浅析重油催化裂化装置沉降器结焦原因及对策
催化裂化油浆系统结焦原因及对策
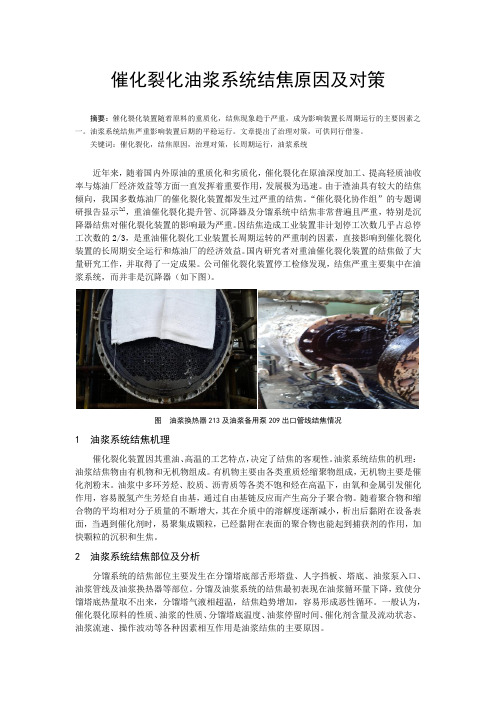
催化裂化油浆系统结焦原因及对策摘要:催化裂化装置随着原料的重质化,结焦现象趋于严重,成为影响装置长周期运行的主要因素之一。
油浆系统结焦严重影响装置后期的平稳运行。
文章提出了治理对策,可供同行借鉴。
关键词:催化裂化,结焦原因,治理对策,长周期运行,油浆系统近年来,随着国内外原油的重质化和劣质化,催化裂化在原油深度加工、提高轻质油收率与炼油厂经济效益等方面一直发挥着重要作用,发展极为迅速。
由于渣油具有较大的结焦倾向,我国多数炼油厂的催化裂化装置都发生过严重的结焦。
“催化裂化协作组”的专题调研报告显示[1],重油催化裂化提升管、沉降器及分馏系统中结焦非常普遍且严重,特别是沉降器结焦对催化裂化装置的影响最为严重。
因结焦造成工业装置非计划停工次数几乎占总停工次数的2/3,是重油催化裂化工业装置长周期运转的严重制约因素,直接影响到催化裂化装置的长周期安全运行和炼油厂的经济效益。
国内研究者对重油催化裂化装置的结焦做了大量研究工作,并取得了一定成果。
公司催化裂化装置停工检修发现,结焦严重主要集中在油浆系统,而并非是沉降器(如下图)。
图油浆换热器213及油浆备用泵209出口管线结焦情况1 油浆系统结焦机理催化裂化装置因其重油、高温的工艺特点,决定了结焦的客观性。
油浆系统结焦的机理:油浆结焦物由有机物和无机物组成。
有机物主要由各类重质烃缩聚物组成,无机物主要是催化剂粉末。
油浆中多环芳烃、胶质、沥青质等各类不饱和烃在高温下,由氧和金属引发催化作用,容易脱氢产生芳烃自由基,通过自由基链反应而产生高分子聚合物。
随着聚合物和缩合物的平均相对分子质量的不断增大,其在介质中的溶解度逐渐减小,析出后黏附在设备表面,当遇到催化剂时,易聚集成颗粒,已经黏附在表面的聚合物也能起到捕获剂的作用,加快颗粒的沉积和生焦。
2 油浆系统结焦部位及分析分馏系统的结焦部位主要发生在分馏塔底部舌形塔盘、人字挡板、塔底、油浆泵入口、油浆管线及油浆换热器等部位。
催化裂化装置结焦原因分析及对策研究

催化裂化装置结焦原因分析及对策研究
催化裂化装置结焦是指在催化裂化过程中,由于反应过程中产生的碳积累在催化剂表面,导致催化剂活性降低,反应效率下降,甚至催化剂失活的现象。
结焦问题严重影响了
催化裂化装置的生产效率和经济效益。
本文将分析催化裂化装置结焦的原因,并提出相应
的对策。
催化裂化装置结焦的原因主要包括以下几个方面:
1. 高温:催化裂化反应需要在较高温度条件下进行,高温会加速碳积聚的过程,导
致催化剂结焦。
2. 高碳含量的原料:催化裂化装置处理高碳含量的原料,会使得产生的碳积聚更多,导致催化剂结焦。
3. 高流速:高流速会引起催化剂表面的碳积聚过程加剧,进而促使催化剂的结焦。
4. 催化剂质量:催化剂材料的选择和质量会影响结焦问题,较差质量的催化剂容易
结焦。
5. 动力不足:催化裂化反应需要消耗大量的热力,如果动力系统供应不足,反应温
度无法保持在适宜的范围内,会导致结焦现象。
针对以上的原因,我们可以采取如下对策来应对催化裂化装置结焦问题:
1. 优化温度控制:通过合理控制反应温度,使其在适宜的范围内,既不过高也不过低,可以减少碳积聚的速度,降低催化剂结焦的风险。
3. 调整流速:合理调整反应器的流速,减缓碳积聚的速度,降低催化剂结焦的风
险。
4. 优化催化剂质量:选择高质量的催化剂材料,并严格控制催化剂制备的过程,以
提高催化剂的抗结焦能力。
催化裂化装置结焦问题是一个复杂的工艺问题,需要从温度控制、原料选择、流速调整、催化剂质量和动力供应等多个方面综合考虑,通过优化工艺参数和采取相应的对策,
才能有效降低结焦的风险,提高催化裂化装置的生产效率和经济效益。
催化裂化油浆结焦原因及对策

催化裂化油浆结焦原因及对策标签:催化裂化;油浆结焦;解决对策在我国炼油厂的催化裂化过程当中,油浆系统当中产生的结焦结垢问题直接影响到了催化裂化设备的正常工作,主要是因为产生大量的结焦结垢物质,直接降低了热换器的热转化效率,同时提高了管道当中材料输送的阻力,进而造成了蜡油渣油的热转换效率降低。
系统内部产生的蒸汽量减少,同时整个反应设备在工作过程当中的能源消耗量加大,油浆当中多余的热量无法及时被排除,进而造成了整个反应系统内部的热平衡性下降,严重的情况下还直接造成油浆输送系统堵塞,进而影响到了整个生产过程的正常进行。
在最近几年发展过程当中,我国炼油厂的催化裂化原材料质量都不是非常理想,外加上在加油的催化裂化技术方面一直是难以攻克的难题。
因此,催化裂化油浆结焦和结垢的问题受到了各大化工企业的广泛关注,必须要采取相应的解决措施来解决这一问题。
1.催化裂化油浆结焦问题分析1.1温度问题的影响从催化裂化的整个反应过程中可以看出,该反应过程中会受到温度的影响,在相同的催化设备当中分馏塔的底部温度越高,那么出现的结焦现象就越明显。
针对己经产生结焦问题来讲,随着温度不断提高整个反应过程的结焦问题就更加明显,就在模拟FCC油浆的结焦单元当中所得出的结论非常明显。
1.2氧含量的影响通过模拟实验分析了FCC油浆当中产生结焦单元的具体原因,通过向试管当中通入一定量的空气或者是氧气,可以看出在不同量的空气和氧气掺入的情况下,对结焦问题的影响比较明显,其中如果空气或者氧气的参与量较大,那么结焦的问题就越严重。
由此可以看出氧气含量的多少对结焦问题的影响非常明显。
1.3固体和电效应影响通过实际的生产过程可以看出,在催化裂化反应过程当中,如果增加油浆内部的沉降器和过滤器设备之后,在产生结焦和结垢的问题上有着明显的缓解。
因此,这一现象也可以得到充分的证明,从中可以得出催化裂化反应过程中油浆当中,所存在的固体杂质对结焦问题的影响比较明显。
催化裂化装置结焦分析和防结焦措施

编号:AQ-Lw-01298( 安全论文)单位:_____________________审批:_____________________日期:_____________________WORD文档/ A4打印/ 可编辑催化裂化装置结焦分析和防结焦措施Coking analysis and anti coking measures of FCC unit催化裂化装置结焦分析和防结焦措施备注:加强安全教育培训,是确保企业生产安全的重要举措,也是培育安全生产文化之路。
安全事故的发生,除了员工安全意识淡薄是其根源外,还有一个重要的原因是员工的自觉安全行为规范缺失、自我防范能力不强。
摘要:随着原油价格上涨,原油重质化和劣质化是各炼油企业实现效益最大化的有效方法,由此带来了催化裂化装置结焦问题,目前重油催化裂化装置不可避免的存在结焦问题。
催化裂化结焦主要是由于原料性质变重后,原料喷嘴的雾化效果差,原料油在催化剂上不能完全汽化而产生湿催化剂,这些湿催化剂粘附结焦是引起提升管及沉降器内结焦的主要原因,而油气中重组分油气遇冷凝结,粘附在器壁上,长时间高温条件下发生缩合反应生成焦块,则是油气大管结焦的主要原因。
关键词:催化裂化;结焦;分析1前言催化裂化装置是炼油企业的核心装置,也是影响炼油企业效益的重要装置,如何减少催化裂化装置结焦延长装置运行周期,已成为各炼油企业实现效益最大化的重要手段。
湛江东兴1 #催化裂化装置经过数次改造,由蜡油催化裂化改为重油催化裂化,2005年由洛阳设计院对催化装置进行扩能改造后,处理量提高至50万吨/年,设计减渣掺炼比例40%。
随着装置掺渣量的提高,结焦已成为影响装置长周期运行的重要因素,特别是沉降器的结焦长期威胁着装置的安全平稳运行。
1#催化裂化装置于05年3月16日一次性喷油成功后,由于掺渣量大,装置结焦较为严重,见表一。
2007年3月14日按计划进行检修,停工打开沉降器清焦时发现,装置结焦严重,清出的焦炭共约50吨,见图一。
催化裂化装置沉降器防结焦技术探讨

催化裂化装置沉降器防结焦技术探讨摘要:沉降器结焦问题给催化裂化装置长周期运行造成较大困扰,不同装置特点和原料性质不同,结焦原因也不相同,所以需要结合装置自身结焦特点“量体裁衣”,制定出具有针对性的防止沉降器结焦的措施。
下面本文就对此展开探讨。
关键词:催化裂化装置;沉降器;防结焦技术;1影响催化裂化装置长周期运行的因素导致催化裂化装置非计划停工的因素一般有再生器一、二级旋风分离器翼阀阀板严重磨损甚至脱落,催化剂严重跑损;再生器烧焦罐密相床层烧焦流化风喷嘴严重磨损,催化剂流化异常,操作难以维持;沉降器严重结焦,焦块脱落堵塞料腿或卡住翼阀,沉降器严重跑剂;各斜管滑阀阀板和导轨严重磨损造成滑阀动作迟缓,严重的还会造成阀板脱落,影响两器压力平衡;分馏塔底油浆系统严重结焦,后路堵塞;富气压缩机组严重故障,装置无法运行等。
其余设备设施出现故障,尽管也会影响装置的运行,但是通过在线处理,一般不会导致装置非计划停工。
2装置累计运行5a后关键部件检查情况沉降器结焦与油气停留时间长短也有一定关系,常规结构的沉降器中,油气在沉降器停留时间一般约为30s,但器壁附近的油气流动速度慢,有时高达数分钟,导致该处容易结焦。
2.1再生器烧焦罐主风分布管喷嘴磨损烧焦罐主风分布管为复合陶瓷喷嘴,其内圆部分内衬陶瓷管,边缘整齐,几乎没有磨损,外面包覆金属骨架,因底部金属暴露在催化剂环境中,磨损严重。
2.2沉降器检查主要问题(1)高效旋风分离器6个翼阀阀板与阀座接触面磨损严重,翼阀阀板吊环磨损严重。
(2)粗旋顶部、高效旋风分离器升气筒和喇叭口槽内结焦较多,见图1。
a b图1沉降器旋风分离器结焦情况2.3各斜管滑阀阀板和导轨磨损情况再生滑阀轨道侧面和远端磨损较重,轨道主体支撑面大部分磨损较轻。
其余滑阀导轨也有不同程度的磨损,从磨损情况看,能够满足“五年一修”的要求。
2.4外取热器管束磨损情况2台外取热器管束,整体状况比较好,磨损较轻。
但是在距离管束底部向上约1.5m处,发现2~3根换热管局部磨损严重。
催化裂化装置结焦原因分析及对策研究
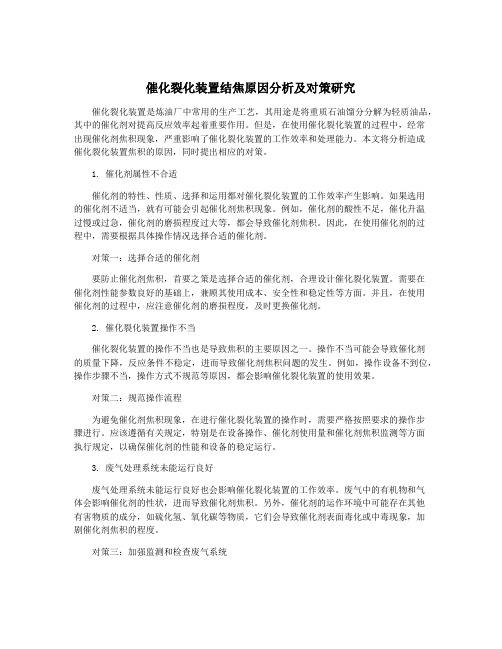
催化裂化装置结焦原因分析及对策研究催化裂化装置是炼油厂中常用的生产工艺,其用途是将重质石油馏分分解为轻质油品,其中的催化剂对提高反应效率起着重要作用。
但是,在使用催化裂化装置的过程中,经常出现催化剂焦积现象,严重影响了催化裂化装置的工作效率和处理能力。
本文将分析造成催化裂化装置焦积的原因,同时提出相应的对策。
1. 催化剂属性不合适催化剂的特性、性质、选择和运用都对催化裂化装置的工作效率产生影响。
如果选用的催化剂不适当,就有可能会引起催化剂焦积现象。
例如,催化剂的酸性不足,催化升温过慢或过急,催化剂的磨损程度过大等,都会导致催化剂焦积。
因此,在使用催化剂的过程中,需要根据具体操作情况选择合适的催化剂。
对策一:选择合适的催化剂要防止催化剂焦积,首要之策是选择合适的催化剂,合理设计催化裂化装置。
需要在催化剂性能参数良好的基础上,兼顾其使用成本、安全性和稳定性等方面。
并且,在使用催化剂的过程中,应注意催化剂的磨损程度,及时更换催化剂。
2. 催化裂化装置操作不当催化裂化装置的操作不当也是导致焦积的主要原因之一。
操作不当可能会导致催化剂的质量下降,反应条件不稳定,进而导致催化剂焦积问题的发生。
例如,操作设备不到位,操作步骤不当,操作方式不规范等原因,都会影响催化裂化装置的使用效果。
对策二:规范操作流程为避免催化剂焦积现象,在进行催化裂化装置的操作时,需要严格按照要求的操作步骤进行。
应该遵循有关规定,特别是在设备操作、催化剂使用量和催化剂焦积监测等方面执行规定,以确保催化剂的性能和设备的稳定运行。
3. 废气处理系统未能运行良好废气处理系统未能运行良好也会影响催化裂化装置的工作效率。
废气中的有机物和气体会影响催化剂的性状,进而导致催化剂焦积。
另外,催化剂的运作环境中可能存在其他有害物质的成分,如硫化氢、氧化碳等物质,它们会导致催化剂表面毒化或中毒现象,加剧催化剂焦积的程度。
对策三:加强监测和检查废气系统为避免催化剂焦积现象的发生,需要严格监测和检查废气系统,确保其正常运行。
重油催化裂化装置沉降器结焦原因分析及对策

l 装置历次结焦 及改造情 况
3 催 化 装 置从 19 9 6年 1 0月 6 日投 产 至今 , 降 沉
器 内稀相 器壁 及旋 分 器外 壁 结 焦 严 重 , 旦 操 作 波 动 一 或 三器 流化 中断 , 落 焦块 将 堵塞催 化 剂 流化 通道 , 脱 因
此 造 成 了装置 五 次非 计 划停 工 。沉 降 器结 焦部 位 主要
表 l 装 置 结 焦 量 及 结焦 速 度 大 致 统 计
再 生工 艺 , 降器 与 第 一再 生 器 ( 再 ) 沉 一 同轴 而第 二再
生器( 再) 二 与之 并列 的 布 置形 式 ; 再 采 用 贫 氧 常 规 一
再 生 而二再 采用 富氧完 全再 生 , 一再 采用 湍 流床再 生 、 二再 采用 快速 床 ( 密 ) 一 +湍 流 床 ( 二密 ) 主风 串联 两 段
大修 时对再 生 斜管 的改 造 反 而 带 来 了负 面 影 响 , 要 主 问题是 再 生斜 管催 化 剂 输送 不 畅导 致 反应 温度 波 动 大 并被 迫频 繁地 大 幅 度 调 整 处 理 量 , 反应 温度 波 动 大 而
提 段 入 口格栅 上 , 塞 了催 化 剂 的 流化 通道 。 堵
19 96年 Βιβλιοθήκη 0月 6日建 成 投 产 。装 置 反 再 系 统 采用 两 段
更 加 剧 了沉 降器 结焦 , 此 沉 降 器 结 焦 问题 仍 然 困 扰 因 着 装 置 的长周 期 生 产 。到 目前 为止 , 降 器 共 清 焦八 沉 次, 每次 的 清焦 量及 结 焦速度 大 致统 计 见表 1 。
2 0m 0 m厚 的 焦 , 分 焦 块 已脱 落 并 堆积 在 沉降 器 汽 部
重油催化裂化装置油浆系统结焦的原因及措施

浅谈重油催化裂化装置油浆系统结焦的原因及措施【摘要】分析了玉门油田炼油化工总厂催化裂化装置现有加工模式下,引起油浆系统结焦的主要原因,并提出相应的解决措施,确保了装置的长周期运行。
【关键词】油浆结焦原因措施玉门炼化总厂80万吨/年催化裂化装置是2004年9月在原50万吨/年蜡油催化裂化装置的基础上扩建而成,改造后可掺炼减压渣油,作为全厂最重要的二次加工装置,承担着重质油轻质化的任务。
随着我厂“短流程燃料型”炼厂的转型,为维持我厂的重油平衡,装置提高了掺渣量,由于掺渣比的上升和原料油变重,油浆系统结焦问题变得日益突出。
本文通过对油浆系统结焦成因分析,有针对性地制定科学合理的对策,保证装置长周期、安全平稳运行。
1 油浆系统结焦的原因1.1 分馏塔低温度由于装置进入三年一修的开炼后期,油浆换热系统结焦严重,换热效率下降,导致分馏塔底部温度长期居高不下(348℃~355℃之间),该温度下塔底组分中的芳烃、烯烃等不饱和烃类进一步缩合成胶质、沥青质,造成结焦前反应物浓度的增加。
1.2 分馏塔低液位由于分馏塔底始终保持着一定的液位,即油浆在分馏塔底有一定的停留时间,而分馏塔底是分馏塔内液相温度最高、催化剂含量最大的部位,在塔底的操作温度下极有可能发生热裂解反应,同时在油浆的稠环芳烃等多种因素的作用下,更进一步趋于缩合脱氢形成焦质,使得塔底出现结焦。
1.3 油浆返塔温度油浆自分馏塔底部抽出,通过换热后,其返塔温度降为250℃~280℃,温度的大幅度降低,使得油浆的粘度增加,流动性能变差,油浆在流动过程中对催化剂以及固体悬浮物的夹带作用减弱,导致催化剂颗粒、固体悬浮物和焦粒变得更易沉积,增加了结焦的几率。
1.4 油浆的停留时间当油浆在某一高温下停留时间足够长时,油浆中将有焦炭生成。
1.5 油浆流速油浆在管道中的流速过低,容易使缩合物沉积在管道表面而得以富集。
聚集的缩合物进一步反应,生成软焦。
1.4 油浆性质玉门炼油厂调和原料和油浆中所含胶质、沥青质比重较高,胶质、沥青质使得结焦倾向增加。
- 1、下载文档前请自行甄别文档内容的完整性,平台不提供额外的编辑、内容补充、找答案等附加服务。
- 2、"仅部分预览"的文档,不可在线预览部分如存在完整性等问题,可反馈申请退款(可完整预览的文档不适用该条件!)。
- 3、如文档侵犯您的权益,请联系客服反馈,我们会尽快为您处理(人工客服工作时间:9:00-18:30)。
20 09年 4月 1 全厂停 电 , 化装置进 入紧 41 3 三催 急停工状 态 。在恢复生产 时 , 现待生催 化剂循 环线 发 路 不 畅 ,经过 现场 操作 验证发 现必 须 实现 负差压 方
可实现 待生催 化剂 转人再 生 器 ,并 且 表现催 化剂 循
u twa h wn b c us fpo rf i e o ni s s utdo e a e o we al n Aprl1 ur i 4,2 09.Buti ou d t tt e c t ls e ic a in wa 0 twasf n ha h a ay tr cr ulto s
焦 结 构 形 态 , 合 生 产 中的 操 作 数 据 , 出沉 降 器 内 结 焦 的原 因 , 提 出 相应 的对 策 。 结 找 并
关键词 : 重油催化裂化 ; 沉降器 ; 结焦 ; 雾化蒸汽 中图分类号 :E 2 . T 6 44 文献标识码 : A
S u n mi g HI Ch a - n Re s n n o u i n o o i g i e te fRFCCU a o sa d s l t sf r c k n s tl r o o n
沉降器内结焦集中在沉降器旋风分离器入 口以
上 至拱形 的广 大空 间 , 包括 旋风 料腿 外壁 上 、 内部支 撑件 上 、 旋肩部 死 区上 、 降器 内壁 上 。并且 料腿 粗 沉 外 壁结焦 严 重 , 度达 到 8~ 0m, 厚 2 c 主体 为无 明显分
层、 质地坚硬 的沉积 焦 。见 图 12 、。
再生器同轴 , 一段在二段上 , 与反应沉降器高低并列 布置。04 20 年应用石油大学辅助提升管技术 , 对装置
进行 了降烯烃改 造 。2 0 0 8年 7月对装 置进行检 修和 改造 , 降 器 壳体 利 旧 , 沉 新设 计 3组粗 旋 , 代原 三 取 叶快分 。升气 管对 3 单级旋 风分离器 , 组 采用软 连接 结构 降低 干气产率 ; 新设 计 待生催 化剂 分配 器 、 第一 再生 器烟气 分布器 、 第一 再 生器 主风分 布板 , 第一 在
( abn P t lu o rnh P t C ia Habn 10 5 , hn ) H ri er em C . ac , e o hn, ri 50 6 C ia o ,B r
Ab t a t T e No3 1 Mt a 1 R C fHa bn P t l u C . sr fr d t e tr a g s 2 0 ; h sr c : h . . 2 。 - FC F o r i er e m o wa e ome o r s t tAu u t 0 8 t e o a
f 中国石油 哈尔滨石化 分公 司。 黑龙江 哈尔滨 1 0 5 5 0 6)
摘
要: 中国石油哈尔滨石化分公 司 1 M ・-三重油催化装 置经检修改造后 于 20 . ta 2 0 8年 8月开工 , 该装
置在 2 0 09年 4月 1 4日全厂停 电后进入紧急停 工状态 。在恢复生产时 , 发现待生催 化剂循环线路不畅 , 不能 正常建立催化剂循环 , 被迫停工处理。 打开沉降器后 , 发现现场结焦严 重。 文通 过分析沉降器结焦部位和结 本
化
学
工
程
师
C e cl nier hmi E gne a
21 0 0年第 l O期
篝
冀f
文 章 编 号 :0 2 12 ( 0 0J0 0 4 — 3 10 — 14 2 1 — 0 9 0 1
蘩
改 : 遭
浅析 重油催化裂化装 置 沉 降器结焦原 因及对策
史传 明
s u o e a s fu a l o w r o mal . e iu o ig wa o n n ie t e s t e .B n l zn h e - h td wn b c u e o n be t o k n r l A s r sc k n sf u d i sd h et r y a a y i g t e s t y o l t me t i n o i g mo p o o y c mb n d wi h p r t n o e p o u t n d t,c k n e s n n ou l e n t a d c k n r h l g , o ie t t e o ea i ft r d ci aa o i g r a o s a d s l — se h o h o t n W r r p s d i eep o oe . o Ke r s RF CU;e t r c k n ao z t n se m y wo d : C s t e ; o i g; tmiai t a l o
中 国石 油 哈 尔滨 石 化 分 公 司 1 ・ 三重 油 . Mt 2
沉 降器 内部 结焦严 重 。
催化 装置装 置 由中石化 北京 设计 院设 计 , 19 于 98年 7月投 产 , 再 系统 采用 新 型重 叠式 两段 再 生 , 反 两段
1 结 焦 部位 及 情 况
11 结焦严重的部位 .
环量较低 , 生催 化剂循 环线路 不 畅 , 待 不能正 常建 立 催 化剂循 环 , 被迫停 工处理 。在沉 降器 打开后 , 现 发
收稿 日期 :0 0 0 — 3 2 1— 7 2
作者简 介: 史传明( 9 3 )男 , 18 一 , 助理工程师 ,0 6 2 0 年毕业于大庆石油
学院化 学化工学 院 , 本科 , 现从 事催化裂 化生产维 护工