注塑模课程设计24938

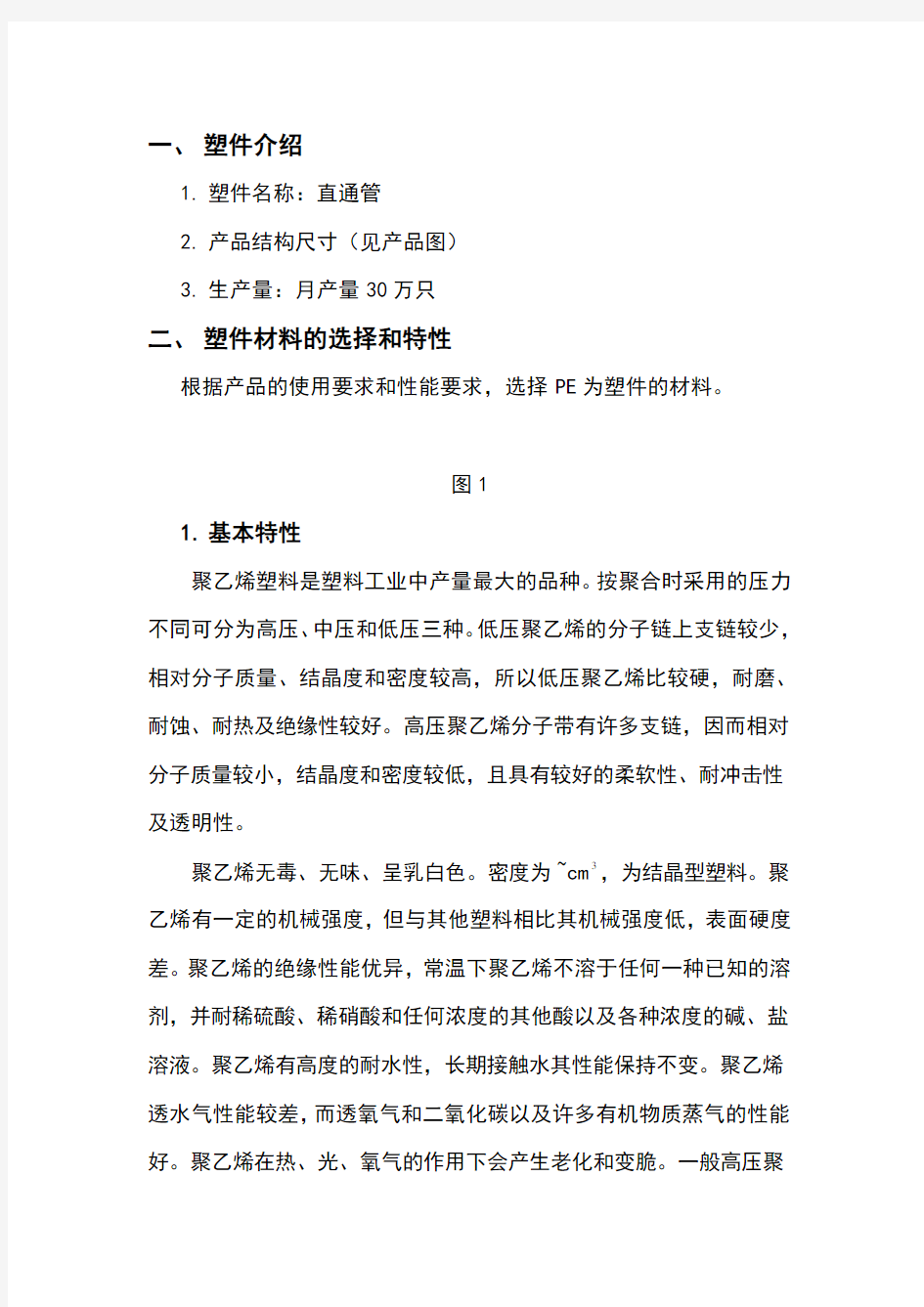
注塑模课程设计
王川
一、塑件介绍
1.塑件名称:直通管
2.产品结构尺寸(见产品图)
3.生产量:月产量30万只
二、塑件材料的选择和特性
根据产品的使用要求和性能要求,选择PE为塑件的材料。
图1
1.基本特性
聚乙烯塑料是塑料工业中产量最大的品种。按聚合时采用的压力不同可分为高压、中压和低压三种。低压聚乙烯的分子链上支链较少,相对分子质量、结晶度和密度较高,所以低压聚乙烯比较硬,耐磨、耐蚀、耐热及绝缘性较好。高压聚乙烯分子带有许多支链,因而相对分子质量较小,结晶度和密度较低,且具有较好的柔软性、耐冲击性及透明性。
聚乙烯无毒、无味、呈乳白色。密度为~cm3,为结晶型塑料。聚乙烯有一定的机械强度,但与其他塑料相比其机械强度低,表面硬度差。聚乙烯的绝缘性能优异,常温下聚乙烯不溶于任何一种已知的溶剂,并耐稀硫酸、稀硝酸和任何浓度的其他酸以及各种浓度的碱、盐溶液。聚乙烯有高度的耐水性,长期接触水其性能保持不变。聚乙烯透水气性能较差,而透氧气和二氧化碳以及许多有机物质蒸气的性能好。聚乙烯在热、光、氧气的作用下会产生老化和变脆。一般高压聚
乙烯的使用温度在800C左右,低压聚乙烯为1000C左右。聚乙烯能耐寒,在-600C时仍有较好的力学性能,-700C时仍有一定的柔软性。
2.主要用途
低压聚乙烯可用于制造塑料管、塑料板、塑料绳以及承载力不高的零件,如齿轮、轴承等;高压聚乙烯常用于制作塑料薄膜、软管、塑料瓶以及电气工业的绝缘零件和包覆电缆等。
3.成型特点
聚乙烯成型时,在流动方向与垂直方向上的收缩差异很大。注射方向的收缩率大于垂直方向的收缩率,易产生变形,并使塑件浇口周围部位的脆性增加;聚乙烯收缩率的绝对值较大,成型收缩率也较大,易产生缩孔;冷却速度慢,必须充分冷却,且冷却速度要均匀;质软易脱模,塑件有浅的侧凹时可强行脱模。
4.制件要求
该塑件尺寸中等,外形为工字形,中间为圆筒形,两端大,中间小,需考虑侧向分型。塑件个部分壁厚均为6mm,属薄壁制品,其它尺寸如图2。一般精度等级IT=4为方便成型,方便开发模具,采用一模二腔,如需要可对制品进行后加工。该制件采用点浇口形式,方便成型。为方便加工和热处理,型腔和型芯采用部分拼镶结构。(1)制件表面光滑平整,不准有飞边、毛刺、及其它的外观缺陷。(2)色泽均匀协调,不准有气泡,裂纹缩孔等缺陷。
(3)制件尺寸要求在偏差范围内,并达到所需要的精度。
三、注塑工艺与模具结构方案
1.模具的型腔数量与布局形式
根据塑件结构特点 ,为保证塑件表面质量和尺寸精度 ,决定采用一模二腔。
直通管零件在模具行业中应用较广,其注塑模一般常采用斜滑块抽芯机构,现我作了改进并设计了如图3 所示的注塑模。结构很简单,成型内孔的型芯设计在定模部分,侧滑块设计在动模部分,斜导柱在定模部分。当动定模分模时,斜导柱开始抽芯动作,定模型芯开始脱模两种动作同时进行定模型芯一方面起内孔的成型作用,在抽芯过程中,它又起定位作用,使塑件不会包禅侧滑块的任何一方。此结构在设计时应注意使斜导柱的抽芯动作与定模型芯的脱模动作同时结束,这样成型后的塑件,就不要依靠任何脱模装置,而自动脱落,便于实现自动化操作。此结构与一般斜导柱抽芯结构比较,可使模具体积缩小 ,节省了钢材,缩短了设计制造周期,减少了注射成型过程的辅助时间,提高了工作效率。
图2
2.模具结构设计
经过对塑件的工艺分析,根据塑件的结构特点,按具体设计要求,这次的注塑模结构设计主要包括: 分型面选择、模具型腔数目的确定及型腔的排列方式、冷却水道布局及浇口位置设计、模具工作零件结构设计及侧向抽芯机构设计等内容。
直通管注射模为双分型面结构 , 模具结构如图 3所示 , 每个模腔均由定模型腔块与动模的 3个侧滑块及型芯和推管闭合而成。模具设计为 1模 2腔 ,选用 2026模架 ,模具闭合高度为 240mm。塑件内部形状由推管及型芯成型 ,推管的外径做为滑块闭合的限位。为保证侧滑块在推管限位处吻合 , 模具上设置了圆锥定位销, 以保证模具的定向基准 , 确保模具侧滑块工作时定位平稳 ,受力均匀。模具在闭合时 ,为保证复位杆带动推板垫板、推板提前复位 , 除复位弹簧外 ,在定模上还设置了确保提前复位的装置 ,由弹簧带动复位杆强行推动复位杆回位 ,这样 ,模具顶出系统就具有了定位强行回位及本身弹簧复位双保险 ,保证了推管提前复位到工作位置 ,防止了侧滑块与推管配合部分产生摩擦 ,避免了此处发生磨损。此时 ,当推动推板垫板推板回位时 ,又带动限位开关确保了模具顶出系统到达工作位置并连动机床进一步闭合模具到工作位置。
该塑件由于为薄壁件 , 因此模具采用了点浇口 ,这样可使塑料在经过进料口的瞬间二次融化 ,提高了塑料的流动性 ,有利于快速充满型腔。
塑件悬臂部分由定模型腔块成型内壁 ,动模型腔块成型外壁 , 点浇口设在动模型腔块外壁一侧 ,增加了开模时塑件滞留在动模的力量 ,开模后 ,塑件悬臂部分留在动模上 ,并处于完全释放无任何阻力状态。
3.模具的工作过程
模具开启 , 定模上的斜导柱带动侧滑块沿动模型腔块、垫板滑
动 ,开启终了 ,机床顶出系统推动模具顶出系统带动推管将塑件推出 ,完成模具一次工作过程。
因型芯成型塑件内部形状 , 为防止推管内壁在工作时磨损型芯的成型部分 , 将推管与型芯配合处的直径设计的略大于型芯的成型部分 ,这样 ,推管在工作时就完全离开型芯的成型部分 , 起到了保护型芯的作用。
4.分型面的选择
a)分型面应选择在塑件外形最大轮廓处;
b)分型面的选择应有利于塑件的顺利脱模;
c)分型面的选择应保证塑件的精度要求;
d)分型面的选择应满足塑件的外观质量要求;
e)分型面的选择要便于模具的加工制造;
f)分型面的选择应有利于排气。
综上所述,选择两边分模,分型面选在最上边的底边。该塑件为机内骨架 , 表面质量无特殊要求 , 但在绕线的过程中上端面与工人的手指接触较多 , 因此上端面最好自然形成圆角; 此外 , 该零件高度为 44mm , 且垂直于轴线的截面形状比较简单与规范 , 故选择工字分型方式 , 这既可降低模具的复杂程度、减少了模具加工难度又便于成型后出件。
该模具采用了 2个分型面 2次分型机构 ,侧向分型抽芯机构为斜导柱带动双锥形滑块进行抽芯 , 由于不便设置推杆 , 推出机构设计为推管推出 , 合理利用了模具内部空间。为降低成本及便于加
工 , 在定模型芯内部设置一冷却水回路 , 以加强型芯内部冷却。
四、 注射机的选用与模具类型
1. 计算单件塑件的体积与质量
塑件的体积的计算,经计算塑件的体积为V ≈42cm 3
(1) 塑件的密度,查表得聚乙烯的密度为ρ=cm 3
(2) 塑件的质量为W=V ×ρ=42×=
2.初步选用成型设备
采用一模2件的模具结构,考虑其外形尺寸,注射时所需压力和工厂现有设备等情况,初步选用注射机型号为XS-ZY-125。
3.模具类型
根据塑件的成型工艺方案确定模具的类型为注射模。
4.选用标准模架
根据结构草图,查标准手册,选用的标准模架为180×150中的派生型,标准模架的选用程序及要点有:
a)模架厚度H 和注射机的闭合距离L 的关系为:
min max L H L ≤≤
通过查表,计算模具闭合高度 :
m L =A+B+30+30+C+25=25+75+30+30+90+25=275mm
b)开模行程与定、动模分开的间距与推出塑件所需行程之间的尺寸关系为:模具推出塑件距离须小于顶出液压缸的额定顶出行程;通过查表,计算模具闭合高度
c)选用的模架在注射机上的安装;
d)选用模架应符合塑件及其成型工艺的技术要求。
五、浇注系统的设计
1.浇注系统的设计原则
a)了解塑料的塑料的成型性能
b)尽量避免或减少产生熔接痕;
c)有利于型腔中气体的排出;
d)防止型芯的变形和嵌件的位移;
e)尽量采用较短的流程充满型腔;
f)流动距离比和流动面积比的校核。
2.浇注系统的设计
(a)浇口套的设计
浇口套一般采用碳素工具钢(如T8A、T10A等)制造,热处理淬火硬度为53~57HRC。由于初选注射机的型号为XS-ZY-125,查表得喷嘴圆弧半径为12mm,喷嘴孔直径为4mm 。主流道通常设计在浇口套中,为了方便注射,主流道始端的球面必须比注射机的喷嘴圆弧半径大1~2mm,防止主流道口部积存凝料而影响脱模,通常将主流道小端直径设计的比喷嘴孔直径大~1mm。
(b) 浇口的设计
常见的形式有:直接浇口、点浇口、侧浇口,本模具选用点浇口。浇口的位置选择:尽量缩短流动距离、避免熔体破裂现象引起塑
件的缺陷、浇口应开设在塑件壁厚处、考虑分子定向的影响、减少熔接良提高熔接强度。
根据塑件材料及形状 , 为保证型腔各部位均衡进料 ,防止塑件变形和缺料 ,浇口设计成 4处点浇口均匀分布的形式 ,以便缩短流程 ,加快注射速率 ,降低流动阻力 ,这样可以做到进料点对称 ,充模均匀。为避免产生分子高度定向 ,局部应力增加 ,甚至开裂的现象 , 将 4点浇口位置设于塑件外侧环形与
轮辐状加强筋交叉处(直径为 <5mm小圆柱上) 。这样 ,点浇口处的制品壁厚增加 ,且其周围呈圆弧形过渡 ,就可防止上述现象发生。
此外 , 模具成型部分设计为镶拼组合式结构 , 4处点浇口设在定模镶块的成型面上 , 有利于利用配合间隙排气 , 避免了因排气不良造成浇口部位塑料烧焦 ,而在制品上产生黑色条斑及黑点。
(c) 主流道设计
依据一模两件一次注射时所需的塑料量 , 选定XS–ZY-125型注射机为成型设备。
根据设计手册查得XS-ZY-125型注射机喷嘴的有关尺寸:
喷嘴前端的孔径0d=Φ4mm;
喷嘴前端的球面半径0R=12mm。
根据模具主流道与喷嘴的关系 , 取主流道球面半径 R =13mm , 取主流道的小端直径 d =。
(d) 分流道及浇口设计
综合考虑塑件的体积、壁厚、形状的复杂程度、注射速率、分流道长度等因素 , 本模具分流道的截面形状采用半圆形 , 查设计手册 , 取 R = 4mm。
根据塑件的成型要求、型腔的排列方式及成型时有利于填充、排气等因素 , 选用截面形状为矩形的侧浇口较为理想。其截形尺寸初选为 (b×l×h) 1mm×× ,试模时修正。
六、模具的相关设计
1.支承零部件的设计
模具支承零件主要有支承板(动模垫板)、垫板(支承块)、支承块、支承板、支承柱(动模支柱)等。支承板的设计要求是,具有较高的平行度和必要的硬度和强度。根据草图,本模具要用支承板,支承块。支承板的厚度根据塑件在分型面上的投影面积得其厚度为30mm.
2.合模导向机构的设计
导向机构的作用有:
a)定位作用;b)导向作用;c) 承受一定的侧向压力。
导柱结构的技术要求有:
a)导柱导向部分的长度应比凸模端面的高度8~10mm;
b)导柱前端应做成锥台形或半球形;
c)导柱应具有硬而耐磨的表面和坚韧而不易折断的内芯,多采
用20钢(经表面渗碳淬火处理)或者T8、T10钢(经淬火处理),硬度为50~55HRC;
d) 导柱应合理均布在模具分型面的四周,导柱到模具边缘应有
足够的距离,以保证模具强度;e)导柱固定端与模板之间一般采用H7/m6的过度配合,导柱的导向部分通常采用H7/f7的间隙配合。
3.侧向分型抽芯机构的设计
该塑件抽芯为外侧向分型抽芯 , 为此设计了 1套斜导柱滑块抽芯机构。滑块采用双滑块形式 ,外形为锥形 , 利用锥形模套对其进行定位和锁紧,既保证牢固可靠 ,又保证抽芯导滑动作平稳 ,并可使动、定模之间具有较高的同轴度。抽芯时 ,滑块由连接板带动 ,两者之间用螺钉连接 ,加工简便。
4.推出机构的设计
由于塑件的加强筋允许有较大的脱模斜度 , 根据塑件空心的特点 , 在动模型芯和中间设计了推管 ,既简化了结构 ,还可使推出动作均匀、可靠。此外 ,还巧妙地利用动模型芯的内部空间设置1复位杆,解决了外部不便设复位杆的问题。
1)推出机构一般由推出、复位和导向三大部件组成。
2)推出机构按其推出动力来源可分为手动推出机构、机动推出机构和液压与气动推出机构等。手动推出机构是掼模具开模后,由人工操作的推出机构推出塑件,它可分为模内手工推出和模外手工推出两种。
3)推出机构按照模具的结构征分为一次推出机构、定模推出机构、二次推出机构、带螺纹的推出机构等。
4)推出机构的设计要求有:
a)设计推出机构时应尽量使塑件留于动模一侧;
b)塑件在推出过程中不发征变形和损坏;
c)不损坏塑件的外观质量;
d)合模时应使推出机构正确复位;
e)推出机构应动作可靠。
5)一次推出机构包括:推杆推出机构、推管推出机构、推件板推出机构、活动镶块或凹模推出机构和多无综全推出机构等。
由上面的结构草图和零件形状,推出机构选用推杆推出,拉料杆选用Z 字型拉料杆。
5.排气方式
该模具为小型模具,可利用配合间隙排气、在分型面上开设排气槽、利用排气塞排气。
七、抽芯机构的设计与计算
1.确定抽芯距
抽芯距一般应大于成型孔 (或凸台)的深度 , 本塑件孔壁 1H 、凸台高度 2H 相等 , 均为1H =2H = (14 – / 2 (mm) =
另加 3 - 5mm 的抽芯安全系数 , 故去抽芯距 S =。
2.确定斜销倾角
斜导柱的倾斜角α是斜抽芯机构的主要技术参数之一 , 它与抽拔力以及抽芯距有直接的关系 ,一般α= 15° ~25° , 本模具选取α= 20° 。
3.确定斜销的尺寸
斜导柱的直径取决于抽拔力及其倾斜角度 , 经进行有关计算 , 取斜导柱直径 d =Φ14mm。
斜销的长度应根据抽芯距、固定端模板厚度、斜销直径、斜角大小等因素确定。根据公式 L = 1l + 2l + 4l + 5l
由于上模座板和上凸模固定板厚度尺寸尚不确定 , 故初选 ha = 25mm (如在后续的设计 ha 有变化则修正L 的长度) ,取 D = 20mm , 经计算后 , 取L = 55mm。
由于塑件上具有外侧凹, 其难点在于塑件不能直接从模具中脱出, 此时需将成型线圈骨架侧凹的模具零件作成活动的侧型芯。在塑件脱模前先将侧型芯从塑件上抽出, 然后再从模具中推出塑件, 侧型芯安装在侧滑块上。如图2 所示。
4.侧滑块抽芯距的计算
斜导柱由于抽芯距较大, 采用斜导柱抽芯, 斜导柱的倾斜角取α= 20° , 锁紧块的角α′ = α+ 3 = 23° , 其开模距斜导柱的抽芯力:
式中: F c——抽芯力N ;
A ——塑件包络型芯的面积为
p——塑件对侧型芯的收缩应力(包紧力) , 其值与塑件的几何形状及塑料的品种、成型工艺有关, 取p=
υ——热状态时对钢的摩擦系数, 取υ=
α——侧型芯的脱模斜度或倾斜角, 取α = 30′=°。
由塑料模手册查得斜导柱的直径d = 14 mm 。斜导柱的长度L z , 如图4 所示:
图3 斜导柱长度计算简图
z 1245=L L L L L +++ =2(510mm 2cos sin d h s tg ααα
+++~) z L ——斜导柱总长度
2d ——斜导柱固定部分大端直径,取Φ20mm
h ——斜导柱固定板厚度,取20mm
d ——斜导柱工作部分直径,取14mm
s ——抽芯距,取25mm
八、冷却系统的设计
模具冷却采用循环水道 ,由于该塑件壁薄 ,过早冷却 ,注射时塑料会来不及充满形腔 ,所以水道采用了稍大于 3倍合理水道直径的数值做为型腔面至水道中心的距离 ,使模具模温均匀适当 ,以适应在正常周期下工作的需要。
冷却水回路的布置:
(1)冷却水道应尽量多、截面尺寸应量大;
(2)冷却水道离模具型腔表面的距离应尽量均匀,水道孔边到型腔表面距离为10~15mm ;
(3)水道出入口的布置,应使出入口温差尽量小;
(4)冷却水道应沿着塑料收缩方向设置;
(5)冷却水道的布置应避开塑件易产生熔接痕的部位。
九、校核模具与注射机的有关尺寸
1.最大注射量的校核
由式,nm + m1≤Kmp知,mp为注射机允许的最大注射量,n为型腔数,m单个塑件的质量,m1为浇注系统所需的塑料质量,K为注射机最大注射量的利用系数,取。
由前面的计算可得:m=63g,n=1,m1=9g
即 1×3+9≤
mp≥90g
经查得注射机的最大注射量为125g,所以最大注射量满足要求。
2.校核锁模力
由式知,Fz=p(nA+A1)<Fp,p为注射压力,查表取其值为:p=35MPa,
Fz=35×[×30×30+1××10×10]=88KN
查表得该注射机的锁模力是900KN,所以满足要求。
3.校核最大最小模厚
查表得注射机XS-ZY-125得最大模厚为300mm,最小模厚为200mm,而Lm为275mm,即满足要求。
4.开合模行程校核
查表得注射机XS-ZY-125的最大开合模行程S=300mm,S≥75+100+(5~10)=185mm,满足要求。