作业溶氧对发酵的影响及控制

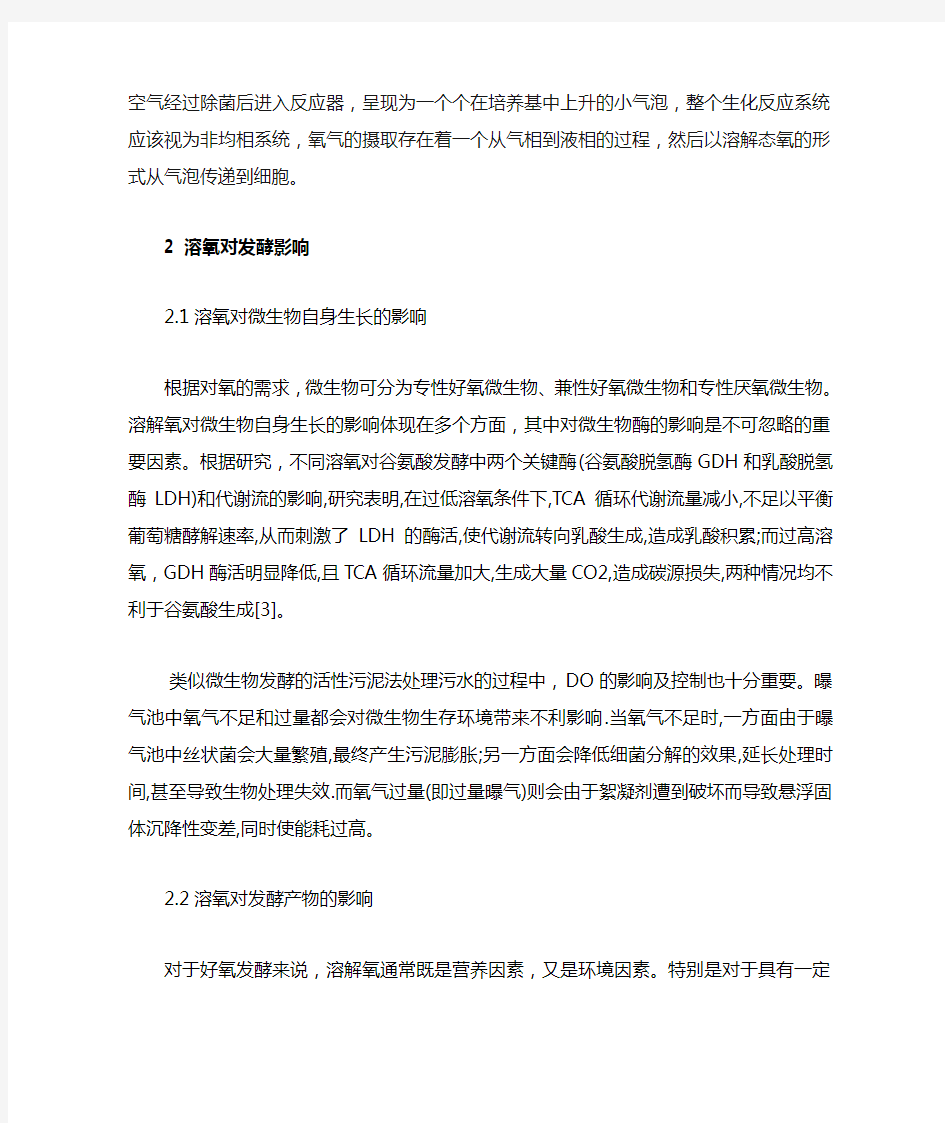
“溶氧对发酵的影响及控制”的读书报告
摘要:发酵液中的溶氧浓度(Dissolved Oxygen ,简称DO)对微生物的生长和产物形成有着重要的影响。在发酵过程中,必须供给适量的无菌空气,菌体才能繁殖和积累所需代谢产物。不同菌种及不同发酵阶段的菌体的需氧量是不同的,发酵液的DO值直接影响微生物的酶的活性、代谢途径及产物产量。发酵过程中,氧的传质速率主要受发酵液中溶解氧的浓度和传递阻力影响。研究溶氧对发酵的影响及控制对提高生产效率,改善产品质量等都有重要意义。这是通过对发酵工艺的学习,记录下的读书笔记。
关键词:溶氧、发酵、发酵工艺、控制
正文:
1 发酵液中氧的溶解及传质速率
1.1 氧的溶解特性
溶解氧(Dissolved Oxygen)是指溶解于水中分子状态的氧,用DO 表示。氧是一种难溶气体,在常压、25℃的条件下,空气中的氧在纯水中的溶解度仅约为0.25mmol/L,在发酵液中,由于各种溶解的营养成分、无机盐和微生物的代谢产物存在,会明显降低氧的溶解度。此外,溶氧浓度会随着温度、气压、盐分的变化而变化。一般说来,温度越高,溶解的盐分越大,水中的溶解氧越低;气压越高,水中的溶解氧越高[4]。
1.2 微生物对氧的利用方式
微生物反应一般是在液相中进行的,只有溶解在溶液中的氧气才能够被微生物所摄取。空气经过除菌后进入反应器,呈现为一个个在培养基中上升的小气泡,整个生化反应系统应该视为非均相系统,氧气的摄取存在着一个从气相到液相的过程,然后以溶解态氧的形式从气泡传递到细胞。
2 溶氧对发酵影响
2.1溶氧对微生物自身生长的影响
根据对氧的需求,微生物可分为专性好氧微生物、兼性好氧微生物和专性厌氧微生物。溶解氧对微生物自身生长的影响体现在多个方面,其中对微生物酶的影响是不可忽略的重要因素。根据研究,不同溶氧对谷氨酸发酵中两个关键酶(谷氨酸脱氢酶GDH和乳酸脱氢酶LDH)和代谢流的影响,研究表明,在过低溶氧条件下,TCA循环代谢流量减小,不足以平衡葡萄糖酵解速率,从而刺激了LDH的酶活,使代谢流转向乳酸生成,造成乳酸积累;而过高溶氧,GDH酶活明显降低,且TCA 循环流量加大,生成大量CO2,造成碳源损失,两种情况均不利于谷氨酸生成[3]。
类似微生物发酵的活性污泥法处理污水的过程中,DO的影响及控制也十分重要。曝气池中氧气不足和过量都会对微生物生存环境带来不利影响.当氧气不足时,一方面由于曝气池中丝状菌会大量繁殖,最终产生污泥膨胀;另一方面会降低细菌分解的效果,延长处理时间,甚至导致生物处理失效.而氧气过量(即过量曝气)则会由于絮凝剂遭到破坏而导致悬浮固体沉降性变差,同时使能耗过高。2.2溶氧对发酵产物的影响
对于好氧发酵来说,溶解氧通常既是营养因素,又是环境因素。特别是对于具有一定氧化还原性质的代谢产物的生产来说,DO的改变势必会影响到菌株培养体系的氧化还原电位,同时也会对细胞生长和产物的形成产生影响。
在黄原胶发酵中,虽然发酵液中的溶氧浓度对菌体生长速率影响不大,但是对菌体浓度达到最大之后的菌体的稳定期的长短及产品质量却有着明显的影响
[2]。
需氧微生物酶的活性对氧有着很强的依赖性。谷氨酸发酵中,高溶氧条件下乳酸脱氢酶(LDH)活性明显比低溶氧条件下的LDH酶活要低,产酸中后期谷氨酸脱氢酶(GDH)的酶活下降很快,这可能是由于在高溶氧条件下,剧烈的通气和搅拌加剧了菌体的死亡速度和发酵活性的衰减[3]。
DO值的高低还会改变微生物代谢途径,以致改变发酵环境甚至使目标产物发生偏离。研究表明,L-异亮氨酸的代谢流量与溶氧浓度有密切关系,可以通过控制不同时期的溶氧来改变发酵过程中的代谢流分布,从而改变Ile等氨基酸合成的代谢流量[4]。
3 溶氧量的控制
3.1控制溶氧量
(C*-CL)是氧溶解的推动力,控制溶氧量首要因素是控制氧分压(C*)。高密度培养往往采用通入纯氧的方式提高氧分压,而厌氧发酵则采用各种方式将氧分压控制在较低水平。如啤酒发酵,麦汁充氧和酵母接种阶段,一般要求氧含量达到8~10PPM;而啤酒发酵阶段,一般啤酒中的含氧量不得超过2PPM[1]。
此外,由于氧是难溶气体,一定温度和压力下,DO值有一上限。为此,向发酵液中加入氧载体是提高DO值的一个行之有效的方法。实验表明,在发酵基质中添加5%正十二烷,可明显地提高发酵介质中的溶氧水平,改善供氧条件,维持溶氧的相对稳定,增加菌体浓度,提高L-天冬酞胺酶发酵水平(21%左右)。
3.2控制氧传递速率
氧传递速率主要考虑KLa的影响因素。从一定意义上讲,KLa愈大,好氧生物反应器的传质性能愈好。控制KLa的途径可分为操作变量、反应液的理化性质和反应器的结构3个部分。操作变量包括温度、压力、通风量和转速(搅拌功率)等;发酵液的理化性质包括发酵液的黏度、表面张力、氧的溶解度、发酵液的组成成分、发酵液的流动状态、发酵类型等;反应器的结构指反应器的类型、反应器各部分尺寸的比例、空气分布器的形式等。当然有些因素是相互关联的[1、2]。
4 结束语
发酵液中的氧含量对菌体生长和产物形成都有着重要的影响,溶氧量的控制主要从氧的溶解和传递两个方面考虑。随着计算机和自动化技术的发展,发酵工业中从DO 的测量到分析控制都正逐步走向自动及控制一体化模式,研究利用DO 作为补料的在线控制信号将大大提高了发酵调控的准确性和自动化性能。
参考文献:
[1]赵东峰,梁春艳,任翔等.溶氧对生物转化泰乐菌素为其酰化物的影响[J]. 中国医药工业杂志,2006,37(3):162-164
[2]林剑,郑舒文,徐世艾.搅拌与溶氧对黄原胶发酵的影响[J].中国食品添加剂,2004(2):63-65
[3]郜培,陆静波等.溶氧浓度对谷氨酸发酵关键酶的影响[J].食品与发酵工食品与发酵工业,2005(31):72-75
[4]冯旭川. 溶氧测量在双丙氨磷(HB)生产中的应用[J]. 食品与发酵工业,2007,33(9):174-175.
啤酒中溶解氧的控制解读
74 酿酒科技·2009年第2期(总第176期)LIQUOR -MAKING SCIENCE &TECHNOLOGY 2009No .2(Tol .176 啤酒中溶解氧的控制 王劲松 (南京金星啤酒有限公司技术质量部, 江苏 摘要:关键词: 南京 210039 啤酒生产过程中除发酵初期氧有利于酵母细胞合成外,其他工序均应严格控制氧的摄入量,防止啤酒中啤酒;溶解氧;控制 文献标识码:B 文章编号:1001-9286(2009)02-0074-03 的还原物质被氧化而影响啤酒质量。溶解氧含量的高低是决定啤酒非生物稳定性和风味稳定性的主要因素之一。中图分类号:TS262.5;TS261.4 Analysis of the Control of Dissolved Oxygen in Beer WANG Jin-song (Technique&Quality Department of Jinxing Beer Co.Ltd., Nanjing, Jiangsu 210039, China
Abstract :Oxygen is helpful for the synthesis of barm cells in early fermentation period in beer production. However, in other production proce-dures, oxygen absorption should be under strict control to prevent the oxidation of reducing substances in beer which would further damage beer quality. The content of dissolved oxygen is the main factor influencing non-biological stability and flavor stability of beer. (Tran.by YUE Yang Key words :beer; dissolved oxygen; control 成品啤酒中溶解氧的含量应控制在0.1mg/L左右,过高易导致啤酒产生类似脂肪氧化后的臭味,影响啤酒的爽快、醇厚性,且使啤酒的后苦味增强,甚至由于成品啤酒中过多氧的存在造成本已还原的双乙酰再次生成,使啤酒产生“生青味”,并氧化啤酒中的一些风味物质,使啤酒风味变差。氧能与蛋白质、多酚化合物反应形成永久性浑浊,降低啤酒的非生物稳定性。啤酒摄入氧主要在过滤与灌装工序,过滤工序中如果能够把清酒的溶解氧水平控制在0.1mg/L以下,就可以有效地提高啤酒的稳定性,延长啤酒贮藏。 发酵液中溶解氧含量很低,经过硅藻土过滤后,清酒溶解氧含量明显增高, 一般用CO 2背压,可达到0.3~ 0.5mg/L,如果用压缩空气背压,清酒中的溶解氧含量可 达1.0mg/L,由于氧的存在,使啤酒中残留的α-乙酰乳酸氧化脱羧而使双乙酰的含量增高。 1.3影响啤酒的风味 啤酒的风味组成包括双乙酰及其前体、醛类、酯类、 高级醇、含硫化合物、挥发性酒花组分等。这些风味组成成分所含有的醛基、羟基、巯基、烯或烯醇基等, 都可以被氧化或进行加氧反应, 结果可能会使啤酒中原来感觉不到的风味成分转化为能感觉到的风味成分, 或改变原有风味成分的呈味性质从而产生异杂味, 并且导致啤酒口感粗劣。例如,多酚物质受到氧化聚合会使啤酒产生涩味、后苦味、辛辣味;酒花中A2酸和不饱和萜烯化合物受到氧化, 会使
好氧发酵过程中溶氧的影响因素和控制策略
好氧发酵过程中溶氧的影响因素和 控制策略 作者:刘伟 单位:河北天俱时自动化科技有限公司 2009年4月10日
好氧发酵过程中溶氧的影响因素和控制策略 刘伟 河北天俱时自动化科技有限公司 摘要:好氧发酵过程中溶氧检测值受多种参数的影响,包括生物代谢过程本身,也包括外部补料、通风量等,为了保证发酵过程中合适的溶解氧含量,对溶氧值进行控制,本文分析了溶氧检测值的影响因素,并指出溶氧控制的一般性控制策略。 关键词:好氧发酵,溶氧调节 一、引言 好氧发酵过程溶氧浓度(DO)是一个非常重要的发酵参数,它既影响细胞的生长,又影响产物的生成。控制发酵液溶氧值一方面可以改善微生物的生长代谢环境,有效促进发酵单位的提高,另一方面还可以起到节能降耗的作用,对企业生产意义重大。 二、影响因素 通常情况下,对发酵液溶氧参数影响较大的几个物理参数包括:通风量、搅拌转速、发酵罐温度、压力等。 通风量的影响 通风量的影响是最直观的,溶氧值大小的影响最主要的是进入发酵罐的氧的量,因为在好氧发酵过程中,如果截断进风的补给发酵液中的氧很快将被微生物消耗掉,通常在进风管道上安装调节阀门进行进风流量的调节。 搅拌的影响 由于溶氧电极在工作中存在明显的电流,自身消耗大量的氧。电
极的信号与氧向电极表面传递的速率成比例,而氧的传递速率则受氧跨膜扩散速率控制。这一速率与发酵液的浓度成比例,其比值(以及电极的校准)取决于总的传质过程。电极的一般工作条件是,氧向膜外表面的传递速率很快且不受限制。因此整个过程受跨膜传递的限制,比例常数(传质系数)较易维持恒定。发酵实验时搅拌操作可以获得满意的跨膜传递速率。需要指出,在对电极进行最初校准的过程中,必须对发酵罐进行搅拌。 温度的影响 溶氧电极的信号随温度的升高而显著增强,这主要是因为温度影响氧的扩散速率。发酵实验过程中需控制发酵罐的温度,因为即使0.5℃左右的温度变化,也会使电极信号发生显著变化(超过1%)。溶氧读数的周期性变化(每隔若干分钟观察1次)显示了温度波动的影响,而且较大的温度变化能引起校准的较大漂移。因此在实验过程中改变温度控制时要格外注意。在以发酵罐的操作温度进行控制以前,需对溶氧电极进行校准。考虑到上述影响的存在,一些溶氧电极带有温度传感器等仪表,以实现自动温度补偿。此外,对于具有计算机监控的发酵罐,可利用来自独立的温度传感器的信号,由相关软件实现温度补偿。 压力的影响 压力变化会影响溶氧电极的读数,尽管这实际上反映了溶氧的变化情况。电极的响应主要由溶液的平衡氧分压确定。读数通常表示为大气压下空气的饱和度(%),100%的溶氧张力(DOT)约相当于160mmHg (1mmHg≈133Pa)的氧分压。如果发酵液的平衡气体总压发生变化,
水域溶解氧分布特征及影响因素研究综述
水域溶解氧分布特征及影响因素研究综述 摘要:基于水域溶解氧分布特征及影响因素的前期研究成果,本文对其进行系统分区整理,总结归纳影响溶解氧含量变化的主要因素,并对后续研究方向提出建议,望能够对同行业有一定的参考性价值。 关键词:溶解氧;影响因素;研究综述 随着海洋经济不断发展,海洋污染日益严重,富含N、P等营养物质的生活、工业废水大量排入海洋造成某些海域富营养化,直接导致某些海区海水缺氧现象日益严重。溶解氧(DO)代表溶解于海水内氧气的含量,绝大部分的海洋生物均需依赖溶解氧来维持生命。溶解氧水平不仅是衡量水体自净能力的一个重要指标,也反映了海洋生物的生长状况和海水的环境质量,对海洋渔业发展有重大影响。 然而,当前低氧已经成为世界范围内沿岸物理交换不良水域的一个主要环境问题,典型的例子当属长江口外的季节性大范围底层低氧现象[1]。Vaquer-Sunyer 等人研究发现,许多海洋生物在溶解氧3mg/L~4mg/L时就受到显著影响[2]。此外,溶解氧水平在很短时间内就会发生剧烈变化,因此海洋溶解氧一直是保持海洋生态平衡最重要的环境因素之一。 为及时有效应对溶解氧含量过低对海洋环境产生的恶劣影响,针对溶解氧含量的分布特征及影响因素研究,一直是海洋环境监测和海洋动力学、海洋化学研究的重要内容之一,国内外众多学者针对重点海域、湖泊及生物养殖区溶解氧的分布特征及影响因素给予大量关注,整理归纳,主要有以下几片海域。 长江口海域溶解氧分布特征及影响因素研究 张莹莹、张经等[3]对长江口及其毗邻海域某断面上的溶解氧的分布特征的研究结果表明,在6月的航次中,DO值随着离岸距离的增加逐渐增加,底层DO值低于表层;8月份调查海区底层明显出现低氧状态,形成原因主要是海水层状结构稳定水交换较弱和有机物分解耗氧;长江径流N、P污染物的不断输入为低氧区域表层浮游植物的生长提供了丰富的营养盐,从而加剧了氧亏损。石晓勇、陆茸等[4]对长江口邻近海域的秋季溶解氧分布特征及主要影响因素进行了研究,结果显示,溶解氧平面分布整体上呈近岸高、外海低,表层高、底层低的分布趋势,在约20m深度存在溶解氧跃层。调查海域溶解氧不饱和状态由表层至底层逐渐加剧。该海域秋季溶解氧分布主要受陆地径流和外海水等物理过程控制,生物活动仅在底层溶解氧低值区有较大的影响。 黄东海海域溶解氧分布特征及影响因素研究 胡小猛、陈美君等[5]分析了黄东海海域的DO分布和季节变化规律,结果表明:基于太阳辐射导致的海水温度时空差异,影响黄东海DO分布及其季节变化的主要因素是黄海暖流和大陆入海径流。杨庆霄、董娅婕等[6]描述了黄、东
溶解氧影响因素
什么是水的溶解氧?受哪些因素的影响? 溶解于水中的游离氧称为溶解氧,常以mg/L、ml/l等单位来表示.天然水中氧的主要来源是大气溶于水中的氧,其溶解量与温度/压力有密切关系.温度升高氧的溶解度下降,压力升高溶解度增高.天然水中溶解氧含量约为8-14mg/l,敞开式循环冷却水中溶解氧一般约为5-8mg/L. 水体中的溶解氧含量的多少,也反映出水体遭受到污染的程度.当水体受到有机物污染时,由于氧化污染质需要消耗氧,使水中所含的溶解氧逐渐减少.污染严重时,溶解氧会接近于零,次数厌氧菌便滋长繁殖起来,并发生有机物污染的腐败而发臭.因此,溶解氧也是衡量水体污染程度的一个重要指标. 影响溶解氧测量的因素氧的溶解度取决于温度、压力和水中溶解的盐,另外氧通过溶液扩散比通过膜扩散快,如流速太慢会产生干扰。 1. 温度的影响由于温度变化,膜的扩散系数和氧的溶解度都将发生变化,直接影响到溶氧电极电流输出,常采用热敏电阻来消除温度的影响。温度上升,扩散系数增加,溶解度反而减小。温度对溶解度系数a 的影响可以根据Henry 定律来估算,温度对膜扩散系数β可以通过阿仑尼乌斯定律来估算。 (1)氧的溶解度系数:由于溶解度系数a 不仅受温度的影响,而且受溶液的成分的影响。在相同氧分压下,不同组分的实际氧浓度也可能不同。根据亨利定律可知氧浓度与其分压成正比,对于稀溶液,温度变化溶解度系数a 的变化约为2%/ ℃。 (2)膜的扩散系数:根据阿仑尼乌斯定律,溶解度系数β与温度T 的关系为: C=KPo2·exp(-β/T),其中假定K、Po2 为常数,则可以计算出β在25℃时为2.3%/ ℃。当溶解度系数a 计算出来后,可通过仪表指示和化验分析值对比计算出膜的扩散系数(这里略去计算过程),膜的扩散系数在25℃时为1.5%/℃。 2. 大气压的影响根据Henry 定律,气体的溶解度与其分压成正比。氧分压与该地区的海拔高度有关,高原地区和平原地区的差可达20%,使用前必须根据当地大气压进行补偿。有些仪表内部配有气压表,在标定时可自动进行校正;有些仪表未配置气压表,在标定时要根据当地气象站提供的数据进行设置,如果数据有误,将导致较大的测量误差。
溶解氧控制系统方案讲课教案
溶解氧控制系统方案(修改稿) 一、概述 污水生化处理的耗氧反应是重要的反应阶段,目前国内的污水生化处理的加氧工作都是采用大功率的鼓风机实现的,需要消耗大量的电能,在保证水质的情况下,如何实现节能控制,降低成本,是目前国内外需要认真考虑的问题。污水中的微生物对氧的需求量是一定的,少了会降低水质,多了不仅不能保证水质,而且还浪费能源,通常以溶解氧的含量来判断某个时候供氧量是否合适。但是,所需要的溶解氧不应该是一个定值,它是随着污水的浓度、天气、气温、时间变化的函数。就是说污水处理过程控制具有显著的非线性、大滞后、多变量、时变性的特点。为此,需要研究在不同工况条件下,溶解氧设定值的优化。建立污水生化处理过程的溶解氧变化的模型,并依据该模型对鼓风量进行低能耗的优化控制。建立能适应环境变化的基于污水生化过程。 在国内曝气量优化控制方面进行了一些研究,常用的方法主要是基于溶解氧目标值的PID 控制。但是,由于污水生化处理过程的非线性、时滞及溶解氧目标值时变性,使PID 控制很难跟踪溶解氧目标值。在PID 控制基础上发展了变增益的PID控制、模糊PD控制, 这些方法仍然不能解决过程不确定性问题。为此,许多学者采用神经网络自动诊断、模糊专家控制等智能控制方法。但是,对于复杂的污水生化处理过程,学习样本有限和专家知识不足,使这些方法的效果不明显。国外这方面成功经验也很少。所以说国内的污水处理过程的自动化水平还有待提高,大多数只停留在数据采集和简单控制(如提升泵、污泥回流泵、鼓风机的
开关控制)的水平上。污水处理过程建模和控制方面的研究属于刚起步,主要用模糊神经网络控制、递阶神经网络、仿人智能、自适应、专家知识等方法来构建可知模型,取得一定成功。但这些方法有待深入研究和完善。 二、方案提出 我们在总结先前的经验和实际运用的基础上,对于污水的入水水质、生化反应过程、出水水质波动等各种在线、离线检测数据进行科学分析,结合智能检测、诊断与控制技术对生物化过程进行综合控制与优化,以保证在各种干扰条件下出水水质稳定达标。主要采用“前馈+串级”的组合控制模型,以污水处理厂进水区温度、流量、进水水质检测值等为前馈信号,来决策溶解氧的给定值;生化处理池中溶解氧检测仪为反馈信号给主回路;鼓风机风量用风量传感器检测作为反馈信号和变频器构成副回路。各回路控制规律为:前馈采用人工智能;主回路采用模糊PID 控制;副回路采用传统的PID 控制。为节省成本对污泥回流控制可以根据回流量流量大小分1-3 档位的控制。参见图2-1 生物化过程前馈- 串级控制系统。
溶解氧对发酵的影响及其控制
溶解氧对发酵的影响及其控制 1 溶解氧对发酵的影响 溶氧是需氧发酵控制最重要的参数之一。由于氧在水中的溶解度很小,在发酵液中的溶解度亦如此,因此,需要不断通风和搅拌,才能满足不同发酵过程对氧的需求。溶氧的大小对菌体生长和产物的形成及产量都会产生不同的影响。如谷氨酸发酵,供氧不足时,谷氨酸积累就会明显降低,产生大量乳酸和琥珀酸。 1.1 溶氧量在发酵的各个过程中对微生物的生长的影响是不同的 改变通气速率发酵前期菌丝体大量繁殖,需氧量大于供氧,溶氧出现一个低峰。在生长阶段,产物合成期,需氧量减少,溶氧稳定,但受补料、加油等条件大影响。补糖后,摄氧率就会增加,引起溶氧浓度的下降,经过一段时间以后又逐步回升并接近原来的溶解氧浓度。如继续补糖,又会继续下降,甚至引起生产受到限制。发酵后期,由于菌体衰老,呼吸减弱,溶氧浓度上升,一旦菌体自溶,溶氧浓度会明显上升。 1.2 溶氧对发酵产物的影响 对于好氧发酵来说,溶解氧通常既是营养因素,又是环境因素。特别是对于具有一定氧化还原性质的代谢产物的生产来说,DO的改变势必会影响到菌株培养体系的氧化还原电位,同时也会对细胞生长和产物的形成产生影响。 在黄原胶发酵中,虽然发酵液中的溶氧浓度对菌体生长速率影响不大,但是对菌体浓度达到最大之后的菌体的稳定期的长短及产品质量却有着明显的影响。
需氧微生物酶的活性对氧有着很强的依赖性。谷氨酸发酵中,高溶氧条件下乳酸脱氢酶(LDH)活性明显比低溶氧条件下的LDH酶活要低,产酸中后期谷氨酸脱氢酶(GDH)的酶活下降很快,这可能是由于在高溶氧条件下,剧烈的通气和搅拌加剧了菌体的死亡速度和发酵活性的衰减。 DO值的高低还会改变微生物代谢途径,以致改变发酵环境甚至使目标产物发生偏离。研究表明,L-异亮氨酸的代谢流量与溶氧浓度有密切关系,可以通过控制不同时期的溶氧来改变发酵过程中的代谢流分布,从而改变Ile等氨基酸合成的代谢流量。 2 溶氧量的控制 对溶解氧进行控制的目的是把溶解氧浓度值稳定控制在一定的期望值或范围内。在微生物发酵过程中,溶解氧浓度与其它过程参数的关系极为复杂,受到生物反应器中多种物理、化学和微生物因素的影响和制约。从氧的传递速率方程也可看出,对DO值的控制主要集中在氧的溶解和传递两个方面。 2.1 控制溶氧量(C*-CL)是氧溶解的推动力,控制溶氧量首要因素是控制氧分压(C*)。高密度培养往往采用通入纯氧的方式提高氧分压,而厌氧发酵则采用各种方式将氧分压控制在较低水平。如啤酒发酵,麦汁充氧和酵母接种阶段,一般要求氧含量达到8~10PPM;而啤酒发酵阶段,一般啤酒中的含氧量不得超过2PPM。 2.2控制氧传递速率氧传递速率主要考虑KLa的影响因素。从一定意义上讲,KLa愈大,好氧生物反应器的传质性能愈好。控制KLa的途径可分为操作变量、反应液的理化性质和反应器的
溶解氧和造成溶氧不足的原因
溶解氧和造成溶氧不足的原因 内容摘要:水质对养殖的水生动物起着至关重要的作用。正常的养殖水体(未被工业污染),影响水质的主要指标是pH值(酸碱度)、溶解氧、氨氮、亚硝酸盐、硫化氢等5项指标。重金属、农药、化工污水等污染的水源,如超出《渔业水质标准》,则不能用于水产养殖生产。对养殖用水,必须定期进行全面科学检测。如果片面检测或仅凭经验主观判断,可能招致灾难性的后果。 一、养鱼先养水,好水养好鱼 俗话说:“养鱼先养水,好水养好鱼”。水是鱼、虾、蟹、鳖、龟、蛙等水产养殖动物的生活环境,水质的好坏直接影响到水产养殖生物的生长和发育,从而影响到产量和经济效益。每一种水产动物都需要有适合其生存的水质条件,水质若能满足要求,养殖动物就能顺利生长发育。如果水质的一些基本指标超出生物的适应和忍耐范围,轻者养殖动物生长速度缓慢,成活率降低,饲料系数提高,经济效益下降。重者可能造成养殖动物的大批死亡,引起严重的经济损失。 恶化的水质不仅有害于动物机体的健康,甚至还危及它们的生命。众所周知水是一种优良的溶剂和悬浮剂,它可溶解各种气体,如氧气、二氧化碳、氨和硫化氢等,也可溶解各种盐类,如亚硝酸盐、磷酸盐、碳酸盐、硫酸盐等,还可悬浮尘埃、有机碎屑、细菌、藻类、小型的原生动物以及各种虫卵等。水体中溶解和悬浮的种种有形或无形的物质和成分,其中一部分对水产动物的生长、发育是必需的,有一些是无益的,而另一部分则是有害的,或者在含量较多时有害,同样,它们对水体中的其他生物,也有有利和不利的方面,特别是某些成分对养殖动物生长和健康不利,而对一些病原体(如病原菌、寄生原生动物)的繁殖、滋生以及产生毒力等是必需的,就容易导致疾病的发生。 水质对养殖的水生动物起着至关重要的作用。正常的养殖水体(未被工业污染),影响水质的主要指标是pH值(酸碱度)、溶解氧、氨氮、亚硝酸盐、硫化氢等5项指标。重金属、农药、化工污水等污染的水源,如超出《渔业水质标准》,则不能用于水产养殖生产。对养殖用水,必须定期进行全面科学检测。如果片面检测或仅凭经验主观判断,可能招致灾难性的后果。 科学的检测的可得出正确的数据。这些数据可以告诉养殖者水质的状况,从而判断水质是否满足水产动物生长的要求,以及是否会引起动物发病。水质检测的另一个作用是为改善水质、鱼病用药提供依据,减少因施肥、投饵、用药等日常管理造成的鱼类死亡损失。因此,水质检测是保证水质健康的必要,也是水产健康养殖的基础。 二、溶解氧——水产动物生命要素 同人一样,水产动物也必须在有氧的条件下生存,不同的是人呼吸空气中的氧气,而水产动物呼吸的是水体中的溶解氧。水体缺氧可使其浮头,严重时泛塘致死。 1. 养殖(育苗)水体溶氧要求 一般来说,养殖(育苗)水体的溶解氧应保持在5~8mg/l(ppm),至少应保持3mg/l 以上。各种鱼、虾类的需要溶解氧条件如表1。
溶解氧使用说明书
敬告用户 ●使用时请遵守本说明书之操作规程及注意事项。 ●在收到仪表时,请小心打开包装,查看仪表及配件是否因运输而损坏,如有损坏,请立 即通知上海博取仪器有限公司或经销商,并保留包装物以便寄回处理。 ●在使用过程中若发现仪器工作异常或损坏请联系经销商或上海博取仪器有限公司,切勿 自行修理。 ●为使测量更精确,仪器须经常配合电极进行校正;若您的电极购买时间已近一年,请注 意更换电极膜头。 ●仪器使用满一年后须送计量部门或有资格的检定单位进行检定,合格后方可再用。 ●因产品更新换代,本说明书如有变动恕不另行通知。 概述 DOG-2092 型工业溶解氧仪表是用于测试和控制溶解氧的的精密仪表。该仪表具有微型计算机存储、计算和补偿有关测定溶解氧值的所有参数;可对相关数据进行设置,如海拔、盐度等;其功能全.性能稳定.操作简便等特点,使其成为溶解氧测试和控制领域的理想仪表。 DOG-2092 型工业溶氧仪采用带背景光LCD显示,具备错误指示;自动温度补偿;隔离式4-20 mA电流输出;双组继电器控制,高低点报警指示;掉电记忆,无需后备电池,资料保存十年以上。 DOG-2092 型工业溶氧仪电极为美国原装膜头,详见《电极使用说明书》。 包装说明 请确认您所购买的DOG-2092 型仪表包装盒是否完整,如有包装损坏或是有任何配件短缺的情形,请您尽快与经销商或上海博取仪器有限公司联系。 ●DOG-2092 仪表一台 ●固定锁紧条两根 ●用户使用说明书一本 ●溶氧电极一支 1
技术性能 1. 测量范围: 0.00~19.99mg/L 0.0~199.9% 2. 分辨率: 0.01 mg/L 0.01% 3. 精确度: ±1.5%F.S 4. 控制范围: 0.00~19.99mg/L 0.0~199.9% 5. 温度补偿: 0~60℃ 6. 输出信号: 4~20mA 的隔离保护输出 7. 控制输出方式: ON/OFF 继电器输出接点 8. 继电器承受负载: 最大交流230V 5A 最大交流115V 10A 9. 电流输出负载: 允许最大负载为500Ω 10. 对地电压绝缘度: 最小负载为500VDC 11. 工作电压: 230V AC ±10%、50/60Hz 12. 尺寸: 96×96×115mm 13. 开孔尺寸: 91×91mm 14. 重量: 1Kg 15. 仪器的工作条件: ① 环境温度:5~35℃ ② 空气相对湿度: ≤80% ③ 除地球磁场外周围无强磁场干扰。 前面板说明 图1 1:高报警指示 2:低报警指示 3:毫克/升指示 4:百分比指示 5:确认 6:数字减少 7:数字增加 8:菜单循环模式 9:显示屏 2
1 溶解氧对发酵的影响
1 溶解氧对发酵的影响 溶氧是需氧发酵控制最重要的参数之一。由于氧在水中的溶解度很小,在发酵液中的溶解度亦如此,因此,需要不断通风和搅拌,才能满足不同发酵过程对氧的需求。溶氧的大小对菌体生长和产物的形成及产量都会产生不同的影响。如谷氨酸发酵,供氧不足时,谷氨酸积累就会明显降低,产生大量乳酸和琥珀酸。 1.1 溶氧量在发酵的各个过程中对微生物的生长的影响是不同的 改变通气速率发酵前期菌丝体大量繁殖,需氧量大于供氧,溶氧出现一个低峰。在生长阶段,产物合成期,需氧量减少,溶氧稳定,但受补料、加油等条件大影响。补糖后,摄氧率就会增加,引起溶氧浓度的下降,经过一段时间以后又逐步回升并接近原来的溶解氧浓度。如继续补糖,又会继续下降,甚至引起生产受到限制。发酵后期,由于菌体衰老,呼吸减弱,溶氧浓度上升,一旦菌体自溶,溶氧浓度会明显上升。 1.2 溶氧对发酵产物的影响 对于好氧发酵来说,溶解氧通常既是营养因素,又是环境因素。特别是对于具有一定氧化还原性质的代谢产物的生产来说,DO的改变势必会影响到菌株培养体系的氧化还原电位,同时也会对细胞生长和产物的形成产生影响。[1] 在黄原胶发酵中,虽然发酵液中的溶氧浓度对菌体生长速率影响不大,但是对菌体浓度达到最大之后的菌体的稳定期的长短及产品质量却有着明显的影响。 [2] 需氧微生物酶的活性对氧有着很强的依赖性。谷氨酸发酵中,高溶氧条件下乳酸脱氢酶(LDH)活性明显比低溶氧条件下的LDH酶活要低,产酸中后期谷氨酸脱氢酶(GDH)的酶活下降很快,这可能是由于在高溶氧条件下,剧烈的通气和搅拌加剧了菌体的死亡速度和发酵活性的衰减。[3] DO值的高低还会改变微生物代谢途径,以致改变发酵环境甚至使目标产物发生偏离。研究表明,L-异亮氨酸的代谢流量与溶氧浓度有密切关系,可以通过控制不同时期的溶氧来改变发酵过程中的代谢流分布,从而改变Ile等氨基酸合成的代谢流量。[4] 2 溶氧量的控制
溶氧控制技术及曝气研究教学文稿
溶氧控制技术及曝气研究 1.污水中溶解氧的控制依据主要有哪些,如何优化? 溶解氧的概念可以理解为水中游离氧的含量,用DO表示,单位mg/L。溶解氧在实际的污水、废水处理操作中具有举足轻重的作用,这一指标的恶化或者波动过大,往往会导致活性污泥系统的稳定性大幅波动,自然对处理效率的影响也非常明显。 <1>书面定义及实际操作的理解 应该说,理论上来讲,当曝气池各点监测到的DO值略大于0(如0.01mg/L)时,可以理解为充氧正好满足活性污泥中微生物对溶解氧的要求。但是事实上,我们还是没有简单的将溶解氧控制在大于0的水平,而是应用教科书中的做法,把DO控制在1~3mg/L的范围内。究其原因还是因为,整个曝气池而言,溶解氧的分布和各曝气池区域内的溶解氧需求是不一样的。为了保守的稳定活性污泥在分解有机物或自身代谢过程中对溶解氧的需求,才将DO控制在1~3mg/L。 但是,实际操作和书面上固定僵化的DO理论值往往是不同的,不能只是依照书面上理论值,还要充分结合实际情况! 从实际情况看,发现在实际运行中,很多情况下将溶解氧控制在1~3mg/L是没有必要的,特别是控制超过3mg/L更是毫无意义,唯一的结果只是导致电能的浪费和出水中含有细小悬浮颗粒。所以,在根据书面理论同时要结合实际情况合理控制溶解氧。 <2>污水中溶解氧的控制依据及优化 主要依据:原水水质(有机物、氮、磷)、活性污泥的浓度、污泥沉降比、pH、温度、食微比(F/M)等进行控制。 当然,书面上给的理论值:一般好氧条件下溶解氧浓度为≥2.0 mg/L,厌氧条件下溶解氧浓度为≤0.2 mg/L,缺氧条件下溶解氧浓度为0.2-0.5 mg/L。具体
溶氧对氨基酸发酵的影响及控制
溶氧对氨基酸发酵的影响及控制 【摘要】本文对溶解氧在氨基酸微生物工业发酵的影响及控制策略进行了系统分析和探讨。 【关键词】氨基酸发酵;DO;溶解氧控制 利用微生物发酵生产氨基酸的技术已历半个多世纪。氨基酸生物发酵是一个复杂的生化反应过程,溶解氧是氨基酸发酵生产工艺的一个非常重要的控制参数[1]。发酵液中溶氧的高低直接影响菌体的生长和代谢产物的积累,并最终决定着氨基酸产量的高低[2]。因此,研究溶解氧在氨基酸微生物工业发酵中对产物生产的影响及控制策略,对氨基酸发酵工艺管理的优化和工艺过程的放大具有重要意义。笔者对氨基酸发酵工艺的供氧问题进行了分析与探讨,对增加溶氧的主要方法进行了综述,以期对氨基酸工业生产提供一定的借鉴。 1 氧在氨基酸好氧发酵过程的作用 氨基酸发酵生产菌大多为需氧菌或兼性厌氧菌。发酵液中的氧(溶解氧)是菌体生长与代谢的必需品。氨基酸的发酵过程主要包括菌体生长和代谢产物积累2个阶段,溶解氧在氨基酸发酵中的主要作用有两点:①参与氨基酸生物合成所必须的ATP,以完成生物氧化作用,并使菌体能够充分生长;②只有在氧的存在下,氨基酸的生物合成过程中产生的NAD(P)H2才能被氧化生成NAD(P),确保反应向合成氨基酸产物的方向进行。因此在氨基酸发酵过程中要保持一定的溶氧量来满足菌体生长和产酸的耗氧需要;溶氧的高低,应该根据不同菌种,不同培养阶段和培养条件等具体情况决定,将溶解氧控制在一个最佳水平以实现糖和酸最大转化率。 1.1 溶解氧对菌体生长的影响 氨基酸发酵的前期是菌体生长的主要阶段,如果发酵液中溶解氧的浓度受到限制,就会影响菌体的生长与繁殖,进而影响到最终的氨基酸产量。如谷氨酸发酵过程中,在菌体生长期,溶解氧浓度过低,在产酸期则抑制谷氨酸合成,生成大量代谢副产物;反之,溶解氧浓度过高,菌体生长受到高氧抑制,生长慢,耗糖慢,造成后期菌体容易衰老,导致糖酸转化率偏低[3]。 1.2 溶解氧对发酵产物积累的影响 氨基酸发酵按照合成途径不同,需氧量的差异可分为三类,第一类,是合成期需供氧充分,产酸量才能达最大的谷氨酸系氨基酸;第二类,是合成期满足供氧,就能达到最高产量,一但供氧受限,产量会受影响但并不十分明显的是天冬氨酸系氨基酸;第三类,是只有在供氧受限、细胞呼吸受抑制时,才能获得最大量的氨基酸,如果供氧充足,产物形成反而受到抑制的亮氨酸、缬氨酸和苯丙氨酸等。因此,在实际生产应用中,应根据合成氨基酸种类及具体需要确定溶氧控
梅特勒-托利多_过程分析_【故障处理】溶氧电极发酵后期读数波动_任嘉麟
知识标题:发酵后期溶氧电极波动的故障处理方法 标签:氧,光学氧,电极,溶解氧,细胞培养,波动 知识来源:□原创;□官方 知识类型:□接线图;□安调指导;□故障处理;□校准说明;□维护保养;□证书;□专业理论;□其他__________ 专业分类:□PH;□DO;□GAS;□电导率;□TOC;□浊度;□CO2;□Si/Na;□Cl/S;□微生物;□Ozone;□其他__________ 设备类型:□传感器;□变送器;□护套;□线缆;□分析仪;□自清洗; □其他__________ 信号类型:□模拟;□智能ISM;□其他__________ 变送器:□M100;□M200;□M300;□M400;□M700;□M800;□M420;□X100;□便携式;□其他__________ 适用行业:□电力;□食品;□化工;□制药;□其他__________ 证书类型:□防暴;□通讯协议;□卫生;□材料材质;□生产标准;□出场证书; □其他__________ 摘要: 本文主要介绍了生物发酵罐,特别是研发小罐,在发酵后期读数波动的解决方法。
下图是细胞培养中常见的一种溶解氧测量读数波动现象,常常会发生在发酵后期。用户往往会发现在发酵后期读数会有不可控波动情况产生。以下介绍了一些故障排查办法。 发酵溶解波动趋势图 遇到类似问题以后,最常见的手段就是过程校准了。但是过程标定往往会更改斜率,影响测量的准确度。
产生这种故障现象的原因一般分为以下几类: 1.极谱氧电极的膜片和电解液没有定期更换或者校准错误导致 2.极谱氧电极内电极积液造成读数波动 3.气泡干扰 4.随着发酵进行,生物生长覆盖传感器膜的现象 5.消泡剂干扰 解决办法: 1.上罐标定前必须正确检测电极性能SOP。严格按照以下步骤操作可以最大程度 的避免上罐后电极异常和波动的产生。在检测电极前建议先更换溶氧膜片和电解液。并作极化(建议6小时) 检测内电极和电极杆的空载电流值:如图所示,将电极连接仪表,并取下溶氧膜把内电极擦干,置于空气中,同时观察电流值。 正常电极空载电流值<±0.03nA(一般使用的电极也应小于±0.5nA)如果大于±1nA则说明电极内有积液,需返厂维修。
影响水中化学需氧量检测的因素分析
影响水中化学需氧量检测的因素分析 水体污染的重要指标之一便是化学需氧量过高,文章从还原性物质、空白实验值及其他方面分析对化学需氧量测定结果的影响进行了分析,并提出相应的解决方法。希望能够为相关工作提供参考。 标签:化学需氧量;检测;因素分析 化学需氧量作为衡量水质标准的一项重要指标,其检测结果的准确性也受到了有关政府部门的高度重视。水中存在着很多还原性的物质,如氯离子、二价铁离子、硫离子等,这些物质会影响化学需氧量测定结果的准确性;此外,水样的取样过程、水样的保存、运输和实验过程中使用的试剂质量、实验用水、试剂加入量、回流时间,以及不同实验人员的操作等,都会对实验结果造成一定程度的影响。因此,作为实验室检测人员有必要对影响其检测结果的因素进行分析,并在检测过程中消除这些因素,保证结果的准确性。文章重点从以下几个方面对影响COD检测结果的准确性的因素进行了简单分析。 1 水中的还原性物质对化学需氧量检测的影响及其解决办法 1.1 氯离子对测定的影响及解决方法 氯离子能够降低催化剂的浓度,导致有机物在进行氧化时并不完全,是测定过程中主要的影响因素。银离子会与氯离子发生反应,使得测定的结果较标准值低;在酸性的条件下,氯离子会被重铬酸钾氧化,反应中产生氯气,氯气能够将水中其他的还原性离子氧化如硫离子和二价铁离子,并且自身为气态能够逸出,导致化学需氧量的测定值偏高。通常实验室采用加入硫酸汞的方法除去部分氯化物,经回流后,氯离子与硫酸汞结合成可溶性的氯汞络合物。 1.2 二价铁离子和硫离子对测定的影响及解决方法 一些水样当中含有二价铁离子和硫离子等干扰元素,在测定前要先测定原始的浓度,默认氧化量是固定的,在测定实验的计算中扣除二价铁离子和硫离子的耗氧量,从而得到实际的化学需氧量。但是这种方法只是理想环境下的方法,在实际应用中的可行性不大,因此可以在水样中提前通入空气,将二价铁离子和硫离子氧化形成沉淀进而除去。 1.3 氨分子或铵根离子对测定的影响及解决方法 当水中有氯离子存在时,氨根离子会发生这样的反应:6NH3+7Cr2O+56H+=6NO2+14Cr3++32H2O,对测定结果的影响更大。因此,可以对水中的氯离子进行消除或是利用重铬酸钾溶液进行测定。 2 空白实验的值对检测的影响及其解决办法
如何控制溶解氧
一、原辅材料的控制 1. 糖化生产时应根据每批进厂麦芽的指标,及时调整生产工艺,如下料温度、蛋白分解温度和时间。糖化温度和时间要根据麦芽质量加以调整,以保证投入原料的相对稳定。从源头上控制溶解氧的上升,以便有效地保证麦汁组分的相对稳定性,避免因啤酒口味差异,导致发酵液合流过滤时溶解氧的上升。 2. 应尽可能使用新鲜的辅料大米,因为随着陈化时间的延长,其游离脂肪的含量会逐渐增多,容易产生脂肪氧化的臭味。 二、糖化过程的控制 1. 为了尽可能避免在糖化过程中麦汁过多地吸氧,糖化醪应使用脱氧水兑制;糖化时尽量减少搅拌,以降低搅拌翻滚时空气溶入其中;糖化和麦汁过滤时最好采用惰性气体覆盖醪液表面,以隔绝空气,避免麦汁吸氧。另外还要根据糖化生产工艺要求,往糖化锅中加入乳酸或磷酸,保证醪液的pH值在5.4~5.8之间,如麦芽中β—葡聚糖的含量高于150mg/L时,应适量加入含β—葡聚糖酶高的复合酶,以降低麦汁黏度,保证醪液的液化效果,减少因麦汁过滤时耕糟、回流次数过多而吸氧。 2. 糊化锅、糖化锅、煮沸锅的人孔在生产时一定要关闭。从糊化锅进入糖化锅、过滤槽和煮沸锅的物料管最好设计为底部进料,以减少醪液和麦汁在输送过程中与氧气的接触机会。煮沸时间应严格控制在90分钟之内。缩短麦汁在回旋沉淀槽中停留的时间。麦汁冷却采用一段薄板冷却,缩短麦汁入罐时间并严格控制麦汁的充氧量。麦汁充氧量过少不利于酵母的繁殖,还会导致双乙酰还原发生困难。充氧量过多会使酵母前期发酵过于旺盛,形成过量的α—乙酰乳酸,还会消耗多量的快速还原物质,阻碍部分风味物质的还原,导致发酵后期双乙酰还原较慢,破坏啤酒香气,诱发异常气味同时副产物增多,高级醇含量高会使啤酒饮用后有“上头”的感觉,所以冷麦汁充氧量应控制在8ppm~10ppm之间。 三、发酵液的控制 1. 酵母发酵阶段如吸入过多氧气,会破坏发酵液中还原物质的平衡,大量消耗发酵液中的还原物质,降低成品啤酒的抗氧化能力。 2. 发酵大罐的备压气体:滤酒前,发酵液用CO2备压。 3. 发酵液压力要求:备压时CO2压力为0.10 Mpa~0.12Mpa,且CO2纯度为99.8%以上。 4. 由于市场竞争激烈,导致企业生产的酒品种较多,有时一种酒的库存较大,另一种酒已告急,需开另一罐酒,导致排土次数增加,未滤完酒的大罐上方空气进入发酵液,引起发酵液溶解氧升高。为了杜绝此类现象,发酵液开罐后原则上要求一次滤完,特殊情况不能一次滤完的,开罐时间不得超过3天。 四、滤酒管路的控制 滤酒的管路要采用不锈钢,且管路内壁光滑,接缝处平整,无凹凸不平的现象。还要保证滤酒的管路、泵、阀门密封良好。
发酵罐对发酵过程中溶氧控制
发酵罐对发酵过程中溶氧控制 在微生物/细胞发酵过程中,溶氧是需氧发酵控制中最重要的参数之一。溶氧的大小对发酵产物的形成及产量都会产生不同的影响,其结果直接影响整个发酵的效率。 现在市面上发酵罐对溶氧的控制,主流的方式是通过控制通入气体的量或者改变通入气体中氧气的比例来调节发酵液中溶氧%。更高一级的控制是将发酵液中溶氧%和通入气体的量、搅拌桨的转速、添加的补料及罐压进行关联,从而通过发酵系统自动控制这些参数来调节溶氧%。但是,直到今日,还没有任何一家发酵罐制造厂家的发酵罐能实现溶氧%与上述4个参数实现4级以上关联。现在市场上普遍能实现的是二级关联,及溶氧%与搅拌转速和通气量的关联,而其中做的最好的是赛多利斯(贝朗)发酵罐,由于其柜式集成化自动关联控制系统,能对发酵总体要求进行自动化多级(最多4级)参数关联调节。 2012年香港环球分析测试仪器有限公司引进了意大利Solaris发酵罐/生物反应器,其智能化的控制系统和全自动化的设计,实现了溶氧%与上述参数4级以上关联,准确说是在参数上下限限制条件内,能实现无限制关联,从而使发酵过程中溶氧%的控制更加方便和精确,并为高密度培养中需要更高的溶氧浓度提供了可能。 意大利Solaris发酵罐/生物反应器的这一特点,在不同程度上超越了赛多利斯(贝朗)等同类厂家,使其在全球的用户感受到实实在在的技术革新。 Solaris发酵罐/生物反应器实现溶氧%无限制关联界面图如下: 上图设置方式是先设定一个你需要的溶氧%,然后,将其与搅拌桨转速关联,如果当转速达到设定的上限的时候实现了你需要的溶氧%,就不进行下一级的关联;如果没有达到你需要的溶氧%,那么你就可以设置2级关联,如果达到设定参数的上限还未达到你需要的溶氧%,那么你就可以设置3级关联,如果达到设定参数的上限还未达到你需要的溶氧%,那么你就可以设置4级关联,如此循环下去,直至达到你需要的溶氧%。在此设置关联参数过程中,同一参数可重复多次设定。
溶氧对发酵的影响及其控制
溶氧对发酵的影响及其控制 摘要:发酵液中的溶氧浓度(Dissolved Oxygen,简称DO)是影响发酵的关键因素,对微生物的生长和产物形成有重要的影响。要根据氧的溶解特性及微生物对氧的需求,分析溶氧对发酵的影响及对发酵产物的影响,进而确定溶氧量的控制及在发酵液中的传递,使生产效益最大化。 关键词:溶氧发酵代谢溶氧量控制传递 Abstrac t: The dissolved oxygen concentration in the fermentation broth (Dissolved Oxygen, referred to as DO) is the key factor to influence the fermentation, has an important influence on microbial growth and product formation. According to the demand of dissolution characteristics and microbial oxygen on oxygen, analysis of the effects of dissolved oxygen on the fermentation and the effect on fermentation, and then determine the control of dissolved oxygen in the fermentation broth and transfer, the maximum production efficiency. Key words: dissolved oxygen; fermentation; metabolism;Dissolved oxygen control transfer 溶氧浓度(DO)作为发酵控制中的一个关键参数,直接影响着发酵生产的稳定性和生产成本,受到工业生产和实验室研究的重视,无论是厌氧还是需氧发酵,研究发酵液中溶氧对发酵的影响都有重要意义。 一·氧的溶解特性 溶解氧(Dissolved Oxygen)是指溶解于水中分子状态的氧,用DO 表示。氧是一种难溶气体,在常压、25℃的条件下,空气中的氧在纯水中的溶解度仅约为0.25mmol/L,在发酵液中,由于各种溶解的营养成分、无机盐和微生物[3] 的代谢产物存在,会明显降低氧的溶解度。此外,溶氧浓度会随着温度、气压、盐分的变化而变化。一般说来,温度越高,溶解的盐分越大,水中的溶解氧越低;气压越高,水中的溶解氧越高。其中就提到一个临界溶氧浓度的确定。 临界溶氧浓度的确定,如右图:[2] 在发酵过程中停止供气,通过观察发酵体系 中DOT的变化可以大致确定细胞生长的临界
城市污水处理系统溶解氧的控制
城市污水处理系统溶解氧的控制 何世钧1,2,王化祥1,杨立功1,2,张 路2 (1.天津大学自动化学院,天津300072;2.河南省自动化工程技术研究中心,河南郑州450008) 摘要: 介绍城市污水处理厂污水处理工艺和控制系统,给出污水处理三级分布式集散控制系统和溶解氧的 P 2FUZZY 2PI 控制方案以及控制算法的实现。 关键词: 污水处理;P 2FUZZY 2PI 控制;集散控制系统 中图分类号:TP273 文献标识码:B 文章编号:100023932(2003)(01)20036203 1 引 言 污水是环境污染的主要污染源。在城市污水中,溶解性有机物质和悬浮固体是两类重要的污染物。奥贝尔工艺作为一种成熟的污水处理工艺,在世界各地的污水处理中得到广泛应用,主要目的是去除污水中的这两类污染物,使出水满足地表水排放标准(工艺流程见图1) 。但其生物和化学过程建立平衡的时间较长,具有大滞后、非线性、随机性、多变量等特点。如果仅采用传统的控 制方式(如常规PI D 控制等),并不能在线整定参 数,随进水水质、水量的变化来控制运行,而使出水水质达不到预期目标。如果采用简单的模糊控制,对复杂的和模型不清楚的系统能进行简单而有效的控制,但由于不具备积分环节,又很难消除稳态误差,在变量分级不够多的情况下,常在平衡点附近出现小的震荡现象。针对这种情况,本文采用具有网络结构的三级分布式集散控制系统、P 2FUZZY 2PI 多模分段控制算法解决实际问题。 图1 奥贝尔污水处理工艺流程 2 城市污水处理控制系统构成 污水处理的基本控制系统由各种物理化学参 数在线监测和控制回路构成。以长葛市污水处理厂为例,总体结构如图2所示。包括两台工控机IPC 、四套美国GE FAUNC 公司90230T M 系列P LC 、 若干Versa Max 系列I/O 模块和德国E +H 公司现场仪表。P LC 按场区进行单元配置,通过G e 2nius LAN 网和所属I/O 模块通信,工控机采用组态王5.1作人机界面,通过E thernet LAN 网以T CP/IP 协议和P LC 进行数据通讯。 控制系统对格栅前后液差、液位,泵房液位、曝气池温度、pH 值、出水流量,氧化沟溶解氧、转碟曝气机状态,二沉池吸泥机状态等参数进行采 集、控制、报警、记录等工作。对重要的控制参数,如氧化沟溶解氧采用P 2FUZZY 2PI 控制。3 污水处理溶解氧P 2FUZZ Y 2PI 控制 在采用奥贝尔工艺的污水处理过程中,对氧化沟的溶解氧浓度的控制是出水水质达标的关键。奥贝尔氧化沟由三个相对独立的同心椭圆形沟道组成,污水由外沟道进入沟内,然后依次进入中间沟道和内沟道,最后经中心岛流出,至二沉池。三个环形沟道相对独立,溶解氧分别控制在 收稿日期:2002205229 基金项目:河南省2001年重点科技攻关项目(河南省2000年重点招标工程(H MECT 22000232022) 过程控制 化工自动化及仪表,2003,30(1):36~38 C ontrol and Instruments in Chemical Industry