抽样检验判定标准
产品检验及抽检标准

浙江莱克诗瑞丰润服饰有限公司一、检验及抽样标准1、抽样数量:总码数的平方根乘以八。
2、抽箱数:总箱数的平方根。
二、十分制检验1、经向疵点扣分法:1”以下扣1分;1”-5”扣3分;5”-10”扣5分;10”-36”之间扣10分。
2、纬向扣分法:1”以下扣1分;1”-5”扣3分;5”-半门幅之间扣5分;半门幅以上扣10分。
疵点的评分原则:A:同一码中所有经纬向的疵点扣分10分。
B:破洞不问大小扣10分。
C:布边半英寸内不扣分。
D:连续性疵点须开裁或将等外品。
E:任何大于针孔的洞均扣10分。
F:无论经向还是纬向,都以看得见为原则,并按疵点评分给予正确扣分。
G:除了特殊规定(比如涂层上胶布),通常只需检验布的正面。
三、等级计算方法1、可接受范围=总分数小于总码数;2、百码扣分不得超过一百分。
四、布匹检验标准对于经纬和其它方向的疵点将按以下标准评定疵点分数;一分:疵点长度为3寸或低于3寸;两分:疵点长度大于3寸小于6寸;三分:疵点长度大于6寸小于9寸;四分:疵点长度大于9寸。
评分的计算:原则上每卷布经检查后,便可将所得的分数加起来。
然后按接受水平来评定等级,但由于不同的布分辨须有不同的接受水平。
所以,若用以下的公式计算出每卷布匹在100平方码的分数,而只须制定一在100平方码下的指定分数,便能对不同布封布匹作出等级的评定。
(总分数×36×100)/(受检码数×可裁剪的布匹宽度)=每100平方码的分数超过指定分数的单卷布匹应被定为二等品。
如果整批布匹的平均评分超过了指定的分数水平,则该批布匹因被视为未通过检验。
不同布匹的接受水平不同类型的布匹被分为四大类。
梭织布匹类型布匹种类单卷整批1、全人造布匹,聚酯/尼龙/醋酸纤维制品;衬衫衣料;仿人造纤维织物;精纺毛料20点/100平方码,16点/100平方码2、粗斜纹棉布帆布/府绸/牛津条纹或方格纹棉布衬衫衣料/仿人造纤维织物/毛织品/染成的靛青纱,所有专用布匹,提花织物/多比灯心绒/天鹅绒/伸展粗斜纹布/人造布匹/混纺28点/平方码20点/平方码3、亚麻布薄细棉布40点/100平方码,32点/100平方码4、多皮奥尼丝绸/轻丝绸50点/100平方码,40点/100平方码抽样程序选择待检卷完全是随机挑选。
抽样检验标准
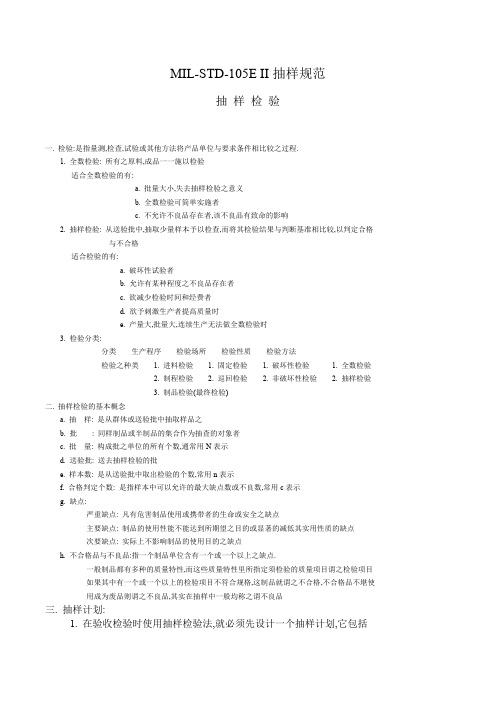
MIL-STD-105E II抽样规范抽样检验一. 检验:是指量测,检查,试验或其他方法将产品单位与要求条件相比较之过程.1. 全数检验: 所有之原料,成品一一施以检验适合全数检验的有:a. 批量大小,失去抽样检验之意义b. 全数检验可简单实施者c. 不允许不良品存在者,该不良品有致命的影响2. 抽样检验: 从送验批中,抽取少量样本予以检查,而将其检验结果与判断基准相比较,以判定合格与不合格适合检验的有:a. 破坏性试验者b. 允许有某种程度之不良品存在者c. 欲减少检验时间和经费者d. 欲予刺激生产者提高质量时e. 产量大,批量大,连续生产无法做全数检验时3. 检验分类:分类生产程序检验场所检验性质检验方法检验之种类 1. 进料检验 1. 固定检验 1. 破坏性检验 1. 全数检验2. 制程检验 2. 巡回检验 2. 非破坏性检验 2. 抽样检验3. 制品检验(最终检验)二. 抽样检验的基本概念a. 抽样: 是从群体或送验批中抽取样品之b. 批: 同样制品或半制品的集合作为抽查的对象者c. 批量: 构成批之单位的所有个数,通常用N表示d. 送验批: 送去抽样检验的批e. 样本数: 是从送验批中取出检验的个数,常用n表示f. 合格判定个数: 是指样本中可以允许的最大缺点数或不良数,常用c表示g. 缺点:严重缺点: 凡有危害制品使用或携带者的生命或安全之缺点主要缺点: 制品的使用性能不能达到所期望之目的或显著的减低其实用性质的缺点次要缺点: 实际上不影响制品的使用目的之缺点h. 不合格品与不良品:指一个制品单位含有一个或一个以上之缺点.一般制品都有多种的质量特性,而这些质量特性里所指定须检验的质量项目谓之检验项目如果其中有一个或一个以上的检验项目不符合规格,这制品就谓之不合格,不合格品不堪使用成为废品则谓之不良品,其实在抽样中一般均称之谓不良品三. 抽样计划:1. 在验收检验时使用抽样检验法,就必须先设计一个抽样计划,它包括四个部份: 批量N、样本大小n、允收水平及合格判定数c.(美国军用标准)2. 我们目前使用计划:MIL-STD-105E(美国军用标准).四. 抽样检验方法:1.正常2.减量3.加严4.它们之间转化关系:五. 抽样检验形式:单次: 根据一次样本检查结果,来决定合格或不合格之形式双次: 第一次抽验结果可能判定为合格、不合格和保留三种情况,当判为保留时,追加第二次样本再决定合格或不合格之形式多次: 是双次抽样之延续,只不过是将双次抽样的次数增多而已比较项目单次抽样双次抽样1. 对供应者心理上之影响恶好2. 总检验费用多少3. 平均检查数多少4. 实施之复杂性简明复杂5. 对质量保证程度相同相同六. 抽样计划使用步骤:a. 指定送样批b. 决定允收水平AQL值c. 决定采用单、双、多次d. 选定检验水平(除非特别指定,一般使用II级水平)e. 由批量及检验水平在表中查得代号f. 视抽样方式及检验严格程度(开始均选用正常检验),由代字及AQL查得抽样计划g. 使用上述各适当抽样表,查代字与AQL值之相交栏,求得样本数n,允收Ac,及拒收数Re附:抽样检验方法它们之间转化关系: 检验方式之变更标准:(一般为正常检验)当连续多批原物料经检验合格后则予以减量检验,反之则予严格检验,其变更类推如下:全檢(1:0)(5:5)加嚴(5:0)(5:2)正常(10:0)(1:1)減量(5:0)(1:1)免驗注:括号内所示之数字,前者代表检查批数,后者代表不合格批数,致于箭头所指,即为变更后之检验方式。
抽样检验标准

适用范围对于形成过程连续,具有自然连续性和整体均匀性的流程性材料,不能进行计数只能进行计量的物料,如没有明确规定抽样检验方式的,按本标准中的有关抽检规定执行。
没有明确规定抽样检验方式的其他批量物料,执行本标准中的、、有关规定,这部分物料包括:外购物料、委外加工的零部件、自制零部件等。
引用标准本标准依据GB/T -2003/ISO 2859-1:1999 计数抽样检验程序制定。
流程性材料抽检规定规格、型号相同,由同一个供应商供货的同批流程性材料作为一个检验批,对于塑料或树脂、钢材炉批号等相同的物料为一个检验批。
钢材的理化试验,每批抽检一组试样不易展开的物料在端头进行常规检验,如线材类等术语及符号批量(N):产品生产批次数,同一个供应商采用相同材质、技术工艺、车间、人员及设备生产出的产品统称为批次.构成一个批的产品产生条件须尽可能相同采购件:规格、型号相同,由同一个供应商供货的的同批产品。
外协件:同一个外协厂按同一图纸,采用相同的工艺方法的同批产品。
自制件:同一班次按同一图纸,采用相同的材料、工艺方法和设备的产品。
样本量(n):样本中产品数量样本的抽取:按简单随机抽样(见GB/T -1993的)从批中抽取作为样本。
样本可在制作完成后或在制作期间抽取。
由本公司自制件的首件必须报捡。
二次或多次抽样的样本应从同一批的剩余部分抽取。
正常、加严、放宽检验正常检验:在规定的时段或生产量内平均过程水平优于可允许的最差过程平均质量水平可使用正常检验方法。
加严检验:当预先规定的连续批数检验结果表明,在规定的时段或生产量内平均过程水平比可允许的最差过程平均质量水平低劣时,采用加严检验。
放宽检验:在预先规定连续批数的检验结构表明平均过程水平优于可接收的质量限时,可进行放宽的检验方法。
转换规则和程序初次检验中连续5批或少于5批中有1批是不可接收的,则转移到加严检验。
加严检验后如果初次检验的接连5批已经被认为是可接收的,应恢复正常检验。
抽样检验标准概述

1.0
0 合格批
α β
生产方 风险率
使用方 风险率
不合格批
一个较好的抽样方案应该由生产方和使用方共同协商,对p0和p1进行通盘 考虑,使生产者和使用者的利益都受到保护。
(3) OC曲线与N、n、Ac的关系
①n、Ac不变,N变化
抽样方案(?,20,0)
结论:
批量大小对OC曲线影响 不大,当N/n≥10时,就可 以采用不考虑批量N影响的 抽样方案。
结论:
大批严,小批宽。
p198
8.3 计数标准型抽样检验
一、计数标准型抽样检验的概念和特点
概念: 同时严格控制生产方与使用方的风险,按供需双方 共同制定的OC曲线所进行的抽样检验。
注:
它同时规定对生产方 的质量要求和对使用方 的质量保护。
A
1.0
生产者 风险点
α β
使用方 风险点
B
一般规定:
0
合格批
理论公式: 计算公式:
k:批数 Ni:第i批产品的批量 Di:第i批产品的不合格数 P_bar:过程平均不合格品率
注:估计过程平均的批数一般不少于20批,且每批不是再次提
交检验的批。
8.2 抽样检验特性曲线
一、抽样方案的接收概率
(1)接收概率的定义 是指根据规定的抽样方案,把具有给定质量水平的检验
(2)按抽样的次数分类
一次抽样检验:只抽取一次样本,就做出是否接收判定的 抽样检验。
批量N
样本n
统计样本中的不合格数d
d≤Ac 接收
d≥Re 不接收
二次或者多次抽样检验: 抽取第一次样本就能够做出是否接收的结论时,则抽样
检验工作终止;否则,再抽取二次或者多次样本,直到最后 做出判定。
抽样检验标准

16-25
26-50
51-90
91-150
AQL抽样方案
3.正常检验二次抽样方案
批量 151-280 281-500 501-1200 1201-3200 3201-10000 10001-35000 35001-150000 150001-500000 样本 第一次 第二次 第一次 第二次 第一次 第二次 第一次 第二次 第一次 第二次 第一次 第二次 第一次 第二次 第一次 第二次 样本量 20 20 32 32 50 50 80 80 125 125 200 200 315 315 500 500 累计样本量 20 40 32 64 50 100 80 160 125 250 200 400 315 630 500 1000 1.5 0/2 1/2 0/3 3/4 1/3 4/5 2/5 6/7 3/6 9/10 5/9 12/13 7/11 18/19 11/16 26/27 2.5 0/3 3/4 1/3 4/5 2/5 6/7 3/6 9/10 5/9 12/13 7/11 18/19 11/16 26/27 11/16 26/27 4.0 1/3 4/5 2/5 6/7 3/6 9/10 5/9 12/13 7/11 18/19 11/16 26/27 11/16 26/27 11/16 26/27 6.5 2/5 6/7 3/6 9/10 5/9 12/13 7/11 18/19 11/16 26/27 11/16 26/27 11/16 26/27 11/16 26/27
AQL抽样方案
2.正常检验一次抽样方案的使用
抽样表使用举例:(基于严重瑕疵AQL2.5;轻微瑕疵AQL4.0) 抽样表使用举例: 1)假设一批待查验货品的数量为450件(套),则需要随机抽取 50件查验样品 2)对50件样品进行查验,并对发现的瑕疵进行分类和记录 3)出现下列任何情况之一者,此批货品最终的查验结果都为不合格 A.发现的严重瑕疵数大于3 B.发现的次要瑕疵数大于5 C.发现的尺寸不良数根据AQL4.0标准判定不合格
10 0001 抽样检验标准

抽样检验标准1适用范围适用于品管部门的抽样检验。
2目的为使进料检验、出货检验、入货检验时有正确的抽样方法及判断依据。
3用语定义3.1抽样检验:即从群体中随机抽出一定数量的样本,经过试验或测定以后,以其结果与判定基准作比较,然后利用统计方法,判定此群体是合格或不合格的检验过程。
3.2缺陷定义:3.2.1致命缺陷(CritiCa1):是指缺陷可能会危及人身生命及安全,例如触摸部位的气孔堵塞、尖点、利边等。
3.2.2主要缺陷(Uajor):是指缺陷存在会影响到产品的使用功能,4.2.3轻微缺陷(MajOr):是指缺陷的存在只影响外观效果,不影响使用功能。
4.工作程序4.1采用GB2828抽样方案1. 1.1决定质量标准:决定检验项目及判定规格。
4. 1.2决定质量允收水准(AQ1)。
5. 1.3决定检验批数量。
6. 1.4求样本代字码。
7. 1.5查出抽检方式1)由抽样计划表查出样本的代字的行。
2)由抽样计划表查出所指定允许水准(AQ1)的列。
3)由样本代字的行与允许水准(AQ1)的列的交会点,查出接收(Ae)数及拒收(Re)数。
8. 1.6由样本代字查出抽取样本数no9. 1.7抽取样本。
10.1.8测定样本,并判定群体批是接收还是拒收11..9当出现严重缺陷的允收水准(AQ1)与轻微缺陷的允许水准(AQ1)得到不同的样本大小时,以严重缺陷的允收水准(AQ1)的样本大小取样,并以此样本数的行与允收水准(AQ1)的列的交会点,查出接收(Ae)数与拒收(Re)数,作为判定的基准。
若样本数的行与允许水准(AQ1)的列的交会点是箭头,则沿着箭头方向,查出箭头所指的第一组接收(AC)数与拒收(Re)数,作为判定的基准。
4.1.10准)。
致命缺陷(CritiCa1) AQ1:0.01主要缺陷(MajOr) AQ1:0.65轻微缺陷(Major) AQ1:1.54.2采用正常一次抽样方案的流程4.2.1决定检验项目、质量标准和各缺陷的接收限。
抽样检验标准完整版

抽样检验标准HUA system office room 【HUA16H-TTMS2A-HUAS8Q8-HUAH1688】抽样检验标准1. 目的:为使进料检验、过程检验、成品检验时有正确之抽样方法及判定依据。
2. 范围:进料检验、过程检验、成品检验均适用本规范。
3. 权责:由进料、过程、成品检验员负责实施之。
4. 定义:4. 1 单位产品: 为实施抽样检查的需要而划分的基本单位,称为单位产品。
4. 2 检查批: 为实施抽样检查汇集起来的单位产品称之为检查批,简称为批。
4. 3 批量: 批中所包含的单位产品数,称为批量。
4. 4 样本单位: 从批中抽取用检查的单位产品,称为样本单位。
4. 5 样本: 样本单位的全体,称为样本。
4. 6 样本大小: 样本中所包含的样本单位数,称为样本大小。
4. 7 抽样检验:依照批量大小,抽出不同数量的样本,将该样本按其规格进行检验,并将检验的结果与预先决定的品质标准比较,以决定个别的样品是否合格。
4. 8 不良率: 不良品的表示方法。
任何已知数量的制品不良率,为制品中所含的不良品数除以单位产品的总数再乘以100%即得:不良率=? 不良品个数 *100%检验单位产品总数4. 9 检验方法: 用检验、量测、试验或其它方式将单位产品和其规定的要求加以比较的方法。
4. 10 抽样计划: 样本大小和判定数组结合在一起,称为抽样计划。
4. 11 抽样程序: 使用抽样计划判断批合格与否的过程,称为抽样程序。
4. 12类别:根据产品质量性能和使用过程的重要程度,由高到低依次分为A、B、C 三类。
A类:成品及构成产品的最主要原料。
其质量直接影响最终产品的质量性能,严重的可能直接导致产品报废。
B类:半成品及重要原材料。
其质量直接影响产品的质量性能,导致产品重要性能指标的下降。
C类:一般原材料,可以根据情况进行检测,备案。
不会对产品的主要性能产生影响,不直接影响产品的应用性能。
说明:原材料分级规定详见附件《原材料分类》5作业内容:5.1 A类原材料需100%检测,B类抽检,C类凭合格证检验,抽样比率如下:5.2 采购回的物品必须检测其产品合格证,检测其产品规格或技术参数是否符合本公司采购的要求,强制性产品必须检查是否印有3C标志及合格证。
产品抽样检验标准

a.从正常检验到加严检验
当进行正常检验时,若在连续五批来料中有两批经检验不合格,则后续来料转到加严检验。
b.从加严检验到正常检验
当进行加严检验时,若连续五批来料合格,则后续来料转到正常检验。
c.从正常检验到放宽检验
当进行正常检验时,若连续10批来料检验合格,则后续来料转到放宽检验。
4. 8不良率:不良品的表示方法。
任何已知数量的制品不良率,为制品中所含的不良品数除以单位产品的总数再乘以100%即得:
不良率=不良品个数*100%
检验单位产品总数
4. 9检验方法:用检验、量测、试验或其它方式将单位产品和其规定的要求加以比较的方法。
4. 10抽样计划:样本大小和判定数组结合在一起,称为抽样计划。
为使进料检验、制程检验、成品检验时有正确之抽样方法及判定依据。
2.范围:
进料检验、制程负责实施之。
4.定义:
4. 1单位产品:为实施抽样检查的需要而划分的基本单位,称为单位产品。
4. 2检查批:为实施抽样检查汇集起来的单位产品称之为检查批,简称为批。
4. 3批量:批中所包含的单位产品数,称为批量。
4. 4样本单位:从批中抽取用检查的单位产品,称为样本单位。
4. 5样本:样本单位的全体,称为样本。
4. 6样本大小:样本中所包含的样本单位数,称为样本大小。
4. 7抽样检验:依照批量大小,抽出不同数量的样本,将该样本按其规格进行检验,并将检验的结果与预先决定的品质标准比较,以决定个别的样品是否合格。
4. 11抽样程序:使用抽样计划判断批合格与否的过程,称为抽样程序。
4. 12符号:
N:批量n:样本大小
Ac:合格判定数(允收数) Re:不合格判定数(拒收数)
- 1、下载文档前请自行甄别文档内容的完整性,平台不提供额外的编辑、内容补充、找答案等附加服务。
- 2、"仅部分预览"的文档,不可在线预览部分如存在完整性等问题,可反馈申请退款(可完整预览的文档不适用该条件!)。
- 3、如文档侵犯您的权益,请联系客服反馈,我们会尽快为您处理(人工客服工作时间:9:00-18:30)。
1.目的
建立公司所有检验的操作标准。
2.适用范围
本标准适用于公司如下的所有检验:
2.1公司所有成品:大小臂、挖斗、振动锤、松土器、贝型斗、抓钳器、油缸、抓爪、快换
接头等。
2.2产品加工过程:下料工序、拼装与焊接工序、装配工序、打磨与喷砂工序、喷油漆工序。
2.3厂内机械加工零配件。
2.4所有外购、外协件。
3.参考资料
3.1《结构件制造技术标准》
3.2《大小臂焊接检验标准》
3.3《挖斗斗耳末端焊接规定》
3.4《外协件管理暂行规定》
3.5《焊接工艺改进方案》
3.6《打磨喷漆检验标准》
3.7《油缸制作、检验标准》
3.8JH/OP04《不合格品管理程序》
3.9JH/OP14《计量器具管理程序》
3.10《质检员的岗位职责》
3.11JH/OP02《质量记录管理程序》
4.职责
4.1质管部质检员检查、判定、记录、处置及汇报。
4.2技术研发中心负责各类产品或物料的技术要求、图纸。
4.3物流部负责提供外购、外协件的相关规格书或供应商的检验报告。
5.程序
5.1缺陷分类等级
5.1.1严重不符合:包括原材料的化学成份、机械性能及产品结构、焊接不符合要求,
结果会危及产品的使用安全或使用寿命的不合格项。
5.1.2一般不符合:包括尺寸、装配、包装的不符合要求,结果会影响产品的正常使
用、对公司造成一定损失或返工的所有不合格项。
5.1.3轻微不符合:包括外观、颜色、来料标识等不符合,结果会一般影响产品的美
观、影响来料品质判定的所有不合格项。
5.2检验依据
5.2.1公司成品(见2.2条)、过程加工工序(见2.3条)及厂内机械加工零配件检
验按技术研发中心的规定要求及标准(见3.1至3.7参考文件)、图纸检验及
相关技术规定检测。
5.2.2外购、外协件按技术部规定的相关要求或图纸、及供应商的规格书与检验报告
为依据验收判定。
5.3抽样规定
5.3.1公司所有成品(见2.2条)及过程加工工序(见2.3条)检验按100﹪全检。
5.3.2厂内机械加工零配件及所有外购、外协件按GB/T2828规定的一般检验水平Ⅱ等
级抽样(见附件6.1)。
5.4合格与不合格判定准则
5.4.1公司所有成品(见2.2条)及过程加工工序(见2.3条):按5.2.1条款要求
进行检验,当所有检查项目符合规定要求,则判定该产品或该过程为合格品或
合格;若检验结果有一项或以上不满足要求,则判定为该产品或该过程不合格。
5.4.2厂内机械加工零配件及所有外购、外协件:按5.2.2条款要求进行检验,若检
验结果所有样口均满足规定要求,则判为该批产品合格。
若在样品中发现不合
格,按如下判定:
5.4.2.1严重不符合、一般不符合按GB2828正常检查一次抽样方案的0.65AQL
值(见附件6.2)合格质量水平判定,样品中发现不合格品数在AQL
值范围内,则判为此批为合格批,不合格品数在AQL值拒收范围内,
则判为此批为不合格批。
5.4.2.2轻微不符合按GB2828正常检查一次抽样方案的1.5AQL值(见附件
6.2)合格质量水平判定,样品中发现不合格品数在AQL值范围内,
则判为此批为合格批,不合格品数在AQL值拒收范围内,则判为此批
为不合格批。
5.5不合格品处置
5.5.1按JH/OP04《不合格品管理程序》(参考3.8参考文件)程序要求执行。
5.6质检器具要求
5.6.1质检员的测量器具应能满足产品或来料的检测需要,其精度等级不低于测量尺
寸的精确度。
5.6.2需计量的仪器按JH/OP14《计量器具管理程序》程序(参考3.9参考文件)要
求执行。
5.7质检员的资格
5.7.1质检员应有足够的能力胜任《品质检验员的岗位职责》(参考3.10参考文件)。
5.7.2部门通过技能培训、检验方法的提高能确保品检员完成公司的所有检测过程。
5.8记录
5.8.1完成每天的各类来料、过程、成品检验记录。
5.8.2记录必须是反映试验或测量过程的客观事实。
5.8.3记录按JH/OP02《质量记录管理程序》程序(参考3.11参考文件)要求控制。
6.附录
6.1附表:GB/T2828.1样本字码
6.2附表:GB/T2828.1-2003正常检查一次抽样方案(Ⅱ级检验水平)
制订陈秉强审核批准
附录6.1
附录6.2。