外文翻译--应用参数动力学研究蜗杆与蜗轮的旋转角度-精品
中英文文献翻译—动力传动技术难点分析

附录APower transmission technology difficulty analysis1 And power system working characteristicsElectric vehicle has the advantages mainly in the following aspects:(1)Compared with the same kind of car engine emission reduction.(2) The motor as auxiliary power, to make the engine can play in good conditions, the efficiency of work and through the recycling braking energy, improve the vehicle's fuel economy.(3) By decrease engine load reduces the noise.(4) Transformed at present only gas stations, does not need to invest in new fuel loading.2, Planet row the characteristic of structure series(1) The engine is always in the best condition driving generators, so high efficiency, energy saving effect, have certain emissions, reduce pollution and low;(2) Installed the engine-generator, flowing energy feed to the traction motor, compared with the electric car trip mileage improved significantly;(3) Control system function, structure is simple, especially the operation control only generator according to the storage battery charging and discharging state decided to power or stopped.3. Selection strategy3.1 A motor vehicles in China for the development of has just started, to speed up the development of the hybrid products in China, the research and use for reference foreign results is very necessary. Power system selection in hybrid developing in a position of importance. Because of the different control strategy is based on a hybrid drive system for making and optimization. Can say power system structure types of the option to decide the hybrid of research and development, the relationship between key development progress and product the level, is the most important of HEV development and the key step. So the development must be in deep research of careful analysis and weigh the advantages and disadvantages, and on the basis of the structure of the power system type make discreet choice. In the development of comprehensive coordination performance should be advanced,technical complexity and costs and maintenance cost, according to the relationship between the use of cars conditions and their technical conditions, choose to meet the performance of both must be advanced, and not beyond the current technology conditions, and the price and maintenance costs for market acceptable to the power system type. Therefore, it is necessary to consider the following factors: (1) Motor drive power system based on particular condition commonly carry on the design. This is because most of the power system is more sensitive to working conditions, different operating conditions of the performance difference is very big, only in specific conditions to be fully low oil consumption, low emission advantages. (2) Different types of hybrid differences between performance is very clear, in the selection of the power system must be caused by the difference between performance to structure sufficient attention. If demand is high for acceleration performance, it is necessary to choose equipped with the structure of peak power regulator type; If the economy too hard, tandem, we cannot be the right choice. (3) The technical conditions, in addition to developing the conditions and power outside, still include industrial base. Stressed because of some common industrial base of power system in China, the components of the product level can not meet the requirements or still cannot production. In the actual product development will always have a certain schedule, if the technology conditions cannot be, it will be difficult to guarantee for achieving the development plan. Necessary to explore for his technical conditions especially industrial base of hybrid structure types, advocate structure innovation. (4)Open power system is to point to the need to further develop the space. Product performance is a gradually perfect process, the same development work might not one pace reachs the designated position, also need to have been the perfect. In the specific development work should be followed from the simple to the complex, from easy to difficult train of thought, to choose the technical conditions of the low required appropriate simple structure, development.(5) The structure of the power system of hybrid cost impact, this is because different types of power system for the kinds of components, the quantity and the performance requirements the difference is very big. And the kinds of components, the quantity and the performance index is the effect of the main factors of hybrid costs. Selection should also consider the use and maintenance costs, the more complex structure, the higher failure rate, use and maintenance cost is higher. Price and maintenance expenses directly related to the industrialization of HEV, if can't industrialization, can provide the necessary for further development of the capital, it will be difficult to promote and raisingthe level of technology to improve the performance of. In fact, the fine performance but because the price too high to commercialization, and even forced to give up the development of HEV examples not rarely seen, we should not repeat it.In view of our country at present the city's air pollution problems and oil shortages are very serious, and the technological basis of weak, preference hybrid system should be relatively simple structure, applicable to general city mode of the structure and the working condition between the cities series of parallel structure, and to buses and cars as a key development targets.It a: a hybrid car engine starting on and off, make frequent driving system and accessories (such as air conditioning and power steering, etc) of power management is complicated, so need advanced detection and control system; The existing to heat engine primarily hybrid unit in the fuel into YouYongGong at the same time, needs to improve the efficiency of conversion, and also to meet strict emission standard.Second: energy storage device (battery) to have higher than power, to meet the car accelerated and climbing to the need of high power when; At the same time, energy storage device must use heat control management, want to have higher than energy, long service life and low production cost.Third: must reduce the size of the power electronics device, reduce the quality and reduce production cost.Its 4: need to build a more advanced driving system mathematical model (including static and dynamic), is this the computer simulation and analysis of the foundation.Its 5: make perfect hybrid cars of relevant standards and regulations, for hybrid cars, which laid the foundation of the market.3.2 Electric drive system and car accessoriesTo make a hybrid car of the power, economy, comfort, safety and convenience to consumers can acceptable level, there must be efficient and economic power drive system and car accessories. However, the system of some components in the traditional car without a corresponding parts, so need to development design. In development at the same time, want to consider the system synthesis performance, costs and maintenance performance.1) Motor in a hybrid car, motor is the role of the generator or energy storage device provide electrical energy into mechanical energy is used to drive the wheels. And the traditional automobile different is, motor speed can provide in full, and engine torque must be to waituntil "mad" can only output loaded with torque. This makes hybrid cars have excellent starting and accelerating performance. In addition, used for a hybrid car motor must have good controllability and fault tolerance, and low noise, high efficiency, and is not sensitive to the voltage fluctuations and performance.Used for a hybrid car motor type has ac induction motor, permanent magnet motor and switched reluctance motor. At present the typical is ac induction motor, but this kind of motor are born is difficult to solve the contradiction between power and efficiency. Therefore, we need to study out can be used for hybrid cars, have higher efficiency and power density of permanent magnet motor, switched reluctance motor, and other advanced motor, to replace current use of ac induction motor. At the same time for the motor control method and the cooling system research also should go further.2)Regenerative braking, this kind of hybrid cars can recycle braking energy consumption part of. When a hybrid car brake, motor, generator, using cars into the kinetic energy to produce electricity, and can be stored in battery in it for later. In hybrid cars, there are many form of energy can be used as the regenerative braking energy storage device, such as high-speed flywheel, super capacitor, elastic device and all kinds of thermal system, etc. Of course, the traditional friction braking is necessary, so you need to consider how to two sets of braking equipment reasonable use, reasonable, and the problems of control. Braking, the electronic control system of the regenerative braking and friction braking system at the same time, the braking performance will be improved.3) Car accessories, any style of car to get consumers and all must consider the car comfort. The automobile air-conditioning accessories can improve the car of comfort, but energy use is very big, if not reduce the load, they will be for the automobile fuel economy have a huge impact. So, whether in the car at the same time, improve the comfort to improve fuel economy is at present to innovation of research. Traditional bus attachments system on the engine design, not for hybrid cars drive system. For example, the traditional automobile accessories (such as air condition, power steering, etc) by the engine drive, but because the hybrid car engines are not always work, need to design and production can the independent powered accessories. Be like again, because a hybrid car engine frequently starting and close, make its drive system and accessories for the power management complicated, need to have a more advanced monitoring and control system.3.3 A hybrid car simulation technologyIn the research and development of a hybrid car components and choose the best structure, need to design and maker can quickly reduce research scope, find technical breakthrough. Technical scheme selection stages, in the system the choice, can rely on efficient modeling tools computer, through the alternate use of candidate subsystems simulation, so as to find the best solutions. Computer models for each candidate subsystem provides a detailed specifications and design parameters, and convenient to the designer's work, but also to make model for designing and manufacturing engineering target and plan.Now, the responsible for electric cars and hybrid vehicles standards and regulations is the organization of the international electrotechnical commission (IEC), the international organization for standardization (ISO), the American auto engineers association (SAE), etc. For our country, because of hybrid cars are already in the experimental stage, and all the standards work should begin corresponding. For future will appear DuoZhong driving car coexistence, car standards will also need to consider the traditional automobile, hybrid cars and pure electric vehicle the comparability between universality and.附录B动力传动技术难点分析1、动力系统工作特点动力汽车所具备的优点主要表现在以下几个方面:(1)与同类发动机车型相比, 排放降低。
旋转泵论文中英文对照资料外文翻译文献

中英文对照资料外文翻译文献附件1:外文资料翻译译文旋转泵旋转泵应用于不同的设计中,在流体动力系统中极其常用。
今天最常用的旋转泵是外齿轮泵、内齿轮泵、摆线转子泵、滑动叶片泵和螺旋泵。
每种类型的泵都有优点,适合于特定场合的应用直齿齿轮泵,这种泵有两个啮合的齿轮在密封壳体内转动。
第一个齿轮即主动轮的回转引起第二个齿轮即从动轮的回转。
驱动轴通常连接到泵上面的齿轮上。
当泵首次启动时,齿轮的旋转迫使空气离开壳体进入排油管。
这种泵内空气运动使泵吸入口处形成了真空,于是外部油箱的液体在大气压的作用下,由泵的入口进入,聚集在上下齿轮和泵壳体之间,齿轮连续的旋转使液体流出泵的出口。
直齿齿轮泵的压力的升高是由挤压啮合齿轮和腔体内的液体产生的。
当齿轮脱开啮合时,腔内形成真空,使更多的液体被吸入泵内。
直齿齿轮泵是定排量的元件,当轴转速不变时,输出流量恒定。
只有一种方法即改变输入轴的转速,能调节这种直齿齿轮泵的排量。
现代应用在流体动力系统的齿轮泵的压力可达3000psi。
图示为直齿齿轮泵的典型特性曲线。
这些曲线表明了泵在不同速度下的流量和输入功率。
当速度给定时,流量曲线接近于一条水平的直线。
泵的流量随出口压力的升高而稍有降低,这是由于泵的出油口到吸油口的齿轮径向泄漏所增加而造成的。
渗漏有时定义为泄漏,泵出口压力的增加也会使泄漏增加。
表征泵的出口压力和流量之间关系曲线常叫做水头流量曲线或泵的HQ曲线;泵的输入功率和泵流量关系曲线叫做功率流量特性曲线或PQ曲线。
直齿齿轮泵的输入功率随输入速度和出口压力的增加而增加。
随着齿轮泵速度的增加,流量(加仑/分)也增加。
于是在出口压力为120psi,转速为200rpm时,输入功率是5马力。
在转速为600rpm时,输入功率是13马力。
纵坐标压力是120psi,横坐标是200rpm和600rpm时,在HQ曲线上可以读出相应的流量分别为40gpm和95gpm。
图示是直齿齿轮泵在粘度不变时的情况。
机械制造专业英语(章跃版)课后句子翻译答案

第一单元应力与应变That branch of scientific analysis which motions, times and forces is called mechanicsand is made up of two parts, statics and dynamics.研究位移、时间和力是科学分析法的一个分支,被称作力学,力学由两大部分组成,静力学和动力学。
For example, if the force operating on a sleeve bearing becomes too high, it will squeeze out the oil film and cause metal-to-metal contact, overheating and rapid failure of the bearing.例如:如果止推轴承上的作用力过大的话,会挤出油膜,引起金属和金属之间的相互接触,轴承将过热而迅速失效。
Our intuitive concept of force includes such ideas as place of application, direction, and magnitude, and these are called the characteristics of a force.力的直观概念包括力的作用点、大小、方向,这些被称为力的三要素。
All bodies are either elastic or plastic and will be deformed if acted upon by forces. When the deformation of such bodies is small, they are frequently assumed to be rigid, i.e., incapable of deformation, in order to simplify the analysis.所有的物体既可以是弹性的也可以是塑性的,如果受到力的作用就产生变形。
franz-morat蜗轮减速机原理

franz-morat蜗轮减速机原理蜗轮减速机是一种重要的传动装置,它主要由蜗轮、蜗杆、机壳和输出轴组成。
蜗轮减速机能将高速旋转的电机输出转变为低速、高扭矩的输出,适用于各种行业,如冶金、化工、食品、包装等。
以下将介绍蜗轮减速机的原理及其工作过程。
1. 蜗轮减速机的原理蜗轮减速机靠蜗杆螺旋线的啮合与蜗轮的齿合来实现实现减速的功能。
蜗轮是一个双头斜齿轮,其齿呈螺旋线形状,与蜗杆的螺旋线相互啮合,蜗杆则是一个滚柔的螺旋形轴。
直接传动,可实现大功率、低转速的传动。
同时,蜗杆与蜗轮啮合时,由于其啮合面的摩擦力,也能实现自锁效果,防止发生自然逆转。
由于蜗轮和蜗杆的啮合角度非常小,故理论上该设备的效率非常低,但在工业生产中,正常情况下,其效率也能达到70%以上,可满足大部分使用要求。
在蜗轮减速机运转时,电机将高速输出的动力传递给减速机,减速机通过蜗杆和蜗轮的啮合,将高速旋转的动力转换为低速。
传动时,蜗杆和蜗轮的啮合点处既有滚动摩擦,也有滑动摩擦。
由于材料和表面的选择,确保摩擦力和摩擦系数的合理,并添加一定的润滑和冷却措施,可进一步提高传输效率和延长使用寿命。
另外,在蜗杆与蜗轮的啮合过程中,由于其齿轮结构的分离性,蜗杆可单独输入功率,而蜗轮单独输出功率,能够灵活地实现各种传动转速的变化。
同时,由于蜗轮减速机的运转速度很慢,可通过多级减速来进一步满足各种需求,提高其使用的灵活性和多样性。
综上所述,减速机是一个非常重要的行业关键件,应用面广泛,服务于各个领域。
蜗轮减速机凭借其特有的工作原理和性能优势,成为重要型号之一。
在未来的工业生产中,蜗轮减速机的应用领域还将增加,市场需求也将逐渐扩大。
俄语阅读:中俄对照:涡轮钻井【译文】

俄语阅读:中俄对照:涡轮钻井【译文】ТУРБИНОЕ БУРЕНИЕ СКВАЖИН 涡轮钻井Турбинное бурение отличается от роторного тем, что буровой двигатель--турбобур--устанавливают в скважине непосредственно над долотом. Промывочная жидкость, протекающая через турбобур. Заставляет вращаться его вал. На котором навинчено долото, а корпус турбобура вместа сбурильными трубамиостаётся неподвижным.涡轮钻井与转盘钻井不同之处是涡轮发动机(涡轮钻机)要沉到井下直接安装在钻头顶上。
流过涡轮钻具的冲洗液使已拧上钻头的钻具轴旋转,钻具壳连同钻杆则保持不动。
Для того чтобы при заклинивании долота корпус турбобура вместе с бурильными трубами не начал вращаться в обратную сторону, верхнюю часть бурильных труб застопоривают в роторе, имеющем для этого специальное стопорноеустройство. Поверхностноеоборудование при турбинномбурении отличается отоборудования при роторномбурении значительноувеличенной мощностьюнасосной группы.为防止卡住钻头时钻具壳连同钻杆向反方向旋转,将钻杆上部锁定在有专门制动装置的转盘上涡轮钻井的地面设备与转盘钻井不同,泵组的功率相当大。
机械类外文文献及翻译
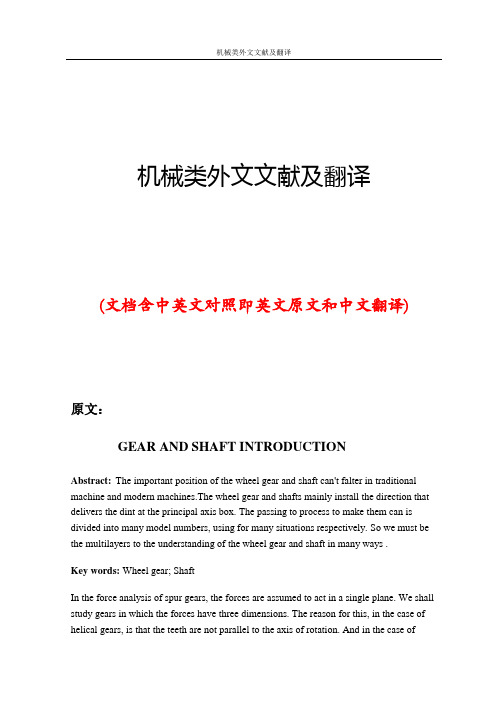
机械类外文文献及翻译(文档含中英文对照即英文原文和中文翻译)原文:GEAR AND SHAFT INTRODUCTIONAbstract:The important position of the wheel gear and shaft can't falter in traditional machine and modern machines.The wheel gear and shafts mainly install the direction that delivers the dint at the principal axis box. The passing to process to make them can is divided into many model numbers, using for many situations respectively. So we must be the multilayers to the understanding of the wheel gear and shaft in many ways .Key words: Wheel gear; ShaftIn the force analysis of spur gears, the forces are assumed to act in a single plane. We shall study gears in which the forces have three dimensions. The reason for this, in the case of helical gears, is that the teeth are not parallel to the axis of rotation. And in the case ofbevel gears, the rotational axes are not parallel to each other. There are also other reasons, as we shall learn.Helical gears are used to transmit motion between parallel shafts. The helix angle is the same on each gear, but one gear must have a right-hand helix and the other a left-hand helix. The shape of the tooth is an involute helicoid. If a piece of paper cut in the shape of a parallelogram is wrapped around a cylinder, the angular edge of the paper becomes a helix. If we unwind this paper, each point on the angular edge generates an involute curve. The surface obtained when every point on the edge generates an involute is called an involute helicoid.The initial contact of spur-gear teeth is a line extending all the way across the face of the tooth. The initial contact of helical gear teeth is a point, which changes into a line as the teeth come into more engagement. In spur gears the line of contact is parallel to the axis of the rotation; in helical gears, the line is diagonal across the face of the tooth. It is this gradual of the teeth and the smooth transfer of load from one tooth to another, which give helical gears the ability to transmit heavy loads at high speeds. Helical gears subject the shaft bearings to both radial and thrust loads. When the thrust loads become high or are objectionable for other reasons, it may be desirable to use double helical gears. A double helical gear (herringbone) is equivalent to two helical gears of opposite hand, mounted side by side on the same shaft. They develop opposite thrust reactions and thus cancel out the thrust load. When two or more single helical gears are mounted on the same shaft, the hand of the gears should be selected so as to produce the minimum thrust load.Crossed-helical, or spiral, gears are those in which the shaft centerlines are neither parallel nor intersecting. The teeth of crossed-helical fears have point contact with each other, which changes to line contact as the gears wear in. For this reason they will carry out very small loads and are mainly for instrumental applications, and are definitely not recommended for use in the transmission of power. There is on difference between a crossed heli : cal gear and a helical gear until they are mounted in mesh with each other. They are manufactured in the same way. A pair of meshed crossed helical gears usually have the same hand; that is ,a right-hand driver goes with a right-hand driven. In the design of crossed-helical gears, the minimum sliding velocity is obtained when the helix angle areequal. However, when the helix angle are not equal, the gear with the larger helix angle should be used as the driver if both gears have the same hand.Worm gears are similar to crossed helical gears. The pinion or worm has a small number of teeth, usually one to four, and since they completely wrap around the pitch cylinder they are called threads. Its mating gear is called a worm gear, which is not a true helical gear. A worm and worm gear are used to provide a high angular-velocity reduction between nonintersecting shafts which are usually at right angle. The worm gear is not a helical gear because its face is made concave to fit the curvature of the worm in order to provide line contact instead of point contact. However, a disadvantage of worm gearing is the high sliding velocities across the teeth, the same as with crossed helical gears.Worm gearing are either single or double enveloping. A single-enveloping gearing is onein which the gear wraps around or partially encloses the worm.. A gearing in which each element partially encloses the other is, of course, a double-enveloping worm gearing. The important difference between the two is that area contact exists between the teeth of double-enveloping gears while only line contact between those of single-enveloping gears. The worm and worm gear of a set have the same hand of helix as for crossed helical gears, but the helix angles are usually quite different. The helix angle on the worm is generally quite large, and that on the gear very small. Because of this, it is usual to specify the lead angle on the worm, which is the complement of the worm helix angle, and the helix angle on the gear; the two angles are equal for a 0-deg. Shaft angle.When gears are to be used to transmit motion between intersecting shaft, some of bevel gear is required. Although bevel gear are usually made for a shaft angle of 0 deg. They may be produced for almost any shaft angle. The teeth may be cast, milled, or generated. Only the generated teeth may be classed as accurate. In a typical bevel gear mounting, one of the gear is often mounted outboard of the bearing. This means that shaft deflection can be more pronounced and have a greater effect on the contact of teeth. Another difficulty, which occurs in predicting the stress in bevel-gear teeth, is the fact the teeth are tapered.Straight bevel gears are easy to design and simple to manufacture and give very good results in service if they are mounted accurately and positively. As in the case of squr gears, however, they become noisy at higher values of the pitch-line velocity. In these cases it is often go : od design practice to go to the spiral bevel gear, which is the bevel counterpart of thehelical gear. As in the case of helical gears, spiral bevel gears give a much smoother tooth action than straight bevel gears, and hence are useful where high speed are encountered.It is frequently desirable, as in the case of automotive differential applications, to have gearing similar to bevel gears but with the shaft offset. Such gears are called hypoid gears because their pitch surfaces are hyperboloids of revolution. The tooth action between such gears is a combination of rolling and sliding along a straight line and has much in common with that of worm gears.A shaft is a rotating or stationary member, usually of circular cross section, having mounted upon it such elementsas gears, pulleys, flywheels, cranks, sprockets, and other power-transmission elements. Shaft may be subjected to bending, tension, compression, or torsional loads, acting singly or in combination with one another. When they are combined, one may expect to find both static and fatigue strength to be important design considerations, since a single shaft may be subjected to static stresses, completely reversed, and repeated stresses, all acting at the same time.The word “shaft” covers numerous v ariations, such as axles and spindles. Anaxle is a shaft, wither stationary or rotating, nor subjected to torsion load. A shirt rotating shaft is often called a spindle.When either the lateral or the torsional deflection of a shaft must be held to close limits, the shaft must be sized on the basis of deflection before analyzing the stresses. The reason for this is that, if the shaft is made stiff enough so that the deflection is not too large, it is probable that the resulting stresses will be safe. But by no means should the designer assume that they are safe; it is almost always necessary to calculate them so that he knows they are within acceptable limits. Whenever possible, the power-transmission elements, such as gears or pullets, should be located close to the supporting bearings, This reduces the bending moment, and hence the deflection and bending stress.Although the von Mises-Hencky-Goodman method is difficult to use in design of shaft, it probably comes closest to predicting actual failure. Thus it is a good way of checking a shaft that has already been designed or of discovering why a particular shaft has failed in service. Furthermore, there are a considerable number of shaft-design problems in which the dimension are pretty well limited by other considerations, such as rigidity, and it is only necessary for the designer to discover something about the fillet sizes, heat-treatment,and surface finish and whether or not shot peening is necessary in order to achieve the required life and reliability.Because of the similarity of their functions, clutches and brakes are treated together. In a simplified dynamic representation of a friction clutch, or brake, two in : ertias I and I traveling at the respective angular velocities W and W, one of which may be zero in the case of brake, are to be brought to the same speed by engaging the clutch or brake. Slippage occurs because the two elements are running at different speeds and energy is dissipated during actuation, resulting in a temperature rise. In analyzing the performance of these devices we shall be interested in the actuating force, the torque transmitted, the energy loss and the temperature rise. The torque transmitted is related to the actuating force, the coefficient of friction, and the geometry of the clutch or brake. This is problem in static, which will have to be studied separately for eath geometric configuration. However, temperature rise is related to energy loss and can be studied without regard to the type of brake or clutch because the geometry of interest is the heat-dissipating surfaces. The various types of clutches and brakes may be classified as fllows:. Rim type with internally expanding shoes. Rim type with externally contracting shoes. Band type. Disk or axial type. Cone type. Miscellaneous typeThe analysis of all type of friction clutches and brakes use the same general procedure. The following step are necessary:. Assume or determine the distribution of pressure on the frictional surfaces.. Find a relation between the maximum pressure and the pressure at any point. Apply the condition of statical equilibrium to find (a) the actuating force, (b) the torque, and (c) the support reactions.Miscellaneous clutches include several types, such as the positive-contact clutches, overload-release clutches, overrunning clutches, magnetic fluid clutches, and others.A positive-contact clutch consists of a shift lever and two jaws. The greatest differences between the various types of positive clutches are concerned with the design of the jaws. To provide a longer period of time for shift action during engagement, the jaws may be ratchet-shaped, or gear-tooth-shaped. Sometimes a great many teeth or jaws are used, and they may be cut either circumferentially, so that they engage by cylindrical mating, or on the faces of the mating elements.Although positive clutches are not used to the extent of the frictional-contact type, they do have important applications where synchronous operation is required.Devices such as linear drives or motor-operated screw drivers must run to definite limit and then come to a stop. An overload-release type of clutch is required for these applications. These clutches are usually spring-loaded so as to release at a predetermined toque. The clicking sound which is heard when the overload point is reached is considered to be a desirable signal.An overrunning clutch or coupling permits the driven member of a machine to “freewheel” or “overrun” bec ause the driver is stopped or because another source of power increase the speed of the driven. This : type of clutch usually uses rollers or balls mounted between an outer sleeve and an inner member having flats machined around the periphery. Driving action is obtained by wedging the rollers between the sleeve and the flats. The clutch is therefore equivalent to a pawl and ratchet with an infinite number of teeth.Magnetic fluid clutch or brake is a relatively new development which has two parallel magnetic plates. Between these plates is a lubricated magnetic powder mixture. An electromagnetic coil is inserted somewhere in the magnetic circuit. By varying the excitation to this coil, the shearing strength of the magnetic fluid mixture may be accurately controlled. Thus any condition from a full slip to a frozen lockup may be obtained.齿轮和轴的介绍摘要:在传统机械和现代机械中齿轮和轴的重要地位是不可动摇的。
机械制造专业英语4B原文及翻译(章跃主编)

CHAIN DRIVESChain drives occupy a unique position in the mechanical field.In a sense,they are similar to belt drives;a chain connects sprockets on the driving and driven shafts.The velocity ratio transmitted from one shaft to the other depends on the size of the two sprockets(at the pitch line);unlike that found with belts,the ratio is positive.In belt drive ,creep and slip play important roles and must be considered;in a chain drive,which is made up of numerous links,there is a small amount of play in the total length of the chain.This may be desirable in case of small overloads.A chain drive is similar to the open-belt type of dirve in that the driving and driven shafts rotate in the same direction.There are also similarities between chain drives and gear drives.Both types transmit a positive velocity ratio.In a regular spur-gear drive,the driving and driven shafts turn in opposite directions unless an idler is employed.In gear drives employing an annular or ring gear,however,the input and output shafts rotate in the same direction.In a spur-gear drive there is very little contact between meshing gears;therefore,tooth loads are excessive.Since the connection between a chain and its sprocket extends over several teeth,no one tooth is subjected to heavy loads.Chain drives are often noisy.The silent chain type of drive was developed to counteract this undesirable characteristic.Belt,chain,and gear drives are all dangerous.Belt and chain speeds are high,as is the pitch-line velocity of most gear drives.All should be adequately covered by suitable guards(or completely enclosed) so that no boby or clothing parts can possibly be caught in the moving components.Other comparisons can be made among chain,belt,and gear drives.Gear drives can operate at higher speeds than the others,and are usually more compact.However,chain drives do not require the mounting precision that is so essential for gearing.An advantage of chain drives in comparison to belt drives is that the former do not require tension on the slack side;this leads to better bearing life.In general,chain drives are more compact than the belt type;for a given ratio,the sprockets can be smaller than belt pulleys.For a given load,chain widths are narrower than comparable flat belts.The connecting link on chain drives makes them easy to install—the chain is merely placed over the sprockets and the proper pins are placed in position.In most belt installations,force is needed to place the belt in the proper position;such action is detrimental to mounting bearings.The angle of contact for the driving sprocket can be smaller than the driving pulley for a belt drive.For a chain drive,this angle can be as small as 120 degrees.The center distance can also be small;if a 120-degree angle of contact is provided,the center distance need be no more than just enough to provide clearance for the sprocket teeth.An essential part of any chain drive is the sprocket.A chain drive requires a sprocket on the driving shaft and another on the driven shaft.Chain drives sometimes contain additional sprockets,used for additional power take-offs or for taking up chain slack.When used to take up chain slack,they are known as idlers.Idlers should be mounted on the slack side,not on the tight side.It is desirable to have an adjustment for idler positioning where possible.Fig.4-5 showsa roller-chain sprocket.Sprocket teeth are standardized to accommodate the roller chain.Various sizes of sprockets may be used,and several types are available.The simplest type is one without a hub.Sprockets are also available with hubs on one side or on both sides.Special arrangements are also possible.Certain of these are used in conjunction with a shear-pin hub;the shear pin is designed to fail in case of an accidental or unexpected overload.Some types can be installed on large lineshafts;these sprockets are made in two parts so that they can be installed without disconnecting the long length of shafting.Smaller sprockets are usually made solid;large ones are sometimes constructed with arms or spokes to reduce weight.In general,the selection of a sprocket depends on the type of application.链传动链传动在机械领域中占据了独特的地位。
蜗轮蜗杆的原理及应用

蜗轮蜗杆的原理及应用蜗轮蜗杆是一种传动装置,其主要原理是利用蜗杆和蜗轮的齿轮副传动,是一种具有较大传动比的传动装置。
下面将从原理和应用两个方面进行详细阐述。
一、原理:1. 蜗杆的原理:蜗杆是一种带有斜拦齿的圆柱形螺旋齿轮。
其工作原理是通过蜗杆的旋转运动,使蜗杆周围的蜗轮做回转运动。
由于蜗杆的齿数较小,与蜗轮的齿数成比例,因此蜗轮的转速较蜗杆的转速明显降低,实现了较大的传动比。
蜗杆的斜拦齿使其具有自锁功能,可以防止传动系统的逆转。
2. 蜗轮的原理:蜗轮是一种带有蜗杆齿的轮形零件,与蜗杆配合使用。
蜗轮的齿数一般较大,与蜗杆的齿数成比例。
当蜗杆旋转时,由于蜗杆齿与蜗轮齿的啮合,使蜗轮做回转运动。
由于蜗轮的大齿数,因此蜗轮的转速很低。
同时,蜗轮与蜗杆的配合精度要求较高,以确保传动的可靠性和稳定性。
3. 蜗轮蜗杆的原理:蜗轮和蜗杆之间的齿轮传动原理使得蜗杆的转速大大降低,同时转矩升高。
蜗杆的斜拦齿具有自锁功能,可以防止传动系统的逆转。
由于蜗杆蜗轮的传动比一般较大(通常为1:40-1:300),因此蜗轮蜗杆传动被广泛应用于需要大传动比的场合。
二、应用:1. 工业领域:蜗轮蜗杆传动广泛应用于工业生产中的各种机械设备,如输送机、搅拌机、搅拌桨、起重机、冷冻机等。
这些设备一般需要大传动比,并且需要稳定的传动和较大的传动力矩。
2. 机械工程领域:在机械工程领域,蜗轮蜗杆传动也有着广泛的应用。
例如,在车辆的转向机构中,蜗轮蜗杆传动可以实现方向盘到车轮的传动;在船舶的舵机机构中,也可以利用蜗轮蜗杆传动实现舵的转动。
3. 精密仪器领域:蜗轮蜗杆传动由于其精度要求较高,常用于精密仪器中的传动装置。
例如,精密测量仪器、光学仪器、数控设备等,都可以采用蜗轮蜗杆传动实现精密传动和准确控制。
4. 机床工具领域:在机床工具领域,蜗轮蜗杆传动也得到了广泛应用。
例如,车床、铣床、钻床等机床中的进给机构,往往采用蜗轮蜗杆传动实现工件和刀具的精确进给。
- 1、下载文档前请自行甄别文档内容的完整性,平台不提供额外的编辑、内容补充、找答案等附加服务。
- 2、"仅部分预览"的文档,不可在线预览部分如存在完整性等问题,可反馈申请退款(可完整预览的文档不适用该条件!)。
- 3、如文档侵犯您的权益,请联系客服反馈,我们会尽快为您处理(人工客服工作时间:9:00-18:30)。
翻译部分英文原文Parametric study of dynamics of worm and worm-gear set undersuddenly applied rotating angleM.Y. Chung, D. ShawDepartment of Power Mechanical Engineering, National Tsing-Hua University, No. 101 Kung Fu Road Section II, Hsin Chu, Taiwan, ROC Received 13 September 2006; received in revised form 23 January 2007;accepted 25 February 2007Available online 17 April 2007AbstractThe dynamics of a worm-gear set under instantly applied rotating angle are affected by several factors (including thefriction force and elastic deformation of the surface between gear teeth). It is found that those factors cause a nonnegligible rotational positioning error. The goals of this study are to (1) set up a mathematic model, (2) carry out anumerical simulation, and (3) carry out an experiment and compare it with the numerical results. The experiments and numerical results have very good agreement. In this research, themoment-inertia of fly wheel, friction, rigidity of shaft andrigidity of gear tooth are also studied. The results can be used as error estimations of relevant angles, angular speed andangular acceleration under a suddenly applied rotational angle, and are useful for establishing the error compensationrequired for position control.1. IntroductionWhen radar tracks an aircraft which turns at a sharp angle; the radar may not be able to lock onto the target due to the small oscillation of the antenna. Sometimes, the oscillation even causes a failure of the radar system . Accurate positioning is a crucial subject in a tracking system. However, due to the design of the trackingtransmission mechanism is restricted by both space and weight, the volume and the weight of the transmissionmechanism must be limited. The worm-gear set is a good choice due to its small volume and high reduction ratio. Owing to the oscillation of the antenna is an important dynamics behavior forhigh precision positioningof radar system, the dynamics of a worm-gear set under instantly applied large torque is very important tounderstand this behavior. This behavior is affected by several factors including the friction force and elastic deformation of the surface between gear teeth. To understand the effect of those factors, a lot of research hasbeen conducted. Yuksel and Kahraman [1] studied the in.uence of surface wear on the dynamic behavior of a typical planetary gear set. The wear model employed a quasi-static gear contact model to compute contact pressures and Archard’s wear model to determine the wear depth distributions. Parker et al. [2] analyzed the dynamic response of a spur pair of a wide range of operating speeds and torques. Comparisons were made to other researchers’ published experiments that reveal complex nonlinear phenomena. The dynamic response of a spur pair was investigated using a .nite element/contact mechanics model that offers signi.cant advantages for dynamic gear analyses. Maliha [3] created a nonlinear dynamic model of a spur gear pair, which was coupled with linear .nite element models of the shafts carrying them, and with discrete models of bearings and disks. The excitations considered in the model were external static torque and internal excitation caused by mesh stiffness variation, gear errors and gear tooth pro.le modi.cation. Britton [4] produced a super .nished gear teeth (with a approximately 0.05 mm Ra Film) and the friction traction in the experiments were simulated theoretically using a thin .lm non-Newtonian micro-elastohydrodynamic lubrication solver and encouraging agreement between friction measurements and theoretical predictions was obtained. Kong [5] predicted elastic contact and elastohydrodynamic .lm thickness in worm gears. Using the undeformed geometry of the gap between gear teeth in contact a three-dimensional elastic contact simulation technique had been developed for calculation of the true area of elastic contact under load relative the wheel and worm surfaces. Tuttle [6]studied the harmonic drives, which exhibited very nonlinear dynamic behavior, in his model not only dynamic models include accurate representation of transmission friction, compliance and kinematical error were understand, but also important features of harmonic-drive gear-tooth geometry and interaction. Experimental observations were used to guide the development of a model to describe harmonic-drive operation.It is important to be aware that worm-gear performance is in.uenced by the lubricant applied and maintained. Helouvry [7] discussed the issue of theservo-orientation control being affected by a surge of both maximum static friction force and dynamic friction force. They reported the occurrence of a stable positioning error, as well as the stopping (or stoking) during tracking at the turning point of a limiting loop of the tracking system. When the system was in a one directional low-speed tracking, it was possible for the stick–slip phenomenon to occur due to the fact that the frictional force to velocity curve appears to be a negative slope and in.uences the static friction force. It was also found that a similar phenomenon occurs at high-speed tracking. Doupont [8] proposed a frictional force model with negative slope. In the reference, relative motion from static to high-speed sliding was divided into four stages. In the .rst stage, the external force was less than the maximum static friction force. In the second stage, two contacting surfaces started to develop a small relative velocity. In the third stage, the relative velocity started to increase between two objects, and lubricant got into the contact area and decreased the frictional force. In the fourth stage, the lubricant had fully .lled the contact area, and the viscous characteristic and the frictional force increased with the velocity. Oguri design handbook [9] included several empirical charts and calculation formulae of the friction coef.cient vs. sliding velocity, the allowable error of manufacturing, the recommended value for the gaps between two teeth, and the allowable contact pressure. Shigley [10] discussed the worm’s pitch circle line velocity as well as the transmission frictional coef.cient.In this study, only the friction force and elastic deformation of the surface between gear teeth are interested. The ZK-type worm-gear set is used to eliminate the backlash. Previous research works on gears and gear sets were focused on the limiting loading, pressure distribution and allowable pressure loading of gears, and on the relationship between friction coef.cient and sliding velocity. Most investigations are base on the assumption that the tooth is rigid. This study is focused on the effects of the elastic deformation of the gear tooth surface and the nonlinear friction coef.cient on the system dynamics. To study the dynamics of the worm-gear set, a dynamic model of the worm-gear set is developed and the comparison between the experimental results and the numerical results is also studied. The parameters of the dynamic model are adjusted by the .ndings of the comparison of the analysis and the experiment. Finally, the effects of moment-inertia of .y wheel, friction, rigidity of shaft and rigidity of gear tooth onthe nonlinear behavior of the transmission mechanism are also studied.2. The dynamic models of the worm-gear set2.1. The equilibrium equations of the worm and worm-gear setThe geometric of worm-gear set is shown in Fig. 1. There are a worm, a worm gear, two shafts, four bearings and a .ywheel. The shaft of worm is driven by an angle y1. The rotational angle of the .ywheel is y4. The rotational angle of the worm’s body is y2 (due to the elastic deformation of the worm shaft; y16¼y2). The rotation angle of worm-gear body is y3. The moment of inertia of the worm is Jw. The pitch radius of the worm’s helical tooth is rw. The worm’s rotational inertia as a rigid body is Jg. The pitch radius of the worm gear is rg. The moment-inertia of the .ywheel is J4. In this study, to neglect the effect of backlash, ZK-type worm and worm gear are used both in analysis and experiment.To simplify the theoretical model, the basic assumptions are listed asfollows:(1) The .ywheel is rigid.(2) The worms and worm-gear teeth are elastic.(3) The body of the worm gear is rigid.(4) Worm and worm gear are perpendicular to each other.(5) The clearance between teeth is ignored.(6) No error on the gear tooth pro.le.(7) The worm is single thread.(8) The worm shaft and worm-gear shaft are two rotational spring. Thedynamic behavior is neglected.(9) Translational degree-of-freedom for all the elements is not considered.(10) Only friction is considered, no other damping effect is considered.2.2. The axial spring constant of bearings, worm shaft and worm-gear shaftThe results of experiment to .nd the relation between load and the axialdisplacement of bearing are shown in Fig. 2. The axial spring constant of worm bearing (KbTws) and worm-gear bearing (KbTgs) are obtained by using Fig. 2. Furthermore, KLws and KbTws can be treat as two series connected spring. As well as KLgs and KbTgs can also be treat as two series connected spring. Therefore, kws can be expressed in terms of KLws with KbTws and kgs can also be expressed in terms of KLgs with KbTgs. The equations are listed as following: Lws bTws ws Lws bTwsLgs bTgsgs Lgs bTgsK K K K K K K K K K =+=+Fig. 1. Geometric of worm and worm gear.2.3. The friction coefficient of contact-gear teethThe relative motion between worm teeth and worm-gear teeth is considered pure sliding, so the friction plays an important role on the performance of worm-gear set. The ef.ciency of gear set is directly affected by the coef.cient of friction. The coef.cient of friction is in.uenced by the surface sliding speed of the both teeth;the friction is reduced as the relative sliding velocity increases. No formulae can be used to calculate the friction coef.cient precisely. In this study, the formula is based on the sliding velocity of the mean worm diameter [8,9,18]: ()()0.50.22360723,0.04707130.1056549e υμθθ-=+In above formula, n the relative sliding velocity of the mean wormdiameter ()w υγθ=⨯, the relative Iangular velocity of the mean worm diameter and rw the pitch radius of the worm’s helical tooth.Fig.2 The relation of axial direction displacements of bearing and axial loads 3. Experimental setupExperimental setup is shown in Fig. 3.and the speci.cations of the worm-gear set are listed in Table 1. The ZK-type worm-gear set was used to eliminate the backlash. The reduction ratio of gear set is (1:56) and the module of gear is 2. In Fig. 3, a Compumotor’s stepping motor, model no. OEM57-83, (with resolution of 1000 steps/rev [0.361/step]) was used to drive the worm shaft. An accelerometer (KS77) positioned on the upper location of the worm-gear shaft was used to measure the angle acceleration of y2 and y4. The angle displacement of y2 and y4 are obtained by integrated the measured angular acceleration twice. The NI USB-6009 DAQ system equipped with Lab-View software was employed to pick and fetch the voltage data from accelerometer.At the beginning of the experiment, the system was set at rest condition The sampling rate of data acquisition was 25_10_6 s. When the experiment started, the motor was accelerated to its maximum speed along the worm axis following the required acceleration curve, then stop after the input angle reaches y1 (y1.0.1130973 rad, 18 steps). The data-acquisition system recorded the acceleration of the accelerometer which attached on the bar end of worm and gear. The angular acceleration can be calculated from acceleration by using geometric relation.Fig. 3. The experiment device of worm-gear set.Table 1Speci.cations of worm-gear set (modulus M2)3.1. Experimental resultsThe measurement results of the worm angle acceleration (y2 curve) and the .ywheel of the worm-gear axis (y4 curve) are shown in Fig. 4. The acceleration oscillates between the zero line. The angular acceleration of y__2and y__4 are integrated twice to get angular displacement, which is shown in Fig. 5.Fig. 4. The measured results: (a) angular acceleration y2 and (b) angularacceleration y4.Fig. 5. The angular displacement obtained by integrating the acceleration twice:(a) angle y2 and (b) angle y4.4. ConclusionsIn this study, the dynamic equilibrium equations of worm-gear set considering the rigidity of the tooth were developed. The analyzed results were compared with the measured data. The comparison shows that the mathematics model is reasonable correct. The in.uence of moment-inertia, friction, rigidityshaft and rigiditygear tooth were also studied. The parameters study has following conclusions:1. The diameter of the .ywheel is reduced gradually, the amplitude of oscillating reduced gradually.2. The larger the module of gear, the higher the maximum amplitude of angles y2 and y4.3. Most oscillation of y2 comes from worm shaft, not from gear tooth. As to the oscillating of y4, the effect ofthe rigidity of the shaft is not important.4. The effect of the rigidity of the gear tooth of the worm is not as much as that of worm gear.5. The effect of friction is larger for y2 than that for y4.Above conclusions indicate that when design a worm-gear set for high precision positioning, the rigidity of the worm gear is very important, that the material of the worm gear should be used more rigid material than that of the worm.中文译文应用参数动力学研究蜗杆与蜗轮的旋转角度清华大学电力机械工程系摘要:应用于旋转角度的动态蜗轮订下瞬间是受多种因素的影响(包括摩擦力和轮齿表面之间的弹性变形) .结果发现,这些因素造成了不可忽略的转动定位误差. 本研究的目的是: ( 1 )建立一个数学模型,( 2 )进行数值模拟, ( 3 )进行实验并与数值计算的结果作比较. 实验结果和实际数值是一致的. 在这项研究中,飞轮的惯性,摩擦力,刚性轴和轮齿的刚度也被研究. 结果,可作为误差估计应用于旋转角度的相关的角度, 角速度和角加速度,并且用于建立误差补偿所需的位置控制.1.概述当采用雷达跟踪正以快速角度旋转的飞机时,该雷达可能由于小振荡的天线无法到达锁定目标,有时,振荡甚至导致失败的雷达系统.在跟踪系统中,准确定位是一个至关重要的问题. 然而,由于跟踪传导机制的设计受到空间和重量, 体积和重量限制.蜗杆齿轮集是一个很好的选择,因为它具有小体积和高还原度的特点.由于高的精度定位雷达系统振动天线是一个重要的动力学表现,要理解这种表现应用于大扭矩的动态蜗轮订下瞬间是非常重要的.此表现是受若干因素影响,包括摩擦力和轮齿表面之间的弹性变形.为了了解这些因素的影响,大量的研究工作已进行了.yuksel和Kahraman:[1]研究有关一个典型行星齿轮的动态特性表面磨损的影响。