最优下料问题的数学模型
一维型材合理下料的数学模型

1 相关研究背景及问题的提出
所 谓 “ 料 问 题 ” 就 是 把 规 格 相 同 的一 些原 材 料 下
目前 , 国 内外 在 优 化 下 料 问题 的研 究上 , 较 多 是
从算法改进的角度上进行的。如文献 l 针对原材料利 l 2
用 率 最 高 的 切 割 方 式 优 先 选 择 策 略 , 设 计 了 贪 心 算
进 行 合理 分 割 后 再 组 合 , 确 定 切 割 下 来材 料 的 排 样 方 案 , 以 达到 材 料 利用 率 最 高。 这 类 问题 可分 为 三大 类 :
切 割 问题 ( u t n S O k P 0 1 m 、排 样 问题 C t i g t C r b ) e ( s O t m n P o l m A S r e e t r b e )和 装箱 问题 ( i P c i g B n a k n
院【 A bs r ct Th ouino h ain l utn fo edme so a r fl a stef u d to o ovn he 兰 t a : es lto fter to a tig o n i n in lp o i ly h n ain frs ligt c e o is s t di i l c tn Fr t e o l bu l n h sa tce etn ag lo 8 e il 学.ueofm uli m ensona uti g. om he viw fm ode idi g.t i ril .s ti g oa f97.4% ofm atra 兰
e o a 唱g p r m m i gm o lI p i i e h s u fm u td m e i na u tn n ne p ie a a nt eh g e t o i. r n de Io tm z st eis eo li i nso l ti g a d e tr rs sc n g i h i h s ft c pr
钢管下料数学建模
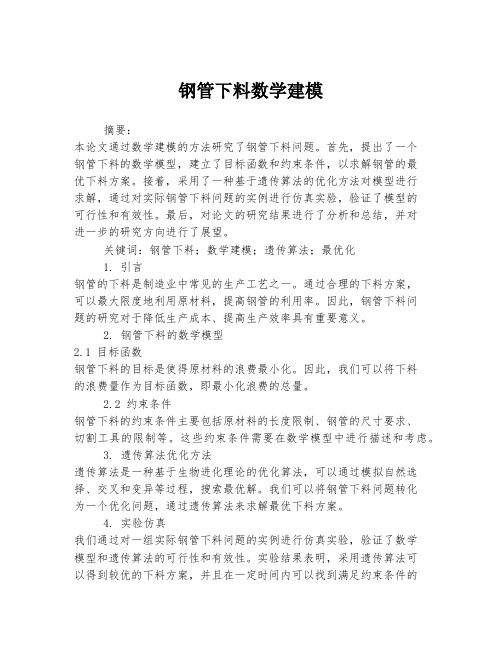
钢管下料数学建模摘要:本论文通过数学建模的方法研究了钢管下料问题。
首先,提出了一个钢管下料的数学模型,建立了目标函数和约束条件,以求解钢管的最优下料方案。
接着,采用了一种基于遗传算法的优化方法对模型进行求解,通过对实际钢管下料问题的实例进行仿真实验,验证了模型的可行性和有效性。
最后,对论文的研究结果进行了分析和总结,并对进一步的研究方向进行了展望。
关键词:钢管下料;数学建模;遗传算法;最优化1. 引言钢管的下料是制造业中常见的生产工艺之一。
通过合理的下料方案,可以最大限度地利用原材料,提高钢管的利用率。
因此,钢管下料问题的研究对于降低生产成本、提高生产效率具有重要意义。
2. 钢管下料的数学模型2.1 目标函数钢管下料的目标是使得原材料的浪费最小化。
因此,我们可以将下料的浪费量作为目标函数,即最小化浪费的总量。
2.2 约束条件钢管下料的约束条件主要包括原材料的长度限制、钢管的尺寸要求、切割工具的限制等。
这些约束条件需要在数学模型中进行描述和考虑。
3. 遗传算法优化方法遗传算法是一种基于生物进化理论的优化算法,可以通过模拟自然选择、交叉和变异等过程,搜索最优解。
我们可以将钢管下料问题转化为一个优化问题,通过遗传算法来求解最优下料方案。
4. 实验仿真我们通过对一组实际钢管下料问题的实例进行仿真实验,验证了数学模型和遗传算法的可行性和有效性。
实验结果表明,采用遗传算法可以得到较优的下料方案,并且在一定时间内可以找到满足约束条件的最优解。
5. 结果分析和总结通过对实验结果的分析和总结,我们可以得出以下结论:数学模型和遗传算法在钢管下料问题中具有较好的应用效果,可以提高下料方案的优化效果和生产效率。
6. 进一步展望在进一步的研究中,我们可以考虑对模型进行改进和扩展,以适应更复杂的钢管下料问题。
此外,可以结合其他优化算法和数据挖掘技术,进一步提高钢管下料的效果和精度。
优化模型 下料问题
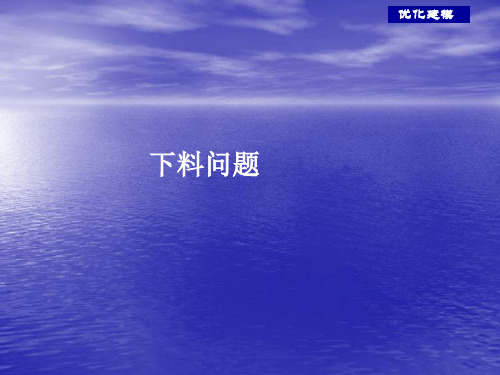
Reduced Cost 1.000000 1.000000 1.000000 0.000000 0.000000 0.000000 0.000000 0.000000 0.000000 0.000000 0.000000 0.000000 0.000000 0.000000 0.000000
优化建模
优化建模
模型求解
1. 将(32),(34)~(36)构成的整数线性规划模型 (加上整数约束)输入LINDO如下: Title 钢管下料 - 最小化余量 Min 3x1 + x2 + 3x3 + 3x4 + x5 + x6 + 3x7 s.t. 4x1 + 3x2 + 2x3 + x4 + x5 >= 50 x2 + 2x4 + x5 + 3x6 >= 20 x3 + x5 + 2x7 >= 15 end gin 7
优化建模
表5-3 钢管下料的合理切割模式
4米钢管根数 6米钢管根数 8米钢管根数 余料(米) 4 0 0 3 3 1 0 1 2 0 1 3
模式1 模式2 模式3 模式4 模式5 模式6 模式7
1 1 0 0
2 1 3 0
0 1 0 2
3 1 1 3
优化建模
问题化为在满足客户需要的条件下,按照哪些种合 理的模式,切割多少根原料钢管,最为节省。而 所谓节省,可以有两种标准,一是切割后剩余的 总余料量最小,二是切割原料钢管的总根数最少。 下面将对这两个目标分别讨论。
优化建模
Variable Value X1 10.00000 X2 10.00000 X3 8.000000 R11 2.000000 R12 3.000000 R13 0.000000 R21 1.000000 R22 0.000000 R23 0.000000 R31 1.000000 R32 1.000000 R33 0.000000 R41 0.000000 R42 0.000000 R43 2.000000
下料问题的线性规划模型
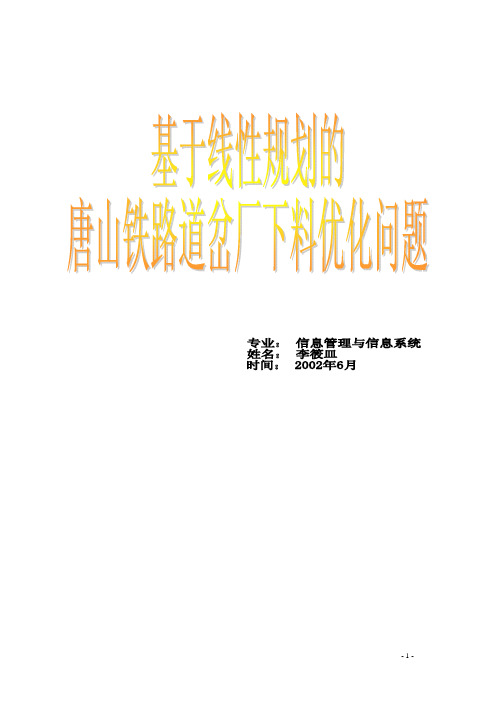
-1-目第一章录绪论 …………………………………………...3第二章 下料问题的线性规划模型2.1 线性规划理论 ……………………. ………4 2.2 线性规划问题的一般数学模型………………...52.3 整数规划问题及其一般解法…………….6第三章 模拟退火算法 3.1 3.2 3.3 3.4 3.5 3.6 参考文献 物理学中的模拟退火………………….…8 米特罗波利斯准则………………….……9 优化问题中的模拟退火算法…….………10 冷却进度表……………………………….16 模拟退火算法应用的要求……………….21 实例分析………………………………….22-2-第一章 绪 论唐山铁路道岔厂位于中国北方重工业城市--唐山,它北依燕山,南临渤海, 毗邻京、津两地,与京唐港咫尺相望,海陆交通便利,地理位置优越。
工厂始 建于 1988 年,是铁道部特别许可生产道岔系列品的专业工厂,厂区占地 12 万平 方米,建筑面积 1.2 万平方米,总资产超亿元,现有职工 500 余人,其中各类高、 中级专业技术人员百余人。
工厂工艺装备先进,检测手段齐全,技术力量雄厚具 备年产高锰钢辙叉 8000 根,整组道岔 2000 组的生产能力。
主要生产各种规格型 号的铁路普通辙叉、机加工辙叉、整组道岔,铁路提速辙叉、道岔及其零配件。
工厂坚持"依靠科技进步,严格质量控制,生产优质产品,满足用户需求" 的质 量方针,严格按照 ISO9000 标准建立了完善的质量保证体系,并于 1999 年 12 月通过了 ISO9002 质量体系认证,产品先后荣获"市优"、"省优"称号,遍布全国 14 个铁路局,地方、地下铁路和大厂企,市场覆盖 28 个省、市、自治区。
产品 不仅满足国内市场,还远销东南亚等国家。
工厂是唐山市"重合同,守信用企业 "、"文明单位"、"五十强企业"、"优秀企业"、河北省"百强企业",被中国企业形 象认定委员会确认为"中国企业形象最佳单位"。
数学建模之下料问题

数学建模第三次作业下料问题摘要本文是针对如何对钢管进行下料问题,根据题目要求以及下料时有关问题进行建立切割费用最少以及切割总根数最少两个目标函数通过结果分析需要使用何种切割模式。
生产方式所花费的成本价格或多或少有所不同,如何选取合理的生产方式以节约成本成为了很多厂家的急需解决的问题。
这不仅仅关系到厂家的利益,也影响到一个国家甚至整个人类星球的可利用资源,人们的生活水平不断提高对物资的需求量也不断上升,制定有效合理的生产方式不仅可以为生产者节约成本也可以为社会节约资源,以达到资源利用最大化。
本文以用于切割钢管花费最省及切割总根数最少为优化目标,通过构建多元函数和建立线性整数规划模型,利用数学及相关方面的知识对钢管的切割方式进行优化求解最佳方案。
本文最大的特色在于通过求解出切割钢管花费最省及切割总根数最少时分别得出两种目标函数取最小值时的切割模式。
通过结果发现两种目标函数取最小值时所需切割根数都一样。
于是选择切割钢管花费最省为目标函数,此时的切割模式达到最少,这样既满足了总根数最小有满足了切割费用最小。
关键词:切割模式 LINGO软件线性整数一、问题的提出某钢管零售商从钢管厂进货,将钢管按照顾客的要求切割后出售。
从钢管厂进货时得到的原料钢管的长度都是1850mm。
现有一客户需要15根290mm、28根315mm、21根350mm和30根455mm的钢管。
为了简化生产过程,规定所使用的切割模式的种类不能超过4种,使用频率最高的一种切割模式按照一根原料钢管价值的1/10增加费用,使用频率次之的切割模式按照一根原料钢管价值的2/10增加费用,依次类推,且每种切割模式下的切割次数不能太多(一根钢管最多生产5根产品)。
此外,为了减少余料浪费,每种切割模式下的余料不能超过100mm。
为了使总费用最小,应如何下料?二、基本假设1、假设所研究的每根钢管的长度均为1850mm的钢管。
2、假设每次切割都准确无误。
3、假设切割费用短时间内不会波动为固定值。
数学建模合理下料问题
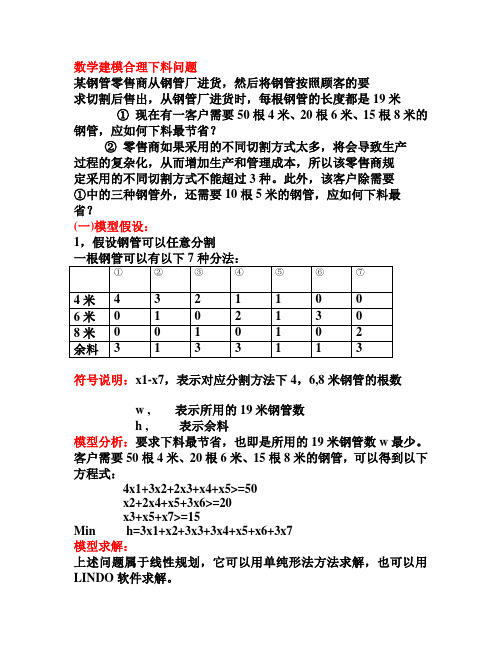
数学建模合理下料问题某钢管零售商从钢管厂进货,然后将钢管按照顾客的要求切割后售出,从钢管厂进货时,每根钢管的长度都是19米①现在有一客户需要50根4米、20根6米、15根8米的钢管,应如何下料最节省?②零售商如果采用的不同切割方式太多,将会导致生产过程的复杂化,从而增加生产和管理成本,所以该零售商规定采用的不同切割方式不能超过3种。
此外,该客户除需要①中的三种钢管外,还需要10根5米的钢管,应如何下料最省?(一)模型假设:1,假设钢管可以任意分割一根钢管可以有以下7种分法:①②③④⑤⑥⑦4米 4 3 2 1 1 0 06米0 1 0 2 1 3 08米0 0 1 0 1 0 2余料 3 1 3 3 1 1 3符号说明:x1-x7,表示对应分割方法下4,6,8米钢管的根数w , 表示所用的19米钢管数h , 表示余料模型分析:要求下料最节省,也即是所用的19米钢管数w最少。
客户需要50根4米、20根6米、15根8米的钢管,可以得到以下方程式:4x1+3x2+2x3+x4+x5>=50x2+2x4+x5+3x6>=20x3+x5+x7>=15Min h=3x1+x2+3x3+3x4+x5+x6+3x7模型求解:上述问题属于线性规划,它可以用单纯形法方法求解,也可以用LINDO软件求解。
用LINDO求解如下:直接输入min 3x1+x2+3x3+3x4+x5+x6+3x7subject to4x1+3x2+2x3+x4+x5=50x2+2x4+x5+3x6=20x3+x5+x7=15end将文件存储并命名后,选择菜单“solve”,并对提示“DO RANGE(SENSITIVITY)ANALYSIS”回答“是”或“否”。
即可得输出结果。
LP OPTIMUM FOUND AT STEP 4OBJECTIVE FUNCTION V ALUE1) 35.00000VARIABLE V ALUE REDUCED COSTX1 0.000000 0.000000X2 10.000000 0.000000X3 5.000000 0.000000X4 0.000000 4.750000X5 10.000000 0.000000X6 0.000000 4.750000X7 0.000000 1.500000模型假设:一根钢管可以有以下15种分法:⑴⑵⑶⑷⑸⑹⑺⑻⑼⑽⑾⑿⒀⒁⒂44 3 3 2 2 2 1 1 1 0 0 0 0 0 0 米0 1 0 2 1 0 3 1 0 2 2 1 1 0 0 5米0 0 1 0 1 0 0 0 1 1 0 2 1 3 0 6米0 0 0 0 0 1 0 1 1 0 1 0 1 0 2 8米3 2 1 1 0 3 0 2 1 3 1 2 0 1 3 余料符号说明:x1-x15,表示对应分割方法下4,5,6,8米钢管的根数w , 表示所用的19米钢管数h , 表示余料模型分析:要求下料最节省,也即是所用的19米钢管数w最少。
钢管下料数学建模
钢管下料数学建模一、引言钢管下料是工业生产中常见的一项工艺,它涉及到如何将原始的钢管按照预定的尺寸进行切割,以便于后续加工和使用。
在进行钢管下料时,数学建模可以帮助我们计算出最佳的下料方案,以最大程度地减少浪费,提高生产效率。
本文将以钢管下料数学建模为主题,探讨如何利用数学方法求解钢管下料问题。
二、问题描述假设有一根长度为L的钢管,需要按照给定的尺寸进行切割。
切割时需要考虑以下几个因素:1. 切割后的钢管长度需要满足给定的要求;2. 切割时需要考虑钢管的浪费情况,即尽量减少剩余钢管的长度;3. 切割时需要考虑生产效率,即尽量减少切割次数。
三、数学建模钢管下料问题可以抽象为一个数学模型,通过建立数学模型,我们可以计算出最佳的下料方案。
下面将介绍两种常见的数学建模方法。
1. 贪心算法贪心算法是一种简单而常用的数学建模方法,它通过每一步都选择局部最优解来达到全局最优解。
在钢管下料问题中,贪心算法可以按照以下步骤进行:1)将钢管初始长度L赋值给一个变量remain;2)根据给定的尺寸要求,选择一个长度小于等于remain的最大钢管尺寸,将其切割出来;3)将remain减去切割出来的钢管长度,得到剩余的钢管长度;4)重复步骤2和3,直到remain小于等于0。
2. 动态规划动态规划是一种更加复杂但是更加精确的数学建模方法,它通过将原问题划分为多个子问题,并保存子问题的解来求解原问题。
在钢管下料问题中,动态规划可以按照以下步骤进行:1)建立一个长度为L+1的数组dp,dp[i]表示长度为i的钢管的最佳下料方案所需的最少切割次数;2)初始化dp数组,将dp[0]设置为0,其余元素设置为正无穷大;3)从长度为1开始,依次计算dp[1]、dp[2]、...、dp[L]的值;4)最终dp[L]即为所求的最佳下料方案所需的最少切割次数。
四、案例分析为了更好地理解钢管下料数学建模,我们以一个具体的案例进行分析。
假设有一根长度为9米的钢管,需要切割成长度分别为2米、3米和4米的三段钢管。
最优下料问题的数学模型
此行为将导致 NL 矩阵中的某一值被 Si 累加了多次,为此,可以将 Step5 中的判断函数:
NoZeros(NL) 0 改为 NoZeros(NL) Length(NL) 10
即
NL
中剩下
1 10
未被选择时即跳出,然后对剩下的
1 10
进行重组合,即将
NL
中等于
0
的数剔除,非零数值重新组合成新的 NL ,再继续运行 Step1~Step5 即可尽量避免当
3切割过程中无人工误差三符号的说明31问题一的符号说明符号说明kmax等额完成任务所需的原材料数k原材料个数i零件标号xi在第个原材料上切割的第个零件标号的零件数量kikm规格种数li需求零件长度l单一原材料长度di12?m需求零件数量is需下料的全部零件总长度q下料方式数l废料总长度3四问题的分析对于问题一为一维下料问题考虑首要目标为使原材料利用率最大然后再使下料方式数尽可能少
最优下料问题的数学模型
摘要
本文通过对两个问题进行分析,分别建立模型一、模型二。针对模型一,设计程序 贪心算法,通过 Matlab 编程,得出相应结果。针对模型二,文中通过将二维问题转换 成为一维问题,引用规划模型,做出相应分析。
在问题一中,为解决一维下料问题,根据一维下料问题的特点,建立起由其约束条 件组合而成的规划模型,在随机决策的基础上利用贪心算法取每个决策中的最优值,较 快地获得问题的最优解为:前 6 天下料方案整和为一个方案比制定 4 天,6 天方案更优, 且前 6 天需用原材料根数为 268,利用率为 99.21%,3 天完成;剩余下料方案为需用原 材料根数为 538,利用率为 98.92%,6 天完成。(详见表 6-1 和附录表 6-2、表 6-3)
LnM
数学建模--钢管下料问题
钢管下料问题摘要:如何建立整数规划模型并得出整数规划模型的求解方法是本实验要点,本题建立最常见的线性整数规划,利用分支定界法和Lingo 软件进行求解原料下料类问题,即生产中通过切割、剪裁、冲压等手段,将原材料加工成所需大小;按照工艺要求,确定下料方案,使所用材料最省,或利润最大。
分支定界法可用于解纯整数或混合的整数规划问题,此方法灵活且便于用计算机求解,所以现在它已是解整数规划的重要方法。
Lingo 软件的功能是可以求解非线性规划(也可以做线性规划,整数规划等),特点是运算速度快,允许使用集合来描述大规模的优化问题。
大规模数学规划的描述分为四个部分: model:1.集合部分(如没有,可省略) SETS:集合名/元素1,元素2,…,元素n/:属性1,属性2,… ENDSETS2.目标函数与约束部分3.数据部分(如没有,可省略)4.初始化部分(如不需要初始值,可省略) end关键字:材料 Lingo 软件 整数规划问题描述:某钢管零售商从钢管厂进货,将钢管按照顾客的要求切割后售出,从钢管厂进货时得到的原料都是19米。
(1)现有一顾客需要50根4米、20根6米和15根8 米的钢管。
应如何下料最节省?(2)零售商如果采用的不同切割模式太多,将会导致生产过程的复杂化,从而增加生产和管理成本,所以该零售商规定采用的不同切割模式不能超过3种。
此外,该客户除需要(1)中的三种钢管外,还需要10根5米的钢管。
应如何下料最节省。
(1)问题简化:问题1. 如何下料最节省 ? 节省的标准是什么?原料钢管:每根19米 4米50根 6米20根 8米15根问题2. 客户增加需求:由于采用不同切割模式太多,会增加生产和管理成本,规定切割模式不能超过3种。
如何下料最节省?问题分析:切割模式,例如:按照客户需要在一根原料钢管上安排切割的一种组合。
为满足客户需要,按照哪些种合理模式,每种模式切割多少根原料钢管,最为节省?两种标准:1.原料钢管剩余总余量最小。
数模_下料问题与计算
下料问题与计算在工业生产中,经常会遇到切割下料问题,即,如何最佳的切割按固定尺寸供应的材料,使得既符合所需要求又尽可能减少浪费。
§10.1一维下料问题例10-1有10米长的钢管,切割成3米长的80根,4米长的70根,问:怎样下料最省料?解:首先讨论切割方法切割方法13×3米+0×4米+废料1米切割方法22×3米+1×4米+废料0米切割方法30×3米+2×4米+废料2米设用切割方法i 切割i x 根钢管目标函数1:总根数最少321min x x x f ++=目标函数2:总废料最少3212*0min x x x f ++=约束条件⎪⎩⎪⎨⎧≥≥++≥++整数,0703221080302213..jx x x x x x x t s 对第一个目标函数求解,得到结果如下:153,402,01,55min ====x x x f 对第二个目标函数求解,得到结果如下:03,702,01,0min ====x x x f 此时总根数为70根,总废料为0。
注意,两个目标函数构成的线性规划问题不等价。
例10-2长500Cm 的钢管,切割成98Cm 、78Cm 的小钢管,要求98Cm 的≥1万根,78Cm 的≥2万根。
怎样切割材料最省?解:首先讨论切割方法切割方法10×98cm +6×78cm +废料32cm 切割方法21×98cm +5×78cm +废料12cm 切割方法32×98cm +3×78cm +废料70cm 切割方法43×98cm +2×78cm +废料50cm 切割方法54×98cm +1×78cm +废料30cm 切割方法65×98cm +0×78cm +废料10cm设用切割方法i 切割i x 根钢管目标函数1:总根数最少654321min x x x x x x f +++++=目标函数2:总废料最少654321103050701232min x x x x x x f +++++=约束条件⎪⎩⎪⎨⎧≥≥+++++≥+++++整数,020000605423325161000065544332210..j x x x x x x x x x x x x x t s 对第一个目标函数求解,得到结果如下:12006,05,04,03,40002,01,5200min =======x x x x x x f 对第二个目标函数求解,得到结果如下:12006,05,04,03,40002,01,60000min =======x x x x x x f 总根数都是5200根,总废料为60000cm 。
- 1、下载文档前请自行甄别文档内容的完整性,平台不提供额外的编辑、内容补充、找答案等附加服务。
- 2、"仅部分预览"的文档,不可在线预览部分如存在完整性等问题,可反馈申请退款(可完整预览的文档不适用该条件!)。
- 3、如文档侵犯您的权益,请联系客服反馈,我们会尽快为您处理(人工客服工作时间:9:00-18:30)。
li xki 5 xki L, k 1,2,, k max
i 1 i 1
m
m
1 ○
(2)需求量约束条件为:
4
k max
x
k 1
ki
ni , i 1,2,, m
2 ○
以及对 xki 的非负整数要求。 (3)下料方式约束条件为:
Q min 5
i 1
m
k max
5
(1)等额完成任务所需的原材料数: k max (2)下料方式数: Q (3)废料总长度: L* 3000 k max l i ni 3000 k max s
i 1 m
(4)下料方案: 从上述模型可得出,下料方案为满足模型约束条件的最优解。 2、算法实现——随机决策下的贪婪算法 Step1: 对于给定需要完成的产品, 长度和需求量分别为 L 和 n, 构造一个 n 行 1 列矩阵 NL,
所引起的锯缝损耗忽略不计.据估计,该企业每天最大下料能力是20块 要求在4天内完 成的零件标号( i )为: 3,7,9,12,15, 18, 20, 25, 28, 36.
二、问题的假设
(1)问题一中的零件厚度和宽度均与原材料相等; (2)问题二中的零件厚度均与原材料相等。 (3)切割过程中无人工误差
4 ○
3 ○
其中, Z {0,1,2,} 为非负整数的集合。 3) .求得所需原材料最小值 设 s l i n i ,表示需下料的全部零件总长度。进而定义:
i 1 m
s / L为整数 s / L, k* int( s / L) 1, 其他
4 ○
则所需原材料的最小值为 k * ,若由目标函数○ 3 求得的结果 k max k * ,则计算结果有误, 需要修正程序算法,或是重新建立模型。由式 ○ 4 求得的最小值可避免犯一些明显的错 误,并且可对程序进行验证。 4)结果表示:
NoZeros( NL) 0
改为
NoZeros( NL)
Length( NL) 10
即 NL 中剩下 1 未被选择时即跳出,然后对剩下的 1 进行重组合,即将 NL 中等于 0 10 10 的数剔除,非零数值重新组合成新的 NL ,再继续运行 Step1~Step5 即可尽量避免当
R i j R i k 时, R i 所对应的 S i 为 max( S i ) 的情况。
6
的,该值不被采用,否则该值被分流进盒子,如果循环操作至第 100 组随机值,最后结 果将产生出 100 组随机策略组合,每组的累加值均满足小于 3000,即:
i i S i S i R j 5 , if S i R j 5 3000 Si i S i S i , if ( S i R j 5 3000
i 1,2,100
j 1,2,20
Step4: 对 Step3 产生的 100 种满足条件的随机组合采取择优选择,即选择 max( S i ) ,此为 一次贪心决策结果,将构成 max( S i ) 的各长度值从 NL 矩阵中去掉,即将其值变为 0. Step5: 判断 NL 矩阵中的非零值个数,当 NoZeros( NL) 0 时,即表示 NL 中的每个值都 已经被选出,否则继续 Step2~Step5。 由以上 Step1~Step5 结束后易知最终结果为各类型需求量均能被满足,此为最终 的解。 在实际操作中可能 Step2 中的 100 个随机数组中有些数组的 20 个随机值出现雷同数值, 亦即 R i j R i k ,此时如果 R i 所对应的 S i 为 max( S i ) ,那么该随机决策将是一种伪决策, 此行为将导致 NL 矩阵中的某一值被 S i 累加了多次,为此,可以将 Step5 中的判断函数:
三、符号的说明
3.1 问题一的符号说明 符号 说明 等额完成任务所需的原材料数 原材料个数 零件标号 在第 k 个原材料上切割的第 i 个零件标号的零件数量 规格种数 需求零件长度 单一原材料长度 需求零件数量 需下料的全部零件总长度 下料方式数 废料总长度
3
k max
k i
xki
m
li
L
d i (i 1,2,, m)
五、模型的建立与求解
5.1 问题一 5.1.1 模型一的建立与求解 1、 模型一的建立 1) .约束条件 如题,设原材料呈长方形,长度为 L ,现在需要将一批这种长方形原料分割成 m 种 规格的零件, 所有零件的厚度和宽度均与原材料一致,第 i 种规格的零件的长度为 li , 需求量为 ni (i 1,2,, m) 个。 共耗用 k max 个原材料, 且在第 k 个原材料上切割的第 i 个零件标号的零件数量为 xki , 则有: (1)原材料规格与锯缝损耗约束条件为:
最优下料问题的数学模型
摘要
本文通过对两个问题进行分析,分别建立模型一、模型二。针对模型一,设计程序 贪心算法,通过 Matlab 编程,得出相应结果。针对模型二,文中通过将二维问题转换 成为一维问题,引用规划模型,做出相应分析。 在问题一中,为解决一维下料问题,根据一维下料问题的特点,建立起由其约束条 件组合而成的规划模型,在随机决策的基础上利用贪心算法取每个决策中的最优值,较 快地获得问题的最优解为: 前 6 天下料方案整和为一个方案比制定 4 天, 6 天方案更优, 且前 6 天需用原材料根数为 268,利用率为 99.21%,3 天完成;剩余下料方案为需用原 材料根数为 538,利用率为 98.92%,6 天完成。 (详见表 6-1 和附录表 6-2、表 6-3) 在问题二中,基于零件长、宽两个方向上的限制的情况后,根据问题 2 中待加工的 零件的宽只集中在 50mm,30mm,35mm,20mm 四种规格上,将二维问题转化为一维问题, 分别用一维下料问题的方法寻求四种宽度条材在一维情况下的最优方案。在这一过程 中,可根据一维下料问题求解的方法,建立模型二,解多目标整数规划,再进行最优组 合,可以得到两个阶段所使用的条材。
的总需求量。 Step2: 产生 100 个随机数组,每个随机数组包含 20 个数,随机数组 R i j 的取值范围为
1 ~ length( NL) ,其中 R i j 表示第 i 个数组里面的第 j 个随机数的值。将每一组数组的值
每组策略有 R i 对应到 Step1 构造的矩阵 NL 中的第 R i 个数中,结果是产生 100 组策略, 20 个值。 Step3: 将产生的 Step2 产生的 100 组策略装进 100 个队列中,对每个队列进行分流操作, 从第 1 组的第一个值开始累加到第一组的第 20 个数,累加过程中如果累加值超出 3000
wi W , i 1,, m ,则问题称为一维下料问题。
一个好的下料方案首先应该使原材料的利用率最大,从而减少损失,降低成本,提 高经济效益。其次要求所采用的不同的下料方式尽可能少,即希望用最少的下料方式来 完成任务。因为在生产中转换下料方式需要费用和时间,既提高成本,又降低效率。此 外,每种零件有各自的交货时间,每天下料的数量受到企业生产能力的限制。因此实用 下料问题的目标是在生产能力容许的条件下,以最少数量的原材料,尽可能按时完成需 求任务, 同时下料方式数也尽量地小.请你们为某企业考虑下面两个问题。 1、建立一维单一原材料实用下料问题的数学模型, 并用此模型求解下列问题,制 定出在生产能力容许的条件下满足需求的下料方案, 同时求出等额完成任务所需的原 材料数,所采用的下料方式数和废料总长度.单一原材料的长度为 3000mm, 需要完成一 项有53种不同长度零件的下料任务. 具体数据见表一, 其中 li 为需求零件的长度,ni 为 需求零件的数量. 此外,在每个切割点处由于锯缝所产生的损耗为5mm. 据估计,该企 业每天最大下料能力是100块 ,要求在4天内完成的零件标号( i )为: 5,7,9,12,15,18,20,25, 28,36,48; 要求不迟于6天完成的零件标号( i ) 为:4,11,24,29,32,38,40,46,50. (提示:可分层建模。 (1).先考虑用材料既少,下料方式又少的模型, 或先仅考虑所用材料最少的模型及 增加一种下料方式大致相当于使原材料总损耗增加0.08%情况下的最佳方案。
至此,利用 Matlab 编程可求出满足题目要求的方案,从方案中可以检测出
R i j R i k 时, R i 所对应的 S i 为 max( S i ) 的情况仅为四种,对四种方案人为处理后即可
关键词:
贪心算法
最优下料
规划
1
一、问题的重述
“下料问题(cutting stock problem)”是把相同形状的一些原材料分割加工成若干 个不同规格大小的零件的问题, 此类问题在工程技术和工业生产中有着重要和广泛的应 用. 这里的“实用下料问题”则是在某企业的实际条件限制下的单一材料的下料问题。 现考虑单一原材料下料问题 . 设这种原材料呈长方形,长度为 L ,宽度为 W ,现在 需要将一批这种长方形原料分割成 m 种规格的零件, 所有零件的厚度均与原材料一致, 但长度和宽度分别为 (l1 , w1 ), , (lm , wm ) ,其中wi < li L, wi W , i 1, , m . m 种零件 的需求量分别为 n1 ,, nm .下料时,零件的边必须分别和原材料的边平行。这类问题在 工 程 上 通 常简 称 为 二维 下 料 问题 。 特 别当所 有 零 件 的宽 度 均 与原 材 4)下料能力约束条件为: 每天的最大下料能力有: K j 100 2) .目标函数的建立 目标函数的建立是为求得 k max 的最小值,因此建立如下:
min k max m l i x ki L, k 1,2, , k max i 1 k max x ki di, i 1,2, , m k 1 x ki Z
L11 1 L n1 L21 其中 L1i 表示第 1 种材料的第 i 个排列, L1 n 中的 n 表示第一种材料 形如: NL 2 Ln L M 1 M Ln M