铜氨废水处理与废铜液回收
铜氨废液中铜回收的新工艺流程

铜氨废液中铜回收的新工艺流程铜氨废液是一种常见的含铜废水,通常产生于电镀、冶炼和化学制剂生产等工业过程中。
传统的铜氨废液处理方法主要是通过化学还原、溶解、电析和电积等步骤将废液中的铜回收。
然而,这些方法存在着许多问题,包括操作复杂、设备投资高、产生大量废物等。
为了解决这些问题,近年来出现了一种新的铜回收工艺流程,该工艺使用离子液体作为溶剂,并借助离子液体的独特性质实现高效的铜回收。
离子液体是一类由有机阳离子和无机阴离子组成的液体。
其具有低熔点、广阔的电化学窗口、优异的溶解性能和良好的可重复使用性等特点,因此在废液处理等领域具有广泛的应用前景。
对于铜氨废液处理而言,离子液体可以替代传统的有机溶剂,与废液中的铜离子发生配位反应并形成络合物,实现铜的有效回收。
基于离子液体的铜回收工艺流程一般包括以下几个步骤:1. 提取:首先将铜氨废液与适量的离子液体混合,通过相分离技术将铜络合物从废液中提取到离子液体相中。
2. 洗涤:将离子液体相中的铜络合物用水或酸性溶液进行洗涤,去除其中的杂质和离子液体残留。
3. 脱水:通过蒸发或其他适当方法将洗涤后的溶液中的水分脱除,得到含有高浓度铜络合物的浓缩液。
4. 还原:将浓缩液与适量的还原剂反应,将铜络合物转化为可溶性的金属铜。
5. 结晶/电积:通过结晶或电积等方法将金属铜从溶液中回收,得到高纯度的铜产品。
可以看出,基于离子液体的铜回收工艺流程相比传统的方法具有以下优势:1. 高效:离子液体作为溶剂,能够与废液中的铜离子快速发生配位反应,并形成稳定的络合物,提高了铜的提取效率。
2. 环保:离子液体具有低挥发性和低溶解性有机物的特点,因此在铜回收过程中几乎没有挥发物和废气排放,达到了绿色环保的要求。
3. 经济:离子液体的可重复使用性和稳定性很高,可以降低处理成本,并减少废物的产生。
4. 高纯度:离子液体的溶解性能良好,可以实现对铜的高效分离和纯化,得到高纯度的铜产品。
总结起来,基于离子液体的铜回收工艺流程是一种具有广泛应用前景的新型工艺。
废水中铜氨络合物的处理 (2)
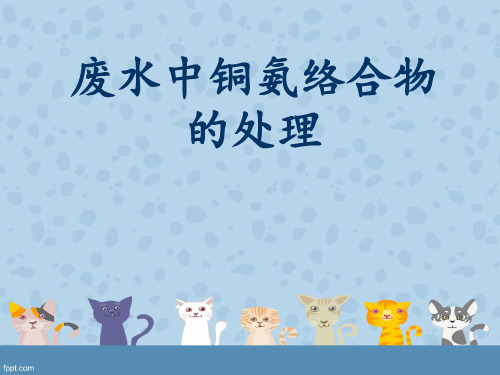
TMT处理含铜氨络合物废水
TMT:
固体Na3(C3N3S3)-9H2O 美国Aldrich公司出品的有机硫药 剂,将33.32g 的Na3(C3N3S3)-9H2O晶 体溶解于100g 的去离子水中,即为 TMT的15%水溶液,俗称TMT-15。
• 当废水中含有络合剂如NH3、EDTA、磷酸 酯、柠檬酸盐和天然有机酸时,它们将与铜 离子配位形成非常稳定的可溶性络合物,从 而干扰传统工艺对铜的处理。
• 采用混凝、中和沉淀、吸附、电解、微生 物法等处理方法,难以达到良好的去除效 果或处理成本太高。
• 采用硫化物沉淀法处理含络合剂的重金属 废水,由于各种重金属硫化物的溶度积都 非常小,重金属的去除效果很好。常用的 硫化物分无机硫(硫化钠)与有机硫 (STC、DTC和TMT)两大类。
• 从表1中可以看出,与TMT相比,硫化钠、 STC和DTC的毒性较大,特别是DTC更具
• 硫酸亚铁法:
• 由于在酸性条件下,EDTA-Cu的稳定常数小于EDTA-Fe3+ 的稳定常数(pH=4,EDTA-Cu的稳定常数的对数值lgK稳 =10.2,EDTA-Fe3+的稳定常数的对数值lgK稳=14.7),因 此,向PCB络合废水中加入Fe3+可以将Cu2+置换出来,即 将络合态铜离子转化成游离态铜离子,然后调高废水的pH 值,可以将Cu2+完全沉淀下来。在实际的工程中加入的是 硫酸亚铁,在酸性条件下,通过机械或空气的搅拌,部分 Fe2+氧化成Fe3+,通过Fe3+置换出EDTA-Cu中的Cu2+,然 后加入NaOH调高pH值至9左右,生成Cu(OH)2、Fe(OH)3、 Fe(OH)2沉淀,利用Fe(OH)3生成的矾花较大,吸附性较强, 沉淀速度较快,加快铜的去除。此法在工程上成功的案例 较多,出水总铜普遍低于0.5mg/L,但也有其缺点:加药量 较大,产生的污泥较多。
铜酸洗废水(液)处理及铜质回收工程应用.

[ 1 ] 周吉林 , 周少奇 . 垃圾填 埋场渗 滤水的 处理技 术 . 环境 污染 与 防治 , 2001, 23( 4) : 187 -189 [ 2 ] 黄霞 , 桂萍 . 膜 - 活性污泥 组合工艺 的污水处 理特性 研究 资 源 发展 与环境 保护 . 第三届 海峡两 岸环境 保护学 术研讨 会论 文
6+ 6+
达到国家一级排放标准 , 如果回用于铜酸洗前处理用 水 , 酸洗过后的铜件 色彩不一 , 对产品有直接 影响 。 再者 , 该企业新建前提 , 不允许废水排放 , 政府审批控 制污染非常严格 。 因此 , 对废水的深度处理是工艺设 计的关键 。 在经过几年的 研究和大量试 验的基础上 , 从小 试、 中试成功后 , 应用到实际生产 , 并解决了废水( 液) 处理零排放最关键的运行成本问题 。 如果运行费用 过高 , 企业负担重 , 又没有经济效益 , 零排放也就难以 实现 。 针对该类废水特点与环保要求 , 其工艺设计为化 学法 反渗透 -蒸发三级深度处理 。 1. 3 废水( 液) 处理及中水回用零排放工艺 废水处理工艺流程见图 1 。
环 境 工 程 2008 年 6 月第 26 卷第 3 期
67
铜酸洗废水( 液) 处理及铜质回收工程应用
赵济强
( 南京市环境科学学会 , 江苏 南京 210024) ( 台州盛世环境工程有限公司 , 浙江 玉环 317604) 摘要 以某金属表面处理有限公司为例 , 介绍铜 酸洗表面处理行业生 产废水处 理与中水回 用零排放 工艺 。 经过多 年 的运 行及实践证明 , 该工艺技术先进 、操作性强 , 实现了废水零排放 , 且回收的铜质品位高 , 具有很大的社会效益 、环 境 效益和经济效益 , 是一种非常实用的废水处理与 中水回用技术 。 关键词 铜酸洗 零排放 铜质回收
醋酸铜氨废液中铜的回收与综合处理

Cu (NO3 ) 2 + H2 SO4
CuSO4 + 2HNO3
5 实验部分
511 仪器和试剂 主要仪器 :ZD22 型自动电位滴定计 ;721 型分光光度计 : PHS22 型酸度计 ;71512DM 控温仪 ;电热套 ;
电动搅拌器 ;空气压缩机 主要试剂 :浓硫酸 ( G. R) ;浓硝酸 (A. R) ;硫化钠 (C. P) ;三氯甲烷 (A. R) ;2 ,92二甲基21 ,102菲口罗 啉
2Cu (NH3 ) 4Ac2 + H2O + Q
如果同时采取吹脱方式 ,不仅可以最大限度的降低游离氨在废液中的浓度 ,而且能使废液中 CO 氧化成
CO2 直接放空. 由于加热吹脱使废液体积缩小 ,铜离子浓度增加而有利于用沉降方法除铜. 312 Cu2 + 的解吸
由于[ Cu (NH3 ) 4 ]2 + 较稳定 ,我们采取在加入足量硫酸的条件下破坏其稳定性 ,使其转化成为简单的
1 前 言
炼油厂催化氢化过程需纯化氢气 ,常采用按一定比例的低价铜离子 (或称亚铜离子) 和高价铜离子 配合的醋酸铜氨溶液除去氢气中的 CO ,CO2 ,O2 , H2 S 等气体. 虽然醋酸铜氨溶液可再生使用 ,但反复使
用其活性也会逐渐降低 ,最终成为醋酸铜氨废液 (简称废液) ,按文献[ 1 ]方法测得该废液含铜量为 11013 克/ 升 ,同时废液呈碱性含有大量游离氨 ,故具有较强的腐蚀性和刺激性. 目前多采用按一定比例加浓硫 酸沉降分离得硫酸铜和在酸性条件下用铁将铜离子置换成海绵金属铜粉等方法处理[2~3] ,但排除的废 液中含铜离子仍在 0101 克/ 升左右 ,这不但对环境造成严重的污染 ,也损失了大量的贵重金属铜. 经实 验我们探索出了中和法和硫化法相结合的方法处理该废液收到了满意的效果.
废水中铜氨络合物的处理 (2)

• 在含有[Cu(NH3)4]2+的废水中加入TMT-15 时,发生以下反应:
用TMT处理实际废液的效果及工艺 流程
TMT能与铜离子强力螯合并沉淀,处理含铜氨络合 物废水的效果好;而且它的处理方法简单,只要添 加药剂即可除去铜离子,不用增加设备费用。
• 试验表明,TMT能较快地将铜从稳定的氨络合物 中解离并沉淀下来,沉淀物在静置24小时后也没 出现再溶解现象;当溶液pH值位于7~10之间时, TMT对铜的去除效果均较好。络合剂氨的浓度会 影响TMT对铜的去除率,对于高氨浓度的铜溶液, 可以适当地加大TMT的剂量从而使残余铜浓度降 至0.5mg/L以下。TMT-15处理实际蚀刻洗涤废水 的效果也较好,铜的去除率大于99.9%。 • 同时渗滤试验表明,沉淀物在去离子水中渗滤出 的饱和铜浓度很低,因此当生成的污泥在填埋场 遭雨水淋沥时,也不会对环境造成重金属的二次 污染。
铜氨络合物概念:
• 在硫酸铜溶液中加入浓氨水,首先析出浅 蓝色的碱式硫酸铜沉淀,氨水过量时此沉 淀溶解,同时形成四氨合铜(Ⅱ)络离子。铜 氨络合物较稳定,不与稀碱液作用。而且 可以利用它在乙醇溶液中溶解度很小的特 点来获得硫酸四氨合铜(Ⅱ)的晶体。但如果 络离子所处的络合平衡在一定条件下被破 坏,随着络合平衡的移动,铜氨络离子也 要离解。
铜氨络离子的破络方法
• 1.硫化物沉淀法: • 重金属离子与S2-易于形成难溶或者不溶沉淀物,加入Na2S 可使废水中的重金属离子完全沉淀下来。如CuS的溶度积 (Ksp=6.3×10-36)的对数值(lgKsp(CuS)=35.2)远远 大于 [Cu(NH3)4]2+和EDTA-Cu离解常数的对数值 ([Cu(NH3)4]2+的稳定常数的对数值为lgK稳=12.59, EDTA-Cu的稳定常数为lgK稳=18.80),因此加入Na2S可 以破络,形成CuS沉淀。但是CuS有形成胶性溶液的倾向 (能透过滤纸),需要添加絮凝剂使之形成大的絮体共同沉 降下来。采用此方法处理PCB络合废水,往往因为沉淀池 沉淀效果不好,使出水不能稳定达标。另外,由于没有硫化 物在线监测仪器,工程上往往需要过量投加Na2S,过量的 S2-使废水产生恶臭,需要添加亚铁盐使之沉淀下来,不然 会造成二次污染。
碱性蚀刻液中铜回收与废液、铜氨废水的循环使用

碱性蚀刻液中铜回收与废液、铜氨废水的循环使用目前碱性蚀刻液由危险废物回收商进行资源化回收铜,生产硫酸铜产品,没有对氨进行回收和处理,也不能回收失效的蚀刻液和铜氨废水的循环使用,对环境有一定的影响,且导致运输过程的能源消耗和成本增加。
为响应国家“清洁生产、变废为宝、发展循环经济、创建节约型社会”的号召,计划安装“在线含铜废蚀刻液的资源化回收”成套设备。
2009年1~7月份含铜废蚀刻液产生量为:碱性蚀刻废液和后面的水洗产生的铜氨废水为本公司主要NH3-N的排放源。
二、减少末端处理前的污染因子—NH3-N1、氨氮对环境的影响氮素物质对水体环境和人类都具有很大的危害,主要表现在以下几个方面:氨氮会消耗水体中的溶解氧;氨氮会与氯反应生成氯胺或氮气,增加氯的用量;含氮化合物对人和其它生物有毒害作用:①氨氮对鱼类有毒害作用;②NO3-和NO2-可被转化为亚硝胺——一种“三致”物质;③水中NO3-高,可导致婴儿患变性血色蛋白症——“Bluebaby”;加速水体的“富营养化”过程;所谓“富营养化”就是指水中的藻类大量繁殖而引起水质恶化,其主要因子是N和P(尤其是P);解决的办法主要就是要严格控制污染源,降低排入水环境的废水中的N、P含量。
2、线路板废水中的氨氮来源目前碱性蚀刻目1) Cu2+: 125~145~165g/L 2) Clˉ: 4.0~4.8~5.3N3) PH值: 8.0~8.4~8.8(PH计读数) 4)比重: 1.165~1.190~1.215)温度: 47~53℃6)目体积1025L7)补充液配制:Clˉ4.0~5.3N ; OHˉ3.4~3.9N单耗:(1) 蚀板盐:60Kg/ K Sq.Ft(2) 蚀板液210LT/ K Sq.Ft。
实际补充蚀刻子液2.5~3吨/天。
氨水洗目1) NH3.H2O: 20% , 30~45~60g/L2)目体积95L单耗:氨水95LT/ K Sq.Ft碱性蚀刻生产线的月产量:由此可见:按照理论计算,月产30万平方英尺的蚀刻线排放浓的蚀刻废液大约:300,000*210/1000 =63,000L=63m3=63*1.19=75吨,大约含铜=75*145=10807Kg=10.8吨/月=129.6吨/年。
铜矿废水的处理及铜的回收

膜提高一级浓缩的效率 ; 二级浓缩时 , 在 由于浓缩倍 数很高 , 膜表面溶 液的离子浓度大幅升高, 容易 出现结 晶浑浊 , 卷式膜 的结构流道易被结 晶物堵塞的特点 , 决定 了它不适合作 为二级浓缩 , 因此本试验选取管式 纳滤膜进行二级浓缩 。
3处 理 效 果分 析 .
31 . 浓缩过 程的结 晶现象 由于浓缩 液的结晶盐析出对卷式膜 的正 常运行有较大 的影响 , 在 工业 系统 中必须避免出现 。因此 , 在本 试验过程 中, 一旦 发现浓缩液 出 现浑浊 , 即视为浓缩终点 。具体情况如表 2 。 表 2浓缩倍数与浑浊现象 操作批次
一
浓缩液 C ( gL um/)
项目
p H
级反渗透
批次 1
23 l
1.4 1 6
批次 2
2 92 5.
77 .5
批次3
2 24 4.
3 3
平均值
28 3
8
进料液 C ( /) u mgL
透 析 液 C ( gL um/)
TS D 电 导 率 F e C U C a N a ( mg ) ( s r ( / ) ( / ) ( / ( /) / m / r mgL mgL mg L c L) mg L
2 8 10
浓缩倍数
1 6
浓缩液外观
有 沉 淀 析 出
级R O批 次 I
一
级R O批 次 2 级R O 8
浑浊少量沉淀 浑浊少量沉淀
一
由于试验设备 限制 , 试验 出现浓缩液结 晶浑浊时 , 无法及时停机检 测, 因此导致浓缩终点 的浓缩倍数不尽相 同。由表 2批次 2和批次 3的 数据可以看出 ,浓缩 至 8倍 时,浓缩液开始 出现浑浊并有少量沉淀析 出 。 因此 , 可推 测 浓 缩 极 限 为 8 。 倍 32一级 R . O浓 缩 的通 量 变 化 试验中采用反渗透 4 O 进行一级浓缩 , FI 运行温度控制在 1~2 ℃, 9 2 运行压力控制在 1br共进行 了三个批次 的运行试验 。图 2是一级反 7 a, 渗透膜运行通量与运行时间的关系图。 从图 中反渗透的运行通量来看 , 在浓缩终点前 , 反渗透保持较高 的运行通量且通量较为稳定 ,反渗透 4O F I的平 均 通量 为 3 .L 3O MH。
从铜氨废液中回收铜的工艺流程

从铜氨废液中回收铜的工艺流程1. 概述铜氨废液是指含有铜离子和氨离子的废液。
回收铜是一项重要的资源恢复利用工作,对环境保护和经济发展具有重要意义。
本文将介绍从铜氨废液中回收铜的工艺流程,并详细探讨每个步骤的工艺条件和操作要点。
2. 废液预处理废液预处理主要是对铜氨废液进行预处理,以去除杂质和提高铜离子的浓度。
具体步骤如下: 1. pH调节:将废液的pH值调节到适宜的范围,常用的调节剂有硫酸、盐酸等。
2. 氧化处理:通过加氧或者加入氧化剂,将废液中的有机物氧化成CO2和H2O,以降低废液的COD浓度。
3. 沉淀处理:加入适量的沉淀剂,将废液中的悬浮颗粒物和杂质沉淀下来,以提高后续处理步骤的效果。
4. 过滤处理:将废液经过滤器进行过滤,去除沉淀物和悬浮颗粒,得到清澈的液体。
3. 铜离子的萃取铜离子的萃取是将废液中的铜离子转移到有机相中,以实现分离和浓缩的目的。
常用的铜离子萃取剂有LIX系列、D2EHPA等。
具体步骤如下: 1. 萃取剂的选择:根据废液中铜离子的浓度和其他成分的特点,选择合适的萃取剂。
2. 萃取剂的配制:将萃取剂与稀释剂按比例混合,得到合适的萃取剂溶液。
3. 萃取反应:将废液与萃取剂溶液进行接触,通过两相之间的分配系数,将铜离子转移到有机相中。
4. 相分离:分离有机相和废液,收集含铜的有机相。
4. 铜离子的还原铜离子还原是将有机相中的铜离子转化为金属铜。
常用的还原剂有亚硫酸钠、亚硫酸氢钠等。
具体步骤如下: 1. 还原剂的选择:根据铜离子的还原特点和废液中其他成分的影响,选择合适的还原剂。
2. 还原反应:将有机相中的铜离子与还原剂进行反应,还原为金属铜。
3. 沉淀处理:将还原后的金属铜以沉淀物的形式分离出来。
4. 分离收集:将沉淀物与液体分离,收集得到纯净的金属铜。
5. 废液处理废液处理是整个工艺流程中不可忽视的环节,目的是对处理后的废液进行安全处理和环境排放。
常用的废液处理方法有中和处理、浓缩处理和盐析处理等。
- 1、下载文档前请自行甄别文档内容的完整性,平台不提供额外的编辑、内容补充、找答案等附加服务。
- 2、"仅部分预览"的文档,不可在线预览部分如存在完整性等问题,可反馈申请退款(可完整预览的文档不适用该条件!)。
- 3、如文档侵犯您的权益,请联系客服反馈,我们会尽快为您处理(人工客服工作时间:9:00-18:30)。
文章编号:1001-3849(2002)01-0031-04 铜氨废水处理与废铜液回收宫本涛, 袁 浩, 李永德, 左洪泽, 唐基禄(深圳市昌宏泰环保设备有限公司,广东深圳 518054)摘要:简述某电子厂生产电路板过程中产生的镀铜废液、废水回收处理方法。
介绍应用高质量浓度含铜废液制取工业硫酸铜与海绵铜的工艺方法和流程。
铜氨废水的处理采用破络添加混凝剂沉淀后可达标排放,对调试、运行中一般故障的排除进行了论述。
关 键 词:含铜废水;回收;处理中图分类号:X781.1 文献标识码:ATreatment of Coppre-Ammonia Waste Water and Recoveryof Waste Solution Containing Copper GON G Ben-t ao,YU A N Hao,L I Y ong-de,ZU O Hong-ze,T A NG Ji-lu (Changhongtai Environent Protection Equipment Co.Ltd,Shenzhen 518054,China) Abstract:M ethods for treamtnet o f copper-am monia w aste w ater and recovery o f w aste solution co ntaining co pper produced in the cir cuit boards pr oduction in a certain electronic factory are br iefly described in this paper.T echnolo gical metho ds and pro cesses for the prepar ation of com-mercial copper sulfate and spong e copper w ith the hig h concentr ation co pper w aste solutio n are intro duced.T he copper ammo nia w aste w ater is treated w ith method of com plex com pound de-stroy ing,coagulatio n pr ecipitation w ith coagulant.The treated w ater is up to standard and then discharge.The remov al of tro ubles occur ing in test and operation pr ocesses is also discussed.Key words:w aste w ater co ntaining copper;reco very;treatment1 前 言我公司在深圳市承接某台资电子有限公司生产电路板时产生的废水治理。
该电子厂每年生产单面板20多万m2、双面板6万多m2,其生产电路板的主要工艺流程为:压合板下料→外发数控钻孔→磨板→沉铜→丝网印刷→曝光显影→电镀(Cu、Ni、Sn、A u)→脱膜→碱刻→↑ 酸刻印阻焊剂→印字符→喷铅锡→外形加工→检验入库。
其中沉铜、电镀、脱膜、蚀刻均产生大量废水,刻铜母液一般铜的质量浓度均在100g/L左右,产生的铜氨废水:50~60t/d,其它重金属、氰化废水、酸收稿日期:2001-07-16作者简介:宫本涛(1976-),男,辽宁大连人,深圳市昌宏泰环保设备有限公司高级工程师,学士. 碱废水、油墨废水等200t/d,本文就高质量浓度含铜废水回收利用,及铜氨废水处理加以论述,这方面国内杂志报导较少,其它废水处理不再赘述。
2 高质量浓度铜废液回收处理电路板经丝网印刷、曝光显影、脱膜后要求保留的设计铜线路用油墨密封护线,其它80%~90%以上的不需要的铜膜须全部腐蚀去除,根据不同工艺要求采用碱刻或酸刻除铜,其中碱刻铜膜以氨水为主要原料蚀铜,碱刻液可反复使用,喷射到敷铜板上,腐蚀去除裸露铜膜,直至刻铜液含铜量达到较高质量浓度,刻铜效果差,不能再使用时更换新液。
经分析这种废液铜的质量浓度高达Cu2+=30~150 g/L,满负荷生产时,每天有1~2t碱蚀浓铜废液。
根据电路板工艺要求不同,另一条生产线采用酸刻铜板,酸刻铜板主要原料是:过硫酸钠、H2SO4、H2O2、HCl……等,不同的工艺采用不同的酸刻液,有的是微刻,经分析酸刻废液铜的质量浓度一般为Cu2+=20~90g/L,当质量浓度过高时,将有CuSO4・5H2O析出,可直接回收硫酸铜。
这两种高质量浓度的含铜废液不能直接排入清洗后的含铜废水中混合处理,否则增加废水处理的负荷和难度,又要加大投资,也浪费了资源。
生产中控制:这两种高质量浓度的酸、碱浓铜废液单独设管分流排出至固定回收槽,积累一定数量后装桶送固体废物处理站回收。
高质量浓度的含铜废液回收处理工艺流程如图1。
高质量浓度的含铜废液是生产硫酸铜的好原料,用这两种废液生产时应注意严格控制各类杂质进入,这样在生产中不须特别提纯,可直接制取纯度较高的一级工业硫酸铜。
其操作工艺流程(如图1):将碱铜浓废液和酸铜(或浓硫酸)浓废液按一定比例在搅拌情况下缓慢加入反应器中,控制相应的反应时间和一定温度,并反复调整pH值为5~6,使之生成颗粒粗大的碱式硫酸铜沉淀,便于后续工序清洗和脱水,其外观颜色为天蓝色,并产生大量(NH4)2SO4和少量硫酸亚铁,这些杂质会影响CuSO4・5H2O的纯度,必须清除,在中性或偏酸性溶液中,碱式硫酸铜沉淀而这两种杂质溶解于水,很容易使它们分离,可用清水反复洗涤3~5次去除这些可溶性杂质,用水清洗时(可用处理合格的废水清洗,能节约用水),控制一定pH值,防止Cu2+流失,一般清洗水铜的质量浓度Cu2+=1.0~0.05g/L,当反应控制不好时,第一池清水有时铜的质量浓度较高,Cu2+=1~2g/L,若排入含铜废水处理池,损失较大,可分流入回收池,用来制作金属海绵铜,当Cu2+<0.05g/L时含铜废水流入含铜废水处理池统一进行废水处理。
图1 浓铜液回收工艺流程图经清洗提纯后的碱式硫酸铜水浆泵入压滤机除去一部分水份,再将浆液注入反应罐,在搅拌下逐渐加入工业纯浓硫酸,控制反应温度 >90℃,经反应一段时间后取样检查,溶液中无蓝白色碱式硫酸铜粉末时可开启底阀出料注入桶中冷却。
结晶CuSO4・5H2O经离心甩干后打包,由于这种含铜废液杂质少,不需要特别纯化处理就可做出按国标(GB-439-80)一级硫酸铜,每吨废液可生产出五水硫酸铜300~500kg,价值一两千元,废物回收,效益可观。
为了增产硫酸铜,提取结晶硫酸铜时,控制进入反应罐中浆液含水量一定,加酸后浓溶液波美度越高,出产硫酸铜也越多;当冷却降温析出硫酸铜时,结晶水温度越低,析出的硫酸铜越多;冷却时一般采用空冷或水冷,若采用机械强冷耗能大,也会增加回收成本,控制冷却温度为20~30℃时可倒出结晶水。
其中CuSO4・5H2O的质量浓度为250g/L左右,虽可加温浓缩再结晶但考虑设备投资大,会提高回收成本,可用来与碱铜液再次反应制取碱式硫酸铜,反复使用。
当铜的质量浓度少(Cu2+≤20g/L)时,可用于做海绵金属铜。
制取海绵铜工艺原理是在酸性条件下(pH= 2~3)用铁将铜离子置换生成海绵金属铜粉[1],具体工艺流程是:将反应池第一池清洗水和硫酸铜结晶稀溶液注入制取海绵铜反应池中,加适量废酸调pH=2~3,再加入去油干净的废铁屑,并定期搅拌,使置换反应生成的铜粉落入池底,更新的铁表面与硫酸铜又继续作用,随反应时间不断增长,铁不断溶解置换铜离子还原成铜粉,废液中铜的质量浓度逐渐减少,当Cu2+<0.01g/L以下时可将清液排出,流入含铜废水处理池进行处理。
海绵铜粉收集打包回收。
3 铜氨废水处理电路板经碱性蚀刻后产生大量的含铜清洗废水和酸性蚀刻后产生的少量清洗含铜废水同管流入铜氨废水均化调节池,因碱性蚀刻水量大,流出的废水偏碱性,NH4+较多,形成更多较稳定的铜氨络合物。
如何处理这类含铜废水,我们进行工艺比较试验,最后确定:将铜氨废水先加Na2S破络沉淀,加碱调pH=11,再加混凝剂搅拌,经2h沉淀取上清液分析Cu2+=0.13mg/L(国家一级排放标准Cu2+≤0.5mg/L)完全可以做到达标排放。
设计中将该电子厂的铜氨废水采用上述方案处理,因为[Cu(NH3)4]2+四氨合铜配离子稳定常数K稳=1012.59,而[Cu(OH)4]2-的配离子稳定常数K稳=106.0,前者稳定常数大于后者,所以单加碱不能破除稳定的铜氨,废水处理不合格,而铜的硫化物溶度积[CuS K S P=6.3×10-36]比铜的氢氧化物溶度积[Cu(OH)2,K SP=5.6×10-20]更小,能完全破坏铜氨络离子形成CuS沉淀。
反应条件:pH=8~12,时间:30m in,处理后废水完全达标,理论加药量:[Cu(NH3)4]2+:N a2S= 1.0∶(1.5~2.0)。
用Na2S破铜氨络合物处理含铜废液,其优点是CuS溶度积小,除铜效率高,适用pH值范围大,用碱或石灰均不能完全破除铜氨络合物,废水处理不合格。
调试运行中一般故障排除:1)铜氨废水如果pH值太低,加Na2S后将产生H2S毒气放出,严重污染环境,影响工人健康,应先将废水pH调到9.0以上再加Na2S;2)药剂Na2S的添加量应严格控制,添加量过多,水质发暗,色度差,COD也可能超标,太少沉铜效果差,废水易超标。
有的工厂无化学分析, [Cu(NH3)4]2+准确量不能确定,Na2S的量也无法计算出来,此时可根据废水颜色来确定Na2S的添加量,加Na2S搅拌10~15m in后,用小烧杯取废水样观察:如果溶液中有大量黑色小颗粒,且颗粒间溶液透明清澈,说明Na2S加量正好;如果加药后溶液呈墨黑色,有时偏蓝绿色或带棕红色,说明N a2S过量,可适当添加一部分废水再搅拌处理,当然多余的Na2S在后续处理工序中也能与重金属离子作用产生沉淀去除;如果加Na2S后废水偏绿,只有少量的小颗粒出现,说明Na2S量不够,再适当补加一些。
3)废水加Na2S后与[Cu(NH3)4]2+作用产生NH3气。
([Cu(NH3)4]2++Na2S→CuS↓+4NH3↑+ 2Na+),需用压缩空气不断搅拌溶液吹脱氨气,一般要搅拌30min以上,如果NH3吹脱不完全,将会再溶,络合成铜氨络离子,在后续处理工序中废水的含铜量不易达标;4)在废水处理中由于CuS颗粒细小,产生悬浮不易下沉,对固液分离有一定困难,可采用先加有机混凝剂聚丙烯酰胺(PAM)产生絮聚,添加量可适当加大,即PAM按质量分数为0.1%配制,再按废水量的0.3%~0.5%加入废水中,后加无机混凝剂聚合氯化铝(PAC)添加质量浓度为100~150mg/L,使之形成较大矾花产生共聚沉淀,控制废水流速(0.1~0.2m/s)[2],就能有效去除铜离子,使外排废水Cu2+≤0.5mg/L。