06_2定位误差定性分析
2.4定位误差的分析与计算(一)

3.以圆孔定位时的定位误差计算
LOGO
Page 23
作业
LOGO
Page 24
复习
工件以圆柱面定位:
固定V型块:限制自由度(长4、短2) 标准化 活动V型块:限制自由度(短1) 标准化
定 位 套:限制自由度(长4、短2)
半 圆 套:限制自由度(长4、短2)
工件以特殊表面定位:
圆锥面定位:固定V型块定位,限制自由度(长4、短2) 锥度轴、套定位,限制自由度(长5、短3) 燕尾导轨定位:限制自由度(5) 齿面定位:限制自由度(长4、短2)
△Y =Xmax=TD + Td + Xmin
LOGO
2.4 定位误差的分析与计算
3.定位误差计算实例
1.
LOGO
Page 21
2.4 定位误差的分析与计算
2.
LOGO
Page 22
课堂小结
1.定位误差的概念
(1)基准不重合误差 △ B (2)基准位移误差 △Y
2.工件以平面定位误差计算
精基准平面定位时,一般认定△Y=0, △D=△B
LOGO
2.4 定位误差的分析与计算
基准不重合误差的计算公式
B i cos
i 1
n
i
——定位基准与工序基准间的尺寸链组成环的公差(包含位
置公差)(mm);
—— i 的方向与加工尺寸方向间的夹角(°)。
LOGO
2.4 定位误差的分析与计算
基准不重合误差练习
习题集P11-3 如图所示工件的加工工序 是镗D孔。如果定位基准分别 选择E、F、G,加工尺寸A的 定位误差分别是多少?
方向上的最大变动量,以“Δ D”表示。 成批加工工件时,夹具相对机床的位置及切削运动的行程调定后
第二章误差分析讲解

第三节 有限测量数据的统计处理
一、偶然(随机)误差的正态分布
同一矿石样品的n次测定值:
23
y
测量值的波动符合正态分布
y
1
2
exp
1 2 x源自2
µ -0 +
x(测量值) x-µ(误差)
y 表示概率密度
σ—总体标准偏差,表示数据的离散程度
μ—无限次测量的总体平均值,
即F
s12 s22
s1
s2
P一定时,查 F , f1, f2
注意:f1为大方差的自由度 f2为小方差的自由度
如F F ,则两组数据的精密度不存在显著性差异 ,f1, f2
如F F ,则两组数据的精密度存在显著性差异 ,f1, f2 33
练习
例:在吸光光度分析中,用一台旧仪器测定溶液的
由P 95%, f大 5,f小 3 F表 9.01
F F表 两仪器的精密度不存在显著性差异
34
(二)t检验(准确度显著性检验)
1. x 与µ比较
x
t
n
S
当t≥tα,f 存在显著性差异 当t<tα,f 不存在显著性差异
35
练习
例:采用某种新方法测定基准明矾中铝的百分含量, 得到以下九个分析结果,10.74%,10.77%, 10.77%,10.77%,10.81%,10.82%,10.73%, 10.86%,10.81%。试问采用新方法后,是否 引起系统误差?(P=95%)已知含量为10.77%。
26
2.t一定时,由于f不同, 则曲线形状不同,所包 括的面积不同,其概率 也不同。
27
第2节 定位误差分析与计算.

(A3)=
2(H – h)tanΔα
(A1)
Δdw(A1) = Δjb(A1)+ Δjy
= δA2 + 2(H – h)tanΔα
2.定位误差的计算方法
1)极限位置法(几何作图法)
先根据工件的定位方案,画出工序(设计)基准
相对起始(调刀、限位)基准最大与最小的两个极限
位置,再根据几何关系求出这两个极限位置间的距离,
jy
4 .如图车外圆,要求外圆对内孔有同轴度要求,已知心 0.009 轴直径为 30- - 0.025 ,计算工件内外圆的同轴度的定位误差 △dw。
jy
5.钻孔O,a)为工序图,图b)~f)为不同定位方案,试分别 计算各种方案的定位误差。
求: Δdw(30)= ?
解:分析可知 Δjb(30)≠ 0 ; Δjy(30)≠ 0 得: Δjb (30)= 0.03/2 + 0.02 = 0.035 0.02 Δjy(30)= = 0.014 0 2 sin 45 Δdw(30)= Δjb (30)+ Δjy(30)= 0.049
已知:大圆直径公差为0.03,小圆直径公差为0.02,同轴度误差为0.02,
0.02,同轴度误差为0.02,定位套直径
公差为0.04。 解:分析得 Δjb (30) ≠ 0,Δjy (30) ≠ 0
Δjb (30) = 0.03/2 + 0.02 = 0.035
0.04 0.02 0.01 0.07
Δjy (30) =
Δdw (30)=Δjb (30) + Δjy (30) =0.105
0.03
解:分析 Δjb (59) ≠ 0 ;Δjy (59) ≠ 0
0 . 12 Δjb (59) = 0.04 0.1 2
定量分析的误差及分析数据的处理
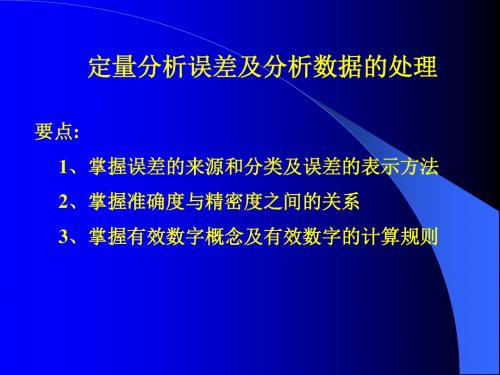
二、减少随机误差 增加平行测定次数 三、消除系统误差 (一)对照试验 —— 检验有无方法误差 1、用标准试样进行对照试验 : 比较测定值与标准值的差异
标准试样的真实值 校正系数 标准试样的测定值
待测组分含量 = 校正系数 待测试样测定值
2、用标准方法进行对照试验 :
对同一样品用标准方法和所选方法进行结果比较
对有限次测定( n < 20 ),S 代替σ ,则平均值的置信区间为:
X
tS n
—— 结果表达式
t : 称为置信因子, 其大小与置信度和自由度( n-1) 有关 ,
见P24 表1 - 4
例:碳原子量的十次平行测定结果如下,计算在95%置信度下平均值的置信 区间 。 12. 0080、 12. 0120、 12. 0095、 12. 0118、12. 0097、 12. 0113 、12. 0101 、 12. 0111 、12. 0106、 12. 0102、
(二)Q 值检验法(适用于n = 3 ~ 10 次)
步骤:1)将数据由小到大排序X1 , X2 , X3 , …, X n 2)求出Q =︱邻差 / 极差︱
3)若Q >Q 表(P26 表1 - 5),则X 舍弃,反之保留
例:在1.11、1.12、1.16、1.12、1.13五个数据中,判断在95%置信度 下1.16 能否舍弃? 解:1)排序 1.11、1.12、1.12、1.13、1.16 2)邻差 = 1.16 - 1.13 = 0.03 , 极差 = 1.16 - 1.11 = 0.05
Sr ,甲
0.9 2 0.7 2 2 0.2 2 4 0.12 0.40 n 1 10 1
2
100 0 0.80
孔定位基准位移误差的分析计算
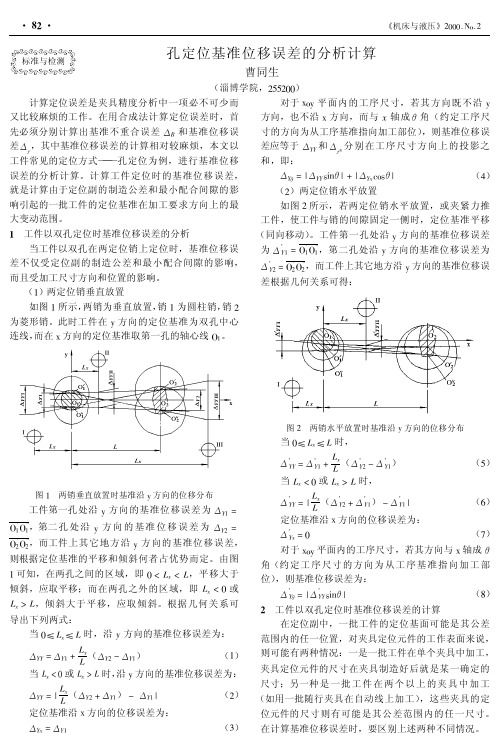
!!!!!!""""标准与检测孔定位基准位移误差的分析计算曹同生(淄博学院,255200)计算定位误差是夹具精度分析中一项必不可少而又比较麻烦的工作。
在用合成法计算定位误差时,首先必须分别计算出基准不重合误差!B 和基准位移误差!y ,其中基准位移误差的计算相对较麻烦,本文以工件常见的定位方式———孔定位为例,进行基准位移误差的分析计算。
计算工件定位时的基准位移误差,就是计算由于定位副的制造公差和最小配合间隙的影响引起的一批工件的定位基准在加工要求方向上的最大变动范围。
!工件以双孔定位时基准位移误差的分析当工件以双孔在两定位销上定位时,基准位移误差不仅受定位副的制造公差和最小配合间隙的影响,而且受加工尺寸方向和位置的影响。
(1)两定位销垂直放置如图1所示,两销为垂直放置,销1为圆柱销,销2为菱形销。
此时工件在y 方向的定位基准为双孔中心连线,而在X 方向的定位基准取第一孔的轴心线01。
图1两销垂直放置时基准沿y 方向的位移分布工件第一孔处沿y 方向的基准位移误差为!Y 1=0’10”1,第二孔处沿y 方向的基准位移误差为!Y 2=0’20”2,而工件上其它地方沿y 方向的基准位移误差,则根据定位基准的平移和倾斜何者占优势而定。
由图1可知,在两孔之间的区域,即0< x < ,平移大于倾斜,应取平移;而在两孔之外的区域,即 x <0或 x > ,倾斜大于平移,应取倾斜。
根据几何关系可导出下列两式:当0# x # 时,沿y 方向的基准位移误差为:!YY =!Y 1+ x(!Y 2-!Y 1)(1)当 x <0或 x > 时,沿y 方向的基准位移误差为:!YY =I x(!Y 2+!Y 1)-!Y 1I (2)定位基准沿X 方向的位移误差为:!Yx =!Y 1(3)对于Xoy 平面内的工序尺寸,若其方向既不沿y 方向,也不沿X 方向,而与x 轴成"角(约定工序尺寸的方向为从工序基准指向加工部位),则基准位移误差应等于!YY 和!yx 分别在工序尺寸方向上的投影之和,即:!Y "=I !YY Sin"I +I !Yx coS "I (4)(2)两定位销水平放置如图2所示,若两定位销水平放置,或夹紧力推工件,使工件与销的间隙固定一侧时,定位基准平移(同向移动)。
定位试验总结分析报告

定位试验总结分析报告
本次定位试验总结分析报告旨在对试验结果进行全面分析,并提出相应的结论和建议。
以下是本次试验的主要内容和分析结果:
1. 实验目的:
本次试验的目的在于评估产品在目标市场的定位效果,以确定其在市场中的竞争优势和消费者认可度。
2. 实验设计:
本次试验采用市场调研方法,通过问卷调查、访谈等方式收集了消费者对产品的意见和反馈。
试验分为两组,分别对比不同的市场定位策略。
3. 实验结果:
根据收集到的数据和统计分析,可以得出以下实验结果:
- 第一组受试者对于产品的理解更加准确,对产品的核心卖点和优势有更清晰的认知;
- 第二组受试者对于产品的认知程度相对较低,对产品的特点和功能理解有误导性。
4. 结论分析:
通过对实验结果的分析,可以得出以下结论:
- 第一组受试者更容易接受产品,因为他们对产品的认知更准确,能够看到产品的实际价值;
- 第二组受试者的认知误导可能导致他们对产品的使用和体验产生偏差,从而影响产品的市场竞争力。
5. 建议:
基于上述结论,提出以下建议来优化产品的定位策略:
- 加强对第二组受试者的产品信息传递,通过更清晰明确的宣传和说明,帮助他们理解产品的实际价值;
- 针对不同消费者群体,采用差异化的定位策略,通过准确传递产品的核心卖点来吸引目标消费者。
总结:
本次定位试验通过市场调研的方式,对产品在目标市场的定位效果进行了评估。
通过分析实验结果,得出了产品定位的有效性和误导性的结论,并提出了优化策略的建议。
这些分析结果和建议有助于产品的市场定位和推广策略的制定,提高产品在市场中的竞争力。
06讲 内孔及心轴定位的定位误差的分析计算

2)当d≠D时(称定位付不准确,因设计、制造原 因产生),O2与O1不重合:
工件向下产生最大平移,即O2相对O1在加工尺寸 方向上向下产生的最大变化量: 1/2(Dmax- dmin) — 1/2(Dmin- dmax)= 1/2 ((T(D)+T(d)),也影 响H1产生误差。
基准位移误差(△db): 因定位付不准确(原因),用调整法加工一批工 件时(条件),引起定位基准在加工尺寸方向上相对 产生的最大变化量(结果),称为基准位移误差。 ※△db为定位基准相对定位基准的max变化量
上述△jb、△db均影响H1,把综合影响称定位 误差△dw。 由图2.39a)知: △dw=△jb+△db。
③对H3:为上下方向,定位基准是O2,工序基 准是B,由图2.39c)知: △jb=△D/2 △db= 1/2 ((T(D)+T(d)) △dw=△db- △jb
可见△db与工序基准变化无关。
⑵结论
①工件定位的任务:a)确定:限制了应该限制的自由度 b)正确:△dw≤1/3T ②△dw产生的原因 a)基准不重合 b)定位付不准确
当工序尺寸为H1时,工序基准A与定位基准O2不 重合,△R直接影响H1 ; 当工序尺寸为H时,工序基准O2与定位基准O2重 合,无这项误差;
基准不重合误差(△jb): 因工序基准与定位基准不重合(原因),用调整 法加工一批工件时(条件) ,引起工序基准相对定位 基准在加工尺寸方向上产生的最大变化量 (结果), 称为基准不重合误差。
自动控制原理误差分析知识点总结

自动控制原理误差分析知识点总结自动控制是现代科学技术的重要组成部分,广泛应用于各个领域。
误差分析是自动控制中的一个关键概念,用于评估实际输出与期望输出之间的差异,并通过相应的控制策略来减小该差异。
本文将对自动控制原理中的误差分析知识点进行总结。
一、误差定义与分类在自动控制中,误差是指实际输出值与期望输出值之间的差别。
根据误差的来源和性质,可以将误差分为系统误差和随机误差两类。
1. 系统误差:指由于系统本身结构、参数、非线性等因素引起的误差,具有一定的规律性和可预测性。
2. 随机误差:指由于外界干扰、测量误差等原因引起的误差,具有无规律性和不可预测性。
二、误差分析方法为了准确评估误差并找到相应的控制策略,可以采用以下常用的误差分析方法。
1. 均方根误差(Root Mean Square Error, RMSE):通过计算误差的平方和的均值再开方得到,用于评估系统的总体误差水平。
2. 最大偏差(Maximum Deviation):指实际输出值与期望输出值之间的最大差异,用于评估系统的极端误差情况。
3. 稳态误差(Steady-state Error):指系统在稳态下输出值与期望输出值之间的差别,用于评估系统的稳定性能。
4. 频域分析:通过对系统的频率响应进行分析,评估不同频率下的误差变化情况,用于优化系统的频率特性。
三、误差补偿控制方法误差分析的目的是找到相应的控制策略来减小误差,常用的误差补偿控制方法包括:1. 比例控制(Proportional Control):根据误差的大小进行比例调整,控制输出与期望输出之间的比例关系。
2. 积分控制(Integral Control):通过积分误差以消除稳态误差,使输出趋于期望输出。
3. 微分控制(Derivative Control):通过对误差的变化率进行调整,改善系统的动态响应特性。
4. 预测控制(Predictive Control):基于模型对未来误差进行预测,提前采取相应控制策略以减小误差。
- 1、下载文档前请自行甄别文档内容的完整性,平台不提供额外的编辑、内容补充、找答案等附加服务。
- 2、"仅部分预览"的文档,不可在线预览部分如存在完整性等问题,可反馈申请退款(可完整预览的文档不适用该条件!)。
- 3、如文档侵犯您的权益,请联系客服反馈,我们会尽快为您处理(人工客服工作时间:9:00-18:30)。
置精度要求高的表面作
粗基准。
图5 不加工表面作粗基准
机械制造技术
(2)选取要求加工均匀的表面为粗基准)
第6章 工件的定位与夹紧
第2节 定位误差定性分析
第 15 页
(2)选取要求加工均匀的表面为粗基准,这 样可以保证作为粗基准的表面加工时,余量均 匀。例如车床床身(动画1),要求导轨面耐磨 性好,希望在加工时 只切去较小而均匀的 一层余量,使其保留
(1) 选取不加工的表面作粗基准
第6章 工件的定位与夹紧
第2节 定位误差定性分析
第 14 页 46
(1)选取不加工的表面作粗基准,如图5所示 ,以不加工的外圆表面作为粗基准,即可在一次 安装中把绝大部分要加工的表面加工出来,又能 够保证外圆面与内孔同轴以及端面与孔轴线垂直 。 如果零件上有好几
个不加工的表面,则应
ε定位=δB+δC 如用H 面作定位基准 (图6c),则 ε定位=δB 如用K 面作定位基准 (图6d),则 ε定位=0
图6
定位误差与定位基准选择的关系
机械制造技术
(2) 基准同一原则
第6章 工件的定位与夹紧
第2节 定位误差定性分析
第 20 页
(2)基准同一原则。位置精度要求较高的某 些表面加工时,尽可能选用同一的定位基准,这
6.2.1 基准分类
第6章 工件的定位与夹紧
第2节 定位误差定性分析
第 2 页 46
在零件和部件的设计、制造过程中,必须 依据一些指定的点、线、或面来确定另一些点 、线或面的位置,这些作为根据的点、线或面, 称为基准。基准按其作用不同,可分为设计基 准和工艺基准。
机械制造技术 1. 设计基准
第6章 工件的定位与夹紧
动画1 床身加工的粗基准
机械制造技术
2. 精基准的选择_(1)基准重合原则
第6章 工件的定位与夹紧
第2节 定位误差定性分析
第 17 页
(4) 选取光洁、平整、面积足够大、装夹稳定 的表面为粗基准。 (5) 粗基准只能在第一道工序中使用一次,不 应重复使用。这是因为,粗基准的表面粗糙,在 每次安装中位置不可能一致,而使加工表面位置 超差。
机械制造技术
第6章 工件的定位与夹紧
第2节 定位误差定性分析
第 21 页
9.42
3/19/2018
视频:定位基准的选择
机械制造技术
第6章 工件的定位与夹紧
第2节 定位误差定性分析
第
页
机械制造技术
第6章 工件的定位与夹紧
第2节 定位误差定性分析
第
页
目 录
6.2 定位误差定性分析
6.2.1 基准分类 6.2.2 定位误差 6.2.3 定位基准的选择
机械制造技术
6.2 定位误差定性分析
第6章 工件的定位与夹紧
第2节 定位误差定性分析
第2节 定位误差定性分析
第 3 页 46
设计时,在零件图纸 上所使用的基准。即在零 件图上用来确定其他点、 线、面位置的基准。如图 1 所示,齿轮内孔,外圆 和分度圆的设计基准是齿 轮的轴线,两端面可以认 为是互为基准。
图1 齿轮
1. 设计基准(续)
机械制造技术
第6章 工件的定位与夹紧
第2节 定位误差定性分析
第 4 页 46
又如图 2所示,表面2、3和孔4轴线的设计基
准是表面1,孔5轴线的设计基准是孔4的轴线。
图2 机座简图
机械制造技术
2. 工艺基准
第6章 工件的定位与夹紧
第2节 定位误差定性分析
第 5 页 46
在制造零件和装配机器过程中采用的基准。 按其用途不同,又可分为测量基准、定位基准和
装配基准。
在使用夹具加工时,除了要求工件安装可靠 、操作方便、调整迅速之外,首要的要求还是保 证加工精度。这是设计夹具结构及决定各项尺寸 公差、形位公差时应该充分考虑的问题。 ●因基准不重合带来的定位误差 定位基准与设计基准不重合时,两个基准之 间的误差会反映到被加工表面上,这类定位误差 有时称为基准转换误差,下面是两种常见的情形.
第6章 工件的定位与夹紧
第2节 定位误差定性分析
第 10 页 46
2
2 sin
2
1 1 k 1 2 sin 2
图4 铣键槽的定位误差
机械制造技术
第6章 工件的定位与夹紧
第2节 定位误差定性分析
第 11 页 46
可以看出,此时轴颈误 差 δ 并非 1:1 地传递给定位 误差△,而需要乘以折算系 数k,k与α有密切关系:
①定位基准。工件在加工时,用以确定工件
对机床及刀具相对位置的表面,称为定位基准。
②测量基准。检验工件尺寸和表面相互位置 时所用的基准。
③装配基准。装配时,用以确定零件或部件
在机器中位置的基准。
本节仅介绍定位基准。
机械制造技术
6.2.2. 定位误差
第6章 工件的定位与夹紧
第2节 定位误差定性分析
第 6 页 46
机械制造技术
2. 精基准的选择_(1)基准重合原则
第6章 工件的定位与夹紧
第2节 定位误差定性分析
第 18 页
2.精基准的选择原则 在第一道工序之后,应当以加工过的表面为 定位基准,这种定位基准称为精基准。其选择原 则如下: (1) 基准重合原则,就是尽可能选用设计基 础作为定位基准,这样可以避免定位基准与设计
α k
120︒ 0.077 90︒ 0.207 60︒ 0.5
图4 铣键槽的定位误差
k随α增大而减小,定位误差也随之减少。但增
加α将使定位时稳定性变坏,因此一般的V型铁常选
α=90︒。
机械制造技术
第6章 工件的定位与夹紧
第2节 定位误差定性分析
第 12 页 46
6.2.3. 定位基准的选择 合理选择定位基准,在保证加工精度、安排 加工顺序和提高加工生产率有着重要的影响。从 定位的作用来看,它主要是为了保证加工表面的 位置精度。因此,选择定位基准的总原则,应该 从有位置精度要求的表面中进行选择。
机械制造技术
1.粗基准的选择
第6章 工件的定位与夹紧
第2节 定位误差定性分析
第 13 页 46
对毛坯开始进行机械加工时,第一道工序只 能以毛坯表面定位,这种基准面称为粗基准。它 应该保证所有加工表面都具有足够的加工余量, 而各加工表面对不加工表面具有一定的位置精度 ,其选择的原则如下:
机械制造技术
样有利于保证各加工表面的位置精度。例如,加
工较精密的阶梯轴时,往往以中心孔为定位基准
车削其他各表面,并在精加工之前还要修研中心
孔,然后以中心孔定位,磨削各表面。这样有利 于保证各表面的位置精度,如同轴度、垂直度等。 (3)基准重合原则。当基准统一原则定位不 能保证加工零件的位置精度时,必须以设计基准 为定位基准。
其中
图4 铣键槽的定位误差
QQ O Q O Q O O OQ O Q
OQ O Q
d
2
d
2
2
机械制造技术
OO O T / sin
则定位误差为
1 1 k 2 sin 2
第 1 页 46
当一批工件逐个在夹具上定位时,它们在夹 具上所占据的位置是有一定差异的。因此会造成 加工尺寸或位置的误差。这种只与定位有关而造 成的加工误差,称为定位误差,用△D表示。定位 误差由两部分组成,即定位基准与设计基准不重 合产生的误差△B和定位副不准确产生的定位误差 △Y。
机械制造技术
基准不重合而引起的误差。
机械制造技术
2. 精基准的选择
第6章 工件的定位与夹紧
第2节 定位误差定性分析
第 19 页
例如,图 6 是轴承座 简图。加工 D 孔时,要求 轴线与 K 面之间的位置尺 A A 寸 0 。M、H 和K 面已 精加工过。 如用M 面作定位基准 ( 图 6b), 则误差可能的最 大值为:
机械制造技术
1. 平面定位
第6章 工件的定位与夹紧
第2节 定位误差定性分析
面,但加工时却
以 B面为定位基面。因此,在实际加工中,是通过
控制铣刀与定位基面B之间的尺寸A而间接获得尺寸
N。即A1、 A2、N构成一工艺尺寸链,其中N为间接 获得的尺寸。由尺寸链可知 δN=δA1+δA2
式中:δA2为
本道工序中加
工误差,δA1
即为基准转换 误差。
机械制造技术
2. V型铁定位 如图 4 所示为铣键
第6章 工件的定位与夹紧
第2节 定位误差定性分析
第 8 页 46
槽时的定位误差。键
槽的深度是由槽底至 轴 下 母线 Q 的 距 离 A 来 控制,此时母线 Q 即为 设计基准,但 V 型铁定
位时,却是以工件与 V
型铁的切点处母线 A 、 C 为基准,因而也会产 生基准转换误差。
图4 铣键槽的定位误差
机械制造技术
第6章 工件的定位与夹紧
第2节 定位误差定性分析
第 9 页 46
设加工是按标准工件( 直径为 d ,圆心为 O )调整的 ,若工件直径有误差,变为
d+δ ,则尺寸由 A 变至 A ', 于是定位误差△为 △=A-A'=QQ'
均匀一致的金相组织
和物理力学性能。
动画1 床身加工的粗基准
机械制造技术
(2)选取要求加工均匀的表面为粗基准)
第6章 工件的定位与夹紧
第2节 定位误差定性分析
第 16 页
若先选择导轨面作粗基准,加工床腿的底 平面(图a),然后再以床腿的底平面为基准加 工导轨面( 图b),就能达到此目的。 (3) 对 于 所 有 表 面都要加工的零件, 应选择余量和公差最 小的表面作粗基准, 以避免余量不足而造 成废品。