乙烯裂解炉的结焦及抑制技术
乙烯裂解炉管的结焦机理及其防护措施
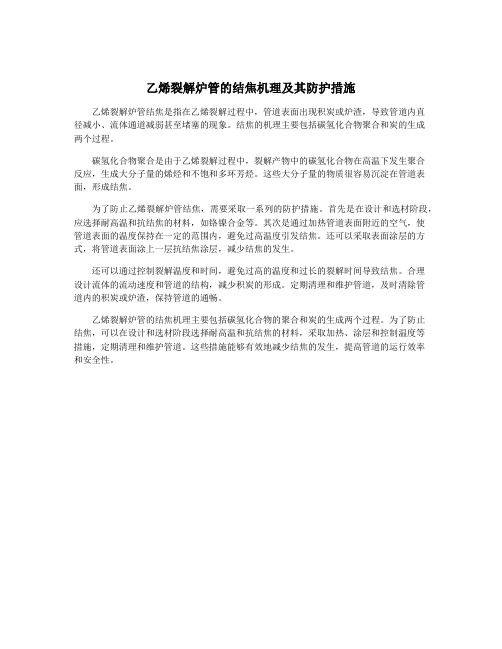
乙烯裂解炉管的结焦机理及其防护措施
乙烯裂解炉管结焦是指在乙烯裂解过程中,管道表面出现积炭或炉渣,导致管道内直
径减小、流体通道减弱甚至堵塞的现象。
结焦的机理主要包括碳氢化合物聚合和炭的生成
两个过程。
碳氢化合物聚合是由于乙烯裂解过程中,裂解产物中的碳氢化合物在高温下发生聚合
反应,生成大分子量的烯烃和不饱和多环芳烃。
这些大分子量的物质很容易沉淀在管道表面,形成结焦。
为了防止乙烯裂解炉管结焦,需要采取一系列的防护措施。
首先是在设计和选材阶段,应选择耐高温和抗结焦的材料,如铬镍合金等。
其次是通过加热管道表面附近的空气,使
管道表面的温度保持在一定的范围内,避免过高温度引发结焦。
还可以采取表面涂层的方式,将管道表面涂上一层抗结焦涂层,减少结焦的发生。
还可以通过控制裂解温度和时间,避免过高的温度和过长的裂解时间导致结焦。
合理
设计流体的流动速度和管道的结构,减少积炭的形成。
定期清理和维护管道,及时清除管
道内的积炭或炉渣,保持管道的通畅。
乙烯裂解炉管的结焦机理主要包括碳氢化合物的聚合和炭的生成两个过程。
为了防止
结焦,可以在设计和选材阶段选择耐高温和抗结焦的材料,采取加热、涂层和控制温度等
措施,定期清理和维护管道。
这些措施能够有效地减少结焦的发生,提高管道的运行效率
和安全性。
乙烯裂解炉管的结焦机理及其防护措施

乙烯裂解炉管的结焦机理及其防护措施乙烯裂解炉是石化行业中常见的生产设备之一,用于将石油、天然气等原料裂解成乙烯等有机物。
长期运行下来,裂解炉管道表面容易结焦,导致生产能力下降,乃至设备损坏,给生产带来很大的影响。
研究乙烯裂解炉管道的结焦机理及其防护措施具有重要的理论和实际意义。
乙烯裂解炉管道的结焦机理较为复杂,主要包括热解、聚合和结焦三个过程。
通过裂解反应,高温高压条件下的乙烯裂解炉产生大量的碳氢化合物。
在此过程中,裂解产物中的不饱和碳氢化合物容易发生热解反应,生成碳黑颗粒。
聚合过程是指碳黑颗粒在高温环境下,发生自身的聚集和生长。
结焦过程是指碳黑颗粒在管道表面积聚形成附着物,引起管道的堵塞、热传导性能下降等问题。
针对乙烯裂解炉管道的结焦问题,应采取一系列的防护措施。
优化裂解炉操作条件,以减少不饱和碳氢化合物的生成和热解反应。
加强管道清洗和维护管理,定期对管道进行清洗和防腐处理,以控制结焦的程度。
应加强管道材料的选用和改进,选择耐高温、耐腐蚀的材料,以提高管道的抗结焦能力。
结合碳氢化合物特性,可以选择一定的添加剂,如抗结焦剂,加入到乙烯裂解炉反应体系中,以削弱或抑制结焦过程。
还可以采取物理方法,如采用超声波技术、高频电场技术等,来破坏碳黑颗粒的聚集和生长过程,从而减少结焦问题。
乙烯裂解炉管道的结焦问题是一个复杂的技术难题,需要从多个方面进行研究和解决。
通过优化操作条件、加强管道维护和材料改进、添加抗结焦剂以及采用物理方法等措施,可以有效地降低结焦的发生和程度,提高乙烯裂解炉的生产效率和设备的寿命。
乙烯装置抑制裂解炉炉管的技术措施

乙烯装置抑制裂解炉炉管的技术措施摘要:乙烯裂解炉炉管是乙烯装置中操作温度最高的部件,在裂解炉炉管内烃类裂解反应中,二次反应生成焦炭。
一直以来,人们一直在试图探索乙烯裂解炉的结焦机理,寻找抑制结焦的方法,以有效延长裂解炉的运行周期,提高烯烃的产量。
关键词:乙烯装置;裂解炉炉管结焦;措施1.引言乙烯是化学工业中最重要的原料之一。
目前,世界上大部分乙烯基都是由管状蒸汽热裂解制成的,在裂解炉管表面和锅炉旁冷却柱表面不可避免地会产生焦炭。
在这种高温下,增加了炉内热传热阻力,降低了炉内管道的内部直径,增加了炉外的温度,增加了炉内液体的压力,甚至阻碍了炉内正常生产。
分析了乙烯装置裂解炉炉管结焦的情况,提出了乙烯装置裂解炉炉管结焦的控制措施,对提高乙烯产量、延长裂解炉运行周期具有重要作用。
2.结焦机制乙烯是一种非常重要的基础原料,通常通过管式炉对烃类进行热裂解生产,而乙烯裂解炉是乙烯装置的核心部分,操作不当会造成严重的结焦。
烃类在裂解炉炉管中的结焦过程十分复杂,一般认为其结焦主要有两个途径:一是通过乙炔途径结焦,主要是在1000℃左右进行的,二是通过芳烃途径结焦,主要是裂解过程中产生的芳烃脱氢缩合而成。
在烃类裂解过程中,裂变不仅发生在炉管内,也发生在急冷锅炉换热器内[1]。
急冷锅炉结焦的主要原因有两个:一是部分裂解气体停留时间过长导致二次反应,促进了结焦,二是当裂解气冷却时,热交换器的冷凝物慢慢脱氢成焦油、焦炭。
急冷锅炉的形状、材料、制造压力和使用时间密切相关。
虽然锅炉快速冷却是必然的,但前提是锅炉设计合理,可以减少冷却时间,延长锅炉运行周期。
高效能锅炉必须设计成高质量、高流量、高压力、短停留和低压并存的锅炉。
3.乙烯装置裂解炉炉管结焦状况分析3.1气相在实际操作过程中,气相焦化主要是指气流主体的形成过程,其中烯烃聚合和环化形成的芳烃是非常重要的产物。
在最后阶段,炭黑颗粒经过脱氢和缩合逐渐形成。
根据已有的相关研究,研究人员在研究这一现象时,将利用电子显微镜等技术手段对气相焦化过程进行判断和分析。
乙烯裂解炉管的结焦机理及其防护措施

乙烯裂解炉管的结焦机理及其防护措施乙烯裂解炉管是乙烯生产过程中的关键设备之一。
由于裂解反应的高温高压条件,炉管容易发生结焦现象,严重影响乙烯生产的正常运行。
研究乙烯裂解炉管的结焦机理以及采取相应的防护措施对于保障乙烯生产的安全和稳定具有重要意义。
乙烯裂解炉管的结焦机理主要包括以下几个方面:1. 碳氢基团转移:在高温下,乙烯在管内发生裂解反应,生成一系列碳氢化合物。
这些化合物在管壁上发生反应,并逐渐形成碳沉积物。
这一过程被称为碳氢基团转移。
2. 聚合反应:管内高温环境下,乙烯分子容易聚合为高分子聚乙烯。
聚合反应也会导致碳沉积物的形成。
3. 热解反应:乙烯在高温环境下会发生热解反应,分解为低碳烷烃和烯烃。
这些烃类物质会在管内发生反应,并生成碳沉积物。
乙烯裂解炉管结焦会导致以下问题:1. 阻塞:碳沉积物会在管壁上逐渐积聚,最终导致炉管阻塞,影响乙烯的正常流动。
2. 传热不良:结焦会导致管壁的热传导性能降低,热能难以有效地传递给乙烯,影响乙烯的加热效果。
3. 强度下降:碳沉积物的形成会使得炉管的机械强度下降,增加炉管开裂的风险。
为了防止乙烯裂解炉管的结焦问题,需要采取下列防护措施:1. 优化炉管设计:通过采用合适的炉管材料和结构设计,提高炉管的抗结焦能力,降低结焦速率。
可以采用抗高温、抗腐蚀的合金钢材料作为炉管材料。
2. 热交换器设计:在裂解炉和炉管之间设置热交换器,通过冷却介质冷却裂解气体,降低气体温度。
这样可以减缓结焦速率,延长炉管的使用寿命。
3. 定期清洗:定期使用清洗剂对炉管进行清洗,去除管壁上的碳沉积物,防止结焦问题的产生。
清洗时要注意避免对炉管产生损害。
4. 添加抗结焦剂:向裂解气体中添加抗结焦剂,改变反应体系的物理化学性质,降低结焦速率。
常用的抗结焦剂有矿物质和有机酸类物质等。
5. 控制操作条件:控制好反应温度、压力等操作条件,避免过高的温度或压力对炉管造成结焦的影响。
了解乙烯裂解炉管的结焦机理以及采取相应的防护措施对于保障乙烯生产的安全和稳定非常重要。
乙烯裂解炉管的结焦机理及其防护措施

乙烯裂解炉管的结焦机理及其防护措施乙烯裂解炉管结焦是裂解工艺中常见的问题之一,主要是由于乙烯在高温下裂解生成的碳黑物质沈积在炉管内壁而导致的。
结焦会增加炉管的阻塞程度、降低传热效率,甚至会引起炉管损坏,严重影响生产运行。
乙烯裂解炉管结焦的机理主要有以下几个方面:1. 易结焦物质存在:乙烯裂解过程中,会产生一些易结焦的碳黑物质,如多环芳香烃等。
这些物质在高温下容易聚集在炉管内壁形成结焦。
2. 温度分布不均匀:乙烯裂解炉管内温度分布不均匀,部分区域温度偏高会加剧易结焦物质的形成。
为了预防乙烯裂解炉管结焦问题,可以采取以下防护措施:1. 控制乙烯裂解过程参数:合理控制乙烯裂解炉的操作参数,如温度、压力、速度等,以减少易结焦物质的生成和沉积。
可增加炉内空气流动,促进物质的扩散和排除。
2. 清洗和保护炉管内壁:定期对乙烯裂解炉管进行清洗,以去除已经沉积的结焦物质。
在炉管内壁上涂覆一层防结焦的保护层,减少结焦物质的附着。
3. 使用抗结焦材料:选用抗结焦能力强的材料制作炉管,如高温合金钢等,能够减少结焦物质的黏附和附着。
4. 提高传热效率:改善乙烯裂解炉的传热方式和热交换设备,提高传热效率,减少炉管温度梯度的差异,从而减少结焦的发生。
5. 定期检查和维护:定期对乙烯裂解炉进行检查,及时发现和处理炉内的结焦问题。
还要定期维护和更换炉管,以保持其良好的工作状态。
乙烯裂解炉管结焦是一个常见的问题,其机理主要包括易结焦物质的生成和沉积、温度分布不均匀以及炉管内物质的沉积。
为了预防结焦问题,需要合理控制裂解过程参数、清洗和保护炉管内壁、使用抗结焦材料、提高传热效率,并定期检查和维护炉管。
只有采取多种综合措施,才能有效防止乙烯裂解炉管结焦问题的发生。
乙烯裂解炉管的结焦机理及其防护措施

乙烯裂解炉管的结焦机理及其防护措施
乙烯裂解炉在运行过程中,炉管表面往往会出现结焦现象,这对炉的安全稳定运行产生了严重的影响,因此对结焦机理及其防护措施进行深入研究并采取切实有效的措施进行防护具有重要的意义。
一、结焦机理
乙烯裂解炉管结焦是由于热传导方式及局部换热流动不均匀造成的。
当炉内热传导过程中,炉管表面温度高于650℃时,在高温下炉壁表面沉淀和溶降的胶体、颗粒、烟雾等物质会与热辐射、对流热量进行吸收;同样,还会受到气流吹拂和氧化环境的影响,这些因素共同作用,导致炉管表面结焦。
二、防护措施
1、采用优质原料:在裂解炉生产中,采用优质原料对防止炉管结焦具有重要意义。
优质原料可大幅降低裂解炉炉管的结焦率,减少结焦所带来的损失。
2、控制炉内氧气含量:适当降低炉内氧气含量是防止炉管结焦的有效措施之一。
增加炉内氢气的含量可以减少热辐射和局部氧化反应,从而有效降低炉管的结焦风险。
3、采取酸洗保养:在裂解炉使用一段时间后,炉管表面往往会形成一定的结焦层,在这时采用酸洗保养的方法可以有效去除结焦层,延长炉管的使用寿命。
4、增加清洗次数:在使用过程中,适当增加清洗次数可以有效清除炉管表面的结焦物质,避免结焦物质叠加产生危险。
5、采用优秀的维护管理:在工作中,对乙烯裂解炉的维护管理应高度重视,及时发现和解决其中的问题,从而确保它的稳定运行。
综上所述,针对乙烯裂解炉管结焦问题,我们应当采取先进的技术手段和合理的措施进行防护,从而保证炉管处于良好的工作状态,保障生产的顺利进行。
乙烯裂解炉管的结焦机理及其防护措施

乙烯裂解炉管的结焦机理及其防护措施乙烯是一种重要的化工产品,在乙烯生产过程中,乙烯裂解炉是一个核心设备,裂解炉管的结焦问题一直是乙烯生产过程中的难题之一。
结焦不仅会影响乙烯生产的正常运行,还会降低设备的使用寿命,因此需要采取有效的防护措施来解决这一问题。
本文将从乙烯裂解炉管的结焦机理入手,介绍乙烯裂解炉管的结焦机理以及针对结焦问题的防护措施。
一、乙烯裂解炉管的结焦机理1. 高温下的碳积聚现象乙烯裂解炉工作在高温、高压的条件下,乙烯在裂解炉管内经历了高温反应,产生了大量的碳积聚物。
这些碳积聚物会在管壁上积聚,形成结焦层。
结焦层的不断积累导致管道的过热,使管壁产生变形和老化,最终导致管道的损坏。
2. 污染物的影响在乙烯生产过程中,还会产生一些污染物,这些污染物也会加剧裂解炉管的结焦问题。
硫化物、氯化物等物质会与碳积聚物相互作用,加速结焦的过程。
一些金属离子也会促进碳积聚物的生成,加重结焦问题。
3. 流动状态的影响裂解炉管内气体、液体和固体经常处于流动状态,而流动状态下的碳积聚物很容易发生剥落和脱落现象,这些碎片也会堵塞管道,形成结焦。
乙烯裂解炉管的结焦问题主要是由高温下的碳积聚、污染物的影响和流动状态的影响三个方面造成的。
了解了结焦机理,我们就可以采取相应的防护措施来解决结焦问题。
1. 优化工艺条件优化工艺条件是解决结焦问题的重要措施。
在裂解炉的操作过程中,可以通过调整操作参数,如温度、压力、气体流速等,来减少碳积聚的生成和积聚速度,减轻结焦问题。
还可以通过改进催化剂和控制添加剂等手段,来降低碳积聚物的生成。
2. 清洗保养定期对裂解炉管进行清洗和保养也是解决结焦问题的重要手段。
清洗可以有效地清除管道内的碳积聚物,防止结焦的发生和加重。
同时对管道进行保养,保持管道畅通,减少结焦问题的发生。
3. 表面涂层对裂解炉管进行表面涂层是有效的防护措施。
涂层可以有效地隔绝碳积聚物与管壁的接触,减少碳积聚物的生成和积聚,从而减轻结焦问题。
乙烯裂解炉管的结焦机理及其防护措施

乙烯裂解炉管的结焦机理及其防护措施乙烯裂解炉是石油化工行业中常用的生产设备。
乙烯裂解炉管的结焦是炉管寿命损失和生产停工的重要原因之一。
本文将探讨乙烯裂解炉管结焦的机理及防护措施。
一、结焦机理乙烯裂解炉管结焦是由于炉管内部高温环境下,炉垢物质被不断加热、分解、聚合,生成一定分子量和分子结构的聚合物和碳化物,最终在炉管内部形成晶状/玻璃状碳化物物质沉积。
其主要机理有以下几个方面:1. 热分解:乙烯裂解炉中,乙烯等烷烃经过高温条件下的热分解,生成大量的碳质物质,附着在炉管壁上。
2. 热解:烷基物质在高温下发生热解反应,生成粘性物质,沉积于炉管内部表面。
3. 烧结:炉内高温环境导致烧结现象,使得沉积物表面的碳质物质发生烧结,继而形成结焦区域。
4. 脱碳:在加热和冷却过程中,炉内的碳质物质发生瞬间的脱碳,导致炉垢物质温差过大,使炉垢物质易于破裂和脱落。
二、防护措施为了延长乙烯裂解炉管的使用寿命,必须采取有效的防护措施,防止炉管结焦。
以下几点是防护措施的建议:1. 提高温度:在保证炉管安全运行的情况下,提高乙烯裂解炉的运行温度,可以有效减少炉管结焦的风险,因为较高的温度可以减少炉垢物质沉积。
2. 加强炉管内部清洁:炉管内部的清洁只有在炉管停机时才能进行。
清除沉积物质可以减少结焦风险。
3. 添加防结焦剂:在乙烯裂解炉中加入防结焦剂,可以有效地抑制炉垢物质的生成和沉积。
4. 优化操作:炉内操作过程的优化有助于减少乙烯裂解炉管结焦的风险。
例如缩短炉管的使用时间,可以有效减少炉垢沉积。
5. 更换炉垢物质:每次停机检修都应该清除炉垢。
而在下一次启动后,在炉内添加新的催化剂和炉垢物质。
总之,乙烯裂解炉管结焦是一个让石油化工行业非常头痛的问题。
但是要做到严格的质量控制和生产管理,以确保乙烯裂解炉管的寿命和安全。
- 1、下载文档前请自行甄别文档内容的完整性,平台不提供额外的编辑、内容补充、找答案等附加服务。
- 2、"仅部分预览"的文档,不可在线预览部分如存在完整性等问题,可反馈申请退款(可完整预览的文档不适用该条件!)。
- 3、如文档侵犯您的权益,请联系客服反馈,我们会尽快为您处理(人工客服工作时间:9:00-18:30)。
乙烯裂解炉的结焦及抑制技术Coking of Ethylene Cracking Furnace and SuppressionTechnology摘要:介绍了乙烯裂解炉的结焦机理、影响结焦的主要因素和抑制炉管结焦的主要技术,着重综述了近几年国内外炉管表面处理技术的研制情况和添加抑制剂技术的进展及其工业应用情况,提出炉管表面处理技术的工业应用有待发展和突破,结焦抑制剂的发展方向是复合的多功能抑制剂。
Abstract:This thesis introduced the principle and affecting factors of coking on the ethylene cracking furnaces also the main technical of inhibiting coking on the furnace. Than discussed the development of the tube surface treatment and inhibitor technology this years.It was suggested that we must try our best to take tube surface treatment technologies to industrial applications shortly and work out more multi-functional inhibitors.关键词:乙烯;裂解炉;结焦;涂层;炉管表面处理;抑制剂Keywords:Ethylene;Cracking Furnace;Coking;Coating;Tube surface treatment;Inhibitors前言在乙烯裂解装置中,裂解炉和急冷锅炉内的结焦是影响乙烯装置长周期运行的大问题。
产生结焦的原因是:(1)原料烃在裂解反应中的高温二次反应形成的脱氢成碳反应;(2)高温裂解气进入急冷锅炉内,高沸点组分在低温管壁上冷凝后长时间与高温裂解气接触而发生脱氢、缩合等反应形成含氢量极低的焦垢。
结焦会引起两个方面的后果一是结焦会使裂解炉管的传热性能下降。
为了维持管内物料的正常温度,必然要提高炉管外壁的温度,这样很容易达到炉管金属材料所承受的高温极限而损伤炉管。
另一方面,炉管内结焦会使管径变小,在处理量不变时,物料在炉内的停留时间将减少,炉管内的压力降也会增大,这种裂解工艺条件的变化可使裂解的选择性变坏,致使目的产物乙烯的收率显著下降。
由于结焦问题的严重性,国内外学者已做了许多抑制结焦技术的研究工作。
内容包括改变裂解工艺条件,加氢裂解技术,原料混合裂解技术,裂解炉和急冷锅炉金属表面处理技术及添加结焦抑制剂技术等对结焦反应的动力学方面也做了一定程度的探索。
其目的均在于降低结焦速率而延长清焦周期。
总起来看,这些工作大都处于试验阶段。
对于已有的裂解装置,裂解原料和工艺条件均已确定,结焦抑制技术就只能从表面处理技术和添加结焦抑制剂两方面着手。
一般认为,添加结焦抑制剂是一种更为经济有效的方法。
1 结焦机理通过对结焦的深入研究,目前已提出的裂解结焦机理有3 种:金属催化结焦、自由基结焦和焦油聚合结焦。
金属催化结焦有实验证明[1-2]镍及铁是炉管结焦的催化剂,在同样工艺条件下用 5 种金属材料与石英管做结焦对比试验,发现镍的催化活性最高,几乎比石英管高出千倍以上,而活性最低的不锈钢也比石英管高出10倍以上,其催化活性顺序[3]是:Ni > Ni - Cr > Fe > Cu > 不锈钢。
而工业裂解炉管为高镍铬合金钢管,因此对结焦有明显的表面催化作用。
在装置运行初期,炉管的金属表面裸露在物料氛围中,催化作用使结焦速度提高,随着焦的生成,炉管表面逐渐被焦层覆盖,催化作用随之减弱。
但由于金属粒子可以通过扩散到达焦的表面,故即使在运行后期,金属催化结焦仍然存在,只是结焦速度趋于稳定。
金属催化结焦生成的主要是纤维状焦,由于金属粒子在纤维状结焦中迁移,在结焦的同时也发生渗碳效应,对炉管造成腐蚀,使炉管寿命缩短。
金属的表面催化作用不但与金属材质有关,也与金属表面的结构有关.表面粗糙利于结焦的形成,而光滑的表面则有防止结焦的作用。
自由基结焦又叫热裂解结焦。
气相裂解反应生成大量自由基(乙炔、乙烯、甲基、乙基、苯基等)与结焦层表面的自由基(由前期结焦进行自由基脱氢反应生成) 通过加成反应促进焦的生长。
通过这个方式,气相中所有未饱和的烃分子都是潜在的结焦前兆体。
焦油聚合结焦在原料中含有的少量芳烃和经过二次反应生成的芳烃、多环芳烃,在气相中能够形成焦油液滴。
部分焦油液滴撞击管壁表面时可以黏附在管壁表面并在高温下脱氢生焦。
芳烃聚合形成的焦通常为球状、褐色膜状或黑色片状。
通常在裂解重质原料如常、减压柴油时才有发生。
2 影响结焦的主要因素原料性质和裂解深度根据结焦机理,结焦主要由原料中的芳烃化合物以及裂解气二次反应生成物产生。
原料中芳烃含量愈多,结焦速率愈快。
轻烃裂解时的结焦母体主要是二次反应的生成物;而重质原料裂解时,原料中的芳烃是主要的结焦母体,特别是带侧链的芳烃。
同时裂解深度提高,结焦活性组分增加,二次反应加剧,结焦也加重。
稀释蒸汽注入稀释蒸汽可以降低烃分压,抑制缩聚反应,从而能减轻结焦程度;可以缩短停留时间,抑制二次反应的进行,从而降低结焦速率;而且水蒸气对Fe 和Ni 有氧化作用,可以抑制催化生炭反应。
停留时间和裂解温度缩短停留时间,可以减少二次反应的发生,有利于降低结焦速度。
但往往缩短停留时间要通过提高流速或缩小炉管直径、提高炉管温度来实现,这样就提高了结焦母体的传质速度,当结焦反应速度低于传质速度时,结焦反应过程由反应速度控制,反之,结焦反应过程由传质控制。
通常,在高温裂解时结焦速度由传质过程控制,此时缩短停留时间,既有减少结焦母体浓度而降低结焦速度的正效应,也有增大传质而增加结焦速度的负效应。
但还是以前者为主,这就是为何裂解技术近年来都朝着高温短停留时间和低烃分压发展的原因。
3结焦抑制技术为了减轻裂解炉管结焦以及在裂解过程中加快焦或其前体的脱除,工业上已采用或正在研制开发的结焦抑制技术口,主要有:(1)裂解原料预处理和改质。
该方法是采用加氢处理、芳烃抽提等工艺,降低芳烃含量,提高氢含量。
(2)改变炉管合金成分,提高炉管合金性能。
使用较好的合金制造炉管能提高耐热温度等级,从而缩短停留时间,降低裂解炉管的压降。
如从25Cr/35Ni升级到35Cr-Ni合金及特种合金(35Cr/45Ni),尤其添加妮、钦和稀土元素显著提高了合金的性能,使用温度高达约1150℃。
最近对陶瓷炉管的开发也取得较大进展,陶瓷炉管可以消除结焦且无需定期更换,乙烷生成乙烯的转化率高达90%,并具有相当高的选择性。
(3)向裂解原料或稀释蒸汽中添加结焦抑制剂,可使结焦量明显减少,甚至达到基本不结焦。
试验还证明,抑制裂解炉炉管结焦效果的好坏不仅与结焦抑制剂有关,而且与分散抑制剂的设备有关。
以前由于缺乏适宜的分散抑制剂溶液的注射器,溶液蒸发不完全,易造成液滴与注射器及炉管的热表面接触,从而损坏注射器和炉管。
(4)将结焦催化气化,生成CO和H2,减少焦垢和厚度。
采用作为稀释剂进行加氢热裂解。
(5)炉管内表面的预处理,即在炉管表面涂覆一层对结焦催化效应小、不利于焦垢粘附的物质。
使金属表面硅化或硼化的技术可有效地防止结焦,该技术是通过烷氧基硅的气相热分解作用使金属表面形成耐火性较高的硅保护层,以减少金属表面的催化活性从而抑制结焦。
通过硅化处理的金属表面,结焦速率比未处理前降低2~8倍,经硼化后的金属表面可以抑制结焦,防止金属疲劳和腐蚀,硬度和抗磨损能力都有增强,硼化后的金属表面抑制结焦率最高达到98%。
4国外结焦抑制技术进展4.1对炉管表面进行处理加拿大Nova 公司在炉管内壁用纳米尖晶石构成涂层来抑制焦炭生成,在加拿大阿尔伯特省Joffre 的工业炉试用表明,在同样的裂解条件下,有涂层的炉子与未涂层的炉子相比运行周期可增加10倍左右[4]。
加拿大Westaim SEP 公司开发了涂层合金技术。
该公司和美国KBR 公司合作,在美国UTP 公司位于路易斯安那州Geismer 的乙烷裂解炉上进行了工业应用,其压降增加的速率不到无涂层的1/ 3,经过1 年的运行,炉管表面没有明显的渗碳腐蚀,证明能有效地减少结焦的形成[4 ]。
韩国SK 公司开发了一种在线涂层技术,可以在高温下用载气携带涂覆物依次在炉管内壁形成过渡层、扩散层和除焦层。
由金属醇盐和含铬化合物组成的过渡层可以缓冲金属炉管与无机扩散层的热膨胀性和机械性能差异,保持整个涂层的稳定不易脱落;无机扩散层可以有效覆盖金属活化中心,抑制金属催化结焦;在扩散层外面沉积一层碱金属除焦层可以促进结焦层发生煤气化反应,达到抑制裂解结焦的效果。
在KBR毫秒炉中试验,其压降增长速率只有未涂层的1/ 2 ,证明能有效减少结焦的形成[5]。
日本Daido Steel 公司与荷兰Shell 公司合作开发了一种涂覆技术。
该技术把Daido Steel 公司的等离子焊接技术与粉末冶金技术结合起来,将2~4 mm 的合金涂层沉积在炉管内形成镜面状表面,可使乙烯装置的操作周期延长1倍,使炉管寿命延长3倍.[6]4.2加入结焦抑制剂美国Nalco 公司开发了一系列以有机硫、磷复合物为主的结焦抑制剂,经过其研究发现硫、磷复合物协同作用,可以更有效地钝化炉管表面,如硫代亚磷酸二乙酯作结焦抑制剂可降低结焦量92%。
在上述抑制剂中加入环烷酸或脂肪酸与聚胺反应制得的咪唑啉类化合物,能在炉管形成防腐保护膜,使防腐作用得到了较大提高[7]。
美国Tetra 公司开发了一种含有乙酸钙、碳酸钾和硼酸铵的抑制剂,在乙烯裂解炉上试用,以乙烷为原料,加入抑制剂的质量分数为(1~50)×10-6 ,裂解炉运行周期可由40 d提高到180 d以上[8]。
4.3改变炉管表面的机械构件Sandvik 材料技术公司成功生产出用于乙烯裂解炉的纵翅型冷抛光处理的炉管[9]。
为了延长炉管的使用寿命,Sandvik公司采用高温奥氏钢制成外径5~10 cm(2~4 in) 的翅片管,合金含35 %铬、25 %镍,具有优异的抗渗炭性和抗氧化性,还含有1.6 %的硅、0.07 %的铈和0.17 %的氮。
纵翅管使炉管内表面积增加25 % ,可以改善传热,提高生产率,这种炉管也有一定的抑制结焦性能。
该公司已经接到了俄罗斯最大的石油公司——LUKoil 欧洲控股公司的定单,用于该公司在保加利亚Burgas新建的乙烯装置上。
日本久保田公司公开了一种新型炉管[10],炉管沿管壁内表面有翅片,呈螺旋形或圆环形,翅片沿轴向有一定斜度,根据操作条件、需要的传热系数以及允许的压降决定,翅片高度以及与轴向角度限定了炉管的内径。