橡胶配方与各性能的关系
橡胶结构与性能关系的研究
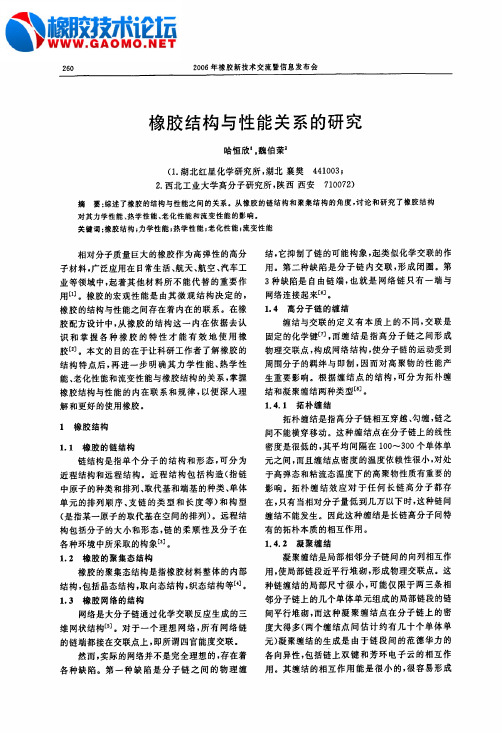
2602006年橡胶新技术交流暨信息发布会橡胶结构与性能关系的研究哈恒欣1。
魏伯荣2(1.湖北红星化学研究所,湖北襄樊441003;2.西北工业大学高分子研究所,陕西西安710072)摘要:综述了橡胶的结构与性能之间的关系。
从橡胶的链结构和聚集结构的角度,讨论和研究了橡胶结构对其力学性能、热学性能、老化性能和流变性能的影响。
关键词:橡胶结构;力学性能f热学性能;老化性能,流变性能相对分子质量巨大的橡胶作为高弹性的高分子材料,广泛应用在日常生活、航天、航空、汽车工业等领域中,起着其他材料所不能代替的重要作用[1]。
橡胶的宏观性能是由其微观结构决定的,橡胶的结构与性能之间存在着内在的联系。
在橡胶配方设计中,从橡胶的结构这一内在依据去认识和掌握各种橡胶的特性才能有效地使用橡胶[2]。
本文的目的在于让科研工作者了解橡胶的结构特点后,再进一步明确其力学性能、热学性能、老化性能和流变性能与橡胶结构的关系,掌握橡胶结构与性能的内在联系和规律,以便深入理解和更好的使用橡胶。
1橡胶结构1.1橡胶的链结构链结构是指单个分子的结构和形态,可分为近程结构和远程结构。
近程结构包括构造(指链中原子的种类和排列、取代基和端基的种类、单体单元的排列顺序、支链的类型和长度等)和构型(是指某一原子的取代基在空间的排列)。
远程结构包括分子的大小和形态,链的柔顺性及分子在各种环境中所采取的构象[3]。
1.2橡胶的聚集态结构橡胶的聚集态结构是指橡胶材料整体的内部结构,包括晶态结构,取向态结构,织态结构等[4]。
1.3橡胶网络的结构网络是大分子链通过化学交联反应生成的三维网状结构[5]。
对于一个理想网络,所有网络链的链端都接在交联点上,即所谓四官能度交联。
然而,实际的网络并不是完全理想的,存在着各种缺陷。
第一种缺陷是分子链之间的物理缠结,它抑制了链的可能构象,起类似化学交联的作用。
第二种缺陷是分子链内交联,形成闭圈。
第3种缺陷是自由链端,也就是网络链只有一端与网络连接起来[6]。
橡胶配方设计与功用
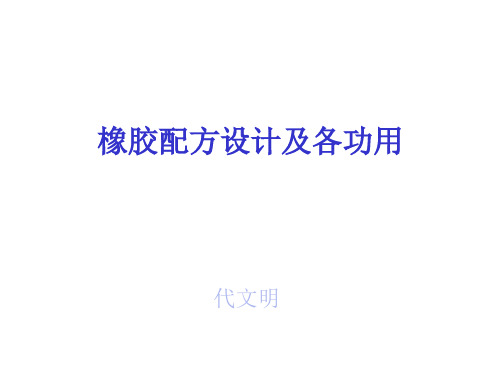
活性剂
原理:指加入胶料后能增加促进剂活性, 减少促进剂用量,缩短 硫化时间的物质.白烟配方中,是针对白烟表面高活性 的烷基与ZnO或促进剂之间反应。 功用: 1.避免锌氧粉与促进剂被白烟吸附而影响硫化速度; 2.增加PH值:因白烟PH值约在5.8—7.3之间,带微酸性; 3.活化白烟表面,增加白烟与橡胶键结来改善物性; 活性剂的种类: 依其化学组成不同区分为: 无机活性剂: 金属氧化物,金属碳酸盐,如锌氧粉,碳酸锌,氧化 镁等; 有机活性剂: 醇类---DEG(乙二醇),PEG(聚乙二醇),尿素衍生 物,其他化合产品等;
增塑剂(软化剂)
结构与作用 由于天然橡胶、丁苯橡胶、顺丁橡胶、异戊橡胶、 丁基橡胶和三元橡胶的分子量很大,多为无官能团 的无定型结构,且具有弹性,为了在加工时使这些 非极性分子能够相对移动产生变形,传统上是在混 炼时添加一定量的无官能团结构的脂肪烃、环烷 烃、芳香烃油品增塑剂和软化剂。对于极性橡胶, 必须剂
焦烧现象
胶料在贮存和加工过程中因受热的作用会发生早期硫化(交联)并失去流动性和再加工 的能力,这就是焦烧现象。
品类与性能 ---可以用作橡胶防焦剂的化学品有三类:
有机酸类; 亚硝基化合物类; 次磺酰胺类。
---任何防焦剂都应符合橡胶加工性能要求,即:
优良的防焦性能; 对不同促进剂和胶料选择性小; 对其他配合剂不敏感; 对胶料的硫化特性和硫化胶性能无不良影响; 贮存稳定和操作性能好; 不结块、不飞扬、易分散、不喷霜; 符合工艺安全和卫生要求。
常用胶料特性介绍
• • 丁二烯橡胶(BR):CH2=CH-CH=CH2 特性:磨耗佳,弹性好,硬度高,但是止 滑性差,延伸率差,不易加工素练。
常用胶料特性介绍
• • • 丁二烯-丙烯晴橡胶(NBR): 分子式:CH2=CH-CH-CH2 CH2=CHCN 特性:耐油胶,抗张,抗压佳,目尼值高, 不易加工,耐油性是以其中含AC量为判 断。丙烯晴值(AC)含量愈高,耐油程序愈 佳。
橡胶件实验报告

一、实验目的本次实验旨在通过实际操作,了解橡胶件的制备过程,掌握橡胶的基本性能测试方法,并分析不同橡胶配方对橡胶件性能的影响。
二、实验原理橡胶是一种具有高弹性、耐磨性、耐腐蚀性等特性的高分子材料,广泛应用于汽车、机械、电子、建筑等领域。
橡胶件的制备过程主要包括混炼、成型、硫化等步骤。
通过调整橡胶配方和工艺参数,可以改变橡胶件的性能。
三、实验材料与设备材料:1. 天然橡胶2. 硫磺3. 促进剂4. 填料(如炭黑)5. 油脂设备:1. 混炼机2. 压缩机3. 硫化罐4. 万能力学试验机5. 摩擦系数试验机四、实验步骤1. 混炼:将天然橡胶、硫磺、促进剂、填料和油脂等材料按照一定比例投入混炼机中,进行充分混炼。
2. 成型:将混炼好的橡胶料投入压缩机中,进行压制成型,制成所需形状的橡胶件。
3. 硫化:将成型后的橡胶件放入硫化罐中,在特定温度和压力下进行硫化,使橡胶分子结构交联,提高橡胶件的性能。
4. 性能测试:- 拉伸强度测试:将硫化后的橡胶件放置在万能力学试验机上,按照规定速度拉伸至断裂,记录最大拉伸强度。
- 压缩永久变形测试:将硫化后的橡胶件放置在压缩试验机上,在一定压力下压缩一定时间,记录压缩后的变形量。
- 摩擦系数测试:将硫化后的橡胶件放置在摩擦系数试验机上,测试其与不同材质表面的摩擦系数。
五、实验结果与分析1. 拉伸强度:实验结果显示,不同配方的橡胶件拉伸强度存在差异。
增加填料含量可以提高橡胶件的拉伸强度,但过高的填料含量会导致拉伸强度下降。
2. 压缩永久变形:实验结果显示,增加硫磺和促进剂的含量可以提高橡胶件的压缩永久变形性能,但过高的含量会导致变形性能下降。
3. 摩擦系数:实验结果显示,增加炭黑含量可以提高橡胶件的摩擦系数,提高其耐磨性能。
六、结论通过本次实验,我们掌握了橡胶件的制备过程和性能测试方法。
不同配方的橡胶件具有不同的性能,通过调整配方和工艺参数,可以满足不同应用场景的需求。
七、实验建议1. 在进行橡胶件制备时,应注意控制温度、压力和时间等工艺参数,以保证橡胶件的性能。
橡胶与各指标的关系
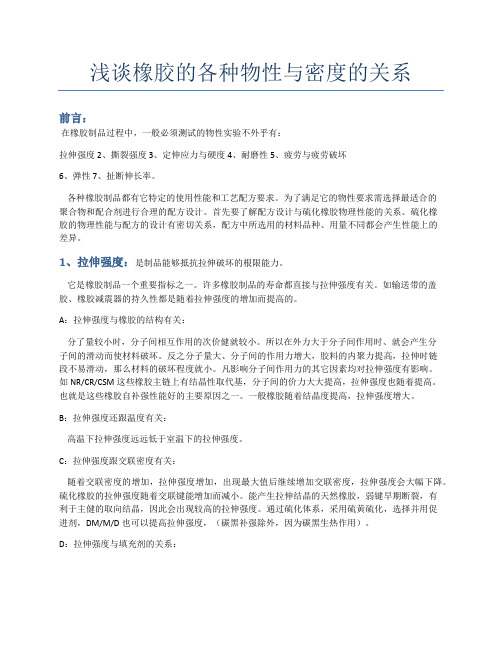
浅谈橡胶的各种物性与密度的关系前言:在橡胶制品过程中,一般必须测试的物性实验不外乎有:拉伸强度 2、撕裂强度 3、定伸应力与硬度 4、耐磨性 5、疲劳与疲劳破坏6、弹性7、扯断伸长率。
各种橡胶制品都有它特定的使用性能和工艺配方要求。
为了满足它的物性要求需选择最适合的聚合物和配合剂进行合理的配方设计。
首先要了解配方设计与硫化橡胶物理性能的关系。
硫化橡胶的物理性能与配方的设计有密切关系,配方中所选用的材料品种、用量不同都会产生性能上的差异。
1、拉伸强度:是制品能够抵抗拉伸破坏的根限能力。
它是橡胶制品一个重要指标之一。
许多橡胶制品的寿命都直接与拉伸强度有关。
如输送带的盖胶、橡胶减震器的持久性都是随着拉伸强度的增加而提高的。
A:拉伸强度与橡胶的结构有关:分了量较小时,分子间相互作用的次价健就较小。
所以在外力大于分子间作用时、就会产生分子间的滑动而使材料破坏。
反之分子量大、分子间的作用力增大,胶料的内聚力提高,拉伸时链段不易滑动,那么材料的破坏程度就小。
凡影响分子间作用力的其它因素均对拉伸强度有影响。
如NR/CR/CSM这些橡胶主链上有结晶性取代基,分子间的价力大大提高,拉伸强度也随着提高。
也就是这些橡胶自补强性能好的主要原因之一。
一般橡胶随着结晶度提高,拉伸强度增大。
B:拉伸强度还跟温度有关:高温下拉伸强度远远低于室温下的拉伸强度。
C:拉伸强度跟交联密度有关:随着交联密度的增加,拉伸强度增加,出现最大值后继续增加交联密度,拉伸强度会大幅下降。
硫化橡胶的拉伸强度随着交联键能增加而减小。
能产生拉伸结晶的天然橡胶,弱键早期断裂,有利于主健的取向结晶,因此会出现较高的拉伸强度。
通过硫化体系,采用硫黄硫化,选择并用促进剂,DM/M/D也可以提高拉伸强度,(碳黑补强除外,因为碳黑生热作用)。
D:拉伸强度与填充剂的关系:补强剂是影响拉伸强度的重要因素之一,填料的料径越小,比表面积越大、表面活性越大补强性能越好。
结晶橡胶的硫化胶,出现单调下降因为是自补强性非结晶橡胶如丁苯随着用量增加补强性能增加、过度使用会有下降趣向。
橡胶配方成分

橡胶配方成分介绍橡胶配方成分是指制造橡胶制品所使用的原材料的组合。
不同的橡胶制品需要不同的配方成分,以满足特定的性能和用途要求。
本文将详细探讨橡胶配方成分的种类、作用和选择。
一级标题1:主要的橡胶配方成分二级标题1:橡胶橡胶是橡胶制品的主要成分,其质量和性能对最终产品的质量和性能有着重要影响。
常用的橡胶包括天然橡胶和合成橡胶。
天然橡胶具有良好的弹性和耐磨性,适用于制造轮胎、橡胶管等产品。
合成橡胶根据不同的化学结构和性能特点,可分为丁腈橡胶、丁苯橡胶、丁二烯橡胶等。
二级标题2:增强剂增强剂是用于增加橡胶强度和耐磨性的成分。
常用的增强剂包括炭黑、硅石粉、纤维素等。
炭黑是最常用的增强剂,能够增加橡胶的强度和耐磨性,并改善橡胶的加工性能。
硅石粉可以提高橡胶的抗老化性能,适用于制造高温橡胶制品。
纤维素可增加橡胶的拉伸强度和耐磨性,适用于制造高强度橡胶制品。
二级标题3:软化剂软化剂是用于提高橡胶的柔软性和可加工性的成分。
常用的软化剂包括石蜡、石油树脂、酯类等。
石蜡可以使橡胶具有良好的柔软性和可塑性,适用于制造橡胶制品。
石油树脂可提高橡胶的可加工性和耐磨性,适用于制造橡胶管、橡胶带等产品。
酯类软化剂可以提高橡胶的柔软性和耐油性,适用于制造橡胶密封件等产品。
二级标题4:硫化剂硫化剂是用于橡胶硫化反应的成分,可使橡胶成型后具有良好的弹性和耐热性。
常用的硫化剂包括硫、过氧化物等。
硫化剂与橡胶中的双键发生反应,形成交联结构,使橡胶成型后具有弹性和耐热性。
过氧化物是一种常用的硫化剂,可在低温下加速橡胶的硫化反应,提高橡胶的硫化效率。
一级标题2:橡胶配方成分的选择二级标题1:产品要求橡胶配方成分的选择应根据最终产品的要求来确定。
不同的橡胶制品对强度、耐磨性、耐油性、耐温性等性能有不同要求,因此需要选择合适的橡胶和配方成分。
二级标题2:成本考虑橡胶配方成分的选择还应考虑成本因素。
一些高性能的橡胶和配方成分价格昂贵,而某些一般性能的成分价格相对较低。
轮胎橡胶配方

轮胎橡胶配方
轮胎橡胶配方是制造轮胎的关键部分,它决定了轮胎的主要性能。
配方中包含多种成分,每种成分都有其特定的作用。
以下是一个典型的轮胎橡胶配方及其成分说明:
1、基础橡胶:这是配方的核心成分,通常使用天然橡胶或合成橡胶。
天然橡胶具有良好的弹性和耐久性,而合成橡胶则提供了更多的性能选项,如低滚动阻力、高耐磨性和耐高温性。
2、填充剂:用于增加橡胶的体积,使其更坚固和耐磨。
常见的填充剂包括碳黑和白炭黑。
碳黑提供了优异的耐磨性和抗撕裂性,而白炭黑则增加了橡胶的抗湿滑性能。
3、硫化剂:使橡胶分子相互交联,形成网状结构,从而提高其弹性和耐久性。
4、增塑剂:如石油和油脂,有助于改善橡胶的加工性能和柔韧性。
5、防老剂:有助于延缓橡胶老化过程,提高其耐久性。
6、抗氧剂:防止橡胶在高温下氧化,有助于延长轮胎的使用寿命。
7、抗紫外线剂:用于抵抗紫外线对橡胶的降解,延长轮胎的使用寿命。
8、粘合剂:有助于增强橡胶与纤维材料之间的粘附力,提高轮胎的结构稳定性。
9、钢丝与纤维材料:用于增强轮胎的结构强度和稳定性。
钢丝主要用于轮胎的骨架结构,而纤维材料则提供额外的支撑和稳定性。
10、其他添加剂:根据特定需求,还可以添加其他一些添加剂,如抗湿滑剂、降噪剂等,以改善轮胎的性能。
除了以上成分外,正确的配方比例也是至关重要的。
不同成分的比例会直接影响轮胎的性能。
通过精确控制这些成分的比例,可以生产出具有优异性能的轮胎。
这需要经验丰富的工程师和技术人员来研发和调整配方,以满足各种不同的应用需求。
橡胶配方设计知识点归纳
橡胶配方设计知识点归纳橡胶配方设计是橡胶制品生产过程中的重要环节,涉及橡胶成分的选择和合理配比等方面。
本文将从橡胶材料的选择、添加剂的选用、硫化系统的设计以及橡胶配方的优化等几个方面,对橡胶配方设计的知识点进行归纳和阐述。
1. 橡胶材料的选择橡胶制品的性能取决于选择的橡胶材料。
橡胶材料常见的有天然橡胶和合成橡胶。
天然橡胶具有良好的弹性和抗拉性能,但耐磨性较差;合成橡胶种类繁多,可以根据需要选择不同种类的合成橡胶,如丁腈橡胶、丁苯橡胶等。
在橡胶配方设计中,需要根据产品的要求选择合适的橡胶材料,并进行混炼。
2. 添加剂的选用除了橡胶材料外,配方中通常还需要添加各种添加剂来改善橡胶制品的性能。
添加剂包括增塑剂、增强剂、防老剂、硫化剂等。
增塑剂可提高橡胶的柔软性和可加工性,增强剂可以提高橡胶的强度和耐磨性,防老剂可以延长橡胶制品的使用寿命,而硫化剂则是橡胶配方中必不可少的成分,其作用是促使橡胶发生硫化反应,使之具有弹性。
3. 硫化系统的设计硫化系统是橡胶配方设计中的关键部分。
硫化反应是橡胶成型过程中的一项重要工艺,通过将硫化剂加入橡胶中,发生交联反应,使橡胶具有更好的力学性能和耐用性。
硫化系统的设计包括硫化剂的选择、硫化剂与促进剂的配比、硫化温度和时间等因素。
不同的橡胶制品对硫化系统的要求有所不同,因此在配方设计时需要根据具体情况进行调整和优化。
4. 橡胶配方的优化橡胶配方的优化是指通过合理的调整橡胶配方的比例和成分,以获得最佳的橡胶制品性能。
橡胶配方的优化需要综合考虑多种因素,如橡胶材料、添加剂的选择和比例、硫化系统的设计等。
通过试验和实践,不断调整和改进配方,可以使橡胶制品的性能得到提高,达到更好的使用效果。
总结:橡胶配方设计是橡胶制品生产中不可或缺的一环,涉及橡胶材料的选择、添加剂的选用、硫化系统的设计以及配方的优化等多个方面。
只有通过科学合理的配方设计,才能制备出性能稳定、质量可靠的橡胶制品。
因此,在进行橡胶配方设计时,需要充分考虑各种因素,并根据具体要求进行精确的调整和优化,以获得最佳的产品性能。
三元乙丙橡胶配方及性能
三元乙丙橡胶配方及性能三元乙丙橡胶(EPDM)是一种合成橡胶,它由乙烯、丙烯和1,4-丁二烯三种单体通过共聚合反应合成而成。
EPDM具有优异的耐老化、耐臭氧、耐腐蚀和耐高温性能,是一种广泛应用于汽车、电气、建筑和管道等领域的工程材料。
本文将介绍EPDM的配方及其性能。
一、EPDM的配方EPDM的配方主要包括橡胶、助剂和填充剂。
1.橡胶EPDM橡胶是由乙烯、丙烯和1,4-丁二烯三种单体通过共聚合反应得到的合成橡胶。
其中,乙烯提供了EPDM的弹性和柔软性,丙烯提供了EPDM的耐老化和耐臭氧性能,1,4-丁二烯提供了EPDM的强度和耐磨性。
根据不同的应用要求,可以根据需要调整乙烯、丙烯和1,4-丁二烯的含量,以获得所需的性能。
2.助剂为了提高EPDM橡胶的加工性能和使用性能,通常需要添加一些助剂。
主要的助剂包括加工助剂、防老化剂和交联剂。
加工助剂用于改善橡胶的流动性和加工性能,降低橡胶的粘度和热稳定性。
常用的加工助剂有抗粘剂、塑化剂和润滑剂。
防老化剂用于提高EPDM橡胶的耐老化性能和耐臭氧性能。
常用的防老化剂有硫化石墨、多硫化物和双酚A等。
交联剂用于将EPDM橡胶进行交联,提高其强度和耐磨性。
常用的交联剂有过氧化物和硫醇等。
3.填充剂填充剂用于提高EPDM橡胶的硬度和强度,降低成本。
常用的填充剂包括碳黑、硅酸钾和滑石粉等。
根据不同的要求,可以调整填充剂的含量和种类,以获得所需的性能。
二、EPDM的性能EPDM具有以下优异的性能:1.耐老化性能:EPDM橡胶具有良好的耐老化性能,能够在高温、高湿、光照等恶劣环境下长期使用而不发生老化和劣化。
2.耐臭氧性能:EPDM橡胶具有出色的耐臭氧性能,能够在高臭氧浓度和高温下长期使用而不发生开裂和劣化。
3.耐腐蚀性能:EPDM橡胶对酸、碱、盐等化学物质具有良好的耐腐蚀性能,能够在腐蚀性介质中使用而不发生腐蚀和溶解。
4.耐高温性能:EPDM橡胶在高温下仍能保持良好的性能,能够在高温环境下使用而不发生软化和融化。
橡胶配方与各种物性之间的关系【范本模板】
“炼胶工人”胶友对《橡胶配方与各种物性之间的关系》进行了针对性的分享,非常感谢他的指点!不同的橡胶产品对胶料的物性都有不同的要求,同时对生产这些产品时胶料的工艺性能(加工性能)也需要不同的要求.所谓的工艺性也就是生产这些橡胶产品的过程不能达到理想的状态,做出来的橡胶产品也就很难做到性能理想化、经济效益最大化。
一句话,无论你要求橡胶产品有什么样的物性要求,也不管你的要求是高还是低,如果工艺性能无法满足要求(实现要求的过程无法满足),那么你就很难顺利的去生产。
不多赘述,该贴将和大家一起谈论各橡胶工艺性能受配方的影响及关系。
一、混炼性能1.各种成分对混炼效果的影响主要分析配方中各种填料、化学药品、操作油等配合成分混入橡胶中的难易性、分散性。
它主要由这些配合成分与橡胶之间的互溶性的高低、浸润性的大小来决定.胶料混炼工艺设计的好坏评价方法之一就是各种成分是否可以在橡胶中能够迅速的分散;混炼效果的好坏,则可以通过各种成分在橡胶中能否均匀分散其中来衡量。
这两个指标都主要取决于配合成分与橡胶之间的互溶性、浸润性。
“互溶性”这个词大家可能会认为橡胶那么大的分子怎么可能溶解在各种配合成分里很多配方里,应该是配合成分溶解在橡胶里才对。
其实,所谓的溶质、溶剂也是相对的,量少的惯称为溶质,量多的则为溶剂,习惯性的认为溶质溶解在溶剂中,如果“溶质"的量比“溶剂”的量大很多的话,那就是“溶剂”溶解在“溶质"中。
所以,也就可以理解为互溶性了。
为了能让胶料达到多种综合性能都很优异的效果,很多配方用到的橡胶都不止一种,可能2、3、4、5种橡胶并用,这就涉及到这些橡胶之间的互溶性(也许橡胶之间的互溶性大家更好理解一些)。
混炼后的胶料如果电镜图片里显示各相之间没有明显的分离、橡胶之间、橡胶与各配合成分之间分散的非常均匀那就表明互溶性好,否则互溶性就差。
互溶性差的配方体系所对应的胶料的各种物性也就不能得到好的体现。
其实,橡胶配合体系是不能像盐溶于水那样做到分子级的互溶性,一是因为橡胶是由不同分子量的高分子复杂体系组成,二是各种配合成分也不是简单的小分子化合物,三它们是固相之间的溶解性。
橡胶配方设计
橡胶配方设计一、橡胶配方设计的基本原则1.1 满足产品性能要求橡胶制品的性能要求包括力学性能、耐热性、耐寒性、耐油性、耐酸碱性等,配方设计要根据产品使用环境和使用要求,合理选择各种橡胶材料和助剂,以满足产品的各项性能指标。
1.2 经济适用橡胶材料和助剂价格不同,配方设计时要考虑成本因素,经济适用是保证产品竞争力的重要因素。
1.3 生产工艺可行橡胶制品生产工艺复杂,配方设计时需要考虑生产工艺可行性,避免出现生产难度大、成本高等问题。
二、橡胶配方中各种材料及其作用2.1 橡胶材料常用的橡胶材料有天然橡胶、合成橡胶和再生橡胶。
天然橡胶具有优异的物理机械性能和加工特性,但价格较高;合成橡胶种类繁多,具有多样化的物理机械性能和加工特性,但价格相对较低;再生橡胶是回收废旧橡胶制品后经过加工处理得到的材料,价格低廉,但物理机械性能和加工特性相对较差。
2.2 填料填料是橡胶配方中的重要组成部分,可以改善橡胶制品的力学性能、耐热性、耐寒性等特性。
常用的填料有碳黑、白炭黑、滑石粉、硅灰等。
2.3 功能助剂功能助剂可以改善橡胶制品的物理机械性能、加工特性和使用寿命。
常用的功能助剂有增塑剂、硫化剂、促进剂等。
2.4 加工助剂加工助剂可以提高橡胶混炼和成型的效率和质量。
常用的加工助剂有防老化剂、润滑剂等。
三、橡胶配方设计流程3.1 确定产品要求根据产品使用环境和使用要求,确定产品各项指标要求,如强度、硬度、耐磨损性等。
3.2 选择合适数量级的材料根据产品要求和经济适用原则,选择合适数量级的橡胶材料、填料和助剂。
3.3 设计初步配方根据所选材料的特性和配比原则,设计初步配方,并进行小批量试制,测试各项性能指标。
3.4 优化配方根据试制结果,对配方进行优化调整,再次试制并测试各项性能指标,直至达到产品要求。
3.5 稳定生产确定最终配方后,进行大批量生产,并对生产过程中的各项参数进行控制和调整,保证产品稳定性能。
四、橡胶配方设计常见问题及解决方法4.1 配方中填料过多或过少导致产品性能不稳定。
- 1、下载文档前请自行甄别文档内容的完整性,平台不提供额外的编辑、内容补充、找答案等附加服务。
- 2、"仅部分预览"的文档,不可在线预览部分如存在完整性等问题,可反馈申请退款(可完整预览的文档不适用该条件!)。
- 3、如文档侵犯您的权益,请联系客服反馈,我们会尽快为您处理(人工客服工作时间:9:00-18:30)。
橡胶性能与配方的关系
不同的橡胶产品对胶料的物性都有不同的要求,同时对生产这些产品时胶料的工艺性能(加工性能)也需要不同的要求。
所谓的工艺性也就是生产这些橡胶产品的过程不能达到理想的状态,做出来的橡胶产品也就很难做到性能理想化、经济效益最大化。
一句话,无论你要求橡胶产品有什么样的物性要求,也不管你的要求是高还是低,如果工艺性能无法满足要求(实现要求的过程无法满足),那么你就很难顺利的去生产。
不多赘述,该贴将和大家一起谈论各橡胶工艺性能受配方的影响及关系。
一、混炼性能
1.各种成分对混炼效果的影响
主要分析配方中各种填料、化学药品、操作油等配合成分混入橡胶中的难易性、分散性。
它主要由这些配合成分与橡胶之间的互溶性的高低、浸润性的大小来决定。
胶料混炼工艺设计的好坏评价方法之一就是各种成分是否可以在橡胶中能够迅速的分散;混炼效果的好坏,则可以通过各种成分在橡胶中能否均匀分散其中来衡量。
这两个指标都主要取决于配合成分与橡胶之间的互溶性、浸润性。
“互溶性”这个词大家可能会认为橡胶那么大的分子怎么可能溶解在各种配合成分里很多配方里,应该是配合成分溶解在橡胶里才对。
其实,所谓的溶质、溶剂也是相对的,量少的惯称为溶质,量多的则为溶剂,习惯性的认为溶质溶解在溶剂中,如果“溶质”的量比“溶剂”的量大很多的话,那就是“溶剂”溶解在“溶质”中。
所以,也就可以理解为互溶性了。
为了能让胶料达到多种综合性能都很优异的效果,很多配方用到的橡胶都不止一种,可能2、3、4、5种橡胶并用,这就涉及到这些橡胶之间的互溶性(也许橡胶之间的互溶性大家更好理解一些)。
混炼后的胶料如果电镜图片里显示各相之间没有明显的分离、橡胶之间、橡胶与各配合成分之间分散的非常均匀那就表明互溶性好,否则互溶性就差。
互溶性差的配方体系所对应的胶料的各种物性也就不能得到好的体现。
其实,橡胶配合体系是不能像盐溶于水那样做到分子级的互溶性,一是因为橡胶是由不同分子量的高分子复杂体系组成,二是各种配合成分也不是简单的小分子化合物,三它们是固相之间的溶解性。
橡胶对配合剂的浸润性也许更能清楚的解释混炼工艺及效果的好坏。
橡胶对配合成分的浸润性高低主要决定于配合成分自身的特性,当然与橡胶的性质也有关系。
有机的、非极性的大多数化学样品(塑解剂、分散剂、操作油等软化剂、防老剂、
硫化体系等)都易溶解在橡胶里,被橡胶浸润。
无机的氧化物、盐类、各种土等则不易被橡胶浸润。
相似相容原理也解释了这些现象。
各种有机化学药品,塑解剂、分散剂、塑分、防老剂、促进剂、SA包括各种硫化都易混入橡胶中,而且加入的量比较少,这里就不对它们多加分析。
填料一般可以分为亲水性的和疏水性的两种。
氧化锌、氧化镁等无机氧化物及硫酸钡、硫酸镁、轻钙、重钙等盐类由于是极性的、亲水性的,在混炼时容易产生负电荷,而橡胶也存在同样的情况,所以二者便会相互排斥,所以难以分散橡胶之中。
陶土、云母、滑石粉、高岭土等虽然也是无机的、极性的,与橡胶之间的形成的界面亲和力小,虽不易被橡胶浸润,但是由于这些材料的粒径比较大且结构性比较低,混入橡胶的速度还是比较快的,分散的效果也可以接收,但补强性都比较差。
白炭黑虽然是亲水性的,但它的粒径非常小、结构性高、视密度小、易飞扬,且容易产生静电,使得它很难混入橡胶中。
炭黑是最典型的疏水性填料,容易被橡胶浸润,非常容易混入橡胶中并均匀分散其中。
另外,由于炭黑的粒径小、结构度高,混炼时生热性强,高填充量下混入橡胶就比较困难,所以炭黑不适合高填充量。
选用结构性低、粒径大的炭黑可以减小生热高、吃粉慢等缺点,填充量可以增大些。
为了能让这些亲水性填料也能容易混入橡胶中并能有好的分散性且还可以发挥更好的补强性,需要对这些填料进行表面改性来提高它们与橡胶间的亲和力。
配方中,我们常见到的加入的硅烷偶联剂、SA等都有这方面的作用。
最有效的方法还是在生产这些填料的时候直接对其进行表面处理。
烷烃油、环烷油、芳烃油、DOP、DBP等软化剂的加入可以改善混炼效果。
油的加入能加快这些填料混入胶料里,但是分散的效果会打折扣。
橡胶吸油的速度会直接影响混炼时间和混炼效果。
油品的粘度比重常数越高、芳香烃含量越高、分子量越小,则越容易被橡胶吸收。
2.配合体系对开炼时的包辊性的影响
橡胶的包辊性对胶料的分散效果也有很重要的影响。
包辊性是橡胶具有流变特性的一个典型的表现。
要想让胶料有良好的包辊性,最重要的是设置合理的温度和橡胶的配合体系。
当橡胶能紧紧地、均匀地、平整地、包裹在辊筒上,而不是出现脱辊、破边、掉渣、粘辊等,配合成分才能容易混入橡胶、分散效果才会好。
一般地,具有自补强性、可结晶、强度高的原材料橡胶的包辊性会比较好些,如NR等。
相反,如果原材料橡胶的自身强度如果很差,则包辊性就会比较差,如BR等。
配方体系中的滑石粉、云母、SA、防护蜡会使胶料有托辊的倾向;操作油及粘合树脂
等可以提高其包辊性。
一般地,软化剂的用量太大则易造成托辊,增粘剂的用量过大则会造成粘辊。
3.配合体系对焦烧的影响
焦烧的发生是胶料操作过程中及停放时非常忌讳的一个危害极大的现象,为了后续工段的操作安全及硫化后的产品不会发生不良影响,必须防止焦烧的发生。
发生焦烧的最主要原因还是硫化体系选择不当或用量过多造成的。
所以在选择促进剂时尽量选择焦烧时间长的次磺酰胺类及噻唑类促进剂为宜,并尽量控制使用份数。
另外,填料的酸碱性、结构度对焦烧也有一定的影响,酸性的、结构性低的填料能抑制焦烧。
操作油等软化剂对焦烧也有一定的抑制作用。
最有效的方法还是在配方里加入少量的防焦剂来防止焦烧的发生。
顾名思义,防焦剂是防止焦烧用的,所以用多了肯定会影响硫化速度的,而且对硫化胶的弹性、老化性等也不利!
4.配合体系对喷霜的影响
有的也叫出霜、喷粉、喷油等,是指软化剂、防老剂、SA、促进剂、硫化等小分子配合成分从胶里内部迁移到胶里表面的现象。
喷霜会严重影响胶料的表面粘性、混炼后胶料的均匀性、硫化胶的性能,总之(除了石蜡迁移到胶料表面其物理防护作用外的任何)尽量降低喷霜的发生。
最容易喷霜的就是硫磺,经常看到的胶料表面一层薄薄的黄色粉末就是硫磺从胶料内部迁移到表面的现象。
为防止硫磺的喷霜,配方里大量使用硫磺时可使用不溶性硫磺并且做到正硫化来加强对硫单质含量的控制。
一般情况下,SA、防老剂的用量不宜过大,在2phr一下喷霜会好些。
胶料里加入适量的操作油等软化剂也可以降低喷霜的发生。
5.配合体系对粘性的影响
像轮胎等由多种半成品贴合在一起的橡胶产品在生产的过程中对胶料的表面粘性有一定的要求,不能不粘,也不能太粘。
各半成品所用的主体胶料可能不一样,比如有的可能用NR为主,有的可能用SBR为主,还有的可能用BR为主等等,这就要求胶料之间不但要有很好的自粘性,还要有很好的互粘性。
如果要贴合在一起的两种胶料粘合性不这么好的话,在同一配方里添加一些第三种与这两种橡胶粘合性都比较好的橡胶是一个办法,也可以在这两种胶料的配方里都加入一些另一种胶料也是一个办法。
不管怎样,要想提高或有个良好的粘性,以下几点是基本原则:
①选择粘性高的橡胶为上
通常情况下,橡胶的分子链越柔顺、活动性高、生胶强度大,粘性就会高些。
所以,通用胶里,NR\CR的粘性比较好,尤其是自粘性更好。
②选择高补强性的填料
基于①中所说生胶强度大粘性会好的说法,如果填料的补强性好,那么就能提高未硫化胶的格林强度,从而提高粘性。
如果填料过多的话,会是胶料变“干”,粘性反而会下降。
③使用增粘树脂
很明显,增粘树脂的主要作用就是增粘。
萜烯树脂、石油类树脂、酚醛树脂、古马隆等都可以有效提高未硫化胶料的粘合性。
④操作油等软化剂可以提高粘合性
主要是因为软化剂的加入可以扩充橡胶大分子间的空隙,使得橡胶分子链的活动性提高,粘合性自然提高。
另外,也能防止填料的过量加入而造成的胶料发“干”。
⑤控制容易喷霜的化学品的配合量
喷霜后,胶料的光洁的表面被损,会大大降低胶料的粘合性。
二、挤出(压出)性能
混炼胶的含胶率、门尼粘度、格林强度、弹性、膨胀率、收缩率等对胶料的挤出性能有着直接的影响。
含胶率高,弹性形变就大,故而挤出后的膨胀性强,高速挤出时半成品的变形就大,影响生产效率;格林强度高,进胶容易、进胶速度快,挤出效率提高;混炼胶的弹性好,挤出时容易出现熔体分裂,造成挤出的半成品表面变的粗糙。
为了提高挤出性能,尽量考虑一下几个配合体系方面:
①胶种及含胶率。
不同的生胶由于分子链不同,弹性等也不同,挤出性能差别很大,NR、BR、CR等由于分子链上的侧基比较小,挤出容易;SBR、IIR等侧基大,挤出比较困难。
含胶率不能太高也不能太低,太高则弹性大,挤出后的半成品在挤出方向就会出现大的收缩率,影响尺寸稳定性和外观质量;太低则胶料变的“干”,塑性变差,挤出困难且半成品表面粗糙。
②加入再生胶、高性能的片层纳米土可以增加在高温下的流动能力,挤出能力提高。
③不同的填料对挤出性能的影响不同。
总体而言,填料的加入可以降低含胶率,降低弹性,可以提高挤出性能。
如果用量过高,出现含胶率极低现象,则是胶料变“干”,对挤出反而不利。
④加入软化剂可以降低胶料的收缩率、且有提高胶料与挤出机桶间的润滑作用而提高胶料的挤出性能。