铝合金高速数控铣削参数优化
典型薄壁零件数控铣削加工工艺

典型薄壁零件数控铣削加工工艺数控铣削是一种高精度、高效率的数控加工方法,广泛应用于模具、航空航天、船舶、汽车、电子、仪器仪表等行业。
在零件加工中,薄壁零件因其结构特殊、加工难度大,对加工工艺要求较高。
本文将针对典型薄壁零件的数控铣削加工工艺进行介绍和分析。
一、工件材料及加工要求1. 工件材料:典型薄壁零件常用的材料有铝合金、钛合金、不锈钢等,材料硬度一般在28-45HRC之间。
2. 加工要求:薄壁零件加工一般要求表面光洁度高、尺寸精度要求高、壁厚薄、结构复杂等特点。
二、数控铣削工艺分析1. 工艺方案选择:根据零件的结构特点和加工要求,选择合适的数控铣削刀具和切削参数。
对于铝合金等材料,一般选择硬质合金刀具,切削参数选择合适的进给速度和转速。
2. 夹紧方式选择:薄壁零件加工时,应选择合适的夹紧方式,避免加工过程中因变形而影响加工质量。
一般可采用夹具夹紧或磁力吸盘夹紧等方式,根据零件尺寸和形状特点选择合适的夹紧方式。
3. 切削力控制:在数控铣削过程中,控制切削力对薄壁零件加工至关重要。
要合理选择切削参数和刀具几何角度,降低切削力,避免引起零件变形和加工质量不稳定。
4. 节渣处理:薄壁零件加工过程中,切屑容易产生,特别是在高速切削时更为显著。
应采取合适的节渣方式,避免切削刀具堵塞,影响加工质量。
5. 冷却润滑:在数控铣削过程中,及时有效的冷却润滑对加工质量和刀具寿命有着重要影响。
对薄壁零件加工,更需要合理选择喷淋位置和冷却润滑液的使用方式,以防止零件变形和表面质量不稳定。
6. 加工精度控制:薄壁零件加工时,对尺寸精度和表面质量要求较高。
在数控铣削过程中,应严格控制切削参数,采取合适的刀具路径和切削刀具轨迹,避免因加工过程中引起加工质量问题。
7. 加工工艺优化:针对典型薄壁零件的形状特点和加工要求,应综合考虑工艺方案和加工工艺优化,在保证加工质量的前提下,提高加工效率和降低成本。
例如采用高速切削、干法加工等新技术,以提高加工效率和节约成本。
铝合金切削刀具加工参数分析与选用

冷加工
! ! !
!"##$%& ’(()*
刀! ! 具
! ! ! ! ! ! !
如车削、镗削加工小型铝合金零件时,可采用小尺 寸的钎焊硬质合金刀具,经整体刃磨后使用。主切削刃 参数应选择:前角 ! " # $% 左右,后角 " " # &&% ’ ()% ,刃 倾角 # * # )% ’ &)% ,主偏角 $ + # ,-% ’ .)% ,刀尖角 % + / .)% ,刀尖圆弧半径 + ! # )0 1 ’ &22。 如采用硬质合金铣刀进行铣削时,切削刃应保持锋 利,前刀面应抗粘接,排屑应流畅。有关切削刃参数选 择为:圆周刃径向前角 ! " %,% ,后角 " " %&)% 。立铣刀 螺旋角 &%1)% ,大的螺旋角可使圆周刃的实际切削前角 变大。用于粗加工的铣刀,在切削刃上开出分屑槽,或 将切削刃制造成波形刃都能使排屑更好,切削更顺畅, 效率更高。 ( ( ) 345 刀具! 一般而言, 345 刀片只制成单刃, 其结 构 形 式 和 几 何 参 数 符 合 67(),$ —&.8) 的 规 定。 345 刀具的刀尖刃口几何参数有如下几种情形:前角 ! " # )% 、&)% ,后 角 " " # ,% 、 &&% 、 ()% , 主 偏 角 $ + # ,-% 、 .)% , 刀 尖 圆 弧 半 径 + ! # )0 )-22、 )0 &22、 )0 (22、)0 922、)0 822、&0 (22,各 切 削 参 数 可 根 据 加工需求组合应用。 ( 1 ) 天然金刚石刀具! 天然金刚石刀具的切削刃有 四种基本几何形状,即尖刃、直刃、圆弧刃和多棱刃。 尖刃,在主切削刃和副切削刃之间有圆角,刀尖圆 弧半径 + ! 一般为 &0 ) ’ &0 822,主偏角 $ + # 9-% ,副偏角 $ + :# (% ,前角 ! " # 80 -% ,后角 " " # )% 。该形状切削刃的 刃磨和对刀比较方便,故应用最为广泛,但磨损后需要 立即重磨。 直刃即修光刃,长度为 )0 &8 ’ )0 (-22。必须与工 件表面平行或形成极小的副偏角,其刃磨和对刀比较困 难,但加工表面粗糙度值较小,多用于铝合金零件表面 质量要求较高的表面加工。 圆弧刃刃口圆弧半径为 (0 -22,该形状切削刃的对 刀调整比较方便,但刃磨最困难,多用于对刀调整比较 困难的场合。具有这种切削刃的刀具在切削时被切金属 的切削区变形程度较大,因而工件的表面粗糙度值较 大。 多棱刃,具有该刃形的刀具切削时,切削层残留面 高度的实际值和理论值较接近,切削区变形程度较小, 因而工件表面质量较好。但其刃磨工作量较大,故其应 用并不广泛。
CNC机床加工中的加工参数调整与优化

CNC机床加工中的加工参数调整与优化随着科技的不断进步和制造业的发展,计算机数控(CNC)机床在工业生产中扮演着越来越重要的角色。
CNC机床通过预先编程的方式控制工具和工件的相对运动,实现复杂零件的加工。
在CNC机床加工中,加工参数的调整和优化是提高加工质量和效率的关键。
一、加工参数的定义和影响因素CNC机床的加工参数包括切削速度、进给速度、进给量和切削深度等。
这些参数的选择和调整直接影响到加工效果和工件质量。
1. 切削速度切削速度是指刀具在工件上接触面上相对于工件表面的移动速度。
切削速度的选择与刀具材料、被加工材料和加工方式等因素有关。
合适的切削速度能够保持刀具寿命、提高加工效率和保证加工质量。
2. 进给速度进给速度是指工件在刀具上运动的速度。
进给速度的选择与刀具直径、被加工材料和切削深度等因素相关。
适当的进给速度能够保持刀具的寿命、减小加工周期并提高加工精度。
3. 进给量进给量是指刀具在过程中每一次接触工件的移动距离。
合适的进给量可以控制切削力和切削温度,从而影响加工的质量和效率。
4. 切削深度切削深度是指刀具在一次切削过程中切削轮廓的垂直距离。
切削深度的选择应该考虑到刀具的强度和创伤力等因素。
切削深度过大会增加切削力、温度和振动,降低切削质量。
二、加工参数调整的方法1. 经验法在实际生产中,经验法是最为常用和简便的调整加工参数的方法之一。
通过工人的经验和实践,根据不同的工件和加工要求,逐渐调整各个加工参数的数值,找到最佳的加工参数组合。
2. 实验法利用实验方法进行加工参数调整是一种科学且系统的方法。
通过合理设计实验方案,对不同参数组合进行实际加工,然后评估加工结果和质量,从而找到最优加工参数。
3. 仿真模拟法借助计算机软件进行CNC机床加工仿真模拟是一种高效且经济的方法。
在模拟软件中,可以根据加工要求和工件特点,调整各个加工参数的数值,然后模拟加工过程,评估加工效果并优化加工参数。
三、加工参数优化的技术手段1. 供应链优化加工参数优化不仅仅局限于CNC机床自身的加工参数调整,还包括整个供应链的优化。
CNC机床动态性能参数建模及优化研究

CNC机床动态性能参数建模及优化研究首先,CNC机床的动态性能参数主要包括机床的加速度、最大加速度、最大速度等。
这些参数对于机床运动的快慢和稳定性有着直接影响。
因此,建立CNC机床的动态性能参数模型是研究的首要任务。
建立CNC机床动态性能参数模型可以通过实验和仿真两种方法进行。
实验方法是在实际的CNC机床上进行测量和测试,以获取实际的性能数据。
仿真方法是基于计算机建立机床的运动模型,通过模拟机床运动过程来预
测性能参数。
这两种方法可以结合使用,相互验证和补充。
在建立了CNC机床动态性能参数模型之后,优化研究可以进一步进行。
优化研究的目标是使CNC机床的动态性能参数达到最佳状态,以提高机床
的工作效率和加工质量。
在优化研究中,可以采用多种方法进行,如遗传算法、粒子群算法、
模拟退火算法等。
这些算法基于数学模型和优化原理,通过迭代计算和优
化选择,逐步找到最佳解。
在应用这些算法时,需要考虑到机床的动态性
能参数之间的相互影响和约束条件,以保证优化的结果符合实际应用需要。
总结起来,CNC机床动态性能参数建模及优化研究是一个复杂而重要
的课题。
通过建立CNC机床的动态性能参数模型,可以预测和评估机床的
性能,进而通过优化研究提高机床的工作效率和加工质量。
这对于提高制
造业的竞争力和生产效益具有重要意义。
CNC机床加工中的刀具路径规划与优化算法
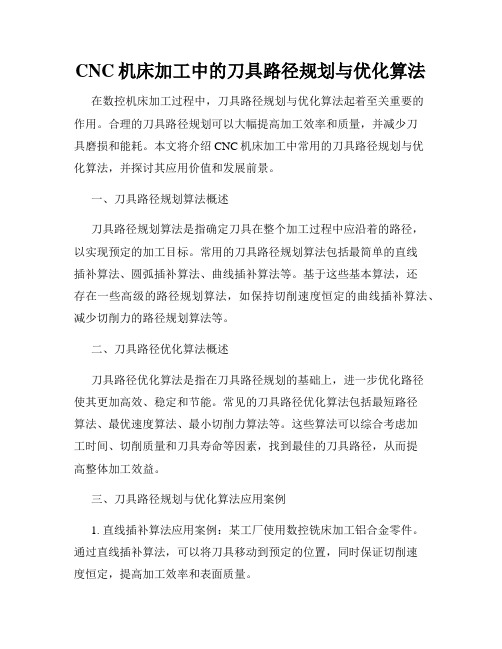
CNC机床加工中的刀具路径规划与优化算法在数控机床加工过程中,刀具路径规划与优化算法起着至关重要的作用。
合理的刀具路径规划可以大幅提高加工效率和质量,并减少刀具磨损和能耗。
本文将介绍CNC机床加工中常用的刀具路径规划与优化算法,并探讨其应用价值和发展前景。
一、刀具路径规划算法概述刀具路径规划算法是指确定刀具在整个加工过程中应沿着的路径,以实现预定的加工目标。
常用的刀具路径规划算法包括最简单的直线插补算法、圆弧插补算法、曲线插补算法等。
基于这些基本算法,还存在一些高级的路径规划算法,如保持切削速度恒定的曲线插补算法、减少切削力的路径规划算法等。
二、刀具路径优化算法概述刀具路径优化算法是指在刀具路径规划的基础上,进一步优化路径使其更加高效、稳定和节能。
常见的刀具路径优化算法包括最短路径算法、最优速度算法、最小切削力算法等。
这些算法可以综合考虑加工时间、切削质量和刀具寿命等因素,找到最佳的刀具路径,从而提高整体加工效益。
三、刀具路径规划与优化算法应用案例1. 直线插补算法应用案例:某工厂使用数控铣床加工铝合金零件。
通过直线插补算法,可以将刀具移动到预定的位置,同时保证切削速度恒定,提高加工效率和表面质量。
2. 圆弧插补算法应用案例:某汽车制造公司使用数控车床加工车轮零件。
通过圆弧插补算法,可以在车轮表面上按照预定轮廓进行切削,从而实现精准的车轮加工。
3. 路径优化算法应用案例:某飞机零件制造公司使用数控车床加工复杂曲面零件。
通过路径优化算法,可以找到最短路径,并在切削过程中减少刀具的停顿时间和切削力,从而提高加工效率和刀具寿命。
四、刀具路径规划与优化算法发展前景随着数控机床技术的不断发展,刀具路径规划与优化算法也将不断改进和创新。
未来的发展趋势包括以下几个方面:1. 人工智能的应用:人工智能技术可以通过学习大量的加工数据和经验,提供更加智能化的刀具路径规划与优化算法,从而实现更高效、更精确的加工。
2. 进一步整合切削力和切削热的优化:通过综合考虑切削力和切削热等因素,优化刀具路径,实现更加稳定和高效的加工过程。
切削参数优化范文

切削参数优化范文一、切削参数的选择和优化方法切削参数的选择和优化是一个复杂的过程,需要考虑到被加工材料的硬度、切削工具的材质和几何形状、切削速度和进给速度等因素。
常用的切削参数包括切削速度、进给速度、切削深度和切削宽度。
(一)试刀法试刀法是一种常用的切削参数选择的方法,通过试刀来确定最佳的切削参数。
试刀前需保证刀具采用合适的刀尖半径,试刀时应逐步调整切削速度、进给速度、切削深度和切削宽度,记录下每种参数对加工表面质量的影响,最终选择最佳的切削参数。
(二)试件法试件法是另一种常用的切削参数选择的方法,通过在试件上进行不同切削参数的加工,然后测量加工表面的质量指标,如表面粗糙度、加工硬度等,最终选择最佳的切削参数。
试件的材料和几何形状需要与实际加工件相似,以确保试削结果的准确性。
(三)数值模拟法数值模拟法是一种现代化的切削参数优化方法,通过建立数值模型,通过数值模拟分析不同切削参数对加工过程和加工表面质量的影响。
数值模拟法可以有效地提前预测切削参数对加工结果的影响,减少试刀试件的数量和试验时间,提高优化的效率和准确性。
二、切削参数的优化步骤切削参数的优化包括参数的选择和调整两个步骤。
(一)参数的选择1.切削速度的选择:切削速度的选择需要考虑材料的硬度、切削工具的材质和几何形状等因素。
一般来说,对于硬度较高的材料,需要选择较低的切削速度;对于切削刚度较低的加工工具,应采用较低的切削速度。
2.进给速度的选择:进给速度的选择需要考虑到切削力和加工表面质量。
较大的进给速度会增加切削力,但可以提高加工效率;较小的进给速度可以获得较好的表面质量,但加工效率较低。
在实际操作中,需要综合考虑进给速度和加工效率的平衡。
3.切削深度和切削宽度的选择:切削深度和切削宽度的选择需要考虑到刀具的切削能力和加工表面质量的要求。
在选择切削深度和切削宽度时,需要确保切削力在刀具的切削能力范围内,并满足加工表面质量的要求。
(二)参数的调整在确定了初步的切削参数之后,还需要进一步调整和优化。
加工中心铰刀铝件铰孔转速进给参数
加工中心铰刀铝件铰孔转速进给参数【加工中心铰刀铝件铰孔转速进给参数优化探讨】一、引言在加工中心车间,铰孔是一项常见但关键的加工工艺,尤其是对于铝件而言。
而如何设置铰刀的转速和进给参数,对于铰孔质量和效率有着至关重要的影响。
本文将从深度和广度两个方面,对加工中心铰刀铝件铰孔转速进给参数进行全面探讨,旨在帮助读者更全面、深入地了解这一主题。
二、深度探讨1. 加工中心铰刀铝件铰孔转速的影响铰孔转速的设置直接关系到铣削切削力和切屑情况,过低的转速可能导致进给率增大,刃口磨损,甚至出现卡刀现象;而过高的转速则可能引起刃口过热,影响铰削效果。
在实际加工中,需要根据铝合金的材质、孔径大小及铰刀的类型等多方面因素进行合理的转速选择。
2. 加工中心铰刀铝件铰孔进给参数的影响铰孔的进给参数直接关系到铰削的速度和表面质量,合理的进给参数可以保证加工效率和质量。
然而,不同铰孔直径、铰刀类型和切削深度下,进给率的选择也存在一定的复杂性和技巧性。
3. 如何优化铰刀铝件铰孔转速进给参数根据以上分析可知,优化铰刀铝件铰孔转速进给参数是一项复杂而又关键的工作。
在实际加工过程中,可以采用试验和经验相结合的方法,根据不同的工件和铰刀类型,逐步调整转速和进给参数,以达到最佳的加工效果。
三、广度探讨1. 切削液对铰刀铝件铰孔加工的影响切削液在铰削加工中发挥着冷却、润滑和清洁的作用,能够有效降低加工温度,减小刀具磨损,改善表面质量。
在选择切削液和设置切削液流量时,需要充分考虑工件材料和加工参数等因素。
2. 铝合金铰孔表面质量的评估与控制铰孔的表面质量不仅关系到工件的装配和使用性能,也直接影响到工件的外观和质感。
对于铝件的铰削加工,需要重视对铰孔表面质量的评估和控制,确保其达到设计要求。
3. 数控加工中心对铰孔加工的适用性与优势相比传统的手动铰孔加工,数控加工中心能够实现自动化、精密化的加工,提高生产效率和产品质量。
在铝件铰孔加工中,数控加工中心的应用具有显著的优势和潜力。
数控加工钛合金TC18的铣削参数优化研究
数控加工钛合金TC18的铣削参数优化研究在现代制造业中,钛合金由于其优异的性能,如高强度、高耐腐蚀性和良好的高温性能,被广泛应用于航空航天、医疗和汽车等领域。
其中,钛合金 TC18 是一种常见的钛合金材料。
然而,钛合金的加工难度较大,尤其是在数控铣削过程中,选择合适的铣削参数对于提高加工效率、保证加工质量至关重要。
钛合金 TC18 的材料特性给数控铣削带来了诸多挑战。
它的导热性差,导致在加工过程中热量容易积聚,从而加速刀具磨损。
其化学活性高,容易与刀具材料发生化学反应,进一步影响刀具寿命。
此外,钛合金的强度高,加工时切削力大,对机床和刀具的刚性要求较高。
铣削参数主要包括切削速度、进给速度、切削深度和切削宽度等。
这些参数的选择直接影响到加工效率、加工质量和刀具寿命。
切削速度过低会导致加工效率低下,过高则会使刀具迅速磨损。
进给速度过小会延长加工时间,过大则可能影响加工表面质量。
切削深度和切削宽度的选择需要综合考虑工件的形状、尺寸和机床的性能。
为了优化数控加工钛合金 TC18 的铣削参数,首先需要进行大量的实验研究。
实验设计是关键的一步,可以采用正交实验法、单因素实验法等。
正交实验法能够在较少的实验次数内获得较为全面的参数组合效果,单因素实验法则可以更深入地研究某个特定参数的影响规律。
在实验过程中,需要对加工后的工件进行详细的测量和分析。
测量的指标包括表面粗糙度、加工精度、残余应力等。
表面粗糙度是衡量加工表面质量的重要指标之一,通常使用粗糙度仪进行测量。
加工精度可以通过三坐标测量机等设备进行检测。
残余应力的测量则需要借助专门的应力测量仪器。
通过对实验数据的分析,可以建立铣削参数与加工质量、刀具寿命之间的数学模型。
常见的建模方法有回归分析、人工神经网络等。
回归分析能够建立较为简单直观的数学表达式,便于工程应用。
人工神经网络则具有更强的非线性拟合能力,但计算较为复杂。
在实际加工中,还需要考虑机床的性能和刀具的特点。
高速加工工艺
高速加工工艺高速加工是一种高效的切削方法,它以高切削速度进行小切削量加工,其金属去除率比普通数控加工要高,并且延长了刀具寿命、减少了非加工时间,它适应了现代生产快速反应的应用特点。
高速加工采用全新的加工工艺,在刀具、切削用量、走刀路径及程序编制等方面,都不同于传统的数控加工。
1.高速加工刀具选择高速加工对刀具材料要求更高。
在实际加工中一般按照下列原则选用合适的刀具材料:粗加工时优先考虑刀具材料的韧性;精加工时优先考虑刀具材料的硬度。
高速加工的刀具材料有立方氮化硼(CBN)、金刚石(PCD)、陶瓷等。
使用CBN刀具铣削端面时,其切削速度可高达5000m/min,主要用于灰口铸铁的切削加工。
聚晶金刚石刀具特别适用于切削含有SiO2的铝合金材料,目前,用聚晶金刚石刀具铣削铝合金端面时,5000m/min的切削速度已达到实用化水平。
此外,陶瓷刀具也适用于灰口铸铁的高速切削加工。
CBN和PCD刀具尽管具有很好的高速切削性能,但成本相对较高,釆用涂层技术的刀具价格低廉,又具有优异性能,可以有效降低加工成本,所以高速加工采用的立铣刀,大都釆用氮化铝钛(TiAlN)系的复合多层涂镀技术进行处理。
不同工件材料的高速加工需要选择与其匹配的刀具材料和加工方式,才能获得最佳的切削效果。
铝合金高速加工时,可以选用金刚石刀具。
如果刀具复杂,可采用整体超细晶粒硬质合金、粉末高速钢、高性能高速钢及其涂层刀具进行高速加工。
加工钢和铸铁及其合金时,采用Al2O3基陶瓷刀具较合适;立方氮化硼适于HRC45-65以上的高速硬切削;氮化硅基和立方氮化硼更适于铸铁及其合金的高速切削,但不宜于切削以铁素体为主的钢铁;WC基超细硬质合金及其TiCN、TiAlN、TiN涂层刀具和TiC/TiN基硬质合金刀具也可加工钢和铸铁。
加工钛合金时,一般可用WC基超细晶粒硬质合金和金刚石刀具。
2.高速加工切削用量选择高速加工的切削速度通常为常规切削速度的5~10倍左右。
硬质合金铣刀加工铝工艺参数表
硬质合金铣刀加工铝工艺参数表1. 引言硬质合金铣刀是一种常用于金属加工中的切削工具,其主要用途是在铣床上对工件进行铣削。
本文将详细介绍硬质合金铣刀加工铝的工艺参数表,包括切削速度、进给速度、切削深度等方面的内容。
2. 工艺参数表序号工艺参数参数说明1 切削速度表示每分钟切割的长度2 进给速度表示每分钟进给的长度3 切削深度表示每次切割时所去除的材料厚度4 刀具直径刀具直径对加工结果有重要影响5 冷却液用量冷却液可提高加工效率和延长刀具使用寿命6 切屑处理方式合理处理切屑可防止对机床和工件造成不利影响2.1 切削速度切削速度是指刀具在工件上切削时的线速度,通常用米/分钟表示。
对于硬质合金铣刀加工铝,适宜的切削速度范围为100-200米/分钟。
切削速度过低会导致铣削效率低下,而切削速度过高则容易导致刀具磨损加剧。
2.2 进给速度进给速度是指工件在切削过程中沿着铣床进给方向移动的速度,也用米/分钟表示。
对于硬质合金铣刀加工铝,适宜的进给速度范围为0.1-0.3毫米/齿。
进给速度过低会导致加工效率低下,而进给速度过高则容易造成表面粗糙度不理想。
2.3 切削深度切削深度是指每次切割时所去除的材料厚度。
对于硬质合金铣刀加工铝,适宜的切削深度范围为0.5-2毫米。
较小的切削深度有助于提高表面质量和延长工具寿命。
2.4 刀具直径刀具直径对加工结果有重要影响。
通常情况下,硬质合金铣刀的直径范围为2-25毫米。
较小的刀具直径适用于精细加工,而较大的刀具直径适用于快速去除材料。
2.5 冷却液用量冷却液可提高加工效率和延长刀具使用寿命。
对于硬质合金铣刀加工铝,适宜的冷却液用量为每分钟100-200毫升。
过少的冷却液会导致切削温度过高,从而影响加工质量和刀具寿命。
2.6 切屑处理方式合理处理切屑可防止对机床和工件造成不利影响。
常见的切屑处理方式包括使用冷却液进行冲洗和采取定期清理措施。
3. 总结本文介绍了硬质合金铣刀加工铝的工艺参数表,包括切削速度、进给速度、切削深度、刀具直径、冷却液用量和切屑处理方式等方面内容。