陶瓷工艺学--6坯体的干燥-0910
陶瓷工艺学第六章坯、釉料制备
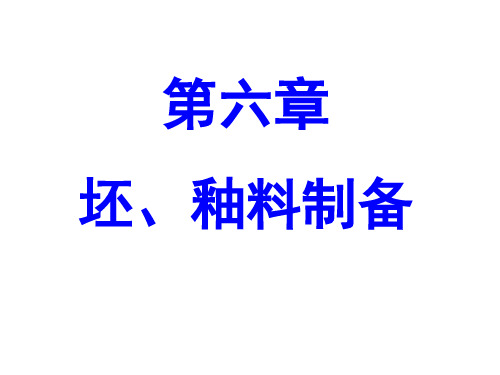
二、生料釉制备 生料釉制备流程参见P309-310。
三、熔块釉料制备 熔块釉料制备流程参见P311。
第四节 坯釉料制备的主要工序及设备
本节主要内容: 一、原料粉碎 二、筛分 三、除铁 四、泥浆脱水 五、陈腐与练泥
一、原料粉碎
块状的固体物料在机械力的作用下而破碎使块度 或粒度达到要求,这种原料的处理操作,即为原 料粉碎。
坯料制备新工艺: 天然原料加工专业化和质量标准化; 采用喷雾干燥代替压滤脱水; 采用电子计算机配料及控制。
(二)日本的塑性坯料制备 日本对原料要求很严格,非常注重原料的研究工
作,他们认为没有标准化的原料,就谈不上后续 工序的产品品质。所有原料都按标准精制,并分 为高级、中级、低级,按质论价。
(二)注浆坯料的品质要求
①泥浆流动性要好,含水量要少。一般泥浆含水量 在28%~38%,含水量过高,要获得厚度符合要求的 坯体,则泥浆在模型中停留时间过长,并是非可塑性 原料颗粒沉降,致使泥浆分层,造成废品;含水量过 少则难于获得粘度相当低的泥浆,粘稠泥浆流动性差, 不能充分注满到模型中的各部位,易产生废品。
坯料的可塑性主要取决于强可塑性粘土的用量,而 瘠性原料如长石、石英等会降低坯料的可塑性。
2、含水量
坯料的含水量应适宜,分布应均匀。对于大型器 皿,手工成形,水分含量在23%~25%;一般器皿,旋 压成形,水分含量在21%~23%;一般器皿,滚压成形, 水分含量在19%~24%。 3、细度
坯料的细度要求能够通过万孔筛,即筛下的颗粒 粒径均小于0.06mm。生产中以通过万孔筛筛余量来控 制,一般要求筛余在0.2%~1%。坯料达到这样的细度, 具有足够大的总表面积,扩大了颗粒之间的接触面,使 各组分之间达到充分混合,提高混合的均匀度。这样在 成瓷过程中能加快固相反应的速度,降低成瓷温度,提 高瓷质强度,改善瓷的半透明度。细度主要是通过研磨 时间来控制。
陶瓷坯料干燥
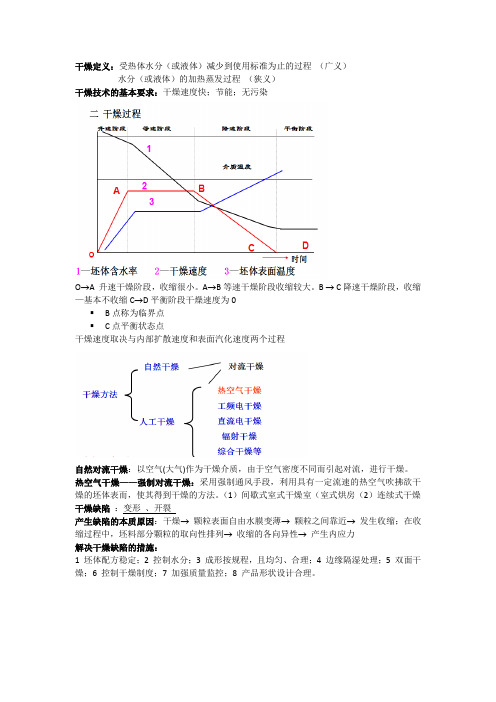
干燥定义:受热体水分(或液体)减少到使用标准为止的过程(广义)
水分(或液体)的加热蒸发过程(狭义)
干燥技术的基本要求:干燥速度快;节能;无污染
O→A 升速干燥阶段,收缩很小。
A→B等速干燥阶段收缩较大。
B → C降速干燥阶段,收缩—基本不收缩C→D平衡阶段干燥速度为0
▪B点称为临界点
▪C点平衡状态点
干燥速度取决与内部扩散速度和表面汽化速度两个过程
自然对流干燥:以空气(大气)作为干燥介质,由于空气密度不同而引起对流,进行干燥。
热空气干燥——强制对流干燥:采用强制通风手段,利用具有一定流速的热空气吹拂欲干燥的坯体表而,使其得到干燥的方法。
(1)间歇式室式干燥室(室式烘房(2)连续式干燥干燥缺陷:变形、开裂
产生缺陷的本质原因:干燥→颗粒表面自由水膜变薄→颗粒之间靠近→发生收缩;在收缩过程中,坯料部分颗粒的取向性排列→收缩的各向异性→产生内应力
解决干燥缺陷的措施:
1 坯体配方稳定;
2 控制水分;
3 成形按规程,且均匀、合理;
4 边缘隔湿处理;
5 双面干燥;
6 控制干燥制度;
7 加强质量监控;
8 产品形状设计合理。
浅析陶瓷高湿坯体的干燥机理及模式

浅析陶瓷高湿坯体的干燥机理及模式技术创造第一生产力,随着现代科技的进步,陶瓷机械行业正发生着日新月异的变化。
陶机的发展给陶瓷生产带来了极大的便利,并革命性地提高了陶瓷的品质。
品质的提升又给陶机提出了更高的要求,两者之间的需求平衡不断被打破,才有了今天陶瓷及陶瓷机械行业一派繁荣的景象。
但繁荣背后也存在一些不足,如一些传统陶瓷产品的部分生产环节依旧延续着80年代的生产工艺,一些新兴产品因某个生产环节脱钩而无法保证其品质。
目前,陶瓷高湿坯体的干燥情况是陶瓷行业需要共同探讨的问题之一。
2 陶瓷高湿坯体的干燥发展状况及出现的问题卫生洁具干燥成形后需放置5~10天,此时含水率约为8%~10%,然后再放入烘干房内1~2天,此时制品已完全干燥。
整个过程耗费了大量的时间与人力,同时这种干燥方式受气候的影响较大,很难保证产品的品质。
其它的高湿坯体,如新兴起的环保建材陶板、传统的西瓦及耐火材料硼板坩锅等干燥周期也较长。
如今在多年从业经验的基础上以及引入国外同行的先进理念,在高湿坯的干燥难题上终于有所突破。
高湿坯体在快速干燥过程中出现的各种开裂和变形等问题。
其主要原因为:干燥过快导致产品内外的含水量相差较大,造成坯体内外收缩不一致,从而导致坯体变形、开裂。
其根本原因是:坯体含水量对坯体体积的影响。
一般地,坯体含水量对体积的影响在一个定量前后相差很大,我们称这个含水量为临界含水量,其值为8%左右(受坯体工艺配方影响)。
如果坯体含水量小于8%时,含水量的变化对体积的影响较小。
因此,在快速干燥过程中合理地控制干燥速度就不易出现坯体变形、开裂等缺陷。
例如,目前墙地砖的成形水分都控制在7%左右,其干燥周期可控制范围为30~90min(坏体越厚需时越长)。
因此,当坯体含水量低于8%以后,可以采用一些现有的干燥手段进行快速干燥。
当坯体中的水分处于临界含水量时,坯体内外的含水量相差较大,对坯体体积的影响较大,内外体积变化不一,易致坯体变形、开裂。
(陶瓷科学与工艺学)第五章3塑性成型及其它成型方法干燥
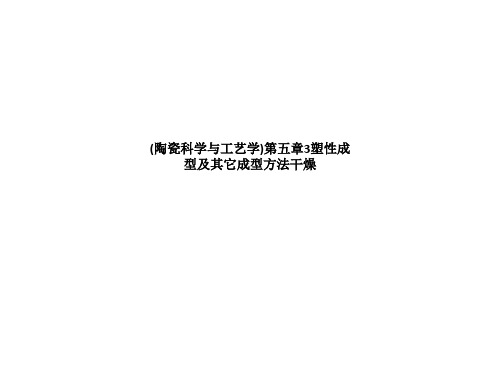
工频电干燥 热源为工频电流。当工频电 流通过湿坯,坯内产生热量 使水分蒸发
坯体内外同时加热,受热均匀,热湿扩 散方向一致,干燥效率高,热损耗少, 设备简单易控制,适合大件厚坯制品
微波干燥
以高频率长波长的电磁波为 热源,通过微波辐射坯体使 其内部极性水分子剧烈运动 并摩擦生热使水分排除
坯体内外同时受热,加热均匀快速,热 湿扩散方向一致,干燥效率和质量高, 设备体小轻巧,易自控,费用高,电耗 大,需避免微波辐射危害,使用范围广
平衡阶段:当坯体干燥到表 面水分达到平衡水分时,干 燥速度降为零。此时坯体与 周围介质达到平衡状态,平 衡水分的多少与周围介质的 温度、相对湿度和坯料组成 有关。坯体的干燥最终水分 一般说来不应低于贮存时的 平衡水分,否则干燥后将再 吸收水分达到平衡水分。
2.6.2干燥制度
干燥制度是砖坯进行干燥时的条件总和。它包括干燥时间、进入和排出干燥剂的温 度和相对湿度、砖坯干燥前的水分和干燥终了后的残余水分等。
降速阶段:随着坯体中水分 的不断蒸发,坯体含水量逐 渐降低,当降至K点时,坯 体内部向表面补充的水分少 于表面蒸发的水分,即内扩 散速度小于外扩散速度。这 样坯体向外界蒸发的水分逐 渐减少,所需热量也减少。 因此干燥速度逐渐降低,坯 体温度逐渐升高。此阶段坯 体体积收缩很小或不收缩, 水分排除形成气孔,使坯 体气孔率上升。
5
10
15
20
25
自由含水率(%)
空气流动速度与干燥速度的关系
干燥方法
干燥方法 热源及加热原理
应用范围与特点
热空气干燥
以热空气为热源;热气体通 热量传递方向与水分扩散方向相反,干 过对流传热将热量传给坯体, 燥效率低,设备简单,热源易得便于控 热量由表及里传递,水分由 制,适合传统陶瓷小件产品的干燥 里及表扩散
无机材料工艺学-陶瓷5-干燥与烧成

4.2 坯体在烧成过程中的物理化学变化
烧成是对陶瓷生坯进行高温焙烧,使之发生质变成为陶瓷
成品的过程。其间,坯釉将发生一系列物理化学变化,形 成一定的矿物组成和显微结构,并获得所要求的性能。 陶瓷制品在窑炉内的加热过程,一般分为:低温阶段、氧化分解 阶段、高温及保温阶段、冷却阶段——四个依次进行又相互联系 的阶段。各个阶段发生的物理化学反应情况,主要取决于坯体的 化学组成,以及烧成温度和烧成气氛等因素。 ▴ 下面以粘土质普通陶瓷制品(即以粘土、长石、石英为主要原 料配制)烧成为例,说明坯体在烧成过程中各个阶段的物理化学
4.1 坯体的干燥
一、坯体中的水分
▴ 干燥过程仅能排除全部自由水和部分吸附水。 ▴ 在干燥过程中,自由水排出时,会引起物料颗粒靠扰,因而 表现出坯体的体积收缩。吸附水的排除不会引起体积收缩。
二、干燥机理及干燥过程
(一)干燥机理
在对流干燥过程中,热风与坯体之间既有传热过程,又有传质
过程,而传质过程又包括外扩散和内扩散两部分。
(三)高温阶段(950℃ ~烧成温度)
3. 形成大量液相和莫来石晶体。 (1)随着温度的升高, 在此阶段将出现大量液
相 , 并 加 速粘 土 与 石 英
等难熔矿物的溶解。至 1000℃ 以 上 , 坯 体 中 的 石英和粘土颗粒已被明 显溶蚀。
1— 石英 2— 长石 3— 液相 4— 粘土矿物
1 2 1 3 2 4
3. 形成大量液相和莫来石晶体。 ● 长石作为熔剂矿物的重
要作用:(1)长石熔体促
进难熔矿物(如粘土、石英 等)溶解,加速固相反应, 促进一次莫来石的生成;同 时填充空隙,使坯体致密化。 (2)导致针状二次莫来石 的形成。