塔四塔热泵热耦合;负压精馏塔塔顶蒸汽经过压缩机一增压升温之后对负压精馏塔再沸器二进行供热;预精馏塔塔顶采出的轻组分杂质,进入到火炬系统进行处理,预精馏塔塔釜经过脱除轻组分杂质的粗甲醇进入到负压精馏塔;负压精馏塔的塔顶采出精甲醇产品,负压精馏塔的塔釜物料进入到加压精馏塔;加压精馏塔塔顶采出精甲醇产品,加压精馏塔侧线采出物料进入到杂醇回收塔,加压精馏塔的塔釜采出废水;杂醇回收塔的塔顶采出燃料甲醇,杂醇回收塔的塔釜采出废水。
- 1、下载文档前请自行甄别文档内容的完整性,平台不提供额外的编辑、内容补充、找答案等附加服务。
- 2、"仅部分预览"的文档,不可在线预览部分如存在完整性等问题,可反馈申请退款(可完整预览的文档不适用该条件!)。
- 3、如文档侵犯您的权益,请联系客服反馈,我们会尽快为您处理(人工客服工作时间:9:00-18:30)。
浦江学院《化工原理》课程设计设计题目甲醇回收塔学生姓名班级、学号指导教师姓名课程设计时间2013年6月17日-2013年6月28日课程设计成绩指导教师签字南京工业大学化工原理课程设计任务书专业:班级:姓名:设计日期:2013 年 6 月17 日至2013 年 6 月28 日设计题目:甲醇回收塔设计条件:进料量:F = 150 吨/天进料组成:X f = 9.5% (w%)进料状态:25℃回收率: η= 99%操作条件:直接蒸汽加热指导教师:年月日目录一、前言---------------------------------------------------------------------3二、设计说明书符号表---------------------------------------------------5三、流程设计---------------------------------------------------------------7四、物性参数---------------------------------------------------------------8五、工艺计算--------------------------------------------------------------11六、塔径的计算-----------------------------------------------------------13七、填料层高度计算-----------------------------------------------------14八、填料塔的流体力学性能--------------------------------------------15九、塔设计计算参数总汇-----------------------------------------------21十、辅助设备的选择-----------------------------------------------------21 十一、参考资料-------------------------------------------------------------24一前言甲醇用途广泛,是基础的有机化工原料和优质燃料。
主要应用于精细化工,塑料等领域,用来制造甲醛、醋酸、氯甲烷、甲氨、硫酸二甲脂等多种有机产品,也是农药、医药的重要原料之一。
塔设备是化工,制药,环保等生产中广泛应用的气液传质设备。
根据塔内气液接触部件的形式,可以分为填料塔和板式塔。
板式塔属于逐级接触逆流操作,填料塔属于微分接触操作。
工业上对塔设备的主要要求:(1)生产能力大(2)分离效率高(3)操作弹性大(4)气体阻力小结构简单、设备取材面广等。
塔型的合理选择是做好塔设备设计的首要环节,选择时应考虑物料的性质、操作的条件、塔设备的性能以及塔设备的制造、安装、运转和维修等方面的因素。
板式塔的研究起步较早,其流体力学和传质模型比较成熟,数据可靠。
尽管与填料塔相比效率较低、通量较小、压降较高、持液量较大,但由于结构简单、造价较低、适应性强、易于放大等特点,因而在70年代以前的很长一段时间内,塔板的研究一直处于领先地位。
然而,70年代初期出现的世界能源危机迫使填料塔技术在近20年来取得了长足进展。
由于性能优良的新填料相继问世,特别是规整填料和新型塔内件的不断开发应用和基础理论研究的不断深入,使填料的放大技术有了新的突破,改变了以板式塔为主的局面。
在我国,随着石油化工的不断发展,传质分离工程学的研究不断深入,使填料塔技术及其应用进入了一个崭新的时期,其工业应用与发达国家并驾齐驱,进入世界先进行列。
评价塔设备的基本性能的指标主要有:1、产量和通量:前者指单位时间处理物料量,而后者指单位塔截面上的单位时间的物料处理量。
2、分离效率:对板式塔是指每层塔板所能达到的分离程度。
填料塔则是单位填料层高度的分离能力。
3、适应能力及操作弹性:对各种物料性质的适应性及在负荷波动时维持操作稳定而保持较高分离效率的能力。
4、流体阻力:气相通过每层塔板或单位高度填料层的压降。
除上述几项主要性能外,塔的造价高低、安装、维修的难易以及长期运转的可靠性等因素,也是必须考虑的实际问题。
填料塔由填料、塔内件及筒体构成。
填料分规整填料和散装填料两大类。
塔内件有不同形式的液体分布装置、填料固定装置或填料压紧装置、填料支承装置、液体收集再分布装置及气体分布装置等。
与板式塔相比,新型的填料塔性能具有如下特点:生产能力大、分离效率高、压力降小、操作弹性大、持液量小等优点。
本设计综合考虑流程,产量,分离要求,操作控制等因素,采用填料塔实现甲醇回收目标。
二、设计说明书符号表三、流程设计图3.1 流程图对于给定的低浓度甲醇水溶液,采用两塔流程回收甲醇,如图4.1所示。
流程概述如下:原料为浓度很低的甲醇水溶液,经预热器加热到泡点进入回收塔;经回收塔将原料中大量的水和杂质从塔底排出,塔顶得到浓度较高的甲醇蒸汽;甲醇蒸气直接引入精馏塔精馏,精馏塔顶可获得高纯度的甲醇。
回收塔塔底产品为甲醇含量极低的水,可直接排放。
回收塔的目的是初步提纯甲醇并除去大量的水,这样在精馏塔中可减少处理量,相比单塔精馏,能耗更低,操作弹性也更大。
针对回收塔要求有很高的甲醇回收率,但不要求塔顶浓度很高。
本设计采用提馏塔的形式,原料从塔顶直接加入,不设回流装置。
此外考虑到塔底浓度已经接近水,本设计采用直接蒸汽加热,省去了再沸器简化了附属设备。
采用直接蒸汽的另一个好处是对蒸汽压要求更低,这是因为省去了间接加热的温度差。
本流程在回收塔前设置原料预热器,这样可减少原料温度的波动对塔分离性能的影响。
加热介质采用低压蒸汽,通过蒸汽压很容易调节加热效果稳定流程工况。
考虑到塔釜排放液中杂质较多,故不利用回收塔塔底排放液的热能。
综合前述考虑,本设计确定甲醇回收塔的工况如下:将25℃下质量百分数为13%的甲醇水溶液预热到泡点;经回收塔浓缩,塔顶产品甲醇回收率不小于98%,塔顶产品浓度和流量将通过优选确定; 回收塔用直接蒸汽加热。
四、 物性数据表4.1 水蒸汽的物性参数水的物性参数:M 水 = 18.02 kg/kmol表4.2 水的物性参数甲醇的物性参数:M 甲醇 = 32.04 kg/kmol表4.3 甲醇的物性参数= 18.02 kg/kmol 水蒸汽的物性参数:M水蒸汽4.1汽液平衡数据和汽液平衡(t-x-y)图由[6]的水—甲醇体系平衡数据:表4.4水—甲醇体系平衡数据可得t-x-y平衡图:4.2理论板数的计算例:Private Sub Command1_Click()Dim y As Double, x As Double, c As Double, n As Integer y = 0.3382x = 0.0557c = 0.3382n = 0Do While (x > 0.000557)x = (y / 1.1214) ^ (1 / 0.4118)y = c / 0.05514 * (x - 0.000557)n = n + 1Print x; yLoopPrint nEnd Sub由图V-N可见,增加气量对理论板数影响不大,且进气量越大,塔顶汽相组成越小,塔径越大,此时取流量为70 kmol/h,选择理论塔板数N T = 6,进气量V0 = 70 kmol/h。
提馏线方程:y=6.014x-0.0033498五、工艺计算5.1 物料衡算4.1.1 数据换算M甲醇= 32 kg/kmolM水= 18 kg/kmolF = 150吨/天= 332.80 kmol/h原料液甲醇的摩尔分率:x F =0.05575.1.2物料衡算F = D + WW = F = 332.80 kmol/hη=1-W Xw/F xf塔釜产品甲醇的摩尔分率:x W=0.000557由XD =C=0.3316D=Vo=V=70 kmol/h5.2回收塔工艺条件及有关物性数据计算5.2.1操作温度计算塔顶温度(33.33- 29.09)/ (76.7-77.8)=(33.16-33.33)/( tD -76.7) tD=76.74℃塔底温度 tW=100℃平均温度 t=( tD + tW)/2=88.37℃5.2.2.平均摩尔质量计算由xD =y1=0.3316, 查平衡曲线得 x1=0.052M VD =y1M甲醇+(1-y1)M水=22.64kg/kmolM LD =x1M甲醇+(1-x1)M水=18.728kg/kmol由于塔底xW 很小,塔底可看成只有主份水,故MVW=M水=MLW=18kg/kmol全塔平均摩尔质量:MV = (MVD+MVW)/2=20.32kg/kmolML = (MLD+MLW)/2=18.364kg/kmol5.2.3.平均密度计算气相平均密度计算:由理想气体状态方程得ρv =PMV/(RT)=101.3*20.32/[8.314*(88.37+273.15)]= 0.685kg/m3液相平均密度计算:由于操作过程中甲醇在液相中浓度很小可近似取ρl=982.4kg/m3 5.2.4.液体平均表面张力计算液体平均表面张力依据δl=Σxi δi计算塔顶液相平均表面张力的计算:由tD =76.74℃,查手册得δ甲醇=15.415*10-3N/m, δ水=63.76*10-3N/mδLD =x1δ甲醇+(1-x1)δ水=61.25*10-3N/m塔底液相平均表面张力的计算:由tW =100℃, 查手册得δ甲醇=12.8*10-3N/m, δ水=58.84*10-3N/mδLW =xWδ甲醇+(1-xW)δ水=58.81*10-3N/m平均表面张力为:δL =(δLD+δLW)/2=60.03*10-3N/m5.2.5.液体平均粘度计算液相平均粘度计算,即㏒μL =Σxi㏒μi塔顶液相平均粘度计算:由tD =76.74℃, 查手册得,μ甲醇=0.00291mPa·s μ水=0.3716 mPa·s㏒μLD =x1㏒μ甲醇+(1-x1)㏒μ水解得μLD=0.289 mPa·s 塔底液相平均粘度计算:由tW =100℃, 查手册得,μ甲醇=0.00225mPa·s μ水=0.2824 mPa·s㏒μLW =xW㏒μ甲醇+(1-xW)㏒μ水解得μLW=0.282 mPa·s 液体平均粘度为:μL =(μLD+μLW)/2=0.2855 mPa·s六、塔径的计算甲醇回收操作,为防止堵塞选择散装填料。