制氢装置加氢脱毒部分工艺管理和操作规程
制氢操作规程

第一章装置概况第一节装置简介1、概述:为了解决焦化油品加氢精制和柴油加氢精制的氢源问题,同时满足生产清洁燃料的需要,搞好全厂气体资源的综合利用,分公司建设一套20000Nm3/h焦化干气制氢装置。
该装置由中石化北京设计院设计,占地5400m2,预计于2002年10月建成投产,装置的外操室与控制室等建筑与50万吨/年延迟焦化装置和120万吨/年柴油加氢精制装置集中布置,装置规模为20000Nm3/h纯氢,按年开工8000小时,相当于产纯氢1.45万吨/年。
装置采用烃类水蒸汽转化法造气和变压吸附氢气提纯的工艺,该工艺流程简单,成熟可靠,产品氢气纯度高。
装置由原料加氢脱硫、水蒸汽转化、中温变换、PSA氢气提纯及余热回收系统五部分组成。
装置原料为净化焦化干气、重整稳定塔顶气及重整拔头油,产品为工业氢气,产量为20000Nm3/h,主要提供给全厂2.0MPa氢气管网,装置副产品为变压吸附尾气,全部用作转化炉燃料。
装置的主要设备原料气压缩机为往复式两级压缩机,一开一备;转化炉炉型结构为垂直管排顶烧箱式炉,设有Ф127×12×1250的转化炉管112根,分四排平行布置,每排28根,转化炉燃烧器设有40台,与炉管平行布置,分5排,每排8台,该燃烧器操作弹性大,燃烧适应性强,可分别或混烧高压瓦斯、中变气、PSA尾气,结构简单,便于维修,不易回火和堵塞,火焰稳定,刚直有力。
2、装置特点:(1)利用廉价的焦化干气作为主要的制氢原料,采用一次通过式绝热加氢脱硫工艺,流程简单﹑可靠,公用工程消耗低,所得产品氢的成本低。
(2)装置的原料范围具有较强的适应性,以焦化干气作为主原料同时考虑了以拔头油作为备用原料,保证了装置的稳定可靠性。
(3)转化炉废热锅炉与转化气废热锅炉共用一台汽包,自然循环式流程,操作安全可靠并降低了能耗。
(4)转化炉总集气管采用有内衬里的冷壁式,降低了集合管的材料等级,节省了投资;(5)采用PSA技术提纯氢气,使流程比常规法制氢简单,产品纯度高;(6)装置内所产酸性水在装置内的汽提塔汽提后回用作装置锅炉给水或做120万吨/年加氢装置注水,降低了能耗。
制氢操作规程

制氢操作规程
《制氢操作规程》
一、目的
为确保制氢过程安全、高效地进行,避免可能发生的事故和意外,制定本操作规程。
二、适用范围
本操作规程适用于制氢设备的操作人员和相关管理人员。
三、责任与权限
1. 设备操作人员应按照规程进行操作,严格遵守安全生产操作规定。
2. 管理人员有权对操作人员的操作进行监督、检查。
四、操作流程
1. 开始操作前,操作人员应仔细阅读操作手册,熟悉设备的操作方法和安全注意事项。
2. 检查设备是否运行正常,各项参数是否符合要求。
3. 打开制氢设备的电源开关,逐步启动设备。
4. 按照操作手册的要求操作设备,注意观察设备运行状况,及时发现并排除故障。
5. 当设备运行结束后,依次关闭设备各项开关,并进行设备的清洁和维护。
五、安全注意事项
1. 操作人员需佩戴好防护装备,如手套、护目镜等。
2. 禁止在设备运行时进行非相关操作。
3. 禁止随意调整设备参数。
4. 在操作中如发现异常情况,应立即停止设备运行,并报告相关管理人员。
六、紧急事件处理
1. 如果发生设备故障或事故,应立即停止设备运行,并及时向相关管理人员报告。
2. 在紧急情况下,可根据设备紧急停止程序进行操作。
3. 如有人员受伤或生命危险,应立即拨打急救电话,并进行相应的急救措施。
七、培训教育
1. 对新入职的操作人员进行必要的安全培训和操作技能培训。
2. 对现有操作人员进行定期的安全教育和技能培训。
以上就是《制氢操作规程》的相关内容,希望各位操作人员严格执行规程,保障生产安全,确保设备和人员的安全。
加氢装置操作规程
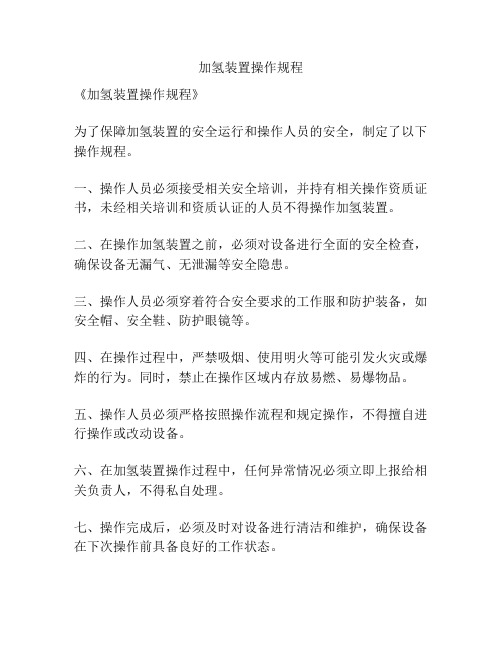
加氢装置操作规程
《加氢装置操作规程》
为了保障加氢装置的安全运行和操作人员的安全,制定了以下操作规程。
一、操作人员必须接受相关安全培训,并持有相关操作资质证书,未经相关培训和资质认证的人员不得操作加氢装置。
二、在操作加氢装置之前,必须对设备进行全面的安全检查,确保设备无漏气、无泄漏等安全隐患。
三、操作人员必须穿着符合安全要求的工作服和防护装备,如安全帽、安全鞋、防护眼镜等。
四、在操作过程中,严禁吸烟、使用明火等可能引发火灾或爆炸的行为。
同时,禁止在操作区域内存放易燃、易爆物品。
五、操作人员必须严格按照操作流程和规定操作,不得擅自进行操作或改动设备。
六、在加氢装置操作过程中,任何异常情况必须立即上报给相关负责人,不得私自处理。
七、操作完成后,必须及时对设备进行清洁和维护,确保设备在下次操作前具备良好的工作状态。
八、操作人员必须遵守相关安全规定和操作指南,严守操作纪律,确保操作过程的安全和稳定。
以上是关于加氢装置操作规程的一些要点,希望操作人员能严格执行规程,确保设备安全运行。
制氢操作规程(终稿)
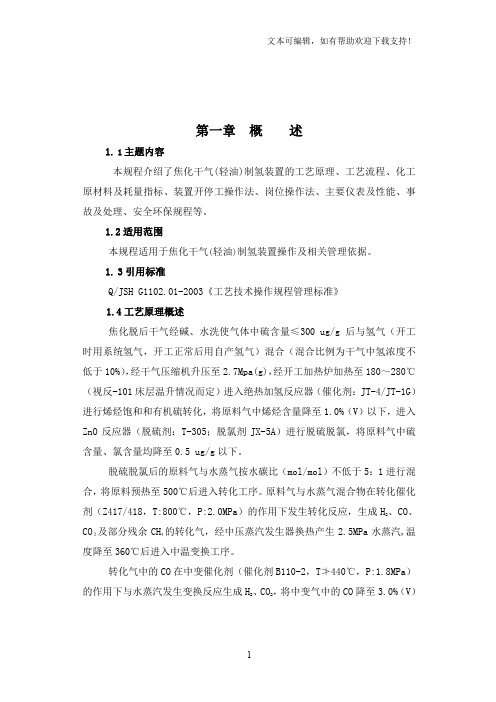
第一章概述1.1主题内容本规程介绍了焦化干气(轻油)制氢装置的工艺原理、工艺流程、化工原材料及耗量指标、装置开停工操作法、岗位操作法、主要仪表及性能、事故及处理、安全环保规程等。
1.2适用范围本规程适用于焦化干气(轻油)制氢装置操作及相关管理依据。
1.3引用标准Q/JSH G1102.01-2003《工艺技术操作规程管理标准》1.4工艺原理概述焦化脱后干气经碱、水洗使气体中硫含量≤300 ug/g后与氢气(开工时用系统氢气,开工正常后用自产氢气)混合(混合比例为干气中氢浓度不低于10%),经干气压缩机升压至2.7Mpa(g),经开工加热炉加热至180~280℃(视反-101床层温升情况而定)进入绝热加氢反应器(催化剂:JT-4/JT-1G)进行烯烃饱和和有机硫转化,将原料气中烯烃含量降至1.0%(V)以下,进入ZnO反应器(脱硫剂:T-305;脱氯剂JX-5A)进行脱硫脱氯,将原料气中硫含量、氯含量均降至0.5 ug/g以下。
脱硫脱氯后的原料气与水蒸气按水碳比(mol/mol)不低于5:1进行混合,将原料预热至500℃后进入转化工序。
原料气与水蒸气混合物在转化催化剂(Z417/418,T:800℃,P:2.0MPa)的作用下发生转化反应,生成H2、CO、CO2及部分残余CH4的转化气,经中压蒸汽发生器换热产生2.5MPa水蒸汽,温度降至360℃后进入中温变换工序。
转化气中的CO在中变催化剂(催化剂B110-2,T≯440℃,P:1.8MPa)的作用下与水蒸汽发生变换反应生成H2、CO2,将中变气中的CO降至3.0%(V)以下,再在低变催化剂(催化剂B202, T≯230℃,P:1.6MPa)的作用下发生同上反应,将低变气中的CO降至0.3%(V)以内,低变气经过一系列的换热分水后进入脱碳工序。
在脱碳塔内,低变气先与再生度较差的脱碳半贫液逆向接触,脱去大部分CO2,然后再与再生度较好的贫液接触将CO2含量降至1.0%(V)以下进入甲烷化工序。
氢气装置安全操作规程

编号:Linkye页码 :1/32 1500Nm3/h甲醇裂解制氢装置操作规程编号:Linkye页码 :2/32第一章工艺简介本装置以甲醇、脱盐水为原料,经预热、汽化、催化转化和冷冻干燥净化,所得转化气,再送入变压吸附装置精制,最后得到纯度≥99.999%的氢气送至用户。
系统操作压力为1.0~1.5MPa,属中低压操作装置,转化裂解反应温度在240~290℃范围,由导热油循环供热。
装置组成本装置包括甲醇罐区、脱盐水工段、导热油工段、甲醇转化工段、变压吸附工段五个主体及装置配电室、控制室、分析检测。
装置的工艺流程如下:编号:Linkye页码 :3/32由于本装置原料及产品均属易燃、易爆危险品,操作过程中必须予以高度重视。
同时本装置操作的稳定性、原料消耗指标、催化剂使用寿命、产品纯度的高低、设备、人员安全等在很大程度上取决于操作水平的高低,因此有关操作、管理和维修人员在装置启动运行之前,必须熟知本操作规程,并经考核合格后才能上岗。
在后面的章节,将分工段介绍。
编号:Linkye页码 :4/32第二章导热油炉房的操作规程一、该部份设备的操作需在物料、气源满足的前提下方可调节,因此该部份在燃烧系统作了联锁之后进行调节;自力式调节阀的调节参数如下:PV501 甲醇阀后压力: 0.4MPaPV502 天然气阀后压力: 0.12MPaPV503 液化气阀后压力: 0.05MPaV559 雾化空气阀后压力: 0.1MPa远传压力开关的调节参数如下:PLS501 新风空气压力低报设定值:3.0KPa,正常值6.0KPaPLS502 PSA解析气压力低报设定值:10.0KPa,正常值30.0KPaPHS502 PSA解析气压力高报设定值:40.0KPa,正常值40.0KPaPLS503 天然气压力低报设定值:50.0KPa,正常值100.0KPaPHS503 天然气压力低报设定值:150.0KPa,正常值100.0KPaPLS504 液化气压力低报设定值:5.0KPa,正常值20.0KPaPLS505 雾化空气压力低报设定值:70.0KPa,正常值370.0KPaPHS505 雾化空气压力高报设定值:520.0KPa,正常值370.0KPa二、操作前先熟悉上位机信号联锁在微机上进行系统内各单体设备的运行控制信号联锁;该燃烧系统共有三组运行控制信号联锁,联锁单体设备如下:压力信号联锁一:PIAS504新风空气压力正常值2~5 KPa,报警值L:2.0KPa、LL:1.5.0KPa,联锁关闭SNV501a/b、SNV502a/b、SNV503a/b。
加氢操作规程完整
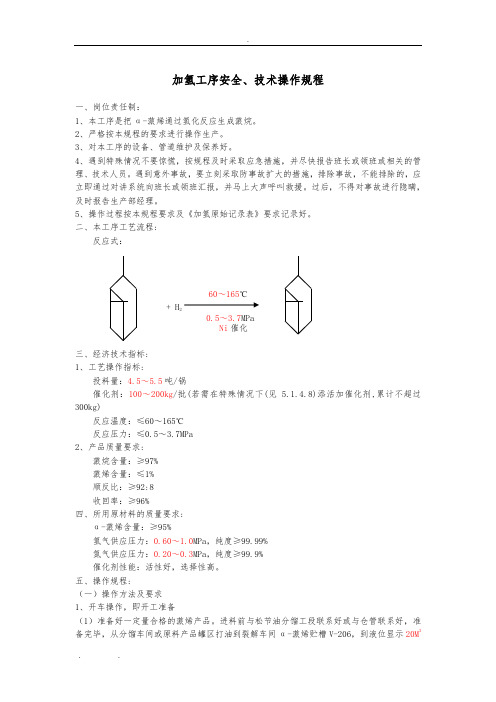
加氢工序安全、技术操作规程一、岗位责任制:1、本工序是把α-蒎烯通过氢化反应生成蒎烷。
2、严格按本规程的要求进行操作生产。
3、对本工序的设备、管道维护及保养好。
4、遇到特殊情况不要惊慌,按规程及时采取应急措施,并尽快报告班长或领班或相关的管理、技术人员。
遇到意外事故,要立刻采取防事故扩大的措施,排除事故,不能排除的,应立即通过对讲系统向班长或领班汇报,并马上大声呼叫救援。
过后,不得对事故进行隐瞒,及时报告生产部经理。
5、操作过程按本规程要求及《加氢原始记录表》要求记录好。
二、本工序工艺流程:反应式:60~165℃+ H20.5~3.7MPaNi催化三、经济技术指标:1、工艺操作指标:投料量:4.5~5.5吨/锅催化剂:100~200kg/批(若需在特殊情况下(见 5.1.4.8)添活加催化剂,累计不超过300kg)反应温度:≤60~165℃反应压力:≤0.5~3.7MPa2、产品质量要求:蒎烷含量:≥97%蒎烯含量:≤1%顺反比:≥92:8收回率:≥96%四、所用原材料的质量要求:α-蒎烯含量:≥95%氢气供应压力:0.60~1.0MPa,纯度≥99.99%氮气供应压力:0.20~0.3MPa,纯度≥99.9%催化剂性能:活性好,选择性高。
五、操作规程:(一)操作方法及要求1、开车操作,即开工准备(1)准备好一定量合格的蒎烯产品。
进料前与松节油分馏工段联系好或与仓管联系好,准备完毕,从分馏车间或原料产品罐区打油到裂解车间α-蒎烯贮槽V-206,到液位显示20M3时,停止打油。
然后取样分析(或是松节油分馏当批次油样),要求α-蒎烯含量在95%以上,其中ß-蒎烯不能超过2%。
(2)检查冷却水、蒸汽、氢气、氮气和电源,保证其供应充足。
(3)清理干净高压釜、氢压机周围环境,无关杂物不得堆放在。
给高压釜搅拌轴处加满甘油,同时检查减速机油箱,要求盛油量不得少于三分之一,不足需加够油后方可运行。
(4)检查氢气压缩机运转顺畅。
加氢安全操作规程及注意事项

一、人员配置及要求1、投料及出料操作需有2人在岗,至少有一位熟练掌握氢瓶操作及压力釜操作。
2、岗位所有操作人员均需参加加氢还原岗位安全操作培训,考核合格后,方能上岗操作。
培训的内容不仅限于危险化学品使用、运输;设备安全操作、应急处理等)。
二、原辅料控制1、一般常使用的催化剂有Pd-C和R-Ni(Pd-C常含有50%的水份,R-Ni (雷尼镍)也常保存在水或醇中,两种催化剂干燥后均易在空气中自燃,固使用前和反应后均应妥善水封保存,避免接触空气。
2、催化剂的包装、领用:1)催化剂按原包装密封储存,车间根据实际的使用量按需领用,避免一次领用过多,长时间放置不用,而导致催化剂活性降低或失活或者干燥失水甚至自燃,暂时存用需用氮气保护。
2)若领用时发现内包装破损禁止使用,并退货。
补充:雷尼镣具有很多微孔,有很大的表面,在催化剂的表面吸附有大量的活化氢,并且Ni本身的活性也很强,容易氧化,因此该类催化剂非常容易引起燃烧,一般在使用之前均放在有机溶剂中,如乙醇等。
也可以采用钝化的方法,降低催化剂活性和保护膜等,如加入NaOH稀溶液,使骨架镣表面形成很薄的氧化膜,在使用前再用氢气还原,钝化后的骨架镣催化剂可以与空气接触。
3、氢气源使用氢气瓶组(12〜15个),禁止使用单个气瓶频繁切换置换。
氮气源使用液氮装置或氮气瓶组,禁止使用单个气瓶频繁切换置换。
避免切换工程中,混入空气。
4、氢气和氮气的供应商应有供应资质,且符合质量要求,氢气选用纯氢。
5、气瓶使用需要做相应记录(包括气体的剩余量,并保证生产正常用气,气瓶逐一开启检查)。
三、设备及管道要求1、氢化反应釜符合质量要求,且供应商有制造资质。
2、氢化反应区域符合地方安全部门的验收规定,避雷设施符合要求。
3、根据反应的具体条件安装相应等级的泄爆口(必须要安装),安全阀不强制安装,如装安全阀,排放管应排出室外。
4、温度计和压力表均经校验合格,尤其是氢气和氮气的压力表头要确认符合使用要求(应每半年进行强检)。
制氢装置操作规定1

制氢装置操作规定1制氢装置操作规定1停泵维修操作1)停泵后,如果泵需要修理,要将泵出入口阀全部关闭,站在上风向将泵出口倒淋翻开,对泵体进行泄压。
2)对粘度较大、易燃易爆的、毒性较大的介质,停泵后要进行密闭吹扫。
3)对高温油泵,待泵体温度降到40℃后,方可翻开泵体倒淋和低点排液阀将泵体介质排放干净。
5)通知室内主操及设备技术员。
6)做好记录。
2控制阀与副线切换操作2.1控制阀改副线操作7)接到内操指令控制阀改副线。
9)缓慢关小控制阀的上游阀,直至室内流量指示有下降趋势。
10)缓慢开控制阀的副线阀,同时按内操指令缓慢关控制阀的上游阀,直至控制阀上游阀全关。
11)按内操指令微调控制阀副线阀,稳定流量。
2.2如果调节阀需要解体那么:13)关闭调节阀的下游阀。
14)翻开调节阀的排凝阀,排净管线内的介质,同时做好防护工作。
15)如果是有毒有害介质,应佩戴好气防用具进行操作,并做好监护工作。
2.3副线改控制阀操作16)接到内操指令副线改控制阀。
18)外操缓慢将控制阀的上游阀全开,室内确认流量无变化。
20)外操缓慢关控制阀的副线阀,同时内操根据流量的变化缓慢翻开控制阀,保持流量的稳定,直至副线阀全关。
21)内操调整流量正常后控制阀投自动。
2.4如果控制阀维修后改回:22)先确认控制阀排凝阀关闭。
24)外操稍开控制阀的上游阀,对控制阀各密封部位进行气密,确认无漏点后内操关闭控制阀。
25)外操缓慢将控制阀的上游阀全开,室内确认流量无变化。
27)外操缓慢关控制阀的副线阀,同时内操根据流量的变化缓慢翻开控制阀,保持流量的稳定,直至副线阀全关。
28)内操调整流量正常后控制阀投自动。
- 1、下载文档前请自行甄别文档内容的完整性,平台不提供额外的编辑、内容补充、找答案等附加服务。
- 2、"仅部分预览"的文档,不可在线预览部分如存在完整性等问题,可反馈申请退款(可完整预览的文档不适用该条件!)。
- 3、如文档侵犯您的权益,请联系客服反馈,我们会尽快为您处理(人工客服工作时间:9:00-18:30)。
制氢装置加氢脱毒部分工艺管理和操作规程1.1 加氢脱毒部分的任务及主要工艺指标1.1.1 加氢脱毒部分的任务脱硫部分的任务是为轻烃水蒸汽转化制氢提供合格的原料(硫含量< 0.5PPm 、烯烃<1%)以防止转化催化剂硫中毒。
其中加氢部分是在催化剂和氢气存在的条件下,将原料中的有机硫,有机氯等转化为无机硫(H2S)和无机氯( HCl ),无机氯被脱氯剂吸收除掉,而硫化氢则被氧化锌吸收,使得脱硫气含硫<0.5PPm。
1.1.2 加氢脱毒部分的主要工艺指标(1) 轻石脑油干点< 160℃含硫量≤ 50PPm(2) 干气干气含硫量≤ 50PPm(3) 加热炉 F2001出口温度340~380℃加热炉炉膛温度≯ 800℃入口压力 3.8MPa(4) 加氢反应器 R2001入口温度340~380℃出口温度≯ 400℃入口压力 3.38MPa(abs)出口压力 3.35MPa(abs)空速1~ 6h-1氢油比(体)80 ~ 100加氢反应器床层最高温度≯400℃(5)氧化锌脱硫反应器 R2002A.B入口温度 350~370℃出口温度 360℃入口压力 3.35MPa(abs)出口压力 3.32MPa(abs)脱硫气含硫量≤ 0.5PPm1.2 R2001反应温度的控制反应温度是调节脱硫气含硫量的主要手段,钴-钼催化剂进行加氢脱硫时,操作温度通常控制在330~400℃范围内。
当温度低于320℃时,加氢脱硫效果明显下降。
温度高于420℃以上,催化剂表面聚合和结碳现象严重。
一般来说,对于 T205 加氢催化剂,当温度高于 250℃时,就具有加氢脱硫活性了。
因此,操作人员在正常操作时,必须调节TC7101 以控制好加氢反应器 R2001 入口温度。
即通过调节加热炉F2001 的燃料气流量来控制加氢反应器R2001入口温度。
反应温度主要参考原料性质的变化,空速的大小,氢油比的高低以及催化剂活性情况来进行控制。
非正常操作因素:影响因素1、加热炉出口温度上升2、原料含烯烃、CO、 CO2、 O2等杂质含量超标控制操作1、降低加热炉出口温度2、降低处理量,查明原料杂质来源,并切出超标的原料;若反应器床层严重超温,则要紧急降温,请示调度,装置作紧急停工处理。
3、原料含硫超标3、及时查明超标原料,联系调度切出超标原料。
4、加热炉出口温度下降4、提高加热炉出口温度5、加热炉出口温控阀TV7101 卡5、联系仪表处理。
6、低变升温过程中,中变气在加氢反应器床层6、按要求将加氢反应器床层温度降至260℃恒易发生甲烷化反应温,在低变升温过程中,严格控制中变气的配入量及低变反应器的升温速度。
7、配氢氢纯度不够,氢油比下降7、增大配氢量1.3 脱硫反应器温度要求及脱硫干气质量监控操作对于氧化锌脱硫剂来说,其低温活性较好,当脱硫反应器床层层温度达到 180 ±30℃时,就开始有脱硫活性了。
温度越高,脱硫剂的脱硫活性越高。
脱硫反应器的最高操作温度不能超过 390℃。
为了确保脱硫气含硫量<0.5PPm,在正常操作过程中,操作人员应对脱硫干气的质量进行监控,通过分析压缩机出口混合干气 H2S 含量、加氢反应器出口及脱硫气中总硫含量或 H2S 含量来控制原料的质量。
当脱硫气不合格 (含硫量≥ 0.5PPm)时,可适当提高加氢反应器入口温度,提温时,严禁忽高忽低或超高,每次提温幅度不能超过 5℃,应缓慢进行。
如果脱硫气超标,应及时查明超标原料,联系调度切出。
1.4 原料油缓冲罐V2001 的控制1.4.1 压力控制操作设计压力, MPa V2001 操作压力, MPa安全阀SV2001定压,MPa0.68常压0.68控制原则外操在巡检过程中应检查器压力。
1.4.2 液位控制操作设计罐容( 60% 液位), m322.26控制原理V2001 现场压力和石脑油泵入口压力显示是否正常,控稳容正常液位操作指标,%报警操作液位指标,% 6540~ 70由 DCS 液位控制回路LCA7101 自动调节石脑油进料控制阀,保证V2001 内有一定液位,达到缓冲的要求,保证进出物料平衡。
控制原则(1)控制进出物料流量平衡,保证V2001 液位在指标范围内。
(2)确保 V2001 保持微压。
非正常操作影响因素控制操作1 、仪表故障:液位测1、内操将进料控制阀由自动调节改为手动调节,根据石脑油进装置量假信号或液位指示流量及泵出口流量手动调节。
失灵2、内操联系仪表处理3、外操根据现场液位显示进行监控。
影响因素控制操作2、调节阀故障1、内、外操配合将进料控制阀由自动调节改副线操作,根据石脑油进装置流量及泵出口流量现场人工调节。
2、内操联系仪表处理。
3、外操根据现场液位显示进行监控。
3 、进料流量突然增大或减小导致液位变化大1、内操调整液控阀进料流控阀的PID 值(自动状态)。
2、内操手动开关进料流量控制阀(手动状态)。
3、内操提高或降低进料量。
4、外操检查石脑油泵P2001 是否抽空或跳停。
5、外操使用流量调节阀副线配合操作。
4、进料中断1、内操适当降低加热炉出口温度及转化炉温,并同时调整好转化炉的水碳比。
2、内操及时联系调度查找原因,尽快恢复原料供应。
3、若压缩机未满负荷生产,可引自产氢进压缩机,调整压缩机负荷。
* 不推荐使用。
1.4.3 温度控制操作设计温度,℃操作温度,℃40常温轻石脑油缓冲罐V2001 通过液控阀LCA7101 控制液位在40~ 70%。
在实际操作过程中,液面控制偏高,有利于当轻石脑油中断时,有缓冲余地。
在液控阀LV7101 阀前有一条DN40的无盐水赶油线,当装置停工检修时,可先打开无盐水赶油线,将系统内的原料油退至罐区;而且液控阀 LV7101 阀前还有一条 DN25 的 1.0MPa 蒸汽吹扫线,在装置停工吹扫过程中,可以打开蒸汽,吹扫V2001及其进出口管线。
注意必须先顶油然后才吹扫。
1.5 石脑油流量的控制石脑油的流量由DCS流量控制回路 FC7103 控制,石脑油的流量显示由FI7103A 及FI7103B 输入。
在正常操作过程中,当石脑油用量在3t/h 以下时,应使用 P2001D 进行生产,将切换开关打至 FI7103B ,通过流量控制回路 FC7103 自动控制石脑油的用量;当石脑油用量在 10t/h 以下时,应使用P2001A/B 进行生产,将切换开关打至FI7103A ,通过流量调节回路 FC7103 自动控制石脑油的用量;当石脑油用量大于8t/h 时,可视情况使用P2001C 进行生产。
1.6 加氢干气流量控制及各种干气的切换操作1.6.1 加氢干气流量控制(1)气油比加氢干气使用流量越大,装置的气油比越高。
而提高气油比对装置的生产有利,气油比越高,转化炉在相同处理量下的生产负荷越低,装置的氢气收率越高,装置的能耗也就越低。
因此,我们应多用加氢干气制氢。
(2)氢气对反应的影响在氢气存在的条件下,石脑油中不易脱除的有机硫,可通过加氢催化剂将转化为无机硫。
因此,加氢干气中氢含量越高,也就是氢油比越高,对加氢反应有利,能提高脱硫率。
在实际操作中,应维持一定的氢油比,氢油比一般要求在80~ 100。
影响氢油比的因素有:进料量、进料组分变化、工业氢返回氢、柴油加氢供氢量及仪表故障等。
而且,加氢干气中氢气含量的变化,会影响装置转化炉水碳比的控制,当加氢干气中氢含量较高时,可视情况稍微降低转化炉的水碳比;当加氢干气中氢含量较低(氢含量 <60%)时,可视情况稍微提高转化炉的水碳比。
1.6.2 各种干气的切换1.6.2.1 正常生产情况下,装置开两台压缩机进行生产,没有备用压缩机。
(1)加裂干气的切入及切出联系调度,检查加裂干气进装置的流程,外操应与内操联系好,先慢慢打开加裂干气界区第一道阀,然后再慢慢打开加裂干气第二道界区阀。
操作过程应严格控制好压缩机入口压力,慢慢将加裂干气引入干气压缩机。
内操应将返回氢压控PC7402 打至自动控制模式,将压缩机入口压控PC7406 打手动控制,随时与外操联系,利用加裂干气第二道界区阀控稳加裂干气流量,避免干气压缩机入口压力超高。
当加裂干气含硫超标或工艺要求需要切出时,内操应将返回氢压控PC7402 打至自动控制模式,将压缩机入口压控PC7406 打手动控制,随时与外操联系,避免干气压缩机入口压力突然降低。
联系调度,停用加裂干气。
外操应与内操联系好,先慢慢关闭加裂干气界区第二道阀,然后再慢慢关闭加裂干气第一道界区阀。
(2)渣油干气、柴油干气的切入及切出联系调度,检查干气进装置的流程,外操应与内操联系好,慢慢打开干气界区阀。
操作过程应严格控制好压缩机入口压力,慢慢将干气引入干气压缩机。
内操应将返回氢压控PC7402打至自动控制模式,将压缩机入口压控PC7406打手动控制,随时与外操联系,避免干气压缩机入口压力超高。
当干气含硫超标或工艺要求需要切出时,内操应将返回氢压控 PC7402 打至自动控制模式,将压缩机入口压控 PC7406 打手动控制,随时与外操联系,避免干气压缩机入口压力突然降低。
联系调度,停用渣油干气。
外操应与内操联系好,慢慢关闭干气界区阀。
3.1.6.2.2 当有一台干气压缩机出现问题需要切出处理时。
此时进行干气的切换操作,可联系调度,准备停用加裂干气,慢慢将干气压缩机的一回一及二回二打开,并将该压缩机降至零负荷,多余干气先经PV7406 放至火炬,然后再慢慢关闭界区阀,将该路干气切出系统,操作过程中注意控稳系统压力,避免操作波动,引起转化催化剂结炭。
1.6.2.3 当有一台干气压缩机正在检修,而另一台压缩机又出现问题需要切出处理时。
联系调度,准备停用干气,慢慢将干气压缩机的一回一及二回二打开,并将该压缩机降至零负荷,多余干气先经PV7406 放至火炬,然后再慢慢关闭界区阀,将干气切出系统;停用干气的同时,与柴油加氢装置协调好,改通柴油加氢循环氢进装置的流程,通过手动控好FCA7102 ,慢慢将柴油加氢循环氢引入装置;同时,内操计算出需要增加的石脑油量,慢慢提大装置的进油量。
整个操作过程中注意控稳转化炉入口原料气的流量及系统压力,避免操作波动过大而引起转化催化剂结炭。
1.7 V2002 的控制1.7.1 压力控制操作设计压力,MPa V2002操作压力,MPa安全阀SV2004定压, MPa0.60.40~ 0.550.73控制原理由 DCS 入口压力控制回路PC7406 自动调节由V2002 的入口压力。
当压力高于给定值时, PC7406 超压打开,当压力低于给定值时,PC7406 自动关回, PC7402 自动打开补压。
控制原则(1)内外操配合首先检查压力控制系统是否正常工作,努力控稳容器压力。
(2)迅速判断判断造成压力波动的其它原因,在满足下游设备不受影响的前提下尽量保证进出物料压力平衡。