油气管道局部腐蚀原因分析
油气长输管道防腐的必要性及阴极保护_2020

油气长输管道防腐的必要性及阴极保护阴极保护是延长管道寿命、抑制埋地管道腐蚀的重要手段,已经广泛地应用在石油、化工、天然气、市政等行业当中。
随时间的推移,管道经常会出现腐蚀穿孔的现象。
1油气长输管道防腐的必要性目前,世界上长距离油、气管道的总长度估计己超过200万km里,埋入地下的管道钢铁总量约2亿t。
输送气、油的钢质管道大都处于复杂的土壤环境当中,所输送的介质也都含有有腐蚀性,所以管道的内壁以及外壁都有可能遭到腐蚀,管道一旦被腐蚀穿孔,就会造成气、油的漏失,这样不仅会造成运输的中断,而且会环境有很强的污染,甚至还有可能引起火灾,造成更加严重的危害。
如果不采取相应的防腐措施,每年腐蚀其l0%,则钢铁年托运将达2千万t以上,这是一个相当惊人的直接损失,其间接造成的经济损失更是难以估计。
所以必须防止油气长输管道腐蚀的损坏。
2阴极保护的原理在被保护的管道上连接一个电位更负的金属或合金作为阳极或给被保护管道外加电流,从而使被保护的管道阴极极化,进而减轻或消除管道腐蚀速率。
(1)外加电流法阴极保护是利用外部电源对被保护体施加阴极电流,从而抑阻被保护体自身的腐蚀过程。
(2)牺牲阳极法阴极保护在土壤等电解质环境中,当与被保护体电连接后将优先腐蚀溶解,释放出的电子在被保护体表面发生阴极还原反应,牺牲阳极因其电极电位比被保护体的更负,抑阻了被保护体的阳极溶解过程,从而对被保护体提供了有效的阴极保护。
(3)牺牲阳极种类及应用范围分别是带状牺牲阳极、锌-铝-镉合金牺牲阳极、镁合金牺牲阳极和镯式牺牲阳极以及铝-锌-铟系牺牲阳极。
带状牺牲阳极主要应用于高电阻率土壤、空间狭窄局部场合及淡水,如套管内;锌-铝-镉合金牺牲阳极适用于海水、机械设备、淡海水介质中的船舶、海洋工程和海港设施以及低电阻率土壤中的电缆、管道等设施金属防腐蚀的阴极保护;然而镁合金牺牲阳极密度相对小,极化率低,电极电位很负,对铁的驱动电压比较的大。
留言列表。
天然气管道的腐蚀原因及防治措施
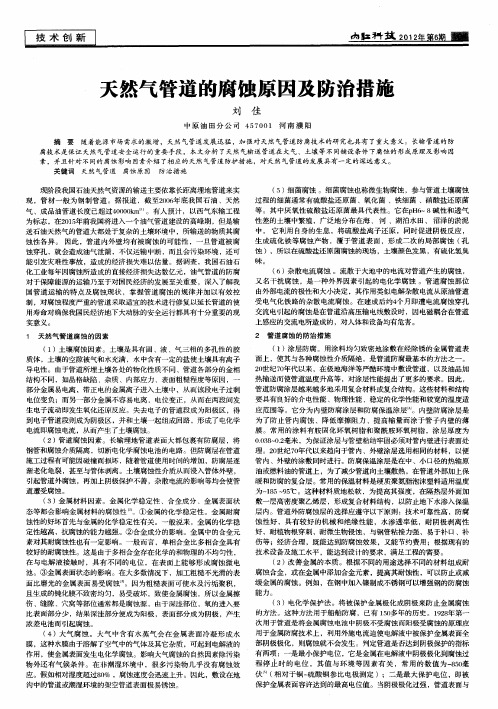
() 5 细菌腐蚀 。细菌 腐蚀 也称微生物腐蚀 ,参 与管道 土壤腐蚀 过程 的细菌通常有 硫酸盐还原菌 、氧化菌 、 细菌 、硝酸盐 还原菌 铁 等 。其 中厌 氧性硫酸盐 还原菌 最具代表性 。它在p 6 碱性和 透气 H ~8
性差 的土壤 中繁殖 ,广泛地分布 在海 、 河 、湖泊水 田 、 沼泽的淤泥 中 , 它利 用 自身 的生 息 ,将硫酸 盐离子还 原 ,同时 促进阴极 反应 , 生成 硫化铁 等腐蚀 产物 , 于管道 表面 ,形成二 次的局 部腐蚀 ( 覆 孔 蚀 ), 以在 硫酸 盐还原菌腐蚀的现场 ,土壤颜色发黑 的输送 主要依靠长距离埋地管道来实 现 ,管材一 般为 钢制管道 。据 报道 ,截 至2 0 年 底我 国石油 、天然 06
气 、成 品油管道长度 已超过4 0 0 m 0 0 k …。有人 预计 ,以西气 东输工程 为标志 ,在2 1年前我 国将进入 一个 油气 管道 建设的高峰期 ,但是输 05 送石油天然气 的管道 大都处 于复 杂的土壤环境中 ,所输送的物质其腐 蚀性 各异 。 因此 ,管道 内外壁均 有被腐蚀 的可能性 ,一旦管道 被腐 蚀穿孔 ,就会造成 油气泄漏 ,不仅运输 中断 ,而且会污染环境 ,还可 能 引发 灾难性 事故 ,造成的经济损失难以估量 。据调查 ,我 国石油石 化工业 每年 因腐蚀所 造成的直接经济损失达数亿元 ,油气管道的防腐 对于保 障能源 的运输 乃至 于对国民经济的发展至关重要 ,深入 了解我 国管 道运输 的特 点及腐蚀现 状 ,掌握管道 腐蚀 的规律并 加 以有效控
技 术 创 新
肉 I 科 技 2 1年第6 l 工 02 期
天然气 管道 的腐蚀原 因及 防治措施
刘 佳
中原 油 田 分 公 司 45 0 7 0l 河 南 濮 阳
油气集输站蒸汽回水管线腐蚀问题及对策

层, 管线 腐蚀 部 位质 量 损失 6 %以上 , 0 内壁 破坏 面积
8 % 以上 。 0
2 腐蚀 原 因分 析与 研 究 2 1 外 管壁 腐蚀 分析 .
靖 安 首 站 地 质 勘查 报 告 表 明 , 该站 属 于 黄 土 地
研 究表 明 , 汽 回水管 线 内壁 腐 蚀 的 主 要 原 因 蒸 是 氧 腐蚀 和酸 腐蚀 L 。给 水 中 的溶 解氧 经 加热 从 水 3 ] 中逸 出而 被水 蒸汽 带走 , 成管 线 内壁氧腐 蚀 。 中 造 水 的溶 解氧 含量 和 锅水 的 C 一 量 是 影 响氧 腐 蚀 的主 l含
摘 要 : 对 长庆 油 田 第三输 油 处油 气集 输 站 蒸汽 回水 管线腐 蚀 问题 , 针 分析 了管 线腐 蚀 的形 式 , 探 讨 了管线 腐蚀 的 原 因和 影响腐 蚀 的 因素 , 出 了有 效的解 决 方 案 , 提 并取得 了良好 的 防腐 效 果 。 关键 词 : 蒸汽 回水 管线 ; 蚀 ; 解 氧 ; 金属 复合 管 腐 溶 双
色 鼓 包 , 蚀 深 处 紧 靠 金属 表 面 存 在 一 黑色 的 F O 腐 e
厚而导致鼓包形成 , 鼓包下金属腐蚀逐渐加深 , 最终 形 成坑 蚀 。 腐蚀 外观 表现 为 大面 积 溃疡 腐蚀 , 与现 这 场管 线 腐蚀 调研 结果 相 一致 。影 响 氧腐 蚀 的主 要 因
素 是土 壤 的含 水率 。土 壤含 水率 增 加一 方面 导致 土 壤 电阻 率 降低 , 一 方面 使 土 壤 中矿 物 质 的 溶 解 量 另 增加 , 形成 电解 质 溶液 , 进 电化学 腐 蚀 的进 行 。 促 2 2 内管壁腐 蚀 分析 .
1 集输站 蒸 汽 回水 管线 腐蚀 状况 金 属 管 线 和设 备 腐 蚀 引 起 的 “ 、 滴 、 ” 跑 冒、 漏 给
油气管道保护工
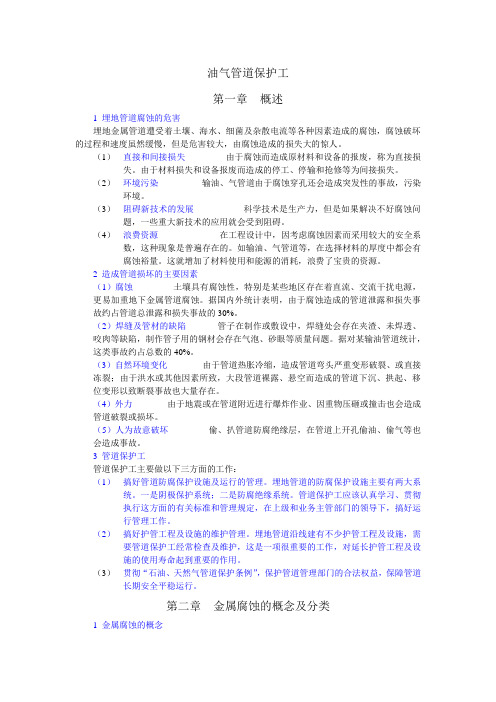
油气管道保护工第一章概述1 埋地管道腐蚀的危害埋地金属管道遭受着土壤、海水、细菌及杂散电流等各种因素造成的腐蚀,腐蚀破坏的过程和速度虽然缓慢,但是危害较大,由腐蚀造成的损失大的惊人。
(1)直接和间接损失由于腐蚀而造成原材料和设备的报废,称为直接损失。
由于材料损失和设备报废而造成的停工、停输和抢修等为间接损失。
(2)环境污染输油、气管道由于腐蚀穿孔还会造成突发性的事故,污染环境。
(3)阻碍新技术的发展科学技术是生产力,但是如果解决不好腐蚀问题,一些重大新技术的应用就会受到阻碍。
(4)浪费资源在工程设计中,因考虑腐蚀因素而采用较大的安全系数,这种现象是普遍存在的。
如输油、气管道等,在选择材料的厚度中都会有腐蚀裕量。
这就增加了材料使用和能源的消耗,浪费了宝贵的资源。
2 造成管道损坏的主要因素(1)腐蚀土壤具有腐蚀性,特别是某些地区存在着直流、交流干扰电源,更易加重地下金属管道腐蚀。
据国内外统计表明,由于腐蚀造成的管道泄露和损失事故约占管道总泄露和损失事故的30%。
(2)焊缝及管材的缺陷管子在制作或敷设中,焊缝处会存在夹渣、未焊透、咬肉等缺陷,制作管子用的钢材会存在气泡、砂眼等质量问题。
据对某输油管道统计,这类事故约占总数的40%。
(3)自然环境变化由于管道热胀冷缩,造成管道弯头严重变形破裂、或直接冻裂;由于洪水或其他因素所致,大段管道裸露、悬空而造成的管道下沉、拱起、移位变形以致断裂事故也大量存在。
(4)外力由于地震或在管道附近进行爆炸作业、因重物压砸或撞击也会造成管道破裂或损坏。
(5)人为故意破坏偷、扒管道防腐绝缘层,在管道上开孔偷油、偷气等也会造成事故。
3 管道保护工管道保护工主要做以下三方面的工作:(1)搞好管道防腐保护设施及运行的管理。
埋地管道的防腐保护设施主要有两大系统。
一是阴极保护系统;二是防腐绝缘系统。
管道保护工应该认真学习、贯彻执行这方面的有关标准和管理规定,在上级和业务主管部门的领导下,搞好运行管理工作。
油气田常用碳钢管道耐蚀性评价及防腐措施研究

随着石油天然气勘探开发的不断深入,陆上油气田集输管道的输送介质日益复杂,不仅有油、气、水等多相流采出物,还有CO 2、H 2S、硫酸盐还原菌等腐蚀性物质,同时随着酸化压裂、空气泡沫驱、CO 2驱、火驱等增产措施的引入,导致管道腐蚀泄漏问题日益严峻[1-2]。
目前,某油田常用的管材以碳钢为主,约占该油田所有集输管道长度的80%,主要以20号钢、20G 钢和L360钢为主,各种油气田常用碳钢管道耐蚀性评价及防腐措施研究王金梭(大庆油田有限责任公司第五采油厂)摘要:为提高管道完整性管理水平,通过化学成分分析、金相组织观察、单轴拉伸实验、电化学腐蚀实验和挂片失重实验等手段,分析20号钢、20G 钢和L360钢在油田环境下的耐蚀特性,并对碳钢管道的安全运行提出防腐措施。
结果表明,L360钢的有益元素较多,有害元素较少;不同管材产生了以铁素体为阳极,珠光体或渗碳体为阴极的电化学腐蚀过程;均匀腐蚀速率从大到小顺序为20号钢、20G 钢、L360钢,最大点蚀速率从大到小顺序为20G 钢、20号钢、L360钢,L360钢的耐蚀性最好;对于轻度腐蚀的管道可采用添加缓蚀剂和动态监测的方法,对于中度和重度腐蚀的管道可采用内穿插修复、风送挤涂修复和局部补强等技术对管道本体和防腐层缺陷进行修复;应用后,管道失效率有所降低,每年可减少损失455.3万元,且产生的环保效益不可估量。
关键词:碳钢;耐蚀性;防腐;铁素体;修复技术DOI :10.3969/j.issn.2095-1493.2023.05.009Research on corrosion resistance evaluation and anti-corrosion measures of carbonsteel pipelines used in oil and gas fields WANG JinsuoNo.5Oil Production Plant of Daqing Oilfield Co .,Ltd .Abstract:In order to improve the management level of pipeline integrity,the corrosion resistance characteristics of 20steel,20G steel and L360steel in oilfield environment are analyzed by means of chemical composition analysis,metallographic tissue observation,single axis tensile experiment,elec-trochemical corrosion experiment and weightlessness experiment and other means,and the anti-corro-sion measures for the safe operation of carbon steel pipeline are put forward.The results show that L360steel has more beneficial elements and less harmful elements.The different tubes is produced the electrochemical corrosion process with ferrite as anode and pearlite or carburite as cathode.The order of uniform corrosion rate from large to small is 20steel、20G steel、L360steel,and the order of maxi-mum pitting rate from large to small is 20G steel、20steel、L360steel.Among them,L360steel has the best corrosion resistance.For mildly corroded pipelines,the method of adding corrosion inhibitors and dynamic monitoring can be adopted.For moderately and severely corroded pipelines,it can be used techniques including internal interpolation repair,wind extrusion coating repair and local rein-forcement to repair defects of pipeline body and anti-corrosion layer.After the application,the fail-ure rate of pipeline is obviously decreased and the loss is reduced by 4553000yuan every year with in-calculable environmental benefits .Keywords:carbon steel;corrosion resistance;anti-corrosion;ferrite;repair technology 作者简介:王金梭,工程师,2007年毕业于佳木斯大学(无机非金属专业),从事管道防腐检测工作,186****6941,****************,黑龙江省大庆油田有限责任公司第五采油厂,163414。
国内外油气管道腐蚀及防护技术研究现状及进展_胡鹏飞

0 前言
随着石油天然气开采量的日益扩大 , 油气管道的腐蚀及防护也越来越受到重视。 CO2 作为石油、 天然 气或地层水的组分存在于油气层中, 采用 CO2 混相技术提高原油采收率时, 也会将 CO2 带入原油生产系 统。CO2 溶于水后, 在相同 PH 值时其总酸度比盐酸高, 故对井内管材的腐蚀比盐酸更严重
[ 10]
。
文献 [ 18] 报道了管道外防腐绝缘层与阴极保护的联合使用是最经济、 最合理的防腐措施 , 还报道了燕 山石化公司对埋地管道采用防腐涂层结合牺牲阳极的阴极保护法, 对管道的防腐起到了良好的效果。 3. 7 镀铝钢在管道防腐技术上的应用 早在 1893 年 , 德国人就发明了钢材热浸镀铝技术, 随后法国、 美国也公布了热浸镀铝的技术专利 , 20 世纪 50 年代到 60 年代 , 国外钢带热浸镀技术处于迅速发展时期 几个镀铝生产厂家
第 24 卷 第 2 期 2003 年 6月
河 南 科 技 大 学 学 报 ( 自 然 科 学 版 ) Journal of Henan University of Science and T echnology ( Natural Science)
Vol. 24 No. 2 June 2003
文章编号: 1000- 5080( 2003) 02- 0100- 04
3 常用的腐蚀防护技术
3. 1 采用缓蚀剂 采用缓蚀剂防腐主要是利用缓蚀剂的防腐作用来达到减缓油管腐蚀的目的。其防腐效果主要与井 [ 12] 况、 缓蚀剂类型、 注入周期、 注入量等有关。该技术成本低, 初期投资少 , 但工艺复杂, 对生产影响较大 。 此外 , 不同井况要求缓蚀剂的类型也不尽相同 , 通常情况下 , 中性介质中多使用无机缓蚀剂, 以钝化型和沉 淀型为主 ; 酸性介质使用的缓蚀剂大多为有机物, 以吸附型为主。但现在的复配缓蚀剂根据需要在用于中 性介质的缓蚀剂中也使用有机物, 而在用于酸性水介质的缓蚀剂中也添加无机盐类。不同金属的原子外 层电子排布、 电位序列、 化学性质等有所不同 , 它们在不同介质中的吸附和成膜特性也不相同
海洋管道内壁局部腐蚀的监测关键技术研究

海洋管道内壁局部腐蚀的监测关键技术研究海洋油气集输管线是海洋油气开采系统的重要组成部分。
由于油气输送管道内的流质含有较多的腐蚀性介质,管道内壁腐蚀成为困扰海洋油气开发的重要问题之一。
海洋油气集输管线的铺设距离较长,管道内部的流质环境复杂,管道内流质的流态、温度、含沙量以及腐蚀成分的变化都可能导致不同类型的局部腐蚀问题。
当管道内外壁存在较大温差时,湿蒸汽在管道内壁的冷凝可能造成顶部腐蚀的发生;在管道内流速较缓的区域,由于腐蚀产物和固体颗粒在管道底部的堆积可能导致沉积物下腐蚀的发生;当管道内的流速较高时,高速流动的腐蚀介质可能导致磨损腐蚀的发生,针对管道常见的局部腐蚀问题,目前仍缺乏有效的手段进行在线监测。
因此,本文依托国家“十二五”重大科技专项“荔湾3-1气田腐蚀监测与防腐系统设计”,研制了基于新型双环电阻传感器的海底管道局部腐蚀监测系统,并在模拟循环管路中针对海底管道一些常见的局部腐蚀问题开展了研究,主要工作归纳如下:(1)提出了一种可用于海底管道内壁局部腐蚀在线监测的双环电阻传感器,通过将管道的环形切片分成六个分区,采用特殊的电路设计,实现了管道内壁全周向的在线腐蚀监测。
双环电阻传感器相比传统的电阻传感器具有更高的监测精度和适用范围,在管道内外壁存在较大温差时仍可以准确测量腐蚀深度。
(2)结合电化学方法和双环电阻传感器,对管道中低流速流质情况下,沉积物覆盖所导致的电化学腐蚀和有机膦缓蚀剂EDTMPS(Ethylene Diamine Tetra Methylene Phosphonic Acid Sodium)的作用效果进行了实验研究。
实验结果表明:由于沉积物覆盖所导致的氧浓差电池是导致沉积物下腐蚀的主要原因。
在静止溶液环境中,有机膦缓蚀剂EDTMPS对裸钢和沉积物覆盖碳钢的腐蚀均表现出良好的抑制效果;但在管道内流质流动状态下,有机膦缓蚀剂EDTMPS对沉积物覆盖碳钢腐蚀的抑制作用却表现出明显的失效,甚至EDTMPS对沉积物覆盖所导致的原电池腐蚀有显著的促进作用。
油田地面集输系统腐蚀原因防腐技术论文
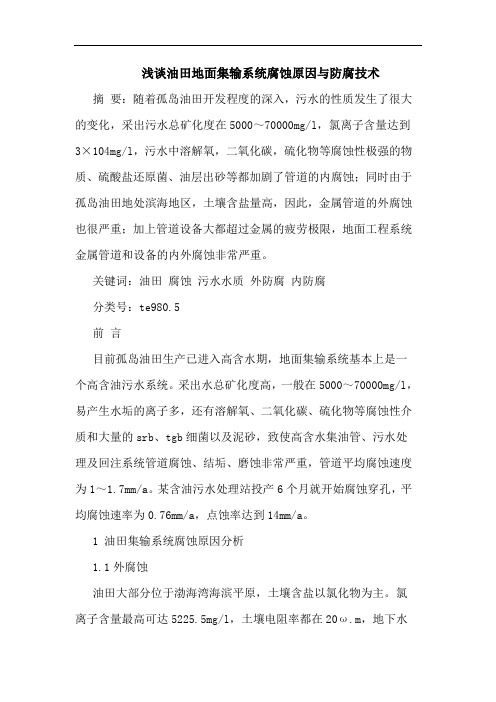
浅谈油田地面集输系统腐蚀原因与防腐技术摘要:随着孤岛油田开发程度的深入,污水的性质发生了很大的变化,采出污水总矿化度在5000~70000mg/l,氯离子含量达到3×104mg/l,污水中溶解氧,二氧化碳,硫化物等腐蚀性极强的物质、硫酸盐还原菌、油层出砂等都加剧了管道的内腐蚀;同时由于孤岛油田地处滨海地区,土壤含盐量高,因此,金属管道的外腐蚀也很严重;加上管道设备大都超过金属的疲劳极限,地面工程系统金属管道和设备的内外腐蚀非常严重。
关键词:油田腐蚀污水水质外防腐内防腐分类号:te980.5前言目前孤岛油田生产已进入高含水期,地面集输系统基本上是一个高含油污水系统。
采出水总矿化度高,一般在5000~70000mg/l,易产生水垢的离子多,还有溶解氧、二氧化碳、硫化物等腐蚀性介质和大量的srb、tgb细菌以及泥砂,致使高含水集油管、污水处理及回注系统管道腐蚀、结垢、磨蚀非常严重,管道平均腐蚀速度为1~1.7mm/a。
某含油污水处理站投产6个月就开始腐蚀穿孔,平均腐蚀速率为0.76mm/a,点蚀率达到14mm/a。
1 油田集输系统腐蚀原因分析1.1外腐蚀油田大部分位于渤海湾海滨平原,土壤含盐以氯化物为主。
氯离子含量最高可达5225.5mg/l,土壤电阻率都在20ω.m,地下水位一般为1~3米。
按土壤腐蚀性标准判断,油田属极强腐蚀区。
钢质设施的外腐蚀主要受海洋腐蚀环境的影响。
海洋腐蚀环境一般分为海洋大气、浪溅、潮差、全浸和海泥区,腐蚀因素复杂多变,钢结构在不同区带腐蚀特点不同。
1.2内腐蚀油田在用管网主要采用钢质管材,当与电解质溶液接触时,由于不同材料相间电位差不同,它们和可以导电的电解质一起构成了成千上万的腐蚀微电池。
除了金属材料本身的杂质以外,不同金属相互接触,新旧管子连接,焊点焊缝都会造成材料性质的不均匀性,从而导致腐蚀。
除去管材本身的因素外,影响内腐蚀的主要原因有以下几种。
1.2.1化学因素(1)矿化度。
- 1、下载文档前请自行甄别文档内容的完整性,平台不提供额外的编辑、内容补充、找答案等附加服务。
- 2、"仅部分预览"的文档,不可在线预览部分如存在完整性等问题,可反馈申请退款(可完整预览的文档不适用该条件!)。
- 3、如文档侵犯您的权益,请联系客服反馈,我们会尽快为您处理(人工客服工作时间:9:00-18:30)。
1
管道局部腐蚀原因分析
1. 磨损、冲刷腐蚀
从查阅资料中发现,有80%的管线穿孔是由磨损、冲刷腐蚀造成。发生穿孔
的管段中体现在井排来油汇管至分离器进口管段,以及污水外输泵出口管段。
穿孔的形式表现为点蚀,穿孔发生的部位突出表现在管线底部、弯头或三通
下游直管段及外输泵出口(弯径后)管段。原因是:进站混输原油介质中含砂严重,
在目前进站原油综合含水量极高的情况下,混输原油介质携砂、裹砂能力大幅度
下降,砂粒随介质在管线底部高速流动,对管线底部形成线状磨损,在高矿化度
含油污水的腐蚀影响下, 加速了管线的穿孔。同时,由于污水经过外输泵的加压
增速,对外输泵出口管段,尤其是外输泵出口管段和闸阀后直管段底部形成强烈
的冲刷磨损磨蚀,穿孔现象频繁发生。
2. 微电池腐蚀
形成微电池腐蚀的原因是多方面的,但主要与金属的化学成分、合金组织、
物理状态的不均、金属表面膜的不完整和土壤结构的差异有直接的关系。因在
同一金属的不同部位存在着一些化学或物理状态上的不均匀分布,从而在相同
金属的不同位置上形成了电极电位的高低差异,这也就产生了许许多多个微小
的腐蚀电池。这种微电池腐蚀在站内工艺管网中是普遍存在的,直观地表现在与
干线连接的压力表头和架空管道金属支撑架部位处的管道腐蚀上。前者主要是
源于压力表接头与干线母材之间存在着化学成分的不均匀及金属组织的不均匀;
后者则是由于金属掺套与架空管道焊接在一起,造成了金属掺套与干线母材均
化学成分不均一,以及在架空管道受到热应力变形时,与支掺套相接触的管道所
受到的应力状态不均匀。这些不均匀性, 都会导致管道受到微电池腐蚀。
3. 浓差电池腐蚀
浓差电池腐蚀是站内工艺管道常见的一种腐蚀现象。穿墙、穿管沟的管线
腐蚀大都属于浓差电池腐蚀。其腐蚀机理是:当同一种金属通过不同的电解质溶
液或电解质溶液的浓度、温度、压力等条件不同时,在金属的表面便产生不同的
电极电位,形成浓差腐蚀电池,电极电位较低的管道部位为腐蚀电池的阳极发生
腐蚀。
站内工艺管网的架空管段,其保温层把伴热线和干线包裹在一起。由于伴热
2
线位于管道的下半部,这样就使得在管道的下部与保温材料之间出现一个气室。
当管道的防水层被破坏后,氧和水分便从管道的顶部(该处的保温层与管道紧紧
相贴)开始向内渗透。因为气室的存在,在管道的上部与下部,就形成了氧浓差腐
蚀电池。管道的上部含氧浓度较低是腐蚀电池的阳极,遭到腐蚀的管道顶部,其
腐蚀面积较大,腐蚀深度可达mm3~2。另外,穿墙管道的腐蚀大多也属于氧浓
差电池腐蚀。
4. 土壤腐蚀
埋地金属管道的腐蚀大多属于土壤腐蚀,土壤腐蚀受土壤pH值、杂散电流、
化学反应、土壤的电阻率和细菌的作用等因素的影响,尤其是土壤的结构,管道
的埋深,回填土的松紧等条件的影响,管道四周的含氧浓度和含水量都将存在着
差异,这就为产生土壤腐蚀提供了必备的条件。根据土壤腐蚀机理分析,埋地管
道上部由于接近地面,且回填土不如原土结实,因此该(沥青防腐有缺陷)部位氧
气浓度大,电极电位高,是腐蚀电池的阴极区,管道底部则氧气浓度小,电极电位
低,是腐蚀电池的阳极区,即遭受腐蚀的部位。
5. 点蚀
点蚀是造成地沟管段及架空管段局部腐蚀的原因之一。由于防水层老化龟
裂,使大部分保温层长年处于潮湿状态。外界水份的渗入,溶解了保温材料中的
盐份(如Cl1—),使之在管壁的外表形成一层电解质溶液。一旦因某种原因,管道
的腐蚀层被局部破坏而显露出金属表面后,由于其组织、杂质物等金属构造上的
不均, 极易成为点腐蚀源。
6. 缝隙腐蚀
缝隙腐蚀也是造成地沟管段及架空管段局部腐蚀的原因之一。在紧贴伴热
线的管道的部位,由于长期受热过高,防腐层老化加快,龟裂成缝隙状,这些缝隙
为缝隙腐蚀的发生提供了客观条件。缝隙腐蚀的腐蚀机理是由缝隙内外氧的浓
度差而引起氧浓差电池的作用。在缝隙内部形成阳极,缝隙外部形成阴极,两极
的反应过程与点蚀反应过程基本相同,随着缝隙内氧的消耗,缝隙内阴离子数量
也相应减少,从而失去电平衡,使得外部的阴离子从外侵入缝隙内,生成电解盐,
而电解盐的水解,又使得缝隙内的pH值降低,为持续缝隙腐蚀提供了进一步发展
的条件。这是一种恶性的腐蚀循环过程,在伴热线区域的管道部位,其腐蚀多呈
3
条形状,并向外延发展成片状腐蚀。
参 考 文 献
[1]王世溪.集输泵站工艺管道局部腐蚀原因及对策.油气田地面工程.防护化工.(2003. 4.22)
[2]谢翔,高安东,李群等.站内工艺管网局部腐蚀分析.油气储运.1996(2)15
[3]王刚,李会影,刘振兴.油气管道的腐蚀与防护[J].黑龙江科技信息.2010
[4]赵海涛.油气输送管道腐蚀因素与防护对策[J].科协论坛(下半月).2009
[5]张玉宝,王强,斯琴图雅.管道内防腐技术现状及发展[J].中国新技术新产品.2010