基于铣削均匀性的切削参数优化
数控机床铣削切削参数的优化与调整技巧
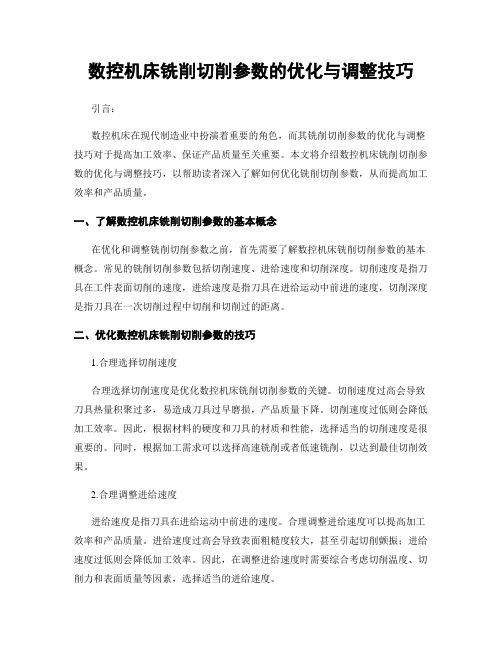
数控机床铣削切削参数的优化与调整技巧引言:数控机床在现代制造业中扮演着重要的角色,而其铣削切削参数的优化与调整技巧对于提高加工效率、保证产品质量至关重要。
本文将介绍数控机床铣削切削参数的优化与调整技巧,以帮助读者深入了解如何优化铣削切削参数,从而提高加工效率和产品质量。
一、了解数控机床铣削切削参数的基本概念在优化和调整铣削切削参数之前,首先需要了解数控机床铣削切削参数的基本概念。
常见的铣削切削参数包括切削速度、进给速度和切削深度。
切削速度是指刀具在工件表面切削的速度,进给速度是指刀具在进给运动中前进的速度,切削深度是指刀具在一次切削过程中切削和切削过的距离。
二、优化数控机床铣削切削参数的技巧1.合理选择切削速度合理选择切削速度是优化数控机床铣削切削参数的关键。
切削速度过高会导致刀具热量积聚过多,易造成刀具过早磨损,产品质量下降。
切削速度过低则会降低加工效率。
因此,根据材料的硬度和刀具的材质和性能,选择适当的切削速度是很重要的。
同时,根据加工需求可以选择高速铣削或者低速铣削,以达到最佳切削效果。
2.合理调整进给速度进给速度是指刀具在进给运动中前进的速度。
合理调整进给速度可以提高加工效率和产品质量。
进给速度过高会导致表面粗糙度较大,甚至引起切削颤振;进给速度过低则会降低加工效率。
因此,在调整进给速度时需要综合考虑切削温度、切削力和表面质量等因素,选择适当的进给速度。
3.合理确定切削深度切削深度是指刀具在一次切削过程中切削过的距离。
合理确定切削深度可以提高加工效率和产品质量。
切削深度过大会增加切削力和切削温度,降低切削稳定性,造成切削颤振,甚至导致刀具断裂;切削深度过小则会降低加工效率。
因此,在确定切削深度时需要综合考虑刀具性能、切削稳定性和加工需求等因素,选择合适的切削深度。
三、常见问题及解决方案1.切削温度过高切削温度过高会导致刀具早期磨损和产品质量下降。
解决方案包括选择适当的切削速度和进给速度,适当降低切削深度和刀具进给量,使用冷却液进行冷却等。
数控铣削加工参数在线优化技术

2.OMAT机床自适应系统
日益加剧的市场竞争要求急剧降低成本,这就要求生产者减少不必要的成本消耗,包括:加工时间、机床保养、维护成本、刀具费用和长交货周期的费用。自适应系统中采用的实时最优化技术在解决到的切削参数,对加工过程实现实时完全优化,使CNC机床发挥出最大潜力,刀具寿命达到最高。
(3)工件间材料不同和工件内材料硬度不均匀,产生硬点和软点。
(4)工件的形状、尺寸变化。
(5)加工中冷却效果不同产生表面硬度变化。
研究切削参数和加工刀具轨迹优化的目的就是使数控机床发挥出最优的加工效率,使产品具有最佳的加工品质。切削参数与刀具寿命、机床参数(主轴转速、功率、转矩)等因素有关。考虑到以上原因,为保证加工安全,程序员除了采取最保守的切削参数外别无选择,这就导致加工效率降低。相反,想要缩短加工时间,程序员不得不设定较大的加工参数,这样会导致对刀具工件和机床的破坏。无论数控程序多么优化,它们不能把加工中的动态变化考虑进去,远不能满足根据实际切削情况来实时调整切削参数的需要。
(3)优铣器的两种操作方法①预先设置方法(缺省方法)。当采用这种方法的时候,优铣器内部的专家系统使用用户输入的操作参数计算出每步走刀的最大负载容许值,并且通过对整个走刀过程连续地优化实际进给速率来达到这一负载。②训练方法这个方法包括“学习”和“再学习”两个阶段,以备特殊情况之用,包括夹具问题、特殊的刀具、应用旧刀具和在优铣器的材料库中不包含的特殊工件材料。
为了提高加工效率,编程者可以考虑到使铣四边时的刀轴切削载荷都保持一个较高的水平。如将铣短边的进给速度设为120mm/min,铣长边的进给速度设为160mm/min,这样可以缩短铣削时间。
简单的二维轮廓加工,为尽可能使材料等体积去除率保持在较好水平上,可以通过手工编写在不同线段的进给速度。然而,在较复杂的二维加工中,由编程者来考虑如何分配进给速度,其工作量是很大的,即使在NC程序中分别编辑不同的进给速度,实际刀轴切削载荷也会有较大波动。若要人工在三维零件的NC程序中为每个切削程序段分配不同的进给速度,将是一件很困难的事。
铣削加工工艺参数的优化
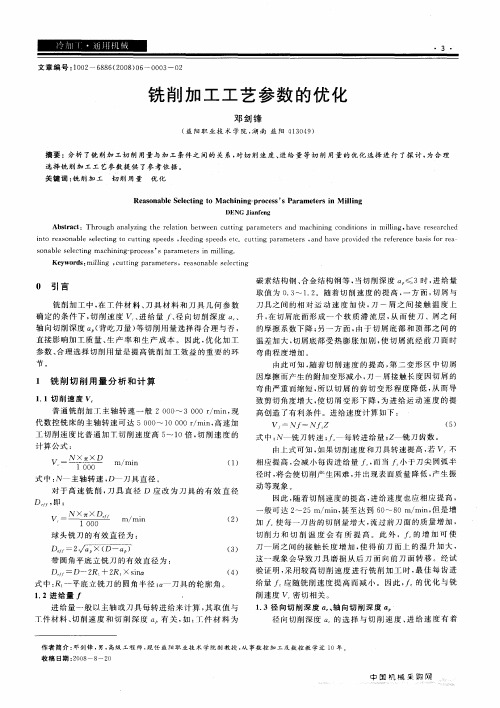
确 定 的条件 下 , 削速度 、 给量 厂、 向切 削 深度 “ 、 切 进 径 轴 向切 削深 度 a ( 吃刀 量) 背 等切 削用 量选择 得合 理 与否 , 直 接影 响加 工质 量 、 产 率 和 生 产成 本 。因此 , 化 加工 生 优
参 数 、 理 选 择 切 削 用 量 是 提 高 铣 削 加 工 效 益 的重 要 的 环主轴转 速 , D
刀具 直径 。
对 于高 速 铣 削 , 刀具 直径 D 应 改 为 刀 具 的有 效 直 径
因此 , 随着 切削速 度的提 高 , 进给速 度也 应相 应提 高 ,
一
般 可达 2 5m/ i , 至达 到 6 ~8 mi, 是增 ~2 r n 甚 a O 0m/ n 但 的增 加 可 使
V/ N_ NfZ 一 , 、 一 () 5
普通 铣 削加工 主轴 转 速 一 般 20 0 0 / n 现 0 ~30 0rmi,
代 数 控 铣 床 的 主 轴 转 速 可 达 50 0 1 0 / i , 速 加 0 00 0r r n 高 a 工 切 削 速 度 比普 通 加 T 切 削 速 度 高 5 1 ~ 0倍 , 削 速 度 的 切 计算公 式 :
・
3 ・
文 章 编 号 : 0 2 6 8 ( 0 8 0 —0 0 —0 10 — 8 6 2 0 ) 6 0 3 2
铣 削 加 工 工 艺 参数 的优 化
邓 剑 锋
( 阳职 业技 术 学 院 , 南 益 阳 4 3 4 ) 益 湖 1 0 9
摘 要 :分析 了铣 削加 工切 削 用量 与 加 工 条件 之 间 的 关 系, 切 削 速 度 、 给 量 等 切 削 用 量 的 优 化 选择 进 行 了探 讨 , 合 理 对 进 为
数控机床铣削切削参数的优化方法

数控机床铣削切削参数的优化方法数控机床是现代制造业中不可或缺的重要设备,而铣削是数控机床的一项常见加工工艺。
优化数控机床铣削切削参数,可以提高加工效率、降低生产成本,并且保证零件的质量。
本文将介绍数控机床铣削切削参数的优化方法。
首先,在选取数控机床铣削切削参数时,需要考虑工件材料的性质以及加工要求。
工件材料的硬度、韧性和切削性是影响切削参数选择的关键因素。
硬度高的材料需要选用较低的切削速度和切削深度,以减小切削力和切削温度,保证刀具寿命和工件表面质量。
韧性较高的材料则需要较大的切削速度和切削深度,以提高切削效率。
此外,加工要求也是选择切削参数的重要参考,比如加工精度要求高的零件需要选用较小的进给速度和进给量。
其次,合理选择刀具和切削液也是数控机床铣削切削参数优化的关键。
刀具的几何形状、材料和涂层会直接影响到切削力、表面粗糙度和加工效率。
在选择刀具时,应根据加工材料的不同选用合适的刀具材料和涂层,比如硬质合金刀具适用于铸铁和普通钢的铣削,而涂层刀具则适合高硬度材料的加工。
切削液的选择也十分重要,它可以降低切削温度、减小切削力、延长刀具寿命和提高表面质量。
常用的切削液有水溶性切削液和油基切削液,选择时需根据材料和加工要求综合考虑。
此外,切削力的控制也是数控机床铣削切削参数优化的重要环节。
切削力的大小直接关系到刀具的寿命和加工精度。
过大的切削力会导致刀具的磨损加剧,降低加工质量,甚至损坏刀具。
因此,在选取切削参数时,应尽量控制切削力的大小。
切削力与切削速度、进给速度和切削深度有关,一般来说,切削速度和进给速度越小,切削力也会相应减小。
同时,还可以采用刀具径向远离刀尖的切削方式,以减小切削力,提高切削稳定性。
此外,根据实际加工情况,需要通过试切试验来确定最佳的切削参数组合。
试切试验是通过不断调整切削速度、进给速度和切削深度,观察工件表面粗糙度、刀具磨损情况和加工前后尺寸误差的变化,从而找到最佳的切削参数组合。
数控机床切削参数的选择与优化
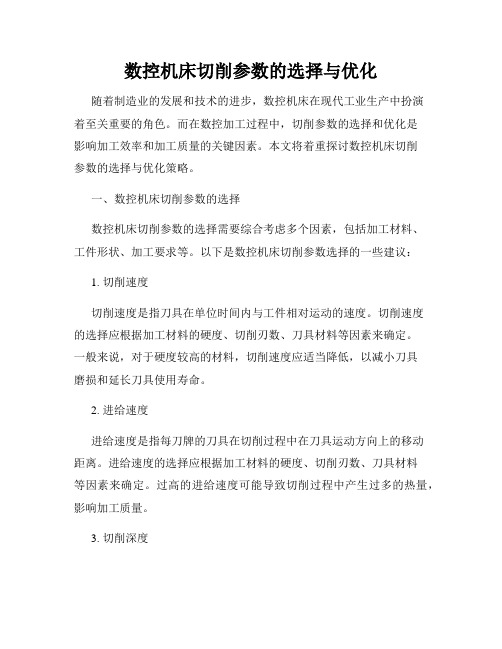
数控机床切削参数的选择与优化随着制造业的发展和技术的进步,数控机床在现代工业生产中扮演着至关重要的角色。
而在数控加工过程中,切削参数的选择和优化是影响加工效率和加工质量的关键因素。
本文将着重探讨数控机床切削参数的选择与优化策略。
一、数控机床切削参数的选择数控机床切削参数的选择需要综合考虑多个因素,包括加工材料、工件形状、加工要求等。
以下是数控机床切削参数选择的一些建议:1. 切削速度切削速度是指刀具在单位时间内与工件相对运动的速度。
切削速度的选择应根据加工材料的硬度、切削刃数、刀具材料等因素来确定。
一般来说,对于硬度较高的材料,切削速度应适当降低,以减小刀具磨损和延长刀具使用寿命。
2. 进给速度进给速度是指每刀牌的刀具在切削过程中在刀具运动方向上的移动距离。
进给速度的选择应根据加工材料的硬度、切削刃数、刀具材料等因素来确定。
过高的进给速度可能导致切削过程中产生过多的热量,影响加工质量。
3. 切削深度切削深度是指刀具在切削过程中与工件接触的最大深度。
切削深度的选择应考虑加工材料的硬度、切削刃数、刀具材料等因素。
较小的切削深度可以减小切削力和切削温度,提高加工精度。
4. 切削方式切削方式包括铣削、车削、钻削等。
选择合适的切削方式可以提高加工效率和加工质量。
对于不同形状的工件,应选择适合的切削方式,以确保切削过程的稳定和切削力的均匀分布。
二、数控机床切削参数的优化除了选择合适的切削参数外,优化切削参数也能提高加工效率和加工质量。
以下是一些常用的数控机床切削参数优化策略:1. 刀具润滑刀具润滑是切削过程中的重要环节,它能减小切削力和摩擦,并提高刀具的使用寿命。
选择合适的切削液类型和使用方法有助于减少切削过程中的热量积累和切削力的产生。
2. 切削力监测与控制通过切削力的监测和控制,可以实时了解加工过程中的切削负荷情况,从而优化切削参数的选择。
采用合适的传感器和控制系统,能够更好地预测和调节切削过程中的切削力,提高加工效率和加工质量。
基于铣削力与稳定性预测的铣削工艺参数优化
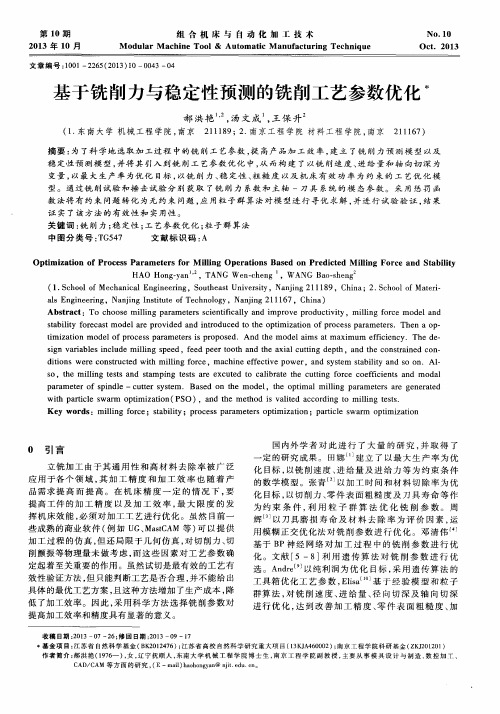
型 。 通 过 铣 削 试 验 和 捶 击 试 验 分 别 获 取 了 铣 削 力 系数 和 主 轴 一刀 具 系 统 的 模 态 参 数 。 采 用 惩 罚 函
数 法将有 约 束 问题 转 化 为无约 束 问题 , 应 用粒子 群 算法 对模 型进 行 寻优 求解 , 并进 行 试验 验 证 , 结 果
数控机床铣削切削参数的动态调整与最优化方法
数控机床铣削切削参数的动态调整与最优化方法摘要:数控机床在现代制造中起着重要的作用,而铣削是其常用的加工方式之一。
铣削切削参数对加工效果有重要影响,因此动态调整和最优化切削参数成为提高铣削加工效率和质量的关键。
本文将针对数控机床铣削切削参数的动态调整与最优化方法进行探讨,并提出一种可行的方案。
关键词:数控机床、铣削、切削参数、动态调整、最优化方法引言:数控机床的出现极大地提高了制造业的生产效率和加工质量。
在数控机床的加工过程中,铣削是一种经常使用的加工方式,因此铣削切削参数的调整和优化对于提高加工效率和质量至关重要。
本文将探讨数控机床铣削切削参数的动态调整与最优化方法,并提出一种可行的方案。
一、动态调整切削参数的必要性与挑战动态调整铣削切削参数对于实现高效率、高质量的加工具有重要意义。
传统的切削参数调整方法往往是经验性的,存在着固定的参数设置,难以针对不同的加工情况进行优化。
而现代制造中常遇到的零件形状复杂、加工精度要求高等问题使得切削参数的优化变得更为复杂。
因此,动态调整切削参数的方法迫在眉睫。
二、动态调整切削参数的方法(一)实时监测与反馈控制:通过现代传感器技术,实时监测铣削过程中的关键参数,如切削力、切削温度等。
根据监测到的参数,利用反馈控制方法实现切削参数的动态调整。
例如,当切削力过大时,可以自动降低进给速度来达到稳定切削的目的。
这种方法可以实现对切削参数的实时调整,提高加工质量和稳定性。
(二)数学模型的建立与仿真:通过对铣削过程进行数学建模,可以通过计算机仿真的方法探究不同切削参数对加工效果的影响。
通过对不同切削参数进行仿真分析,找出最佳参数组合,优化铣削加工过程中的产品质量和加工效率。
(三)人工智能算法的应用:近年来,人工智能算法在加工制造领域得到了广泛的应用。
利用人工智能算法,可以通过大量数据的学习和训练,快速找到最佳的切削参数组合。
例如,可以通过遗传算法、模糊逻辑控制等方法自动调整切削参数,在保证加工质量的前提下提高加工效率。
数控铣削参数的回归分析及优化处理
要求 Y 在一定范围 Y≤ Y≤ y 内取值 ,应该把变量 。 2
控制 在 什么范 围 内。
达到最小的值是最好的。 运 用数 学知 识 , 不在 此 推导 , 接应 用其 结果 直
事实上 , 回归方程( ) 用 1可知变量 取 %时对应
Y =口+6 0 o
6等 =
口 Y A 一
加 工 过 程 进 行 控 制 和预 测 。用 一元 线 性 回归 处理 的
实验数据 , 为生产提供参考经验公式 。
1 用 一 元线 性 回归和 正 交 多项 式 分 析各 参
数 之 间的联 系
11 回归 方 程 的求解 .
02 . 0 4 . 06 . . . 0 3 . 0 5 . 0 7 0 8 X
度 高等特点 , 对制 造业实现 自动化 、 集成化 、 智能化 即可 , 没有什么具体参数供参考 , 那么就研究跨度对 起着举足轻重的作用【 l 】 。随着制造业与数控技术结合 加 工表 面 品质 的影 响 ,这 里 主要 分 析 表 面粗 糙 度 与
一
的 日益紧密 , 机械制造设备 的数控化率 , 已成为衡量 跨度之间的线性 回归关系。 个 国家制 造 技术 水平 的重要 标 志 。 测得 实 验数 据 如 表 1 。 而在生产和科学研究 中, 常遇到不止一个变量 , 而这些变量之间又存在复杂 的对应关系 、甚至是相
处理( 为了方便表达 , 麓代替 ’ 用 ) 。 据最小二乘法 ,求 回归系数归结为解线性方程
组
( mm) di
(
(/ i ) ( m (/ i ) ( m r r ma ) r r ma )
lll 1b+1b=z fb+1 2 1 3 l l 2 3 0
基于VERICUT7_3的数控加工程序参数的优化
基于 VERICUT 7.3 的数控加工程序参数的优化宋 运 波 1 ,钟 海 雄 2(1.桂林电子科技大学职业技术学院,广西 北海 536000;2.南宁职业技术学院,广西 南宁 530008) 【摘 要】 通过实例分析基于 VERICUT 7.3 的数控铣削加工程序切削参数的优化设计全过程,取得了较好的优化效果,使该零件的加工工时比优化前节省了 40.88%,优化的切削参数让刀具使用更为合理,从而提高数控加工效率和产品质量,减轻一线员工的劳动强度,并能消除由于切削参数不当造成的零件过切超差。
【关键词】 VERICUT 7.3;铣削加工;切削参数;优化;加工效率【中图分类号】 TP391 【文献识别码】 A 【文章编号】2095-3518(2014)08-61-031 VERICUT 7.3 的程序优化模块对数控程序的优化 方法VERICUT 7.3 的程序优化模块对数控程序的优化方法有 三种:(1)体积去除率:每分进给被调整为以保持恒定体积去除 率,该方法主要用于粗加工,可以高效率地去除工件的余量,获 得较高的加工效率。
(2)削厚:每分进给被调整为以保持恒定最大削厚,该方法 主要用于余量较少且均匀的精加工,高速加工时可使刀具切削 稳定,能获得较高的表面面积去除率。
(3)体积去除率和削厚组合: 每分进给被调整以保持:①恒 定的体积去除率,①恒定的削厚,取其中一方计算生成的最低进 给速度,该方法适合于加工余量不大但不是很均匀的零件。
当 在余量不均匀的区域时按固定材料去除率优化,当在余量均匀 区域时按固定切屑厚度优化。
从以上三种优化方法得知,VERICUT 7.3 的优化模块是对 数控加工程序切削参数(主要是进给速度)的优化,从而达到优 化加工程序的目的。
图 1 工件与毛坯2 使用机床设备及刀具(1)数控机床:云南 CY 集团有限公司生产的 VMC8655L 立 式加工中心主轴电机功率 PE=7.5KW ,主轴转速 n=(50~8000) rpm ,进给速度 f=(0.254~6350)mm/min 。
数控机床铣削切削力的计算与优化
数控机床铣削切削力的计算与优化数控机床是现代制造业中的重要设备之一,其广泛应用于各个行业的零部件加工中。
在数控机床的运行过程中,切削过程是一个重要的环节,而切削力的计算与优化是提高加工效率和质量的关键。
本文将重点探讨数控机床铣削切削力的计算方法和优化措施。
首先,数控机床铣削切削力的计算是数控加工过程中的重要任务。
切削力的大小直接影响到机床的加工效率和切削工具的寿命。
在数控机床铣削中,切削力主要包括切向力和径向力两个方向的力。
切向力是沿着刀具切削方向的力,而径向力是与刀具旋转轴垂直的力。
为了准确计算数控机床铣削切削力,需要考虑多个因素,如工件材料的硬度、切削速度、刀具类型等。
其中,材料硬度是影响切削力最重要的因素之一。
通常情况下,硬度较大的材料在切削过程中需要更大的切削力。
此外,切削速度的大小也会对切削力产生影响。
一般来说,切削速度越大,切削力也会相应增加。
刀具的形状和材料也是影响切削力的因素,不同形状和材料的刀具在切削过程中对切削力的影响不同。
在数控机床铣削切削力的优化中,我们可以通过调整切削参数来降低切削力的大小,提高加工效率。
首先,可以通过减小切削深度和切削宽度来减少切削力的大小。
当切削深度和切削宽度较大时,切屑的形成和排出会增加切削力的大小。
因此,在实际加工中,可以根据工件的材料和形状合理设定切削深度和切削宽度,以达到最佳的加工效果。
其次,选择合适的切削工具也是优化切削力的重要手段之一。
不同类型的刀具对切削力的产生有不同的影响。
一般来说,刀具的刃数越多,切削力也会相应减小。
此外,刀具的材料也会影响切削力的大小。
选择高硬度的刀具材料可以降低切削力的大小,提高切削效率。
最后,数控机床铣削切削力的优化还可以通过提高机床的刚性和减小机床的振动来实现。
刚性越大,机床的抗变形能力越强,切削力产生的变形也会减小。
另外,减小机床的振动可以有效地降低切削力的大小,提高加工质量。
总之,数控机床铣削切削力的计算与优化是提高加工效率和质量的重要任务。
- 1、下载文档前请自行甄别文档内容的完整性,平台不提供额外的编辑、内容补充、找答案等附加服务。
- 2、"仅部分预览"的文档,不可在线预览部分如存在完整性等问题,可反馈申请退款(可完整预览的文档不适用该条件!)。
- 3、如文档侵犯您的权益,请联系客服反馈,我们会尽快为您处理(人工客服工作时间:9:00-18:30)。
3 Gradi ek Janez, Kalveram Martin, Weinert Klaus. Mechanistic identification of specific force coefficients for a general end mill. International Journal of M achine Tools & Manufacture, 2004 ( 44) : 401~ 414
关键词: 高速铣削, 铣削力, 铣削均匀性, 螺旋角
Optimization of Machining Parameters Based on Milling Uniformity
Pan Yongzhi Ai Xing Zhao Jun et al
Abstract: The engagement behavior between tool workpiece during chip formation in high speed milling process was ana lyzed. A milling uniformity model was presented by terms of axial depth of cut and radial depth of cut. Based on the milling uni formity model, the optimal model of machining parameters was built, where the constraint was the constant metal removal rate, and the optimized target was the milling uniformity coefficient. The milling uniformity and optimal model was validated by means of high speed milling experiments. For high speed milling of aeronautical aluminum alloy 7050- T7451, it is advantageous to improve milling uniformity and decrease cutting force by using bigger axial depth of cut and smaller radial depth of cut.
Q=
vapae 1000 D
( 6)
式中 v 是切削速度, 单位为 m/ min。由式( 6) 可
知, 选择不同的轴向切深组合可获得恒定的金属去
除率。以恒定金属去除率为优化条件、铣削均匀性
系数为优化目标, 建立切削参数的优化模型。假定 金属去除率 Q 、每 齿进给量 f z 和主轴 转速 n 为常 量, 式( 6) 简化为
* 国家自然科学基金资助项目( 项目编号: 50575126) 全国优秀博士学位论文作者专项资金( 项目编号: 200231)
收稿日期: 2007 年 7 月
2 铣削均匀性建模
2. 1 刀具 工件接触分析
铣削均匀性建模的基本思想是通过改善切屑形
成过程中刀具 工件的啮合程度, 来减小切削刃切
入/ 切出工件时的振动与冲击, 获得平稳的切削过
38
工 具技 术
基于铣削均匀性的切削参数优化*
潘永智 艾 兴 赵 军 宋清华
山东大学
摘 要: 分析了高速铣削加工切屑形成过程 中刀具 工件 的接触 行为, 提出 了考虑 轴向切削 深度和 径向切 削 深度的铣削均匀性模型。在此基础上, 以恒定的金属去除 率为约束条件、铣削均匀 性系数为优 化目标, 建立了切 削 参数的优化模型。通过对航空铝 合金进 行高 速铣削 试验, 验 证了铣 削均 匀性理 论及 优化 模型的 合理 性。结果 表 明, 对于航空铝合金的高速铣削加工, 采用大径向切深 小轴向切深有利于提高铣削均匀性, 减小切削力。
程。如图 1 所示, 在刀具 工件接触的不同时刻, 切
削刃与工件的接触线沿 A 向移动至不同位置, 铣削
力的分布也随之改变。在 BCD 区域内, 随着刀齿逐 渐切入, 切削面积逐渐增大, 切削力也随之增大。在
CDEF 区域内, 对于特定切削刃, 切削面积和切削力
保持恒定。在 EFG 区域内, 刀齿逐渐切出, 切削面 积逐渐变小, 切削力随之减小[ 6] 。切削力只作用在
( 2)
= arccos( 1- 2ae/ D)
( 3)
其中, CL 是刀具 工件接触表面进给方向上的
长度, 圆弧 BMC 在展开是刀具接触角, D 是刀具
直径, ae、ap 分别是轴向和径向切削深度。图 3a 和
2008 年第 42 卷 6
39
图 3b 中, 刀具 工件的接触面积相同, 而轴向和径 向切削深度的改变导致了同时参与切削的切削刃数 量和切削刃总长度均不相同。当轴向切深 ap > 轴 向齿距 P 时, 齿间角 p> 时, 接触面积内同时参 与切削的切削刃数量将大于 1, 有利于改善 铣削过 程的均匀性, 减小刀具切入 切出工件时的冲击作 用。
图 1 切屑形成过程
图 2 铣 削示意图
( a) 大径向切深, 小轴向切深
( b) 小径向切深, 大轴向切深 图 3 刀 具展开图
2. 2 铣削均匀性系数 考虑到轴向和径向切削深度对铣削过程均匀性 的影响, 可用 铣削均匀性系数 来衡量铣削过程中 刀具 工件接触面积内刀具与工件的啮合程度, 即
切屑形成过程中轴向和径向上同时参与切削的切削
如表 1 所示。
表 1 恒定金属去 除率铣削试验条件
工况
1 2 3 4 56 7 8
径向切深( a e/ mm) 1 1. 5 2 3 5 7. 5 10 15
轴向切深( ap/ mm) 15 10 7. 5 5 3 2 1. 5 1
金属去除率
( Q / cm3/ min)
72
图 4 显示了在恒定金属去除率 Q= 72cm3/ min 下不同齿数刀具的切削力和 铣削均匀性的 对比, 2 齿铣刀的切削力明显高于 3 齿铣刀, 而铣削均匀性 系数低于 3 齿铣刀。随着径向切深的增大, 2 齿铣 刀和 3 齿铣刀呈现出相似的变化趋势, 即切削力先
参考文献
1 Lazoglu Ismail. Sculpture surface machining: a generalized model of ball end milling force system. International Journal of Machine Tools & Manufacture, 2003( 43) : 453~ 462
刀具 工件接触面积内, 而接触面积的长度和宽度
分别由轴向和径向切削深度决定。高速铣削加工过
程中, 刀具的旋转速度远大于进给速度, 因此可假定
在某一进给位置, 刀具轴线固定不动, 刀具做旋转运 动[ 7] , 如图 2、3 所示。刀具 工件接触面积 S 可按
下式近似计算
S= CLa
( 1)
CL = D / 2
Q= Cap ae
( 7)
其中, C=
v 1000
D 是常数。轴向切削深度表示
为
ap = Q / Cae
( 8)
将式( 8) 代入式( 5) 中, 可得
=
2N+
QN tan C Dae
( 9)
对 a e 求导得到
=
N D
(
2
D ae( D -
ae)
Qtan
Ca
2 e
)
( 10)
令 = 0, 整理可得
40
工 具技 术
数单调性原理可知, 在区间 0 ae D 内有 且只有
一点 ae, 0 满足 f ( ae) = Байду номын сангаас, 即
=
a3e+
Aa e -
A D
=
0。
此时, = min。铣削均匀性系数 在 a e ae, 0时是
a e 的单调递减函数, 在 ae ae, 0时是 ae 的单调递增
函数。
4 结果与分析
刃数量。铣削均匀性系数可表示为
=
N 2
+
a pN Dc t an
( 5)
其中 是铣削均匀性系数, N 是切削刃数量,
是刀具螺旋角。式( 5) 由两项组成, 前者考虑了径向
切削深度的影响, 后者考虑了刀具螺旋角引起的轴 向切深方向上的切削滞后作用[ 7] 。
3 切削参数优化
高速铣削是典型的断续加工, 刀具切入 切出
( a)
( b) 图 4 恒定金属去除率 条件下径向切深与切削
合力及铣削均匀 性系数的关系
升后降, 铣削均匀性系数先降后升。当径向切削深 度 ae 为 2mm 和 3mm 时, 切削力和铣削均匀性系数 分别达到最大和最小值。由轴向和径向切深优化公 式( 11) , 当 ae, 0 = 2. 4mm 时, 铣 削均匀性 系数 =
高速铣削试验在五轴高速加工中心 DMU- 70V 上进行, 主轴转速为 16000rpm, 干切削, 工件材料是
7050- T 7451 航空铝合金。刀具采用超细晶粒硬质 合金整体立铣刀, 刀具直径为 20mm, 齿数为 3, 螺 旋角为 30 。采用 Kestler 测力仪测量不同条件下的 铣削力, 结果取三次测量的平均值。具体试验条件