丰田公司的TPS管理模式
丰田汽车的TPS管理模式概要

浅议丰田汽车的TPS 管理模式(Ⅰ文◎杨永清摘要:文章就丰田管理的沿革、理念、内涵、举措和效应等方面进行了简析,认为丰田的管理模式及其TPS 管理系统是企业产业核心竞争的源泉,值得借鉴。
关键词:TPS 管理模式;丰田汽车公司;生产管理系统0前言巨大董事长曾经说过“如果不是当年用心学TPS ,就不可能有今天的巨大。
”他进而提出“以TPS 为师,植入改善的基因。
”可见丰田管理不仅在汽车业界令人刮目相看,同样在自行车行业亦有借鉴发扬光大之效。
本文就丰田管理的沿革、理念、内涵、举措和效应等进行简述与浅议。
20世纪80年代,电视广告语打出“有路必有丰田车”,当时觉得有点夸大其词,后有机会境外公干,从号称“汽车王国”的美国到发展中国家的泰国,以及宝岛台湾等等,Toyota 汽车广告满目琳琅,比比皆是,这才深信无疑。
纵观丰田汽车的成长历程,再看《丰田的秘密》的记叙,对该企业的发展沿革,方有所了解和感悟。
1沿革1933年,丰田喜一郎(Ki-ichiro Toyoda 在丰田纺织机械厂内设立汽车部,介入汽车产业,先后引进销量极好的通用公司的雪佛兰(Chevrolet 和德国迪克瓦公司的“DKW ”牌轿车作为样车,模仿制造。
后又购买美国福特(Fort 汽车作研发参考。
此时,从散件组装起步,化油器、速度表、火花塞等全部进口,谈不上自制率。
1937年8月,“丰田汽车工业株式会社”正式成立。
由于侵略战争的需要,纳入军工生产,汽车销量大增。
当年,共生产汽车4.1万辆,其中小车577辆。
截止1945年日本无条件投降,丰田汽车公司共产93293辆。
1950年,按银行要求,成立丰田汽车销售公司,实现产销分离。
当年,朝鲜战争爆发,美军46亿日元的巨额订货,给丰田带来了丰厚的利润,丰田从而大展宏图。
以产品为龙头,1955年5月1日丰田极力精心打造的皇冠(Crown 轿车下线,其魅力使德国大众甲壳虫相形逊色,受到美国消费者的青睐,风靡全球。
丰田模式(TPS)学习心得
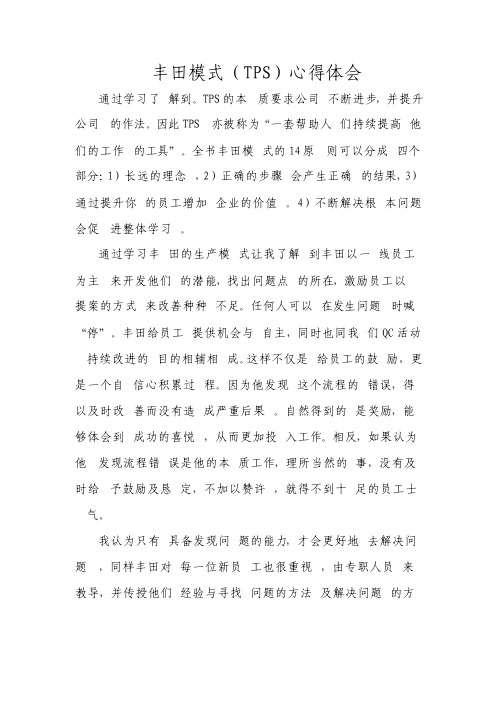
丰田模式(TPS)心得体会通过学习了解到。
TPS的本质要求公司不断进步,并提升公司的作法。
因此TPS亦被称为“一套帮助人们持续提高他们的工作的工具”。
全书丰田模式的14原则可以分成四个部分:1)长远的理念,2)正确的步骤会产生正确的结果,3)通过提升你的员工增加企业的价值。
4)不断解决根本问题会促进整体学习。
通过学习丰田的生产模式让我了解到丰田以一线员工为主来开发他们的潜能,找出问题点的所在,激励员工以提案的方式来改善种种不足。
任何人可以在发生问题时喊“停”。
丰田给员工提供机会与自主,同时也同我们QC活动持续改进的目的相辅相成。
这样不仅是给员工的鼓励,更是一个自信心积累过程。
因为他发现这个流程的错误,得以及时改善而没有造成严重后果。
自然得到的是奖励,能够体会到成功的喜悦,从而更加投入工作。
相反,如果认为他发现流程错误是他的本质工作,理所当然的事,没有及时给予鼓励及恳定,不加以赞许,就得不到十足的员工士气。
我认为只有具备发现问题的能力,才会更好地去解决问题,同样丰田对每一位新员工也很重视,由专职人员来教导,并传授他们经验与寻找问题的方法及解决问题的方法。
当然,首先要学会独立,不能依靠他人来完成自己的事,若是这样永远不会成长。
丰田非常重视方法。
无论是生产还是在原物料上,他们都会想方设法去降低一切能降低的成本。
如:丰田帮助供应商找到流程的上错误,来降低自己的原物料成本。
不但降低了供应商自己的成本,也降低了自己的成本。
大多企业都不会去做这样的事情,认为我帮他来解决问题降低成本谁为帮我解决问题降低成本啊?而丰田却相反主动极枳去帮助供应商解决问题来达到降低自己的原物料成本。
丰田重视过程管理。
让生产设备具有发现问题并能立即停止生产的能力。
精益系统改善(丰田TPS)

现场管理与成本
JIT生产基本原则1
流动化的要素
一个流
(1)工程流动化的三要素
想法 效果
物
同●在制品不会停滞 个一个流动 ●要做工程同步化 ●作业者持多任务序 ●需要多能工化 ●走动式作业 ●相邻作业间互助 ●可缩短前置时间 ●一个流程为可能 ●作业者无等待的 浪费
现场管理与成本
而「自动化」在不良品的发生和在机械、 模具、制具异常时,除非经人去关上开关, 否则会继续运转,很容易产生很大的问题。
现场管理与成本
异常管理
1)何谓异常
一切和平常工作不同的状况都叫做异常。 2)能否发现异常 利用目视管理方法使一切异常情况暴露在表面。 3)需要多少时间才能发现异常
利用现地现物主义随时把握现状。
现场管理与成本
现场管理与成本
自働化的两个要素 目视管理: 设备,生产线或是人,异常或是生产线停止的 情况可以被所有的人看到。 显示真正的原因和再发生防止:追查异常发生 的原因并采取对策使异常不再发生,也就是说非设 法防止再发生不可。
现场管理与成本
定位停止系统: 所谓定位停止方式是在生产线上每一位员工都被 “授权”,当异常时可以停止生产线,线内人员在异常 时实施停止、呼叫、等待三个步骤,确保问题的充分暴 露。 就「定位停止」方式的运用说明如此,生产线作业 员发现异常时,按上「ON」开关,警示灯即会亮灯,监 督人员即迅速的到达亮灯工程之处,能够马上掌握异常 之状况。 还有,装配线在停止的状态时,就先做好准备工作, 让装配线能恢复运转为首要之工作。
设 备
依工序顺序 ●物的顺畅流动 配置
流动化
●无物的滞留,会 ●物如整流的流动 顺流 ●人员顺畅的动作都加以考虑的 ●作业者无浪费的 设备配置 动作
{选篇}TPS-丰田管理模式 ln

5s(整理、整顿、清扫、清洁、素养)
并不是说实施了5s管 理,两大支柱就形成了
TPS的两大支柱之一——准时化
何谓“准时化生产”?
在必要的时候 生产必要数量的 必要产品
J I T ust n ime
适品 ·适量 ·适时
JIT的基本思想是:只在需要的时候、按需要 的量、 生产所需的产品,故又被称为准时制生产、适时生产 方式、看板生产方式。
柔 性 生 产 系 统
TQM 精 益 质 量 保 证
生 产 与 物 流 规 划
TPM 全 面 设 备 维 护
产 品 开 发 设 计 系 统
现 代
IE 运 用
均 衡 化 同 步 化
全员现场5S活动 ·观念革新 ·全员改善活动
TPS追求的目标
零 7个“
”目标 ☆ 零切换浪费
☆ 零库存
☆ 零浪费
☆ 零不良
实践性、有效性、劳动生产率提高、不良品的
降低、库存量的减少生产制造时间的缩短、节省生 产空间、提高机器设备的可动率、最终达到生产成 本的减少。
三种生产方式比较
项目 产品特点 设备和工装 作业分工 与作业内容 对操作工人
要求 库存水平 制造成本 产品质量 所适应的 市场时代
Байду номын сангаас
手工生产方式 完全按顾客要求 通用、灵活、便宜
JIT的核心是:零库存和快速应对市场变化。 精益生产不断消除所有不增加产品价值的工作, 所以,精益是一种减少浪费的经营哲学。
前提:
总量均衡
平准化:就是把产品的流量波动尽可 能控制到最小程度,实现总量和品种 数量的均衡。
平准化生 产
按品种和数量均衡
准
一个流
时
TPS丰田模式的十四项原则
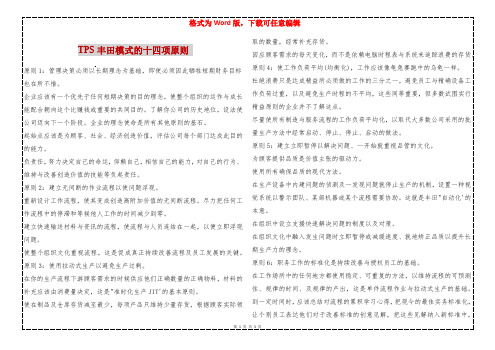
如此一来,当员工异动时,便可以把学习心得移转给接替此职务工作的员工。
一切都要标准化。
原则7:使用视觉管控,使问题无从隐藏。
使用简单的视觉指示,以帮助员工立即确定他们是否处于标准状况下,抑或状况发生变异。
避免使用电脑屏幕而致使员工的注意力从工作场所移开。
设计简单的视觉系统,安装于执行工作的场所,以支持单件流程作业与拉动式生产。
尽可能把报告缩减为一页,即使是最重要的财务决策报告亦然。
原则8:使用可靠的、已经经过充分测试的技术以支持人员及流程。
技术应该是用来支持员工,而不是取代员工,许多时候,最好的方法是在加入技术以支持流程之前,先以人工方式检视与研究流程。
新技术往往不可靠且难以标准化,因此,反而会危害到流程。
促成有成效与效率的流程,其重要性优于未经充分测试的新技术。
在业务流程、制造系统、或产品中应用新技术之前,必须先经过实际测试。
和组织文化之间具有冲突性、或可能会损及稳定性、可靠性、与可预测性的技术,必须予以修正或干脆摒弃。
不过,在寻求新的工作方法时,必须鼓励员工考虑新技术。
若一项适合的技术业已经过充分测试,且能改善你的流程,就应该快速实施。
原则9:栽培那些彻底了解并拥护公司理念的员工成为领导者,使他们能教导其他员工。
宁愿从组织内部栽培领导者,而不是从组织外聘雇。
不要把领导者的职务视为只是完成工作和具备良好的人际关系技巧,领导者必须是公司理念与做事方法的模范。
一位优秀的领导者必须对日常工作有巨细无遗的了解,方能成为公司理念的最佳教导者。
原则10:栽培与发展信奉公司理念的杰出人才与团队。
创造坚实稳固的文化,使公司的价值观与信念普及并延续多年。
训练杰出的个人与团队以实现公司理念,达成杰出成果。
非常努力地持续强化公司文化。
运用跨部门团队以改善品质与生产力,解决困难的技术性问题,以改进流程。
所谓授权,系指员工使用公司的工具以改善公司营运。
持续努力教导员工如何以团队合作方式达成共同目标,团队合作是员工务必学习的东西。
丰田公司的TPS管理模式

邁向Just-In-Time管理的道路--豐田公司的TPS管理模式豐田的生產和管理系統長期以來一直是豐田公司的核心競爭力和高效率的源泉,同時也成為國際上企業經營管理效仿的榜樣,例如,作為豐田生產管理一大特點的看板管理已被世界各地的企業所採用。
如今,世界很多大型企業都在學習豐田管理模式的基礎上,建立了各自的管理系統,以試圖實現標杆超越,像通用電氣公司、福特公司、克萊斯勒公司等世界著名企業都加入了這一行列。
但是,令人驚異的是,儘管豐田管理模式已為全球所認同和接受,真正成功的企業卻並不多,如今位於日本的豐田公司每天都要接受數以萬計的企業高級管理者參觀,這些參觀者將他們看到的管理方式帶到本國後,並沒有得到意想的效果,為此,很多人認為豐田管理模式的成功根源於其獨特的文化因素。
但事實並非如此,例如同是日本公司的尼桑和本田卻並沒有達到豐田的標準,而豐田本身卻將其獨特的管理模式帶到了全世界,這其中的代表就是位於美國肯塔基州的豐田喬治城汽車生產廠,該廠自1988年7月開始在1300英畝的廠址上進行批量生產,年生產能力為200000輛Camry轎車,相當於以往美國從日本進口同類型轎車的總量,1991年秋天豐田美國公司引入了全新的Camry轎車,1992年該類型車的供應量為40000輛,銷售額將增加20%。
新的Camry轎車屬於中等家庭車系列,佔有美國所有轎車市場l/3的市場份額,價格平均為$18500,稅前平均利潤為17%,顯然,其經營績效是十分矚目的。
由此看來,豐田管理模式並不是因為其獨特的日本文化而難以為其他國家的企業所學習,之所以存在管理方法難以移植的情況,主要原因在於參觀者所看到的豐田管理模式只是其外在的東西,諸如它的活動、連接和生產流等都是較為固定、甚至死板的東西,但是,在這些看似簡單的活動和流程後面,卻蘊含著豐田公司巨大的柔性和適應性,正是這些看似簡單、卻頗具柔性的管理特點,造就了豐田公司舉世矚目的經營業績,也使得他的柔性化生產管理方式--TPS(Toyota Production System)成為管理中的精髓,並使大規模定制模式下的敏捷產品開發和生產成為現實。
tps

丰田式生产管理丰田式生产管理(Toyota Management),或称丰田生产体系(Toyota Production System,TPS)由日本丰田汽车公司的副社长大野耐一创建,是丰田公司的一种独具特色的现代化生产方式。
它顺应时代的发展和市场的变化,经历了20多年的探索和完善,逐渐形成和发展成为今天这样的包括经营理念、生产组织、物流控制、质量管理、成本控制、库存管理、现场管理和现场改善等在内的较为完整的生产管理技术与方法体系。
精益生产( Lean Production)管理是美国麻省理工学院给丰田式生产管理的名称。
丰田式生产管理哲理的理论框架包含“一个目标”、“两大支柱”和“一大基础”。
“一个目标”是低成本、高效率、高质量地进行生产,最大限度地使顾客满意。
“两大支柱”是准时化与人员自觉化。
准时化(JIT-Just in time)生产。
即以市场为龙头在合适的时间、生产合适的数量和高质量的产品,JIT需要以拉动生产为基础,以平准化(Leveling System)为条件。
所谓拉动生产是以看板管理为手段,采用“取料制”即后道工序根据“市场”需要进行生产,对本工序在制品短缺的量从前道工序取相同的在制品量,从而形成全过程的拉动控制系统,绝不多生产一件产品。
平准化是指工件的被拉动到生产系统之前要进行人为的按照加工时间、数量、品种进行合理的搭配和排序,使拉动到生产系统中的工件流具有加工工时上的平稳性,保证均衡生产,同时在品种和数量上实现混流加式运动,起到对市场多品种、小批量需要的快速反应和满足功能。
人员自主化是人员与机械设备的有机配合行为。
生产线上产生质量、数量、品种上的问题机械设备自动停机,并有指示显示,而任何人发现故障问题都有权立即停止生产线,主动排除故障,解决问题。
同时将质量管理溶入生产过程,变为每一个员工的自主行为,将一切工作变为有效劳动。
“一大基础”是指改善(Improvement)。
改善是丰田式生产管理的基础。
丰田生产系统管理工具

丰田生产系统管理工具丰田生产系统(Toyota Production System,简称TPS)是丰田汽车公司开发并成功实施的生产管理方法,其核心理念是以精益为导向,追求持续改进和高效率的生产方式。
在TPS中,有许多管理工具被广泛使用,以帮助企业实现精益生产。
一、五问法(5 Whys)是TPS中最常用的管理工具之一。
它的基本原理是通过连续反问为什么,将问题一层层分解,找到根本原因。
通过深入分析问题背后的本质原因,可以避免单纯解决表面问题的方法,从而实现持续改进。
二、流程图(Process Flow Diagram)是TPS中用于描述生产流程的图形工具。
它通过可视化生产过程中的各个环节、工序和资料流动,帮助员工更好地理解整个流程,并找到改进的机会。
流程图也可以帮助员工迅速发现操作中的瓶颈和浪费,从而提高效率。
三、标准作业(Standardized Work)是在TPS中广泛应用的管理工具之一。
通过清晰地规定生产过程中的每个步骤、时间和要求,能够确保每个员工按照同样的标准工作,从而提高稳定性和质量。
标准作业也为员工提供了一个参考框架,帮助他们更好地理解工作要求,并减少错误的发生。
四、Kanban(看板)是TPS中用于控制生产流程的一种视觉化管理工具。
通过设置看板,可以实时了解生产线上的物料和工序的状态,并及时调整生产进度。
看板还可以帮助员工识别缺货和过量生产的问题,从而避免浪费和效率低下。
五、持续改善(Continuous Improvement)是TPS的核心理念之一,也是一种管理工具。
通过设立改善的目标、制定改善计划、实施改善措施和评估改善效果,可以不断推动生产过程的优化和创新。
持续改善还鼓励员工积极参与改进活动,发挥他们的创造力和提高意识,为企业创造更大的价值。
综上所述,丰田生产系统的管理工具是为了帮助企业实现精益生产,持续改进和高效率的生产方式。
通过运用这些工具,企业可以深入分析问题、优化流程、控制生产,并不断提高质量和效率,从而实现更高水平的竞争力和持续发展。
- 1、下载文档前请自行甄别文档内容的完整性,平台不提供额外的编辑、内容补充、找答案等附加服务。
- 2、"仅部分预览"的文档,不可在线预览部分如存在完整性等问题,可反馈申请退款(可完整预览的文档不适用该条件!)。
- 3、如文档侵犯您的权益,请联系客服反馈,我们会尽快为您处理(人工客服工作时间:9:00-18:30)。
丰田公司的TPS管理模式 作者:美奇 发布日期:2007-04-16 丰田的生产和管理系统长期以来一直是丰田公司的核心竞争力和高效率的源泉,同时也成为国际上企业经营管理效仿的榜样,例如,作为丰田生产管理一大特点的看板管理已被世界各地的企业所采用。如今,世界很多大型企业都在学习丰田管理模式的基础上,建立了各自的管理系统,以试图实现标杆超越,像通用电气公司、福特公司、克莱斯勒公司等世界著名企业都加入了这一行列。但是,令人惊异的是,尽管丰田管理模式已为全球所认同和接受,真正成功的企业却并不多,如今位于日本的丰田公司每天都要接受数以万计的企业高级管理者参观,这些参观者将他们看到的管理方式带到本国后,并没有得到意想的效果,为此,很多人认为丰田管理模式的成功根源于其独特的文化因素。但事实并非如此,例如同是日本公司的尼桑和本田却并没有达到丰田的标准,而丰田本身却将其独特的管理模式带到了全世界,这其中的代表就是位于美国肯塔基州的丰田乔治城汽车生产厂,该厂自1988年7月开始在1300英亩的厂址上进行批量生产,年生产能力为200000辆Camry轿车,相当于以往美国从日本进口同类型轿车的总量,1991年秋天丰田美国公司引入了全新的Camry轿车,1992年该类型车的供应量为40000辆,销售额将增加20%。新的Camry轿车属于中等家庭车系列,占有美国所有轿车市场l/3的市场份额,价格平均为$18500,税前平均利润为17%,显然,其经营绩效是十分瞩目的。
由此看来,丰田管理模式并不是因为其独特的日本文化而难以为其他国家的企业所学习,之所以存在管理方法难以移植的情况,主要原因在于参观者所看到的丰田管理模式只是其外在的东西,诸如它的活动、连接和生产流等都是较为固定、甚至死板的东西,但是,在这些看似简单的活动和流程后面,却蕴含着丰田公司巨大的柔性和适应性,正是这些看似简单、却颇具柔性的管理特点,造就了丰田公司举世瞩目的经营业绩,也使得他的柔性化生产管理方式--TPS(Toyota Production System)成为管理中的精髓,并使大规模定制模式下的敏捷产品开发和生产成为现实。以下从纵(历史发展)、横(管理特点)两个方面来揭示丰田公司JIT管理的奥秘。 的"Just in Time"这一理念的具体体现。
日本汽车工业从其起步到今天经历了一个"技术设备引进对国产化→建立规模生产体制→高度成长→工业巨大化→强化国际竞争力→出口增大对全球战略"这样一个过程。但是,从一开始的技术设备引进阶段,日本汽车工业就没有全部照搬美国的汽车生产方式。这其中除了当时的日本国内市场环境、劳动力以及二次世纪大战之后资金短缺等原因以外。一个很重要的原因是,以丰田汽车公司副总裁大野耐一等人为代表,他们从一开始就意识到了,美国汽车工业的生产方式虽然已很先进,但需采取一种更灵活,更能适应市场需求的能够提高产品竞争力的生产方式。
在20世纪后半期,整个汽车市场进入了一个市场需求多样化的新阶段,而且对质量的要求也越来越高,随之给制造业提出的新课题即是,如何有效地组织多品种小批量生产,否则的话,生产过剩所引起的只是设备、人员、库存费用等一系列的浪费,从而影响到企业的竞争能力以至于生存。 在这种历史背景下,1953年,日本丰田公司的副总裁大野耐一综合了单件生产和批量生产的特点和优点,创造了一种在多品种小批量混合生产条件下高质量、低消耗的生产方式即准时生产(Just In Time,简称JIT)。
JIT生产方式的基本思想是"只在需要的时候,按需要的量,生产所需的产品",也就是追求一种无库存,或库存达到最小的生产系统。JIT的基本思想是生产的计划和控制及库存的管理。
JIT生产方式以准时生产为出发点,首先暴露出生产过量和其他方面的浪费,然后对设备、人员等进行汰淘、调整,达到降低成本、简化计划和提高控制的目的。在生产现场控制技术方面,JIT的基本原则是在正确的时间,生产正确数量的零件或产品,即准时生产。它将传统生产过程中前道工序向后道工序送货,改为后道工序根据"看板"向前道工序取货,看板系统是JIT生产现扬控制技术的核心,但JIT不仅仅是看板管理。 JIT的目标是彻底消除无效劳动和浪费,具体要达到以下目标:
1.废品量最低(零废品)。JIT要求消除各种引起不合理的原因,在加工过程中每一工序都要求达到最好水平。
2.库存量最低(零库存),JIT认为,库存是生产系统设计不合理、生产过程不协调、生产操作不良的证明。
3.准备时间最短(零准备时间)。准备时间长短与批量选择相联系,如果准备时间趋于零,准备成本也趋于零,就有可能采用极小批量。 4.生产提前期最短。短的生产提前期与小批量相结合的系统,应变能力强,柔性好。
5.减少零件搬运,搬运量低。零件送进搬运是非增值操作,如果能使零件和装配件运送量减小,搬运次数减少,可以节约装配时间,减少装配中可能出现的问题。 6.机器损坏低。 7.批量小。 为了达到上述目标,JIT对产品和生产系统设计考虑的主要原则有以下三个方面:
1.在当个产品寿命周期已大大缩短的年代,产品设计应与市场需求相一致,在产品设计方面,应考虑到产品设计完后要便于生产。 2.尽量采用成组技术与流程式生产。 3.与原材料或外购件的供应者建立联系,以达到JIT供应原材料及采购零部件的目的。
在JIT方式中,试图通过产品的合理设计,使产品易生产,易装配,当产品范围扩大时,即使不能减少工艺过程,也要力求不增加工艺过程,具体方法有:(1)模块化设计;(2)设计的产品尽量使用通用件,标准件;(3)设计时应考虑易实现生产自动化。
JIT的基础之一是均衡化生产,即平均制造产品,使物流在各作业之间、生产线之间、工序之间、工厂之间平衡、均衡地流动。为达到均衡化,在JIT中采用月计划、日计划,并根据需求变化及时对计划进行调整。 JIT提倡采用对象专业化布局,用以减少排队时间、运输时间和准备时间,在工厂一级采用基于对象专业化布局,以使各批工件能在各操作间和工作间顺利流动,减少通过时间;在流水线和工作中心一级采用微观对象专业化布局和工作中心形布局,可以减少通过时间。
JIT可以使生产资源合理利用,包括劳动力柔性和设备柔性。当市场需求波动时,要求劳动力资源也作相应调整。如需求量增加不大时,可通过适当调整具有多种技能操作者的操作来完成;当需求量降低时,可采用减少生产班次、解雇临时工、分配多余的操作工去参加维护和维修设备。这就是劳动力柔性的含义;而设备柔性是指在产品设计时就考虑加工问题,发展多功能设备。
JIT强调全面质量管理,目标是消除不合格品,消除可能引起不合格品的根源,并设法解决问题,JIT中还包含许多有利于提高质量的因素,如批量小、零件很快移到下工序、质量问题可以及早发现等。
JIT生产管理方式在70年代末期从日本引入我国,长春第一汽车制造厂最先开始应用看板系统控制生产现场作业。到了1982年,第一汽车制造厂采用看板取货的零件数,已达其生产零件总数的43%。8O年代初,中国企业管理协会组织推广现代管理方法,看板管理被视为现代管理方法之一,在全国范围内宣传推广,并为许多企业采用。
近年来,在我国的汽车工业;电子工业、制造业等实行流水线生产的企业中应用JIT,获得了明显效果,例如第一汽车 车制造厂、第二汽车制造厂、上海大众汽车有限公司等企业,结合厂情创造性地应用JIT,取得了丰富的经验,创造了良好的经济效益。
JIT以订单驱动,通过看板,采用拉动方式把供、产、销紧密地衔接起来,使物资储备,成本库存和在制品大为减少,提高了生产效率,这一生产方式在推广应用过程中,经过不断发展完善,为日本汽车工业的腾飞插上了翅膀,提高了生产效率。这一生产方式亦为世界工业界所注目,被视为当今制造业中最理想且最具有生命力的新型生产系统之一。 二、"看板"方式管理方法
以往日本汽车生产商从各自独立的公司那里获得零部件,而单个企业内部的纵向联系又显得不够紧密,因此为了彻底解决这个问题民主高度相互信任和尊重的基础上,丰田公司同它们的零部件供应商建立了牢固的协作关系,这种作关系主要依靠交叉管理、相互融资、技术转移和规定作业区来维系,所以,"看板"和"及时供应"等管理方法能在供应商中到采用。其结果合理的生产流水线的安排减少了运输费用,使运输中造成的损失减少到最低程度,并大幅度降低了必要的库存作备。在"看板"制度下,很多部件一直要等到下一道工序需要前几个小时才生产出来,免去这些库存也就暴露了人员过多、人员不足及机器效率低等早就存在的问题,并加以纠正。以上这些管理上的变革产生的效果是惊人的,丰田汽车每售100辆因质量问题受到申诉的数量从1969年的4.5次下降到1973年的l.3次,生产效率也大为很高。 三、TPS的管理方法与精髓
丰田管理的一个主要思想就是在保持稳定质量的同时,能够使生产能及时反映市场的变化,并在逐步改善提高的基础上,最大限度地降低成本。而这种指导思想反映在丰田的发展战略上,就表现为不盲目地进行扩张,或步其他企业的后尘,匆匆进入某一市场,而是稳扎稳打,在充分了解市场和建立起自己完整的供应体系或竞争力后,再当机立断地进入海外市场,无论是他进入美国市场,还是后来进入亚洲,包括中国市场,都表现为这一特点。当然,丰田公司独特的经营管理意识不仅反映在它的发展战略上,更反映在它的日常管理上,为了全面揭示丰田的管理艺术,特别是以JIT为重要内容的TSP,下面将从4个方面来介绍他的现场作业管理,从中可以使我们对它的JIT有着更深入的了解。 1.员工该如何工作
丰田公司的管理思想中认为,要想实现及时化、质量稳定的生产,就必须从作业活动的细微之处抓起,把所有的工作分化为一个一个相互衔接的流程,并规定好各流程的作业内容、所处的位置、作业时间和作业绩效。例如,在汽车座椅的安装活动上,螺丝的安装都是以同样的顺序进行,安装的时间也是规定好的,甚至连上螺丝的扭矩也被规定得清清楚楚。这种精确的管理方法不仅仅运用在重复性的生产活动中,同时也被运用在企业的所有活动中,无论是职能型的活动,还是管理活动也都如此。这一管理方法表面上看起来非常简单,但事实上并不是所有的企业都能做到。 以TMM(Toyota Motor Manufacturing,U.S.A.,Inc,简称美国丰田汽车工厂)厂中安装前座椅为例,操作人员被要求从纸板箱中取出4颗螺丝,然后安装在汽车上,扭紧,然后在计算机中输入一个代码,以表明整个作业已经无暇疵地完成,再等待下一辆汽车的安装。新手往往由经验丰富的老工人手把手地教,当新手遇到任何困难和问题时,如没有扭紧螺丝或忘记输入代码时,老工人就会立刻帮助他们。上述管理现象看上去并不十分复杂,但事实上并不这么简单。如果作业现场存在大量新手时,往往会比经验丰富的工人表现出更多的作业差异性,从而使得质量变得不稳定,如有的操作员可能先安装前面的螺丝,再安装后面的螺丝,而有的可能正好相反;有的先安装好全部螺丝后再扭紧,而有的边上螺丝边扭紧,这种作业上的差异性必然会产生低生产率和高成本,而且更为重要的是,作业上的差异性必然阻碍相互的学习和改善。为了防止这种状况出现,丰田公司制定了精细、完善的流程和步骤,所有员工无论新手还是经验丰富的员工都必须遵守,并且任何偏离行为也能够及时被发现。