提钒尾渣内配碳球团直接还原试验
冶金含铁尘泥复合球团直接还原试验研究

冶金含铁尘泥复合球团直接还原试验研究雷鹏飞【期刊名称】《甘肃冶金》【年(卷),期】2017(009)001【摘要】以酒钢高炉瓦斯灰、转炉OG泥、转炉二次除尘灰和自产铁精矿为主要含铁原料制备复合球团开展直接还原试验.通过利用马弗炉模拟平铺料式隧道窑焙烧过程开展基础性试验研究,考察焙烧温度、焙烧时间、球团配比等条件对金属化球团金属化率、抗压强度的影响,结果表明:金属化球团金属化率和抗压强度指标均随焙烧温度的提高和焙烧时间的延长而升高,综合考虑金属化率和抗压强度指标,球团在焙烧温度1 200 ℃、焙烧时间100 min时是比较适宜的;不同瓦斯灰配入量条件下试验结果表明,球团金属化率随瓦斯灰配入量的增加而升高,抗压强度随瓦斯灰配入量的增加而降低.在此基础上,利用30 m平铺料式隧道窑装置开展了直接还原半工业验证试验,最终取得金属化球团铁品位73.51%、金属化率88.76%、抗压强度平均2 328 N、脱锌率95.10%的试验指标,金属化球团抗压强度等各项指标均满足酒钢高炉或转炉用料要求,说明通过平铺料式隧道窑处理冶金含铁尘泥复合球团在技术上是可行的.【总页数】5页(P18-22)【作者】雷鹏飞【作者单位】酒钢集团宏兴股份公司钢铁研究院,甘肃嘉峪关 735100【正文语种】中文【中图分类】TF046.2;TF042【相关文献】1.含锌含铁尘泥球团自还原试验研究 [J], 于淑娟;吕志升;侯洪宇;王向锋;修国涛2.复合粘结剂球团和氧化球团直接还原对比研究 [J], 李建;朱德庆;邱冠周;李肇毅3.铁碳复合球团直接还原试验研究 [J], 张旭;张建良;郭豪;柏凌4.典型工艺参数对含锌球团直接还原冶金性能的影响 [J], 王玮;赵瑞海;雍海泉;王贤君;伍成波;5.冶金含铁尘泥还原提铁的试验研究 [J], 潘晓因版权原因,仅展示原文概要,查看原文内容请购买。
提钒尾渣常压酸浸提钒
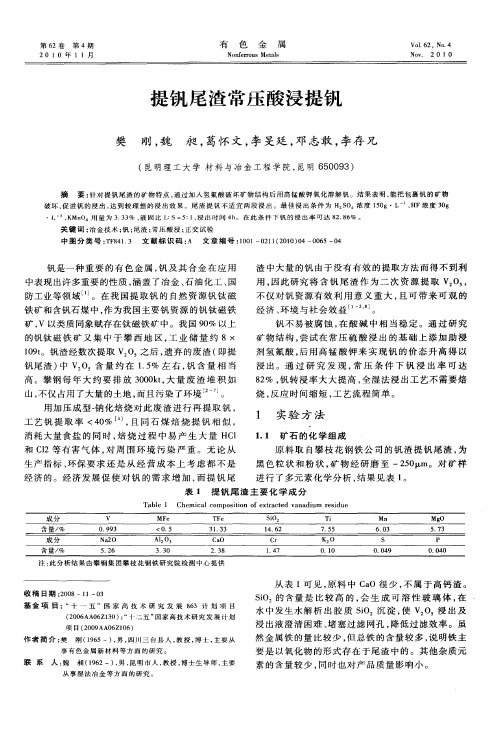
也 说 明 , 常 压条 件 下 H 在 可 进 入 矿 物 晶 格 中 ,
入 H , 一 定 时 问 后 加 人 氧 化 剂 K O 。 恒 温 浸 F在 Mn
出反应 至一定 时间 后迅 速 打 开瓶 塞 , 浆 用真 空 抽 矿 滤过滤 , 固液分 离 , 出渣 洗 涤数 次 , 浸 出渣 进 行 浸 取 钒 浸 出率 计算 。 钒 的浸 出 率 (/ 计 算 公 式 为 :[ 7) 1一m y / ( ) m ]×10 , 中 为 钒 的浸 出率 , 为 浸 出 0% 式 m。 物 料质量 , 为浸 出渣质 量 , 为物 料 中钒 V含 量 , m 为浸 出渣 中 V含 量 。
F . 1 3 3 2 . 6 但大 于 F . 5 3 3 9 2 , 0 0 ( ,)= 9 4 , O O ( , )= . 8 说 明 C因素 ( 氧化 剂 K O Mn 用量 ) 浸 出率 的影 响是 对 高度 显 著 影 响 。F =8 8 . 4小 于 F . 5( , )= 0O 3 3 9 2 , 大 于 F .0( , )=5 3 , 明 D因 素 ( . 8但 01 33 .9 说 液
见 表 3 。 表 2 正 交 试 验 结 果
Ta e 2 Re ut fo t o o a x e i n bl s lso rh g n le p rme t
常压浸 出所需 的仪器设 备包括 D K 4电子恒 Z W-
温 水 浴 锅 、 口圆 底 烧 瓶 、 回 流 冷 凝 管 , 密 增 力 五 双 精
原 料 取 自攀 枝 花 钢铁 公 司 的 钒渣 提 钒 尾渣 , 为
复杂氰化尾渣生产球团矿的工艺试验研究

安环与分析黄 金GOLD2023年第12期/第44卷复杂氰化尾渣生产球团矿的工艺试验研究收稿日期:2023-06-08;修回日期:2023-10-11作者简介:高 亮(1986—),男,高级工程师,硕士,从事贵金属生产管理与资源再生利用研究工作;E mail:gaoliang0403@163.com高 亮,尹福兴,裴增文,高起方(云南黄金矿业集团股份有限公司)摘要:为实现氰化尾渣的无害化和高值化利用,以3种含铁复杂氰化尾渣为原料,按不同配比制备球团矿,并对试验条件进行了优化。
结果表明:在膨润土用量1.2%、造球水分12.0%~12.4%、造球时间10~12min、无需高压辊磨条件下,生球落下强度超过4.0次/(0.5m),抗压强度超过10N/个,爆裂温度超过400℃,满足生产指标要求;在预热温度700℃、预热时间9min、焙烧温度1250℃、焙烧时间6min、均热温度1000℃、均热时间3min条件下,成品球团矿抗压强度≥2793N/个。
所制备的成品球团矿化学成分、冶金性能和物理特性均能满足工业生产要求。
关键词:氰化尾渣;球团矿;综合利用;球团强度;爆裂温度 中图分类号:TD926.4 文章编号:1001-1277(2023)12-0090-07文献标志码:Adoi:10.11792/hj20231219 云南某黄金矿山从含金硫化磁铁矿、褐铁矿和硫酸渣中氰化提取金、银,产出含铁氰化尾渣约120万t/a。
这些氰化尾渣因铁含量低、有害杂质元素含量高、冶金性能差等原因而未能得到有效利用,仅硫化磁铁矿氰化尾渣可低价出售给钢铁企业配矿使用,大量褐铁矿、硫酸渣氰化尾渣只能就地堆存,一方面环境安全风险压力巨大,另一方面造成大量含铁资源浪费。
目前,褐铁矿和硫酸渣氰化尾渣可作为烧结配料使用,但其配加后会导致烧结矿产品质量下降[1-4],难以大量开发利用。
褐铁矿和硫酸渣氰化尾渣烧制球团矿的特点是生球强度低、干燥过程中易爆裂,成品球团矿铁品位低及性能、质量差等[4-5],这两种物料的球团生产应用尚欠缺研究。
某氰化尾渣直接还原焙烧——磁选选铁试验

某氰化尾渣直接还原焙烧——磁选选铁试验
刘娜;孙体昌;刘真真;蒋曼
【期刊名称】《金属矿山》
【年(卷),期】2012(000)011
【摘要】对铁品位高达48.05%的某氰化尾渣进行了直接还原焙烧磁选试验研究.结果表明,在烟煤2用量为20%,还原温度为1 150℃,还原时间为40 min,还原产物磨矿细度为-0.074 mm占78%,1次弱磁选磁场强度为87.56 kA/m情况下获得了铁品位为94.11%、回收率为90.14%的还原铁粉.该工艺不仅高效地富集了铁,而且使硫等含量较高的有害成分富集到了尾矿中.
【总页数】3页(P145-147)
【作者】刘娜;孙体昌;刘真真;蒋曼
【作者单位】北京科技大学土木与环境工程学院;北京科技大学土木与环境工程学院;北京科技大学土木与环境工程学院;北京科技大学土木与环境工程学院
【正文语种】中文
【相关文献】
1.高硫氰化尾渣还原焙烧脱硫-磁选试验 [J], 李正要;曹君磊;邓文翔;王维维;乐坤
2.某氰化尾渣煤基还原焙烧—磁选试验 [J], 孙美芬;张亦飞;王新文
3.某氰化尾渣强磁预选-直接还原焙烧-弱磁选提铁研究 [J], 冯杰;傅平丰;边振忠
4.铜冶炼渣直接还原焙烧—磁选回收铜、铁试验研究 [J], 邱廷省;周丽萍;李国栋
5.硫铁矿炼磺渣选铁还原焙烧磁选还原剂试验研究 [J], 刘金浪;张桂芳;张宗华;张昱
因版权原因,仅展示原文概要,查看原文内容请购买。
铁精矿氧化球团回转窑直接还原试验研究

铁精矿氧化球团回转窑直接还原试验研究
吴振中;贺明;陈得贵
【期刊名称】《甘肃冶金》
【年(卷),期】2024(46)2
【摘要】采用新疆某地生产的铁精矿氧化球团,在Φ2.8 m×48 m回转窑中试装置开展煤基直接还原试验,研究外配碳量、投料量、还原时间、供风结构等因素对铁精矿氧化球团还原效果的影响。
试验结果表明,在投料量4 t/h、外配碳比40%、还原时间266 min、采用窑背风机多点供风模式下,金属化球团的金属化率可以达到87.55%。
【总页数】4页(P64-66)
【作者】吴振中;贺明;陈得贵
【作者单位】甘肃酒钢集团宏兴钢铁股份有限公司
【正文语种】中文
【中图分类】TF548
【相关文献】
1.峨口矿氧化球团直接还原生产工艺的试验研究
2.铁精矿冷固球团和氧化球团直接还原对比研究
3.蒙库球团煤基回转窑直接还原的试验研究
4.含钒钛铁精矿氧化球团气基竖炉直接还原模拟试验
5.氧化球团直接还原铁熔分试验研究
因版权原因,仅展示原文概要,查看原文内容请购买。
我国煤基直接还原炼铁工艺发展
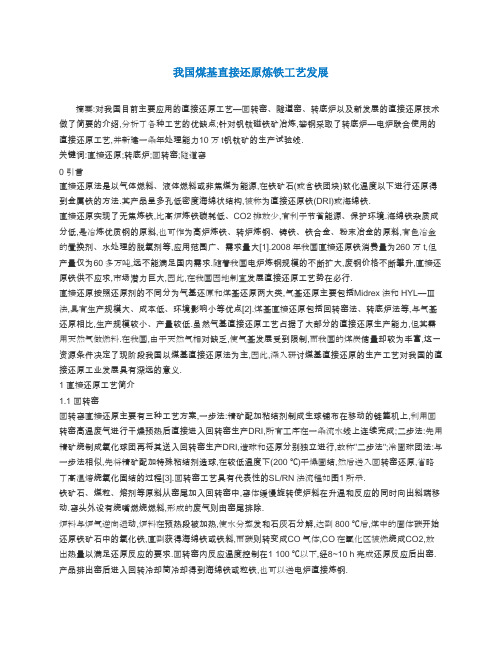
我国煤基直接还原炼铁工艺发展摘要:对我国目前主要应用的直接还原工艺—回转窑、隧道窑、转底炉以及新发展的直接还原技术做了简要的介绍,分析了各种工艺的优缺点;针对钒钛磁铁矿冶炼,攀钢采取了转底炉—电炉联合使用的直接还原工艺,并新建一条年处理能力10万t钒钛矿的生产试验线.关键词:直接还原;转底炉;回转窑;隧道窑0 引言直接还原法是以气体燃料、液体燃料或非焦煤为能源,在铁矿石(或含铁团块)软化温度以下进行还原得到金属铁的方法.其产品呈多孔低密度海绵状结构,被称为直接还原铁(DRI)或海绵铁.直接还原实现了无焦炼铁,比高炉炼铁碳耗低、CO2排放少,有利于节省能源、保护环境.海绵铁杂质成分低,是冶炼优质钢的原料,也可作为高炉炼铁、转炉炼钢、铸铁、铁合金、粉末冶金的原料,有色冶金的置换剂、水处理的脱氧剂等,应用范围广、需求量大[1].2008年我国直接还原铁消费量为260 万t,但产量仅为60多万吨,远不能满足国内需求.随着我国电炉炼钢规模的不断扩大,废钢价格不断攀升,直接还原铁供不应求,市场潜力巨大,因此,在我国因地制宜发展直接还原工艺势在必行.直接还原按照还原剂的不同分为气基还原和煤基还原两大类,气基还原主要包括Midrex法和HYL—Ⅲ法,具有生产规模大、成本低、环境影响小等优点[2].煤基直接还原包括回转窑法、转底炉法等,与气基还原相比,生产规模较小、产量较低.虽然气基直接还原工艺占据了大部分的直接还原生产能力,但其需用天然气做燃料.在我国,由于天然气相对缺乏,使气基发展受到限制,而我国的煤炭储量却较为丰富,这一资源条件决定了现阶段我国以煤基直接还原法为主,因此,深入研讨煤基直接还原的生产工艺对我国的直接还原工业发展具有深远的意义.1 直接还原工艺简介1.1 回转窑回转窑直接还原主要有三种工艺方案,一步法:精矿配加粘结剂制成生球铺布在移动的链篦机上,利用回转窑高温废气进行干燥预热后直接进入回转窑生产DRI,所有工序在一条流水线上连续完成;二步法:先用精矿烧制成氧化球团再将其送入回转窑生产DRI,造球和还原分别独立进行,故称"二步法";冷固球团法:与一步法相似,先将精矿配加特殊粘结剂造球,在较低温度下(200 ℃)干燥固结,然后送入回转窑还原,省略了高温焙烧氧化固结的过程[3].回转窑工艺具有代表性的SL/RN法流程如图1所示.铁矿石、煤粒、熔剂等原料从窑尾加入回转窑中,窑体缓慢旋转使炉料在升温和反应的同时向出料端移动.窑头外设有烧嘴燃烧燃料,形成的废气则由窑尾排除.炉料与炉气逆向运动,炉料在预热段被加热,使水分蒸发和石灰石分解,达到800 ℃后,煤中的固体碳开始还原铁矿石中的氧化铁,直到获得海绵铁或铁料,而碳则转变成CO气体,CO在氧化区被燃烧成CO2,放出热量以满足还原反应的要求.回转窑内反应温度控制在1 100 ℃以下,经8~10 h完成还原反应后出窑.产品排出窑后进入回转冷却筒冷却得到海绵铁或粒铁,也可以送电炉直接炼钢.与高炉工艺相比较,回转窑工艺设备简单,投资少,适用于地方钢铁工业,弥补了高炉—转炉工艺的不足,此外,回转窑还适用于复合矿冶炼,冶金灰尘及各种工业废渣的回收利用,减少环境污染,降低了钢铁生产能耗.同时,回转窑工艺也存在一些缺点,包括窑内结圈、还原温度低(1 100 ℃以下)、流程长、对块矿或球团矿冷强度要求高、要求使用低硫煤等[4].我国山东鲁中矿山公司通过采取提高冷固烧结球团的冷热态强度、加强还原煤的选择和管理、优化回转窑的送风、抛煤、控温温度等措施,预防并降低回转窑结圈,取得了较好的收效.图1 SL/RN法工艺流程1.2 隧道窑隧道窑工艺即将精矿粉、煤粉、石灰石粉,按照一定的比例和装料方法,分别装入还原罐中,然后把罐放在罐车上,推入条形隧道窑中或把罐直接放到环形轮窑中,料罐经预热到1 150 ℃加热焙烧和冷却之后,得到直接还原铁.目前江苏永钢集团拥有两条260 m长煤气隧道窑,为亚洲最长隧道窑.隧道窑生产海绵铁工艺流程如图2所示.图2 隧道窑生产海绵铁工艺流程煤基隧道窑直接还原工艺具有技术成熟、作简单的特点,可因地制宜采用此工艺,利用当地小型分散的铁矿及煤矿资源优势,发展直接还原铁生产,为电炉提供优质原料.但是,总体上讲,我国隧道窑直接还原中存在生产规模较小、能耗高、污染严重、缺乏稳定的原料供应渠道等问题[5],所以,提高机械化程度、改变原料入炉方式、改进燃料及其燃烧、增设余热回收等成为各厂家不断努力改进工艺的方向.我国已建成或正在建设的隧道窑有100多座,约70多个单位规划建设产能5~30 万t/a的隧道窑直接还原铁厂,在不断总结实践经验的基础上,改进现行工艺,开发出诸如大型隧道窑直接还原、AMR—CBI隧道窑直接还原工艺、宽体球状海绵铁隧道窑、L-S快速还原工艺等多种新技术,掀开了隧道窑工艺规模扩大、产能提高、机械及自动化提升的序幕.1.3 转底炉转底炉煤基直接还原是最近几十年间发展起来的炼铁新技术,代表工艺为Fastmet,它由美国Midrex公司与日本神户制钢于20世纪60年发,是采用环形转底炉生产直接还原铁的一种方法.经过多年的半工业性试验和深入的可行性研究,现已完成工艺作参数和装置设计的优化.Fastmelt和ITmk3工艺是在此基础上增加对直接还原铁的处理.图3显示了这三种以转底炉为主体的直接还原工艺流程.图3 转底炉直接还原工艺流程煤粉与铁精粉按比例混匀制成球团,干燥后以1~3层球铺放在转底炉床面,随着炉底的旋转,炉料依次经过预热区、还原区和冷却区.还原区内球团被加热到1 250~1 350 ℃,由于煤粉与铁氧化物紧密接触,铁氧化铁被碳迅速还原成DRI,成品在800~1 000 ℃左右连续从转底炉卸出.球团矿在炉底停留8~30 min,这取决于原料特性、料层厚度及其他因素,成品可作电炉热装炉料或者转炉炉料,也可冷却或生产热压块(HBI).Fastmet工艺技术特点:①在高温敞焰下加热实现快速还原,反应时间只需10~20 min,生产效率高;②原料来源广泛,铁原料方面,除使用高品位粉矿、精矿外,还可用氧化铁皮、代油铁泥、炼钢粉尘、含En、Pb、As等有害杂质的铁矿等;还原剂方面,除煤以外焦末、沥青均可利用,不必担心出现结圈问题;③炉料相对炉底静止,对炉料强度要求不高;④废气中含有大量显热,可用作预热空气、干燥原料等[6]. Fastmelt工艺流程基本与Fastmet一致,只是在后续添加一个熔炉来生产高质量的液态铁水.Itmk3工艺是使金属化球团在转底炉中还原时熔化,生成铁块(Nuggets),同时脉石也熔化,形成渣铁分离.当然转底炉也存在着设备复杂、炉内气氛难控制、传热效率低以及对还原剂硫含量要求严格的缺点.就目前转底炉工艺开发的水平和规模而论,与高炉还有较大差距,但仍存在发展的广阔空间,天津荣程联合钢铁集团已兴建一条100万t级Fastmet生产线,建成目前世界最大的转底炉.另外,用转底炉可处理一些特殊铁矿,如含锌、铅、砷等有害杂质,或含镍、钒、钛等有用元素,均可利用转底炉的工艺优势,或高温挥发,或选择性还原,配合后续工艺,实现资源综合利用.马钢尘泥脱锌转底炉工程项目于2008年5月开工建设,2009年7月6日正式竣工投产,建成了整套转底炉(RHF)脱锌工艺技术装置,不仅解决了含锌尘泥循环利用的后顾之忧,而且将综合利用技术上升到高品质资源化水平.1.4 其他新工艺1.4.1 PF法煤基竖炉直接还原工艺中冶集团北京冶金设备研究设计总院,结合国内情况创新发明了PF法竖炉直接还原工艺.PF法是在吸收K-M法外热式竖炉煤基直接还原工艺的经验基础上,设计的以一种中国特色的罐式还原炉为主反应器的直接还原法.这种工艺技术可靠,技术经济指标在各种煤基直接还原工艺中属先进水平.PF法直接还原工艺流程如图4所示.图4 PF法直接还原工艺流程PF法直接还原工艺主要特点[1]:1)主体设备选用外热式竖炉,预热、还原、冷却三段根据不同的作用和温度选用不同材质和结构,便于传热和化学反应进行,提高热效率和设备寿命.2)原燃料适用性强,对精矿、还原剂和燃料没有特殊要求.3)采用外配碳工艺,还原剂适当过量,扩大了煤的选用范围,造球工艺也因不定量配入煤粉而简化,球团强度较高,DRI质量较好.4)多个反应罐可并列组成任意规模的还原设备,设计和组织生产灵活.1.4.2 低温快速还原新工艺2004年钢铁研究总院提出了低温快速冶金新工艺.新工艺利用纳米晶冶金技术的特点将铁矿的还原温度降低到700 ℃以下.新流程分为气基和煤基两种方法,工艺流程如图5、图6所示.图5 煤基低温快速还原新工艺图6 气基低温快速还原新工艺煤基法使用煤粉为还原剂,在700℃左右快速还原铁精矿粉;气基法使用还原性气体还原铁精矿粉,还原温度可低于600℃.新工艺具有能耗低、环境友好等特点,省去了烧结或造球工艺,缓解了钢铁行业对焦煤的依赖,符合我国国情[7].2 攀钢现状钒钛磁铁矿是攀西地区的特色资源,与普通矿相比,钒钛矿直接还原温度较高、还原时间较长,还原过程产生特有的膨胀粉化现象,因此,存在竖炉结瘤、流化床失流和黏结、回转窑结圈等技术难题.高炉流程冶炼钒钛矿,只回收了铁和钒,钛进入高炉渣没有回收,造成钛资源的大量流失.2005年以来,攀钢科研人员在充分吸收、借鉴新流程及相关研究成果的基础上,通过大量的试验研究,针对钒钛磁铁矿特点,提出并验证了钒钛磁铁矿"转底炉直接还原—电炉深还原—含钒铁水提钒—含钛炉渣提钛"工艺路线,彻底打通了钒钛矿资源综合利用新工艺流程,稳定获得了质量满足要求的低碳生铁、达到GB3283-87要求的片状V2O5和PTA121质量要求的钛白产品.依托该研究成果,攀钢集团攀枝花钢铁研究院于2008年5月4日正式启动了攀钢10 万t/a钒钛矿资源综合利用新工艺中试线工程项目,新建一条转底炉—熔分电炉联合使用,年处理能力10万t钒钛矿的试验生产线,为更深入地研究实践,实现转底炉处理钒钛矿的规模化生产提供了广阔的平台.中试线工艺流程如图7所示.本流程采用硫含量较低的白马铁精矿,还原剂采用无烟煤煤粉,粘结剂为有机粘结剂,原料混合后经高压压球机压球,生球烘干后进入转底炉系统.球团在转底炉内停留10~30 min后出料,金属化球团直接热装进入熔分电炉,在一定温度下还原后,产出含钒铁水及含钛炉渣.继续对铁水进行脱硫、提钒后,得到半钢、脱硫渣及钒渣,半钢进入铸铁机铸铁,生产出铸铁块.钛渣制取钛白,实验室条件下钛回收率达到80%以上;钒渣制取钒氧化物(V2O5),实验室条件下,钒回收率达到65%以上.与高炉流程相比,转底炉流程采用100%钒钛矿冶炼,克服了高炉流程必须配加普通矿的不足,在当前铁资源紧张的形势下,有助于充分发挥攀西地区资源优势,拉动区域经济发展.此外,转底炉流程的铁精矿不需烧结处理,不使用焦炭,从根本上避免了烧结烟气脱硫、焦煤资源采购困难以及环保压力大等问题.3 结语图7 资源综合利用中试线工艺流程煤炭资源总量丰富、焦煤短缺,铁矿资源储量大、富矿少、贫矿和共生矿多是中国钢铁工业面临的现实状况.这种能源、资源结构给煤基直接还原法生产海绵铁的发展提供了机遇.转底炉直接还原技术由于在生产率、规模化、投资费用、单位成本等方面都占有明显的优势,可作为发展直接还原技术的首选工艺.鉴于转底炉处理钒钛磁铁矿技术尚属世界首创,并无较多的经验借鉴,因此要大力开展针对钒钛磁铁矿直接还原的基础研究工作,在实践中借鉴各种直接还原方法已取得的成果,开拓创新,开创钒钛矿直接还原新纪元.参考文献[1] 陈守明,黄超,张金良.煤基竖炉直接还原工艺//2008年非高炉炼铁年会文集.中国金属学会,2008:132-135.[2] 杨婷,孙继青.世界直接还原铁发展现状及分析.世界金属导报,2006.[3] 刘国根,邱冠周,王淀佐.直接还原炼铁中的粘结剂.矿产综合利用,2001(4):27-30.[4] 韩跃新,高鹏,李艳军.白云鄂博氧化矿直接还原综合利用前景.金属矿山,2009 (5):1-6.[5] 魏国,赵庆杰,沈峰满,等.非高炉生产技术进步//2004年全国炼铁生产技术暨炼铁年会文集.2004:878-882.[6] 陶晋. 环形转底炉直接还原工艺现状及发展趋势. 冶金信息工作, 1997.6.[7] 郭培民,赵沛,张殿伟.低温快速还原炼铁新技术特点及理论研究.炼铁,2007,26(1): 57-60.来源:攀枝花钢铁研究院网站。
提钒尾渣的综合利用研究

% 此方
,
目
前 我 国 钢 铁行 业 年 产 含 钒 尾 渣 约
。
万
法 使 得尾 渣 中 的 钒 得 到 高 效 的 浸 取 但 是 生 产 中 使
用 大量 的 硫 酸 和 氢 氟 酸 腐 蚀 性 较 大 对 设 备 要 求
,
吨 并 呈逐 年 上 升趋 势
、 、
含钒 尾 渣 中 含 有 的 有 价 值
,
过 氧化 钠 化 焙 烧 浸 出 后 的 废 弃 物 虽 然 经 过 提 钒
、
,
在 要 浸 出 这 部 分 钒 必 须 破 坏 尖 晶 石 结构 使 尖 晶
石 结 构 中 的 钒 得 以 释 放 再进 行 氧 化 和转 化 邓 志
,
工艺
,
提 钒 尾 渣 中 的 钒含 量仍 可 高 达 % 质 量 分
,
尾 渣 的 彻 底 解 决 渣 将减 少 含 钒尾 渣 库 的 建 设 减 少 环 境 污 染 实 现
。
,
尾渣 中 钒 铁 的 有 效 利 用
、
。
3
提钒 尾 渣浸取 提钒
-
44
-
北 方 钒 钛 2 0
5
1
6
年第
4
期
制 作 建 筑 黑 瓷 出 矿 渣 微 晶 玻 璃 另 有研 究 可 利 用 含 钒 尾 渣 制 备 保
提 钒 尾 渣 的 综 合利 用 研 究
解本 学
(
高
静
)
钒钛事业 部
摘
要 本 文 针 对 提 钒尾 渣 介 绍
:
了 几 种 处 理 提 钒 尾渣 的 方 法
- 1、下载文档前请自行甄别文档内容的完整性,平台不提供额外的编辑、内容补充、找答案等附加服务。
- 2、"仅部分预览"的文档,不可在线预览部分如存在完整性等问题,可反馈申请退款(可完整预览的文档不适用该条件!)。
- 3、如文档侵犯您的权益,请联系客服反馈,我们会尽快为您处理(人工客服工作时间:9:00-18:30)。
2011年i1期 有色金属(冶炼部分)(http://ysy1.bgrimm.on) ・ 17 ・ DOI:10.3969I/j.issn.1007—7545.201 1.1 1.005
提钒尾渣内配碳球团直接还原试验
吴恩辉,黄平,杨绍利,马兰,张树立 (攀枝花学院四川省钒钛材料工程技术研究中心,四川攀枝花617000) 摘要:在实验室条件下,对提钒尾渣压力成型工艺进行研究,考察煤粉配比、粘结剂配比、生石灰配比及 成型压力等因素对提钒尾渣内配碳球团强度的影响,确定了最佳方案。结果表明,球团的强度可满足后 续处理工艺的要求。并研究了配碳量、碱度、还原温度及还原时间与该种球团直接还原金属化率的关 系。 关键词:提钒尾渣;压力成型;直接还原;内配碳球团 中图分类号:TF841.3 文献标识码:A 文章编号:1007—7545(2011)11 0017-04
Experimental Study on Direct Reduction of Vanadium Tailings Carbon。Containing Pellets
WU En—hui,HUANG Ping,YANG Shao—li,MA Lan,ZHANG Shu—li (Panzhihua College,Sichuan Province Engineering Research Center for Vanadium&Titanium Materials Panzhihua 61 7000,Sichuan。China)
Abstract:Under laboratory conditions,pressure forming process for vanadium tailings was investigated. The effecting factors,such as coal ratio,binder ratio,quicklime ratio and molding pressure,on pellets strength were studied and the optimum process parameters were determined.The results show that the strength of pellets can meet the requirement of follow—up processing.The relations between coal ratio,al— kalinity,reduction temperature and time and the metallization percentage in the process of metalized pellet were also studied with experiments. Key words:Vandium railings;Pressure forming;Direct reduction;Carbon—containing pellets
提钒尾渣是钒渣经过氧化钠化焙烧、酸浸等工 序将钒氧化物提取出来后产生的固体废弃物,全国 钒企业每年大约排放提钒尾渣约3O万t[1],而且随 着钒企业产能的不断过大,提钒尾渣的排放量也将 逐渐提高,如此多的废渣常年堆积,不但占用了大量 土地,而且会造成环境污染。 提钒尾渣中铁含量相对较高,还富集有钒、铬、 镓等稀贵金属,是非常宝贵的二次资源,然而由于其 碱金属含量高,矿相及成分复杂,目前其综合利用程 度并不高lz]。对其开发应用主要集中在以下几个方 面:一是将提钒尾渣进行二次提钒,目前研究主要集 中在常压或加压酸浸提钒工艺l3 ;二是提钒尾渣 作者简介:吴恩辉(1984),男,安徽泗县人,助教,硕士 经过热处理和改性可以作为远红外涂料的填料,替 代钴系列黑色颜料 ;三是利用提钒尾渣具有较高 的光热吸收率、红外辐射率和较高的光热转换效率 等特性,将提钒尾渣煅烧制黑色陶瓷材料 ],成为优 良的光热转换材料和成瓷材料;四是将提钒尾渣经 过煤基直接还原一磁选工艺回收其中的金属铁[7]。 本文主要研究提钒尾渣内配碳球团压力成型工艺, 得出了合理的工艺参数,生产的内配碳球团可以满 足后续冶炼工艺对其强度的要求;在此基础上,初步 探索了该球团直接还原的相关规律,为后续提钒尾 渣金属化球团电弧炉冶炼提供依据和参考。 ・ 18 ・ 有色金属(冶炼部分)(http://ysy1.bgrimm.on) 2011年11期 1 试验原料及流程 2 试验方法 1.1试验原料 化学成分( ):TFe 37.97、Ga 0.008、TiO2 12.90、V2O5 2.08、MnO 7.84、SiO2 16.32、Al2O3 3.72、CaO 2.5、MgO 3.57、Cr2O3 2.24,原料粒度 ( ):+0.35 mm 7.8、~0.35~+0.25 mill 6.0、~ 0.25~+0.152 mm 20.6、一0.152~+0.104 miTl 25.2、一0.104~+0.074 him 1.6、一0.074 mm 39。4。可以看出提钒尾渣有以下几个特点: 1)原料中Fe含量达到37.97 ,V O 和 Cr。O。含量分别达到2.08 和2.24 ,具有较高的 综合利用价值。 2)原料粒度组成大于0.25 lnm的占86.2 , 适合内配碳球团压力成型工艺。 3)具有利用价值的金属种类多,比如金属镓、 钒、铬、钛等_8]。 1.2试验流程 煤粉、提钒尾渣和生石灰一起混合成型后,制成 球团,在竖炉内进行直接还原,得到金属化球团。 采用L (3。)正交试验方法,考察煤粉配比、粘 结剂配比、CaO配比和成型压力对球团强度的影 响。人工配料,加入一定量粘结剂混匀之后在粉末 压片机上压制成球。生球未经干燥在0.5 m高落 至钢板上,测定其落下强度;生球自然干燥后在智能 压力测定机上测定其抗压强度。 直接还原试验利用上述压力成型工艺制成的内 配碳球团作为原料,每次试验用钢丝网兜装人一个 球团,球团先在竖炉上端低温区预热一分钟,然后放 入炉底高温区进行还原,还原时通入CO作为保护 气。球团在一个温度点还原预先设定的时问后,迅 速取出放入木炭中自然冷却,冷却完成后,取样分 析。
3试验结果及讨论 3.1压力成型试验 压力成型正交试验结果如表1所示。
表1造球正交试验试验结果 Table 1 The orthogonal test results of pelletizing 序号 因素 考查指标 煤粉配比/ 粘结剂配比/ 生石灰配比/ 成型压力/MPa 抗压强度(N/球) 落下强度/次
采用极差法处理表1中的数据,处理结果列入 表2~3。其中,尼 表示第 因素,第 水平的平均 值,R,表示极差。
表2球团抗压强度的极差分析 Table 2 Extreme difference analysis of pressured strength of pellet 项目煤 比粘 比生 比
1,, 25.47 37.27 36.17 30.67 2., 35.53 34.50 31.83 33.47 3. 42.17 31.17 35.17 39.O3 R, 16.70 6.10 4.34 8.36
表3对球团落下强度的极差分析 Table 3 Extreme difference analysis of drop strength of pellet 项目煤 比粘 比生 比
1., 7.33 1.33 6.00 3.67 2, 6.00 4.33 5.00 7.67 3,J 3.00 10.67 5.33 5.00 R.4.33 9.34 1.00 4.00
由表1~3可知,采取压力成型工艺,提钒尾渣 内配碳球团的抗压强度可达48.7 N/球,落下强度 可达14次,提钒尾渣具有良好的成球性,不需要对 201i年II期 有色金属(冶炼部分)(http://ysy1.bgrimm.cn) ・ 19 ・ 原料做特殊处理,就可以得到各方面性能优异的内 配碳球团。在影响球团抗压强度的各因素中,主次 关系为:煤粉配比>粘结剂配比>Cao配比>成型 压力;影响球团落下强度的各因素中,主次关系为: 粘结剂配比>煤粉配比>成型压力>CaO配比。 试验确定的最佳方案是:提钒尾渣:煤粉:氧化钙 。粘结剂一1O0:25:15:2。 3.2直接还原试验 3.2.1 还原温度对球团金属化率的影响 试验在理论配碳量、碱度1.2、还原时间25 min、C0气氛下进行,还原温度对球团金属化率的 影响结果见图1。在1 150℃时,球团的金属化率为 41.39 ,就趋势而言,随着温度的升高,球团的金属 化率不断增加。由于球团在接近1 200℃时就开始 熔化,无法从竖炉取出,因此无法检测其结果,但是 就现象来看,球团的金属化率一定很高,因为可以明 显发现其中有铁颗粒的存在。
\ 褥
噻
还原温度/℃ 图1 还原温度对球团金属化率的影响 Fig.1 Effect of reduction temperature on metallization rate of pellet
3.2.2 配碳量对球团金属化率的影响 试验在还原温度1 090℃、碱度1.2、还原时间 25 min、c0气氛下进行,配碳量对球团金属化率的 影响结果见图2。配碳量为14.4 时,球团的金属 化率为35.35 。图中数据显示,随着配碳量的增 加,球团的金属化率有震荡升高的趋势。出现金属 化率减小的主要原因是在取出球团时,由于未及时 将球团埋在木炭深处,导致了炙热球团与空气接触, 发生氧化导致。另外分析结果显示有剩炭的出现, 说明提钒尾渣中铁的还原并不充分,这也是金属化 率较低的原因之一。 3.2.3还原时间对球团金属化率的影响 还原温度1 090℃,配碳为理论配碳量、碱度 1.2、CO气氛,还原时间对球团金属化率的影响结
\ 碍
噬
目 碳比/% 图2配碳量对球团金属化率的影响 Fig.2 Effect of carbon addition on metailization rate of pellet
果见图3。当还原时间为30 min时,球团的金属化 率为33.O9 ,由图3可以看出,球团的金属化率随 着还原时间的增长,其金属化率表现为震荡升高。 出现震荡的主要原因应为试验操作过程中球团氧化 造成的,因为通过分析球团中残碳量可知,随着时间 的增加残碳是不断减少的,说明球团中的铁是不断 被还原的。
\ 得
L崛
还原时间/min 图3还原时间对球团金属化率的影响 Fig.3 Effect of reduction time on metallization rate of pellet