碳钢表面共渗金属技术及应用
渗碳处理知识点总结
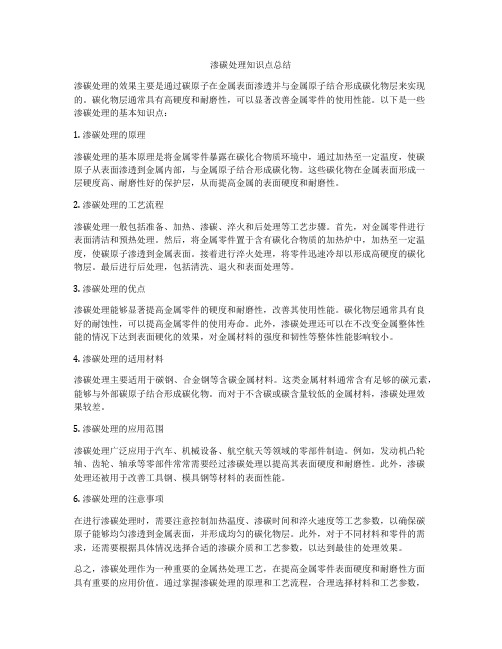
渗碳处理知识点总结渗碳处理的效果主要是通过碳原子在金属表面渗透并与金属原子结合形成碳化物层来实现的。
碳化物层通常具有高硬度和耐磨性,可以显著改善金属零件的使用性能。
以下是一些渗碳处理的基本知识点:1. 渗碳处理的原理渗碳处理的基本原理是将金属零件暴露在碳化合物质环境中,通过加热至一定温度,使碳原子从表面渗透到金属内部,与金属原子结合形成碳化物。
这些碳化物在金属表面形成一层硬度高、耐磨性好的保护层,从而提高金属的表面硬度和耐磨性。
2. 渗碳处理的工艺流程渗碳处理一般包括准备、加热、渗碳、淬火和后处理等工艺步骤。
首先,对金属零件进行表面清洁和预热处理。
然后,将金属零件置于含有碳化合物质的加热炉中,加热至一定温度,使碳原子渗透到金属表面。
接着进行淬火处理,将零件迅速冷却以形成高硬度的碳化物层。
最后进行后处理,包括清洗、退火和表面处理等。
3. 渗碳处理的优点渗碳处理能够显著提高金属零件的硬度和耐磨性,改善其使用性能。
碳化物层通常具有良好的耐蚀性,可以提高金属零件的使用寿命。
此外,渗碳处理还可以在不改变金属整体性能的情况下达到表面硬化的效果,对金属材料的强度和韧性等整体性能影响较小。
4. 渗碳处理的适用材料渗碳处理主要适用于碳钢、合金钢等含碳金属材料。
这类金属材料通常含有足够的碳元素,能够与外部碳原子结合形成碳化物。
而对于不含碳或碳含量较低的金属材料,渗碳处理效果较差。
5. 渗碳处理的应用范围渗碳处理广泛应用于汽车、机械设备、航空航天等领域的零部件制造。
例如,发动机凸轮轴、齿轮、轴承等零部件常常需要经过渗碳处理以提高其表面硬度和耐磨性。
此外,渗碳处理还被用于改善工具钢、模具钢等材料的表面性能。
6. 渗碳处理的注意事项在进行渗碳处理时,需要注意控制加热温度、渗碳时间和淬火速度等工艺参数,以确保碳原子能够均匀渗透到金属表面,并形成均匀的碳化物层。
此外,对于不同材料和零件的需求,还需要根据具体情况选择合适的渗碳介质和工艺参数,以达到最佳的处理效果。
渗氮 渗碳 碳氮共渗

渗氮渗碳碳氮共渗碳氮共渗是一种常见的表面处理技术,通过渗碳和渗氮来改善材料的硬度和耐磨性。
本文将对渗氮、渗碳和碳氮共渗的原理、应用和工艺进行详细介绍。
一、渗氮渗氮是将氮原子渗入材料表面形成氮化物层的过程。
氮原子通过高温处理和氮气氛的作用,渗透到材料表面并与材料中的元素反应,形成硬质氮化物层。
这一薄层氮化物层不仅能提高材料的硬度和抗磨损性能,还能改善材料的耐腐蚀性。
渗氮的主要应用领域包括机械制造、汽车工业、航空航天等。
在机械制造中,渗氮可以增加零件的硬度和耐磨性,延长使用寿命;在汽车工业中,渗氮可以提高引擎零件的耐磨性和抗腐蚀性能;在航空航天领域,渗氮可以增强航空发动机部件的耐高温和耐磨性能。
渗氮的工艺流程一般包括清洗件表面、装配件和炉内预处理、渗氮和回火处理等步骤。
渗氮一般采用封闭式和开放式两种方式进行,根据具体应用需求可以选择合适的渗氮工艺。
二、渗碳渗碳是将碳原子渗入材料表面形成碳化物层的过程。
碳原子通过高温处理和含有碳气体的氛围,渗透到材料表面并在表面与材料中的元素反应,形成硬质碳化物层。
渗碳技术不仅能提升材料的硬度和耐磨性,还可以改善材料的断裂韧性和抗腐蚀性。
渗碳广泛应用于机械零件、钢铁制品等领域。
渗碳后的材料表面硬度高、耐磨性好,适用于制作耐磨零件,如轴承、齿轮等;同时碳化层的外表面与空气隔绝,降低了材料的腐蚀速率,提高了零件的使用寿命。
渗碳的工艺流程包括预处理、渗碳、淬火和回火等。
渗碳一般采用气体渗碳和液体渗碳两种方式进行,具体工艺参数可以根据材料的要求进行选择。
三、碳氮共渗碳氮共渗是将碳原子和氮原子同时渗入材料表面形成碳氮共渗层的过程。
碳氮共渗通过碳氮共渗剂和高温处理,使碳原子和氮原子分别与材料中的元素发生反应,形成硬质碳氮化物层。
碳氮共渗能够同时获得渗碳和渗氮的特性,提高材料的硬度、耐磨性和抗腐蚀性。
碳氮共渗广泛应用于汽车工业、航空航天等领域。
在汽车工业中,碳氮共渗可以提高零部件的硬度和耐磨性,同时还可以提高零部件的抗磨损能力和抗腐蚀性;在航空航天领域,碳氮共渗可以增强发动机部件的抗高温性能和抗腐蚀能力。
渗碳的方法原理应用

渗碳的方法原理应用1. 渗碳的定义渗碳是一种金属表面处理工艺,通过在金属表面形成富碳层,提高金属材料的硬度和耐磨性。
渗碳是通过将含碳化合物加热至高温,使其在金属表面扩散,形成富碳层的过程。
2. 渗碳的原理渗碳的原理基于扩散理论,即在高温下,含碳化合物中的碳原子会从高浓度区域向低浓度区域扩散,最终在金属表面形成富碳层。
渗碳的速率取决于温度、时间和温度梯度。
3. 渗碳的方法渗碳的方法主要包括以下几种:•固体渗碳:将含碳化合物(如氰化钠、氰化钾等)与金属样品一同加入高温容器中,通过高温加热使碳原子扩散到金属表面。
•液体渗碳:通过将含有碳源的液体(如液态碳氢化合物)浸泡金属样品,使碳原子通过溶液扩散到金属表面。
•气体渗碳:通过在高温环境下,将含碳气体(如甲烷、一氧化碳等)与金属样品接触,使碳原子在金属表面扩散。
•离子渗碳:通过将含碳化合物(如氰化物)溶解在溶剂中,再通过电场作用将碳离子引入金属样品,实现渗碳。
4. 渗碳的应用渗碳广泛应用于许多领域,主要包括以下几个方面:•机械工程:在机械工程中,渗碳可以提高金属的硬度和耐磨性,用于制造轴承、齿轮等零部件,增加其使用寿命。
•汽车工业:在汽车工业中,渗碳可以用于制造曲轴、减震器等零部件,提高其耐磨性和强度。
•航空航天:在航空航天领域,渗碳可用于制造发动机零部件、航空轴承等高性能材料,提高其抗腐蚀性能和疲劳寿命。
•工具制造:在工具制造中,渗碳可以用于制造刀具、钻头等工具,提高其切削性能和寿命。
•能源领域:在能源领域,渗碳可用于制造石油钻具、钻井机零部件等设备,提高其耐磨性和使用寿命。
5. 渗碳的优点和注意事项渗碳具有以下优点:•提高材料硬度和耐磨性;•延长材料使用寿命;•显著改善材料表面性能。
渗碳需要注意以下事项:•清洁金属表面,避免表面有锈蚀、油污等影响渗碳效果;•控制渗碳工艺参数,如温度、时间,以保证渗碳层的质量;•选择合适的渗碳方法,根据不同材料和应用场景进行选择;•进行适当的后处理,如淬火、回火等,以提高渗碳层的性能。
渗碳和渗氮的新概念及其实际运用
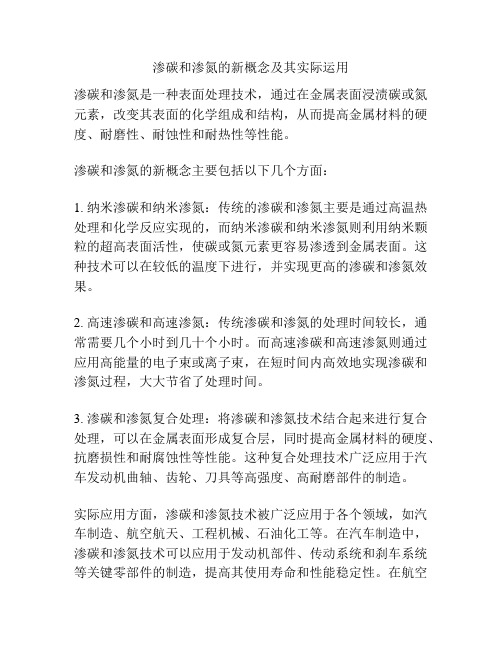
渗碳和渗氮的新概念及其实际运用
渗碳和渗氮是一种表面处理技术,通过在金属表面浸渍碳或氮元素,改变其表面的化学组成和结构,从而提高金属材料的硬度、耐磨性、耐蚀性和耐热性等性能。
渗碳和渗氮的新概念主要包括以下几个方面:
1. 纳米渗碳和纳米渗氮:传统的渗碳和渗氮主要是通过高温热处理和化学反应实现的,而纳米渗碳和纳米渗氮则利用纳米颗粒的超高表面活性,使碳或氮元素更容易渗透到金属表面。
这种技术可以在较低的温度下进行,并实现更高的渗碳和渗氮效果。
2. 高速渗碳和高速渗氮:传统渗碳和渗氮的处理时间较长,通常需要几个小时到几十个小时。
而高速渗碳和高速渗氮则通过应用高能量的电子束或离子束,在短时间内高效地实现渗碳和渗氮过程,大大节省了处理时间。
3. 渗碳和渗氮复合处理:将渗碳和渗氮技术结合起来进行复合处理,可以在金属表面形成复合层,同时提高金属材料的硬度、抗磨损性和耐腐蚀性等性能。
这种复合处理技术广泛应用于汽车发动机曲轴、齿轮、刀具等高强度、高耐磨部件的制造。
实际应用方面,渗碳和渗氮技术被广泛应用于各个领域,如汽车制造、航空航天、工程机械、石油化工等。
在汽车制造中,渗碳和渗氮技术可以应用于发动机部件、传动系统和刹车系统等关键零部件的制造,提高其使用寿命和性能稳定性。
在航空
航天领域,渗碳和渗氮技术可以应用于航空发动机涡轮叶片、导向叶片等高温部件的制造,提高其耐热性和耐腐蚀性。
总之,渗碳和渗氮的新概念和实际运用不断拓展着金属材料表面处理的领域,为各个行业提供了更高性能的金属材料解决方案。
钢的渗碳和碳氮共渗、淬火、回火工艺
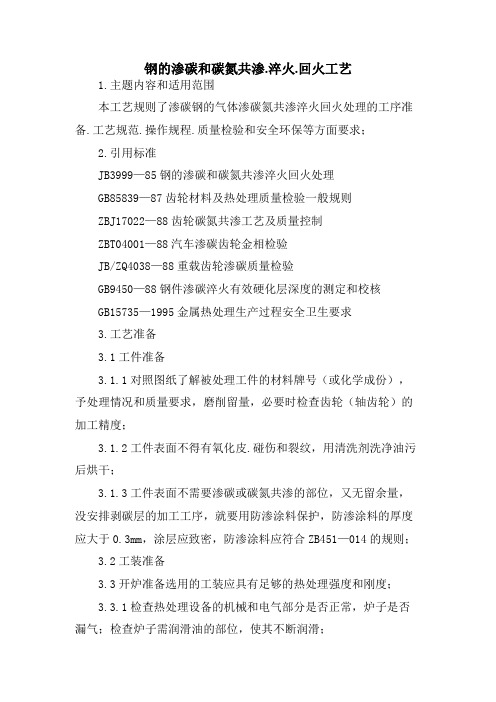
钢的渗碳和碳氮共渗.淬火.回火工艺1.主题内容和适用范围本工艺规则了渗碳钢的气体渗碳氮共渗淬火回火处理的工序准备.工艺规范.操作规程.质量检验和安全环保等方面要求;2.引用标准JB3999—85钢的渗碳和碳氮共渗淬火回火处理GB85839—87齿轮材料及热处理质量检验一般规则ZBJ17022—88齿轮碳氮共渗工艺及质量控制ZBT04001—88汽车渗碳齿轮金相检验JB/ZQ4038—88重载齿轮渗碳质量检验GB9450—88钢件渗碳淬火有效硬化层深度的测定和校核GB15735—1995金属热处理生产过程安全卫生要求3.工艺准备3.1工件准备3.1.1对照图纸了解被处理工件的材料牌号(或化学成份),予处理情况和质量要求,磨削留量,必要时检查齿轮(轴齿轮)的加工精度;3.1.2工件表面不得有氧化皮.碰伤和裂纹,用清洗剂洗净油污后烘干;3.1.3工件表面不需要渗碳或碳氮共渗的部位,又无留余量,没安排剥碳层的加工工序,就要用防渗涂料保护,防渗涂料的厚度应大于0.3mm,涂层应致密,防渗涂料应符合ZB451—014的规则;3.2工装准备3.3开炉准备选用的工装应具有足够的热处理强度和刚度;3.3.1检查热处理设备的机械和电气部分是否正常,炉子是否漏气;检查炉子需润滑油的部位,使其不断润滑;3.3.2检查测温仪表,热电隅是否正常,要定期进行校验;3.3.3定期清理气体渗碳炉炉罐中的碳黑和灰烬;3.4工件的表卡和试样3.4.1根据工件的形状和要求,选用适当的吊具和夹具;3.4.2工件间要有5~10mm的间隙;3.4.3应随炉放臵与装炉工件材质和予处理相同和符合GB8539—87“齿轮材料及热处理质量检验的一般规则”规则的样式,并放臵在有代表性的位臵,以备炉前操作抽样检查;4.渗碳和碳氮共渗淬火回火处理的工艺规范和操作规程4.1渗碳.碳氮共渗处理4.1.1装炉4.1.1.1工件装炉前应把炉温升到渗碳或共渗温度,连续生产时可干上一炉出炉后立即装炉;4.1.1.2工件应装在炉子的有效加热区内,加热区的炉温不得超过±15℃;4.1.1.3每炉装载量不大于设备的装载量;4.1.2气体渗碳工艺规范和操作规程4.1.2.1气体渗碳工艺规范参照图1,低碳合金渗碳钢的渗碳温度取上限;4.1.2.2排气期排气期的渗剂滴入量,参照表1,炉子到温后的排气时间的长短取决于排气程度,应取气进行分析,当CO2和O2的含量低于0.5%时,即可关闭试样孔,转入强渗期;无气体分析仪时,可观察废气火苗的颜色和状态,当火苗呈杏黄色,上升无力时,排气基本结束;一般地排气时间为1~1.5小时;4.1.2.3强渗期,关闭试样孔,点燃排出的废气;检查炉盖及通风机轴处是否漏气;调整煤油.异丙醇的滴入量,滴量多少取决于设备大小,装炉工件表面积的大小及炉子密封的情况,表1的滴量供选择时参考;强渗期炉气成份应控制在表2规则的范围内;有条件应采用红外线CO2碳位自控仪或露点仪控制炉气或用奥氏体分析仪对炉气进行分析,作为调正滴量的依据;强渗期的炉压控制在100~300pa;废气燃烧的火苗高度控制在200~250㎜的长度;根据工件有效硬化层要求和渗速经验,约达到1/2~2/3渗层深度时,抽验第一根试样,根据第一个试样的渗层确定第二个试样的时间,当有效硬化层深度达到或接近工件的有效硬化深度时,即可进入扩散期;4.1.2.4扩散期:扩散期的煤油.异丙醇滴量约为强渗期的0.5倍,为了保证炉压,并同时加滴甲醇,扩散期的时间与工件要求的有效硬化层深度有关,有效硬化层深度愈深,扩散时间要求愈长一些,与工件的碳势(试样的碳势)有关,碳势高要求扩散时间长一些,还与试样渗层深度有关,为了保证工件表面0.85~1.0%的碳浓度和合理的过滤层,扩散时间约为1~3小时;4.1.2.5降温期:抽验的第三个试样,如果网状碳化物≥5级为作正火处理,920℃出炉空冷,对20CrMnMo17Cr2Ni20CrNi2Mo当工件室冷到300-400℃时要放到回火炉中炉冷,防止在表面和次层在空冷时产生马氏体,形成表面裂纹;对于17CrNi2Mo.20Cr2NiMo等Cr.Ni渗碳钢即使碳化物不超级也要出炉空冷,空冷的炉温度为860~880℃;对于碳化物不超级的20CrMnTi.20CrMnMo~840℃,保渗碳齿轮,随炉冷到830温0.5~1H后直接淬火;4.1.3气体碳氮共渗工艺规范和操作规程;4.1.3.1气体碳氮共渗操作规程;4.1.3.2采用煤油加氨氧的气体碳氮共渗工艺曲线4.1.3.3共渗过程其炉气成分应符合下表规则4.2.1工件渗碳后直接淬火;对本质细晶粒钢工件渗碳后可采用直接淬火的方法,以获得所需要的表层和心部硬度以及有效硬化层深度,如20CrMo.20CrMnMo,以及含硼和稀土的合金钢渗碳件;直接淬火一般在炉中降温到830~850℃,均温0.5~1H出炉后淬火工件渗碳后直接淬火另一个条件是渗层金相组织网状碳化物≤4级;工件要求渗层深,炉中碳势又高的情况,容易造成碳化物超级,而对于模数≤5的20CrMnTi.20CrMnMo齿轮,渗碳深度1.2~1.3㎜(含磨量)碳化物不易超级,可以直接淬火,模数大于5的齿轮视渗层的金相组织中网状碳化物的级别而定,如果网状碳化物小于4级可以直接淬火;5级以上则要高温正火,消除网状碳化物或降低网状碳化物级别;4.2.2工件渗碳后空冷后再淬火,按方法有以下几种原因:a.工件渗碳后需要进行机械加工,如制碳层;b.容易发生过热的碳钢和非细晶粒合金钢件,以及某些不宜直接淬火的工件(如需要在压床上淬的齿轮);c.渗层组织如出现网状碳化物超级对于a.b两种情况,炉冷到850~860℃空冷,但对20CrMnMo渗件要求在400℃以下缓冷,否则易再次表层出现马氏体组织形成裂纹,对于C种情况,要求在900~930℃出炉直接空冷;4.2.312CrNi3.12Cr2Ni4.17CrNi2Mo.20CrNi4.20Cr2Ni4.20Cr2Ni4MoA.20Cr2Ni4WA等高强合金渗碳件,渗碳炉冷到920℃出炉空冷(用于制作大模数齿轮),400以下缓冷,并增加一次至二次650~680℃,5~6H的高温回火;这种高温回火称为催化或促变处理,它不仅能改善机械加工性能,更主要它是获得良好淬火组织的条件和保证;必须严格执行;4.2.4碳氮共渗的工件一般都从共渗温度或低于共渗温度出炉直接淬火;4.2.5经过渗碳淬火或碳氮共渗淬的工件,通常采用180℃±10℃的低温回火;4.2.5.1碳氮共渗齿轮回火的温度为180℃±10℃,回火时间3H;4.2.5.2模数1~3的齿轴渗碳淬火后温度200~210℃,时间3H,模数1~3的齿轮渗碳淬火后的回温度220℃±10℃,时间3H4.2.5.3模数3~5的齿轴.齿轮渗碳淬火后进行二次回火;第一次回火温度230℃,时间4H;第二次齿轴的回火温度230℃,回火时间3H;4.2.5.4模数≥6的齿轮.齿轴,渗碳后直接淬火的工件,需要进行三次回火;第一次回火温度230℃,回火时间3H;第二次回火,齿轴的回火温度230℃,时间3H,齿轮的回火温度240℃,时间3H;第三次回火,齿轴的回火温度220℃,时间3H,齿轮的回火温度240℃,时间3H;4.2.5.5模数≥6的齿轮齿轴渗碳后空冷,后加热淬火;进行二次回火;第一次回火温度230℃,时间4H;第二次回火,齿轴的回火温度220℃,时间4H,齿轮的回火温度240℃,时间4H;4.2.5.6前一次回火后,工件空冷到室温或≤50℃,才能进行下一次回火;4.2.5.7工件回火必须放在回火炉的有效加热区内(渗碳淬火的齿轮部分需量出回火炉底部300㎜);4.3渗碳和碳氮共渗淬火回火件的最后处理;4.3.1清理:进行喷砂,以清除赤面的油污和氧化模;4.3.2校直和矫正:用偏摆仪检查齿轴的变形,当超过允许变形时,应对其校直和矫正;随后进行去应力回火;条件允许(淬火工件量少时)应在淬火后马上进行校直,然后再回火;5.质量检验5.1外观:不得有裂纹和碰伤5.2表面硬度5.2.1硬度检验方法,按GB23083《金属洛氏硬试验法》或其他硬度试验法进行;5.2.2表面硬度的偏差范围,表面硬度不得超过下表规则:5.3.1有效硬化层检验方法,按GB《钢的渗碳硬化层有效硬化层深度的测定和校验》中的规则执行;5.3.2有效硬化层深度偏差不得超过下表规则;根据零件的要求,按有关标准进行检定;5.5变形:零件的变形应符合技术要求;6.安全与环保6.1操作者要穿戴好必须的劳动保护用品;6.2执行所用设备的安全操作规程;6.3气体渗碳或碳氮共渗出炉淬火时,同时淬火的工件量大时,应先检查油温,当油温>100℃时,应先降油温后淬火,以防止油槽着火;着火时需用灭火器,石棉被灭火,严禁用水灭火;6.4要防止渗碳炉滴注器渗漏,以免引起炉盖着火,烧毁电机或造成渗剂失火;6.5其它方面按GB15735—1995,金属热处理生产过程安全卫生要求;。
中国古代的钢铁渗碳和渗氮技术汇总
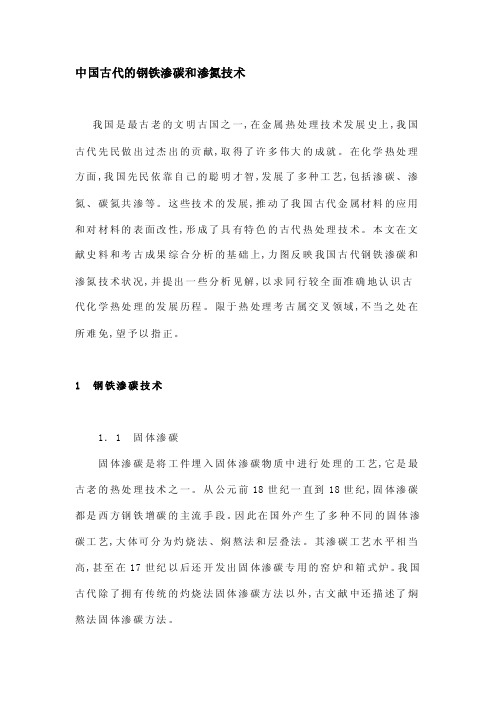
中国古代的钢铁渗碳和渗氮技术我国是最古老的文明古国之一,在金属热处理技术发展史上,我国古代先民做出过杰出的贡献,取得了许多伟大的成就。
在化学热处理方面,我国先民依靠自己的聪明才智,发展了多种工艺,包括渗碳、渗氮、碳氮共渗等。
这些技术的发展,推动了我国古代金属材料的应用和对材料的表面改性,形成了具有特色的古代热处理技术。
本文在文献史料和考古成果综合分析的基础上,力图反映我国古代钢铁渗碳和渗氮技术状况,并提出一些分析见解,以求同行较全面准确地认识古代化学热处理的发展历程。
限于热处理考古属交叉领域,不当之处在所难免,望予以指正。
1钢铁渗碳技术1.1 固体渗碳固体渗碳是将工件埋入固体渗碳物质中进行处理的工艺,它是最古老的热处理技术之一。
从公元前18世纪一直到18世纪,固体渗碳都是西方钢铁增碳的主流手段。
因此在国外产生了多种不同的固体渗碳工艺,大体可分为灼烧法、焖熬法和层叠法。
其渗碳工艺水平相当高,甚至在17世纪以后还开发出固体渗碳专用的窑炉和箱式炉。
我国古代除了拥有传统的灼烧法固体渗碳方法以外,古文献中还描述了焖熬法固体渗碳方法。
1.1.1 灼烧法固体渗碳一般认为人工冶铁的发源地是两河流域北部、土耳其及其附近地区。
该地有很多的铁矿,而铜矿又较少。
在靠近土耳其的Cha nga r Ba zar镇出土的匕首柄,其年代可定为公元前2700年以前。
而根据报道,在Giz eh的大金字塔内遗存一块铁板,使人工冶炼金属铁板的年代提前到公元前2761年以前。
这些人工冶铁器件是将铁矿石还原后经锻接的产物。
人工冶铁的初级产品是海绵铁,它是由铁矿石在约1200℃的木炭火的温度下还原出来的,海绵铁是杂质含量很高的松散、柔软的金属块,其杂质主要有未还原的氧化铁、铁橄榄石、木炭粉等,为了用它制作器物,只有将其反复加热锻打、去渣、聚块、分散杂质后,才能获得可以造型的熟铁,这种熟铁通常被称为块炼铁。
海绵铁的加热往往是在灼热的木炭中进行,其时铁被埋在木炭之间,在铁的作用下,未完全燃烧的一氧化碳发生分解,分解的活性碳形成高的碳势,铁在碳势气氛中,自然而然地被渗碳。
低温化学热处理方法——氮碳共渗
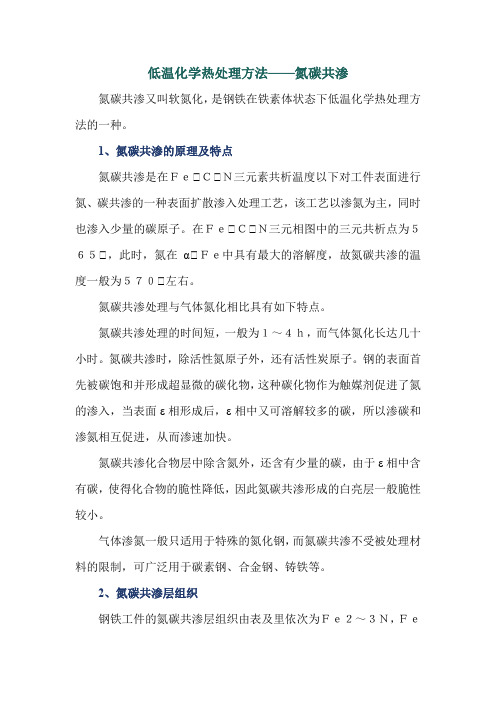
低温化学热处理方法——氮碳共渗氮碳共渗又叫软氮化,是钢铁在铁素体状态下低温化学热处理方法的一种。
1、氮碳共渗的原理及特点氮碳共渗是在Fe⁃C⁃N三元素共析温度以下对工件表面进行氮、碳共渗的一种表面扩散渗入处理工艺,该工艺以渗氮为主,同时也渗入少量的碳原子。
在Fe⁃C⁃N三元相图中的三元共析点为565⁃,此时,氮在α⁃Fe中具有最大的溶解度,故氮碳共渗的温度一般为570⁃左右。
氮碳共渗处理与气体氮化相比具有如下特点。
氮碳共渗处理的时间短,一般为1~4h,而气体氮化长达几十小时。
氮碳共渗时,除活性氮原子外,还有活性炭原子。
钢的表面首先被碳饱和并形成超显微的碳化物,这种碳化物作为触媒剂促进了氮的渗入,当表面ε相形成后,ε相中又可溶解较多的碳,所以渗碳和渗氮相互促进,从而渗速加快。
氮碳共渗化合物层中除含氮外,还含有少量的碳,由于ε相中含有碳,使得化合物的脆性降低,因此氮碳共渗形成的白亮层一般脆性较小。
气体渗氮一般只适用于特殊的氮化钢,而氮碳共渗不受被处理材料的限制,可广泛用于碳素钢、合金钢、铸铁等。
2、氮碳共渗层组织钢铁工件的氮碳共渗层组织由表及里依次为Fe2~3N,Fe3N和Fe4N构成的化合物层(如是合金钢,还有Cr、W、V、Al、Mo等合金氮化物)和扩散层(主要是氮在α⁃Fe中的固溶体)。
碳钢氮碳共渗后的组织由白亮的化合物层和暗黑色的扩散层组成。
化合物层主要为ε相和γ′相。
合金钢氮碳共渗后,表面也得到由ε相和γ′相组成的白亮化合物层。
3、氮碳共渗层性能(1)共渗层硬度氮碳共渗显著提高工件表面硬度及耐磨性,与调质、感应淬火相比较,磨损失重分别降低1~2个数量级。
(2)共渗层的抗疲劳性能氮碳共渗后的疲劳强度高于渗碳或碳氮共渗淬火以及感应淬火。
低、中碳钢可提高40%~80%;合金结构钢提高25%~35%;不锈钢提高30%~40%;灰铸铁提高20%左右,见下图。
▲氮碳共渗处理使疲劳强度提高的情况(球墨铸铁)最近采取在氮碳共渗后高频淬火的复合热处理工艺。
表面渗碳处理的作用
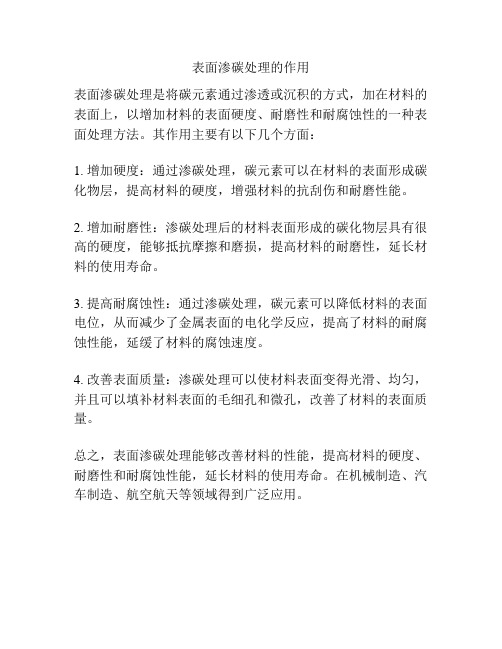
表面渗碳处理的作用
表面渗碳处理是将碳元素通过渗透或沉积的方式,加在材料的表面上,以增加材料的表面硬度、耐磨性和耐腐蚀性的一种表面处理方法。
其作用主要有以下几个方面:
1. 增加硬度:通过渗碳处理,碳元素可以在材料的表面形成碳化物层,提高材料的硬度,增强材料的抗刮伤和耐磨性能。
2. 增加耐磨性:渗碳处理后的材料表面形成的碳化物层具有很高的硬度,能够抵抗摩擦和磨损,提高材料的耐磨性,延长材料的使用寿命。
3. 提高耐腐蚀性:通过渗碳处理,碳元素可以降低材料的表面电位,从而减少了金属表面的电化学反应,提高了材料的耐腐蚀性能,延缓了材料的腐蚀速度。
4. 改善表面质量:渗碳处理可以使材料表面变得光滑、均匀,并且可以填补材料表面的毛细孔和微孔,改善了材料的表面质量。
总之,表面渗碳处理能够改善材料的性能,提高材料的硬度、耐磨性和耐腐蚀性能,延长材料的使用寿命。
在机械制造、汽车制造、航空航天等领域得到广泛应用。
- 1、下载文档前请自行甄别文档内容的完整性,平台不提供额外的编辑、内容补充、找答案等附加服务。
- 2、"仅部分预览"的文档,不可在线预览部分如存在完整性等问题,可反馈申请退款(可完整预览的文档不适用该条件!)。
- 3、如文档侵犯您的权益,请联系客服反馈,我们会尽快为您处理(人工客服工作时间:9:00-18:30)。
用 于耐碳 酸 、 化镁 、 酸 钡 和 硫 酸钠 等 介 质 的防 氯 硫 腐 蚀 。 日本 为 增 加 混 凝 土 结 构 强 度 , 少 海 水 侵 减
蚀, 在金属 构件表 面采用 铝 、 、 、 、 、 、 和 硅 钛 钼 锌 铬 锆
绍了铝钼共渗钢 的抗 高温硫 、 环烷酸的性能和铝钛共渗钢 的耐湿硫化 氢腐蚀的性 能 以及 两者的焊接 性 能, 阐述 了共渗钢的工业应 用情况和应 用范围。并对共渗钢 未来的推广应用作 了展 能 工 业 应 用
中图 分 类 号 :G 5. T 168
第2 7卷
伊轻 等中东含硫 原油 的 中国石 化 镇海 炼 油化 工股
份有 限公 司 8Mta Ⅲ套常 减压 蒸馏 装置 的 多部 /第 位挂 片 , 试验 时 间 为 2 0 0 1年 3月 至 2 0 0 3年 3月。 铝钼共渗 钢 、 渗铝 钢在高 温段与低 温段 的耐蚀性 能 有较大 的差异 , 图 4 见 。温度 在 2 0c 5 c以上 改性材
面制备钛 化合物涂 层 , 钢铁 增加 防腐蚀 性 。德 国 使 采 用钼 、 、 和硼 的多元粉 末共 渗技术 , 钛 铬 其共 渗钢
渗 金属就是 采用 加热扩散 的方法 , 一种或 多 使
种金属 渗入工 件表 面 , 成表 面合 金层 , 形 成 的 形 所
表面合 金层通 常称为 渗层或扩散 渗层 J 。 渗 金属和 电镀 、 喷镀 、 化学镀 等一样 , 都是在 金
蚀等性 能 。在共 渗 技 术 中 即使 采 用 性 能优 异 的贵
重、 稀有元素 , 也不会显著提高成本 , 具有较高的技 术 经 济价 值 。
2 国内外研 究共渗 技术 的概 况
2 1 国外情 况 .
了二种或多种元素 的共渗层 。多 元元素共渗 不但 能
充分发挥单一元素 的各 自优点 , 弥补其缺 点 , 而且还 可 以赋予金属材料表面以新 的更好的性能 , 该文 主 要对包埋共渗金属技术 和应用进行探讨 。
件 , 目前技术 也未 能对共 渗过 程提 供一种 廉价有 而
效 的防止渗剂 及 构 件 氧化 的方 法 。进行 工 业 化生
产 的较少 。某磷 肥 厂 开 发 的一 种 对 铜 或铜 合 金制 的高炉风 口或 渣 口铬 、 、 或 其 合 金粉 末 多元 金 钼 钨
收 稿 日期 :0 0— 3—1 ; 稿 日期 :0 0— 9— 1 21 0 5修 21 0 2 。
根据所渗元 素 , 金属法 又可分为单 元渗 和多元共 渗 渗 。渗入一 种元素 的称 为单 元渗 ; 同时或顺序 渗入
两种或两种 以上 的元 素 的扩 散过程 , 达到所要 求 的
国内对钢铁构件共渗工艺方法研究不多, 共渗
工艺处 于实验 室研 究 阶段 或 只 能处 理 小尺 寸 的工
表面合 金层 , 为 二元 或 多元共 渗 。 目前 , 称 应用 较 多的单元 渗有 : 渗铝 、 铬 、 钛 、 硅 、 渗 渗 渗 渗硼 等 ; 二 元共 渗 有 : 铬 共渗 、 钛共 渗 、 硅共 渗 、 铝 铝 铝 硼铝 共 渗、 铬硼共渗 等 。多 元共渗 的研 究方法 大多数采 用 的是 固体粉 末 包 渗 法 _ 。根据 渗 人 金 属 的 不 同 , 4 J
文献标识 码 : A
文章 编号 : 0 05 2 L)6 05 0 1 7— 1X(OOO - 02— 5 0
金属表面保护 防腐蚀 技术 在防腐 蚀领域起着 十
分重要 的作用 。随着科学技术和工业 的发展 , 对金属 材料表面 l 生能的要求越来越高 , 原来渗人单一元素所 得的渗层 已不能完全满足要求 , 因而国内外陆续发展
殛 碳 钢 表 面 共 渗 金 属 技 术 及 应 用
一 一
盛长松 李选亭 晁君瑞 刘文 亮
( 中国石化集 团洛 阳石油化工工程公 司 , 河南 洛 阳 4 10 ) 7 03
摘要 : 对碳钢表面共渗金属的特点和方 法及 国内外共渗金 属的研 究进展 情况作 了简要介 绍。介
可 以在 同一种 材料 的表面获 得不 同的组织和性 能 , 作者简介 : 盛长松, 高级工程师 , 毕业于抚顺石油学院炼油化工 使材 料表面具 有优 良的 耐高 温 氧化 、 耐磨 损 、 耐腐 机械专业 , 一直从事石油化工设备防腐蚀 的研究和开发工作。
第6 期
・
5 4・
石 油 化 工腐 蚀 与 防护
成本 较高 , 不适宜 实 现 大规 模 工 业 化 生产 , 产 品 且
渗 金属 的方 法 按热 处理 时所 用渗 入元 素 介质
较难 推广 。有些技 术处理 的渗 层较 薄 , 恶劣 环 对在 境下 工作 的金属构 件难 以起 到足够 的保 护作用 。 2 2 国 内情 况 .
的物理状态可分为: 固体渗、 液体渗和气体渗三种。
结合 为冶金结合 , 因此 渗金 属 比电镀 、 化学 镀 等方 法所形成 的镀层 更 牢 固 , 易脱 落 , 其它 镀 覆方 不 是
法难 以媲美 的 。
镍 等粉末共 渗或 渗 钼 , 层 厚 度 为 3~ 0p 涂 5 . m。以 上技 术共渗 剂基本 都采用 价格 较贵 的纯金 属粉末 ,
1 碳钢表面 共渗 金属 的特 点和方 法
前 苏联采 用铬 、 、 钼 四溴 化 锆 等 复合 物 处理 钢 铁 机械 和设备 中 的部 件 , 以增 加 防腐 蚀 性 能 , 长 延 使 用寿命 , 减少脆 性 。采用 钼 、 、 钛 硅对 钢材共渗 处 理, 用于化 工或航 天器设 备 的高温 防腐 。在钢铁 表
应 用 技 术
.
C o i 化oe t n腐 to 与a n 护 石r so & Pr t工o er c e 防u ty 油 蚀h mi l d sr o r n ci i P n c I
2 1 0 , 2 0 7 ( 6 ) ・ 5 2 ・
一 综一