铝合金轮毂UG建模和ANSYS有限元应力分析
UG有限元分析第12章

UG有限元分析第12章第12章:有限元分析在结构密集度设计中的应用导言:有限元分析是一种基于离散化方法的数值分析技术,可以用于求解结构力学问题。
它已经成为现代工程设计的重要工具之一、本章将研究有限元分析在结构密集度设计中的应用,以及相关的优化算法。
1.结构密集度设计的概念和要求结构密集度设计是指通过优化设计,将结构尺寸和重量最小化的设计方法。
在工程实践中,通常需要同时考虑结构的强度、刚度、稳定性和减震等因素。
有限元分析为结构密集度设计提供了一种有效的数值分析方法。
2.有限元模型的建立在进行有限元分析之前,首先需要建立结构的有限元模型。
有限元模型的建立包括网格划分、单元类型的选择和边界条件的设定等步骤。
在结构密集度设计中,需要使用合适的单元类型和足够的网格密度来保证分析结果的准确性。
3.结构的优化设计在有限元分析的基础上,可以进行结构的优化设计,以实现结构密集度的最小化。
常用的优化算法包括遗传算法、粒子群算法和模拟退火算法等。
这些算法可以通过调整结构的参数,如尺寸、形状和材料等,来实现结构的优化设计。
4.结构密集度设计的应用案例本章还将介绍几个结构密集度设计的应用案例,包括飞机机翼、汽车车身和桥梁等结构的优化设计。
这些案例将展示有限元分析在结构密集度设计中的应用效果,并讨论其对结构性能和重量的影响。
5.研究进展和展望最后,本章将总结有限元分析在结构密集度设计中的应用,并对未来的研究方向进行展望。
随着计算机技术的不断发展和优化算法的改进,有限元分析在结构密集度设计中的应用将变得更加广泛和深入。
总结:有限元分析在结构密集度设计中发挥了重要作用。
通过建立合适的有限元模型和使用优化算法,可以实现结构的最优设计和重量的最小化。
未来的研究还应该关注如何进一步提高有限元分析的准确性和效率,以及如何将其与其他优化技术相结合,为工程实践提供更好的解决方案。
UG有限元分析步骤精选整理.doc

UG有限元分析步骤精选整理.doc
1. 准备模型:首先,在UG中绘制需要分析的零件或装配体的3D模型。
确保模型的几何尺寸和材料等参数设置正确。
2. 网格划分:将模型分割成许多小单元,称为网格单元。
这些单元的大小和形状应
该足够小和简单,以便于计算程序的处理。
3. 材料属性定义:为每个网格单元定义材料性质。
这些属性包括弹性模量、泊松比、密度等。
4. 约束条件设置:定义所有约束条件,如边界约束、支撑条件等。
这些条件对应于
被分析部件的实际使用场景。
5. 载荷应用:将载荷应用于模型。
这些载荷可以是静态或动态载荷、温度载荷等,
也可以模拟外部力或压力。
6. 求解模型:选定求解器,使用许多数学方法解决数学方程,以有效地计算应力、
应变和变形等设计参数。
7. 结果分析:对有限元分析的各个方面进行评估和评估,检查计算的准确性和可靠性。
这些结果可以用于优化设计,以改进零件或装配体的性能。
8. 优化设计:如果有必要,使用有限元分析的结果来重新设计零件或装配体,并在
再次进行分析前进行修改。
总之,UG有限元分析是一种重要的工具,用于设计和生产过程中的性能优化和验证。
这个步骤需要正确的建模和分析,以确保计算是精确和可靠的。
铝合金焊接件的结构应力与变形有限元分析
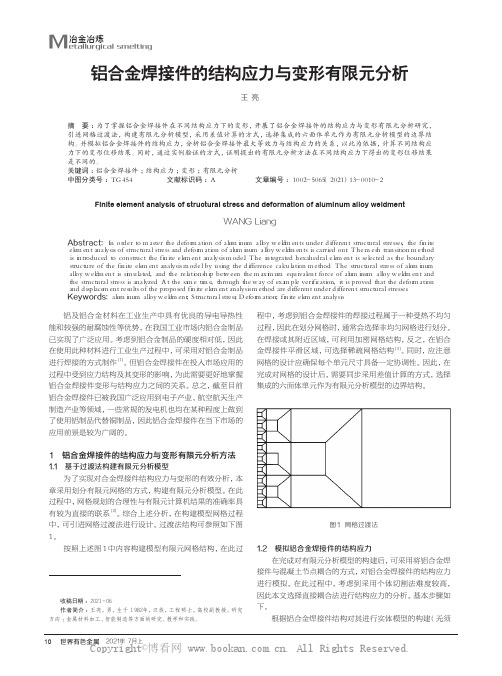
世界有色金属 2021年 7月上10冶金冶炼M etallurgical smelting铝合金焊接件的结构应力与变形有限元分析王 亮(甘肃能源化工职业学院,甘肃 兰州 730207)摘 要:为了掌握铝合金焊接件在不同结构应力下的变形,开展了铝合金焊接件的结构应力与变形有限元分析研究,引进网格过渡法,构建有限元分析模型,采用差值计算的方式,选择集成的六面体单元作为有限元分析模型的边界结构。
并模拟铝合金焊接件的结构应力,分析铝合金焊接件最大等效力与结构应力的关系,以此为依据,计算不同结构应力下的变形位移结果。
同时,通过实例验证的方式,证明提出的有限元分析方法在不同结构应力下得出的变形位移结果是不同的。
关键词:铝合金焊接件;结构应力;变形;有限元分析中图分类号:TG454 文献标识码:A 文章编号:1002-5065(2021)13-0010-2Finite element analysis of structural stress and deformation of aluminum alloy weldmentWANG Liang(Gansu Vocational College of energy and chemical engineering Lanzhou 730207,China)Abstract: In order to master the deformation of aluminum alloy weldments under different structural stresses, the finite element analysis of structural stress and deformation of aluminum alloy weldments is carried out. The mesh transition method is introduced to construct the finite element analysis model. The integrated hexahedral element is selected as the boundary structure of the finite element analysis model by using the difference calculation method. The structural stress of aluminum alloy weldment is simulated, and the relationship between the maximum equivalent force of aluminum alloy weldment and the structural stress is analyzed. At the same time, through the way of example verification, it is proved that the deformation and displacement results of the proposed finite element analysis method are different under different structural stresses.Keywords: aluminum alloy weldment; Structural stress; Deformation; finite element analysis铝及铝合金材料在工业生产中具有优良的导电导热性能和较强的耐腐蚀性等优势,在我国工业市场内铝合金制品已实现了广泛应用。
基于Ansys Workbench的铝合金轮毂结构的疲劳分析

基于Ansys Workbench的铝合金轮毂结构的疲劳分析徐浩【摘要】车轮是汽车上主要的运动和支撑部件,镁合金由于其具有高强度、良好的导热性、重量轻等特点,因此在当今汽车上的应用越来越多.但统计可知,轮毂仍是车辆故障的常见零件之一.本文从轮毂的实际结构出发,以Ansys Workbench有限元分析软件作为分析工具,模拟分析某家用轿车的轮毂使用情况,验证了该材料的性能满足要求的同时找出易发生故障的部位,为车辆后续维修、优化提供了理论依据.【期刊名称】《三门峡职业技术学院学报》【年(卷),期】2018(017)001【总页数】3页(P142-144)【关键词】轮毂;Ansys Workbench;疲劳【作者】徐浩【作者单位】商丘工学院机械工程学院,河南商丘476000【正文语种】中文【中图分类】U463.34随着世界范围性的环保法规的日趋严格以及人们环保意识的不断加强,汽车排放法规也越来越严,汽车重量作为影响车辆排放的主要因素之一在环保中占据的地位日益重要。
因此汽车轻量化设计已成为当今汽车行业主流的研发方向之一,轮毂是车辆行驶系中轮胎装配的基础,对轮毂进行优化设计能够有效降低整车质量[1]。
实测可知,采用铝合金材料的轮毂质量为7.852Kg,而相同尺寸下,普通材料轮毂质量为20.714Kg,以每辆车5条轮胎(含备胎)计算,采用铝合金材料的轮毂的车辆整备质量可以降低64.31Kg,占车辆整备质量的5.145%。
由《汽车用钢轻量化战略合作框架协议》可知,汽车自重每减少10%,可降低油耗6~8%,排放降低12%。
笔者选用LC4铝合金铸造成型工艺的整体式车轮为研究对象,参照汽车行业标准GB/T5334-2005《乘用车车轮性能要求和试验方法》所规定的轻质合金车轮的动态弯曲疲劳性能和动态径向疲劳性能试验所要求的加载参数和试验方法[2],利用Ansys Workbench软件对车轮的动态疲劳试验进行模拟分析,从而为车辆的优化设计、故障检测及维修提供有力的理论支撑。
铝合金轮毂冲击试验瞬态有限元分析
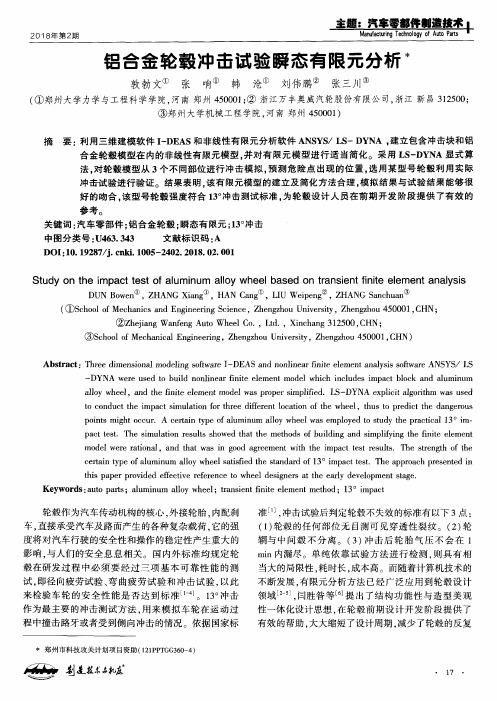
DUN Bowen① ZHANG Xiang① HAN Cang① LIU W eipeng② ZHANG Sanchuan③
,
,
,
,
(@School of Mechanics and Engineer ing Science,Zhengzhou University,Zhengzhou 450001,CHN;
Keywords:auto par ts;aluminum alloy wheel;transient f inite element method;1 3。impact
轮毂 作 为汽 车传 动机 构 的核 心 ,外接 轮胎 .内配刹 车 ,直 接 承受 汽 车及路 面产生 的各 种 复杂 载荷 ,它 的强 度 将 对 汽车行 驶 的安 全性 和操 作 的稳 定性 产 生重 大 的 影 响 ,与人 们 的安 全 息 息 相 关 。 国 内外 标 准 均 规 定 轮 毂 在 研发 过 程 中必 须 要 经 过 三 项 基 本 可 靠 性 能 的 测 试 ,即径 向疲 劳试 验 、弯 曲疲 劳 试 验 和 冲 击试 验 ,以此 来 检验 车 轮 的 安 全 性 能 是 否 达 到 标 准 E卜 。13。冲击 作为最主要 的冲击测试 方法 .用来模拟车轮在运动过 程 中撞 击路 牙 或者 受到 侧 向 冲击 的情况 。依 据 国家标
@ Zh ̄iang Wanfeng Auto Wheel Co.,Ltd.,Xinchang 3 1 2500,CHN;
@ School of Mechanical Engineer ing,Zhengzhou University,Zhengzhou 450001,CHN)
Abstract:Three dimensional modeling software I—DEAS and nonlinear finite element analysis software ANSYS/ I5 — · DYNA were used to build nonlinear finite element model which includes impact block and aluminum alloy wheel,and the f inite element model was proper simplif ied. LS—DYNA explicit algorithm was used to conduct the impact simulation for three different location of the wheel,thus to predict the dangerous points might Occur. A certain type of aluminum alloy wheel was employed to study the practical 1 3。im— pact test. The simulation results showed that the methods of building and sim plifying the finite element model were rational,and that was in good agreement with the impact test results. The strength of the certain type of alum inum alloy wheel satisfied the standard of 1 3。 impact test.The approach presented in this paper provided effective reference to wheel designers at the early developm ent stage.
轮毂性能分析

UG汽车轮毂性能分析一、冲击试验(安全系数105Mpa)1.设计载重转换计算例:690KG试验条件:F=F1+F2 两个分力F1=690KG ×9.8N/Kg ×Cos13°×1.5(安全系数)=2282N Y轴方向F2=690KG ×9.8N/Kg ×Sin13°×1.5(安全系数)=9883N Z轴方向``2.准备操作选择气门嘴对面的辐条端;直线命令在象限点,作线段,然后将线段向下偏置25 mm` 投影命令,将偏置后的曲线投影到倒圆角面;方向:沿Z轴投影;利用投影曲线分割曲面。
选择分割面命令确认此面已分割3. UG结构分析操作选择结构P.E.解算器;4.(1)附着材料;选择材料命令;选择材料库;单击,确定;选择A356;选择轮毂3D ;附着;(2)给定载荷;单击,选择分割好的面,输入载荷方向和值;Y轴和Z轴负方向出现载荷力方向完成给定载荷操作(3)给定约束条件;单载荷击,选择安装盘作为约束,固定;(4)划分网格;单击划分网格;类型选用TETRA10 ,单位默认完成划分网格;(5)解算;单击解算;确定直到出现:完成划分网格;(6)后处理单击后处理;出现选择Scenario导航器,再选择STRESS 项目;单击后处理视图选择颜色条,最大值输入105 ,以105作为一个最大值的参考界限,超出0值过大,显示红块面积较大,表示此轮毂不能通过冲击试验。
打开显示标记开关,可以显示最大和最小的单元格值打开识别按钮;可以利用查看笔,查看显示每个单元网格的值;显示红块没危险区域,如此区域过大,此轮毂性能叫差。
(7)创建报告完成试验。
二、弯曲疲劳试验1. 试验条件:(1)试验弯矩计算公式:M=1.5×F1×(0.7×r+d)[kN•m]{F1=试验适用载荷值(KN);r=静负荷半径(m) ;d=偏距值(m)}例:轮毂参数:size:18×8.5 ; pcd:5-120 ; et:35 单位转换成N•m查表给定数据:M=1.5×7950N×(0.7×0.354m+0.035m)×2(安全系数)=11925×0.2828×2=6744.78 N•m此值给定Fy 矢量;(2)试验约束状况;将轮毂安装在一根1M长的铁柱上,旋转10万转,试验后查看偏移量,轮毂裂纹;UG分析试验条件:将安装盘拉伸500mm(0.5M)与轮毂做合并的布尔运算。
基于ANSYS Workbench的轮毂弯曲疲劳分析
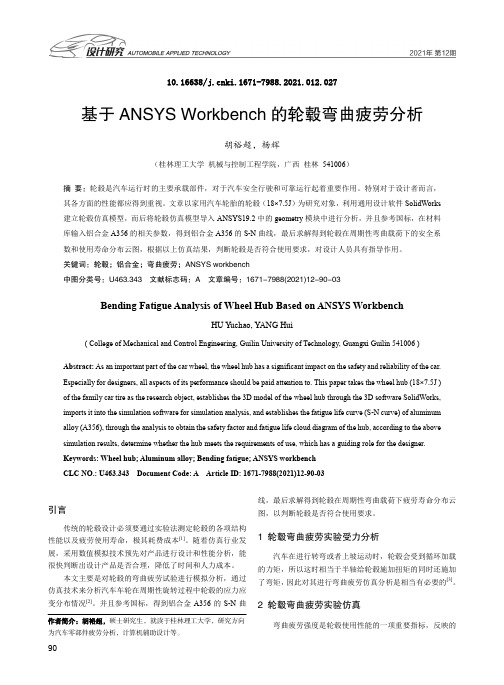
10.16638/ki.1671-7988.2021.012.027基于ANSYS Workbench的轮毂弯曲疲劳分析胡裕超,杨辉(桂林理工大学机械与控制工程学院,广西桂林541006)摘要:轮毂是汽车运行时的主要承载部件,对于汽车安全行驶和可靠运行起着重要作用。
特别对于设计者而言,其各方面的性能都应得到重视。
文章以家用汽车轮胎的轮毂(18×7.5J)为研究对象,利用通用设计软件SolidWorks 建立轮毂仿真模型,而后将轮毂仿真模型导入ANSYS19.2中的geometry模块中进行分析,并且参考国标,在材料库输入铝合金A356的相关参数,得到铝合金A356的S-N曲线,最后求解得到轮毂在周期性弯曲载荷下的安全系数和使用寿命分布云图,根据以上仿真结果,判断轮毂是否符合使用要求,对设计人员具有指导作用。
关键词:轮毂;铝合金;弯曲疲劳;ANSYS workbench中图分类号:U463.343 文献标志码:A 文章编号:1671-7988(2021)12-90-03Bending Fatigue Analysis of Wheel Hub Based on ANSYS WorkbenchHU Yuchao, YANG Hui( College of Mechanical and Control Engineering, Guilin University of Technology, Guangxi Guilin 541006 )Abstract: As an important part of the car wheel, the wheel hub has a significant impact on the safety and reliability of the car. Especially for designers, all aspects of its performance should be paid attention to. This paper takes the wheel hub (18×7.5J ) of the family car tire as the research object, establishes the 3D model of the wheel hub through the 3D software SolidWorks, imports it into the simulation software for simulation analysis, and establishes the fatigue life curve (S-N curve) of aluminum alloy (A356), through the analysis to obtain the safety factor and fatigue life cloud diagram of the hub, according to the above simulation results, determine whether the hub meets the requirements of use, which has a guiding role for the designer. Keywords: Wheel hub; Aluminum alloy; Bending fatigue; ANSYS workbenchCLC NO.: U463.343 Document Code: A Article ID: 1671-7988(2021)12-90-03引言传统的轮毂设计必须要通过实验法测定轮毂的各项结构性能以及疲劳使用寿命,极其耗费成本[1]。
基于ANSYS的巴哈赛车轮毂法兰的优化设计

- 30 -高 新 技 术0 前言中国汽车工程学会巴哈大赛(Baja SAE China)是由中国汽车工程学会主办,在各院校间开展的小型越野赛车设计和制作的竞赛。
前轮毂法兰在巴哈赛车上用于安装制动盘和轮辋并为其提供支撑作用,承受着径向载荷与轴向载荷的同时,在制动时还要承受扭转载荷,是一个非常重要的安全件。
轮毂法兰同时还属于非簧载质量,对于赛车来讲轻量化尤为重要;同时巴哈赛车的路况非常复杂,常伴随着飞坡、撞击圆木、快速通过炮弹坑等恶劣路况,因此更需要保证巴哈赛车的前轮毂法兰强度。
该文在对轮毂法兰的设计和三维建模的基础上,选取3种极限路况下的受力情况,利用ANSYS 软件对其进行静力学仿真分析,得到轮毂法兰的最大应力分布情况,并对其进行形状优化,由此来减轻轮毂法兰的质量,最后再利用应力应变的仿真分析,校验优化设计。
1 轮毂法兰的设计轮毂设计是在对称安装的圆锥滚子轴承的基础上,在两端进行制动盘安装法兰与轮辋安装法兰的设计,轮辋安装法兰由于安装的是轮辋,所以需要传递轮胎所受的径向载荷与轴向载荷。
因此,在轮芯与法兰的过渡处进行了大角度倒角设计以增加其强度,如图1所示。
图1 轮毂三维设计图2 轮毂法兰的受力分析ANSYS 分析以静力分析为主,主要用于校核零件的刚强度,分析时输入的是3种极限工况下的受力,包括急转向工况、制动紧急制动以及越过不平路面工况,在3种工况下分别求得该工况下的最大受力。
2.1 急转向工况在急转向工况下,以安装在转向节上的轴承作为约束点,求出地面与轮胎接触点的受力,通过力的平移法求得轮辋给轮毂的受力, 由此来设定轮毂的边界条件。
2.2 越过不平路面工况在越过不平路面工况下,以炮弹坑为例,轮毂的受力主要有来自于路面给轮胎的Z 方向的载荷以及越过不平路面的X 方向的受力。
2.3 紧急制动工况在紧急制动工况下,轮毂的受力主要由2个部分组成,一部分由地面传给轮胎的制动力矩M 制与制动盘传给制动销钉的支座反力矩组成;另一部分由紧急制动下轴荷转移产生的F Z 支与转向节轴的支座反力组成。