COMSOL Multiphysics钢铁铸造工艺的优化
CAE技术指导优化铸造钢材质和性能
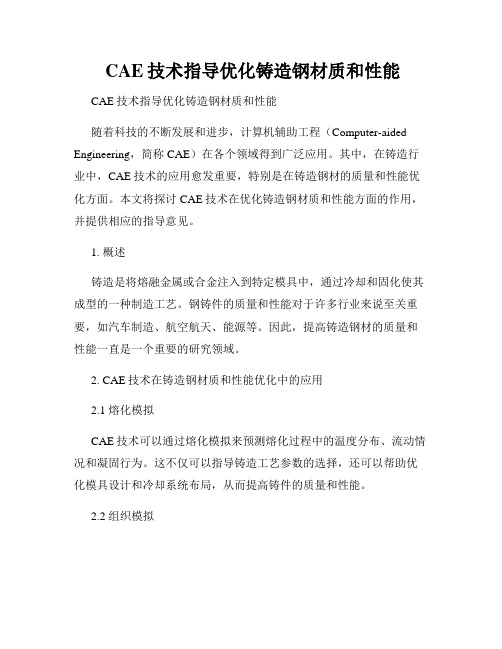
CAE技术指导优化铸造钢材质和性能CAE技术指导优化铸造钢材质和性能随着科技的不断发展和进步,计算机辅助工程(Computer-aided Engineering,简称CAE)在各个领域得到广泛应用。
其中,在铸造行业中,CAE技术的应用愈发重要,特别是在铸造钢材的质量和性能优化方面。
本文将探讨CAE技术在优化铸造钢材质和性能方面的作用,并提供相应的指导意见。
1. 概述铸造是将熔融金属或合金注入到特定模具中,通过冷却和固化使其成型的一种制造工艺。
钢铸件的质量和性能对于许多行业来说至关重要,如汽车制造、航空航天、能源等。
因此,提高铸造钢材的质量和性能一直是一个重要的研究领域。
2. CAE技术在铸造钢材质和性能优化中的应用2.1 熔化模拟CAE技术可以通过熔化模拟来预测熔化过程中的温度分布、流动情况和凝固行为。
这不仅可以指导铸造工艺参数的选择,还可以帮助优化模具设计和冷却系统布局,从而提高铸件的质量和性能。
2.2 组织模拟通过CAE技术进行组织模拟可以模拟钢铸件的凝固过程和组织形成。
这有助于预测铸造钢材的晶粒尺寸、相组成和组织均匀性等方面的参数,从而指导铸造工艺控制和材料优化。
2.3 应力和变形模拟铸造钢材在冷却和固化过程中会受到热应力和冷却收缩等因素的影响,可能导致铸件产生变形和应力集中。
CAE技术可以用于模拟这些因素对铸造钢材质和性能的影响,通过优化工艺和材料选择,减少铸件的变形和应力集中,提高铸件的质量和性能。
3. CAE技术的指导意见3.1 工艺参数优化通过CAE技术的应用,可以分析和模拟不同工艺参数对铸造钢材质和性能的影响。
在具体的铸造过程中,可以根据模拟结果选择合适的工艺参数,如浇注温度、浇注速度、冷却时间等,以优化铸件的质量和性能。
3.2 模具设计和冷却系统优化CAE技术可以模拟铸造过程中的温度分布和流动情况,从而指导模具设计和冷却系统的优化。
通过合理设计模具结构和布局冷却系统,可以均匀降低铸件温度梯度,减少组织偏差,提高材料的稳定性和性能。
外壳体铸件成型数值模拟及工艺优化

外壳体铸件成形数值模拟及工艺优化廖兴银(贵州航天新力铸锻有限公司贵州遵义)摘要:利用“CAE软件”计算外壳体铸件充型凝固过程模拟,对定量缩孔模拟计算进行了探讨。
应用此计算方法对外壳体不锈钢铸件进行数值模拟,优化其铸造工艺。
关键词:外壳体铸件;数值模拟;工艺优化目前,在国内的中小型铸造企业中,都面临市场份额不足,铸件质量要求高,原辅材料不断上涨,铸件利润空间变得越来越窄的困境。
这样的前提下,企业急需解决的问题就是提高产品质量来争取更大的市场份额,同时寻求较高的利润空间来壮大企业。
要实现这两点,除了加强生产管理和企业资金运作外,还要去对铸造工艺的优化来保证铸件的质量和降低铸件在实现过程中的成本。
本论文主要研究方向是利用CAE软件来优化大型铸件(对中小企业来说)的铸造工艺,寻找一个最佳的工艺方案,在保证铸件质量的前提下来提高工艺出品率,同时已能解决该类企业由于设备能力的局限带来的钢水量不足的问题。
1、计算机辅助设计的发展史铸造成形优良的随意性、复杂性和经济性在所有的热加工成形技术中占有很大的优势。
而计算机数字模拟技术、计算力学和传热传质学的迅速发展,可以将铸造成形过程又不可视化为可视,使铸造工艺设计由定性转向定量,由经验设计走向科学预测。
由于上述优点,从20世纪60年代到目前,美、日、英、德、法等工业发达国家的冶金铸造技术人员都开展了这方面的研究,掀起了一次次高潮。
在1988年5月第四届铸造和焊接的计算机数值模拟的会议上,模拟比赛的结果表明三维温度场计算已经成熟,充型过程的数值模拟随之兴起。
1983-1993年,美国、西德、丹麦、加拿大、比利时等国的研究人员采用MAC、SMAC、SOLA-VOF方法,在砂铸、压铸、实型铸造中模拟了灰铸铁、铝合金、球墨铸铁的充型过程,进行二维、三维速度场和温度场的计算,获得液态金属流动模式、充型次序、速度分布、各部位充型时间,预测冷隔、气孔、氧化膜卷入等缺陷,并与高速摄影、水力模拟试验对比验证,开辟了模拟新领域。
钢铁制造工艺优化方法

钢铁制造工艺优化方法介绍在钢铁制造行业中,优化工艺是提高生产效率和质量的关键。
通过采用先进的技术和方法,可以降低能耗、减少废料产生、改善产品性能等,从而提高企业的竞争力。
本文将介绍一些常用的钢铁制造工艺优化方法。
1. 设备升级钢铁制造过程中使用的设备对产品质量和工艺流程至关重要。
通过升级设备,采用先进的技术,可以提高生产效率。
例如,使用高效的炼钢炉和炼铁炉可以降低能耗,并减少废料产生。
此外,采用先进的控制系统和自动化设备可以提高生产线的稳定性和准确性。
2. 原料优化钢铁制造中的原料选择和使用对产品质量和成本有重要影响。
优化原料选择,可以提高产品性能,并减少生产过程中的损耗。
例如,选择高质量的铁矿石和焦炭,可以降低焦炭消耗量,并减少废料产生。
此外,合理调配原料比例,可以获得更好的熔炼效果。
3. 工艺流程优化钢铁制造的工艺流程包括炼铁、炼钢、连铸等环节。
通过优化工艺流程,可以提高生产效率和产品质量。
例如,采用先进的热处理技术,可以改善产品性能。
此外,合理调整生产参数,可以减少废品率,并提高产品一致性。
4. 能源管理能源在钢铁制造中占据重要地位。
优化能源管理,可以降低能耗,并减少对环境的影响。
例如,采用高效的燃烧设备和回收利用技术,可以降低能耗和废气排放量。
此外,合理控制生产线的运行时间和负荷,可以减少能源浪费。
5. 质量控制质量控制是保证产品质量的关键环节。
通过建立完善的质量管理体系,采用先进的检测技术和方法,可以降低产品缺陷率,提高一致性。
例如,使用先进的无损检测技术可以及时发现潜在问题,并采取相应措施。
结论钢铁制造工艺优化是提高生产效率和质量的重要手段。
通过设备升级、原料优化、工艺流程优化、能源管理和质量控制等方法,可以降低成本、提高产品性能,并减少对环境的影响。
钢铁制造企业应该积极采用这些方法,不断优化工艺,以提升自身竞争力。
以上文档共计843字。
希望对你有所帮助!。
铸造工艺中的数值模拟与优化研究

铸造工艺中的数值模拟与优化研究第一章:引言铸造工艺是制造业中一项重要的制造技术,它涉及到金属材料的熔化、铸型和凝固等过程。
随着现代科学技术的不断发展,数值模拟与优化研究成为铸造工艺改进的重要手段。
本文将从数值模拟和优化两个方面进行研究,以探索如何利用现代技术提高铸造工艺的效率和质量。
第二章:数值模拟在铸造工艺中的应用数值模拟是通过使用计算机模拟铸造过程中的物理现象和工艺参数,以预测和改进铸造工艺的一种方法。
在铸造过程中,流体力学、传热学和固相变化等多种物理现象相互作用,对铸件的性能和质量产生重要影响。
利用数值模拟方法可以定量地解决这些问题,并优化铸造工艺参数。
3.1 流体力学模拟铸造过程中,熔融金属流动的方式和路径对铸件质量和内部缺陷的形成有重要影响。
数值模拟可以利用计算流体力学(CFD)方法,分析流动行为、温度分布和气体冲击等因素,并通过调整浇注方式、浇注温度和铸型设计等工艺参数,优化铸造工艺,减少缺陷的产生。
3.2 传热学模拟铸造过程中的热传递对铸件的凝固和晶粒生长等过程起着重要作用。
数值模拟可以使用传热学模拟方法,分析热能在铸件中的分布和传递方式,进而优化冷却方式、浇注温度和浇注速度等工艺参数,控制铸件的凝固过程,改善铸件的组织和性能。
3.3 固相变化模拟铸造过程中,熔融金属的凝固过程会引起固态相变。
数值模拟可以模拟和预测这些相变过程,通过调整铸造参数,使固态相变能够更加均匀地进行,从而提高铸件的力学性能和组织均匀性。
第三章:优化方法在铸造工艺中的应用优化方法是指通过数学模型和算法,寻找最优解或接近最优解的一种方法。
在铸造工艺中,优化方法可以应用于铸造工艺参数的调整和铸造工艺方案的选择。
4.1 参数优化在铸造工艺中,有许多参数需要进行调整,如浇注温度、浇注速度、尺寸设计等。
优化方法可以通过建立数学模型,以最小化铸件的缺陷和提高铸件的性能为目标,确定最优的工艺参数。
4.2 工艺方案优化铸造工艺方案的选择对于铸件的质量和产能起着决定性作用。
铸造合金的超塑性与成型工艺优化

铸造合金的超塑性与成型工艺优化铸造合金是一种常见的金属材料,广泛应用于工业领域。
其中,超塑性是一种特殊的力学行为,指材料在高温条件下具有显著的塑性变形能力。
超塑性材料的成型工艺优化对于提高产品质量和生产效率至关重要。
本文将重点探讨铸造合金的超塑性特性及其成型工艺优化。
一、铸造合金的超塑性特性铸造合金是通过熔融金属倾注到特定模具中,通过冷却凝固形成所需产品的过程。
合金的化学成分和冷却过程会影响材料的力学性能,包括超塑性。
常见的铸造合金如锌合金、铝合金等都具备一定的超塑性。
超塑性材料的主要特点是在高温下具有优异的塑性变形能力,可以实现较大的应变。
通常来说,超塑性的温度范围为材料的熔点到固溶温度之间。
在这个温度范围内,合金的晶粒可以发生迁移和重组,从而使其形变能力得到提高。
此外,超塑性材料还具备细化晶粒和改善材料的韧性的特点。
二、成型工艺优化的重要性成型工艺是指将铸造合金进行成型和制造所需产品的过程。
优化成型工艺可以改善产品质量和生产效率,降低成本和资源浪费。
在铸造合金的超塑性成型过程中,合适的工艺优化可以实现以下目标:1. 提高产品的致密性:通过合理的温度控制和形变条件,可以使铸造合金的晶粒细化,从而提高产品的致密性和力学性能。
2. 减少缺陷和变形:合金的超塑性成型过程容易产生缺陷和变形,因此需要精确控制温度、应变速率和周围环境等因素,以减少产品的缺陷和变形。
3. 提高工艺稳定性:合理的成型工艺可以提高生产的稳定性和可重复性,降低生产过程中的变异性和不良品率。
三、铸造合金的超塑性成型工艺优化方法1. 温度控制:超塑性成型的温度控制非常重要。
一般来说,温度控制在合金的熔点到固溶温度之间,以保证合金处于超塑性状态。
此外,温度的均匀性也对成型的质量具有重要影响,需要通过加热设备和热处理工艺进行控制。
2. 应变速率控制:合金的超塑性成型过程中,应变速率对产品的细化效果有直接影响。
较低的应变速率有利于晶粒的细化,但也会导致成型时间加长。
冶金行业中的铸造工艺优化技术研究

冶金行业中的铸造工艺优化技术研究铸造工艺在冶金行业中扮演着至关重要的角色,它对于产品质量、生产效率和能源消耗等方面都有着直接的影响。
为了进一步提高铸造工艺的效率和质量,并减少对环境的不良影响,研究人员一直致力于铸造工艺的优化技术。
铸造工艺优化技术的研究有助于发现和解决传统铸造工艺中的问题,提高生产效率和产出质量。
首先,铸造工艺的优化可以通过改进铸件的设计和制造工艺来减少缺陷。
例如,通过使用模拟软件来优化铸件的造型和冷却系统,可以减少铸件中的热裂纹和气孔等缺陷的产生。
其次,优化技术还可以通过减少原材料和能源的使用来改善铸造工艺的可持续性。
例如,通过优化熔炼过程、提高铸造温度和改良冷却系统等方法,可以减少能耗并提高能源利用率。
与此同时,新型材料的引入也为铸造工艺的优化提供了更多的可能性。
例如,使用抗热裂降合金铸铁代替传统灰铸铁,可以改善铸件的强度和抗热裂性能。
此外,使用新型颗粒弥散强化材料可以提高铸件的硬度和耐磨性。
通过优化合金配方和添加合适的纳米材料,可以获得更高性能的铸件,满足现代高要求的冶金工业。
铸造工艺优化技术的研究还包括对生产过程的智能化控制。
随着物联网和人工智能等技术的发展,智能铸造系统的研究已经取得了一定进展。
这些系统可以通过在线监测和控制铸造过程的关键参数,实时调整工艺参数,从而提高铸造工艺的一致性和稳定性。
智能铸造系统还可以通过自动化和机器学习技术,提高生产过程的效率和质量,并降低操作风险。
此外,铸造工艺优化技术的研究还涉及到对工艺参数和原材料的优化。
通过优化熔炼温度、冷却速度和砂型配方等参数,可以获得更好的铸造质量和碳足迹。
通过优化原材料的选择和处理方法,可以减少铸件中的杂质和夹杂物,提高材料的纯度和强度。
这些优化措施可以显著提高铸造工艺的效率和质量,降低生产成本和环境污染。
综上所述,冶金行业中铸造工艺优化技术的研究是必要且紧迫的。
通过改进铸造工艺和控制系统,优化材料和工艺参数,我们可以获得更高质量、高效率和可持续发展的铸造工艺。
基于模拟技术的球墨铸铁件铸造工艺优化

2 . 铸 件工艺分析
铸 件 的三 维立 体结 构 如 图2 所 示 , 铸 件 轮 廓 尺寸 为8 5 5 mm ×4 7 4 m1 T I ×5 1 5 mm,最 小 壁 厚 为 1 0 mm,最大 壁 厚 为7 5 mm,质量 为 1 6 8 k g ,材 质为
QT 5 o 0 —7 ,其 化学 成 分 见表 1 ,力学 性 能 见表 2 。
造
Ca s d n g
基于模拟技术的球墨铸铁件
铸造工艺优化
西 安文理学 院物理与机械 电子工程 学院 ( 陕西 7 1 0 0 6 5 ) 鲁瑞 轩 何斌锋
铸造是零件毛坯最常用 的生产工艺之一 。铸造
具 有 很 多特 点 ,与其 他 成 形 工艺 相 比 ,其 不 受 零件
毛 坯 的 重 量 、尺 寸 和形 状 的 限制 。对 机 械加 工 十分
软件进行 网格划分。网格划分越细 ,计算结果越精 确 。虽然细化网格有助于计算结果的精确性 ,但会 导致 计算时 间过长 。基本模拟思路为 :利用Vi e w
西安文理学院校级大学生创新创业训练计划资助项 目。
象 ,故对铸型刚度有一定要求 ,球化等级需达 四级
以上 ,金 属液 浇 注 前进 行 型 外球 化 处 理 ,铸 件 不 得
C a s t 软 件 预 测铸 件 产生 缩 孔 、缩松 的 部 位和 大 小 , 然后 改 进 和优 化 铸 造 工艺 ,实现 铸 造 工 艺设 计 一 数 值模 拟 验证 一改 进 设计 的 优 化 设计 路 线 ,直 到 模 拟 结果 符 合 工艺 要 求 。
困 难 ,甚 至 难 以 制 得 的 零 件 ,都 可 用 铸 造 方 法 获 得 。铸 造 工 艺 ( 造 型 、造 芯 、浇注 、落 砂 、清 理 及 其后 处 理 等 )是 铸 造 生产 的 核心 ,是 能 否生 产 优 质
数值模拟在铸钢壳体铸件工艺优化中的应用

陷 ,按 比例 作 图法设 计 出 冒 口尺 寸 , 过 利 用 通 浇 注系 统来 对铸 件进 行
一
该铸件为铸钢件 , 铸造收缩率为 2 加工余量 %, 4mm, 水平 分 型 , 工水 玻 璃 砂 造 型 , 箱 一 型 , 手 一 铸 造工 艺 示意 见 图 2 。
收 稿 日期 :0 0 0 — 0 21~42
由于 华铸 C E分 析 系统 是 一 套基 于有 限 差分 A
原理编制的用 于模拟铸造充型凝 固过程的计算机 数值仿真软件 , 分为前置处理 、 计算处理和后 置处 理 三个 相对 独立 的模块 E。 前置处 理模 块 , 照不 在 按 同 的工 艺 方 案导 人 所 需 的组 成部 分 的 S L格式 文 T
定 的补 缩 。远 离浇 注
图 4 原始铸造 工艺 方案
系统 的部 位 用 2个 冒口 来 补 缩 , 寸 101I x 0 l 尺 2 I 20lm。见 图 4 TT I l 。
1 . 熔 化 工 艺 设 计 4
作者简 介 : 袁书仓 (9 2 )男 , 17 一 , 河南宜 阳人 , 工程 师 , 主要 从事铸 造 工艺设计和铸造凝固模拟应用 。
和发 生 的 时 间予 以有 效 的预 测 , 而优 化 铸 造 工 艺 从
1 . 浇 注 系统 设 计 2
根 据 铸 造 工 程
师手册 [, 结合现 场 生 产 经验 , 定 其 浇 确
注 系 统 尺 寸 ,直 浇 道 、 浇道 和 内 浇 口 横
设 计 , 保 铸件 质 量 l。 确 l l 本 设计 通 过采 用 PoE三维 造 型 软件 对 铸 钢壳 r/
2铸 件 的凝 固过程数 值模 拟
21 产 品 实体 建模 .
- 1、下载文档前请自行甄别文档内容的完整性,平台不提供额外的编辑、内容补充、找答案等附加服务。
- 2、"仅部分预览"的文档,不可在线预览部分如存在完整性等问题,可反馈申请退款(可完整预览的文档不适用该条件!)。
- 3、如文档侵犯您的权益,请联系客服反馈,我们会尽快为您处理(人工客服工作时间:9:00-18:30)。
COMSOL Multiphysics钢铁铸造工艺的优化
在所有的工业生产方法中, 主要目标之一是速度的优化。
对于法国不锈钢制造商Ugitech S.A.公司来说,主要的目标就是在保证质量的前提下让连铸机尽可能快速的不间断运转。
然而,如果过早将方形钢坯切分,钢坯断面可能还没有完全固化,含有1.5吨的熔融金属井中的钢水会流入立式连铸机中,会造成毁灭性的灾难。
通过数学模拟,Ugitech公司正在对所生产的150种钢的浇铸温度和浇铸速度进行优化。
固化壳的形成
在铸造过程中,熔融钢水进入锥形铜管模具,并通过外部水循环进行强制冷却。
在这个过程中,固化壳结构要能承受熔融金属形成的静压力。
在成型之后,要进行三次水喷洒过程来增加壳的强度,同时要进行旋转防止膨胀。
最终钢坯通过热辐射冷却下来(图1)。
图1 铸造过程仿真结果。
钢水进入水冷模,并通过传导对流过程实现冷却和固化。
一旦固化壳形成,就可以通过一系列的水喷洒过程实现冷却,而不用依靠热辐射自然冷却。
熔融金属井的长度对于钢绞线的切割位置非常重要。
图中反映了钢绞线的温度分布。
首先通过建模研究的问题是关于钢水早期的固化过程,在这个过程中会导致钢表面出现裂缝和凹陷状振痕等缺陷。
随着壳体冷却,开始收缩并在某些位置出现空隙,如图2。
这些缺陷的位置对钢绞线有着重要影响,而且控制缺陷是非常精细的过程。
如果表面裂缝出现的太早,减弱了壳体部分热量,这时熔融钢液表面开始固化,内部缺陷随之开始出现。
如果裂缝太细,会导致模具形成很尖的锥形,导致钢液与铜模之间的摩擦力增加,过分摩擦力会导致模具下部壳体出现突出。
图2 检查空隙出现情况的模型(左),以及结晶过程中热流和温度模拟结果。
空隙不仅影响热流动和铸体的冷却,还对连铸坯表面有重要影响。
仿真首先要优化各种机器组件的尺寸,如驱动器的线圈和磁铁,并研究它们对连铸过程的影响。
此外,当这两个组件产生单向移动的时候,特别在高频时在结晶器的另一侧平面形成非常复杂的波纹,单向振动会导致声音失真以及振型改变。
要研究当钢水流过连铸器时钢结晶器中的物理过程,只有通过多物理场模拟才能实现。
研究人员选择COMSOL Multiphysics的传热模块和结构力学模块来计算在固化过程中钢坯表面的变形情况,并与实验数据进行对比验证。
接触条件和相变
模型实际包含两个部分。
第一部分是纯热传导模型,可以预测温度和结晶器中的相变,然后第二部分是热机械模型用来深入分析模具和钢坯接触面情况,并解释结晶表面缺陷,如图2。
钢坯和模具之间的非线性接触条件是创建模型过程中一个比较棘手的问题,而且钢水成坯过程还涉及到相变问题。
要研究这些问题,首先要找到每一个钢的热物理参数并添加到模型中。
Ugitech公司的研究人员利用三阶多项式将多年积累的热导率数据添加到COMSOL Multiphysics模型中,但是在临界温度范围内的数据,他们建立了40-100个格点数据的表格,让COMSOL自动插值来推断。
Ugitech公司的研究人员利用COMSOL Multiphysics模型来研究各种冷却条件,在不影响产品质量的前提下提高浇铸速度,并提高最终产品的性能。
研究人员说:“这是一个非常微妙的问题,我们不想拿我们的顾客做实验。
”在汽车和核工业市场中,最终用户会对钢质量作出判断和评价。
因此,加过过程改革需要进行充分的思考和规划,而建模模对于理解和揭示改革提供了非常有价值的可行性参考。
利用模型研究人员也可以评价浇铸机的改进方案。
一时间,生产工程师们都向研究人员询问为了便于维护他们想把二次冷却设备移动几个厘米是否可行。
对于加工过程来说,即使一些非常小的改动,都有可能产生很大的影响,何况是在这么昂贵的机器上做实验。
最终研究人员通过数学模拟证实移动冷却装置不会产生严重的后果。
还有一件事情,模拟帮助避免了一个重大事故。
生产人员想在固化安全线1m以后的地方对钢坯进行切割。
研究人员模拟结果显示,这会导致切割到熔融金属井部分,会带来灾难性的后果。
利用COMSOL仿真,Ugitech公司的研究人员可以更加精确的调整安全线位置,如图3所示。
图3 结晶器中的金属凝固之后才能进行绞线切割。
最终选择COMSOL Multiphysics
Ugitech公司经过大量的考察和慎重考虑之后,最终选择COMSOL Multiphysics,一流的产品一流的服务,远高于其它CAE产品的性价比的COMSOL Multiphysics无疑是Ugitech公司的最佳选择。
虽然他们已经拥有了专业的机械工程软件,研究人员不得不说服管理者购买多物理场工具是一项非常好的投资。
对于Ugitech公司研究人员来说,都想拥有一个能够解决各种问题的多用途工具。
最初的工程中是研究在加热管中移动绞线中的温度分布。
利用COMSOL Multiphysics研究人员模拟得出温度分布,并让管理者知道COMSOL Multiphysics能够很简单很方便的进行这样的模拟。
由于COMSOL Multiphysics能实现多物理场的耦合,研究人员发现了求解问题的新途径。
在使用COMSOL Multiphysics期间,他们的研究成果比以往使用其他任何仿真软件时都多。
这些第一手的仿真结果都会给生产工程师们带来新的想法,同时也会产生新的问题,并鼓励他们想出新的解决问题的方法。
越来越多的人因为Ugitech公司的研究人员在仿真模拟方面的努力而受益。
人们不再问他们“你能计算这个吗?”,而是问他们“如果…会发生什么?”。
COMSOL Multiphysics还能很好的帮助研究人员和顾客交流想法。
COMSOL在中国,中仿科技公司(CnTechCo.,Ltd)凭借个性化的解决方案、成熟的CAE产品线、专业的市场
推广能力以及强有力的技术支持服务赢得了国内众多科研院所以及企业的一致认可,目前国内几乎所有知
名大学以及中国科学院下属各研究所都已选择使用COMSOL Multiphysics作为其科研分析的CAE主要工具。
随着中仿科技公司(CnTechCo.,Ltd)在全国各地的分公司、CAE技术联合中心、CAE培训中心的成立,为广大客户提供更专业、更周到的本地化技术服务,众多企业也纷纷选用COMSOL Multiphysics作为企业的分
析工具,应用全球最先进制造技术,最终增强企业的核心竞争力,保证了企业持续发展。
COMSOL Multiphysics是一款业界领先的科学仿真软件,主要是利用偏微分方程来对系统建模和仿真。
它
的特别之处在于它的多物理场耦合处理能力。
从事专业科学研究的科研人员也可以开发具有专业用户界面
和方程设置的附加模块;现在已经有的模块有化工、声学、地球科学、高频电磁场、准静态电磁场、传热、
微机电系统、结构力学等模块。
软件可以在多种操作系统上使用,包括Windows、Linux、Solaris、HP-UX
等系统。
其他可选软件包有CAD输入模块、以及COMSOL化学反应工程实验室等。
更详细的介绍可参看
中仿科技网站:
关于COMSOL
COMSOL公司是1986年在瑞典斯德哥尔摩成立,现在已经在多个国家(比利时、荷兰、卢森堡、丹麦、
芬兰、法国、德国、挪威、瑞士、英国、美国)成立分公司及办事处。
详细信息请登陆。