钢中夹杂物控制原理

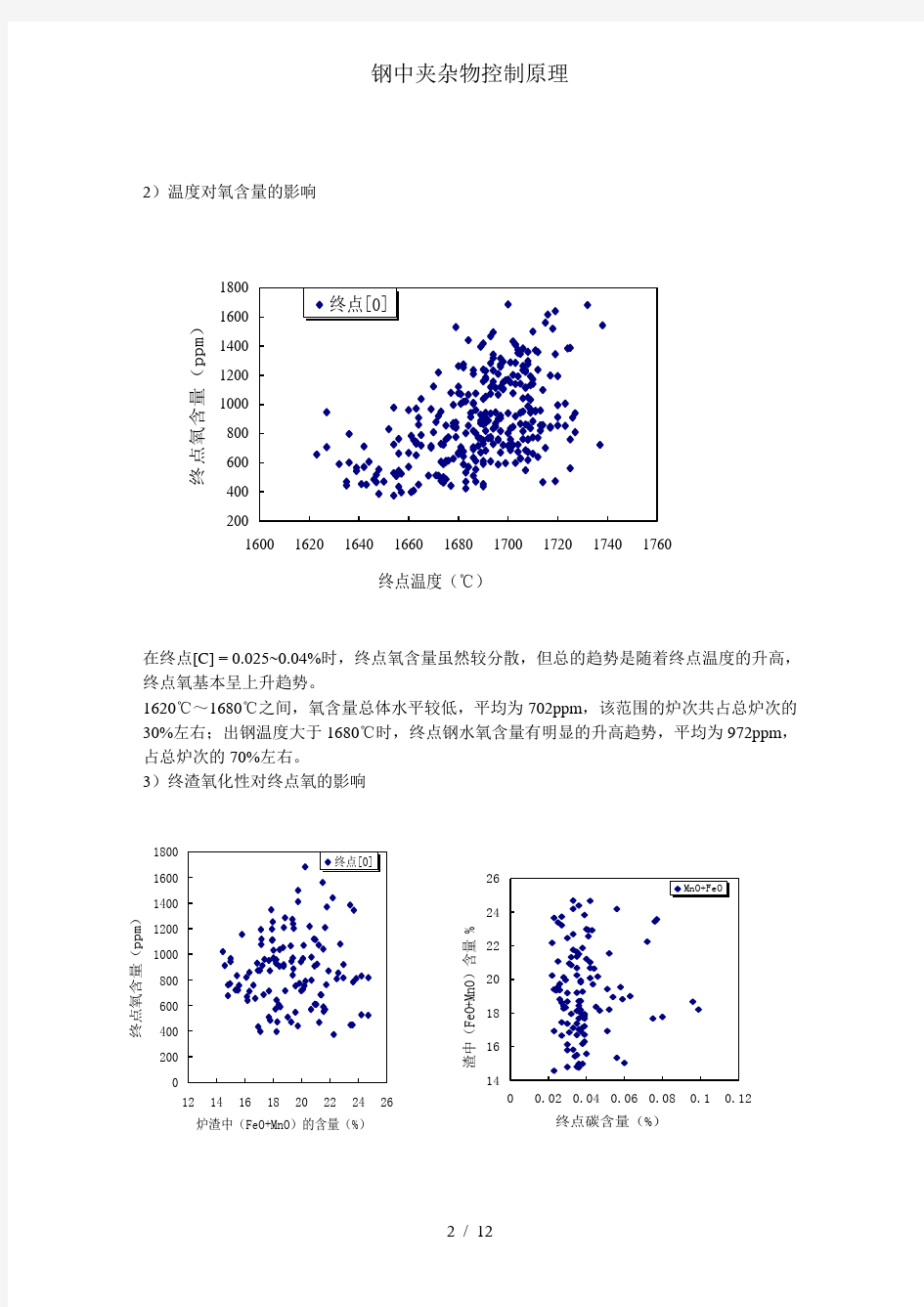
钢中夹杂物控制原理钢中氧的存在形式
T[O]=[O]溶+[O]夹
(1)转炉吹炼终点:
[O]夹=>0,T[O]→[O]溶=200~1000ppm
[O]溶决定于:
l 钢中[C],转炉吹炼终点钢中[C]及a[O] 关系如图l 渣中(FeO);
l 钢水温度。 1 顶底复吹转炉炉龄
C–Fe的选择性氧化平衡点
根据式[C] + [O] = {CO} (1) lg (Pco/ac* [%O])= 1149/T–2.002
以及反应[Fe] + [O] = (FeO)(2) lg aFeo/[%O] = 6317/T – 2.739
得到反应(FeO)+ [C] = [Fe] + {CO} (3) lg (Pco/ac* aFeo)= –5170/T+4.736 结论钢液中C-Fe的选择性氧化平衡点为[C]=0.035%,也就是说终点[C] < 0.035%时,钢水的过氧化比较严重。图1-1的统计数据也说明了这点。同时由式(1)可以求出此时熔池中的平衡氧含量为740ppm。
理论分析
1)终点[C]-[O]关系
1) 当终点[C]<0.04%时钢水的终点氧含量较高
2) 当终点[C]在0.02~0.04%范围时,有些炉次钢水氧波动在平衡曲线附近(区域Ⅰ)有些炉次钢水氧含量则远离平衡曲线(区域Ⅱ),说明在该区域钢水过氧化严重。
2)温度对氧含量的影响
在终点[C] = 0.025~0.04%时,终点氧含量虽然较分散,但总的趋势是随着终点温度的升高,
终点氧基本呈上升趋势。
1620℃~1680℃之间,氧含量总体水平较低,平均为702ppm ,该范围的炉次共占总炉次的
30%左右;出钢温度大于1680℃时,终点钢水氧含量有明显的升高趋势,平均为972ppm ,
占总炉次的70%左右。
3)终渣氧化性对终点氧的影响
200400
600800100012001400
1600
1800160016201640166016801700172017401760终点温度(℃)终点氧含量(p p m )
渣中(FeO+MnO)增加,终点[O]有增加趋势;
终点[C]<0.04%,渣中(FeO+MnO)增加且波动较大,说明此时吹氧脱碳是比较困难的,而铁则被大量氧化。
图1-3<2500炉终点C-O关系图1-4 2500~5000炉终点C-O关系
钢中夹杂物控制原理
(2)钢包脱氧合金化+精炼后:
[O]溶=>0 T[O]=[O]夹
Al-K钢:
[Al]S=0.02-0.05%,[O]溶=4-8ppm(图2)
如在连铸坯中测定T[O]=20ppm,说明除[O]溶外,氧化物夹杂[O]夹为12-18ppm,说明钢中很干净。
Si-K 钢:
用Si、Mn脱氧平衡[O]溶含量如图3。仅用Si、Mn脱氧钢中[O]溶为40~60ppm,在结晶器内凝固时铸坯易产生皮下气孔。
图2钢中[Al]S及[O]溶关系
y = 25.054x-0.9996
200
400
600
800
1000
1200
1400
1600
00.020.040.060.080.1
终点碳含量(%)
终
点
氧
含
量
(
p
p
m
)
终点[0]
乘幂 (平衡[O])
y = 25x-1
400
600
800
1000
1200
1400
1600
1800
0.020.030.040.05
转炉终点碳含量(%)
转
炉
终
点
氧
含
量
(p
p
m
)
终点[0]
乘幂 (平衡[O])
人们预测2000年后生产超洁净钢,钢中T[O]要达到5ppm 水平,
T[O]=[O]溶+[O]夹杂
解决途径:
生产“零夹杂物”钢:
[O]夹杂→0,即钢中夹杂物完全去除;
进一步降低[O]溶
对于Al-K 钢,炉外精炼改变Al-O 热力学平衡,Al2O3溶于渣中可使熔渣中Al2O3活度达到0.001,及[Al]S 相平衡的[O]溶<1ppm 。(效果有限)
对于Si-K 钢,炉外精炼控制炉渣组成,使SiO2溶于铝酸钙渣中,降低aSiO2,可使钢中[O]溶降到及Al-K 钢水平。(可行)
根据各类物的形态和分布,把中的夹杂物分为四个基本类型
A 类——硫化物类型
B 类——氧化铝类型
C 类——硅酸盐类型
D 类——球状氧化物类型
A 类夹杂物
属塑性夹杂物,经锻轧加工以后沿加工方向变形,成纺锤状。
随着夹杂物的化学成分的不同,通常在明视场下呈浅灰色、蓝灰色或亮黄色;在暗场下呈不透明或弱透明。
B 类夹杂物
脆且容易断裂,其在经轧制加工后沿加工方向排列成链状。
在明视场下多呈暗灰色,少数不常见的氧化物也呈亮灰色。在暗视场下多位不透明,少数呈透明的。
C 类夹杂物
有易变形和不易变形的两种。
图3 Deoxidation equilibria with Si/Mn for the deoxidation product saturated with Al 2O 3
易变形的硅酸盐夹杂及硫化物相似,沿加工方向延伸呈线段状,在明视场下呈暗灰色,在暗视场下透明。铁硅酸盐(2Fe?SiO2)、硅锰酸盐(2MnO?SiO2)、锰偏硅酸盐(MnO?SiO2)都属于易变形硅酸盐。
不易变形的硅酸盐夹杂物,以氧化物相似,沿加工方向呈颗粒状分布。铝硅酸盐(Al2O3?SiO2)、钙硅酸盐(CaO?SiO2)等属于不易变形硅酸盐。
D类夹杂物
为氧化物或硅酸盐,这种夹杂物精加工后是不变形的,仍以点球状存在。
B类夹杂物使钢材表面质量和性能恶化。
为了克服这一缺点,必须减少这类夹杂物的数量并且改变氧化物的性质,以降低甚至消除其危害。
由以上分析可知,要降低钢中T[O],就是要减少钢中夹杂物,降低[O]夹,降低[O]夹其方法是:
1)去除脱氧产物
它决定于:
夹杂物形成;
夹杂物传输到钢/渣界面;
渣相吸附夹杂物。
方法:控制脱氧产物+炉外精炼+搅拌
→T[O]=20~40ppm
就脱氧而言,分三种情况:
硅镇静钢(用硅+锰脱氧)
硅-铝镇静钢(Si+Mn+少量Al脱氧)
铝镇静钢(用过剩Al脱氧[Al]s>0.01%)
a)用Si+Mn脱氧
如图4所示:
形成的脱氧产物有:
纯SiO2(固体);
MnO·SiO2(液体);
MnO·FeO(固溶体)。图4 FeO-MnO-SiO2三元相图
硅镇静钢
用Si+Mn脱氧,形成的脱氧产物一般有纯SiO2(固体),MnO?SiO2(液体),MnO?FeO (固溶体)。
Mn/Si低时形成SiO2夹杂会导致水口堵塞;Mn/Si高时生成典型的液态MnO?SiO2,夹杂物容易上浮。因此因调整钢成分,保持Mn/Si>2.5。
但及Mn、Si平衡的[O]溶较高,当钢水浇入结晶器时会产生皮下针孔,同时MnO ?SiO2会污染钢水。
为此在LF精炼采用白渣操作+Ar搅拌,钢渣精炼扩散脱氧即能把钢水中[O]溶降到<20ppm的最佳范围,也能有效脱硫,降到0.01%以下。
2)用Si+Mn+Al脱氧
用Si+Mn+少量Al脱氧可防止Si+Mn脱氧中极易产生的皮下针孔,其可能的脱氧产物有蔷薇辉石(2MnO?2Al2O3?5SiO2),锰铝榴石(3MnO?Al2O3?3SiO2)和纯Al2O3(Al2O3>25%)。
其中锰铝榴石区域夹杂物熔点低,球形易上浮;可塑性及变形性好且不堵水口;脱氧良好不生成气孔。
夹杂物中Al2O3含量控制
当其中Al2O3超过25%时,Al2O3将析出;若Al2O3含量低于10%,SiO2将析出,两者均为不变形相。
为了控制Al2O3含量以形成20%的Al2O3锰铝榴石夹杂物,必须及渣系中的Al2O3联系起来,通过调整渣的组成防止渣中Al2O3过高导致锰铝榴石中Al2O3析出来平衡钢水中的夹杂物成分。
最有效的方法是采用Ca(CaO粉剂)及钙硅石处理,不仅可以控制夹杂物中Al2O3含量而且可将锰铝榴石夹杂转变为热轧时可变形的非晶体假硅石灰。
在钢中Si=0.2%,Mn=0.4%,温度为1550℃条件下,要把夹杂物成分控制在相图中的阴影区,则必须钢中[Al]S<=0.006%(图6),若钢中[Al]s≤0.006%,则钢中[O]<20ppm,生成锰铝榴石而无Al2O3析出,钢水可浇性好,不堵水口,铸坯又不产生皮下气孔。
图5 MnO-SiO2- Al2O3相图图6 钢中〔Al〕及〔O〕关系
※
3)用过剩铝脱氧
对于低碳细晶粒钢,要求钢中酸溶铝不低于0.01%;
对于低碳铝镇静钢,为改善薄板深冲性能,要求钢中酸溶铝为0.02~0.05%;
为此要求用过剩铝脱氧,其脱氧产物全部为Al2O3
Al2O3熔点高(2050℃),钢水中呈固态;可浇性差,堵水口;Al2O3可塑性差,不变形,影响钢材性能。
为此采用钙处理来改变Al2O3形态
图4 纯铁脱氧期间形成的枝晶状和点簇状Al2O3夹杂(左图)和珊瑚状Al2O3夹杂(右图)
图5 低碳钢Al脱氧期间的点簇状Al2O3
图6 低碳铝镇静钢脱氧过程中形成的Al2O3夹杂(左:花盘型Al2O3;右:小多面体颗粒的聚集)
点簇状氧化铝夹杂来自脱氧或二次氧化,如图5所示,为铝脱氧钢中的典型存在形式。
由于具有较高的界面能,氧化铝夹杂容易通过碰撞、聚集形成三维点簇状。点簇状夹杂内每个单体直径约为1~5微米。
在及其他颗粒碰撞、分离或聚集之前,这些单体可能是花盘型或多面体型夹杂物,如图6所示。
簇状Al2O3夹杂物的形貌块状Al2O3夹杂物的形貌
钙处理(喂Si-Ca线或Ca线,改变Al2O3形态);
[Al]s较低,钙处理生成低熔点2CaO·Al2O3·SiO2(图7);
[Al]s较高,钙处理保持合适Ca/Al比,最好能形成12CaO·7 Al2O3(图8和9)。
对于Al-K钢,钙处理后:
解决了可浇性,不堵水口;
夹杂物易上浮去除。
改变夹杂物形态,改善钢性能
就夹杂物传输到钢/渣界面而言,它决定于:
夹杂物尺寸:
夹杂物的形核,长大速率。形核约15nm,在炼钢条件下很快长大到1~5μm;
液体流动,搅拌,夹杂物碰撞、聚合,尺寸5~200μm;
夹杂物性质:液态或固态;
夹杂物上浮:静止溶池还是搅拌溶池。
共焦扫描激光显微镜观察到的钢水表面Al2O3夹杂物形成点簇状的过程
夹杂物聚集
借助于表面张力,固态夹杂物的聚集能够出现在任何界面上,包括在耐火材料表面上和气泡表面上。
Al2O3及钢水的接触角较大(134~146°),促使这类夹杂物为减少及钢液的接触而自发的粘附在耐火材料上。
1530°C的高温可以使得Al2O3出现烧结相。较大的接触角和较大的夹杂物尺寸有利于夹杂物聚集(图18)。
由于碰撞及集聚,随着时间和温度的增加,夹杂物趋向长大。
就渣相吸附夹杂而言
●钢/渣界面能:
●夹杂物溶于渣相。
液体夹杂完全溶解于渣相,而固体夹杂在渣中是有限溶解,决定于渣成分、温度和渣量。
2)防止浇注过程钢水再污染,它决定于:
●钢水二次氧化;
●钢水及环境(渣、包衬、水口)相互作用;
●渣相乳化(紊流、涡流);
●非稳定态浇注。
连铸坯中夹杂物来源
1)内生夹杂物:主要是脱氧产物,其特点是:
●[O]溶↑,脱氧产物增加;
●夹杂物尺寸细小<20μm;
●在钢包精炼搅拌,大部分85%夹杂物上浮;
●一般来说,对产品质量不构成大的危害;
●钢成分和温度变化时有新的夹杂物沉淀(<5μm)。
在连铸坯中常见的内生夹杂(endogenesis-inclusions):
铝镇静钢(Al-K): Al2O3
硅镇静钢(Si-K):硅酸锰(MnO·SiO2)或MnO·SiO2·Al2O3
钙处理Al-K钢:铝酸钙
钛处理Al-K钢: Al2O3,TiO2,TiN
镁处理Al-K钢:铝酸镁
所有钢: MnS(凝固时形成,以氧化物夹杂形核)
钢水冷却和凝固过程中产生的沉淀析出夹杂物
在冷却期间,液态钢水中溶解氧、氮、硫的浓度变大,同时这些元素的溶解度减小。这样造成氧化铝、硅、氮化铝和硫化物的沉淀析出。
凝固过程中硫化物在枝晶间析出,亦经常以钢水中已存在的氧化物为核心析出。这类夹杂物通常较小(<10μm)。
图19连铸过程中氧化物夹杂的来源
(2)外来夹杂:钢水及环境(空气、包衬、炉渣、水口等)二次氧化产物
在产品机械加工时,钢中的这类夹杂物可产生噪音,在机加工表面形成凹坑和划痕,容易引起断裂,以及造成工具磨损。钢中外来夹杂物的含量可通过大样电解的方法测定。其特点是:
1)夹杂物粒径大>50μm,甚至几百μm;
来自耐火材料侵蚀的夹杂物通常比卷渣造成的夹杂物要大
2)复合成分及多相结构
由于钢水和渣中的SiO2, FeO, and MnO以及炉衬耐火材料之间的多元反应造成夹杂物成分复杂,产生的Al2O3可以覆在这些夹杂物表面;
由于外来夹杂尺寸较大,它们在运动时,容易吸收捕获脱氧产物如Al2O3夹杂(图10右及图11右);
外来夹杂作为异相形核核心,在钢水中运动的新夹杂物以此核心沉淀析出(图11左);
渣或者二次氧化产物及炉衬耐火材料或其脱落物之间的反应;
3)形状不规则
但卷渣或者脱氧产物氧化硅类夹杂物为球形。球形外来夹杂物通常尺寸较大(>50μm)并且大多数为多相,但球形脱氧产物夹杂通常较小并且单相.
4)相比小夹杂物而言数量较少
偶然性分布
及小夹杂物均匀弥散分布不同,外来夹杂物在钢中零星分布。
由于此类夹杂通常是在浇铸和凝固时被捕捉,因此具有偶然性,呈零星分布状态。
另一方面,由于此类夹杂容易上浮去除,所以它们只集中在凝固速度最快的区域或
者在某些方面上浮受阻的区域。因此,此类夹杂经常出现在表层附近。
6) 对产品性能危害最大。
生产洁净钢,就是要减少钢中夹杂物,尤其是减少大颗粒夹杂而奋斗
不论这些夹杂物的来源如何,问题在于这么大尺寸的夹杂物为何没有迅速上浮而得到去除。原因可能是:
在浇铸之前,在冶炼、运输或钢包、中间包等其他冶金容器的侵蚀过程中该类夹杂物形成较晚造成上浮时间不足;
缺乏足够的过热度;
在凝固过程中由于流场流动影响造成结晶器保护渣卷入,或者已上浮的夹杂物在未完全进入渣中之前被重新卷入。
(3)二次氧化产生的夹杂物
钢中发现的二次氧化产生的大型夹杂物最常见的形式点簇状Al2O3、球状MnOFeO、MnOSiO2。空气作为二次氧化的共同来源,以下列方式进入钢液:
-由于在钢水注入处强烈的湍流造成中间包钢水表面吸入空气,流动的钢液表面形成的氧化薄膜重新卷入钢液后形成很薄的氧化物颗粒带;
-钢水从钢包进入中间包以及从中间包进入结晶器的水口连接处吸入空气;
-在浇铸过程中,钢包、中间包和结晶器钢水表面的空气渗透。
在这类二次氧化过程中,脱氧元素如Al、Ca和Si等优先氧化,氧化产物发展成为非金属夹杂物,通常比脱氧夹杂物大一到二个数量级。
防止此类二次氧化的方法是在浇铸过程中防止钢液暴露于空气中:
1)在钢包长水口和中间包浸入式水口连接处采用钢环或透气砖环吹入惰性气体形成气幕保护;
2)浇铸前在中间包内充入保护气体以及浇铸过程中中间包钢液表面采用气体保护;
3)控制钢包内的气体吹入避免形成气眼。
二次氧化产物另一来源是渣中以及包衬耐火材料中的SiO2,、FeO 和MnO。通过此类二次氧化产物形成的机理,靠近渣或包衬界面时钢水中的夹杂物通过反应
SiO2/FeO/MnO+[Al][Si]/[Fe]/[Mn]+Al2O3
而长大,由此生成的氧化铝夹杂尺寸较大且含有各种成分。这种现象以下列方式进一步影响外来夹杂物的形成:
-上述反应能够侵蚀包衬耐火材料表面并可使其表面凹凸不平,从而改变包衬壁附近的钢水流场,并且引起包衬的破损加速;
-包衬破损产生的大型外来夹杂物以及卷入的渣可以捕捉小夹杂物如脱氧产物,也可以作为异相形核核心产生新的析出物,这就使得外来夹杂物的成分变得比较复杂。
为防止来自渣和包衬耐火材料的二次氧化,使这些材料保持较低的FeO、MnO和SiO2含量非常重要。文献表明较低自由SiO2含量的高铝质或氧化锆质砖具有更好的适用性
(4)卷渣造成的外来夹杂物
任何冶炼上或钢水传递上的操作,尤其是在钢水从一种容器到另一种容器时,会引起渣钢间的剧烈混合,造成渣颗粒悬浮在钢液中。特点:
卷渣形成的夹杂物尺寸在10~300μm之间,
含有大量的CaO和MgO成分,
在钢水温度下通常为液态,因此在外形上为球形(图12)。
使用H型中间包并且通过两个钢包注入可以在换钢包期间减少卷渣夹杂物。
钢中夹杂物控制原理修订稿
钢中夹杂物控制原理 WEIHUA system office room 【WEIHUA 16H-WEIHUA WEIHUA8Q8-
钢中夹杂物控制原理钢中氧的存在形式 T[O]=[O]溶+[O]夹 (1)转炉吹炼终点: [O]夹=>0,T[O]→[O]溶=200~1000ppm [O]溶决定于: l 钢中[C],转炉吹炼终点钢中[C]与a[O] 关系如图 l 渣中(FeO); l 钢水温度。 1 顶底复吹转炉炉龄 C–Fe的选择性氧化平衡点 根据式 [C] + [O] = {CO} (1) lg (Pco/ac* [%O])= 1149/T–2.002 以及反应 [Fe] + [O] = (FeO) (2) lg aFeo/[%O] = 6317/T – 2.739 得到反应(FeO)+ [C] = [Fe] + {CO} (3) lg (Pco/ac* aFeo)= –5170/T+4.736 结论钢液中C-Fe的选择性氧化平衡点为[C]=0.035%,也就是说终点[C] < 0.035%时,钢水的过氧化比较严重。图1-1的统计数据也说明了这点。同时由式(1)可以求出此时熔池中的平衡氧含量为740ppm。 理论分析
1)终点 时钢水的 当终点[C]在0.02~0.04Ⅰ)有些 2)温度对氧含量的影响 200400 600800100012001400 16001800160016201640166016801700172017401760 终点温度(℃)终点氧含量(p p m )
在终点[C] = 0.025~0.04%时,终点氧含量虽然较分散,但总的趋势是随着终点温度的升高,终点氧基本呈上升趋势。 渣中(FeO+MnO )增加,终点[O]有增加趋势;
钢中夹杂物的类型及控制技术发展
钢中夹杂物的类型及控制技术发展 XX (河北联合大学冶金与能源学院,唐山,063009) 摘要:综合论述了钢中非金属夹杂物的按化学成分、形态、粒度、来源的分类以及控制夹杂物含量时所采用的气体搅拌-钢包吹氩、中间包气幕挡墙、电磁净化-钢包电磁搅拌、中间包离心分离和结晶器电磁制动、过滤器技术、超声处理技术和渣洗技术,并针对钢中夹杂物的控制技术的优、缺点进行了简要的归纳。随着氧化物冶金工艺纯净钢产品的开发,夹杂物去除技术的不断进步,非金属夹杂物的控制技术仍面临着新任务。 关键词:非金属夹杂物;夹杂物类型;控制技术 Types and Progress on Technique for Removel of inclusions in steel XX (College of Metallurgy and Energy Hebei United University, Tangshan 063009) Abstract:The behavior of inclusions in molten steel includes physical processes such as nucleation, growth, polymerization and transmission. The removal of inclusions can be seen as the result of transmission, which involves inclusion growth, floating and separating. The key progress on technique for removal of inclusions in steel is gas stirring-ladle argon blowing, gas shielding weir and dam in tundish, electromagnetic cleaning-ladle electromagnetic stirring, tundish centrifugal separating and mold electromagnetic braking, slag washing, ultrasonic technique ,and filter technique. Key words:non-metallic inclusions Typesof inclusions, Technique for Removel of inclusions 1引言 钢中非金属夹杂物是指钢中不具有金属性质的氧化物、硫化物、硅酸盐或氮化物。它们是钢在冶炼过程中加入脱氧剂而形成的氧化物、硅酸盐和钢在凝固过程中由于某些元素溶解度下降而形成的硫化
钢中的非金属夹杂物分类方法如何
钢中的非金属夹杂物分类方法如何?来源何处 2009-05-21 11:17 评论(0)浏览(289)一)分类方法很多,但常见的有以下四种: 1.按来源分类,可分为两类: (1)内在的:包括在冶炼过程中所形成的化合物、脱氧时产生的脱氧产物、或在钢水凝固过程产生的化合物,当这些化合物来不及从钢水中彻底排出,而残存在钢中者,叫做内在的非金属夹杂物。 (2)外来的:包括从炉衬或包衬、或从汤道砖、中包绝热板、保护渣迸人钢水中的夹杂物(有人还将钢水二次氧化生成的夹杂物包括在内)。 一般说来外来夹杂物颗粒较人,在钢中比较集中,而内在夹杂物则一与此相反。 2.按化学成分分类,一般分三类。 (1)氧化物:如FeO, Si02 , Al2O3等,有时它们各自独立存在,有时形成尖晶石(如MnO.Al203)或固溶体 (如FeO 和MnO)。 (2)硫化物:如FeS、MnS及(Fe. Mn) S的固溶体。当加Al过多时可能以A12S3出现。 (3)氮化物:如TiN, ZrN 等 3.按夹杂物的变形性能分类,当钢进行热加工时,例如:轧制时,夹杂物此时是否也变形,它对钢的性能有明显的影响。为此,把夹杂物分为三类:(1)脆性:这类夹杂物完全没有塑性,在热加工时,尺寸和形状都没有变化,属于这一类的主要是A1203、Cr203等,‘它们属于高熔点
的夹杂物。 (2)塑性:钢在加工变形时,夹杂物也能随之变形,形成条状,属于这类的有硫化物以及含 SiO240--60%的铁、锰硅酸盐。 (3)球状(或点状)不变形:属于这类的有Si02 及SiO2 >70%的硅酸盐。 4.按尺寸大小分类,可分三类:(1)大型:尺寸> 100微米。 (2)中型:也叫显微型,尺寸1-100微米。(3)小型:也叫超显微型,尺寸<100微米。 (二)钢中非金属夹杂物主要来源于: 1.钢中杂质氧化的产物、脱氧产物和钢在浇注与凝固过程中的反应产物、因溶解度下降的析出物; 2.原材料带人的杂质; 3.混人的炉渣或炉衬与浇注设备的耐火材料等。 来源:中国钢铁新闻网
钢中夹杂物得去除与控制
钢中夹杂物去除与控制 刘金刚 刘浏 (钢铁研究总院冶金工艺研究所,北京100081) 摘要:通过对钢包—中间包—结晶器中不同环节中的去除夹杂物的不同手段进行综合分析,得到各环节中间包均应保护浇注和防止卷渣卷气,中间包应具有合理的结构(上下挡墙、湍流抑制器、旋涡抑制器)以得到合理的流场;利用钢包注流的剪切破碎作用在中间包中生成的小气泡、中间包气幕挡墙和电磁搅拌离心流动可以有效去除钢水中夹杂物;电磁制动技术日趋成熟但其能耗较大,因此可以发展低能耗的中间包真空浇注对结晶器液面波动进行抑制。电磁搅拌和电磁连铸有利于改善铸坯的内部质量和防止振痕的产生。 关键词:中间包夹杂物去除控制 Inclusions Removal and Control in the Steel Melt Liu Jingang Liu Liu (CISRI, Beijing 100081) Abstract: Through synthetic analysis of various methods to remove inclusions during ladle-tundish-mold processes, it was found that using protective casting, avoiding gas and slag wrapping are important measures for clean steel production. The structure of the tundish should be reasonable, (dam, weir; turbulence inhibitor; vertex inhibitor) in order to get a preferred flow pattern. It could also utilize the shear flow from ladle to tundish to form small gas bubbles, utilize gas bubble curtain and electromagnetic stirring caused centrifugal flow to remove inclusions from steel melt. Electromagnetic braking technology is gradually raped but it was very energy consumed, thus it could develop low energy consumption vacuum tundish casting technology to control the fluctuation of melt surface in mold. Electromagnetic stirring is good for improving inner quality of slab and preventing the oscillation marks formation. Keywords: tundish, inclusion, remove, control 二○○三年我国钢产量已达到2.7亿吨,但由于质量问题一些高品质钢材仍需进口,这已经成为我国钢铁工业发展的障碍,影响我国钢铁产品走向世界。钢质量问题也已经成为我国由钢铁大国转变为钢铁强国的限制性环节,因此提高钢质量以增强国内钢铁企业的竞争力十分重要。提高钢质量重点是提高钢的洁净度、对钢中夹杂物进行严格控制。 1钢水脱氧与保护浇注 钢中夹杂物可分为内生和外来夹杂物,内生夹杂物主要是脱氧和合金化元素与溶解在钢液中的氧以及硫、氮的反应产物所形成的夹杂物。外来夹杂物是钢液与空气、耐火材料、炉渣及保护渣相互作用的产物以及机械卷入钢中的各种氧化物[1]。因此提高钢质量必须通过控制内生夹杂物和减小外来夹杂物两个方面进行控制。
夹杂物分类,来源和降低钢中夹杂物含量的技术措施
夹杂物分类、来源和降低钢中夹杂物含量的技术措施 冶093 孙苏皖099014200 摘要:非金属夹杂物降低了钢的塑性、韧性和疲劳寿命,使钢的冷热加工性能乃至某些物理性能变坏,对钢的强度、延伸性、韧性、切削性、抗腐蚀性能、表面光洁度、焊接性能等各方面的性能有着直接的影响。夹杂物对钢的性能影响的具体程度决定于一系列因素,比如夹杂物的数量、颗粒大小、形态及分布等。 关键词:挡渣出钢;中间包污染;二次氧化;结晶器液面波动 一.钢中夹杂物的分类 分类方法很多,但常见的有以下四种: 1.按来源分类,可分为两类: (1)外来夹杂物:耐火材料、熔渣或两者的反应产物混入钢中并残留在钢中的颗 粒夹杂称为外来夹杂。包括从炉衬或包衬、或从汤道砖、中包绝热板、保护渣进入钢水中的夹杂物(有人还将钢水二次氧化生成的夹杂物包括在内)。这类夹杂颗粒较大,易于上浮,但在钢中,它们的出现带着偶然性且不规则。 (2)内生夹杂物:在冶炼、浇注和凝固过程中,钢液、固体钢内进行着各种化学 反应,对于在冶炼过程中所形成的化合物、脱氧时产生的脱氧产物、或在钢水凝固过程产生的化合物,当这些化合物来不及从钢水中彻底排出而残存在钢中者,叫做内在的非金属夹杂物。 内生夹杂物形成的时间可分为四个阶段: ①一次夹杂(原生夹杂):钢液脱氧反应时生成的脱氧产物;
②二次夹杂:在出钢和浇注过程中温度下降平衡移动时生成的夹杂物; ③三次夹杂(再生夹杂):凝固过程中生成的夹杂; ④四次夹杂:固态相变时因溶解度变化生成的夹杂。 一般说来外来夹杂物颗粒较大,在钢中比较集中,而内生夹杂物则与此相反。从组成来看,内生夹杂物可以是简单组成,也可以是复杂组成;可以是单相的,也可以是多相的。在铸坯凝固以及随后的冷却过程中,夹杂物不仅与钢基体保持平衡,而且夹杂物本身也不断发生改变,例如析出新的化合物以趋于稳定状态。在轧制或热处理时,每次加热都为夹杂物和钢基体之间趋向平衡提供了条件,在室温下所观察到的夹杂物,实际上是经过了一系列复杂变化的结果。 2.按化学成分分类,一般分三类。 (1)氧化物:如FeO, Si02 , Al2O3等,有时它们各自独立存在,有时形成尖晶 石(如MnO.Al203)或固溶体 (如FeO 和MnO)。 (2)硫化物:如FeS、MnS及(Fe. Mn) S的固溶体。当加Al过多时可能以A12S3 的形态出现。 (3)氮化物:如TiN, ZrN 等 3.按夹杂物的变形性能分类 当钢进行热加工时,例如:轧制时,夹杂物此时是否也变形,它对钢的性能有明显的影响。为此,把夹杂物分为三类: (1)脆性:这类夹杂物完全没有塑性,在热加工时,尺寸和形状都没有变化,属于这一类的主要是A1203、Cr203等,它们属于高熔点的夹杂物。 (2)塑性:钢在加工变形时,夹杂物也能随之变形,形成条状,属于这类的有硫 化物以及含SiO240--60%的铁、锰硅酸盐。 (3)球状(或点状)不变形:属于这类的有Si02 及SiO2 >70%的硅酸盐。4.按尺寸大小分类,可分三类:
铸钢铸锭中产生夹杂物的原因
炼钢、铸锭过程中产生非金属夹杂物的原因 摘要:论述钢中非金属夹杂物对钢锭质圣的影响,分析了非金属夹杂物在冶炼和铸锭过程中产生的原因,提出了控制夹杂物产生的几点行之有效的措施。 关键词:非金属夹杂物冶炼浇注电弧炉精炼炉质控制2010-02-02 08:34 非金属夹杂物,一般是指钢锭在冶炼和浇注过程中产生或混人的非金属相,都是一些金属元素(Fe、Mn、Al等)及51与非金属元素(0、S、N、P、C等)结合而生成的氧化物和硫化物(如Feo、Si02、Mno、A12O3、MnS、MnC)等。非金属夹杂物按来源分为内生夹杂物和外来夹杂物。内生夹杂物是钢内部发生的反应产物或者因为温度降低而形成夹杂析出。外来夹杂物是由炉料带人,耐火材料及炉渣混人的颗粒。内生夹杂物可以以外来夹杂物为核心聚集到后者的颗粒上。外来夹杂物也可能与钢液反应被还原。钢中如果有非金属夹杂物的存在,即使在钢中含量极少(通常是小于万分之一)也会给钢的质量带来极为有害的影响。从2002年1~7月份重点产品的投料统计情况看,锻钢支承辊共生产68支,经探伤发现其中2支因有密集夹杂物缺陷而报废,有4支因有夹杂物等缺陷造成锻造裂纹。电站锻件钢共生产41支,经探伤发现其中4支有严重的条状缺陷,缺陷性质为夹杂物。半钢辊钢共生产27支,其中14支因夹杂物造成不同程度的裂纹。可见夹杂物对钢锭质量造成的经济损失是非常巨大的。 1 冶炼过程中产生非金属夹杂物的原因 造渣材料碱性电弧炉常用的造渣材料采用石灰、萤石。石灰,主要成份为CaO,其含量不应小于85%,SiO2含量不大于2%,硫含量应小于0.15%。石灰易吸收水分而变成粉末,所以,造渣时要使用刚烧好的、烧透的石灰,或对石灰进行预热后再使用,这样能防止石灰给钢液带人过多的水分,否则就会使钢液氢含量增加,影响钢的质量,严重时会使钢报废。萤石,主要成份为CaF2,含量为85%、95%, SiO2含量约为6%。石中若掺杂硫化物矿石,必须将这种萤石排除掉,否则会降低炉渣的脱硫能力,易造成硫化物(MnS)夹杂。 铁合金在冶炼时,如果使用烘烤时间短、烘烤温度低、甚至根本未经烘烤的铁合金材料,势必会增加外来夹杂物和气体带人钢液中的机会。经过烘烤的铁合金上到炉台,在寒冷的冬季,露天摆放的铁合金会很快凉下来,将这些凉的铁合金加人到炼钢包内,不可能很快熔化并且在钢液中分布均匀,它们得经过一段时间的熔化和搅拌的过程。对于精炼炉来说,钢水在真空结束后,有时还要补加一些铁合金调整钢液元素含量,如果没在工艺规定的时间内出钢,势必影响真空除气、去杂质的效果,又增加了外来夹杂物进人钢液中的机会,影响钢水质量。 精炼炉真空操作精炼炉冶炼的大都是重点钢种,精炼炉的真空操作起到了画龙点睛之功效。钢水经真空处理是为了脱氢、脱氧和排除非金属夹杂物。精炼炉冶炼的钢水是由电弧炉提供的初炼钢水,有些初炼钢水在初炼过程中没有一定的脱碳量,脱碳速度也达不到要求,这样就造成钢液
钢中非金属夹杂物的分类
钢中非金属夹杂物的分类 (一) 夹杂物的来源 钢中非金属夹杂物按其形成原因可分为两类:即内生夹杂物和外来夹杂物。 内生夹杂物的来源主要有以下几个方面: (1) 脱氧剂及合金添加剂和钢中元素化学反应的产物,在钢液凝固前未浮出而残留在钢中。 (2) 出钢、浇注过程中钢水与大气接触,钢水中易氧化、氮化元素的二次氧化、氮化产物。 (3) 出钢至铸锭过程中,随钢水温度的下降,造成氧、硫、氮等元素及化合物溶解度的降低,因而产生或析出各种夹杂物。 一般的讲,内生夹杂物较为细小,合适的工艺措施可减少其含量,控制其大小和分布,但不可能完全消除。 外来夹杂物的主要来源有二个途径: (1) 冶炼、出钢及浇注过程中,钢水、炉渣及耐火材料相互作用而被卷入的耐火材料或炉渣等。 (2) 与原材料同时进入炉中的非金属夹杂物。 这类夹杂物一般较粗大,只要工艺、操作适当是可以减少和避免的。钢中常规检验遇到的夹杂物多数是内生夹杂物。 (二) 夹杂物的分类 1.按夹杂物的化学组成分类 通常根据夹杂物的化学组成可分为简单氧化物(如Al 2O 3 ,SiO 2 );复杂氧化物 (如FeO?Al 2O 3 ,CaO?Al 2 O 3 );硅酸盐及硅酸盐玻璃(如2FeO?Si O 2 );硫化物(如MnS, FeS);氮化物(如TiN);复杂夹杂如硫氧化物(Ce 2O 2 S),氟氧化物(LaOF),氮碳 化物(TiCN),硫碳化物(Ti 4C 2 S 2 )等。 钢中实际存在的夹杂物与钢的成分、冶炼过程、脱氧方法等因素有关。 2. 按夹杂物的塑性及分布分类 在生产检验中又根据夹杂物的塑性及分布特性分为脆性夹杂物、塑性夹杂物、点状不变形夹杂物。
连铸中夹杂物的控制
连铸中夹杂物的控制 连铸提高钢的质量控制夹杂物的办法有两类:第一类是防止夹杂物的生成和带入,第二类是去除钢液中已存在的夹杂物。 主要采取的对策包括:保护浇注、中间包冶金技术、中间包钢水流动控制、中间包覆盖渣、碱性包衬、中间包电磁离心分离技术、中间包热循环操作技术、防止下渣和卷渣技术、结晶器钢水流动控制、结晶器电磁搅拌技术等 采取的一些具体做法如下: 1、防止钢液的二次氧化 钢液的二次氧化是指钢液脱氧后,继续和空气中的氧或其他氧化物作用,使钢中的氧含量升高。为了防止钢液的二次氧化,应对钢液进行保护浇注,具体措施如下: (l)注流的保护。钢液注流的保护包括钢包注流的保护和中间包注流的保护。通常有长水口、浸入式水口及惰性气体屏蔽等方法。通过注流保护浇注,既可以防止注流的二次氧化,又可避免浇注时钢流冲击液面使钢液裸露而造成的二次氧化。 (2)合理使用中间包覆盖剂。为了防止钢液的二次氧化,生产高纯净钢,仅仅靠对注流的保护是不够的,因为中间包内高温钢液裸露于空气中,同样会受到空气的污染,因此减少钢液的二次氧化的另一措施就是在中间包内加覆盖剂。从提高钢水清洁度的角度来讲,覆盖剂应具备隔绝空气、绝热保温、吸收从钢液中分离出来的非金属夹杂物的功能。目前使用的覆盖剂有三种:酸性:典型的为炭化稻壳,绝热性好,成本低,但不利于吸收中间包中上浮的夹杂;中性:典型的为SiO2-A12O3质材料,有一定的绝热性,成本较低,有吸收夹杂的能力;碱性:以MgO或白云石为基的材料,吸收夹杂能力强,但绝热性能不好,易产生保护渣结壳现象。有研究表明高的碱性覆盖剂的使用效果比酸性和中性覆盖剂的使用效果好。 (3)合理使用结晶器保护渣。在结晶器中高温钢液面上加入低熔点的渣,会迅速形成粉渣层,烧结层和液渣层三层结构,并均匀地覆盖整个钢液面,将空气与钢液隔开,有效地阻止空气中的氧进入钢液。但是,渣中氧化物(如FeO)的存在会增加渣金界面的氧势,提高了液渣层中氧的扩散速率,促进空气中的氧经过渣层进入钢液中,因此一般要求保护渣中FeO<4%,有的要求小于1%。 2、防止钢包渣、中间包渣和结品器保护渣的卷入 钢包渣、中间包渣和结晶器保护渣被卷入钢液后将直接成为钢液中的夹杂物或夹渣。钢包渣在一炉钢水浇注后期易进入中间包。中间包渣的卷入是由于中间包入
钢中夹杂物控制原理
钢中夹杂物控制原理钢中氧的存在形式 T[O]=[O]溶+[O]夹 (1)转炉吹炼终点: [O]夹=>0,T[O]→[O]溶=200~1000ppm [O]溶决定于: l 钢中[C],转炉吹炼终点钢中[C]及a[O] 关系如图l 渣中(FeO); l 钢水温度。 1 顶底复吹转炉炉龄 C–Fe的选择性氧化平衡点 根据式[C] + [O] = {CO} (1) lg (Pco/ac* [%O])= 1149/T–2.002 以及反应[Fe] + [O] = (FeO)(2) lg aFeo/[%O] = 6317/T – 2.739 得到反应(FeO)+ [C] = [Fe] + {CO} (3) lg (Pco/ac* aFeo)= –5170/T+4.736 结论钢液中C-Fe的选择性氧化平衡点为[C]=0.035%,也就是说终点[C] < 0.035%时,钢水的过氧化比较严重。图1-1的统计数据也说明了这点。同时由式(1)可以求出此时熔池中的平衡氧含量为740ppm。 理论分析 1)终点[C]-[O]关系 1) 当终点[C]<0.04%时钢水的终点氧含量较高 2) 当终点[C]在0.02~0.04%范围时,有些炉次钢水氧波动在平衡曲线附近(区域Ⅰ)有些炉次钢水氧含量则远离平衡曲线(区域Ⅱ),说明在该区域钢水过氧化严重。
2)温度对氧含量的影响 在终点[C] = 0.025~0.04%时,终点氧含量虽然较分散,但总的趋势是随着终点温度的升高, 终点氧基本呈上升趋势。 1620℃~1680℃之间,氧含量总体水平较低,平均为702ppm ,该范围的炉次共占总炉次的 30%左右;出钢温度大于1680℃时,终点钢水氧含量有明显的升高趋势,平均为972ppm , 占总炉次的70%左右。 3)终渣氧化性对终点氧的影响 200400 600800100012001400 1600 1800160016201640166016801700172017401760终点温度(℃)终点氧含量(p p m )
钢中夹杂物的产生与去除途径
钢中夹杂物的产生与去除途径 李振旭钢中夹杂物对钢质量的影响越来越受到重视,怎样减少钢中夹杂物对钢材性能的影响,各大院校、钢铁研究机构有很多研究成果及文献。生产清洁钢有很多措施与手段,在此不作详细介绍,我想就电弧炉单设备冶炼,结合很多的文献作一下具体分析与验证。 钢中夹杂物的来源无非有两大类:一、外来夹杂。二、内生夹杂。 外来夹杂是由原材料、炉渣、耐火材料等引起的。如炼钢的废钢带入的泥沙、铅锌砷锑鉍等,出钢时钢液混渣,炉衬、出钢槽、盛钢桶等耐火材料的侵蚀、冲刷剥离等造成的。 内生的夹杂物是由脱氧产物、析出气体的反应产物构成的。一般脱氧产物称为一次夹杂。二次夹杂为钢液从浇注温度下降到液相线,由于温度下降气体的溶解度下降析出而产生的夹杂物。三次夹杂是金属在固相线下由于结晶而产生的。四次夹杂是结晶完成后到常温过程中由于发生组织转变而产生的。由此可以看出钢中的夹杂物大部分是一次夹杂和二次夹杂。 外来夹杂通过现场管理及使用优质耐火材料是可以控制或减少的,三、四次夹杂是无法消除的,故此不做讨论。重点讨论一二次夹杂的产生与去除。 钢在熔炼的过程中为了去除由原料带入的杂质及有害元素,往往采取氧化法冶炼。利用碳氧沸腾来增加熔池的动能,通过一氧化碳的排出将熔于钢液中的气体及夹杂物去除,氧化以后钢液得到净化。但当氧化结束以后,钢液中存在较多的溶解氧及氧化铁,这种钢液在浇注时会因气体含量高而引起冒涨而导致无法使用,那么就要对钢液进行脱氧操作。目前脱氧主要有沉淀脱氧、扩散脱氧及两种方法结合的综合脱氧法。硅铁、锰铁是目前最常用的脱氧剂,其他的有铝、硅铝铁、硅锰合金、硅钙合金、硅钙钡、硅铝钡、硅镁、镍镁合金混合稀土等等。用于扩散脱氧的有碳粉、硅铁粉、硅钙粉、铝粉、碳化硅粉等。作为沉淀脱氧剂的硅铁、锰铁等直接加入钢液,它的脱氧产物是SIO2和MnO,MnS等,用铝作为终脱氧剂脱氧其产物是AI2O3,其中一部分会上浮排除,当然还会有部分存在于钢液中,造成氧化物夹杂。另一方面,由于钢液中存在少量的氮、硫、磷、氢、氧,他们也会与铁等元素发生反应生成非金属夹杂物。分为硫化物、氧化物、氮化物,如FeS、MnS、SIO2、VN、AIN、TIN等,简单氧化物MnO、FeO、AI2O3等,复合氧化物FeO.MnO,FeO.AI2O3,还有铁硅酸盐、锰硅酸盐等。 钢中夹杂物的形态特征:内生夹杂物的特点是颗粒小、分布较均匀。硫化物一般为网状、也可以呈细长针状,呈网状的硫化物易引起热脆性,三氧化二铝夹杂往往呈簇状或串链状。硫化钙、铝酸钙及尖晶石类硅酸盐为点状不变形夹杂。硫化物夹杂在轧钢中表现为沿轧制方向的带状物。二氧化硅或含二氧化硅高的硅酸盐类夹杂一般呈球状不变形物。但如果想要知道究竟是哪一类夹杂要依靠EPMA(电子探针)扫描电镜和自带能谱分析仪(SEM、EDS)的帮助。为了减少钢中夹杂物的数量,控制夹杂物的形成、形态及分布很重要,为此众多的研究及技术人员加入研究之中。首先从脱氧方法、脱氧工艺入手,通过优化脱氧工艺,改变传统的脱氧方法,采用新的脱氧剂、发展炉外精炼等手段,使纯净钢的冶炼得到很大发展。 一般的脱氧程序是:加入硅铁、锰铁沉淀脱氧,然后加碳粉、碳化硅、或硅铁粉、硅钙粉等扩散脱氧,出钢时用铝终脱氧。这种方式易产生二氧化硅、三氧化二铝等夹杂。 用铝作为终脱氧剂,也称深脱氧。他的优点是脱氧较充分,尤其是钢液中Mn=0.66%,SI=0.17%时(锰硅比大约为4)铝的脱氧能力提高5--10倍。同时残铝可以起到固氮的作用,生成的AIN起到强烈细化晶粒的作用,可以显著提高钢的性能、特别是韧性指标。另外钢中含有部分残铝,可以防止钢液的二次氧化,特别是硅的二次氧化,为了充分利用他的优点,往往要求钢中的酸熔铝[AI]S为0.02—0.05%,而钢中残铝大于0.010%则被视为过度铝脱氧。
钢中夹杂物知识
摘要:根据钢中非金属夹杂物的来源和分类,综述了鉴定钢中非金属夹杂物的方法和定量评级标准,并且给出了典型夹杂物的扫描电镜照片,分析了不同类型夹杂物的形成机理及其在光学显微镜下的基本特征。 随着现代工程技术的发展,对钢的综合性能要求也日趋严格,相应地对钢的材质要求了越来越高。非金属夹杂物作为独立相存在于钢中,破坏了钢基体的连续性,加大了钢中组织的不均匀性,严重影响了钢的各种性能。例如,非金属夹杂物导致应力集中,引起疲劳断裂;数量多且分布不均匀的夹杂物会明显降低钢的塑性、韧性、焊接性以及耐腐蚀性;钢中呈网状存在的硫化物会造成热脆性。因此,夹杂物的数量和分布被认定是评定钢材质量的一个重要指标,并且被列为优质钢和高级优质钢出厂的常规检测项目这一。 非金属夹杂物的性质、形态、分布、尺寸及含量不同,对钢性能的影响也不同。所以提高金属材料的质量,生产出洁净钢,或控制非金属夹杂物性质和要求的形态,是冶炼和铸锭过程中的一个艰巨任务。而对于金相分析工作者来说,如何正确判断和鉴定非金属夹杂笺也因此变得十分重要。 1 钢中非金属夹杂物的来源分类 1.1 内生夹杂物 钢在冶炼过程中,脱氧反应会产生氧化物和硅酸盐等产物,若在钢液凝固前未浮出,将留在钢中。溶解在钢液中的氧、硫、氮等杂质元素在降温和凝固时,由于溶解度的降低,与其他元素结合以化合物形式从液相或固溶体中析出,最后留在钢锭中,它是金属在熔炼过程中,各种物理化学瓜形成的夹杂物。内生夹杂物分布比较均匀,颗粒也较小,正确的操作和合理的工艺措施可以减少其数量和改变其成分、大小和分布情况,但一般来说是不可避免的。 1.2 外来夹杂物 钢在冶炼和浇注过程中悬浮在钢液表面的炉渣、或由炼钢炉、出钢槽和钢包等内壁肃落的耐火材料或其他夹杂物在钢液凝固前未及时清除而留于钢中。它是金属在熔炼过程中与外界物质接触发生作用产生的夹杂物。如炉料表面的砂土和炉衬等与金属液作用,形成熔渣而滞留在金属中,其中也包括加入的熔剂。这类夹杂物一般的牲是外形不规则,尺寸比较大,颁也没有规律,又称为粗夹杂。这类夹杂物通过正确的操作是可以避免的。 2 钢中非金属夹杂物按化学成分分类 钢中非金属夹杂物按化学成分详细分类见图1,主要分为三大类。 图1 钢中非金属夹按照化学成分分类图 2.1 氧化物系夹杂 简单氧化物有FeO,Fe2O3,MnO,SiO2,Al2O3,MgO和Cu2O等。在铸钢中,当用硅铁或铝进行脱氧时,夹杂比较常见。在钢中常常以球形聚集呈颗粒状成串分布。复杂氧化物,包括尖晶石类