铸造工艺的数值模拟优化
轮毂挤压铸造数值模拟与参数优化

C A M E O 凯模C A E 案例库w w w .c a m e o .o r g .c n《热加工工艺》2013年3月第42卷第5期轮毂属于汽车的受力件,承受着汽车的全部质量。
在汽车高速运行过程中,面临着地面的摩擦、碰撞,要求有很好的强度、抗撞击能力;同时,在运行过程中,一直暴露在露天,饱受风吹雨淋,要求有一定的气密性。
总之,服役环境复杂,对其力学性能等都有很高的要求,由此选择铸造成型方法就成了关键。
1轮毂成型工艺试验方法轮毂挤压铸造成型所涉及的工艺参数很多,而每个工艺参数又有多种选择情况,工艺参数组合不同,所铸造出来的轮毂质量也不相同,如果对每种工艺参数组合都做一次试验,则试验次数繁多,甚至试验无法完成。
本文采用正交试验设计法对参数进行试验安排,通过少量试验次数,得出所需要的数据[1]。
正交试验设计,是利用规格化的正交表,恰当的设计出试验方案和有效的分析试验结果,提出最优配方和工艺条件,并进而设计出可能更优秀的试验方案的一种科学方法。
正交表则是利用“均衡搭配”与“整齐可比”这两条基本原理,从大量的全面试验中,为挑选出少量具有代表性的试验点,所制成的排列整齐的规格化表格[2]。
2轮毂成型工艺参数方案的确立挤压铸造不同于其他铸造方式之处是液态合金一直处于压力下直至凝固结束,相对于普通压铸而言,多了一个压力下补缩的过程,挤压压力是其最显著的一个工艺参数,针对38mm 铝合金汽车轮毂,已有较为成熟的挤压力取值为110MPa 。
由于在相同铸造工艺下,镁合金的压力通道阻力比铝合金要大,对于相近形状与体积铸件来说,镁合金应采用比铝合金略高的挤压力[3]。
根据轮毂“挤压压铸”的工艺特性,模具温度和合金液温度对铸件的充型和凝固过程有较大的影响。
初始加压时间以合金液充型完成开始,通过Anycasting 软件自动计算铸件体积与内浇口充型速度的比值得到,与保压时间设定为软件凝固过程模拟结束时自动结束。
3试验过程及结果分析本文针对挤压压力,合金液浇注温度,模具初始温度3个参数,选取的因素和水平表见表1。
材料加工过程数值模拟
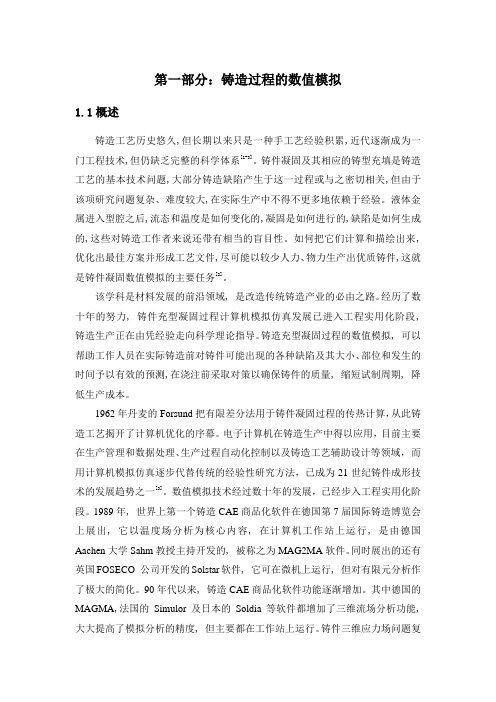
第一部分:铸造过程的数值模拟1.1概述铸造工艺历史悠久,但长期以来只是一种手工艺经验积累,近代逐渐成为一门工程技术,但仍缺乏完整的科学体系[1-3]。
铸件凝固及其相应的铸型充填是铸造工艺的基本技术问题,大部分铸造缺陷产生于这一过程或与之密切相关,但由于该项研究问题复杂、难度较大,在实际生产中不得不更多地依赖于经验。
液体金属进入型腔之后,流态和温度是如何变化的,凝固是如何进行的,缺陷是如何生成的,这些对铸造工作者来说还带有相当的盲目性。
如何把它们计算和描绘出来,优化出最佳方案并形成工艺文件,尽可能以较少人力、物力生产出优质铸件,这就是铸件凝固数值模拟的主要任务[2]。
该学科是材料发展的前沿领域, 是改造传统铸造产业的必由之路。
经历了数十年的努力, 铸件充型凝固过程计算机模拟仿真发展已进入工程实用化阶段, 铸造生产正在由凭经验走向科学理论指导。
铸造充型凝固过程的数值模拟, 可以帮助工作人员在实际铸造前对铸件可能出现的各种缺陷及其大小、部位和发生的时间予以有效的预测,在浇注前采取对策以确保铸件的质量, 缩短试制周期, 降低生产成本。
1962年丹麦的Forsund把有限差分法用于铸件凝固过程的传热计算,从此铸造工艺揭开了计算机优化的序幕。
电子计算机在铸造生产中得以应用,目前主要在生产管理和数据处理、生产过程自动化控制以及铸造工艺辅助设计等领域,而用计算机模拟仿真逐步代替传统的经验性研究方法,已成为21世纪铸件成形技术的发展趋势之一[3]。
数值模拟技术经过数十年的发展,已经步入工程实用化阶段。
1989年, 世界上第一个铸造CAE商品化软件在德国第7届国际铸造博览会上展出, 它以温度场分析为核心内容, 在计算机工作站上运行, 是由德国Aachen大学Sahm教授主持开发的, 被称之为MAG2MA软件。
同时展出的还有英国FOSECO公司开发的Solstar软件, 它可在微机上运行, 但对有限元分析作了极大的简化。
CAE仿真指导铸造关键工艺参数优化设计
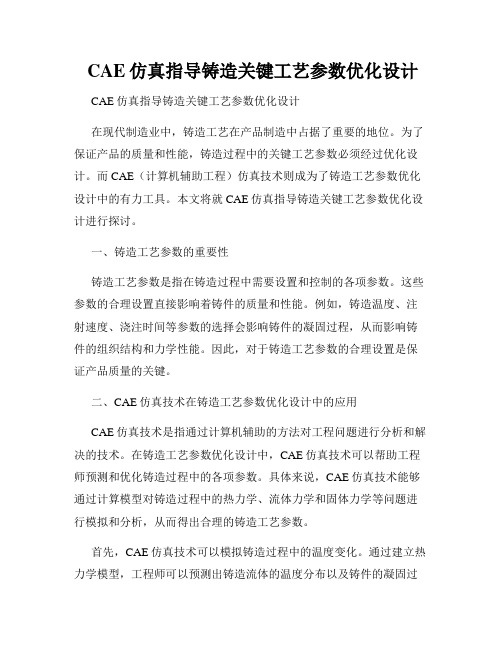
CAE仿真指导铸造关键工艺参数优化设计CAE仿真指导铸造关键工艺参数优化设计在现代制造业中,铸造工艺在产品制造中占据了重要的地位。
为了保证产品的质量和性能,铸造过程中的关键工艺参数必须经过优化设计。
而CAE(计算机辅助工程)仿真技术则成为了铸造工艺参数优化设计中的有力工具。
本文将就CAE仿真指导铸造关键工艺参数优化设计进行探讨。
一、铸造工艺参数的重要性铸造工艺参数是指在铸造过程中需要设置和控制的各项参数。
这些参数的合理设置直接影响着铸件的质量和性能。
例如,铸造温度、注射速度、浇注时间等参数的选择会影响铸件的凝固过程,从而影响铸件的组织结构和力学性能。
因此,对于铸造工艺参数的合理设置是保证产品质量的关键。
二、CAE仿真技术在铸造工艺参数优化设计中的应用CAE仿真技术是指通过计算机辅助的方法对工程问题进行分析和解决的技术。
在铸造工艺参数优化设计中,CAE仿真技术可以帮助工程师预测和优化铸造过程中的各项参数。
具体来说,CAE仿真技术能够通过计算模型对铸造过程中的热力学、流体力学和固体力学等问题进行模拟和分析,从而得出合理的铸造工艺参数。
首先,CAE仿真技术可以模拟铸造过程中的温度变化。
通过建立热力学模型,工程师可以预测出铸造流体的温度分布以及铸件的凝固过程。
根据模拟结果,工程师可以调整铸造温度和凝固时间等参数,以实现理想的凝固结构和性能。
其次,CAE仿真技术可以模拟铸造过程中的流体流动情况。
通过建立流体力学模型,工程师可以预测出浇注过程中的金属液流动速度和压力分布。
根据模拟结果,工程师可以调整注射速度和浇注时间等参数,以优化铸造工艺,避免产生缺陷,提高铸件的质量。
此外,CAE仿真技术还可以对铸件的固态变形进行模拟和分析。
通过建立固体力学模型,工程师可以预测出铸件在凝固和冷却过程中的应力和变形情况。
根据模拟结果,工程师可以调整铸造温度和冷却速率等参数,以减少应力集中和变形产生,提高铸件的整体性能。
三、CAE仿真技术的优势和挑战CAE仿真技术在铸造工艺参数优化设计中具有许多优势。
排气阀壳体铸造工艺的数值模拟优化

李宝治 , 杨 军 z艾秀兰 z ,
(. 1 沈阳铸造研究所, 辽宁 沈 阳 l02 ;. 10 I2大连交通大学 材料科学 一 程学 院, 宁 人连 16 2 ) r 辽 10 8 摘要 : 为消除排气 阀壳体 的渗漏缺 陷 , 利用 Z A T数值模拟软件对 原铸 造工艺 ‘ CS 案进i. _ J 模拟 , 现产牛渗漏的区域属 发
.
a trsn l i e e i n d b t he p e s r d a d n n—p e s r d g tng s se fe im at ng r d sg e oh t r s u e n o r s u e a i y t ms,ha e sn h n t twh n u ig te no —pr s e y tm , esurd s se t mo d iln Wa s o t a t e r n he ul flig s m oh nd h io met e e wa r iig t by, n t e eo e h la a e r b e l lv l s asn sa l a d h r fr t e e k g p o l m o e e uM n i g n h d a i e tWaSs h' .Th o a c b n o lm a e lo S Ie ) sn h o i a d. r ulc ls o ed y e lc ls a big pr b e h sbe n as Ol d 1y u ig c r m t s n ’ e Ke r :nun r lsm ua in; x a tv l u ig; a tn t o y wo ds le a i lto e h us a ̄eho sn c sig me h d
CAE仿真指导优化铸造关键工艺参数设计
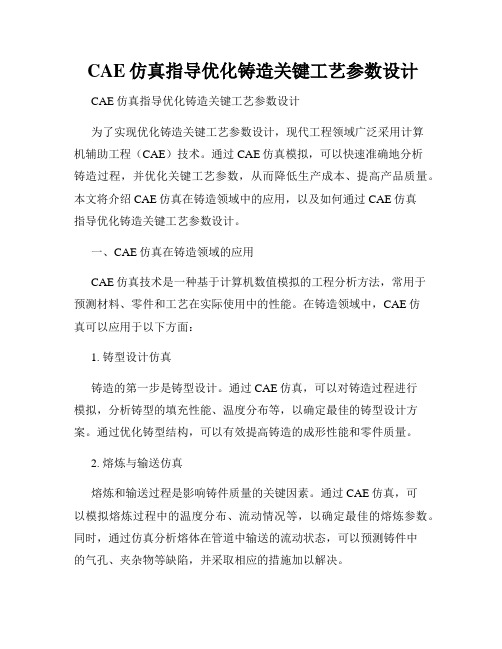
CAE仿真指导优化铸造关键工艺参数设计CAE仿真指导优化铸造关键工艺参数设计为了实现优化铸造关键工艺参数设计,现代工程领域广泛采用计算机辅助工程(CAE)技术。
通过CAE仿真模拟,可以快速准确地分析铸造过程,并优化关键工艺参数,从而降低生产成本、提高产品质量。
本文将介绍CAE仿真在铸造领域中的应用,以及如何通过CAE仿真指导优化铸造关键工艺参数设计。
一、CAE仿真在铸造领域的应用CAE仿真技术是一种基于计算机数值模拟的工程分析方法,常用于预测材料、零件和工艺在实际使用中的性能。
在铸造领域中,CAE仿真可以应用于以下方面:1. 铸型设计仿真铸造的第一步是铸型设计。
通过CAE仿真,可以对铸造过程进行模拟,分析铸型的填充性能、温度分布等,以确定最佳的铸型设计方案。
通过优化铸型结构,可以有效提高铸造的成形性能和零件质量。
2. 熔炼与输送仿真熔炼和输送过程是影响铸件质量的关键因素。
通过CAE仿真,可以模拟熔炼过程中的温度分布、流动情况等,以确定最佳的熔炼参数。
同时,通过仿真分析熔体在管道中输送的流动状态,可以预测铸件中的气孔、夹杂物等缺陷,并采取相应的措施加以解决。
3. 铸造工艺仿真铸造工艺参数对铸件质量起着决定性作用。
通过CAE仿真,可以模拟铸造过程中的铸件填充、凝固过程,分析温度变化、应力分布等,以指导优化铸造工艺参数的设计。
通过合理调整工艺参数,可以降低缺陷率、提高产品质量。
二、CAE仿真指导优化铸造关键工艺参数设计的方法实施CAE仿真指导优化铸造关键工艺参数设计,需要遵循以下步骤:1. 确定铸造关键工艺参数根据具体铸造工艺的特点,确定需要优化的关键工艺参数,例如铸型温度、浇注速度、浇注温度等。
2. 建立仿真模型基于CAE软件,建立铸造过程的仿真模型。
包括铸型结构、材料性质、初始条件等。
3. 设置边界条件根据实际情况,设置仿真模型的边界条件,如环境温度、初始温度、填充时间等。
4. 进行仿真分析运行仿真模型,进行铸造工艺的仿真分析。
《2024年低压铸造铝合金轮毂的数值模拟与工艺优化》范文
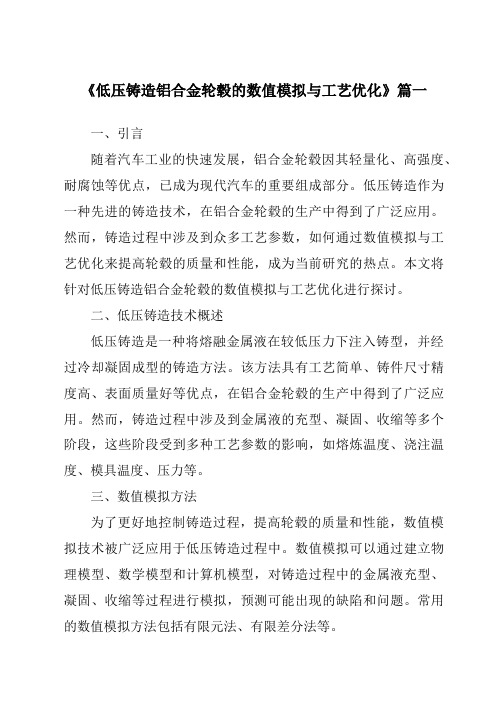
《低压铸造铝合金轮毂的数值模拟与工艺优化》篇一一、引言随着汽车工业的快速发展,铝合金轮毂因其轻量化、高强度、耐腐蚀等优点,已成为现代汽车的重要组成部分。
低压铸造作为一种先进的铸造技术,在铝合金轮毂的生产中得到了广泛应用。
然而,铸造过程中涉及到众多工艺参数,如何通过数值模拟与工艺优化来提高轮毂的质量和性能,成为当前研究的热点。
本文将针对低压铸造铝合金轮毂的数值模拟与工艺优化进行探讨。
二、低压铸造技术概述低压铸造是一种将熔融金属液在较低压力下注入铸型,并经过冷却凝固成型的铸造方法。
该方法具有工艺简单、铸件尺寸精度高、表面质量好等优点,在铝合金轮毂的生产中得到了广泛应用。
然而,铸造过程中涉及到金属液的充型、凝固、收缩等多个阶段,这些阶段受到多种工艺参数的影响,如熔炼温度、浇注温度、模具温度、压力等。
三、数值模拟方法为了更好地控制铸造过程,提高轮毂的质量和性能,数值模拟技术被广泛应用于低压铸造过程中。
数值模拟可以通过建立物理模型、数学模型和计算机模型,对铸造过程中的金属液充型、凝固、收缩等过程进行模拟,预测可能出现的缺陷和问题。
常用的数值模拟方法包括有限元法、有限差分法等。
四、工艺优化策略针对低压铸造铝合金轮毂的工艺优化,主要从以下几个方面进行:1. 优化熔炼工艺:通过调整熔炼温度、合金成分等参数,获得具有良好流动性和充型的金属液。
2. 优化浇注工艺:通过调整浇注温度、浇注速度等参数,控制金属液的充型过程,避免产生气孔、缩松等缺陷。
3. 优化模具设计:根据轮毂的结构特点和使用要求,设计合理的模具结构和尺寸,以提高轮毂的尺寸精度和表面质量。
4. 引入先进技术:如引入机器人自动化技术、在线检测技术等,实现铸造过程的自动化和智能化,提高生产效率和产品质量。
五、实例分析以某铝合金轮毂为例,通过数值模拟技术对其低压铸造过程进行模拟,分析不同工艺参数对轮毂质量和性能的影响。
在此基础上,对熔炼工艺、浇注工艺和模具设计进行优化,得到一组较佳的工艺参数。
铸造过程仿真及优化方法的研究
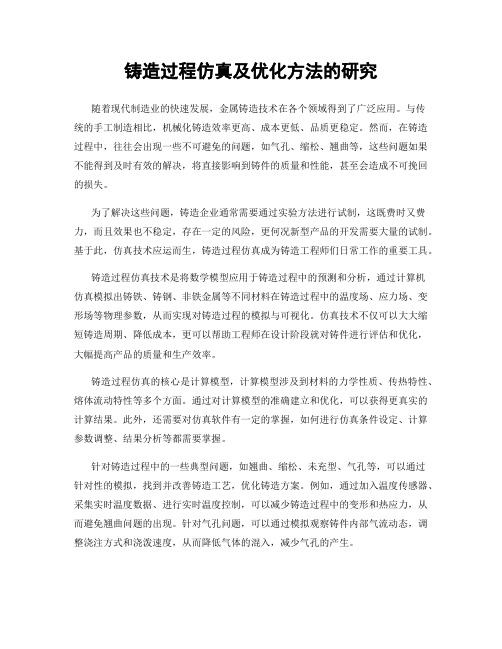
铸造过程仿真及优化方法的研究随着现代制造业的快速发展,金属铸造技术在各个领域得到了广泛应用。
与传统的手工制造相比,机械化铸造效率更高、成本更低、品质更稳定。
然而,在铸造过程中,往往会出现一些不可避免的问题,如气孔、缩松、翘曲等,这些问题如果不能得到及时有效的解决,将直接影响到铸件的质量和性能,甚至会造成不可挽回的损失。
为了解决这些问题,铸造企业通常需要通过实验方法进行试制,这既费时又费力,而且效果也不稳定,存在一定的风险,更何况新型产品的开发需要大量的试制。
基于此,仿真技术应运而生,铸造过程仿真成为铸造工程师们日常工作的重要工具。
铸造过程仿真技术是将数学模型应用于铸造过程中的预测和分析,通过计算机仿真模拟出铸铁、铸钢、非铁金属等不同材料在铸造过程中的温度场、应力场、变形场等物理参数,从而实现对铸造过程的模拟与可视化。
仿真技术不仅可以大大缩短铸造周期、降低成本,更可以帮助工程师在设计阶段就对铸件进行评估和优化,大幅提高产品的质量和生产效率。
铸造过程仿真的核心是计算模型,计算模型涉及到材料的力学性质、传热特性、熔体流动特性等多个方面。
通过对计算模型的准确建立和优化,可以获得更真实的计算结果。
此外,还需要对仿真软件有一定的掌握,如何进行仿真条件设定、计算参数调整、结果分析等都需要掌握。
针对铸造过程中的一些典型问题,如翘曲、缩松、未充型、气孔等,可以通过针对性的模拟,找到并改善铸造工艺,优化铸造方案。
例如,通过加入温度传感器、采集实时温度数据、进行实时温度控制,可以减少铸造过程中的变形和热应力,从而避免翘曲问题的出现。
针对气孔问题,可以通过模拟观察铸件内部气流动态,调整浇注方式和浇泼速度,从而降低气体的混入,减少气孔的产生。
除了利用仿真技术进行铸造工艺优化,还可以结合多项优化策略,如优化铸造设计、改进模具结构、采用提高材料液态流动性能的铸造材料等,综合提高铸造产品的质量和生产效率。
总之,铸造过程仿真技术的应用可以大大降低铸造过程中的损失,提高产品质量,同时节约时间和成本,是铸造生产过程中不可或缺的重要工具。
数值模拟在后桥壳体铸造工艺优化中的应用

铸
・Hale Waihona Puke 造 J n2 1 a .00
V 15 NO 1 o .9 .
4 ・ 2
F UND只Y O
数值 模 拟在 后 桥 壳体 铸 造 工 艺优 化 中的应用
袁 书仓 ,张佳伟 ,汤明健
(. 1 中国一拖集 团有 限公司工艺材料研 究所 ,河南洛阳 4 10 ;2 沈阳铸造研 究所 ,辽宁沈阳 10 2 ) 7 04 . 10 2
s l ic t n p o e swa a r d o t sn a h oi f a i rc s s c ri u ig Hu z u CAE s f di o e u ot r . ru ht e c m p r o fl ud wa e Th o g h o a i n o q i s i p a e d n m i i r u in c u s u ig s l ic t n r c s n e ie e tc sig t c nc I h s y a c ds i t o re d r oi f a i po e s u d r df r n a t e h ia tb o n di o n
c n i n 。v r u e d n is o h i k g e e t o m i g c n e f r c s e .T e s r k g o dt s a i s t n e ce f s r a e d f c s f r n a b o e a t d i o o n h hi a e n d s r u i n a d t c nc I i l f h a t g n e i e e t a t g p o e s s we e c m p r d a d iti t n h i a ed o e c s i s u d r f r n s i r c s e r o b o e y t n d c n ae 。 n
- 1、下载文档前请自行甄别文档内容的完整性,平台不提供额外的编辑、内容补充、找答案等附加服务。
- 2、"仅部分预览"的文档,不可在线预览部分如存在完整性等问题,可反馈申请退款(可完整预览的文档不适用该条件!)。
- 3、如文档侵犯您的权益,请联系客服反馈,我们会尽快为您处理(人工客服工作时间:9:00-18:30)。
两端的冒口
图5 3#浇注系统模型 Fig.5 No.3 model of pouring system
图6 3#浇注系统缩孔缺陷预测 Fig.6 Shrinkage hole prediction of No.3
艺 参 数 : 浇 注 温 度 为825 ℃, 浇 注 时 间 为15 s, 水 平 分 型。
浇注时间15 s, 采用水平分型 。应用表明, 铸造模拟软件能够准确地预测充型凝固过程中可能产生的缺陷, 从而辅助 工艺
人员进行工艺优化。
关键词: 凝固模拟; 军用汽车转向臂; 铸造工艺优化; 浇冒口系统; 缩孔; 铸造模拟软件
中图分类号: TG250.6
文献标识码: A
文章编号: 1004- 244X( 2006) 06- 0051- 03
度 ; t为 时 间 ; P为 金 属 液 体 内 压 力 ; μ为 金 属 液 动 力 粘
度; gx、gy、gz为x、y、z方向重力加速度。 铸造充型模拟计算的过程实质上是求解式2、式3的
过程, 模拟计算可分为以下几个步骤。几何数据文件读
入, 利用MAGMA软件中的预处理模块, 将有UG制作的三
维造型的几何数据文件读入, 生成用于MAGMA软件计算
经过数值模拟显示, 在凝固后期1#浇注系统有宏观 缩孔出现, 2#和3# 浇注系统纠正了宏观收缩, 3#浇注系 统进一步改善了铸件端部质量, 并且不需要横浇道。2# 浇 注 系 统 工 艺 出 品 率 大 约71%, 3#浇 注 系 统 工 艺 出 品 率大约77%, 因此, 3#浇注系统是比较经济的设计方法。
1 铸造过程充型数值模拟方法
军 用 汽 车 转 向 臂 的 几 何 实 体 造 型 采 用 UG软 件 建 立, 在得到三维几何数据后, 利用UG软件的反向出模模 块, 通过设定铝合金收缩率、铸件起模斜度、浇注系统的 位置和分型面等, 作为凝固模拟的几何模型。由于金属 液充型过程数值模拟技术所涉及的控制方程多而复 杂, 需要根据连续性方程、动量方程及能量方程, 并进
直浇道 横浇道
图1 1#浇注系统模型 Fig.1 No.1 model of pouring system
图2 1#浇注系统缩孔缺陷预测 Fig.2 Shrinkage hole prediction of No.1
加冒口
图3 2#浇注系统模型 Fig.3 No.2 model of pouring system
铸造数值模拟是要通过对铸件充型凝固过程的数 值计算, 分析工艺参数对工艺实施结果的影响, 便于技 术人员对所设计的铸造工艺进行验证和优化, 以及寻 求工艺问题的尽快解决办法。为技术人员设计较合理 的铸件结构和确定合理的工艺方案提供了有效的依 据, 从而避免传统的依靠经验进行结构设计和工艺制 定的盲目性, 节约试制成本[1-4]。
用砂型铸造工艺热处理后进行机加工。
2 充型模拟与结果分析
转向臂是军用汽车上重要部件, 材料是A354铝合 金, 由于该铸件壁较厚, 且壁厚差很大, 对铸件内在质量 要求极高, 如果铸造工艺不合理往往会在厚大部位产生 集中缩孔和分散缩松。因此对于壁很厚且壁厚差大的铸 件, 同时又是承受载荷的关键部件, 如何避免壁厚部位 的内部缩孔, 就成了制定铸造工艺的关键。下面对转向 臂的三种不同浇注系统工艺方案进行凝固模拟, 根据 凝固模拟结果显示的缺陷及内部缩松情况, 为了表述 方便将三种浇注系统分别命名为1#、2#、3#工艺模型。
根据国内外的生产经验, 1#浇注系统 采 用 底 注 式
( 如图1所示) , 水平分型, 一般认为这样将避免卷气且 充型平稳, 有利于杂质上浮, 从而减少内部缺陷。传统 的观点认为, 这种方案会导致充型紊流, 甚至卷气且不 利于氧化皮等杂质的上浮, 有可能增加其他部位的缺 陷 。 在 此 模 型 的 基 础 上 利 用 MAGMA软 件 进 行 模 拟 仿 真, 判定该方案的优劣, 模拟计算结果如图2所示。从图 2中可以直观地看出产生缩孔的位置, 红颜色表示在铸 件凝固后期, 由于热节部位无法得到足够补缩, 导致产 品存在较严重的缩孔缺陷倾向, 而且缩孔处于转向臂 承受载荷的厚大部位, 很容易在交变载荷作用下断裂。
兵器材料科学与工程
第 29 卷
量热容, qv为内热源项。 熔融金属充型与凝固过程为高温流体于复杂几何
型腔内作有阻碍和带有自由表面的流动及向铸型和空
气的传热过程。该物理过程遵循质量守恒、动量守恒
和能量守恒定律, 假设液态金属为常密度不可压缩的
粘性流体, 并忽略湍流作用, 则可以采用连续、动量、体
积函数和能量方程组描述这一过程, 式( 3) 是三维方向
Abstr act: In order to study and predict the influence of casting process on castings quality, the rational pouring system and pro cess parameters are set. Three kinds solidification simulation scheme have been applied with the help of simulation software. Re- sults and appearance defects and inner shrinkage porosity of the castings in trial production have been based upon to bring for- ward different technology improvements and select an optimal project used in batch production. Research results show that no.3 castings structure is reasonable, the most reasonable pouring temperature is 825 ℃, pouring time is 15 s. The application shows that the software can help technologists to optimize casting process by forecasting casting defects during mold filling and solidi- fication processes and instruct the production of casting. Key wor ds: solidification simulation; steering arm component used in heavy military truck; casting process optimization; pour- ing and riser system; shrinkage; casting simulation software
Optimization of casting pr ocesses based on computer numer ical simulation
HU Hong- jun, YANG Ming- bo, GONG Xi- bing, LI Guo- rui
( Chongqing Institute of Technology, Chongqing 400050, China)
第 29 卷 第 6 期 2006年 11 月
兵器材料科学与工程 ORDNANCE MATERIAL SCIENCE AND ENGINEERING
Vol.29 No.6 Nov., 2006
铸造工艺的数值模拟优化!
胡红军, 杨明波, 龚喜兵, 李国瑞
( 重庆工学院 材料科学与工程学院, 重庆 400050)
摘 要: 为了研究和预测铸造工艺对铸件质量的影响, 设置合理的军用汽车转向臂的铸造浇冒口系统和工艺参数。应用铸
造模拟软件对转向臂的三种不同工艺方案进行凝固模拟, 根据凝固模拟结果显示的缺陷及内部缩松情况, 提出改进工艺
方案并对其进行凝固模拟, 选择最佳方案应用于生产。研究表明, 3#是最合理的浇冒口布置方式, 最优的浇注温度825 ℃,
行速度场、压力场的反复迭代, 计算量大而且迭代容易
发散, 致使其难度很大。通过不断完善数值计算方法,
如有限差分法和SOLA- VOF 体积函数法, 开发出一些
实用软件。该产品的凝固模拟就是采用MAGMA软件。
作为整个模拟的核心部分, CAE的数值模拟效果最终
将影响模拟的真实与否。在液态金属浇注过程中, 热
传导过程计算是数值模拟的主要内容。处理热传导问
题采用傅里叶定律( 式1) , 式2是根据能量守恒定律推
导的方程[5- 8] 。
q=- λ!t
( 1)
!n
ρc !t = !τ
! !x
(
λ!t !x
)
+
! !y
(
λ!t !y
)
+
! !z
(
λ!t !z
)
+qv
( 2)
其中q为热流密度, λ为导热系数, t为温度( 函数) ,
的几何图形。然后加上INLET( MAGMA软件计算的入口
点) , 调整各部分的材质, 调整相对顺序, 将全部数据保
存在1个文件中。进行网格剖分, 选择ENMESHMENT,
进入网格剖分。确定模拟边界参数, 该类参数主要根
据工厂实际生产同类工艺的参数来初步确定。材料选
择, 汽车转向臂要求没有气孔, 材料为铝合金A354, 使
为了消除缩松, 3#浇注系统采用顶注 式 浇 注 系 统 ( 图5) , 直浇道在铸件最厚处的中心, 并且在容易产生分 散式缩松的位置增加2个冒口。图6是流场和温度场的模 拟状况, 原来发生集中缩孔缺陷的部位是铝液的最后流 经的部位, 但现在是最后凝固的部位, 因此得以补缩。冒 口距离直浇道短, 铝液温度降低不大, 因而补缩效果将 得到极大地提高, 缩松严重程度得到较好的改善。在实 际生产中, 还可以借助保温涂料的作用, 在冒口和铸件 顶部涂上保温涂料, 从而进一步提高冒口的补缩效果, 因而实际采用顶注式是最好的浇注系统。主要铸造工