催化裂化油浆系统结焦原因及对策
浅析重油催化裂化装置沉降器结焦原因及对策

20 09年 4月 1 全厂停 电 , 化装置进 入紧 41 3 三催 急停工状 态 。在恢复生产 时 , 现待生催 化剂循 环线 发 路 不 畅 ,经过 现场 操作 验证发 现必 须 实现 负差压 方
可实现 待生催 化剂 转人再 生 器 ,并 且 表现催 化剂 循
u twa h wn b c us fpo rf i e o ni s s utdo e a e o we al n Aprl1 ur i 4,2 09.Buti ou d t tt e c t ls e ic a in wa 0 twasf n ha h a ay tr cr ulto s
焦 结 构 形 态 , 合 生 产 中的 操 作 数 据 , 出沉 降 器 内 结 焦 的原 因 , 提 出 相应 的对 策 。 结 找 并
关键词 : 重油催化裂化 ; 沉降器 ; 结焦 ; 雾化蒸汽 中图分类号 :E 2 . T 6 44 文献标识码 : A
S u n mi g HI Ch a - n Re s n n o u i n o o i g i e te fRFCCU a o sa d s l t sf r c k n s tl r o o n
沉降器内结焦集中在沉降器旋风分离器入 口以
上 至拱形 的广 大空 间 , 包括 旋风 料腿 外壁 上 、 内部支 撑件 上 、 旋肩部 死 区上 、 降器 内壁 上 。并且 料腿 粗 沉 外 壁结焦 严 重 , 度达 到 8~ 0m, 厚 2 c 主体 为无 明显分
层、 质地坚硬 的沉积 焦 。见 图 12 、。
再生器同轴 , 一段在二段上 , 与反应沉降器高低并列 布置。04 20 年应用石油大学辅助提升管技术 , 对装置
催化裂化装置油浆系统长周期运行影响因素及对策

提高 油浆 在换 热器 内流 速 .避免换 热 器结 焦堵 塞 。 以上 措施 可见 图 1 。
油浆蒸汽发生器A B
降 。2 1 0 1年 7月份 对 其 中一 组 蒸 汽 发生 器 进行 切 除清 理 后 .油 浆 循 环 有 了显 著 提 升 . 目前 分馏 塔
底 液 相 温度 控 制 不 大 于 3 0℃ .气 相 温度 控 制 不 4 大 于 3 5℃。 7 为解决该 问题 ,装 置准备 采 取 以下措 施 : ( )从油 浆 过滤 器 出 口引一 条 D 0 管 1 N 1omm 线 至 油 浆 上返 塔 .通 过 控制 阀控 制 油 浆 至 上 返塔 流 量 。达 到调 节油浆 返 塔温 度 的 目的 : ( )油 浆蒸 汽 发生 器 增 设 一 条 串联 线 ,使 其 2 流 程 由并联 改 为既 可 以并联 也可 串联 增 设 高 温 油浆 热 路 线 后 .高 温 油浆 与 油浆 蒸
势 必 会 增 加油 浆 系 统 的 阻力 .可 能 会 导 致油 浆 泵
油 浆 的 流 量 即可 调 节 油 浆返 塔 温 度 .最 大 限 度 地
保 证 了油浆 至 油浆一 料 换热 器 、油浆 蒸 汽发 生 器 原 的流 量 ,提 高 了油 浆 在 换热 器 中 的流 速 ,避 免换
热 器结 焦堵 塞 油 浆蒸 汽 发生器 增 设 串联 线后 ,可实 现 可并 、 可 串流 程 .在装 置 低 处 理 量 时投 用 串联 流 程 。可
1 分馏 塔底 油 浆停 留时 间的影 响 . 3
根 据 目前 运 行 状 态 .对 油 浆 系 统 进 行 核 算 ( 表 1 。为 避 免 油浆 在 高温 情 况 下 结 焦 .油 浆 见 )
化 剂 粉末堵 塞 ,从 而确 保分 馏塔 的分 离效 率
重油催化装置反应系统结焦原因与防治
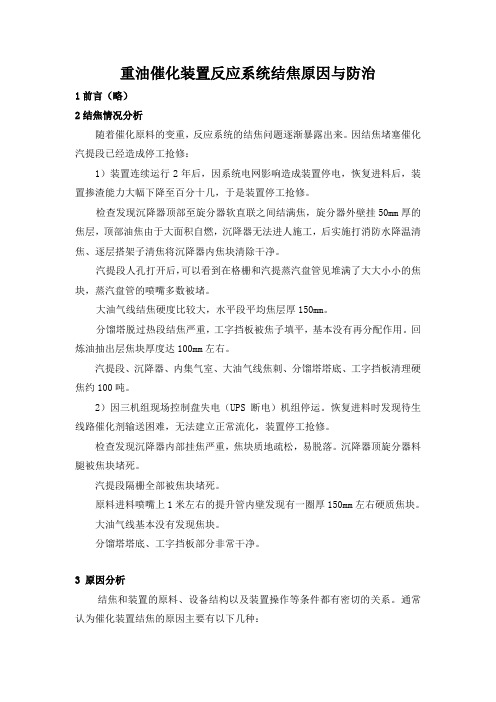
重油催化装置反应系统结焦原因与防治1前言(略)2结焦情况分析随着催化原料的变重,反应系统的结焦问题逐渐暴露出来。
因结焦堵塞催化汽提段已经造成停工抢修:1)装置连续运行2年后,因系统电网影响造成装置停电,恢复进料后,装置掺渣能力大幅下降至百分十几,于是装置停工抢修。
检查发现沉降器顶部至旋分器软直联之间结满焦,旋分器外壁挂50mm厚的焦层,顶部油焦由于大面积自燃,沉降器无法进人施工,后实施打消防水降温清焦、逐层搭架子清焦将沉降器内焦块清除干净。
汽提段人孔打开后,可以看到在格栅和汽提蒸汽盘管见堆满了大大小小的焦块,蒸汽盘管的喷嘴多数被堵。
大油气线结焦硬度比较大,水平段平均焦层厚150mm。
分馏塔脱过热段结焦严重,工字挡板被焦子填平,基本没有再分配作用。
回炼油抽出层焦块厚度达100mm左右。
汽提段、沉降器、内集气室、大油气线焦刺、分馏塔塔底、工字挡板清理硬焦约100吨。
2)因三机组现场控制盘失电(UPS断电)机组停运。
恢复进料时发现待生线路催化剂输送困难,无法建立正常流化,装置停工抢修。
检查发现沉降器内部挂焦严重,焦块质地疏松,易脱落。
沉降器顶旋分器料腿被焦块堵死。
汽提段隔栅全部被焦块堵死。
原料进料喷嘴上1米左右的提升管内壁发现有一圈厚150mm 左右硬质焦块。
大油气线基本没有发现焦块。
分馏塔塔底、工字挡板部分非常干净。
3 原因分析结焦和装置的原料、设备结构以及装置操作等条件都有密切的关系。
通常认为催化装置结焦的原因主要有以下几种:1、原料中未汽化的高沸点物质挂壁后在催化剂作用下炭化生焦。
2、反应油气中重组分在死区冷壁处液化形成“焦核”,逐渐发生缩合生焦。
3.1 原料性质的影响原料中的渣油以VRDS减压渣油为主,原料掺渣比例变化如下表1,渣油性质见表2所示。
VRDS减压渣油中高沸点物质含量在80%以上,随着装置掺渣的增加,原料中高沸点物的比例不断上升,反应产物中高沸点组分相应增加,结焦的趋势增加。
表1 催化原料掺渣变化(略)表2 VRDS渣油性质列表(略)催化装置原料性质变化情况,见下表(略)3.2 设备结构的影响3.2.1 提升管内结焦情况分析从提升管内结焦的位置分析其原因应该是原料油滴穿透现象的结果。
防止催化裂化装置结焦的技术措施

156科技展望TECHNOLOGY OUTLOOK中国航班CHINA FLIGHTS 防止催化裂化装置结焦的技术措施张建峰|中海石油中捷石化有限公司摘要:现阶段正处于社会发展建设的关键时期,对于石油化工产品的需求量在不断提升,这就对石油化工生产行业的生产效率和生产安全提出了更高的要求和标准。
催化裂化装置作为石化生产中极其重要的一部分,为了确保催化裂化装置的正常运行,就需要做好防结焦技术的研究分析,有效掌握催化裂化装置在运行中产生结焦的原因,制定并采取切实有效的防结焦技术措施,为催化裂化装置的高效稳定运行提供有效保障,提高对催化裂化焦化问题的处理水平。
关键词:催化裂化;装置结焦;技术措施催化裂化装置在生产运行中的结焦问题,会对整个装置的运行带来极大不良影响,不仅会影响生产效率,并且还会引发安全隐患。
尤其在现阶段对于石化产品质量及需求量要求在不断提升,更需要从抗结焦方便入手,积极研究和创新相关防结焦技术,这对于石油化工行业的发展有着非常重要的意义和作用。
1催化裂化装置结焦的原因分析1.1结焦部位在现阶段原油重质化情况比较突出,所以在当下催化裂化中多数都会采用常减压渣油来充当相关原材料,但是该材料在性质这两方面相对有限,所以在催化裂化生产中,会容易导致相关设备产生结焦,进而对整个催化裂化装置的安全稳定运行带来不良影响,严重影响了整个产品的质量以及生产的安全和效率。
提升管原油喷嘴顶部、旋风分离外壁、沉降器穹顶、分馏油浆系统等重要部件,在原油质量较差的环境下,催化裂化装置极易结焦。
1.2造成结焦的因素一般而言,催化裂化装置的结焦是由于重质原油在反应过程中发生的不良反应、原料的雾化和汽化、二烯烃、芳烃等的聚合缩合所导致的。
并且在催化裂化生产中温度条件以及环境条件的影响,所以必然会导致装置结焦,同时由于部分催化裂化装置需要一直在沉积和高温条件下进行运行,所以更容易产生结焦问题。
因为在现阶段原油原料方面的质量较差已经成为非常普遍的一种情况,所以有部分原油在催化裂化的过程中,有相当一部分残渣中的某些重组分在高温下不能汽化。
防止催化裂化装置结焦的技术措施

工业生产化 工 设 计 通 讯Industrial ProductionChemical Engineering Design Communications·203·第46卷第1期2020年1月随着我国经济社会的快速发展和科技水平的进一步提升,人们对工业生产和生活品质的要求不断提高,对石油资源的消费需求也稳步增强。
另一方面,随着全球原油重质化、劣质化趋势的不断加强,催化裂化技术已成为炼油企业获取重要化工原材料的核心加工手段,拥有较为广阔的发展前景。
但是,催化裂化装置的不同部位却很容易在使用过程中出现结焦现象,进而影响到整个催化裂化装置的安全性、稳定性和可靠性。
在现阶段石油资源需求量较大和各种不利因素不断增加的情况下,如何提高催化裂化装置的防结焦水平成为相关技术人员和管理人员考虑的重要内容。
在此背景下,对防止催化裂化装置结焦的技术措施进行一定探讨和研究便有着不容忽视的重要理论意义和现实价值。
1 催化裂化装置结焦的原因分析1.1 结焦部位近年来随着原油劣质化、重质化趋势的进一步增强,常压、减压渣油直接成为石油炼化企业催化裂化的原材料,其较差的化学物理性质使得催化裂化装置相关部位的结焦问题进一步加重,已然成为影响催化裂化装置安全稳定运行和可靠优质生产的重要原因之一。
通常情况下,催化裂化装置在原油劣质化环境下非常容易出现结焦的部位主要有提升管原料油喷嘴上方、旋风分离器外壁、沉降器穹顶、分馏油浆系统等重要部位。
1.2 造成结焦的因素一般而言,原油催化裂化装置结焦的根本原因在于原油重质,原料雾化和汽化的不良反应,还有原料在反应过程中产生的双烯、大分子芳烃缩合及双烯烃聚合物反应等。
同时,催化裂化面临较高的温度环境和外在劣质油气环境,因此催化裂化装置结焦的可能性是客观存在且不可避免的,催化裂化装置的某些特殊部位在冷凝沉积和长时间高温环境下停留缩合,进而出现关键部位结焦的情形。
就原料性质而言,现阶段原油重质化和劣质化趋势不断明显,重质原料导致催化裂化装置的沉降器结焦,更在一定程度上使其后续雾化效果大打折扣。
浅析重油催化裂化装置结焦原因及防止对策
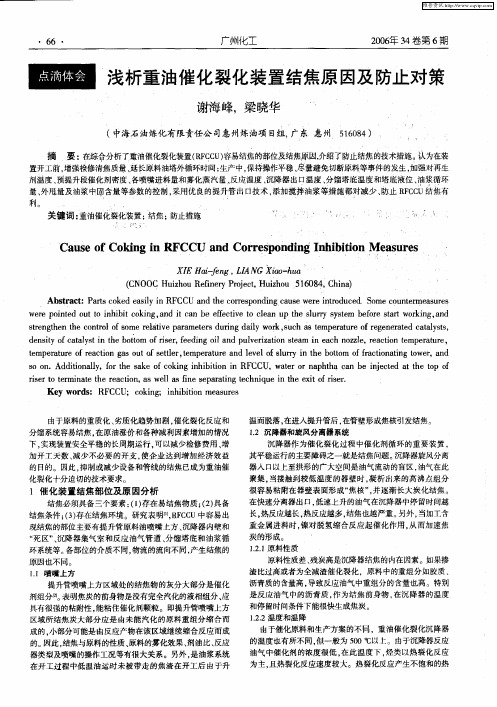
S n A dt nl , o esk f o igihbt ni R C U, ae o a hh a eijc da tet f Oo . d io a y fr h a eo kn n iio n F C w t rn p tac nb net t h o o i l t c i r e p
.
由于原料 的重质化 、 劣质化趋势加剧 。 催化裂化反 应和 分馏系统容易结焦 . 油涨价 和各种减 利因素增加 的情况 在原 下, 实现装置安全平稳 的长周期运行 , 以减少检修费用 、 可 增 加开工 天数 、 少不必要 的开支 。 减 使企业达到增 加经济效益 的目的。因此, 抑制或减少设备和管线的结焦已成为重油催 化裂化 十分迫切的技术要求 。
XI i n , [ E Hn g L ANG Xio h a a- u
(N O uzo e nr rjc Huzo 5 8, hn) C O C H i uR f eyPo t i u 0 4 C ia h i e, h 1 6
Ab ta t at o e a i nRF C n ec rep n igc u eweeit d c d o o neme s rs sr c :P r c k d e sl i C U a dt ors o dn a s r nr u e .S mec u tr a ue s y h o weep itd o tt ihb t o i g a d i c n b f ciet la p tesu r ytm eo esatw rig a d r one u o n ii c k n ,n t a e ef t o ce n u lry sse b fr tr okn , n e v h
温而脱落 , 在进入提升管后 , 在管壁形成焦核引发结 焦。 1 沉降器 和旋风分离器 系统 . 2 沉降器作 为催 化裂化 过程 中催 化剂循 环的重要 装置 , 其平稳运行 的主要障碍之一就是结 焦问题 。 沉降器旋风分离 器入 口以上至拱形 的广大 空间是油 气流 动的盲 区, 油气在此
关于催化裂化分馏岗位油浆循环系统堵塞预防和治理
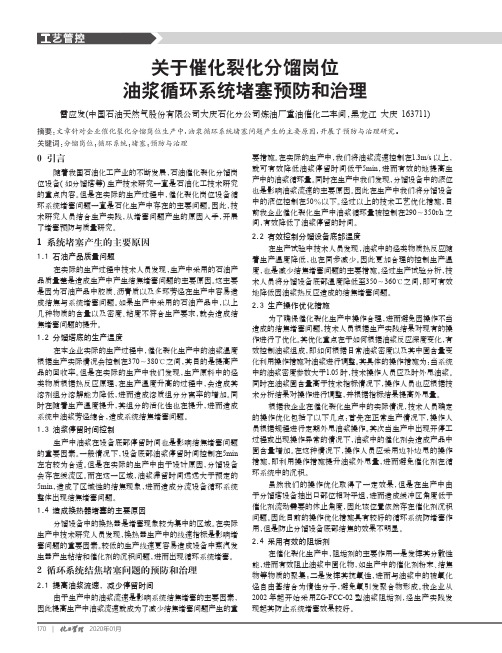
要措施。
在实际的生产中,我们将油浆流速控制在1.3m/s 以上,就可有效降低油浆停留时间低于5min ,进而有效的地提高生产中的油浆循环量。
同时在生产中我们发现,分馏设备中的液位也是影响油浆流速的主要原因。
因此在生产中我们将分馏设备中的液位控制在50%以下。
经过以上的技术工艺优化措施,目前我企业催化裂化生产中油浆循环量被控制在290~350t/h 之间,有效降低了油浆停留的时间。
2.2 有效控制分馏设备底部温度在生产试验中技术人员发现,油浆中的烃类物质热反应随着生产温度降低,也在同步减少。
因此更加合理的控制生产温度,也是减少结焦堵塞问题的主要措施。
经过生产试验分析,技术人员将分馏设备底部温度降低至350~360℃之间,即可有效地降低因油浆热反应造成的结焦堵塞问题。
2.3 生产操作优化措施为了确保催化裂化生产中操作合理,进而避免因操作不当造成的结焦堵塞问题,技术人员根据生产实践结果对现有的操作进行了优化。
其优化重点在于如何根据油浆反应深度变化,有效控制油浆组成,即如何根据日常油浆密度以及其中固含量变化利用操作措施对油浆进行调整。
其具体的操作措施为:当系统中的油浆密度参数大于1.05时,技术操作人员应及时外甩油浆。
同时在油浆固含量高于技术指标情况下,操作人员也应根据技术分析结果对操作进行调整,并根据指标结果提高外甩量。
根据我企业在催化裂化生产中的实际情况,技术人员确定的操作优化包括了以下几点:首先在正常生产情况下,操作人员根据规程进行定期外甩油浆操作。
其次当生产中出现开停工过程或出现操作异常的情况下,油浆中的催化剂会造成产品中固含量增加。
在这种情况下,操作人员应采用边补边甩的操作措施,即利用操作措施提升油浆外甩量,进而避免催化剂在循环系统中的沉积。
虽然我们的操作优化取得了一定效果,但是在生产中由于分馏塔设备抽出口部位相对平坦,进而造成缓冲区角度低于催化剂流动需要的休止角度,因此该位置依然存在催化剂沉积问题。
催化裂化装置结焦原因分析及对策研究

催化裂化装置结焦原因分析及对策研究摘要:炼油企业是我国的重要产业,如何在炼油过程中减少不必要的消耗,提高原油的使用效率成为炼油企业的发展方向。
催化裂化装置在炼油企业中占据重要地位,减少催化裂化装置在消化重油过程中的结焦现象是提高企业经济效益的重要条件。
基于此,本文就催化裂化装置出现结焦的原因进行分析并提出相应的对策。
关键词:催化裂化装置;结焦原因;应对措施引言:催化裂化装置结焦原因是多种多样的,可能是因为设备结构不合理、炼油原材料够不到标准、工人对设备的操作不合理等。
炼油企业只有从中找出催化裂化装置结焦的原因,才能够更好的进行原油炼化,提高催化裂化装置对重油消化的使用效率。
一、催化裂化装置概述:催化裂化装置是炼油企业中必不可少的装置,催化裂化装置的主要功能是对原材料进行催化裂化,使不同的原材料在催化裂化装置内进行化学反应,从中提炼出稳定的汽油的装置。
二、催化裂化装置结焦几大常见原因(一)、催化裂化设备结构不符合炼油标准炼油企业在进行催化裂化装置的购买时可能会因为资金不足等原因而没有选择高质量的装置,以及在购买了催化裂化装置后没有安排相应的技术部门对装置进行维护,容易造成催化裂化装置出现结焦现象。
(二)、炼油原材料和催化剂使用不当炼油企业在对原油提炼时对原材料使用不当,用劣质原材料代替原本原材料以及没有根据催化裂化装置选择适宜的催化剂导致残渣多也会造成催化裂化装置出现结焦现象。
(三)、装置操作环境不当和不合理操作催化裂化装置进行炼油时对操作环境要求高,没有适合炼油的操作环境以及装置操作者对装置的不熟练,没有掌握炼油的步骤都会出现催化裂化装置结焦现象。
三、对催化裂化装置结焦原因的对策研究(一)、购买高规格、高质量的催化裂化装置炼油企业在对催化裂化装置进行购买时要尽量选择购买高规格,高规格的催化裂化装置,如果炼油企业因为想要节省炼油成本而购买落后的催化裂化装置,反而会对炼油企业造成更大的损失,落后的催化裂化装置出现的问题往往会被先进高质量的装置多,炼油企业花在维修上的资金反而会更多,而且一旦对催化裂化装置进行维修就意味着企业只能停止生产,生产线一旦停止可能会出现顾客订单不能及时完成的状况,这会对企业造成更大的损失。
- 1、下载文档前请自行甄别文档内容的完整性,平台不提供额外的编辑、内容补充、找答案等附加服务。
- 2、"仅部分预览"的文档,不可在线预览部分如存在完整性等问题,可反馈申请退款(可完整预览的文档不适用该条件!)。
- 3、如文档侵犯您的权益,请联系客服反馈,我们会尽快为您处理(人工客服工作时间:9:00-18:30)。
催化裂化油浆系统结焦原因及对策
摘要:催化裂化装置随着原料的重质化,结焦现象趋于严重,成为影响装置长周期运行的主要因素之
一。油浆系统结焦严重影响装置后期的平稳运行。文章提出了治理对策,可供同行借鉴。
关键词:催化裂化,结焦原因,治理对策,长周期运行,油浆系统
近年来,随着国内外原油的重质化和劣质化,催化裂化在原油深度加工、提高轻质油收
率与炼油厂经济效益等方面一直发挥着重要作用,发展极为迅速。由于渣油具有较大的结焦
倾向,我国多数炼油厂的催化裂化装置都发生过严重的结焦。“催化裂化协作组”的专题调
研报告显示[1],重油催化裂化提升管、沉降器及分馏系统中结焦非常普遍且严重,特别是沉
降器结焦对催化裂化装置的影响最为严重。因结焦造成工业装置非计划停工次数几乎占总停
工次数的2/3,是重油催化裂化工业装置长周期运转的严重制约因素,直接影响到催化裂化
装置的长周期安全运行和炼油厂的经济效益。国内研究者对重油催化裂化装置的结焦做了大
量研究工作,并取得了一定成果。公司催化裂化装置停工检修发现,结焦严重主要集中在油
浆系统,而并非是沉降器(如下图)。
图 油浆换热器213及油浆备用泵209出口管线结焦情况
1 油浆系统结焦机理
催化裂化装置因其重油、高温的工艺特点,决定了结焦的客观性。油浆系统结焦的机理:
油浆结焦物由有机物和无机物组成。有机物主要由各类重质烃缩聚物组成,无机物主要是催
化剂粉末。油浆中多环芳烃、胶质、沥青质等各类不饱和烃在高温下,由氧和金属引发催化
作用,容易脱氢产生芳烃自由基,通过自由基链反应而产生高分子聚合物。随着聚合物和缩
合物的平均相对分子质量的不断增大,其在介质中的溶解度逐渐减小,析出后黏附在设备表
面,当遇到催化剂时,易聚集成颗粒,已经黏附在表面的聚合物也能起到捕获剂的作用,加
快颗粒的沉积和生焦。
2 油浆系统结焦部位及分析
分馏系统的结焦部位主要发生在分馏塔底部舌形塔盘、人字挡板、塔底、油浆泵入口、
油浆管线及油浆换热器等部位。分馏及油浆系统的结焦最初表现在油浆循环量下降,致使分
馏塔底热量取不出来,分馏塔气液相超温,结焦趋势增加,容易形成恶性循环。一般认为,
催化裂化原料的性质、油浆的性质、分馏塔底温度、油浆停留时间、催化剂含量及流动状态、
油浆流速、操作波动等各种因素相互作用是油浆结焦的主要原因。
从上图可以看出油浆备用泵出口管线结焦堵死,主要原因是备用机泵切换频率过低,预
热线孔板过小,预热不均匀导致油浆备用泵出口结焦。所以增大备用机泵的切换频率和加大
预热线的孔板,可以避免高温油浆在备用机泵管线上的结焦。
2.8Mt/a催化油浆循环量大约维持在600-800t/h。由此可以计算出,油浆在不同循环量
和分馏塔不同液面下的停留时间及在换热设备上的线速度。计算结果见表一和表二。
从表一可以看出,在油浆液面50%,装置在油浆循环量在≤600t/h时,油浆在分馏塔的
停留时间为≥5.85min;油浆循环量在≥800t/h时,油浆在分馏塔的停留时间≤4.39min。
而且油浆液面只要超过80%,在油浆循环量正常的情况下,停留时间都>5min,在分馏塔的
停留时间过长,容易造成分馏塔底结焦。因此,通过调节反应深度,将分馏塔液面控制在
50%以下,油浆循环量控制在600t/h以上,可以降低油浆在分馏塔的停留时间,从而可以避
免油浆在高温下因停留时间过长而发生的结焦。
表一 油浆在分馏塔的停留时间(油浆密度按330℃平均826kg/m-3)
项 目 油浆循环量600t/h 油浆循环量800t/h
体积/m³ 停留时间/min 体积/m³ 停留时间/min
液面
5% 30.83 2.54 30.83 2.59
20% 44.17 3.65 44.17 2.74
50% 70.84 5.85 70.84 4.39
80% 95.50 8.05 95.50 6.04
100% 115.28 9.53 115.28 7.14
从表二可以看出,催化油浆在通过原料换热器时的线速度在0.9至1.2m/s,在正常范
围内。所以开工前四年以来油浆原料油换热器运行正常,只是到了后期由于油浆温度高导致
其结焦。油浆蒸汽发生器在长岭2.8Mt/a催化裂化装置中,采取单台运行、两台并联和三台
并联的运行方式。但主要的运行方式是单台运行或者两台并联运行。从表二可以看出在两台
油浆蒸汽发生器并联运行,油浆循环量在600至800t/h时,油浆蒸汽发生器的线速度都<
1.0m/s,只有在单台运行的情况下油浆蒸汽发生器的线速度才>1.0m/s。较低的线速度导致
油浆容易在换热器及蒸汽发生器上粘结,是导致油浆蒸汽发生器结焦的直接原因。所以在蒸
汽发生器负荷正常的情况下,可以采取单台运行方式,控制油浆在蒸汽发生器的线速度,从
而可以避免油浆在高温下因线速度过小而发生的结焦。
表二 油浆在换热器中的线速度(油浆密度按330℃平均826kg/m-3)
项目 油浆与原料换热器E212A/B 油浆蒸汽发生器E213A/B/C
单台流通面积(油
浆)/m2
0.0827 0.1250
油浆循环量/t.h-1
600 800 600 800
不同换热流程的线速度/m.s-1
单台 1.19 1.59
两台并联 0.60 0.79
三台并联 0.40 0.53
两台串联 0.90 1.20
从近几年结焦的情况来分析,油浆系统结焦原因除了线速之外还有就是外取热的泄漏。
从2013年以来,外取热系统出现过三次大量泄漏、几次小泄漏。外取热泄漏期间,油浆固
含量、灰分明显都超过工艺指标。油浆系统大量的催化剂会加速油浆系统结焦而且会堵塞换
热器,所以必须控制外取热的泄漏避免催化剂的跑损,防止油浆系统在高温下因催化剂的跑
损固含量高而发生的结焦。
2.1 影响分馏塔及油浆系统结焦的因素
分馏塔及油浆系统结焦因素如下:①油浆性质。随着油浆中的多环芳烃含量的增加,油
浆相对密度和黏度增大,流动性变差;油浆中稠环芳烃和不饱和烯烃在高温下很容易发生缩
合反应,生焦能力强。②塔底温度。分馏塔塔底温度是导致油浆系统结焦的关键因素。随着
塔底温度的升高,轻馏分逐渐蒸发,油浆浓缩,黏性增加,生焦性能增强。当温度升高到一
定值时,热裂化和聚合反应速度会变得很快。当油浆在某一高温下停留时间足够长时,油浆
中将有焦炭生成。③停留时间。分馏塔底部是一个平坦的缓流区,当积存一部分催化剂和焦
时,油浆在此区域的停留时间会远超过平均停留时间,油浆中的稠环芳烃、胶质、沥青质等
就会和夹带的催化剂颗粒一起沉积,最终形成包含催化剂粉末的焦块。④油浆流速。由于油
浆中芳烃和胶质含量较高,在高温下极易发生聚合反应,油浆在管道中的流速过低时,停留
时间延长,油浆中夹带的催化剂和重组分就会沉积于管线底部,发生热裂化和结焦反应。⑤
催化剂及油浆固体含量的影响。随着催化裂化进料的重质化和低氢转移活性超稳分子筛催化
剂的使用,一部分原本可能生焦的重芳烃不成焦而以稠环芳烃形式富集于油浆中,从而加重
塔底的结焦问题。油浆中含有催化剂颗粒,当油浆流速低或停留时间较长时,催化剂颗粒发
生沉降成为油滴聚集的中心,促使结焦发生,固含量增大使结焦性能增强,油浆换热器系统
的普通结垢机理为含炭催化剂颗粒的重力沉降。⑥塔的底部存在缓流区和死区。从分馏塔底
的椭圆形来看,其中的油浆抽出口附近是相对平坦的,其角度也远小于催化剂流动休止角,
客观上是一个催化剂积存的条件,一旦有催化剂在塔底沉积就很难再彻底被液体油带走,这
样就造成了分馏塔底的一个高含催化剂颗粒的缓流区或死区,油浆在塔底流动线速不均一,
为垢物团的重力沉积和结焦创造了必要条件。
2.2 相应对策
防止分馏塔及油浆系统结焦的措施如下:
(1)控制好分馏塔塔底温度和塔底油浆停留时间。
采用较低的分馏塔塔底温度可以降低聚合生焦反应的速度。长岭2.8Mt/a催化裂化装置
从2010年开工以来,分馏塔底温度控制在320~340 ℃,油浆系统正常。但是运行到后期
由于油浆蒸汽发生器结焦严重,分馏塔底温度升至350~360 ℃。严重影响装置的平稳生产。
所以必须控制好分馏塔塔底温度,主要措施有降低循环油浆返塔温度,加大油浆返塔下返塔
量等,此外引一股急冷油(油浆或回炼油)对塔底进行急冷,既可加强对塔底的冲涮,防止
催化剂在分馏塔底的缓流区堆积,又可使塔底油浆快速降温,防止油浆重组分高温聚合。分
馏塔塔底宜保持较低的分馏塔液面(30%~45%)和较短的停留时间(小于5 min),液面
高,油浆在塔内的停留时间长;液面太低,油浆泵易抽空,威胁安全生产。
控制好脱过热段挡板上方的气相温度就可以保证油浆中的轻组分基本拔出,满足分馏所
需的热量。实际上分馏塔塔底已处于过冷状态(非平衡液相),较低的塔底温度对油浆中轻
组分含量并没有实质性的影响。
(2)加强平稳操作,减少非正常结焦。
精心操作,尽量减少波动及非计划停工,减少非正常结焦,对于防止结焦有着非常重要