天然橡胶的合成和加工工艺
合成橡胶生产工艺

合成橡胶生产工艺(总1页)
--本页仅作为文档封面,使用时请直接删除即可--
--内页可以根据需求调整合适字体及大小--
合成橡胶生产工艺
合成橡胶的生产工艺大致可分为单体的合成和精制、聚合过程以及橡胶后处理三部分单体的生产和精制。
合成橡胶的基本原料是单体,精制常用的方法有精馏、洗涤、干燥等。
聚合过程是单体在引发剂和催化剂作用下进行聚合反应生成聚合物的过程。
有时用一个聚合设备,有时多个串联使用。
合成橡胶的聚合工艺主要应用乳液聚合法和溶液聚合法两种。
目前,采用乳液聚合的有丁苯橡胶、异戊橡胶、丁丙橡胶、丁基橡胶等。
后处理是使聚合反应后的物料(胶乳或胶液),经脱除未反应单体、凝聚、脱水、干燥和包装等步骤,最后制得成品橡胶的过程。
乳液聚合的凝聚工艺主要采用加电解质或高分子凝聚剂,破坏乳液使胶粒析出。
溶液聚合的凝聚工艺以热水凝析为主。
凝聚后析出的胶粒,含有大量的水,需脱水、干燥。
氯丁橡胶
性能:氯丁橡胶由于分子链中含氯原子,因而具有极性,在通用橡胶中,其极性仅次于丁腈橡胶。
氯丁橡胶的物理机械性能和天然橡胶相似。
其生胶具有很高的抗张强度和伸长率,属于自补强性橡胶。
它的耐老化、耐热、耐油及耐化学腐蚀性比天然橡胶好。
氯丁橡胶的耐老化性甚为优越,特别表现在耐天候及耐臭氧老化上。
用途:主要用于:耐老化制品,如电线、电缆外皮等;耐热、耐燃制品,如耐热运输带、胶管等;耐油、耐化学腐蚀制品,如胶管、胶辊、拖拉机配件等;其他如胶布制品、胶鞋和粘合剂等。
橡胶加工工艺
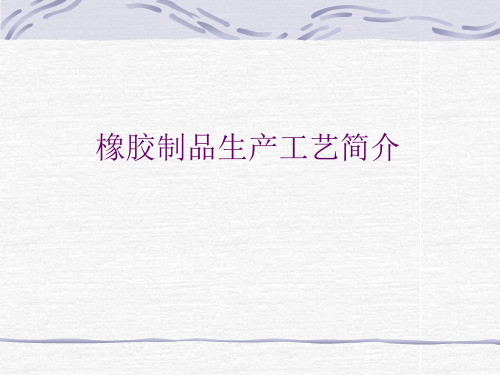
➢ 化学塑解剂:塑解剂的用量,在NR中一般为生胶重量的0.1~0.3%,合 成橡胶则应增大到2~3%。
橡胶制品生产工艺简介-塑炼工艺塑炼工艺
不同胶料开炼机混炼时辊筒温度
胶种
天然胶 丁苯胶 氯丁胶 丁基胶 丁腈胶 顺丁胶 三元乙丙胶 氯磺化聚乙烯 氟橡胶23—27 丙烯酸酯橡胶
橡胶制品生产工艺简介-塑炼工艺塑炼工艺
常用橡胶的塑炼特性
2. SBR ➢ 软SBR的初始门尼粘度一般在54~64之间,不需进行塑炼。 ➢ SBR采用机械塑炼效果不大,比较有效的方法时采用高温
塑炼法,以130~140℃温度最好,温度过高易生成凝胶。 3.BR ➢ BR一般不需要进行塑炼。 4.CR ➢ CR的初始门尼粘度都较低,一般不需要进行塑炼。但在储
➢ 物料在密炼室中主要受到几种作用: 转子间及转子与混炼室内壁间的作用;
转子棱间的搅拌作用;
转子轴向的往复切割作用。
➢ 优点:自动化程度高,生产效率高,节能,劳动强度低
➢ 缺点:温度高,冷却困难,易过炼,出料为无定形状
橡胶制品生产工艺简介-塑炼工艺塑炼工艺
密炼机
橡胶制品生产工艺简介-塑炼工艺塑炼工艺
存过程中其可塑性会下降,因此CR仍需经过塑炼加工,才 能获得所要求的可塑性。 ➢ CR宜采用开炼机进行塑炼,低温薄通塑炼效果最好。
橡胶制品生产工艺简介-塑炼工艺塑炼工艺
常用橡胶的塑炼特性
5.IIR ➢ 门尼粘度在38~75之间的品种一般不需要塑炼。 ➢ IIR采用机械塑炼效果不大,但用密炼机在120℃以上,并
且加入塑解剂进行高温塑炼则可取得较好的塑炼效果。 6.NBR ➢ NBR的塑炼应采用开炼机在低温(40℃以下)、小辊距
广义地说,橡胶其实是塑料的一种,塑料包括橡胶
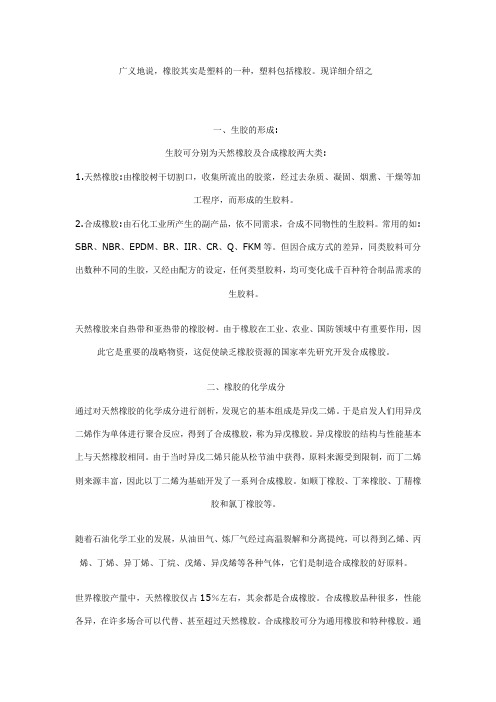
广义地说,橡胶其实是塑料的一种,塑料包括橡胶。
现详细介绍之一、生胶的形成:生胶可分别为天然橡胶及合成橡胶两大类:1.天然橡胶:由橡胶树干切割口,收集所流出的胶浆,经过去杂质、凝固、烟熏、干燥等加工程序,而形成的生胶料。
2.合成橡胶:由石化工业所产生的副产品,依不同需求,合成不同物性的生胶料。
常用的如: SBR、NBR、EPDM、BR、IIR、CR、Q、FKM等。
但因合成方式的差异,同类胶料可分出数种不同的生胶,又经由配方的设定,任何类型胶料,均可变化成千百种符合制品需求的生胶料。
天然橡胶来自热带和亚热带的橡胶树。
由于橡胶在工业、农业、国防领域中有重要作用,因此它是重要的战略物资,这促使缺乏橡胶资源的国家率先研究开发合成橡胶。
二、橡胶的化学成分通过对天然橡胶的化学成分进行剖析,发现它的基本组成是异戊二烯。
于是启发人们用异戊二烯作为单体进行聚合反应,得到了合成橡胶,称为异戊橡胶。
异戊橡胶的结构与性能基本上与天然橡胶相同。
由于当时异戊二烯只能从松节油中获得,原料来源受到限制,而丁二烯则来源丰富,因此以丁二烯为基础开发了一系列合成橡胶。
如顺丁橡胶、丁苯橡胶、丁腈橡胶和氯丁橡胶等。
随着石油化学工业的发展,从油田气、炼厂气经过高温裂解和分离提纯,可以得到乙烯、丙烯、丁烯、异丁烯、丁烷、戊烯、异戊烯等各种气体,它们是制造合成橡胶的好原料。
世界橡胶产量中,天然橡胶仅占15%左右,其余都是合成橡胶。
合成橡胶品种很多,性能各异,在许多场合可以代替、甚至超过天然橡胶。
合成橡胶可分为通用橡胶和特种橡胶。
通用橡胶用量较大,例如丁苯橡胶占合成橡胶产量的60%;其次是顺丁橡胶,占15%;此外还有异戊橡胶、氯丁橡胶、丁钠橡胶、乙丙橡胶、丁基橡胶等,它们都属通用橡胶。
三、橡胶原料的配制:橡胶原料的配制可分三个基本过程:1.塑炼:塑练是将生胶剪断,并将生胶可塑化、均匀化,帮助配合剂的混练作业。
其效果是改善药品的分散,防止作业中产生摩擦热,而致橡胶发生焦烧现象,进而改变橡胶的加工性。
橡胶加工工艺-橡胶的混炼
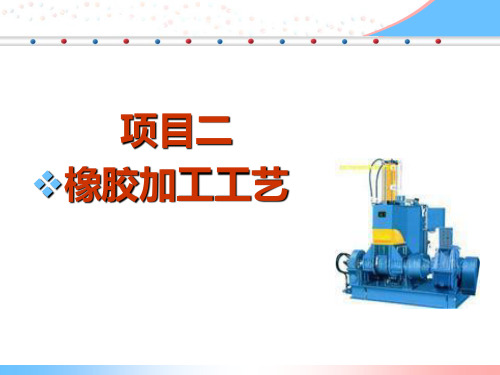
❖ 混炼的目的、意义和要求
❖ 为了提高橡胶使用性能、改进工艺性能和降低成本,
要在橡胶中添加各种配合剂。
❖ 在炼胶机上将各种配合剂加入生胶中制成混炼胶的工 艺过程称之为混炼。
❖ 混炼的内涵
❖ 混炼中发生复杂的物理、化学变化,绝不仅仅是简单 的混合。
炭黑被生胶和软化剂浸润和分散
炭黑与生胶之间产生强的相互作用(物理吸附为主)
项目二 ❖橡胶加工工艺
学习目标
❖ 知识目标 ❖ 1.熟悉橡胶加工的基本工艺过程 ❖ 2.掌握物料的配制对加工及制品性能的影响 ❖ 3.掌握橡胶的塑炼和混炼的原理及工艺参数 ❖ 4.掌握橡胶压延挤出的特点、工艺原理及工艺过程 ❖ 5.掌握橡胶硫化工艺历程及各阶段的特点 ❖ 6.掌握正硫化点的概念及其与制品性能的关系
工伤事故。
❖ 1.混炼过程 ❖ (1)包辊
堆积胶
包辊胶
橡胶在开炼机中的几种状况
1-不易进入辊缝;2-紧包前辊;3-脱辊成袋囊状;4-呈粘流态包辊
❖ (2)吃粉
粉料
堆积胶断面图 (黑色部分表示配合剂随皱纹沟进入胶料内部的 情况)
❖ (3)翻炼
混炼胶吃粉时断面图
❖ 混炼的第三个阶段为翻炼。由于橡胶黏度大,混炼时 胶料只沿着开炼机辊筒转动方向产生周向流动,而没有轴 向流动,而且沿周向流动的橡胶也仅为层流,因此大约在 胶片厚度约1/3处的紧贴前辊筒表面的胶层不能产生流 动而成为“死层”或“呆滞层”,见图4-3所示。此外,辊 缝上部的堆积胶还会形成部分楔形“回流区”。以上原因都 使胶料中的配合剂分散不均。
❖ 因此,必须经多次翻炼,左右割刀、打卷或三角包,薄通 等,才能破坏死层和回流区,使混炼均匀,确保质地均一。
❖ 2.开炼机混炼的工艺条件
橡皮的原料及制作过程

橡皮的原料及制作过程一、橡胶的原料1. 天然橡胶天然橡胶是橡皮制作中最主要的原材料,它是一种由橡胶树分泌的胶乳经过浓缩、干燥而得到的橡胶材料。
橡胶树是一种热带植物,主要分布在东南亚地区,如马来西亚、泰国、印度尼西亚等。
橡胶树的胶乳含有丰富的橡胶成分,经过提炼和加工后就可以得到我们常见的天然橡胶。
2. 合成橡胶除了天然橡胶外,橡皮制作中还可以使用合成橡胶作为原料。
合成橡胶是通过化学合成的方式制备的一种类似于天然橡胶的材料,具有类似的弹性和耐磨性。
合成橡胶通常用于一些特殊领域的橡皮制品生产中。
二、橡皮的制作过程橡皮的制作主要包括胶乳制备、挤压成型、硫化处理等步骤。
以下是橡皮制作的详细步骤:1. 胶乳的制备首先,将收集到的橡胶乳进行过滤和浓缩处理,得到纯净的橡胶浆。
然后,在橡胶浆中添加适量的添加剂,如硫化剂、促进剂、防老剂等,以调节橡胶的性能和增强其耐用性。
混合均匀后,就得到了成熟的胶乳。
2. 挤压成型接下来,将成熟的胶乳倒入橡皮制作用的模具中,通过挤压方法将橡胶胶乳填充到模具中,使其成形。
不同形状的橡皮制品需要采用不同的模具,并在填充过程中控制好橡胶的填充密度和厚度,确保成品的质量。
3. 硫化处理填充成型后的橡皮制品需要进行硫化处理,以增强其硬度和弹性。
硫化是通过加热橡皮制品使其中的硫化剂和橡胶发生化学反应,从而形成交联结构,提高橡皮的耐磨性和耐用性。
硫化的温度和时间需要根据橡皮的种类和用途进行精确控制,以确保成品具有良好的性能。
4. 裁切和包装经过硫化处理的橡皮制品通常会被裁切成适当的大小和形状,然后进行包装。
包装时需要注意避免橡皮受潮或受阳光暴晒,以免影响其使用寿命。
常见的橡皮包装方式包括塑料袋包装、纸盒包装等,以便于携带和存放。
通过以上的制作过程,我们就可以得到一款优质的橡皮制品。
橡皮作为一种常见的文具用品,广泛应用于办公、学习和绘画等领域,具有擦拭干净、不留痕迹的优点,深受人们喜爱。
希望通过本文的介绍,读者能更加了解橡皮的原料及制作工艺,对其有更多的认识和了解。
异戊橡胶
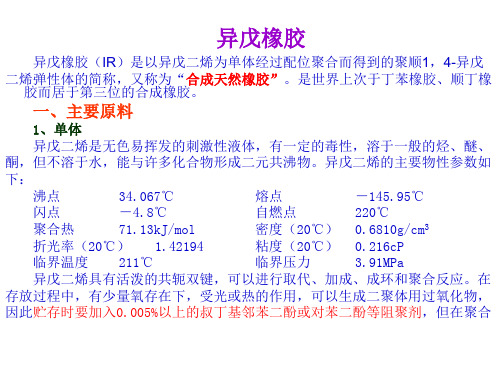
其中不同的生产方法其产物的质量规格不甚一样,如下表所示。
不同生产方法获得的异戊二烯单体的质量对比
纯度及杂质含量,%
脱氢法
抽提法
合成法
异戊二烯 二聚体
环戊二烯 戊二烯 炔烃 烯烃 烯烃
羰基化合物 过氧化合物
硫 乙腈
97 <0.1 <0.0001 <0.008 <0.005 <1.0 <2.8 <0.001 <0.0005 <0.0005 <0.0008
异戊橡胶
100%),可省去单体回收工序。不足之处是顺式-1,4含量低,相对分子质量高, 分布窄,给加工带来一定的困难;并且对氧、水、硫等非常敏感,因此对操 作条件要求很严格。
三、异戊橡胶的结构、性能及用途
由于异戊橡胶具有与天然橡胶相似的化学组成、立体结构和物理机械性能, 因此它是一种综合性能好的通用合成橡胶。两者的差别在于异戊橡胶的顺式-1, 4结构含量(92%~97%)没有天然橡胶高(>98%);结晶性能低于天然橡胶;相 对分子质量低于天然橡胶,并且带部分支链和凝胶。因此造成两者的物理性能不 完全一样如表9-2所示。与天然橡胶相比还具有质量均一,纯度高;塑炼时间短,
99.5
<0.0003 <0.008 <0.005
0.5
99.4 <0.005 <0.005 <0.005
<0.0005
异戊橡胶
无论采用什么方法生产异戊二烯,如何获得廉价的异戊二烯单体都是制约合 成异戊橡胶发展的关键。
2.引发剂体系 用于生产异戊橡胶的引发剂体系主要有齐格勒引发剂中的Ti系(TiCl4和 AlR3)、Li系(LiC4H9)和有机酸稀土盐三元引发体系(如[Ln(naph)3Al(C2H5)3Al(C2H5)2Cl]和 [Nd(RCOO)3-Al(C2H5)3-Al2(C2H5)3Cl3])。后者是我国采用的,它 克服了Ti系凝胶含量高,挂胶严重,非均相引发剂体系加料困难等弱点,异戊橡 胶顺式-1,4-结构含量为93%~94%,最高达97%。
橡胶的形成
橡胶基础知识橡胶基础知识一、生胶的形成:生胶可分别为天然橡胶及合成橡胶两大类:1.天然橡胶:由橡胶树干切割口,收集所流出的胶浆,经过去杂质、凝固、烟熏、干燥等加工程序,而形成的生胶料。
主要成分:异戊二烯。
目前天然橡胶的消耗量全世界已超过500万吨,90%是固态。
后来出现合成橡胶,如今,合成橡胶已经超过天然橡胶1倍,但天然橡胶仍被公认为性能最好的通用橡胶。
品质最好,有经济价值,现今大量种植发展的只有赫薇亚系的三叶橡胶树一种,原产于巴西,现在主要集中在东南亚和中非地区,马来西亚,印尼和泰国三个国家产量分别超过100万吨,占全世界的77%,80~90%的产量供应给世界各大工业发达国家。
这种产销形势使天然橡胶成为世界性的战略物资。
巴西橡胶树从播种,育苗起,经过5~8年才能开始割胶,10~20年为盛产期,30年后为衰老期,需更新,更新方法一般采用育苗芽接法栽植。
没课橡胶树每年产干胶约2.5~4KG,每亩栽25~40棵,因此每亩年产干胶量60~100KG以上。
------------------------------------------------------------------------------- 天然橡胶的品种及制法(乳胶经加工制成干胶):1)烟胶片(RSS):使用于小胶园生产,表面带有菱形花纹的棕黄色片状橡胶。
因为是以新鲜乳胶为原料,并且烟熏干燥时,烟气中的有机酸和酚类物质,对橡胶防腐和防老化有很大作用。
是天然橡胶中最好的品种。
要耗用大量木材,生产周期长,成本较高。
2)绉(zhou)胶片:①乳胶绉胶片:以乳胶为原料制成,有白绉胶片和浅色绉胶片,还有一种低级的乳黄绉胶片。
白绉胶片用分级凝固法制成,浅色绉胶片用全乳凝固法制成,颜色浅黄。
与烟胶片相比,含杂质少,但物理力学性能稍低,成本更高(尤其白绉胶片)。
用分级凝固法值得白绉胶片的同时,所得到的乳黄绉胶片,因橡胶烃含量低,为低级绉胶片,通常用作制造杂胶绉胶片的原料。
橡胶加工工艺基础知识
橡胶加工工艺基础知识一、塑炼橡胶受外力作用产生变形,当外力消除后橡胶仍能保持其形变的能力叫做可塑性。
增加橡胶可塑性工艺过程称为塑炼。
橡胶有可塑性才能在混炼时与各种配合剂均匀混合;在压延加工时易于渗入纺织物中;在压出、注压时具有较好的流动性。
此外,塑炼还能使橡胶的性质均匀,便于控制生产过程.但是,过渡塑炼会降低硫化胶的强度、弹性、耐磨等性能,因此塑炼操作需严加控制。
橡胶可塑度通常以威廉氏可塑度、门尼粘度和德弗硬度等表示。
1、塑炼机理橡胶经塑炼以增加其可塑性,其实质乃是使橡胶分子链断裂,降低大分子长度。
断裂作用既可发生于大分子主链,又可发生于侧链。
由于橡胶在塑炼时,遭受到氧、电、热、机械力和增塑剂等因素的作用,所以塑炼机理与这些因素密切相关,其中起重要作用的则是氧和机械力,而且两者相辅相成。
通常可将塑炼区分为低温塑炼和高温塑炼,前者以机械降解作用为主,氧起到稳定游离基的作用;后者以自动氧化降解作用为主,机械作用可强化橡胶与氧的接触.塑炼时,辊筒对生胶的机械作用力很大,并迫使橡胶分子链断裂,这种断裂大多发生在大分子的中间部分。
塑炼时,分子链愈长愈容易切断。
顺丁胶等之所以难以机械断链,重要原因之一就是因为生胶中缺乏较高的分子量级分。
当加入高分子量级分后,低温塑炼时就能获得显著的效果。
氧是塑炼中不可缺少的因素,缺氧时,就无法获得预期的效果。
生胶塑炼过塑炼时,设备与橡胶之间的摩擦显然使得胶温升高。
热对塑炼效果极为重要,而且在不同温度范围内的影响也不同。
由于低温塑炼时,主要依靠机械力使分子链断裂,所以在像章区域内(天然胶低于110℃)随温度升高,生胶粘度下降,塑炼时受到的作用力较小,以致塑炼效果反而下降。
相反,高温塑炼时,主要是氧化裂解反应起主导作用,因而塑炼效果在高温区(天然胶高于110℃)将随温度的升高而增大,所以温度对塑炼起着促进作用。
各种橡胶由于特性不同,对应于最低塑炼效果的温度范围也不一样,但温度对塑炼效果影响的曲线形状是相似的。
常用典型橡胶的混炼工艺特点
常用典型橡胶的混炼工艺特点橡胶的混炼就是将各种配合剂借助炼胶机机械力的作用,将各种配合剂均匀地分散在橡胶中,以形成一个以橡胶为介质或者以橡胶与某些能和它相容的配合组分(配合剂、其它聚合物)的混合物为介质,以与橡胶不相容的配合剂(如粉体填料、氧化锌、颜料等)为分散相的多相胶体分散体系的过程。
对混炼工艺的具体技术要求是:配合剂分散均匀,使配合剂特别是炭黑等补强性配合剂达到最好的分散度,以保证胶料性能一致。
混炼后得到的胶料称为“混炼胶”,其质量对进一步加工和制品质量有重要影响。
1·天然橡胶的混炼天然橡胶是生胶塑炼的主要胶种,用开炼机和密炼机进行塑炼均能获得良好效果。
用开炼机塑炼时,通常采用低温(40~50℃)薄通(辊距0.5~1mm)塑炼法和分段塑炼法效果最好。
用密炼机塑炼时,温度宜在155℃以下,时间约在13min 左右。
塑炼时间增加,塑炼胶的可塑性随之增大。
但不要过炼,否则可塑性变得过高而使物理机械性能下降。
天然橡胶塑炼时常加入促进剂M作塑解剂,来提高塑炼效果。
促进剂M对开炼机塑炼和密炼机塑炼都适用。
天然橡胶塑炼后,为使橡胶分子链得到松弛(俗称恢复疲劳)和可塑性均匀,需停放一定时间(4~8h),才能供下道工序使用。
目前国内使用的天然橡胶主要品种有:国产烟片胶和标准胶,进口烟片胶和马来西亚标准胶等。
由于上述胶种的初始门尼粘度不同,欲获得相同的可塑性,所需的塑炼时间当然不同。
其塑炼时间按长短排列的顺序为:进口烟片胶>国产烟片胶>国产标准胶>马来西亚标准胶。
恒粘和低粘标准马来西亚橡胶、充油天然橡胶、轮胎橡胶、易操作橡胶的初始门尼粘度较低(一般小于65),可不经塑炼直接混炼。
天然混炼胶(NR)具有综合性好的物理机械性能,在常温下具有很高的弹性,弹回率可达50%~85%以上。
天然胶还具有较高的机械强度,很好的耐屈挠疲劳性能,滞后损失小,多次变形下生热量低,撕裂强度高,耐磨性和耐寒性良好,以及良好的气密性、防水性、电绝缘性和绝热性。
橡胶加工工艺培训教材
橡胶的简介
2.配合剂 ★硫化剂
硫化剂是一类使橡胶由线形长链分子转变为网状大分子的物 质,这种转变称为硫化。
硫化剂:硫磺、一氯化硫、硒、碲及其氯化物、硝基化 物、有机过氧化物以及某些金属氧化物。
硫磺硫化橡胶最正确温度120~140 ℃ 。
11
橡胶的简介
★硫化促进剂
硫化促进剂可促进橡胶的硫化作用,降低硫化所需温度, 缩短硫化时间,并改善硫化胶的物理机械性能。 硫化促进剂的种类很多。无机类硫化促进剂(如氧化铅,氧 化镁等〕硫化效果较差,已被淘汰。目前主要使用有机类硫 化促进剂,
橡胶加工工艺培训教材
Contents
1
橡胶
2
橡胶的塑炼和混炼
3
压延成型
4
轮胎的简介和成型
2
橡胶的简介
生胶及其配合剂经过一系列化学与物理作用制成橡 胶制品的过程。
•胶料的组成与配合 •胶料的加工
•硫化
3
橡胶的简介
一、 胶料的组成〔生胶与配合剂〕
1.生胶 •天然胶 •合成胶:
通用合成胶:丁苯、顺丁、氯丁、丁基、聚异 戊二烯、乙丙、丁腈等。 特种合成胶:三元乙丙、氯磺化聚乙烯、氯化聚乙烯、
17
橡胶的塑炼和混炼
2. 塑炼机理
橡胶经塑炼以增加其可塑性,其实质乃是使橡胶分子链断裂, 降低大分子长度。断裂作用既可发生于大分子主链,又可发 生于侧链。由于橡胶在塑炼时,遭受到氧、电、热,机械力 和增塑剂等因素的作用,所以塑炼机理与这些因素密切相关, 其中起重要作用的那么是氧和机械力,而且两者相辅相成。
装有子午线轮胎的汽车与装有斜交胎的汽车相比,其耐磨性可提高 50%-100%,滚动阻力降低20%-30%, 可以节约油耗约6%-8%.
- 1、下载文档前请自行甄别文档内容的完整性,平台不提供额外的编辑、内容补充、找答案等附加服务。
- 2、"仅部分预览"的文档,不可在线预览部分如存在完整性等问题,可反馈申请退款(可完整预览的文档不适用该条件!)。
- 3、如文档侵犯您的权益,请联系客服反馈,我们会尽快为您处理(人工客服工作时间:9:00-18:30)。
天然橡胶的合成和加工工艺
天然橡胶是一种重要的工业原料,广泛应用于汽车轮胎、胶管、导电垫等领域。
虽然人工合成橡胶已经取得了许多进展,但天然橡胶仍然是不可或缺的。
本文将探讨天然橡胶的合成和加工工艺。
一、天然橡胶的合成
天然橡胶是从橡胶树中提取的一种乳液,主要成分是聚异戊二烯。
橡胶树在干
燥季节里,通过在其樱果上割口,让橡胶树的乳液从这些樱果中流出,最后将这些乳液自然地凝固成块,形成自然橡胶。
然而,这种方法的生产效率低,同时橡胶树的种植和维护也需要大量的时间和
资金。
为了提高生产效率,人们研究出了其他的橡胶合成方法。
在第二次世界大战期间,人们开发出了一种合成橡胶的方法,即使用合成乳胶。
合成乳胶是一种液态聚合物,类似于橡胶树释放的乳液。
这种方法比起从橡胶树中提取天然橡胶效率更高,产量更大。
二、天然橡胶的加工工艺
天然橡胶通常用于制造各种橡胶制品,包括橡胶管、轮胎、电线、密封件等。
在加工橡胶前,需要将其成行的胶块先切成小块,然后通过加热、充填、挤出、模压等工艺,使其成为所需形状的制品。
1. 加热
加热是加工天然橡胶的首要工艺。
在加热过程中,胶块变得更加柔软,更容易
进行后续的加工。
通常,将橡胶加热到适当的温度,然后快速地冷却,这样可以降低橡胶的黏度。
2. 充填
充填指将加热的橡胶填充到所需形状的模具中。
充填时需要考虑橡胶弹性、流动性等特性,以精确地填充到模具内部。
3. 挤出
挤出是将橡胶通过一系列滚筒和挤出机器,挤出成特定截面的橡胶型材或气密型材的过程。
4. 模压
模压是针对需要大量生产的橡胶制品,在特定的模具中将橡胶加工成所需形状和尺寸的过程。
这种方法需要特殊的模具和压力机器。
综上所述,天然橡胶是重要的工业原料之一,虽然存在一些合成天然橡胶的方法,但自然的天然橡胶仍然是不可或缺的。
对于加工天然橡胶而言,加热、充填、挤出和模压是不可或缺的工艺。