精益思想与精益管理
精益思想

精益思想精益思想(Lean Thinking)源于20世纪80年代日本丰田发明的精益生产(Lean Production)方式,精益生产方式造成日本汽车的质量与成本优势,曾经压得美国汽车抬不起头。
世界汽车工业重心已向日本倾斜。
精益思想更进一步从理论的高度归纳了精益生产中所包含的新的管理思维,并将精益方式扩大到制造业以外的所有领域,尤其是第三产业,把精益生产方法外延到企业活动的各个方面,不再局限于生产领域,从而促使管理人员重新思考企业流程,消灭浪费,创造价值。
产生背景二战结束不久,汽车工业中统治世界的生产模式是以美国福特制为代表的大量生产方式,这种生产方式以流水线形式少品种、大批量生产产品。
在当时,大批量生产方式即代表了先进的管理思想与方法,大量的专用设备、专业化的大批量生产是降低成本,提高生产率的主要方式。
与处于绝对优势的美国汽车工业相比,日本的汽车工业则处于相对幼稚的阶段,丰田汽车公司从成立到1950年的十几年间,总产量甚至不及福特公司1950年一天的产量。
汽车工业作为日本经济倍增计划的重点发展产业,日本派出了大量人员前往美国考察。
丰田汽车公司在参观美国的几大汽车厂之后发现,采用大批量生产方式降低成本仍有进一步改进的余地,而且日本企业还面临需求不足与技术落后等严重困难;加上战后日本国内的资金严重不足,也难有大量的资金投入以保证日本国内的汽车生产达到有竞争力的规模,因此他们认为在日本进行大批量少品种的生产方式是不可取的,而应考虑一种更能适应日本市场需求的生产组织策略。
以丰田的大野耐一等人为代表的精益生产的创始者们,在不断探索之后,终于找到了一套适合日本国情的汽车生产方式:及时制生产、全面质量管理、并行工程、充分协作的团队工作方式和集成的供应链关系管理,逐步创立了独特的多品种、小批量、高质量和低消耗的精益生产方法。
1973年的石油危机,使日本的汽车工业闪亮登场。
由于市场环境发生变化,大批量生产所具有的弱点日趋明显,而丰田公司的业绩却开始上升,与其它汽车制造企业的距离越来越大,精益生产方式开始为世人所瞩目。
精益生产管理的核心及五个原则

精益生产管理的核心及五个原则
随着市场经济发发展,企业竞争激烈,精益生产管理已经成为众多企业必不可少的管理方式,便于企业更好的推行精益生产管理。
下面就和小编一起来了解下,精益生产管理的核心及五个原则吧。
一、精益生产管理的核心
精益生产管理的核心是通过持续不断滴排除浪费来赢得利润、创造价值。
二、精益思想五个原则
1.流动——使价值不间断地流动。
2.尽善尽美——永远追求尽善尽美。
3.价值——精确地确定特定产品的价值。
4.拉动——让用户从生产者方面拉动价值。
5.价值流——识别出每种产品的价值流。
精益生产管理是一种以客户需求为拉动,以消除浪费和不断改善为核心,使企业以最少的投入获取成本和运作效益显着改善的一种全新的生产管理模式。
精益生产管理之精益思想学习心得
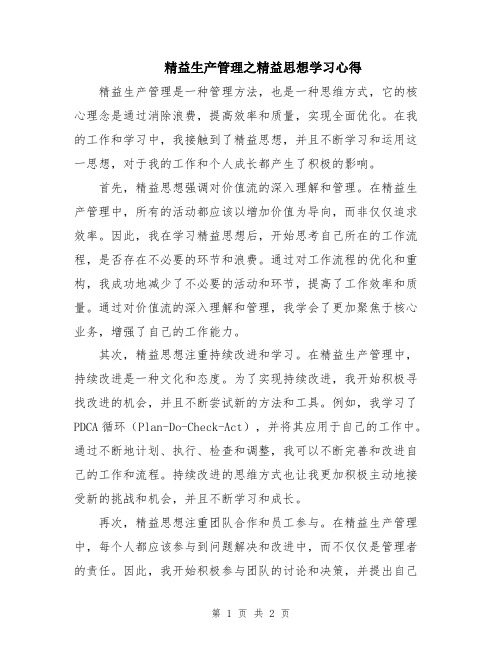
精益生产管理之精益思想学习心得精益生产管理是一种管理方法,也是一种思维方式,它的核心理念是通过消除浪费,提高效率和质量,实现全面优化。
在我的工作和学习中,我接触到了精益思想,并且不断学习和运用这一思想,对于我的工作和个人成长都产生了积极的影响。
首先,精益思想强调对价值流的深入理解和管理。
在精益生产管理中,所有的活动都应该以增加价值为导向,而非仅仅追求效率。
因此,我在学习精益思想后,开始思考自己所在的工作流程,是否存在不必要的环节和浪费。
通过对工作流程的优化和重构,我成功地减少了不必要的活动和环节,提高了工作效率和质量。
通过对价值流的深入理解和管理,我学会了更加聚焦于核心业务,增强了自己的工作能力。
其次,精益思想注重持续改进和学习。
在精益生产管理中,持续改进是一种文化和态度。
为了实现持续改进,我开始积极寻找改进的机会,并且不断尝试新的方法和工具。
例如,我学习了PDCA循环(Plan-Do-Check-Act),并将其应用于自己的工作中。
通过不断地计划、执行、检查和调整,我可以不断完善和改进自己的工作和流程。
持续改进的思维方式也让我更加积极主动地接受新的挑战和机会,并且不断学习和成长。
再次,精益思想注重团队合作和员工参与。
在精益生产管理中,每个人都应该参与到问题解决和改进中,而不仅仅是管理者的责任。
因此,我开始积极参与团队的讨论和决策,并提出自己的观点和建议。
通过与团队成员的合作和交流,我不仅学到了很多新的知识和技能,还培养了良好的团队合作精神和沟通能力。
这些经验也让我意识到,团队合作和员工参与是实现持续改进和优化的重要因素。
最后,精益思想注重长期价值和持续发展。
在精益生产管理中,长期价值才是最重要的,而不是短期利益和效果。
因此,我在工作中开始思考自己的长期发展和职业规划,并与团队和组织保持一致。
通过设定长期目标和规划,我可以更好地寻找和把握机会,为自己的职业生涯铺平道路。
同时,我也明白到,持续发展和学习是实现长期价值和成功的重要途径。
全面质量管理-精益管理

Tianjin | 2012
一、精益管理的基本概念
七种典型的浪费现象:
在企业管理及生产活动中,存在七种典型的浪费,它们 是: 1、过量生产:生产出的产品数量超过顾客的要求,或 生产出未有订单的产品,精益管理强调“在必要的时间, 生产必要数量的必要产品”。 2、等待:作业的过程有空档,在等待下一个作业。 3、运输:包括移动、放置等不增加产品附加价值的运 输等。 4、额外作业:作业浪费分为两种:一种是质量标准过 高造成的浪费,另一种是额外作业过程造成的浪费。
7、返工返修:任何不合格品的产生和修复都是额外的时 间和成本支出,造成浪费。精益管理强调“零缺陷”,控制 不合格品产生的源头。
Tianjin | 2012
一、精益管理的基本概念 七种典型的浪费现象:
精益管理强调将浪费揭示出来,找到浪费的 源头和根本原因,坚持以“人”为本、以“简化” 为手段、以“尽善尽美”为最终目标。以整体优 化的观点,科学、合理的组织和配置企业的生产 要素,彻底消除一切浪费现象 。
Tianjin | 2012
一、精益管理的基本概念
精益管理的核心思想:
精益: 精,即精准,不投入多余的生产要素,只
在适当的时间生产必要数量的市场需要的产品。
益,即所有经营活动都要具有经济效益。
精益管理以消除浪费为核心思想。
Tianjin | 2012
一、精益管理的基本概念
生产过程中的浪费两种:
1、不创造价值,现有技术、生产条件不可避免 (称为Ⅰ型浪费)。 2、不创造价值,可立即去掉的作业活动(称为 Ⅱ型浪费)。
均衡生产
标准作业(Standard Operation) 目视管理(Visual Management) 5S\TPM
精益思想

精 益 思 想
Lean Thinking
2、精益思想的价值观 “ 价值 ” 的通常定义:
古典主义经济学:认为价值和价格并不等同。按照马克思主义
政治经济学的观点,价值就是凝结在商品中无差别的人类劳动,即商 品价值。
新古典主义经济学:物体的价值就是该物体在一个开放和竞争
的交易市场中的价格,因此,价值主要决定于对于该物体的需求,而 不是供给。
精 益 思 想
Lean Thinking
浪费的种类 (2) 等待的浪费 两个相互依存的变量不完全同步导致的时间等待
生产线上不同品种之间的切换,每天的工作 量变动幅度过大,有时很忙,有时造成人员和设 备闲置不用;上游的工序出现问题,导致下游工
序无事可做;生产线劳逸不均。
精 益 思 想
Lean Thinking
1. 生产过剩的浪费
2. 等待的浪费 3. 搬运的浪费
4. 过度加工的浪费
5. 库存的浪费 6. 动作的浪费
7. 纠正错误的浪费
精 益 思 想
Lean Thinking
工作中识别浪费的思维模式
思维模式
工作中有哪些浪费现象 ?
1、人: 2、机: 3、料: 4、法: 5、环: 6、
“ 每时每处都存在浪费
• 不能创造价值而且可以立即去除的活动(Muda2)
精 益 思 想
Lean Thinking
2、价值流图
价值流图是丰田精益生产系统框架下的一种用来描述物流 和信息流的形象化工具,是精益生产用来识别目前和未来的价 值状况,寻求改善机会,设定改善方向和愿景以及行动计划的 工具。
价值流图,是查找和发现浪费的基本工具!
精 益 思 想
Lean Thinking
精益管理理念

精益管理理念精益思想是从顾客端开场,由此往回推,把任何不能为顾客创造价值的活动定义为浪费。
精益管理的目的是通过持续消除浪费、波动与僵化,努力在尽可能最短的时间把价值奉献给顾客。
有些理念是所有精益企业所共通的,这就是我们所谓的精益理念,精益理念中,有些和许多传统组织中流行的理念正好相反。
拉动与推动拉动是主动的思维方式,推动是被动的思维方式。
拉动是为达成目的实现目标而采取的积极行动,是一种在的力量促使事物开展,相反推动那么是在外力的逼迫下被动的做事方式。
两者的效果有什么不同?举一个实例,将一根珍珠项链展开放在桌面上,我们想将这根珍珠项链向一个方向移动一段距离,这个展开的珍珠项链好比一个流程,每颗珍珠是流程的节点,要到达的位置就是流程的目标。
我们拉动与目标方向一样的一段移动会很容易将项链移动到指定位置;如果我们在相反的一段推动项链,结果又将如何呢?这就是拉动与推动效果的不同。
什么是拉动的源?目的与目标、个人追求、工作标准、客户要求等就是拉动我们生活和工作的力量源。
“拉动〞是精益管理中很关键的理念。
“拉动式计划〞是精益生产中物料与计划排产的灵魂,“拉动式计划〞就是计划只下到达最后工序,后工序拉动前工序,而“推动式计划〞那么是前工序推动后工序,这样就不可防止延长生产周期,延误交货。
在工作和生活中拉动的理念至关重要,她决定了工作绩效的大小和人生目标的实现。
根据本人多年对企业的考察和研究,发现多数国人的理念是推动式的,甚至我们的社会机制和企业机制也成为“推动〞理念的温床。
比方我们提倡的“人人平等〞和“政府补助〞导致国人形成依赖心态,不去积极进去,而是坐等别人资助,这样就丧失了自我开展的动力,国营企业的衰败足以说明这个问题。
在日常生活中,很多人说“80后〞“90后〞是一个很头痛的问题,这类人大多追求享受,不愿意辛苦与付出,缺乏责任心和上进心,之所以出现这个结果本人认为与这代人父母的溺爱有很大关系,一味满足他们的低等需求,没有帮助他们树立追求目标,优越的生活条件使他们丧失了进取的动力。
什么是精益管理

精益管理的内涵精益管理要求企业的各项活动都必须运用“精益思维” (Lean Thinking)。
“精益思维”的核心就是以最小资源投入,包括人力、设备、资金、材料、时间和空间,创造出尽可能多的价值,为顾客提供新产品和及时的服务。
精益管理:企业在为顾客提供满意的产品与服务的同时,把浪费降到最低程度。
浪费现象有:错误Defective Parts——提供有缺陷的产品或不满意的服务;积压Inventory——因无需求造成的积压和多余的库存;过度加工Over Production——实际上不需要的加工和程序;多余搬运Transportation——不必要的物品移动;等候Waiting——因生产活动的上游不能按时交货或提供服务而等候;多余的运动Motion——人员在工作中不必要的动作;提供顾客并不需要的服务和产品。
7 Types of Waste•Defective Parts•Over Production•Inventory•Motion•Transportation•WaitingManual Touches由顾客确定产品价值结构1.产品价值结构的涵义。
产品价值结构即产品价值的组成、比例及其价值流程,即某种产品所提供的各种利益、支出及其比例关系以及价值的实现过程。
产品价值结构就是要确定企业的某一种产品具体提供给顾客那些具体的利益,每种利益的数量;还要确定顾客购买产品的各种支出,各种支出的数量;各种利益、支出之间是一种什么样的联系;各种利益和支出是按照什么样的流程来实现产品价值的。
如对一般顾客,家乐福超市免费提供盛物塑料袋,麦德龙的盛物塑料袋却要收费。
这表明家乐福向一般顾客提供盛物塑料袋这一利益,麦德龙不向一般顾客提供该种利益。
其原因是两商家的目标群体不一样,家乐福主要面对一般顾客,而麦德龙主要面对团体顾客。
2.产品价值结构由顾客确定。
在当前信息经济社会的背景下,由于高素质的人才、低成本的信息,先进的技术、成熟的管理模式、顾客的强势购买力等等外部环境因素,企业已具有了经济的满足顾客多样化需求的社会条件。
精益管理知识
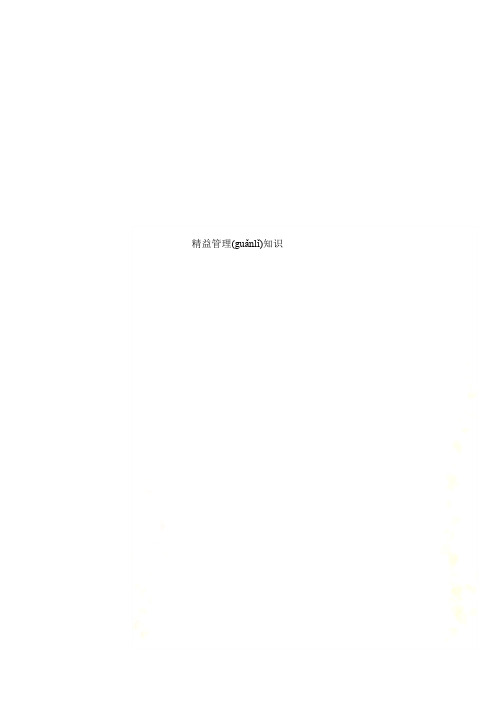
精益管理(guǎnlǐ)知识精益管理(guǎnlǐ)知识集团公司年度工作会明确提出:着眼降本提效,全面引入精益管理的理念和方法,推动管理转型,提升企业应对市场危机的内生竞争力。
为宣贯精益管理的理念和方法,营造推动精益管理的浓厚氛围,淄矿网站特开设“精益讲堂”栏目,普及精益管理基础知识,助大家(dàjiā)明确内涵、把握核心、用好工具,助推精益管理在集团公司落地生根、开花结果。
一、精益管理(guǎnlǐ)的概念“精”就是少投入、少消耗资源、少花时间(shíjiān),尤其是要减少不可再生资源的投入和耗费,高质量。
“益”就是多产出经济效益,实现企业升级的目标,更加精益求精。
精益管理的概念,是以最小资源投入,包括人力、设备、资金、材料、时间和空间(kōngjiān),创造出尽可能多的价值,为顾客提供高质量产品和及时的服务,提高顾客满意度。
精益管理的目标,就是企业在为顾客提供满意(mǎnyì)的产品与服务的同时,把浪费降到最低程度。
精益管理的实质,是精益思想、理念或者思维在生产现场的综合体现;是根据用户需求定义企业生产价值,按照价值流组织全部生产活动,使要保留下来的、创造价值的各个活动流动起来,让用户的需求拉动产品生产,充分暴露出价值流中所隐藏的浪费,不断完善,达到尽善尽美。
精益管理包括生产管理、质量管理、设备管理、安全管理、成本管理、现场管理、人员技能管理、合理化建议、班务公开等9项内容。
精益管理七大浪费是指生产过剩的浪费、等待的浪费、搬运的浪费、不良品的浪费、动作的浪费、库存的浪费、管理的浪费。
二、精益生产现场管理概念1.现场管理五要素是人、机、料、法、环。
2.现场管理六个基本管理目标是Q质量、C成本、D交货期、P生产效率、S安全、M士气。
3.现场管理的优化原则是准时、准确、快速、降低成本、提高效率、系统集成、信息化。
4.现场精益管理(guǎnlǐ)的流程是①当问题发生时,要先去现场;②检查现场,查询原因;③当场采取暂行解决措施;④发掘问题的真正原因并将它排除;⑤标准化处理,以防止问题再次发生。
- 1、下载文档前请自行甄别文档内容的完整性,平台不提供额外的编辑、内容补充、找答案等附加服务。
- 2、"仅部分预览"的文档,不可在线预览部分如存在完整性等问题,可反馈申请退款(可完整预览的文档不适用该条件!)。
- 3、如文档侵犯您的权益,请联系客服反馈,我们会尽快为您处理(人工客服工作时间:9:00-18:30)。
精益思想与精益管理内容安排市场竞争及全球化 精益思想和精益企业 识别和消除7种浪费 价值流分析 实施精益管理1.市场竞争及全球化Shorter lead time and on time delivery 快速并准时交货 Grow the mix,special configurations 需求品种增加,特殊定制 Maintain / improve quality and reduce price 不断改进质量及降低销售价格 Total life cycle of product becoming shorter and shorter 产品的生命周期越来越短 No boundary,business globalize village 无国界,业务“地球村”生命周期及商品种类Life Cycle Change/产品生命周期Life Cycle in year 30 25 20 15 10 5 0 化装品 玩具 机床 食品 药品50 年前 现在Product Styles In Supermarket 超级市场之商品种类60000 40000 20000 0 19701980199020002. 精益思维和精益企业精益生产的起源 精益生产的要点 精益思想五项原则 关注流程 从增值比看改善空间 构筑企业精益之屋精益生产的起源on in the mid – 80’s in the reminder of the industrial world, Lean Manufacturing has become a key strategy for manufacturersStarting with Toyota in the late 50’s and catching起源于20世纪50年代丰田汽车公司,而在80中 期被欧美企业纷纷采用。
随着微利时代的来临, 精益生产模式成为企业竞争的有力武器制造系统演化史Henry Ford • Assembly line mass production • Produce in high volume with low variety • Single skill福特首创的装配线是大规模低品种生产方式的代表, 工人被当成工作的机器Toyota Production System (TPS) • Just-In-Time Production (produce only what is needed) • Pull System • High variety to meet customers wants丰田系统是建立在准时化观念上的拉动 式生产模式,以应付小订单多品种的挑战What Is Lean?精益思想的要点“精益”释义:精益 - 形容词:无肉或少肉,少脂肪或无脂肪, 文体或措词简练 反义词: 肥胖的,多肉的,过重的,不结实的,过分 肥胖的,丰满的,粗短的,肥大的,软的精益思想: 通过消除企业所有环节上的不增值活动,来达到 降低成本、缩短生产周期和改善质量的目的精益思想的五个原则Value 价值Perfect 完美站在客户 的立场上Value Stream 价值流没有任何事物 是完美的 不断改进精益管理从接单到发货 过程的一切活动Demand Pull 需求拉动按需求生产象开发的河流 一样通畅流动Flow 流动降低成本, 改善质量, 缩短生产周期精益思想:关注流程企业的生产流程包括:订单处理、物料计划、采购下单、 供应商备料、运输、来料检验、存储、搬运、加工、检验 和返工、过程等待、成品库存、发运、货款回收等环节订 单 处 理 采 购 下 单 供 应 商 备 料 来 料 检 验 原 料 存 储 搬 运 和 等 待 加 工 检 验 及 返 工 成 品 存 储 成 品 发 运 货 款 回 收运 输制造周期 交付周期 想一想,职能部门的流程?精益思想:时间与影响传统做法供应商 L/T 运送顾客原材料 在制品 成品根据预测 生产/采购根据需求 生产流动制造/精益生产原材料/在制品/成品顾客精益思想:从增值比率看改善空间增值比率 =X 100% 制造周期(Manufacturing cycle time) 增值时间(Value added time)增值时间:站在客户立场看制造过程中的增值动作和时间 如:改变形状、改变性能、组装、包装等物料从进厂到出厂,只有不到 10% 的时间是增值的!构筑精益企业之屋精益企业消除浪费降低成本 库存降低 全 面 生 产 维 护 设 备 总 有 效 性 准时化生产 看板拉动 均衡混流生产 缩短生产周期 小批量生产 作业快速转换 流动生产 设备布局 多技能员工 全 面 质 量 管 理 自 动 化 及 防 错观念转变,消除浪费,价值流管理,团队精神及5S,持续改进观念比较传统理论由生产者决定价值,向用户 推销 分工 流程支离破碎 层级的金字塔 总经理集权 部门职能化、专业化 集中的推式管理 大批量,等待 流程 无间断 扁平结构 赋予职能岗位的决策权 按流程重构的团队或Cell 拉式 不间断的单件流精益思想由最终用户来确定,价值只有 满足用户需求才有存在的意义精益企业的领先优势5年生产效率的提高5.00% 4.50% 4.00% 3.50% 3.00% 2.50% 2.00% 1.50% 1.00% 0.50% 0.00%Electronic & Electrical50% 45% 40% 35% 30% 25%5年一次性合格生产的提高52% 的提高20% 15% 10% 5% 0%Electronic & Electrical40% 的提高Industrial EquipmentHandtools and HardwareControls & MeasuringIndustrial EquipmentHandtools and HardwareControls & Measuring3.00% 2.50% 2.00% 1.50% 1.00% 0.50% 0.00% -0.50% -1.00%Electronic & Electrical5年生产成本的改进650% 的较优广泛应用精益生产技术 稍有应用/不应用Industrial EquipmentHandtools and HardwareControls & Measuring成功企业的应对-精益生产模式美国从80年代开始研究,90年代开始行动,至今在汽车、 航空等行业已经大有成效 1993年美国国防部出台了防务制造企业战略的报告,建议 美国的国有的和私有的军工企业都推行精益制造 同年,美国空军的精益飞机研制计划( Lean Aerospace Initiative ,LAI),大张旗鼓地推行精益制造原则 1998年4月启动了“英国精益航空发展计划(UK Lean Aerospace Initiative ,UK LAI )3.识别和消除所有浪费MUDA – 浪费Anything other than absolute minimum resource of material, machine and manpower required to add value to the product 除了使产品增值所需的材料,设备和人力资源之 绝对最小量以外的一切东西Anything Other Than Necessary 任何非必需的东西!七种浪费1. Overproduction 过量生产(供应) 2. Inventory 库存 3. Conveyance 搬运 4. Correction 缺陷 5. Processing 流程不当 6. Motion 无用动作 7. Waiting 等待4 实施精益管理在各种环境下都会有不同 依赖于“企业文化”的改变步调 一般情况下 (生产企业) 生产试验区 – 3个月 第一个“全方位”的生产车间 – 半年到一年 工厂:4 - 5 年精益征程:准备工作Without INCENTIVE -- Gradual Change 没有原动力 -- 逐步改变 Without VISION -- Confusion 没有愿景 -- 不清不楚 Without ACTION PLAN -- False starts 没有行动计划 -- 难免失败 Without SKILLS -- Anxiety 没有知识 -- 焦虑不安 Without RESOURCES -- Frustration 没有资源 -- 沮丧消沉精益实施之进程危机意识 和实施动力规划与准备当前状态项目管理与执行平衡生产线;生产线设计;培训管理层培训内部组织培训行动计划数据采集 - 当前业务指标 - 产品/工艺 - 批量 / 混线生产 - 流程图 -工作内容 - 差距评估拉动式进度安排;看板 精益商业流程设计持续改进未来状态设计目标流程 和目标测定• 品质改善 •TTPM其它工具和培训(按需要)减少作业准备 6 sigma差错预防• •全员参与的文化5S - 整理工作场地系统化的解决问题方案。