金属粉末涂料的分类及生产工艺
粉末涂料的制备和配方技术
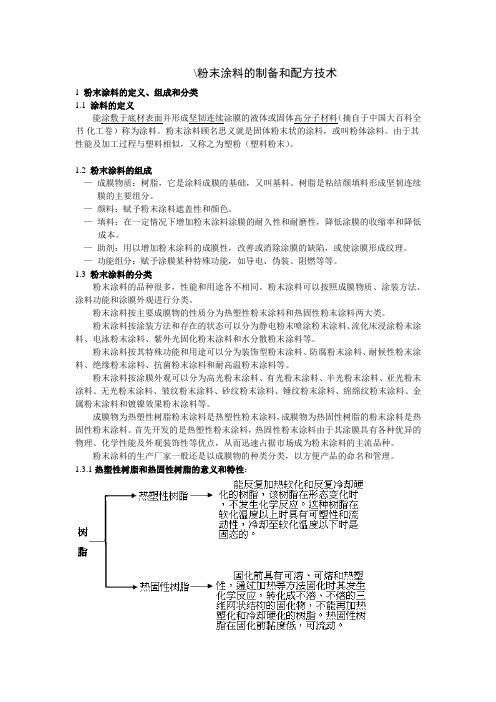
\粉末涂料的制备和配方技术1 粉末涂料的定义、组成和分类1.1 涂料的定义能涂敷于底材表面并形成坚韧连续涂膜的液体或固体高分子材料(摘自于中国大百科全书-化工卷)称为涂料。
粉末涂料顾名思义就是固体粉末状的涂料,或叫粉体涂料。
由于其性能及加工过程与塑料相似,又称之为塑粉(塑料粉末)。
1.2 粉末涂料的组成—成膜物质:树脂,它是涂料成膜的基础,又叫基料。
树脂是粘结颜填料形成坚韧连续膜的主要组分。
—颜料:赋予粉末涂料遮盖性和颜色。
—填料:在一定情况下增加粉末涂料涂膜的耐久性和耐磨性,降低涂膜的收缩率和降低成本。
—助剂:用以增加粉末涂料的成膜性,改善或消除涂膜的缺陷,或使涂膜形成纹理。
—功能组分:赋予涂膜某种特殊功能,如导电、伪装、阻燃等等。
1.3 粉末涂料的分类粉末涂料的品种很多,性能和用途各不相同。
粉末涂料可以按照成膜物质、涂装方法、涂料功能和涂膜外观进行分类。
粉末涂料按主要成膜物的性质分为热塑性粉末涂料和热固性粉末涂料两大类。
粉末涂料按涂装方法和存在的状态可以分为静电粉末喷涂粉末涂料、流化床浸涂粉末涂料、电泳粉末涂料、紫外光固化粉末涂料和水分散粉末涂料等。
粉末涂料按其特殊功能和用途可以分为装饰型粉末涂料、防腐粉末涂料、耐候性粉末涂料、绝缘粉末涂料、抗菌粉末涂料和耐高温粉末涂料等。
粉末涂料按涂膜外观可以分为高光粉末涂料、有光粉末涂料、半光粉末涂料、亚光粉末涂料、无光粉末涂料、皱纹粉末涂料、砂纹粉末涂料、锤纹粉末涂料、绵绵纹粉末涂料、金属粉末涂料和镀镍效果粉末涂料等。
成膜物为热塑性树脂粉末涂料是热塑性粉末涂料,成膜物为热固性树脂的粉末涂料是热固性粉末涂料。
首先开发的是热塑性粉末涂料,热固性粉末涂料由于其涂膜具有各种优异的物理、化学性能及外观装饰性等优点,从而迅速占据市场成为粉末涂料的主流品种。
粉末涂料的生产厂家一般还是以成膜物的种类分类,以方便产品的命名和管理。
1.3.1热塑性树脂和热固性树脂的意义和特性:1.3.2热固性粉末涂料和热塑性粉末涂料的性能特性比较:见下表1-12.热塑性粉末涂料简介热塑性粉末涂料是由热塑性树脂、颜料、填料、增塑剂等经过熔融混合、粉碎、过筛分级得到的。
金属效果粉末涂料制备工艺
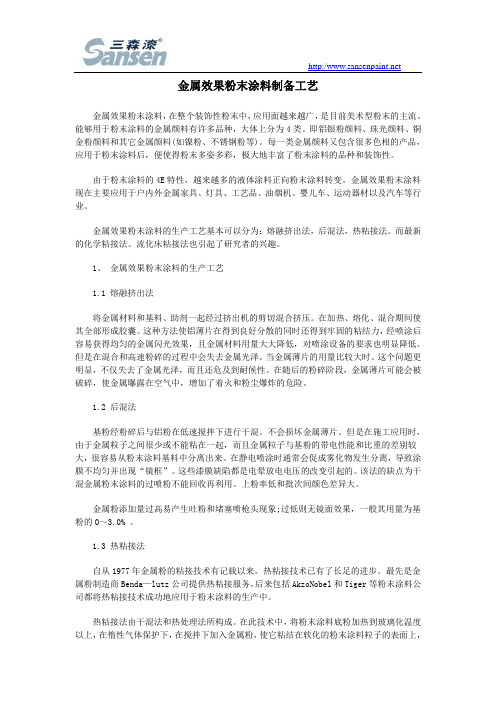
金属效果粉末涂料制备工艺金属效果粉末涂料,在整个装饰性粉末中,应用面越来越广,是目前美术型粉末的主流。
能够用于粉末涂料的金属颜料有许多品种,大体上分为4类。
即铝银粉颜料、珠光颜料、铜金粉颜料和其它金属颜料(如镍粉、不锈钢粉等)。
每一类金属颜料又包含很多色相的产品,应用于粉末涂料后,便使得粉末多姿多彩,极大地丰富了粉末涂料的品种和装饰性。
由于粉末涂料的4E特性,越来越多的液体涂料正向粉末涂料转变。
金属效果粉末涂料现在主要应用于户内外金属家具、灯具、工艺品、油烟机、婴儿车、运动器材以及汽车等行业。
金属效果粉末涂料的生产工艺基本可以分为:熔融挤出法,后混法,热粘接法。
而最新的化学粘接法。
流化床粘接法也引起了研究者的兴趣。
1、金属效果粉末涂料的生产工艺1.1 熔融挤出法将金属材料和基料、助剂一起经过挤出机的剪切混合挤压。
在加热、熔化、混合期间使其全部形成胶囊。
这种方法使铝薄片在得到良好分散的同时还得到牢固的粘结力,经喷涂后容易获得均匀的金属闪光效果,且金属材料用量大大降低,对喷涂设备的要求也明显降低。
但是在混合和高速粉碎的过程中会失去金属光泽。
当金属薄片的用量比较大时。
这个问题更明显,不仅失去了金属光泽,而且还危及到耐候性。
在随后的粉碎阶段,金属薄片可能会被破碎,使金属曝露在空气中,增加了着火和粉尘爆炸的危险。
1.2 后混法基粉经粉碎后与铝粉在低速搅拌下进行干混。
不会损坏金属薄片。
但是在施工应用时,由于金属粒子之间很少或不能粘在一起,而且金属粒子与基粉的带电性能和比重的差别较大,很容易从粉末涂料基料中分离出来。
在静电喷涂时通常会促成雾化物发生分离,导致涂膜不均匀并出现“镜框”。
这些漆膜缺陷都是电晕放电电压的改变引起的。
该法的缺点为干混金属粉末涂料的过喷粉不能回收再利用。
上粉率低和批次间颜色差异大。
金属粉添加量过高易产生吐粉和堵塞喷枪头现象;过低则无镜面效果,一般其用量为基粉的0~3.0% 。
1.3 热粘接法自从1977年金属粉的粘接技术有记载以来。
粉末涂料生产工艺流程
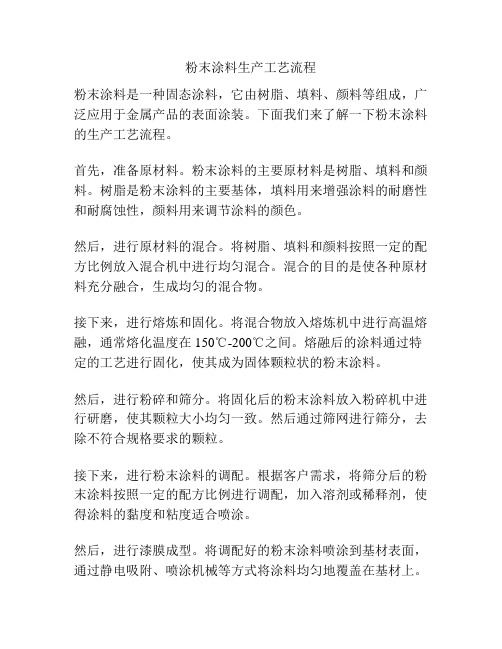
粉末涂料生产工艺流程粉末涂料是一种固态涂料,它由树脂、填料、颜料等组成,广泛应用于金属产品的表面涂装。
下面我们来了解一下粉末涂料的生产工艺流程。
首先,准备原材料。
粉末涂料的主要原材料是树脂、填料和颜料。
树脂是粉末涂料的主要基体,填料用来增强涂料的耐磨性和耐腐蚀性,颜料用来调节涂料的颜色。
然后,进行原材料的混合。
将树脂、填料和颜料按照一定的配方比例放入混合机中进行均匀混合。
混合的目的是使各种原材料充分融合,生成均匀的混合物。
接下来,进行熔炼和固化。
将混合物放入熔炼机中进行高温熔融,通常熔化温度在150℃-200℃之间。
熔融后的涂料通过特定的工艺进行固化,使其成为固体颗粒状的粉末涂料。
然后,进行粉碎和筛分。
将固化后的粉末涂料放入粉碎机中进行研磨,使其颗粒大小均匀一致。
然后通过筛网进行筛分,去除不符合规格要求的颗粒。
接下来,进行粉末涂料的调配。
根据客户需求,将筛分后的粉末涂料按照一定的配方比例进行调配,加入溶剂或稀释剂,使得涂料的黏度和粘度适合喷涂。
然后,进行漆膜成型。
将调配好的粉末涂料喷涂到基材表面,通过静电吸附、喷涂机械等方式将涂料均匀地覆盖在基材上。
然后将喷涂好的基材送入烘干炉中进行高温固化,使粉末涂料形成坚硬、耐候、耐腐蚀的漆膜。
最后,进行质量检验和包装。
对漆膜进行硬度、附着力、耐腐蚀等性能的检测,确保粉末涂料的质量符合标准要求。
然后将成品进行包装和标识,准备发货。
以上就是粉末涂料的生产工艺流程。
通过以上的工艺控制,可以获得高质量、环保、耐候性好的粉末涂料,广泛应用于汽车、家具、建筑等领域。
粉末涂料的详细介绍
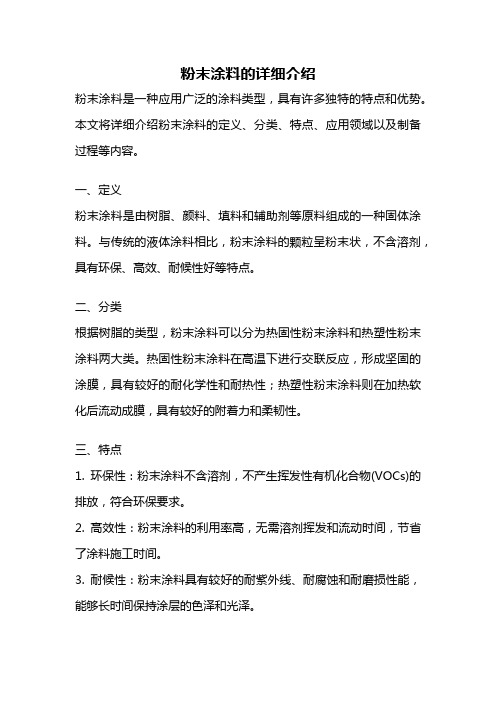
粉末涂料的详细介绍粉末涂料是一种应用广泛的涂料类型,具有许多独特的特点和优势。
本文将详细介绍粉末涂料的定义、分类、特点、应用领域以及制备过程等内容。
一、定义粉末涂料是由树脂、颜料、填料和辅助剂等原料组成的一种固体涂料。
与传统的液体涂料相比,粉末涂料的颗粒呈粉末状,不含溶剂,具有环保、高效、耐候性好等特点。
二、分类根据树脂的类型,粉末涂料可以分为热固性粉末涂料和热塑性粉末涂料两大类。
热固性粉末涂料在高温下进行交联反应,形成坚固的涂膜,具有较好的耐化学性和耐热性;热塑性粉末涂料则在加热软化后流动成膜,具有较好的附着力和柔韧性。
三、特点1. 环保性:粉末涂料不含溶剂,不产生挥发性有机化合物(VOCs)的排放,符合环保要求。
2. 高效性:粉末涂料的利用率高,无需溶剂挥发和流动时间,节省了涂料施工时间。
3. 耐候性:粉末涂料具有较好的耐紫外线、耐腐蚀和耐磨损性能,能够长时间保持涂层的色泽和光泽。
4. 色彩丰富:粉末涂料的颜色多样,可根据需求调配出各种亮丽的色彩,满足不同客户的个性化需求。
5. 膜厚可控:粉末涂料的膜厚可以通过喷涂工艺和条件控制,以满足不同涂装要求。
四、应用领域粉末涂料广泛应用于金属制品、家具、建筑、汽车、电器等行业。
在金属制品领域,粉末涂料可用于防腐、装饰和增加产品表面硬度;在家具领域,粉末涂料可用于木质家具和金属家具的表面装饰和保护;在建筑领域,粉末涂料可用于室内外墙面、门窗等的装饰和防护;在汽车领域,粉末涂料可用于汽车车身、零部件的涂装和防腐。
五、制备过程粉末涂料的制备过程主要包括原料混合、熔融混合、研磨、喷粉和固化等步骤。
首先,将树脂、颜料、填料和辅助剂等原料按一定比例混合均匀;其次,将混合后的原料加热熔融,使其形成均匀的涂料糊;然后,将熔融的涂料糊经过研磨处理,使颗粒粒径适中;接着,将研磨后的粉末通过喷粉设备均匀喷涂在待涂物体表面;最后,将喷涂后的物体置于高温下进行固化,形成坚固的涂膜。
金属表面喷粉工艺

金属表面喷粉工艺一、工艺简介金属表面喷粉是一种将粉末涂料通过特定的喷枪喷射到金属表面上形成一层均匀、耐磨、耐腐蚀的涂层的工艺。
它可以改变金属表面的颜色、质感和性能,增强其抗氧化性、耐磨性和耐腐蚀性。
该工艺适用于各种金属制品,如铁、铝、不锈钢等。
二、工艺流程1. 准备工作(1)清洗:将待处理的金属制品进行清洗,去除表面油污和杂质。
(2)打磨:使用打磨机对金属表面进行打磨,去除表面氧化物和锈迹,使其表面光滑。
(3)除尘:使用吸尘器或压缩空气将金属制品表面的灰尘和杂质彻底清除。
2. 喷涂操作(1)选择喷枪:根据所选用的涂料和需要处理的金属制品选择合适的喷枪。
(2)调整喷枪:根据涂料粘度和颗粒大小调整喷枪的喷嘴和压力。
(3)涂料制备:将所选用的涂料按照一定比例与稀释剂混合均匀,制成可喷涂的液体。
(4)喷涂:将调好的涂料倒入喷枪罐中,将喷枪对准金属制品表面,按下开关开始喷涂。
每一次喷涂应保持相同的距离和速度,以保证涂层的均匀性。
3. 固化处理(1)自然干燥:将已经喷涂好的金属制品放置在通风良好、温度适宜的地方进行自然干燥。
时间根据所选用的涂料种类和厚度而定。
(2)烘干:对于某些需要快速固化的涂料,可以使用烘干机进行加热固化处理。
温度和时间应根据所选用的涂料种类和厚度而定。
4. 检验检查已经固化处理好的金属制品表面是否均匀、光滑,是否有起皮、剥落等现象。
如果出现问题,需要重新进行修补或重新喷涂。
三、注意事项1. 安全操作:在使用喷枪进行喷涂时,应注意安全,戴上防护眼镜、口罩和手套等防护用品。
2. 喷涂环境:喷涂环境应保持通风良好,避免粉尘和有害气体的积聚。
3. 涂料选择:根据金属制品的用途和环境条件选择合适的涂料种类,以确保涂层的耐久性和稳定性。
4. 喷涂技巧:喷涂时应保持相同的距离和速度,以保证涂层的均匀性。
5. 固化处理:固化处理时应根据所选用的涂料种类和厚度控制温度和时间,以确保固化效果。
6. 检验质量:检验已经固化处理好的金属制品表面是否均匀、光滑,是否有起皮、剥落等现象。
金属粉
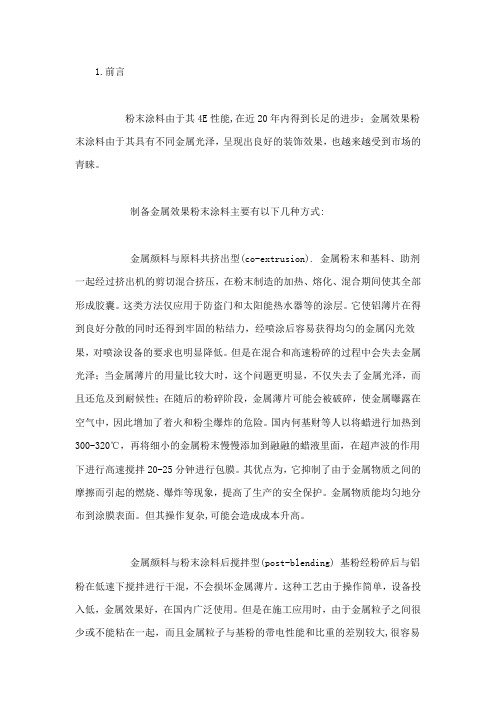
1.前言粉末涂料由于其4E性能,在近20年内得到长足的进步;金属效果粉末涂料由于其具有不同金属光泽,呈现出良好的装饰效果,也越来越受到市场的青睐。
制备金属效果粉末涂料主要有以下几种方式:金属颜料与原料共挤出型(co-extrusion). 金属粉末和基料、助剂一起经过挤出机的剪切混合挤压,在粉末制造的加热、熔化、混合期间使其全部形成胶囊。
这类方法仅应用于防盗门和太阳能热水器等的涂层。
它使铝薄片在得到良好分散的同时还得到牢固的粘结力,经喷涂后容易获得均匀的金属闪光效果,对喷涂设备的要求也明显降低。
但是在混合和高速粉碎的过程中会失去金属光泽;当金属薄片的用量比较大时,这个问题更明显,不仅失去了金属光泽,而且还危及到耐候性;在随后的粉碎阶段,金属薄片可能会被破碎,使金属曝露在空气中,因此增加了着火和粉尘爆炸的危险。
国内何基财等人以将蜡进行加热到300-32 0℃,再将细小的金属粉末慢慢添加到融融的蜡液里面,在超声波的作用下进行高速搅拌20-25分钟进行包膜。
其优点为,它抑制了由于金属物质之间的摩擦而引起的燃烧、爆炸等现象,提高了生产的安全保护。
金属物质能均匀地分布到涂膜表面。
但其操作复杂,可能会造成成本升高。
金属颜料与粉末涂料后搅拌型(post-blending) 基粉经粉碎后与铝粉在低速下搅拌进行干混,不会损坏金属薄片。
这种工艺由于操作简单,设备投入低,金属效果好,在国内广泛使用。
但是在施工应用时,由于金属粒子之间很少或不能粘在一起,而且金属粒子与基粉的带电性能和比重的差别较大,很容易从粉末涂料基料中分离。
在静电喷涂时通常会促成雾化物发生分离,导致涂膜不均匀并出现“镜框”,这些漆膜缺陷都是电晕放电电压的改变引起的。
其缺点为干混金属粉末涂料的过喷粉不能回收再利用,上粉率低和批次间巨大颜色差异。
邦定型(bonded) 又叫热粘接法, 其历史可追溯到1976年,英国五星行金属粉末公司将它叫做机械熔接或邦定的方法,并向市场推广.他是将粉末涂料底粉,加热到玻璃化温度左右,在惰性气体保护下,在搅拌中加入金属粉,使它粘结在软化的粉末涂料粒子的表面上,避免了粘有金属的粉末涂料结块,增加了聚合物的反应活性。
金属型粉末涂料
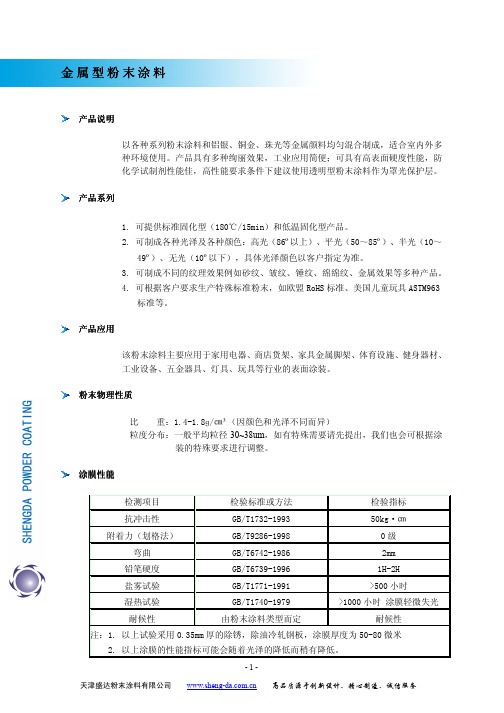
金属型粉末涂料
产品说明
以各种系列粉末涂料和铝银、铜金、珠光等金属颜料均匀混合制成,适合室内外多
种环境使用。
产品具有多种绚丽效果,工业应用简便;可具有高表面硬度性能,防
化学试制剂性能佳,高性能要求条件下建议使用透明型粉末涂料作为罩光保护层。
产品应用
该粉末涂料主要应用于家用电器、商店货架、家具金属脚架、体育设施、健身器材、
工业设备、五金器具、灯具、玩具等行业的表面涂装。
包 装装
纸箱包装,内衬双层聚乙烯塑料袋,每箱净重20公斤。
贮存要求
贮存在低于30℃、通风、干燥、清洁的室内,不得靠近火源、热源,避免阳光直射,
严禁露天堆放。
在此条件下粉末可稳定贮存12个月,超过贮存期可重新进行检验,
如结果符合要求,仍可使用。
卫生与安全
粉末涂料是一种无毒产品,但在使用过程中应避免吸入粉尘。
建议操作人员配戴合
适的防尘口罩、眼镜。
应避免皮肤与粉末涂料的长期接触,附着于皮肤上的涂料可
用肥皂清洗。
浅谈金属铝粉粉末涂料

于高级轿车面漆的涂装方面,只能用于装饰性要求不是 很高的涂装。6结语金属铝粉粉末涂料作为粉末涂料的重 要品种,所有粉末涂料用热固性树脂都可以配制这种粉 末涂料,因此涂料的品种多,应用领域广。如果今后用 于分散铝粉的“邦定”设备价格
下降,并得到普及;再则内加工艺用金属铝粉品种得到 进一步开发,成本又降低,那么各种金属铝粉粉末涂料 的品质将得到提高,价格降低,应用领域将进一步扩大, 使用量会增长得更快,取代溶剂型铝粉涂料的比例会更 大。
料,涂料成膜固化时,由于花纹剂对表面在粉末涂料底粉中添加金属铝粉和锤纹剂而制造 的粉末涂料,涂料成膜固化后形成银色锤纹。(5)金属光 泽纹理粉末涂料,是在粉
末涂料底粉中添加金属铝粉和纹理剂(砂纹剂或皱纹剂)制 造的粉末涂料,涂料成膜固化后,由于铝粉和纹理剂的 作用,形成金属光泽纹理涂膜外观。3金属粉末涂料的制 造工艺金属铝粉粉末涂料的主要制造工艺与一般粉末涂 料的制造工艺差不多,包括
种,可以采用内加或外加两种方法添加进去。花纹剂也 可以采用内加或外加方法加进去。在这种配方中般情况 下不加流平剂,如果需要添加时用量也很少。在配方中 花纹剂和铝粉是影响涂膜外观的重要因素,随着花纹剂 用量的增多,花纹变小,涂膜变平
整,立体感变差;随着铝粉用量的增加,涂膜的金属亮 度增强;铝粉的粒径对涂膜外观也有影响,在同样用量 的情况下,铝粉粒径越小涂膜亮度越亮。另外,成膜物 质的熔融黏度、反应活性、颜填料的品种和用量等因素 对花纹纹理也有一定的影响。4.
量为底粉或配方总量的1%~5%,根据涂膜外观和金属 镀层亮度选择不同粒径和用量的铝粉,使用粒径在2.6~ 15μm的浮型铝粉。目前主要用的铝粉品种为干混合 法外加型的浮型铝粉。已经开发出内加型的铝粉,虽然 有许多优点,但比起
- 1、下载文档前请自行甄别文档内容的完整性,平台不提供额外的编辑、内容补充、找答案等附加服务。
- 2、"仅部分预览"的文档,不可在线预览部分如存在完整性等问题,可反馈申请退款(可完整预览的文档不适用该条件!)。
- 3、如文档侵犯您的权益,请联系客服反馈,我们会尽快为您处理(人工客服工作时间:9:00-18:30)。
金属粉末涂料的分类及生产工艺
金属粉末涂料的分类及生产工艺
一、金属粉末涂料的分类
金属粉末涂料涂膜呈金属光泽,具有绚烂的多色效应以及突出的保护功能,为汽车、家电、仪器仪表等高档工业品提供了绚丽多彩的外观装饰。
目前金属粉末涂料的分类主要根据涂膜外观效果、金属颜料种类或涂膜的功能来进行。
根据涂膜外观的平整度可以分为平面型和纹理型两大类产品。
根据涂膜的外观光泽效果可以将平面型金属粉末涂料分为高光泽、闪光(多彩、随角异色)、金属效应几类,闪光及金属效应类产品目前已推广应用到高级轿车的面涂上;根据涂膜外观的纹理效果可将金属粉末涂料分为锤纹、砂纹、斑纹几类。
根据金属颜料的种类划分。
目前市场能在粉末涂料上广泛应用的金属颜料基本就是铝粉、铜粉和锌粉,主要有德国爱卡(ECKART)、舒伦克(SCHLENK),英国的五星行(Wolstenholme)以及国内少数生产厂家,人们习惯按使用金属颜料相应地将粉末涂料区分为银粉(Al)、金粉(Cu)和富锌粉(也称锌基涂料、Zn)。
根据涂膜的功能主要分为装饰性与防护性两类,装饰性产品有普通装饰性和高装饰性;防护性则有耐候性及防静电(导电)类产品。
二、金属粉末涂料的生产工艺
粉末涂料涂膜金属效果的形成是通过加入金属颜料来实现的,加入的方式主要有两种:熔融挤出法和干混法,在实际生产中二者工艺又进行了不断的改进与完善。
2.1熔融挤出法
刚开始的金属粉末涂料基本是采用熔融挤出法进行生产的,与传统粉末涂料的生产工艺类似,在各种粉末涂料的原料中增添了金属颜料,然后高速预分散、熔融挤出、压片破碎、磨粉筛分,制得成品。
该法工艺简便,金属颜料与粉末基料达到充分的混合与黏结,但由于工艺过程中存在着高温(130℃)挤出、高剪切粉碎,造成金属颜料表面的部分氧化、粒片变形或被粉碎,造成涂膜外观金属颜色灰暗甚至无金属效果。
为了提高涂膜外观效果,金属颜料生产商改进了颜料生产工艺,生产过程中采用惰性气体保护,对金属颜料粒子表面进行覆膜保护处理,显著提高了金属颜料耐高温耐腐蚀的能力;粉末制造商则在研磨成的粉末中再加入少量的金属颜料,然后进行简单干混处理,达到改进产品外观效果的目的。
虽然各方都采取了努力,但最终适宜该法生产的只有少量金属粉末涂料产品,如闪光粉末涂料(微闪银效果)、锤纹粉末涂料。
2.2热混工艺
初期的干混生产工艺就是将金属颜料加入预先加工好的粉末状的基料中,使用高速混合设施进行充分混合分散后成为成品,该法的优点可以将金属颜料很好地分散而不破坏颜料粒子的形状,颜料片的漂浮与定向能力得到充分发挥,涂膜的金属效果突出。
其明显不足是金属颜料粒子与基料粉末粒子两者的物性(如密度、形状)差别较大,且二者没有黏结吸附,在流化、喷涂带电、静电吸附的过程中产生分
离,造成涂膜外观色泽不一,回收粉因金属颜料含量明显增加而难以回收再使用,普遍还存在喷枪枪头积粉、放电击人、烧枪等其他问题。
上述问题促进了干混设备与干混工艺的改进与完善,针对颜料片与基料粉末颗粒分离的问题,技术人员开发了加热混合(热混技术也称邦定技术)的生产工艺,就是将金属颜料与粉末基料加入混料罐(釜)中,往夹套中通入热水或热油对罐(釜)体加热,边混合分散边对材料进行加热,同时采用惰性气体保护措施,在一定的温度下(50~60℃)粉末基料粒子表面逐渐软化并与金属颜料片产生黏附,黏结一定时间后,将物料冷却至常温,然后进行粉体处理,筛分即得成品。
因材料系统有别,不同厂家采用的热混工艺与热混设备有不同,但热混制得的金属粉末涂料产品其涂膜外观效果都有显著改善。
目前热混工艺逐渐臻于成熟,能生产出众多的金属粉末涂料产品,涂膜装饰效果五光十色,应用的范围十分广泛,市场上的销量与日俱增。
三、金属粉末涂料的基本配方设计
金属粉末涂料配方设计涉及的因素很多,主要有产品金属色泽(金属颜料品种)、涂膜美术效果(平面或纹理)、生产工艺(挤出或干混)、固化条件(烘箱或烘道、常温或高温喷涂),上述任一条件的变化都需要对原有配方进行重新设计,一些关键助剂的取舍与用量大小也显著影响着涂膜的外观效果。
在此介绍一下热混工艺的金属粉末涂料的基本配方。
热混工艺的金属粉末涂料有个共同特点,就是配方设计分为两个部分:基料配方与干混配方。
基料配方主要是树脂、固
化剂、流平剂、普通颜填料、常用助剂等,根据产品要求进行材料品种的取舍及用量的调整,有高光类基料、斑纹基料、砂皱基料,将基料部分的原料按配方要求称取后进行高速预分散、熔融挤出、压片破碎、磨粉筛分,制得基料粉末。
干混配方是将金属颜料和各种助剂与基料粉末按比例设计,生产时按配比称取物料,按各类产品设计的工艺参数和流程进行投料、混合、加热、黏结、冷却、粉体处理及筛分等生产操作。
由于该类工艺生产的金属粉末涂料品种众多,仅选择目前用途较广的高光类、效应类、斑纹类、砂纹类进行介绍。
高光类产品基料配方与常规的高光粉末产品配方相比,只是在颜填料的用量上有些区别。
在基料配方中可以添加一定量的颜填料并能保证涂膜良好的镀铬效果,另外为提高金属漂浮效果,基料中还可以加入黏度调节剂,如701增亮剂、W-1等;干混配方中一般只有一种金属颜料,要求漂浮性能优异,如爱卡的ChromaluxⅣ、PC100。
效应类产品与高光类产品比较,只是基料配方可以设计得更加多样化,其借助花色多、成本低、质量稳定的优势占据了主要的金属粉末涂料应用市场。
斑纹基料配方中最明显的特点是没有流平剂。
其中基料黏度的调节十分重要,因为控制黏度有利于金属颜料的上浮也有利于斑纹剂发挥扩散作用,从而获得满意的斑纹效果。
另外由于斑纹的凹凸效果造成凹处涂膜厚度较薄(30~50μm,个别处20μm以下),极易产生露底现象,基料中颜料应为常规用量的2~4倍,这样才能保证凹处涂
膜的颜色与整体一致。
笔者根据自己多年来设计、生产与应用的研究经验,总结认为产品斑纹效果的设计首先要依据产品使用者的涂装条件(包括喷室条件、固化条件以及产品的最终使用环境条件),来确定基料与干混的基本配方构架,如:树脂类型(户内或户外)、金属颜料品种(Al、Cu)、基料黏度要求(颜填料品种与数量、黏度调节助剂),再根据纹理大小与厚度要求去确定金属颜料的用量、基料中颜填料用量、斑纹剂的粒度与用量、表面固定剂的用量,试验确定初步配方,然后再根据干混生产工艺调试,进行物料用量的精确调整,最终确定产品配方。
在以后的重复生产过程中,会遇到材料批次的变换甚至是不同厂家的材料,此时只要认真地分析材料的变化趋势,预测涂膜纹理的变化情况,调节斑纹剂、表面固定剂及金属颜料三者的用量,基本上就可以将纹理效果调节与原来一致。