铸轧铝带坯常见缺陷原因分析及消除方法
铸铝转子的常见缺陷及原因分析课件

案例分析与讨论
结合具体案例,对铸铝转子缺陷进行 分析和讨论,加深学员对理论知识的 理解和应用。
02 铸铝转子常见缺 陷类型
气孔
形成原因
影响:降低铸件的致密性,减少有效承 载面积,可能导致铸件在使用过程中提 前失效。
模具预热不足或模具温度过高。
铝液含氢量过高。
浇注系统设计不合理,导致气体不能及 时排出。
促进技术交流
课件可作为企业内部或行 业内的技术交流资料,促 进经验分享和技术进步。
课件内容概述
铸铝转子常见缺陷类型
介绍铸铝转子生产过程中常见的缺陷 类型,如气孔、缩孔、裂纹等。
缺陷原因分析
针对每种缺陷类型,深入分析其产生 的原因,如原材料质量、工艺参数、 操作规范等。
改进措施及预防方法
提出针对性的改进措施和预防方法, 如优化工艺参数、加强原材料质量控 制、提高操作水平等。
选用优质铝锭
确保铝锭成分均匀、无杂质,降低气孔、夹杂等 缺陷的产生。
控制回炉料比例
合理ห้องสมุดไป่ตู้配新料与回炉料,避免过多使用回炉料导 致成分波动和性能下降。
加强原材料检验
对每批次的原材料进行严格检验,确保质量符合 要求。
优化铸造工艺参数
调整熔炼温度
01
控制熔炼温度在合理范围内,避免过高温度导致铝液氧化和吸
应力腐蚀
铸铝转子在受到应力和腐蚀介质的共同作用时,容易发生 应力腐蚀开裂。这种开裂往往从表面开始,逐渐向内部扩 展,对铸件的耐腐蚀性能产生严重影响。
晶间腐蚀
由于晶界处的能量较高,容易成为腐蚀的敏感区域。晶间 腐蚀会导致晶粒间的结合力减弱,从而降低铸件的耐腐蚀 性能。
05 缺陷预防措施与 改进建议
铸铝件出现缺陷的原因有哪些

铸铝件出现缺陷的原因有哪些铸铝件是一种常见的工业制品,应用广泛。
然而,它们在生产过程中经常出现各种缺陷,这些缺陷可能会影响生产效率、产品质量、甚至会对人的安全造成威胁。
本文将就铸铝件出现缺陷的原因进行探讨。
1.金属液体的不完全流动铸铝件的生产需要通过铸造技术的注入工艺,在金属液体凝固之前,将金属液体注入铸型中。
如果注入时金属液体未能完全流动,铸铝件中就会出现针孔、气孔、夹杂物等缺陷。
导致这种情况的原因可能是铸型准备不充分、铸造工艺过程控制不当,或者金属液体的流动性能欠佳。
2.金属液体和模具表面产生反应在铸铝件生产过程中,金属液体会和模具表面产生反应,这会导致表面缺陷、裂纹、潜在缺陷等问题。
这种反应的产生可能源于模具表面材料选择的不合适,或者模具表面处理不当。
3.杂质和氧化物金属液体中的杂质和氧化物可能导致铸铝件表面粗糙或出现孔洞。
与此相关的因素包括金属载体的质量、金属液体的成分组成和处理方式,以及熔炼和处理过程中的环境因素(如空气中的湿度和温度)。
4.铸造工艺的不合理铸造工艺的控制是铸铝件生产中至关重要的一环。
过渡浇口或计划不良的浇注过程可能会引起内部缺陷或表面缺陷。
如果浇口过小或规划不良,就会导致金属液体工作室的决堤现象,或者其他压力变化,从而引起铸造缺陷。
5.模具和工装的磨损寿命长、使用时间长的模具和工装会出现磨损并且减少铸造质量。
模具磨损可以导致表面缺陷、裂纹和尺寸不准确等问题。
由于磨损会影响精度和表面的光洁度,所以模具需要定期检查和维护。
6.温度和湿度温度和湿度变化可能会影响铸造产品的质量。
温度的变化可能会引起塑性变形,从而改变产品的形状和尺寸。
湿度的变化可能会对表面质量产生负面影响。
结论铸铝件是一种重要的工业产品,但制造出高质量的铸铝件需要全面考虑上述因素。
如果生产时无法控制或纠正上述因素以及其他因素,铸铝件就容易出现各种缺陷。
因此,在生产铸铝件的同时,应定期检查设备和工具状态,确保生产过程具有可维护性、可重复性和可预测性。
铝合金铸造常见缺陷与对策

(4)增大充型压力。
4、凹陷: 特征:在平滑表面上出现的凹陷部分。
形成原因:
(1)铸件结构不合理,在局部厚实部位产生热节。
(2)合金收缩率大。
(3)浇口截面积太小。
(4)模温太高。
防止方法:
(1)改进铸件结构,壁厚尽量均匀,多用过渡性连接,厚实部位可用镶件消除热节。
(2)减小合金收缩率。
(9)调整慢速充型和快速充型的转换点。
7、缩孔特征:铸件在冷凝过程中,由于内部补偿不足所造成的形状不规则,表面粗糙的孔 洞。
形成原因:
(1)铝液浇铸温度高。
(2)铸件结构壁厚不均匀,产生Байду номын сангаас节。
(3)补缩压力低。
(4)内浇口较小。
(5)模具的局部温度偏高。
防止方法:
(1)遵守作业标准,降低浇铸温度。
(2)改进铸件结构,消除金属积聚部位,缓慢过渡。
(2)确定最佳开模时间,增加铸件刚性。
(3)放大铸造斜度。
(4)取放铸件应小心,轻取轻放。
(5)放置在空气中缓慢冷却。
10、错位
特征:铸件一部分与另一部分在分型面错开,发生相对位移。 形成原因:
(1)模具镶块位移。
(2)模具导向件磨损。
(3)模具制造、装配精美度。
防止方法:
(1)调整镶块加以紧固。
(2)交换导向部件。
(3)涂料太厚或何温性能差,则擦干净涂料后再补喷。
(4)缩短铸造周期。
C环缩松:
(1)推迟或关掉轮网与辐条交接处风道。
(2)上模辐条补喷保温涂料,涂料太厚擦干净重喷。
(3)可适当加快充型速度。
辐条根部(辐条与轮网交接处)
(1)在上模对应处拉排气线。
铸造中常见缺陷及其处理方法
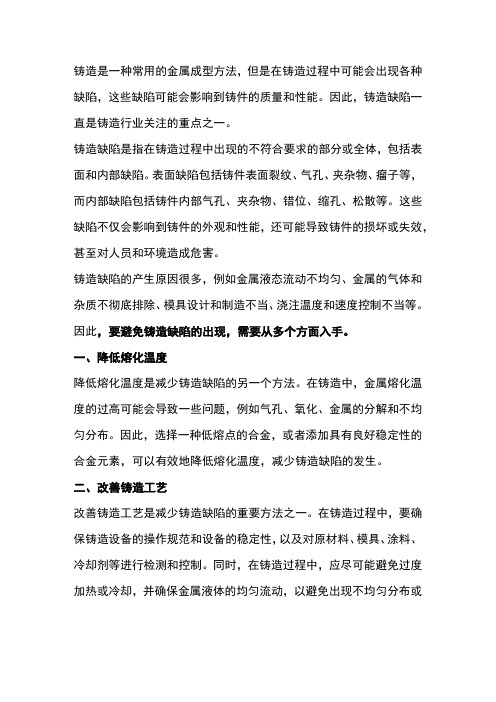
铸造是一种常用的金属成型方法,但是在铸造过程中可能会出现各种缺陷,这些缺陷可能会影响到铸件的质量和性能。
因此,铸造缺陷一直是铸造行业关注的重点之一。
铸造缺陷是指在铸造过程中出现的不符合要求的部分或全体,包括表面和内部缺陷。
表面缺陷包括铸件表面裂纹、气孔、夹杂物、瘤子等,而内部缺陷包括铸件内部气孔、夹杂物、错位、缩孔、松散等。
这些缺陷不仅会影响到铸件的外观和性能,还可能导致铸件的损坏或失效,甚至对人员和环境造成危害。
铸造缺陷的产生原因很多,例如金属液态流动不均匀、金属的气体和杂质不彻底排除、模具设计和制造不当、浇注温度和速度控制不当等。
因此,要避免铸造缺陷的出现,需要从多个方面入手。
一、降低熔化温度降低熔化温度是减少铸造缺陷的另一个方法。
在铸造中,金属熔化温度的过高可能会导致一些问题,例如气孔、氧化、金属的分解和不均匀分布。
因此,选择一种低熔点的合金,或者添加具有良好稳定性的合金元素,可以有效地降低熔化温度,减少铸造缺陷的发生。
二、改善铸造工艺改善铸造工艺是减少铸造缺陷的重要方法之一。
在铸造过程中,要确保铸造设备的操作规范和设备的稳定性,以及对原材料、模具、涂料、冷却剂等进行检测和控制。
同时,在铸造过程中,应尽可能避免过度加热或冷却,并确保金属液体的均匀流动,以避免出现不均匀分布或过热的情况,从而减少铸造缺陷的发生。
三、质量检测和控制质量检测和控制是减少铸造缺陷的关键步骤之一。
在铸造完成后,应对铸件进行全面的检测和控制包括X射线检测、超声波检测、金相分析、硬度测试等。
通过这些检测和控制方法,可以及时发现铸造缺陷,及时采取措施进行修复或重新铸造,从而保证铸件的质量和稳定性。
四、培养专业人才铸造行业的专业人才对于减少铸造缺陷的重要性不言而喻。
铸造行业需要拥有一批专业的技术人员和工人,他们能够理解和掌握铸造技术的各个方面,并能够在实践中灵活应对各种情况。
因此,铸造企业应该加强人才培养和引进工作,提高行业整体素质,从而减少铸造缺陷的发生。
铝合金铸造常见缺陷与对策

铝铸件常见缺陷及整改办法铝铸件常见缺陷及整改办法1、欠铸(浇不足、轮廓不清、边角残缺):形成原因:(1)铝液流动性不强,液中含气量高,氧化皮较多。
(2)浇铸系统不良原因。
内浇口截面太小。
(3)排气条件不良原因。
排气不畅,涂料过多,模温过高导致型腔内气压高使气体不易排出。
防止办法:(1)提高铝液流动性,尤其是精炼和扒渣。
适当提高浇温和模温。
提高浇铸速度。
改进铸件结构,调整厚度余量,设辅助筋通道等。
(2)增大内浇口截面积。
(3)改善排气条件,增设液流槽和排气线,深凹型腔处开设排气塞。
使涂料薄而均匀,并待干燥后再合模。
2、裂纹:特征:毛坯被破坏或断开,形成细长裂缝,呈不规则线状,有穿透和不穿透二种,在外力作用下呈发展趋势。
冷、热裂的区别:冷裂缝处金属未被氧化,热裂缝处被氧化。
形成原因:(1)铸件结构欠合理,收缩受阻铸造圆角太小。
(2)顶出装置发生偏斜,受力不匀。
(3)模温过低或过高,严重拉伤而开裂。
(4)合金中有害元素超标,伸长率下降。
防止方法:(1)改进铸件结构,减小壁厚差,增大圆角和圆弧R,设置工艺筋使截面变化平缓。
(2)修正模具。
(3)调整模温到工作温度,去除倒斜度和不平整现象,避免拉裂。
(4)控制好铝涂成份,成其是有害元素成份。
3、冷隔:特征:液流对接或搭接处有痕迹,其交接边缘圆滑,在外力作用下有继续发展趋势。
形成原因:(1)液流流动性差。
(2)液流分股填充融合不良或流程太长。
(3)填充温充太低或排气不良。
(4)充型压力不足。
防止方法:(1)适当提高铝液温度和模具温度,检查调整合金成份。
(2)使充填充分,合理布置溢流槽。
(3)提高浇铸速度,改善排气。
(4)增大充型压力。
4、凹陷:特征:在平滑表面上出现的凹陷部分。
形成原因:(1)铸件结构不合理,在局部厚实部位产生热节。
(2)合金收缩率大。
(3)浇口截面积太小。
(4)模温太高。
防止方法:(1)改进铸件结构,壁厚尽量均匀,多用过渡性连接,厚实部位可用镶件消除热节。
铸铝工业件常见缺陷及分析一氧化夹渣缺陷特征

.;.铸铝工业件常见缺陷及分析一氧化夹渣缺陷特征1.氧化夹渣多分布在铸件的上表面,在铸型不通气的转角部位。
断口多呈灰白色或黄色,经x光透视或在机械加工时发现,也可在碱洗、酸洗或阳极化时发现产生原因:1.炉料不清洁,往返炉料使用量过多2.浇注系统设计不良3.合金液中的熔渣未清除干净4.浇注操作不当,带渗透夹渣5.精炼变质处理后静置时间不够。
防止方法:1.炉料应经过吹砂,回炉料的使用量适当降低 2.改进浇注系统设计,提高其挡渣能力 3.采用适当的熔剂去渣4.浇注时应当平稳并应注重挡渣5.精炼后浇注前合金液应静置一定时间二气孔气泡缺陷特征:铸铝加工使壁内气孔一般呈圆形或椭圆形,具有光滑的表面,一般是发亮的氧化皮,有时呈油黄色。
表面气孔、气泡可通过喷砂发现,内部气孔气泡可通过X光透视或机械加工发现。
气孔气泡在X光底片上呈黑色产生原因:1.浇注合金不平稳,卷入气体2.型(芯)砂中混渗入渗出有机杂质(如煤屑、草根马粪等)3.铸型和砂芯通气不良4.冷铁表面有缩孔5.浇注系统设计不良.防止方法:1.正确掌握浇注速度,避免卷入气体。
2.型(芯)砂中不得混渗透有机杂质以减少造型材料的发气量 3.改善(芯)砂的排气能力4.正确选用及处理冷铁5.改进浇注系统设计三缩松缺陷特征:铸铝件缩松一般产生在内浇道附近飞冒口根部厚大部位、壁的厚薄转接处和具有大平面的薄壁处。
在铸态时断口为灰色,浅黄色经暖处理后为灰白浅黄或灰黑色在x光底片上呈云雾状严重的呈丝状缩松可通过X光、荧光低倍断口等检查方法发现。
产生原因:1.冒口补缩作用差2.炉料碳硫分析仪含气量太多3.内浇道附近过暖4.砂型水分过多,砂芯未烘干5.合金晶粒粗大6.铸铝件在铸型中的位置不当7.浇注温度过高,浇注速度太快。
防止方法:1.从冒口补浇金属液,改进冒口设计2.炉料应清洁无腐蚀3.铸铝件缩松处设置冒口,安放冷铁或意气消沉铁与冒口联用4.控制型砂水分,和砂芯干燥5.采取细化品粒的措施6.改进铸件在铸型中的位置,降低浇注温度和浇注速度。
铝铸件孔洞解决方案(3篇)
第1篇一、引言铝铸件作为现代工业中广泛应用的一种材料,具有重量轻、耐腐蚀、导电导热性好等特点。
然而,在铝铸件的生产过程中,孔洞缺陷是常见的问题,严重影响了铸件的质量和性能。
本文将针对铝铸件孔洞问题,从原因分析、预防措施和解决方案三个方面进行详细阐述。
二、铝铸件孔洞原因分析1. 材料原因(1)合金成分不合适:铝铸件孔洞产生的一个重要原因是合金成分不合适,如铝硅合金中的硅含量过高,会导致缩孔、气孔等缺陷。
(2)杂质含量过高:铝铸件中的杂质含量过高,会导致孔洞、夹渣等缺陷。
常见的杂质有铁、铜、硅等。
2. 工艺原因(1)熔炼工艺:熔炼过程中,熔体温度过高或过低、熔炼时间过长等,都会导致孔洞缺陷的产生。
(2)浇注工艺:浇注速度过快、浇注温度过低等,都会使铸件产生孔洞缺陷。
(3)模具设计:模具设计不合理,如浇注系统设计不合理、模具排气不畅等,会导致孔洞缺陷。
3. 操作原因(1)操作不规范:在熔炼、浇注、冷却等过程中,操作不规范会导致孔洞缺陷的产生。
(2)设备维护不当:设备维护不当,如模具、熔炼炉等,会导致孔洞缺陷。
三、铝铸件孔洞预防措施1. 优化合金成分(1)根据铸件性能要求,选择合适的合金成分,如铝硅合金中硅含量应控制在合适范围内。
(2)严格控制合金中的杂质含量,如铁、铜、硅等。
2. 优化熔炼工艺(1)控制熔炼温度,避免过高或过低。
(2)缩短熔炼时间,减少熔体氧化。
(3)加强熔炼过程中的搅拌,确保熔体均匀。
3. 优化浇注工艺(1)控制浇注速度,避免过快。
(2)提高浇注温度,保证铸件凝固良好。
(3)优化浇注系统设计,确保熔体顺利流动。
4. 优化模具设计(1)设计合理的浇注系统,确保熔体顺利流动。
(2)优化模具排气系统,保证铸件内部无气体残留。
(3)提高模具材料性能,延长模具使用寿命。
5. 规范操作(1)加强操作人员培训,提高操作技能。
(2)严格执行操作规程,避免不规范操作。
(3)加强设备维护,确保设备正常运行。
铸坯出现大凹陷缺陷的原因及措施
在连铸的生产中,铸坯凹陷的发生频率很高,不但影响铸坯的合格率,严重时还会造成生产事故。
铸坯凹陷主要有两类:一类是产生于结晶器内的“小凹陷”;一类是产生于扇形段内的“大凹陷”。
本文主要介绍大凸陷的原因及补救措施。
1、形貌
铸坯大凹陷产生于扇形段中,宽度一般贯穿整个面,深度5-50mm(甚至更深),沿着铸坯的浇铸方向连续分布,如果不及时处理长度可以延续几个班次。
2、原因
铸坯大凹陷的产生主要原因是扇形段积渣。
铸坯大凹陷中心随着扇形段积渣,中心位置的变化而变化,越靠近结晶器下口大凹陷的深度越深。
解决大凹陷的关键是,解决扇形段积渣问题。
扇形段积渣的原因有:扇形段辊子变形、扇形段开口度不合适、扇形段对弧偏差、喷嘴堵塞、辊子表面质量不好。
3、措施
1)严格扇形段的上线标准。
保证每一个上线的扇形段开口度、弧度不超过20道,辊子表面光滑平整、辊子转动自由。
在对弧过程中采用多点对弧,辊子对弧达标后,旋转夹角为90度的面再进行对弧,保证每个辊子四个点都达到标准要求。
对线下辊子变形程度和表面平整度进行检测,发现超标的辊子立即报废。
2)扇形段在使用过程中杜绝出现喷嘴堵塞的现象。
3)对辊子进行改造,将原有的辊子全部改成水冷的,减少辊子受热膨胀变形的机率,在保证强度的同时将辊子改成五段凹槽辊,降低辊子积渣的面积,增大辊子的散热速度,同时保证每个辊子润滑点的油路畅通和润滑的油量消耗,辊子表面光滑平整。
方坯铸坯缺陷产生原因及预防措施
答辩论文方坯铸坯缺陷产生原因及预防措施沈阳东洋制钢有限公司炼钢厂陈世峰2008.6.19方坯铸坯缺陷产生原因及预防措施1.前言由于连铸坯质量问题多发于连铸,因此对连铸质量缺陷进行了分析,总结出发生原因,以减少连铸坯质量问题的发生。
2.铸坯主要有以下几种缺陷: 2.1卷渣2.1.1表面卷渣(见图1) 2.1.2内部卷渣(见图2)图1 图22.2裂纹2.2.1表面裂纹:头部表面裂纹(图3 )、尾部表面裂纹(见4) 。
图3 图42.2.2内部裂纹(见图5)图52.3气泡缺陷(见图6、见图7)Array Array图6 图73、缺陷产生原因及预防措施3.1卷渣产生原因及预防措施3.1.1表面卷渣产生原因及预防措施产生原因:(1)结晶器内形成渣条,当结晶器内钢液面波动量大于熔渣层厚度时、或挑渣条未挑净时、或在挑渣条过程中将渣条带入结晶器坯壳上时形成卷渣。
(2)在换包或等包降速过程中,由于操作不当造成中包液位较浅,导致中包内钢液形成涡流将中包渣卷进结晶器内,在上浮过程中被坯壳捕作形成卷渣。
(3)调整渣线高度超过液渣层厚度、或有渣条未挑净、等原因时造成颗粒渣被卷到坯壳上而形成卷渣。
(4)在开浇升速前液渣厚度未达到标准,造成颗粒渣或予熔层的保护渣直接与钢液接触,升速过程中在结晶器内造成钢液面发生波动,导致保护渣被卷入到坯壳上,形成卷渣。
(5)中包掉料或有杂物,开浇过程中被钢水冲到结晶器内,从而形成卷渣。
(6)中包内钢液面剧烈波动时,造成中包内覆盖剂被卷入中包钢液中,此时被卷入的覆盖剂受两个力作用:向上的钢水的浮力和向下的钢流股吸力作用,当向下的钢流股吸力大于向上钢水的上浮力时,卷入的覆盖剂就被卷入到结晶器内,在钢流流股的作用下,如被坯壳捕作而形成皮下卷渣,如被向下流股带入液相穴深处而形成内部卷渣。
(7)挑渣条用8#钢线(或细铁线),在钢线上结钢瘤或渣块,有钢瘤的8#线熔断到结晶器钢液内部,如被坯壳捕作到而形成皮下卷渣,如进入液相穴深处而形成内部卷渣。
铸造缺陷及其解决方法
铸造缺陷及其解决方法
铸造缺陷是指制造过程中铸造件表面或内部所出现的不良现象,如气孔、夹杂、疏松、缩孔、热裂、变形等。
下面是一些常见的铸造缺陷及其解决方法:
1.气孔:造成气孔的原因有很多,如铸造温度过高、金属液中杂质含量过多等。
解决方法可以采用减少铸造温度、加入消泡剂、熔炼清洁等措施。
2.夹杂:夹杂通常是指铸造件中未能完全融化的金属,常见于不锈钢等高合金材料。
解决方法可以采用改善合金化学成分、掌握铸造温度和速度等。
3.疏松:疏松是指铸造件中出现的弱点或空隙,通常是由于铸造温度不均匀或金属流动不畅造成。
解决方法可以采用加大浇口、改善铸型、增强金属流动等。
4.缩孔:缩孔是指铸造件中因金属凝固不充分而形成的孔洞,通常出现在铸造件中央。
解决方法可以采用增加浇口、改善铸型、增大斜率等。
5.热裂:热裂是指铸造件在冷却过程中发生的裂纹,通常是由于金属结构不稳定或温度变化过大造成。
解决方法可以采用改善铸造温度和速度、提高金属质量等。
6.变形:变形通常是指铸造件在冷却过程中发生的形变,通常是由于铸造温度、铸型或金属流动不均造成。
解决方法可以采用优化铸造参数、改善铸造过程等措
施。
- 1、下载文档前请自行甄别文档内容的完整性,平台不提供额外的编辑、内容补充、找答案等附加服务。
- 2、"仅部分预览"的文档,不可在线预览部分如存在完整性等问题,可反馈申请退款(可完整预览的文档不适用该条件!)。
- 3、如文档侵犯您的权益,请联系客服反馈,我们会尽快为您处理(人工客服工作时间:9:00-18:30)。
铸轧铝带坯常见缺陷原因分析及消除方法袁蔚【摘要】文章根据双辊式连续铸轧法生产铸轧铝带坯的生产工作原理,结合现场生产实践,对铸轧铝带坯的几种常见缺陷进行总结,分析了其产生的原因并提出了相应的消除方法,目的是减少废料量、提高成品率、降低生产成本,同时提高企业竞争力.【期刊名称】《有色金属加工》【年(卷),期】2018(047)001【总页数】6页(P11-16)【关键词】双辊式连续铸轧法;铸轧铝带坯;工艺参数;缺陷;原因;消除方法【作者】袁蔚【作者单位】中色科技股份有限公司,河南洛阳471039【正文语种】中文【中图分类】TG249.9双辊式连续铸轧法生产铸轧铝带坯是指液态金属直接在两旋转辊间结晶,并同时进行加工成型的板带坯料的一种生产方法。
因其生产工艺简单、建设周期短、生产成本低、投资少及占地面积小等优点,自上世纪50年代初由美国亨特公司最先开发应用以来,世界各国争先效仿研制,此技术得到了广泛发展[1-2]。
我国从上世纪60年代开始研究此技术生产铸轧铝带坯并制造铸轧机设备,经过多年的探索与研发,其核心技术及设备已达到国际先进水平。
但在铝带坯铸轧生产过程中,铸轧铝带坯仍会出现很多缺陷,而大部分缺陷主要是因工艺参数控制不当而产生的。
随着国民经济的发展以及人民生活水平的提高,各行业对冷轧铝板带箔的质量要求越来越高,这也必将对铸轧铝带坯生产厂家提出更为严格的供坯要求,不允许铸轧铝带坯出现任何缺陷。
1 连续铸轧工作原理连续铸轧过程是在两个相对旋转的内部通水冷却的铸轧辊辊缝间连续不断地输入液态金属,通过冷却、铸造,直接连续轧出铸轧铝带坯,如图1所示。
图1 连铸连轧工作原理图Fig.1 Working principle diagram of continuous casting and rolling此种工艺的显著特点是,两个内部通水冷却的旋转铸轧辊作为结晶器,铝熔体在铸轧辊辊缝间在很短的时间内完成凝固和热轧变形两个过程。
此工艺生产出的铝带坯废料损失少,成品率高,生产工序少,周期短,生产效率高。
2 影响铸轧铝带坯质量的主要因素连续铸轧生产铸轧铝带坯,铸轧铝带坯质量的好坏一般除与设备自身加工精度、配置以及辅材优劣有关外,主要取决于铸轧辊磨削工艺、辊缝大小、辊面润滑、铸轧温度(前箱内铝熔体温度)、水冷强度、前箱内铝熔体液面高度、铸轧区长度和铸轧速度等工艺参数的选配。
这些工艺参数之间相互影响,当某一参数发生变化时,其他参数也要随之进行调整。
连续铸轧各主要工艺参数之间的关系,可按下述原则进行调整控制[3]:1)当浇注温度较高时,应该相应降低其铸轧速度;相反,当浇注温度较低时,应适当地提高其铸轧速度。
由于较低的铸轧温度有利于细化晶粒度,改善铸轧铝带坯的综合性能,而较高的铸轧速度有利于提高产量。
因此,合理的工艺制度应是较低的铸轧温度配以较高的铸轧速度。
2)当供料前箱内铝熔体液面高度较低时,其静压力小,铸嘴嘴腔内的铝熔体流动性小,应该相应降低其铸轧速度;相反,当供料前箱内铝熔体液面高度较高时,其静压力大,铸嘴嘴腔内的铝熔体流动性大,则应该相应提高铸轧速度。
3)铸轧区长度增大,其轧制区相对变小,循环水带走的热量就多,则铸轧速度可以加快;相反,铸轧区长度降低,其轧制区相对变大,循环水带走的热量就少,则铸轧速度则相应减慢。
4)当降低进水口温度和增加冷却水流量来提高水冷强度时,则应该相应提高铸轧速度。
正常情况下,一般设定好水温及水量后,在铸轧过程中,不要再对其进行调整,最好让其保证在一个恒定的范围内,便于其他工艺参数的调节。
根据上述控制原理,同时结合现场生产实践经验,以某铝加工厂采用Ф960mm×1850mm铸轧机生产6~10mm铸轧铝带坯为例,将几种典型合金的主要生产工艺参数进行预设,如表1所示。
在生产过程中,根据实际情况再进行微量调整,减少缺陷,生产优良的铸轧铝带坯。
表1 主要生产工艺参数预设表Tab.1 Preset table of main production process parameters合金牌号成品厚度/mm铸轧区长度/mm前箱内液面高度铸轧温度/℃铸轧速度/mm/min1060300380116~1050~7045~5550~55前箱内的液面高度比铸轧中心线高20~30mm685~7051000~1100800~900800~9003 常见的铸轧铝带坯缺陷原因分析及消除方法在连续铸轧过程中,由于各工艺参数调整不当,铸轧铝带坯会产生各种缺陷,常见的几种缺陷为热带、孔洞或凹坑、横向波纹、气道、裂边和板型超差等。
3.1 热带热带又称为“铸带”或“铸造带”[4],此缺陷是铝熔体在铸轧区内局部区域未完全凝固成形而被铸轧辊带出来未经轧制的板面缺陷。
热带缺陷一般不穿透带坯,其外形是较为粗糙的铸态组织,沿板面纵向延长。
这种缺陷多发生在立板到开始铸轧过程中或熔铝炉与保温炉转注过程中。
某铝加工厂采用Φ960mm×1850mm铸轧机生产1060合金时,在熔铝炉与保温炉转注过程中出现了热带,热带缺陷出现于板面中部,偶尔出现在边部,如图2、3所示。
主要参数如下:1)前箱内铝熔体温度约为720℃;2)铸轧速度为1080mm/min;3)入口水温28℃,出口水温30℃,水量为180t/h;供水压力0.55MPa(闭路循环水系统供回水)。
3.1.1 原因分析(1)前箱内的铝熔体温度相对于铸轧速度偏高,流入铸轧区内温度分布不均匀造成半凝固状态,导致局部温度过高而使液穴变深,来不及凝固即被铸轧辊带出,而形成中间热带;(2)铸轧速度过快,液穴较深的液态金属尚未完全凝固就被铸轧辊带出而产生中间热带;(3)前箱内铝熔体液面偏低,其静压力减小,液态金属局部供给不足,致使在边部区域出现热带;(4)辊面喷涂不均匀,局部润滑不够,也可产生热带。
生产1060合金时,在熔铝炉与保温炉转注过程中熔铝炉转注温度约为750℃,保温炉的温度迅速增加,其铸轧速度没变,而前箱内铝液温度达到720℃左右,正常铸轧温度为690℃左右,温度过高,从而产生了中间热带。
图2 中间热带图3 边部热带Fig.2 Middle unrolled stria Fig.3 Edge unrolled stria3.1.2 消除方法当铸轧铝带坯出现热带时,要仔细观察热带的形貌及其位置,判断其产生的原因,合理调整工艺参数。
(1)当前箱内铝熔体温度在正常工艺范围内,但相对于铸轧速度偏高时,则需适当增加铸轧速度。
(2)检查前箱铝熔体液面是否过低。
若前箱铝熔体液面偏低时,要及时清除前箱内及流槽内的浮渣,并适当调整保温炉放流口流量,将前箱内金属液面调整至合适高度;现场可事先自制一个简易浮漂放置在流槽内,并划上最低和最高液位刻度,以便随时观察调整。
(3)调整并清理好火焰喷涂喷枪,使其炭黑能均匀喷涂在铸轧辊辊面上,保证铸轧辊辊面润滑。
(4)用温度仪核查保温炉尤其前箱内铝熔体温度是否过高。
如果前箱内铝熔体温度偏高,则要重新校正设置前箱内的温度,温度过高需要快速降温。
铸轧现场的实际具体操作为,保持铸轧速度不变,或稍微调高铸轧速度,同时打开保温炉炉门进行炉内充入氮气精炼和冷却,并将过滤箱盖打开对铝熔体温度进行迅速降温,最终将其前箱内的铝熔体温度降至690℃左右,达到工艺要求的正常范围内,热带不再出现。
3.2 孔洞或凹坑在铸轧铝带坯上有时会出现穿透或未穿透板面的孔洞或凹坑。
此外,当热带出现后,进一步恶化也会出现孔洞。
这种缺陷多发生在开始铸轧时以及铸轧很长一段时间之后。
某铝加工厂采用Φ960mm×1850mm铸轧机生产1060合金时,铸轧铝带坯出现孔洞,如图4、5所示。
图4 普通孔洞图5 热带孔洞Fig.4 Ordinary hole Fig.5 Unrolled stria hole3.2.1 原因分析(1)普通孔洞或凹坑的形成,主要是铸轧区内有小气泡或夹杂物阻碍了铝熔体的流动,影响了铝熔体的连续供给;(2)普通孔洞或凹坑的形成也由于铸轧辊辊面上粘有夹杂物或铝渣,在铸轧时,对铸轧铝带坯表面造成的破坏;(3)热带孔洞的形成原因与热带形成原因相同。
3.2.2 消除方法(1)对于普通孔洞或凹坑缺陷,应加强炉内的精炼扒渣,以及加强在线精炼除气及过滤的处理;每次立板后必须更换过滤板,且生产同一合金3~5d后,过滤箱前后高度差大于70~100mm时,需及时更换过滤板;(2)观察火焰喷枪口,及时清理喷枪口处的积炭;人工加强清理铸轧辊辊面,及时调整喷枪火焰大小和位置,保证铸轧辊辊面的炭黑喷涂均匀;(3)对于热带孔洞缺陷,其消除方式与热带缺陷处理方式相同。
3.3 横向波纹横向波纹也叫“水波纹”、“斑马纹”或“虎皮纹”[5],其铸轧铝带坯表面会出现很明显的明暗相间的横向条纹。
这种缺陷经常出现在开始铸轧时或熔铝炉与保温炉转注过程中。
如果前箱液面波动一直较大时,此种缺陷会一直出现。
某铝加工厂在熔铝炉与保温炉转注过程中,采用Φ960mm×1850mm铸轧机生产1060合金时出现了横向波纹,如图6所示。
主要参数如下:1)前箱内铝熔体温度为690℃;2)铸轧速度为1070mm/min;3)入口水温27℃,出口水温30℃,水量为180t/h;供水压力0.55MPa(闭路循环水系统供回水);4)前箱内液面波动为±3mm。
图6 横向波纹Fig.6 Transverse ripple3.3.1 原因分析(1)由于冷却水水温、水压不稳定以及铸轧速度偏低导致铸轧时铸轧铝带坯表面冷热不均而产生横向波纹;(2)由于铸轧时嘴辊间隙处包覆铝液的氧化膜周期震荡并发生破裂,使带坯表层的凝固速度周期变化,从而使表面出现横向波纹。
铸轧1060合金,在熔铝炉与保温炉转注过程中,其液面波动大,而保温炉转注至铸轧机采用的是气动装置自动控流,其控流精度不高,导致前箱内液面波动变化大,其范围为±3mm,从而产生横向波纹。
3.3.2 消除方法(1)采用闭路循环水系统对每台铸轧机单独供回水,保持恒定的冷却水水温、水压及水流量;(2)人工精细控流或采用先进的自动控流技术(如电动装置控流),必须保持前箱内铝熔体液面微小波动幅度。
如上述现场实例,具体做法为,在其他工艺参数不改变的情况下,在熔铝炉与保温炉转注时,将气动控流装置改成手动,依靠经验丰富的操作人员精细控流,严格控制液面波动,使其保持在±1.5mm,从而消除了横向波纹。
3.4 气道在铸轧过程中,铝铸轧带坯表面呈现连续不断的纵向白道,此种缺陷就是气道。
这种缺陷多发生在开始铸轧时以及铸轧很长一段时间之后。
某铝加工厂采用Φ960mm×1850mm铸轧机生产1060合金时出现了气道,如图7所示。
图7 气道Fig.7 Air flue3.4.1 原因分析形成气道的主要原因是由于精炼时间和精炼气体量不够,精炼效果不佳,使前箱内铝熔体内的氢气过多,来不及析出而积聚在铸嘴前沿形成气泡,在铸轧过程中,拉长的气泡沿带坯纵向延伸,从而形成一段白道。