深孔钻削切屑形态的研究
浅析机械加工过程中的深孔加工方法

浅析机械加工过程中的深孔加工方法发布时间:2021-11-15T08:50:10.463Z 来源:《科学与技术》2021年8月23期作者:齐宇杨若森[导读] 现阶段我国科学技术发展水平的提升,对机械加工制造产生了积极影响,逐渐扩大了其产业规模。
齐宇杨若森长城汽车股份有限公司天津哈弗分公司天津市 300000摘要:现阶段我国科学技术发展水平的提升,对机械加工制造产生了积极影响,逐渐扩大了其产业规模。
实践中为了使机械加工效果更加显著,增加深孔加工中的技术含量,则需要考虑与之相关的加工技术使用,落实好具体的研究工作,确保深孔加工状况良好性,为机械加工行业的可持续发展提供专业支持。
基于此,本文将对机械加工作用下的深孔加工技术进行系统阐述。
关键词:机械加工;深孔加工;技术1、深孔处理技术的技术特征1.1深孔加工技术很困难首先,大多数深孔加工是在半封闭或完全封闭的环境中进行的,因此无法直接观察到诸如加工,切削和切削之类的操作人员。
因为孔的半径与深度之间的比率较大,所以它会排干金属屑并使孔难以堵塞。
毕竟,如果钻头太长,则会出现严重降低钻头刚性的问题。
由于孔偏移或抖动等问题,难以有效地保证深孔加工的精度,并且由于孔加工的散热问题,在封闭环境下,由于孔的温度升高,钻头可能会磨损。
1.2锻炼方法本身很特殊在深孔加工的整个过程中,可以通过多种方式来操作工件和刀具,其中工件旋转并且刀具同时进给。
固定工件并同时进给刀具。
选择多种运动方法,例如定向进给,是使用深孔加工技术的主要挑战之一。
1.3深孔加工中的排屑问题深孔加工中的排屑问题是要重点解决的问题之一,排屑方法主要分为两种。
首先是外部排屑。
将冷却液倒入岩心钻杆中以清除切屑。
切割区域已清洁。
第二个是去除内部切屑,将其倒入钻杆的孔和外壁中以从切削区域去除切屑。
在实际的加工过程中,内部排屑处理方法通常是优选的,因为该方法不会引起孔壁的二次摩擦,并且钻杆的高刚度不会影响孔的表面质量。
深孔加工简介

2.喷吸钻
喷吸钻是一种新型的内排屑深孔钻,主要用于加工直径18~ 180mm、深径比在100以内的深孔。加工精度为IT10~IT7,表面 粗糙度Ra3.2~0.8μm,孔的直线度可达0.1mm/1000mm。
(1)喷吸钻的结构
喷吸钻的组成结构
喷吸钻钻头结构
(2)喷吸钻的工作原理 喷吸钻利用液体的喷吸效应实现冷却排屑。即当高压
➢有利于分屑和排屑,可使径向分力得到较合理的平 衡,减少导向支承块上的支承力。
➢刀齿也可根据受力情况和切削条件不同,选用不同 的刀具材料。
错齿内排屑深孔钻的工作原理
一、深孔加工的特点
➢深孔加工时,刀杆细长,刚性差。 ➢切削液难以引入到切削区,切屑不易排出,钻尖冷却困难。 ➢切削刃上各点的切削速度变化较大,尤其是近中心处的切 削速度为零,切削条件差。 ➢转矩和轴向力大,钻进困难,且易引偏,致使刀具耐用度 及生产率很低。
二、深孔钻
(1)按切削刃的多少分 ➢单刃 ➢多刃
流体经过一个狭小的通道高速喷射时,在这股喷射流的周 围形成了低压区,将喷嘴附近的流体吸走。
3.错齿内排屑深孔钻(高压内排屑钻)
错齿内排屑钻由钻头和钻杆两部分组成。 用途:加工直径60mm以上、深径比在100以内的深孔。 加工精度为IT9 ~IT7,表面粗糙度为Ra6.3~1.6μm。
ห้องสมุดไป่ตู้
结构特点:切削刃成交错排列,刀具上无横刃。 优点:
(2)按深孔钻的排屑方式分 ➢内排屑 ➢外排屑
常用的深孔钻有枪孔钻、喷吸钻和高压内排屑钻。
1.枪孔钻
概念:枪孔钻是单刃外排屑深孔钻,因最早用于加工枪 管而得名。
特点:仅在轴线的一侧有切削刃,没有横刃,并分为外 刃和内刃两段,使切出的切屑短小,便于排屑。
基于机械加工的深孔加工技术探析
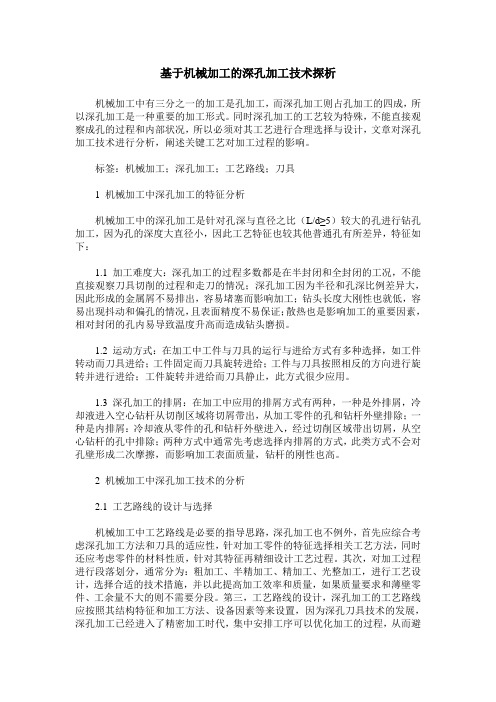
基于机械加工的深孔加工技术探析机械加工中有三分之一的加工是孔加工,而深孔加工则占孔加工的四成,所以深孔加工是一种重要的加工形式。
同时深孔加工的工艺较为特殊,不能直接观察成孔的过程和内部状况,所以必须对其工艺进行合理选择与设计,文章对深孔加工技术进行分析,阐述关键工艺对加工过程的影响。
标签:机械加工;深孔加工;工艺路线;刀具1 机械加工中深孔加工的特征分析机械加工中的深孔加工是针对孔深与直径之比(L/d≥5)较大的孔进行钻孔加工,因为孔的深度大直径小,因此工艺特征也较其他普通孔有所差异,特征如下:1.1 加工难度大:深孔加工的过程多数都是在半封闭和全封闭的工况,不能直接观察刀具切削的过程和走刀的情况;深孔加工因为半径和孔深比例差异大,因此形成的金属屑不易排出,容易堵塞而影响加工;钻头长度大刚性也就低,容易出现抖动和偏孔的情况,且表面精度不易保证;散热也是影响加工的重要因素,相对封闭的孔内易导致温度升高而造成钻头磨损。
1.2 运动方式:在加工中工件与刀具的运行与进给方式有多种选择,如工件转动而刀具进给;工件固定而刀具旋转进给;工件与刀具按照相反的方向进行旋转并进行进给;工件旋转并进给而刀具静止,此方式很少应用。
1.3 深孔加工的排屑:在加工中应用的排屑方式有两种,一种是外排屑,冷却液进入空心钻杆从切削区域将切屑带出,从加工零件的孔和钻杆外壁排除;一种是内排屑:冷却液从零件的孔和钻杆外壁进入,经过切削区域带出切屑,从空心钻杆的孔中排除;两种方式中通常先考虑选择内排屑的方式,此类方式不会对孔壁形成二次摩擦,而影响加工表面质量,钻杆的刚性也高。
2 机械加工中深孔加工技术的分析2.1 工艺路线的设计与选择机械加工中工艺路线是必要的指导思路,深孔加工也不例外,首先应综合考虑深孔加工方法和刀具的适应性,针对加工零件的特征选择相关工艺方法,同时还应考虑零件的材料性质,针对其特征再精细设计工艺过程。
其次,对加工过程进行段落划分,通常分为:粗加工、半精加工、精加工、光整加工,进行工艺设计,选择合适的技术措施,并以此提高加工效率和质量,如果质量要求和薄壁零件、工余量不大的则不需要分段。
关于深孔钻削加工时若干问题的探讨

关于深孔钻削加工时若干问题的探讨作者:赵玉梅来源:《硅谷》2009年第17期[摘要]提出深孔加工过程中出现的一些技术问题,并对这些问题的解决方案做详细论述,对深孔钻削加工技术的完善具有一定的指导意义。
[关键词]深孔钻钻削钻削速度切削液中图分类号:TH6文献标识码:A文章编号:1671-7597(2009)0910090-01最近几年国内深孔钻发展很快。
但由于深孔钻削还有一些关键技术问题尚未解决,使深孔钻削仍属于金属切削加工的“瓶颈”工序。
笔者根据实践经验,仅就深孔钻削中的几个问题提出几点意见。
一、深孔钻削中的断屑问题对于深孔钻头,目前主要的断屑方法有两个:(1)合理的设计刀具角度和断屑槽;(2)合理的选择钻削进给量S和钻削速度V。
合理的刀具角度就是在钻切削力允许的情况下,应尽可能使切屑塑性变形大,造成硬化,为其折断提供条件。
断屑槽的作用在于强迫切屑弯曲、折断。
对于错齿式硬质合金深孔钻头,其常见的典型形状是:前角γ:边刃、中间刃为0~2°,中间刃在靠近内角的中心处磨成负角,一般为-3°~-10°,其作用在于增加中间刃的强度及帮助分屑。
后角:一般为8°~10°,内刀刃处的后角为12°~14°。
对于高速钢双刃口无横刃深孔钻头,与错齿式硬质合金深孔钻头不同,其形状如下:前角γ一般为10°~12°,主后角一般为10°~14°,两切削刃交错开有分屑槽。
这种钻头两内刀刃必须磨有足够的后角,否则轴向力特大,甚至无法钻削。
其后角一般为16°~18°, 对于同样几何形状的深孔钻头,选用不同钻削进给量S,其断屑情况也就不同。
当断屑不良时,一般采用加大钻削进给量S 的办法,其目的在于使切屑变厚,与断屑槽相碰时产生较大应力,促使切屑折断。
但这种方法不能过分加大S,以免切削力过大而损坏刀具或“闷车”。
小口径深孔钻削切屑形成及控制
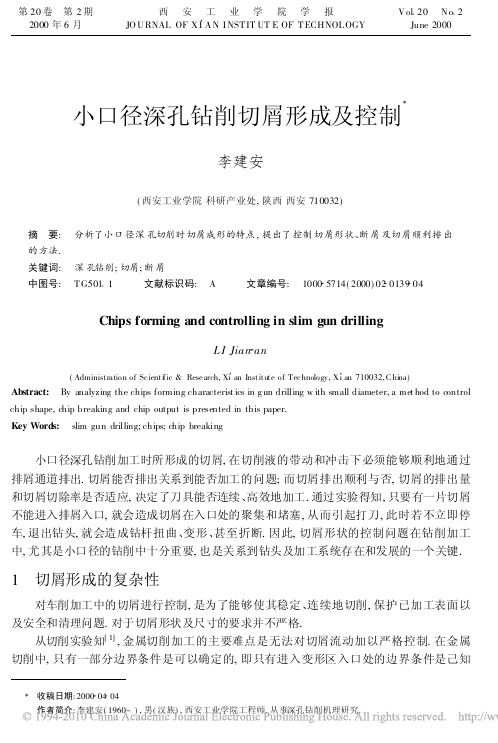
第20卷 第2期 西 安 工 业 学 院 学 报 V ol 20 N o 2 2000年6月 JO U RNAL OF X I A N I NST IT UT E OF T ECHNOL OGY June2000小口径深孔钻削切屑形成及控制李建安(西安工业学院科研产业处,陕西西安710032)摘 要: 分析了小口径深孔切削时切屑成形的特点,提出了控制切屑形状、断屑及切屑顺利排出的方法.关键词: 深孔钻削;切屑;断屑中图号: T G501 1 文献标识码: A 文章编号: 1000 5714(2000)02 0139 04Chips forming and controlling in slim gun drillingL I Jian an(Administration of Scienti fic&Research,Xi an Institute of Technology,Xi an710032,C hi na)Abstract: By analyzing the chips forming characterist ics in g un drilling w ith small diameter,a met hod to control chip shape,chip breaking and chip output is presented in this paper.Key Words: slim gun drilling;chips;chip breaking小口径深孔钻削加工时所形成的切屑,在切削液的带动和冲击下必须能够顺利地通过排屑通道排出.切屑能否排出关系到能否加工的问题;而切屑排出顺利与否,切屑的排出量和切屑切除率是否适应,决定了刀具能否连续、高效地加工.通过实验得知,只要有一片切屑不能进入排屑入口,就会造成切屑在入口处的聚集和堵塞,从而引起打刀,此时若不立即停车,退出钻头,就会造成钻杆扭曲、变形、甚至折断.因此,切屑形状的控制问题在钻削加工中,尤其是小口径的钻削中十分重要,也是关系到钻头及加工系统存在和发展的一个关键.1 切屑形成的复杂性对车削加工中的切屑进行控制,是为了能够使其稳定、连续地切削,保护已加工表面以及安全和清理问题.对于切屑形状及尺寸的要求并不严格.从切削实验知[1],金属切削加工的主要难点是无法对切屑流动加以严格控制.在金属切削中,只有一部分边界条件是可以确定的,即只有进入变形区入口处的边界条件是己知收稿日期:2000 04 04作者简介:李建安(1960-),男(汉族),西安工业学院工程师,从事深孔钻削机理研究.的,其余的边界条件都是未知的,甚至连边界本身也无法确定.这就是切削过程无法用解析法得出切屑形成、流动的解析解的原因.据同一资料可知:在切削加工中,当切削条件不变时,实验测出的切削力和切屑厚度往往有较大出入,其变化可达40%左右.切削加工中对切屑形成及切屑形状的影响因素很多,并且很复杂,影响结果也相当大.在实际加工中,许多不稳定的因素如刀具的磨损、工件材料的不均匀性及机床的动态特性都会导致切屑形状的改变.而对于不同的刀具刃型、材料以及不同的加工参数,其切屑形状的差异就更大.因此,切屑形成的因素错综复杂,如果不经过预先试验,一般很难准确的测出切屑的形状.但是,切削过程与切屑形成有其本身的规律,当切削条件在一定范围内变更时,切屑形状的变化有一定规律可循.切削加工实践及研究证明,使切屑的形状控制在一定的允许范围内是能够做到的.2 钻削中切屑形成的特点如前所述,在钻削加工中,切削过程和切屑形成沿刃向差异极大.切削速度沿径向从边刃的名义切削速度直到中心接近于零速,以及在中心处为负前角,决定了切屑变形沿径向是不同的.我们知道,切屑金属晶粒在其宽度方向上的速度不同,这就使得切屑流过前刀面时发生旋转.也就是说,在钻削加工中,切屑发生了侧向卷曲.研究表明,从切屑流出速度与剪切角间满足v h =v c sin cos=v c tan (1)其中,v h 为切屑速度;v c 为切削速度; 为剪切角,其表达式为 = 4- +!(2)式中, 为切屑与刀具前刀面间的摩擦角;!为刀具前角.由(1)式可知:v c 、 二个变量中有一个变化,切屑速度v h 沿刃向变化极大.(2)式表明,由于 随切削速度的降低而减少,而在内刃处前角!为负值,但他们的影响较小.即v h 主要受v c 的影响.因此,其切屑速度沿刃向变化相当大,在中心处也接近零.这样,由于切屑沿刃向差异极大,沿刃向就要采用不同的处理方式加以控制.在接近心部处,即中心刃或内刃处,由于切削速度及切屑速度很低,刀具又为负前角,因此剪切角很小,切屑变形很大,切屑的硬化程度就比较严重.而由于此处沿刃向切屑速度差异很大、沿垂直方向单位时间内切屑流出长度不同.因此,在流动过程中相互制约,会产生很大的内应力,切屑比较容易折断.外刃处的切削速度高,切屑变形小,生成的切屑韧性较大,不易折断.因此,对于钻头,切屑控制主要在外刃处.3 钻削中切屑控制方式及特点用直径16m m 的单刃钻头和直径12mm 的单刃和错齿钻头分别进行了实验加工.为了切屑能够顺利地通过他们本身不大的排屑入口,就需要使切屑在其切削宽度上分开,从而使切屑宽度减少.从切屑断面强度考虑,分屑也有利于切屑的进一步卷曲、变形和折断.从实验中知道过宽的切屑是不易从排屑口排出的.对于小口径钻头,其排屑入口由于其尺寸及结140 西 安 工 业 学 院 学 报 第20卷构的限制面很小.实验表明,按照一般设计的刀具结构,只要切屑能顺利地进入排屑入口,就可以顺利地通过钻杆内孔而排出.因此,切屑形状及尺寸的控制主要按其排屑入口的大小和进屑能力而确定.钻削中,一般都是采用断屑台来控制切屑的卷曲与折断,即所谓切屑的附加变形.而在小口径深孔钻削加工中,断屑台与进给量的匹配关系与一般的切削加工的规律及应用范围有所不同.由于在一般的切削加工中进给量较大,因而切屑变形大、厚度大,截面强度也就高,所以,对于断屑台要求的强制卷曲作用很大.而在小口径钻削加工中,切削深度大,刀杆强度低、刚度弱,排屑通道小,不能采用像车削及大口径钻削加工那样大的进给量.从各国目前应用情况看,直径16mm 以下的钻头,其进给量都小于0.1mm/r,大部分使用的进给量为0.02~0.08m m/r.这样,切屑厚度小,相应的进给量与断屑台的匹配关系也就会发生一些变化.实验中发现,进给量与断屑台的关系应比一般推荐的车削中B =8-12f 的比例大一些.这是由于切屑厚度小,截面的强度低,对断屑台的附加作用要求也就小一些.从实验中对材料及变形的分析可知:对于超过了一确定值并在一定范围内变化的进给量值,对于某一被加工材料,有一个相对应的断屑台宽度和高度值范围,在此条件下所得到的切屑就会折断.进给量小于此值,切屑就成为带状屑,即在小于这个进给量值时,进一步减小断屑台宽度,也无法使切屑折断.这一现象说明,在进给量较小时,切屑变形小,硬化程度低、厚度薄,一般的附加变形是无法使其硬化到足以折断的程度的,并且由于切屑薄、横截面小,切屑呈现出较大的弹性,从而不易产生塑性变形.从切屑流出时的变形及受力状态也可以知道,由于切屑薄、切屑上下层流出时的速度差小,内应力也就比较小,流出后卷曲小、硬化程度低,从而不易折断.由此得出,对于一定的材料,一般存在有一个可以用断屑台控制其切屑折断的初始折断进给量,而这个进给量值依不同材质情况而有很大差异.在切削过程中,一般来说切屑是否容易折断,首先是由工件材料的力学性质决定的.控制切屑变形也就是控制切屑的硬度和塑性,使其硬化而达到强度极限,从而易于折断,并且只有在切削变形中产生了一定程度的硬化后,才有可能通过进一步设置障碍使其得到附加变形.如果基本变形量不充分,切屑就呈现出较大的弹性,当它经过断屑台时达不到应有的塑性变形,从而无法折断.由于小口径深孔钻削加工切屑的变形空间很小,其横截面积一般只是钻头截面的1/3~1/4,因此,它与一般外表面加工的切屑流出情况大不相同,就是同一般大口径孔加工的切屑流动也不相同.由于狭窄空间的限制,切屑流动中受到了刀具结构、被加工孔的孔底与孔壁、孔壁孔底与刀具的相对转动等因素的强烈干扰.在单刃钻头中,由于设置了分屑台,切屑沿径向的差异,切屑流出角与切削刃的角度不同,在切屑经受了断屑台的卷曲之后,就会相互碰撞、冲击或挤压而进一步产生变形.这一点从直径12mm 单刃与错齿钻头切削中的相互比较就可以看出.在钻削条件相同的情况下,单刃钻头的切屑比较容易折断,而错齿刀具的切屑,尤其是中间刃处的切屑就不易折断.在钻削初始阶段,切削预钻孔时,切削深度大约为直径2m m 的情况下所得到的是带状切屑,而一旦完全切入工件,切屑就会折断.这些结果与切屑之间的相互干扰关系密切.实验还可以看到,对于韧性、塑性较大的材料,当钻削直径很小时,由于采用的进给量比141第2期 李建安:小口径深孔钻削切屑形成及控制较小,切屑不容易折断,而一旦折断,由于其尺寸比较大,不易或无法顺利排出,常常产生堵塞而造成事故.在这种情况下,通过减小进给量,得到较薄的带状切屑.这种切屑的弹性、韧性较大,很容易在高速流动的冷却液冲击下变形,从而顺利排出.参考文献:[1] [美]P.Deuhurst 编.断屑装置对切削加工力学的影响.1992[2] [美]霍尔登丁 斯温哈特.深孔加工[M ].北京:国防工业出版社,1986142 西 安 工 业 学 院 学 报 第20卷。
深孔金属切削原理与刀具材料的选择优化

深孔金属切削原理与刀具材料的选择优化深孔金属加工作为一种高精度、高效率的加工方式,广泛应用于航空航天、军工、汽车制造等领域。
在深孔金属切削过程中,选择合适的刀具材料对于工件加工质量和切削效率至关重要。
本文将对深孔金属切削原理和刀具材料的选择进行探讨和优化建议。
一、深孔金属切削原理深孔金属切削是通过旋转刀具快速移动并与工件相对运动,从工件表面切削掉一定厚度的金属材料,以达到加工尺寸和精度的要求。
深孔切削过程中要解决的主要问题包括切削力的控制、热量的扩散与排出,以及刀具磨损等。
1. 切削力的控制深孔金属切削过程中,切削力的控制是非常重要的。
过大的切削力会导致刀具断裂、切削表面质量下降以及对工件的损坏。
切削力主要由刀具几何参数、刀具材料、切削速度和切削深度等因素决定。
对于深孔加工,刀具的几何参数应合理设计,减小切削角度和主偏角,以降低切削力。
2. 热量的扩散与排出切削过程中产生的热量需要及时扩散和排出,以避免过高温度引发刀具和工件的变形及损坏。
深孔切削过程中,可以通过采用内冷却方法来降低热量的积累。
内冷却可以利用内腔加工的空间,通过内部喷冷剂的喷射来实现热量的迅速扩散和排出。
3. 刀具磨损由于深孔切削加工的特殊性,使得刀具容易受到磨损的影响。
刀具磨损不仅会降低切削质量,还会影响切削力和切削温度。
因此,选择具有良好耐磨性能的刀具材料是关键。
下面将着重探讨刀具材料的选择优化。
二、刀具材料的选择优化刀具材料的选择对深孔金属切削的效果和刀具寿命有着重要的影响。
根据加工材料的不同,选择合适的刀具材料可以提高切削质量、降低切削力、延长刀具寿命。
下面将介绍几种常用的刀具材料及其特点。
1. 碳化钨(WC)碳化钨是一种常用的刀具材料。
它具有高硬度、高强度、耐高温、耐磨损等特点。
在高温高速切削加工中,碳化钨刀具能够保持较长的切削时间,减少切削力和磨损。
2. 氮化钛(TiN)涂层材料氮化钛涂层材料是在刀具表面涂层一层薄膜。
深孔钻原理
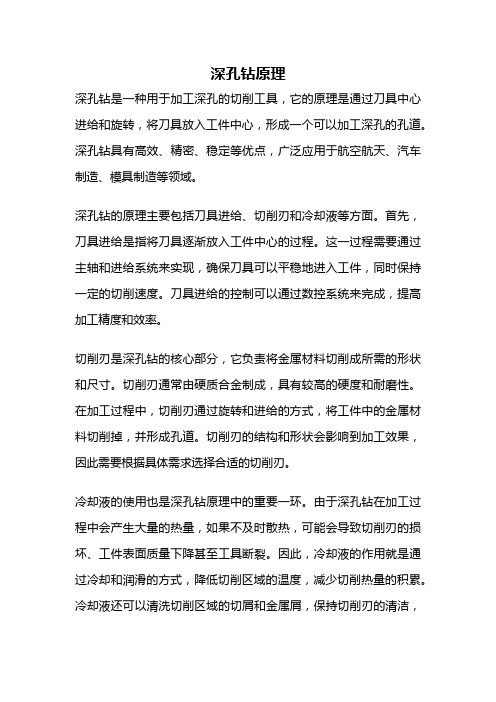
深孔钻原理深孔钻是一种用于加工深孔的切削工具,它的原理是通过刀具中心进给和旋转,将刀具放入工件中心,形成一个可以加工深孔的孔道。
深孔钻具有高效、精密、稳定等优点,广泛应用于航空航天、汽车制造、模具制造等领域。
深孔钻的原理主要包括刀具进给、切削刃和冷却液等方面。
首先,刀具进给是指将刀具逐渐放入工件中心的过程。
这一过程需要通过主轴和进给系统来实现,确保刀具可以平稳地进入工件,同时保持一定的切削速度。
刀具进给的控制可以通过数控系统来完成,提高加工精度和效率。
切削刃是深孔钻的核心部分,它负责将金属材料切削成所需的形状和尺寸。
切削刃通常由硬质合金制成,具有较高的硬度和耐磨性。
在加工过程中,切削刃通过旋转和进给的方式,将工件中的金属材料切削掉,并形成孔道。
切削刃的结构和形状会影响到加工效果,因此需要根据具体需求选择合适的切削刃。
冷却液的使用也是深孔钻原理中的重要一环。
由于深孔钻在加工过程中会产生大量的热量,如果不及时散热,可能会导致切削刃的损坏、工件表面质量下降甚至工具断裂。
因此,冷却液的作用就是通过冷却和润滑的方式,降低切削区域的温度,减少切削热量的积累。
冷却液还可以清洗切削区域的切屑和金属屑,保持切削刃的清洁,提高加工质量。
深孔钻在实际应用中需要注意一些技术要点。
首先是刀具的选择和刃磨。
根据具体的加工要求和工件材料,选择合适的刀具和切削参数,以确保加工效率和质量。
同时,定期对刀具进行刃磨和保养,延长其使用寿命。
其次是冷却液的选用和供给。
根据加工材料和切削条件,选择合适的冷却液,并保证冷却液的供给充分,以保证加工的稳定性和质量。
最后是加工过程的监控和控制。
通过实时监测切削力、温度、振动等参数,及时调整加工参数,确保加工过程的稳定性和可控性。
深孔钻是一种高效、精密、稳定的加工工具,其原理是通过刀具进给和旋转,在工件中心形成一个可以加工深孔的孔道。
深孔钻的加工过程需要注意刀具进给、切削刃和冷却液等方面的技术要点,以确保加工效率和质量。
基于FANUC宏程序的钻深可变式深孔加工应用研究1
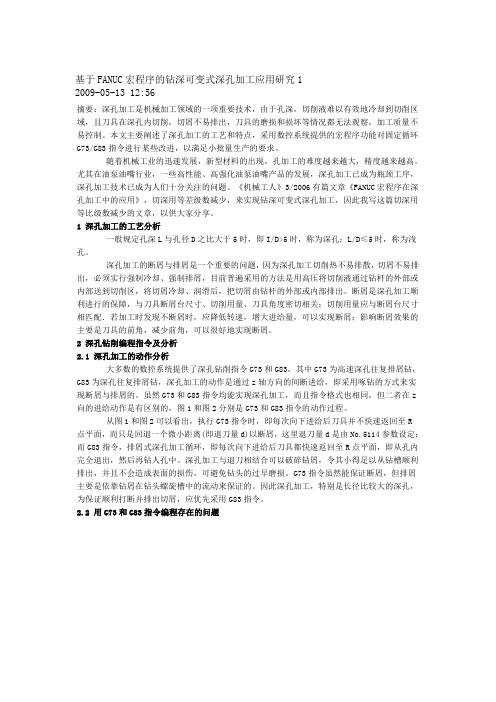
基于FANUC宏程序的钻深可变式深孔加工应用研究12009-05-13 12:56摘要:深孔加工是机械加工领域的一项重要技术,由于孔深,切削液难以有效地冷却到切削区域,且刀具在深孔内切削,切屑不易排出,刀具的磨损和损坏等情况都无法观察,加工质量不易控制。
本文主要阐述了深孔加工的工艺和特点,采用数控系统提供的宏程序功能对固定循环G73/G83指令进行某些改进,以满足小批量生产的要求。
随着机械工业的迅速发展,新型材料的出现,孔加工的难度越来越大,精度越来越高。
尤其在油泵油嘴行业,一些高性能、高强化油泵油嘴产品的发展,深孔加工已成为瓶颈工序,深孔加工技术已成为人们十分关注的问题。
《机械工人》3/2006有篇文章《FANUC宏程序在深孔加工中的应用》,切深用等差级数减少,来实现钻深可变式深孔加工,因此我写这篇切深用等比级数减少的文章,以供大家分享。
1 深孔加工的工艺分析一般规定孔深L与孔径D之比大于5时,即I/D>5时,称为深孔;L/D≤5时,称为浅孔。
深孔加工的断屑与排屑是一个重要的问题,因为深孔加工切削热不易排散,切屑不易排出,必须实行强制冷却、强制排屑,目前普遍采用的方法是用高压将切削液通过钻杆的外部或内部送到切削区,将切屑冷却、润滑后,把切屑由钻杆的外部或内部排出。
断屑是深孔加工顺利进行的保障,与刀具断屑台尺寸、切削用量、刀具角度密切相关;切削用量应与断屑台尺寸相匹配.若加工时发现不断屑时,应降低转速,增大进给量,可以实现断屑;影响断屑效果的主要是刀具的前角,减少前角,可以很好地实现断屑。
2 深孔钻削编程指令及分析2.1 深孔加工的动作分析大多数的数控系统提供了深孔钻削指令G73和G83,其中G73为高速深孔往复排屑钻,G83为深孔往复排屑钻,深孔加工的动作是通过z轴方向的间断进给,即采用啄钻的方式来实现断屑与排屑的。
虽然G73和G83指令均能实现深孔加工,而且指令格式也相同,但二者在z向的进给动作是有区别的,图1和图2分别是G73和G83指令的动作过程。
- 1、下载文档前请自行甄别文档内容的完整性,平台不提供额外的编辑、内容补充、找答案等附加服务。
- 2、"仅部分预览"的文档,不可在线预览部分如存在完整性等问题,可反馈申请退款(可完整预览的文档不适用该条件!)。
- 3、如文档侵犯您的权益,请联系客服反馈,我们会尽快为您处理(人工客服工作时间:9:00-18:30)。
压 间隙可调 的负压 装 置 ; 油 系 统采 用 叶 片定量 泵 供 供 冷却 润滑液 , 由溢 流阀控制 冷却润 滑液供 给压力 ,
最大供 给 流量 为 7 m。mi , 大压 力 为 6 ×1 5d / n 最 5 O P , 了避 免排 屑载荷 以及 钻 削 深度 对 分 流 比 q的 a为 影 响 , 流结构 改为 由 2个 调 速 阀分 别控 制 各通 道 分 的流量 , 屑通 道载荷 压力 P 排 由压 力表 1测量 , 系 统 如 图 2所 示 ; 工材 料 为 3 #退 火 钢 , 加 0 硬度 1 8 6 HB; 钻头 为 声1 T 的 YT1 4ml l 5刀 片 B TA钻 、 涂层刀
图 2 供 油 系 统
. .
2 试 验 结 果 及分 析
表 明, 屑容屑 系数越 小排屑越 好 , 切 而且 c形切屑 的切屑 容屑 系数最 小 , 对排屑 最有 利 。 关键 词 : 深孔钻 削 ; 削参 数 ; 切 排屑 ; 切屑 容屑 系数
中图分类 号 : G 5 3 T 2 文献标 志码 : A
S u n t e Chi o p lg fDe p h l o e sng t dy o h p M r ho o y o e 。 o e Pr c s i
rm ov 1 e a. Ke r s: e — l r e sng,Cuti r m e e s,Chi e y wo d De p ho e p oc s i tng pa a t r p r mov l a ,Chi a a iy f cor p c p ct a t
排 屑的影 响和润 滑液 的冷 却 、 屑 的作 用有 很 大 的 断
实 际意义 。
本文的研 究 基 于 D F系统 上 , F系统 的结 构 如 D 图1 所示 , 系统供 给 的润滑液 经 流量控 制 阀后分 流 ,
一
片 B A 钻和 陶瓷刀 片 B A 钻 ; 却润 滑 液为低 粘 T T 冷
ZH A O u ,G UA N i i R yi Sh x
( olg fElcrme h nc t& E gn e ig,No t iest f ia C l eo e to c a ia e n ie rn rhUnv r i o n ,Tay a 3 0 1 y Ch iu n 0 0 5 ,Chn ) ia
Ab t a t I h sp p r h fe t ft ec i h p n h p c p ct a t r(o n tv l me o t l h p ih h v sr c :n t i a e ,t ee f c so h h p s a ea d c i a a i f c o f ru i o u fmea is wh c a e y c a v l me ft e1 mm o u )o h 4 YT1 l d b a eBTA rl, imo d c a e ld rl a d c r mi ld rl i i e e tc ti g p r me 5 d i d a n o td b a e d i n e a cb a e d i n d f r n u t a a — l l l f n t r n t ec i e v l r t de h o g h x mp e .Th e u t h w t a e h h p c p ct a t ri s l r e s o h h pr mo a we es u id t r u h t ee a ls e r s lss o h twh n t ec i a a i f c o s ma l , y e t e c i e v l s b te .M e n i h h p c p ct a t ro y ec i h ma ls ,a d i i mo tb n fca t h p h h p r mo a e t r i a wh l t e c i a a i f co fC t p h p i t es le t n s e y s t s e e iil o c i
深 孔钻 削切 屑形 态 的研 究
赵如意, 关世 玺
( 中北 大 学 机 电5 程 学 院 , - 山西 太 原 0 0 5 ) 3 0 1
摘 要 : 通过试验 研 究 了 1 T 的 YT 5刀 片 B 4ml l 1 TA钻 、 涂层 刀片 B A 钻 和 陶瓷 刀片 B A 钻在不 T T 同切 削参 数 的切 屑形 态和切屑 容屑 系数 ( 为单 位体 积金 属 的切 屑 所具 有 的容积 ) 对排 屑 的影 响 , 验 试
深孔加 工技术 在机械 制造及 装备制造 中占有 重
要 的地位 。深孔加 工 的特 点及特 殊性表现 为在封 闭 的条件下切 削 , 削 条件 恶 劣 , 切 断屑 和 排 屑 困难 , 切 削热 不易扩 散 冷 却 , 统 刚性 差 , 工 质 量难 以 保 系 加 证 ] 。深孔加 工 中切 屑形态对 排屑有很 大影 响 , 切 削液用于 冷却 、 滑 和 断屑 。 因此研 究 切 屑形 态 对 润
度的 5 #机油 , 其运 , 另一 部分经负压 通
道及负压装置 单锥 面喷 嘴射人排 屑通 道 。排 屑通 道
的流量为 , 负压通道流量为 Q , 负压间隙为 S 。
Q
撼量计 1 Q6 翌 —3 B 调速 阏1