五金模具技术规范
五金模具设计规范
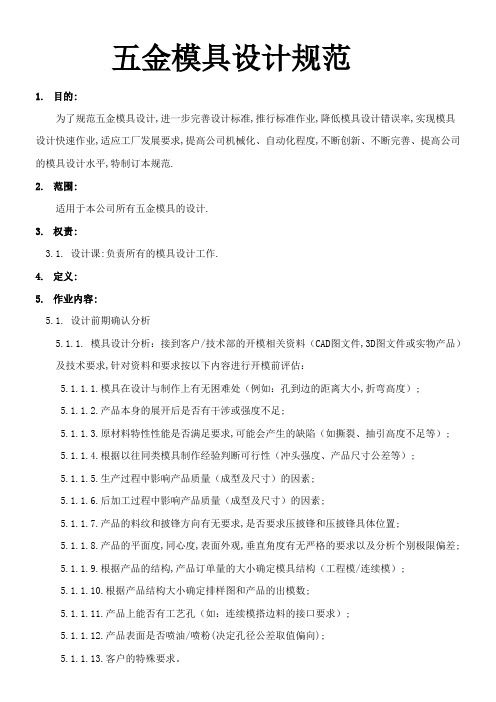
五金模具设计规范1.目的:为了规范五金模具设计,进一步完善设计标准,推行标准作业,降低模具设计错误率,实现模具设计快速作业,适应工厂发展要求,提高公司机械化、自动化程度,不断创新、不断完善、提高公司的模具设计水平,特制订本规范.2.范围:适用于本公司所有五金模具的设计.3.权责:3.1.设计课:负责所有的模具设计工作.4.定义:5.作业内容:5.1.设计前期确认分析5.1.1.模具设计分析:接到客户/技术部的开模相关资料(CAD图文件,3D图文件或实物产品)及技术要求,针对资料和要求按以下内容进行开模前评估:5.1.1.1.模具在设计与制作上有无困难处(例如:孔到边的距离大小,折弯高度);5.1.1.2.产品本身的展开后是否有干涉或强度不足;5.1.1.3.原材料特性性能是否满足要求,可能会产生的缺陷(如撕裂、抽引高度不足等);5.1.1.4.根据以往同类模具制作经验判断可行性(冲头强度、产品尺寸公差等);5.1.1.5.生产过程中影响产品质量(成型及尺寸)的因素;5.1.1.6.后加工过程中影响产品质量(成型及尺寸)的因素;5.1.1.7.产品的料纹和披锋方向有无要求,是否要求压披锋和压披锋具体位置;5.1.1.8.产品的平面度,同心度,表面外观,垂直角度有无严格的要求以及分析个别极限偏差;5.1.1.9.根据产品的结构,产品订单量的大小确定模具结构(工程模/连续模);5.1.1.10.根据产品结构大小确定排样图和产品的出模数;5.1.1.11.产品上能否有工艺孔(如:连续模搭边料的接口要求);5.1.1.12.产品表面是否喷油/喷粉(决定孔径公差取值偏向);5.1.2.对所得资料检查完毕, 如有疑问先行提出,并经客户/技术部确认后, 再做后继工作。
如果因时间关系要先行设计,来不及确认的数据要继续主动跟进。
5.1.3.设计草图5.1.3.1.为了提高工作效率,减少修改的工作量,设计人员可以将设计意图及关键结构的构思绘制草图,经评审后,再进行后继的绘图工作。
五金冲压连续模设计规范产品展开设计

五金冲压连续模设计规范产品展开设计Document serial number【UU89WT-UU98YT-UU8CB-UUUT-UUT108】:产品展开标准文件编号:SB-B0035一.目的推行作业标准化﹐实现模具设计快速统一。
二.适用范围冲模设计三.内容弯曲制品产品展开展开计算标准:1)概算法分为直边部分与弯曲部分,以中立面的长度之和求得的方法。
L=a+b+2πα°(R+λt) /360弯曲形式 R/t λ以下~V形弯曲 ~3~55以上以下 ~~U形弯曲 ~5以上Romanowski的方法(V,U形弯曲共用)R/tλ2)外侧尺寸加算法:弯曲处很多时的计算法是先将外侧尺寸全部加算,从其和减去取决于板厚和弯曲半径两要素的伸长量。
L=(l1+l2+l3+…ln)-﹛(n-1)c﹜n-1……弯曲处数目 C ……伸长补正系数板厚C类别:技术标准制定日期:2002/06/11版次:A共14页第1页产品展开标准文件编号:SB-B00353)卷曲(Romanowski)L=A+B+a (mm) L:胚料长度R/ty4)内侧尺寸计算法对边长之和再加set back值(补正长度值)的方法L=πρ+2R-tρ=R-yt5)收缩凸缘的概算展开尺寸(90°)弯曲a= (R+h)γγ2-h2-R类别:技术标准制定日期:2002/06/11版次:A共14页第2页第一部分:产品展开标准文件编号:SB-B0035γ比R小时a= (R+h)γ-h2-R6)伸长凸缘的概算展开尺寸(90°)弯曲a=R- (R-h)2+γγ2-h2γ比R小时a= R- (R-h)2 +γ-h27)整线加工(hemming) 概算展开尺寸a:凸缘的展开尺寸h1:整缘后的凸缘长度h0:整缘前的凸缘长度t1,t2:板厚8)非90°折弯(3) R=0,θ≠90°λ=T/3L=[A-T*tg(α/2)]+[B-T*tg(α/2)]+ α/180°*πT/3类别:技术标准制定日期:2002/06/11版次:A共14页第3页五金冲压连续模具设计规范五金冲压连续模具设计规范五金冲压连续模具设计规范凯五金冲压连续模具设计规范*****************五金冲压连续模具设计规范五金冲压连续模具设计规范模具工程冲模设计三.内容一. 定义(一).弯曲成形加工金属材料由於受力超过其弹性限度及降伏强度,但低于其极限抗拉强度之应力,使金属板料产生永久变形而得到所要求之尺寸及轮廓形状.(二).中立层(面)金属材料由於弯曲加工式一面(弯曲外侧)受到抗拉应力而另一面(弯曲内侧)受到压缩应力,因此在材料板厚某处所受之应力为零,此零应力之平面为中立层(面)(Netural Plane)(三).展开计算依据由於中立轴线受到零应力,此其长度等於原始胚料之长度,边是作为胚料尺寸展开之基准,中立轴线之位置则视材料种类﹑特性机弯曲内侧板与板厚比而不同﹒中立轴位置之测定,一以金属板料弯曲内侧为基准,亦即位於从弯曲内侧板厚中心处之某处一距离,此位置约是板厚30~50%(图二﹒弯曲成形加工之种类(1).V形或形弯曲加工(图(2).U形弯曲加工(图(3).Z形弯曲加工(图(4).弯缘加工(Hermming)(图(5).卷缘加工(Curing)(图类别:技术标准制定日期:2002/06/11版次:A共14页第9页五金冲压连续模具设计规范展开计算标准(弯曲成形)概论篇之二文件编号:SB-B0035五金冲压连续模具设计规范五金冲压连续模具设计规范模具工程冲模设计三.内容(9)卷缘加工(侧推)L=*T*r+R-T r=r-λ*Tλ之数值表(软钢板)R/T之值以上Λ之值(10)卷缘加工(上压)1>L=L1+C2>L1=π*r+R-Tr=R-λ*T3>C=T/4*2*π*1/4=λ之数值表(同上)(11)冲切弯曲之冲切宽度W=H-X(setback)*冲切弯曲冲头之R=T*r最小值为零T(mm)X(12)综合计算如图:L= 料内+料内+补偿两=A+B+C+D+E+F+﹝(AA+BB+CC+DD+EE) 补偿量﹞λ之数值表AA: λ=T/3BB: λ=T/3CC: λ=T/3DD: λ=T/3EE: λ=T/3类别:技术标准制定日期:2002/06/11版次:A共14页第12页五金冲压连续模具设计规范展开计算标准(弯曲成形)限制篇文件编号:SB-B0035展开计算标准(弯曲成形)反弹篇文件编号:SB-B0035一.目的推行作业标准化﹐实现模具设计快速统一。
五金模具规范要求

五金模具规范要求第一篇:五金模具规范要求五金冲压模具规范要求----德之佳为了规范和保证五金冲压模具品质、提高生产效率及结合我司实际情况,特制定本规范要求。
具体要求如下:结构及工艺要求:1.所有模具都必须有导柱、导套,特殊模具除外,但须和模具负责人沟通协定2.模具垫板、模座必须足够厚足够宽,防止模座(板)变形,16-25T模座(板)厚度≥25mm,30-40T模座(板)厚度≥30mm,60T及以上模座(板)厚度≥35mm;模柄要求使用标准模柄3.凹凸模及重要工作部件必须做真空热处理,冲裁硬度HRC58-60度,压型硬度HRC55-56度,不接受利用火焰枪直接做热处理4.推料、卸料机构必须灵活,无干涉现象5.所有活动部件应平稳灵活、无滞止干涉现象6.冲孔、落料的漏料孔必须保证通畅7.所有紧固件必须锁紧无松动,起限高作用的长螺丝需要有等高套或加用螺母锁死8.模具要求便于操作且安全,当模具需要有定位时必须要有定位外观要求:1.模具零部件不允许有裂纹,工作零部件表面不允许有划痕、机械损伤、锈蚀等表面缺陷2.凹凸模刃口及侧刃等必须锋利,不允许有蹦刃、缺刃和机械损伤3.凹凸模及工作面必须是光面,不接受没有处理的线割纹等不良表面4.模具外观面要求平整,不允许有锯齿纹等类似的粗糙面包装要求:1.必须在模具正面非工作区打上模具铭牌,铭牌内容:模具名称、出厂日期、供应商2.模具出厂前应清洗干净,所有工作件零件表面应涂覆防锈剂,不接受锈蚀的模具3.模具外观面清洗后需要涂覆油漆做防腐处理,不接受没有做涂覆处理的模具送样及送货要求:1.模具在送货前,必须先送样确认,每套产品必须送至少10PCS 样品,送样材料可以由我司提供2.模具负责人确认样品符合要求后再通知模具商送货3.送货时模具商必须派至少1人和我司维修工一起试模,模具负责人确认模具状况和加工出来的产品是否符合要求售后服务要求:1.所有冲压模具工作部件要求在10万次或6个月内免费维修,除工作部件外如模架部分等要求保修1年,我司人为原因除外2.模具维修时须遵循先报价且双方确认报价后再维修的原则注:1.出厂日期为最后确认模具的日期2.按照每月4周,每周冲压4000次计算,6个月计96000次3.如有一些特殊五金冲压模具不能符合本规范要求时,模具商须和模具负责人沟通协定4.本规范要求最终解释权利归本公司所有,且保留不断修改的权利5.本公司保留因供应商模具设计不当而造成损失要求赔偿的权利编制:杨芬洪审核:日期:版本:A/0第二篇:五金模具知识五金模具知识:模具基础知识 2009/9/28/10:02 来源:机械专家网[慧聪五金网]模具的基本构成(1)前模(母模)(定模),(2)后模(公模)(动模),(3)嵌件(镶件),(4)行位(滑块),(5)斜顶,(6)顶针,(7)浇口(入水口)2.模具制品形状对制品的影响壁厚,几何形状,会影响成形收缩率,脱模斜度大小。
五金模具检验规范标准

进行判定,对不符合图纸要求或试作中的问题点以及顾客提出要求设计更改的容 向生产部提出修正。 5.3.2.4 试作合格的模具移交客户验收。 6.检验和试验 6.1 取样 同一规格的物品按每批 3~5PCS 抽取样本或由品管担当确定,小于 3 件的批次进行 全检,有公差标准的关键尺寸在现有资源可以测量的情况下要全部测量。 6.2 检验要求 6.2.1 品管人员抽取样本后,先分别对外观、尺寸进行判定,再进行破坏性检验。 6.2.2 外观检查环境要求:采用常态照明(40W 日光灯使光线充足),待测量物品测量面 与检验人员肉眼距离 25~35cm,观察角度要求垂直于待测量物品被测面的±45º 角,观察时间为 10±5 秒。 6.2.2 监视和测量装置要求:卡尺精度等级不低于 0.02mm,千分尺精度等级不低于 0.01mm,标准规精度等级不低于 0.01mm,其它或自制的检具等装置要满足相关 的工艺、检验文件或工程图纸上的测量要求。
a.部件尺寸超差,但实配后符合要求的可特采(产品面间隙不得大于 0.03mm)。
b.经重新加工或修补后,能达到要求的可特采。
c.有缺陷但与客户沟通后能接受的可特采。
6.6 免检
要求不高且工艺能完全保证的、现有资源不能检测的项目经主管人员同意后免于检查。
6.7 紧急放行
生产急需来不及进行检验,且本工序的不合格品不影响下道工序加工,才能紧急放行。
2、冲裁模之凸凹模刃口及侧刃等必须锋利,不允许有崩刃、缺刃和机械损坏
3、热处理后的零件硬度应均匀,不允许有软点和脱碳区,并清除氧化物
4、模具正反面都应有该模具的标识,至少包括:产品名称及图号、模具名称
五金件技术要求
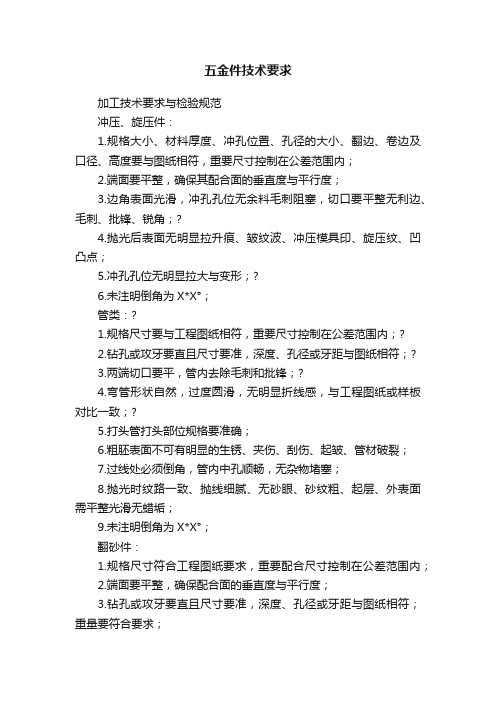
五金件技术要求加工技术要求与检验规范冲压、旋压件:1.规格大小、材料厚度、冲孔位置、孔径的大小、翻边、卷边及口径、高度要与图纸相符,重要尺寸控制在公差范围内;2.端面要平整,确保其配合面的垂直度与平行度;3.边角表面光滑,冲孔孔位无余料毛刺阻塞,切口要平整无利边、毛刺、批锋、锐角;?4.抛光后表面无明显拉升痕、皱纹波、冲压模具印、旋压纹、凹凸点;5.冲孔孔位无明显拉大与变形;?6.未注明倒角为X*X°;管类:?1.规格尺寸要与工程图纸相符,重要尺寸控制在公差范围内;?2.钻孔或攻牙要直且尺寸要准,深度、孔径或牙距与图纸相符;?3.两端切口要平,管内去除毛刺和批锋;?4.弯管形状自然,过度圆滑,无明显折线感,与工程图纸或样板对比一致;?5.打头管打头部位规格要准确;6.粗胚表面不可有明显的生锈、夹伤、刮伤、起皱、管材破裂;7.过线处必须倒角,管内中孔顺畅,无杂物堵塞;8.抛光时纹路一致、抛线细腻、无砂眼、砂纹粗、起层、外表面需平整光滑无蜡垢;9.未注明倒角为X*X°;翻砂件:1.规格尺寸符合工程图纸要求,重要配合尺寸控制在公差范围内;2.端面要平整,确保配合面的垂直度与平行度;3.钻孔或攻牙要直且尺寸要准,深度、孔径或牙距与图纸相符;重量要符合要求;4.粗胚表面光滑,表面粗糙度不得大于XX;5.配重类粗胚材质表面良好,应无明显模痕、缺料、变形现象;其它翻砂类产品抛光、抛砂后无明显瑕疵;6.抛光时纹路一致、抛线细腻、不出现粗砂纹、起层、外表面需平整光滑无腊垢,表面砂眼抛光后在同一可视面可接受两处且大小不能超过1mm;7.外观造型花纹整批一致,与样品对比无明显差异;8.产品不可有毛刺、批锋、利边;焊接组件:1.焊接工艺:铜焊、银焊、铁焊、碰焊、亚弧焊、二氧化碳焊等2.所有焊接零件需打砂后方可焊接;3.焊接要牢固,不能虚焊、漏焊;4.焊接尺寸要控制在公差范围内,角度要准确;5.焊接时不能使产品变形且焊疤面积不能太大;6.管类焊接时不能堵塞管;7.抛光纹路一致,扫线正确、抛线细腻、不出现粗砂纹、起层、外表面需平整光滑无蜡垢,表面外观后同一可视面不能出现两处大于2mm之瑕疵。
五金模具检验规范标准

a.部件尺寸超差,但实配后符合要求的可特采(产品面间隙不得大于 0.03mm)。
b.经重新加工或修补后,能达到要求的可特采。
c.有缺陷但与客户沟通后能接受的可特采。
6.6 免检
要求不高且工艺能完全保证的、现有资源不能检测的项目经主管人员同意后免于检查。
.
.
.
.
6.7 紧急放行
生产急需来不及进行检验,且本工序的不合格品不影响下道工序加工,才能紧急放行。
.
1. 目的
对来自于外部的物料、部加工的部品以及总成后的模具按要求进行检验,以确保投入使用的物料、部
品和模具满足预期的要求。
2. 围
适用于所有组成模具的部品及模具,包括采购的物料、委外和部加工的部品。
3.定义 来料检验:外部购买的物料和委外加工部品的检验。 过程检验:部加工的模具零部件、半成品和成品检验。 最终检验:模具总成后的检验,包括模具外观、可成形性、成形产品等的检验。 4.职责 4.1 工程部负责相关检验数据的提供。 4.2 质检部负责对物料、部品以及模具实施来料检验、过程检验和最终检验。 4.3 仓库对采购物资质量负责,并配合质检部做好来料检验工作。 4.4 生产部协助做好过程检验,并确保未经检验或检验不合格的物资不投入使用。 5.检验作业流程 5.1 来料检验 5.1.1 作业流程图
不合格处理。 5.2.2.2 质检部接到报检信息后进行抽样或全数检查,并将检验结果填入《出/入库检验
记录》。 5.2.2.3 检验合格的部件以“合格”进行标识,移交下一道工序。 5.2.2.4 检验不合格的部件,质检部会同设计、钳工、数控等相关人员进行检讨,可接受
的以“特别采用”进行标识,无法采用的贴上“不合格”标签并予以隔离。 5.2.2.5 对于不合格项质检部开《不合格项整改报告》,相关部门对问题点分析、纠正和预
五金模具设计规范大全(二)
第一篇:设计技术规范页次第 1 页共 1 页1 总则1.1目的推行模具零部件结构标准化,实现模具设计快速作业.1.2适用范围冲压模具设计部.2 压筋冲子规定2.1压筋目的减少工件折弯时的拉料或折弯以后的回弹,提高弯曲件的精度.2.2压筋冲子形状(1)压筋冲子的形状,根据其功能性不同,而有几种不同的形式.图(a)形状的压筋冲子一般用于防止或减少折弯时工件有拉料现象的时候;图(b)形状的压筋冲子一般用于防止或减少折弯时工件有回弹现象的时候,图(b)中的尺寸L根据材料的厚度选择合适值:当厚度T<1.5时取1.0;厚度T≧1.5时L取1.5.(2)压筋的高度[图(a)中 40%*T的计算值和图(b)中的0.20], 采用UNIT2的标注形式,标注小数点后两位小数.角度45∘是供加工方便性参考的尺寸.宽度尺寸采用UNIT1的标注形式,标注小数点后一位小数.第一篇:设计技术规范页次第 1 页共 4 页1 总则1.1目的推行模具零部件结构标准化,实现模具设计快速作业.1.2适用范围冲压模具设计部.2. 定位销(块)规定2.1定位销(块)结构形式(1)定位销(块)材质用 SK3或SKD11,投外加工时热处理HRC58;设变由组立自行处理时不需热处理.(2)圆定位销,适用于圆内孔定位(定位销直径 D=工件上的圆孔直径减去0.10MM. )或不考虑拉料现象时的外形定位.如图(a):(3)异形定位销,适用于异形内孔定位,一般做成长方形.如图(b).(4)方形定位块,适用于冲孔兼小折有材料拉料现象时的外形定位,如图(c).图中尺寸 L与W依产品大小取值.(一般L=15MM,W=20MM).此种定位方式调整较为方便.(5)方形导料定位块,适用于连续下料模的材料导正(一般置于下模板.数量约 4~6个).如图(d).图中尺寸:E一般取5MM,产品变形较严重时要适当增大E值;L与W依产品大小取值.(一般L=30~35MM,W=15MM).第一篇:设计技术规范页次第 2 页共 4 页(6)弯曲模定位形式,适用于折弯成形模中的产品定位,如图(e).图中加有方框的尺寸(10)可依需要适当加大,此时要注意定位支承块的相关尺寸.图(e)注意:a.使用固定式定位(案内)时要确认相关模板的厚度及消孔大小.一般情况下:消孔单边大0.1MM,须使用线割加工.b.定位销(块)露出模板外直段高度 B(不包括圆弧段)取值: 一般情况下:精细定位,B=顶料销顶出高度+T; 有内(钩)孔定位时:外形定位,B=顶料销顶出高度+T+(3~5MM); 式中T为材料厚度.c.图(b),(c)中,C值一般取10MM.如下图所示:第一篇:设计技术规范页次第 3 页共 4 页(7) 挡块定位,适用于单边折弯模结构中.定位块的高度尺寸应和装在折块(刀)上的定位块尺寸相配合,保证同时导入材料.2.2定位销(块)选用分布设计原则(1)T>=0.8 时,精细定位块以材料边往料外偏0.03MM;T<0.8时,精细定位块以材料边往料外偏0.02MM.(2)素材为片料的第一工程料片定位,使用固定式与活动式相结合的定位方式.注意:使用固定式定位的材料边为产品尺寸形状要求较高的边,使用活动式定位的材料边为产品尺寸要求较低的边.第一篇:设计技术规范页次第 4 页共 4 页(3)后续工程必须使用前工程冲出的剪口做为精定位,并避开接刀处.(4)冲剪模尽量用固定式,折弯模尽可能用异形且可调式.(5)用内孔定位时,优先选用顺序:圆形----方形----异形.(6)各工程须使用相同的基准边,避免因公差造成段差刃边.(7)单边折弯模易有拉料现象,定位方式须设计成两边可调式,如前页图(e).业规范第一篇:设计技术规范页次第 1 页共 1 页1 总则1.1目的推行模具零部件结构标准化,实现模具设计的快速作业.1.2适用范围冲压模具设计部.2 定位支承块规定2.1定位支承块功用用在成形模的可调式定位中,将定位块联接在折刀上.2.2尺寸要求图(a):是定位支承块的装配示意图.设计过程中注意折刀和定位块上螺纹孔上下位置尺寸(12及10)与定位支承块上孔距尺寸(22.0)的对应关系.图(b):是定位支承块的规格尺寸.尺寸25或30视实际情况确定.定位支承块材质用SS41,不需要热处理.2.3五金零件需求表书写范例特殊规格的定位支承块,由设计者画零件图.如选用图(b)标准尺寸的定位支承块,不需要画零件图,在五金零件需求表中按以下范例格式写出.例: 定位支承块 30*40*10 定位支承块: 零件名称30*40*10: 规格规范第一篇:设计技术规范页次第 1 页共 1 页1 总则1.1目的推行模具零部件结构标准化,实现模具设计快速作业.1.2适用范围冲压模具设计部.2 作业原则2.1下模板上的圆孔较小需采用入子时,一般使用图a所示的入子形式.对应的模板入子孔的形状如图b所示.注意:A.上图(a)中入子直径D及尺寸“A-0.2”的选取要考虑保证挂钩宽度尺寸“1~2MM”和入子最小处壁厚“>=3MM”.(此两尺寸在实际画零件图时不标注).B.图(b)中反面沉孔的直径大小D2要保证挂钩能顺利装入,“S”孔的加工要求可按如下格式书写:“S 1-C+0.01 HATCHING: Φ**.0 BOT DEP 5.3”意思是:S 孔在加工时按图示尺寸单边加大+0.01MM,其中有影(剖面)线部分反面沉孔直径Φ**.0,深度5.3MM.2.2下模板上的异形孔如需采用入子时,一般使用普通的方形入子(带挂钩).第一篇:设计技术规范页次第 1 页共 3 页1 总则1.1目的保证设计出的模具具有较好的加工性,便于模具组立作业.1.2适用范围冲压模具设计部.2 作业标准与原则2.1线割孔(3MM以下的小孔除外)除刀口外,一般均需消线头,并在尖角处清角,设计者要按标准标明批注,不需用图形表示清角消线头,尺寸由加工者确定.如附图1:2.2一般在非刀口板(例:打板和夹板)上的孔不参与成形,都需清角及消线头.冲子和入子零件不可留线头,消线头的方法由加工单位确定.2.3无特殊需要的入子一般做成长方形,并倒C角,方式如附图2(模板倒R角).C值取0.5或1.0,甚至更大.同时注意入子的防呆措施(可利用在入子的本身倒一个较大的C角等方法).2.4铣加工中角部无特殊要求,只要求清角时,图形示出,不标圆角尺寸,由加工者现场确定圆角尺寸,如附图3.2.5铣加工中不清角时,一般取圆角大于R2.R按标注的尺寸加工,公差按标准取值,如附图4. 铣床的部分刀具规格参考附件一.第一篇:设计技术规范页次第 2 页共 3 页0.5mm~1mm.2.7模板厚度方向有攻牙孔或其它结构时,设计者必须画侧视图表示其位置.2.8为了确保入子的装配稳定性,设计者应将入子固定槽形状设计成如附图5所示,并画出详图.2.9对于细长类零件,应当考虑进行分段以利保证加工精度.分段后零件的长宽比视零件形状尺寸而定,一般取值可在10~15之间.2.10 3mm以下的小孔,刀口板要做入子,小孔较多且密集时请示上级.2.11为了方便模具的搬运,在模座的侧面适当部位需加工起重螺纹孔.一般情况下,起重螺纹孔规格取M20*40,特殊情况下(例模座厚度小于30MM时)才考虑取M16*40.2.12冲孔/落料/连续模中冲子过孔或落屑孔(SB/CB/DP/DD板)的铣加工优化处理(尤其是SB/DD):SB/DD在不影晌强度时可进行处理,并保证R≧3MM,DD板尽可能保证R≧5MM;CB/DP板一般不进行处理,除非孔形状较规则不会对模具局部强度产生影响.不能处理成铣加工的R角时,设计者按标准放间隙和注解公差(±0.1),加工单位依自身状况确定加工方法,设计者及主管检查审核图面时应将此项要求重点确认.附件一:加工部门CNC铣床程序现行刀具表1. 钻头规格A.直柄钻头:第一篇:设计技术规范页次第 3 页共 3 页B.锥柄钻头:直径:Æ13.5,Æ14,Æ14.5,Æ15,Æ17,Æ18,Æ18.5,Æ19,Æ20.5,Æ21,Æ21.5,Æ22,Æ22.5,Æ23.0C.潜水钻:直径:Æ26(L=76mm), Æ32(L=80mm)2.铣刀规格(注:括号内数据为铣刀有效部份长度)a micro-100直径:Æ3(7), Æ4(9), Æ5(11), Æ6(12), Æ8(22), Æ10(25), Æ12(30)b粗铣刀(过中心)直径:Æ6(15), Æ8(21), Æ10(24), Æ12(28), Æ14(28), Æ16(45), Æ18(33), Æ20(41)加长型:Æ12(52), Æ20(75)c精铣刀:直径:Æ6(15),Æ8(20),Æ10(25),Æ11(39),Æ12(28),Æ13(55),Æ14,Æ16,Æ18,Æ20第一篇:设计技术规范页次第 1 页共 3 页1 总则1.1目的规范沙拉孔的展开计算方法及相关模具尺寸和成形方法.1.2适用范围冲压模具设计部.2 沙拉孔规定2.1沙拉孔的分类沙拉孔(英文名COUNTER SINK、C.S.K或C’SINK)根据产品的要求不同,一般可将沙拉孔分成两类:产品铆合连接用的沙拉孔和通过螺钉(铆钉、拉钉)头部的沙拉孔.2.2沙拉孔尺寸的确认(1)在产品确认时,除了向客户确认清楚图面中的详细尺寸规格外且必需要求客户提供五金件实物,有实物以后可以请组立等相关单位进行试验以获得经验数据。
五金设计规范
竭诚为您提供优质文档/双击可除五金设计规范篇一:五金件技术要求加工技术要求与检验规范冲压、旋压件:1.规格大小、材料厚度、冲孔位置、孔径的大小、翻边、卷边及口径、高度要与图纸相符,重要尺寸控制在公差范围内;2.端面要平整,确保其配合面的垂直度与平行度;3.边角表面光滑,冲(五金设计规范)孔孔位无余料毛刺阻塞,切口要平整无利边、毛刺、批锋、锐角;4.抛光后表面无明显拉升痕、皱纹波、冲压模具印、旋压纹、凹凸点;5.冲孔孔位无明显拉大与变形;6.未注明倒角为x*x°;管类:1.规格尺寸要与工程图纸相符,重要尺寸控制在公差范围内;2.钻孔或攻牙要直且尺寸要准,深度、孔径或牙距与图纸相符;3.两端切口要平,管内去除毛刺和批锋;4.弯管形状自然,过度圆滑,无明显折线感,与工程图纸或样板对比一致;5.打头管打头部位规格要准确;6.粗胚表面不可有明显的生锈、夹伤、刮伤、起皱、管材破裂;7.过线处必须倒角,管内中孔顺畅,无杂物堵塞;8.抛光时纹路一致、抛线细腻、无砂眼、砂纹粗、起层、外表面需平整光滑无蜡垢;9.未注明倒角为x*x°;翻砂件:1.规格尺寸符合工程图纸要求,重要配合尺寸控制在公差范围内;2.端面要平整,确保配合面的垂直度与平行度;3.钻孔或攻牙要直且尺寸要准,深度、孔径或牙距与图纸相符;重量要符合要求;4.粗胚表面光滑,表面粗糙度不得大于xx;5.配重类粗胚材质表面良好,应无明显模痕、缺料、变形现象;其它翻砂类产品抛光、抛砂后无明显瑕疵;6.抛光时纹路一致、抛线细腻、不出现粗砂纹、起层、外表面需平整光滑无腊垢,表面砂眼抛光后在同一可视面可接受两处且大小不能超过1mm;7.外观造型花纹整批一致,与样品对比无明显差异;8.产品不可有毛刺、批锋、利边;焊接组件:1.焊接工艺:铜焊、银焊、铁焊、碰焊、亚弧焊、二氧化碳焊等2.所有焊接零件需打砂后方可焊接;3.焊接要牢固,不能虚焊、漏焊;4.焊接尺寸要控制在公差范围内,角度要准确;5.焊接时不能使产品变形且焊疤面积不能太大;6.管类焊接时不能堵塞管;7.抛光纹路一致,扫线正确、抛线细腻、不出现粗砂纹、起层、外表面需平整光滑无蜡垢,表面外观后同一可视面不能出现两处大于2mm之瑕疵。
五金模具设计规范
五金模具设计规范1.目的:为了规范五金模具设计,进一步完善设计标准,推行标准作业,降低模具设计错误率,实现模具设计快速作业,适应工厂发展要求,提高公司机械化、自动化程度,不断创新、不断完善、提高公司的模具设计水平,特制订本规范.2.范围:适用于本公司所有五金模具的设计.3.权责:3.1.设计课:负责所有的模具设计工作.4.定义:5.作业内容:5.1.设计前期确认分析5.1.1.模具设计分析:接到客户/技术部的开模相关资料(CAD图文件,3D图文件或实物产品)及技术要求,针对资料和要求按以下内容进行开模前评估:5.1.1.1.模具在设计与制作上有无困难处(例如:孔到边的距离大小,折弯高度);5.1.1.2.产品本身的展开后是否有干涉或强度不足;5.1.1.3.原材料特性性能是否满足要求,可能会产生的缺陷(如撕裂、抽引高度不足等);5.1.1.4.根据以往同类模具制作经验判断可行性(冲头强度、产品尺寸公差等);5.1.1.5.生产过程中影响产品质量(成型及尺寸)的因素;5.1.1.6.后加工过程中影响产品质量(成型及尺寸)的因素;5.1.1.7.产品的料纹和披锋方向有无要求,是否要求压披锋和压披锋具体位置;5.1.1.8.产品的平面度,同心度,表面外观,垂直角度有无严格的要求以及分析个别极限偏差;5.1.1.9.根据产品的结构,产品订单量的大小确定模具结构(工程模/连续模);5.1.1.10.根据产品结构大小确定排样图和产品的出模数;5.1.1.11.产品上能否有工艺孔(如:连续模搭边料的接口要求);5.1.1.12.产品表面是否喷油/喷粉(决定孔径公差取值偏向);5.1.2.对所得资料检查完毕, 如有疑问先行提出,并经客户/技术部确认后, 再做后继工作。
如果因时间关系要先行设计,来不及确认的数据要继续主动跟进。
5.1.3.设计草图5.1.3.1.为了提高工作效率,减少修改的工作量,设计人员可以将设计意图及关键结构的构思绘制草图,经评审后,再进行后继的绘图工作。
五金模具设计规范大全(一)
冲压模具设计标准目录编号內容版本发版日2007 AA01 图框填写作业标准 1.01.0 1.0 1.0 1.0 1.0 1.0 1.0 1.0 1.0 1.0 1.0 1.0 1.0 1.0 1.0 1.0 1.0 1.0 1.0 1.0 1.0 1.0 1.0 1.0 2007 2007 2007 2007 2007 2007 2007 2007 2007 2007 2007 2007 2007 2007 2007 2007 2007 2007 2007 2007 2007 2007 2007 2007AA02 模具图面图层作业标准AA03 尺寸标注作业标准AA04 展开图画法标准AA05 工程图画法标准AA06 产品展开计算标准AA07 结构图画法标准AA08 图示注解作业标准AA09 共用件注解标准AA10 设变图档作业标准AA11 模具图档作业规范AA12 公差及间隙标准AA13 五金零件加工要求AA14 板(零)件图画法作业规范AA15 中英文对照AA16 零部件作业规范(字模冲子)AA17 五金零件作业规范(弹簧)AA18 五金零件作业规范(顶料销)AA19 五金零件作业规范(导正销)AA20 五金零件作业规范(止付螺丝)AA21 零部件作业规范(圆冲子)AA22 零部件作业规范(异形冲子)AA23 零部件作业规范(切边冲子)AA24 零部件作业规范(折刀)AA25 零部件作业规范(滑块)2007 2007 2007 2007 2007 2007 2007 2007 2007 2007 2007 2007 2007 2007 2007 2007AA26 零部件 作业规范(压线冲子) AA27 零部件作业规范(压毛边冲子) AA28 零部件作业规范(压筋冲子) AA29 零部件作业规范(定位销,块) AA30 零部件作业规范(定位支承块) AA31 零部件作业规范(下模入子) AA32 加工组立工艺性 1.0 1.0 1.0 1.0 1.0 1.0 1.0 1.0 1.0 1.0 1.0 1.0 1.0 1.0 1.0 1.0AA33 小折模具结构(沙拉孔) AA34 小折模具结构(卷圆压平) AA35 模板备料作业规范(垫板夹板) AA36 模板备料作业规范 AA37 模座备料作业规范 AA38 滚轴成形公模退0.1mm 说明 AA39 铆合螺帽模具结构说明 AA40 带 N 折的成形模结构AA41 零部件作业规范(细小圆孔冲子) AA42 高凸成形方法标准件编码说明03第1页1 标准件编码规定0 3 □□—□……□—□□扩充编码 ○4 规格编码 小系列编码 大系列编码○ 2 3 ○ ○12标准件类编码表 序号 1 标准件名称 标准件分类码01 序号 标准件名称 标准件分类码21 螺丝 螺母 21 22 23 24 25 26 27浇口套(咀嘴) 2 3 02 03 04 05 06 07 08 09 10 11 12 13 14 15 16 17 18 19 20定位环 带钢球螺丝 顶出限位 22 23 24 25 26 27垫片 4 防松弹簧垫片冲针 5 支承柱 6 弹簧 锥度内6角螺塞垃圾钉7 顶针 8 内导柱(导套) 外导柱(导套)定位销 9 10 11 12 13 14 15 16 17 18 19 20顶料销 两用销 弹钉 ………………………引导销 检知销 等高套筒 华司 限位柱 下模圆形刀口 脱料圆形1 整套模具编码规定0 5 □□ □□□□□□-套数编码 ○ 4 5 ○ 月份编码 年份编码 ○ 3 ○ 等级编码 2 ○ 1大系列编码1.1列表说明○○2 ○3 ○4 ○5 1 代码说明 代码 06 说明 06年07年 08年代码 01 说明1月2月 3月 代码 01说明0102 0304 051级 2级 3级 4级 5级07 02 02 080303流水号05…… ………… …………9999年 12 12月 99(1)模具等级列表说明 代码 等级01 02 03 04 05 1级2级3级4级5级上盖板 无 S45C+M S45C+M S45C+M S45C+M S45C+铝合金 +M+TZ+YJ 上模座 无 S45C+M S45C+M S45C+M+TZ+JG上垫板 上夹板 S45C S45C 无 D2+H D2+H+W D2+H D2+H D2+H SKD11+H+S D2+H+W SKD11+CO+S D2+H+W SKD11+SC+S D2+H+W 背垫板 D2+H+W 脱料板无 D2+H+W SKD11+H+S SKD11+H+S D2+H+W SKD11+CO+S SKD11+CO+S D2+H+W SKD11+SC+S+PG SKD11+SC+S+PGD2+H+W 说 明下模板 S45C S45C 无 D2+H+W 下垫板D2+H+W 下模座 S45C+M+W SKD11+D2+W D2+SKD11+W SKD11+D2+W无S45C+M+WS45C+M+W+T2+JGS45C+M+W+TZ凹模入了 脱板入子 夹板入子 外导柱 无 SKH9+SKD11+S WC+SKH9+SKD11+S+PG WC+SKH9+SKD11+S+PG 无 SKD11+S SKD11+WC+S+PG SKD11+WC+SKH9+S+PG无 SKH9+SKD11+S WC+SKH9+SKD11+S+PG WC+SKD11+SKH9+S+PG无 钢珠导柱钢珠导柱 铜珠导柱 “一”字 导柱内导柱“一”字导柱 “一”字导柱钢珠导柱铜钛钨钢导柱(2)说明A 板件处理:H 热处理、深冷CO 、超冷SC 、调质T2、阳极YJ ;B 材质:WC 、SKH9、SKD11、D2、S45C ;C 加工方式:快走丝W 、慢走丝S 、光研PG 、内研磨JG 、铣床M 。
- 1、下载文档前请自行甄别文档内容的完整性,平台不提供额外的编辑、内容补充、找答案等附加服务。
- 2、"仅部分预览"的文档,不可在线预览部分如存在完整性等问题,可反馈申请退款(可完整预览的文档不适用该条件!)。
- 3、如文档侵犯您的权益,请联系客服反馈,我们会尽快为您处理(人工客服工作时间:9:00-18:30)。
冷冲压模具设计制造技术规范1.目的提高五金件冷冲压模具质量;建立模具标准化;统一模具的设计标准及制造技术规范。
2.适用范围本标准适用于本公司模具车间设计、制造的冷冲压模具,也适用于委外设计、制造的冷冲压模具。
3.引用标准GB1298 《碳素工具钢技术条件》GB1299 《合金工具钢技术条件》GB699 《优质碳素结构钢号和一般技术条件》GBT2854 《冲模模架技术条件》GB2870 《冷冲模零件技术条件》GB2867.5 《冷冲模卸料装置,圆柱头卸料螺钉》GB2867.6 《冷冲模卸料装置,圆柱头内角卸料螺钉》4.技术要求4.1 模具设计要点:4.1.1模具工艺编排应保证: ①模具加工之产品所有尺寸及技术要求符合图纸且品质有保障: ②模具结构合理且强度足够; ③模具制造及维修难度中等; ④模具设计寿命与预计生产订单相适应; ⑤产品及模具加工费用均最经济合理.4.1.2整体结构设计应保证: ①操作简便、安全; ②适应批量生产且效率高; ③定位可靠; ④工作精度的稳定与持久性; ⑤维护及维修方便;⑥封闭高度与所安装机床匹配; ⑦模具结构标准化.4.1.3 零件设计基本规范:4.1.3.1模架选用原则: ①原则上必须设置导向结构,对于成形类模具若在结构上可以保证质量和使用寿命及效率时可以不设置,但此必须征得模具部工艺工程师同意,冲裁模架的导向件结构设置应方便工作刃口的刃磨;②在工作中导柱导套尽可能不脱离导向,导柱长度以合模后短于闭合高度10mm为宜;③外导柱、导套的结构采用独立导柱,普通导向精度要求的模架采用滑动独立导柱(TUB),高导向精度要求的模架采用滚动独立导柱(TUR)加内导柱, 内导柱、导套的结构采用压入结构;④模架有效面积大于400X300mm的模具不得使用铸件模架,对于选用的铸件模架应符合GB2854《冷冲模模架技术条件》规定,导柱直径和数量的设置应考虑导柱的刚度和模架面积大小,模架面积大于400X300mm应选取导柱直径大于φ25mm。
4.1.3.2 模板设计规范:①凹模: ⑴厚度(B):零件尺寸300*300以下,材料厚度(T)小于1.6MM时, 凹模板厚不小于24MM;材料厚度大于1.6MM小于5MM时, 凹模板厚不小于34MM; 材料厚度大于5MM,凹模板厚不小于45MM;零件尺寸大于300*300,材料厚度小于1.6MM时, 凹模板厚不小于34MM;材料厚度大于1.6MM小于5MM时, 凹模板厚不小于44MM; 材料厚度大于5MM,凹模板厚不小于55MM. ⑵凹模工作刃口至边距(A):最小边距(A min)为凹模厚度(B)的1.5倍以上,但应大于30MM; 材料厚度大于1.6MM时, 边距(A)为凹模厚度(B)的2倍以上.②上下模座:⑴外形尺寸应稍大于凹模外形尺寸;⑵模座厚(H):尽可能选用标准化模架;普通冲模自制模架: 模座厚(H)为大于或等于凹模厚度(B)的1.4-1.8倍; 高速冲模自制模架: 模座厚(H)为大于或等于凹模厚度(B)的2.6-3.8倍.③垫板: ⑴外形尺寸与凹模外形尺寸一致;⑵厚度(H1)为5-10MM,冲裁力偏大取大值.④固定板: ⑴外形尺寸与凹模外形尺寸一致;⑵厚度(H1)一般为凹模厚度(B)的0.8-0.9倍.4.1.3.3零配件设计时采用标准件.4.2薄板料冲裁模设计要点:薄板料冲裁模的结构基本上与普通冲裁模相同,但由于其凸、凹模间隙比普通模要小得多,在结构上有其独特的特点,板料冲模大都采用浮动模柄结构,以消除压力机导轨误差对冲模导向精度的影响。
薄板料冲模一般采用滚珠导柱模架或导套可调式模架。
对于特别薄的板料冲压,要采用3-4支导柱、导套做为导向,以提高模具的导向精度。
⑴ 薄板料冲模的压力中心应与上模的重心完全重合,重心不得偏斜,以免影响冲裁精度和制品零件的质量。
⑵ 薄板冲模要求导向精度较高,一般采用滚珠导向模架,在使用时,导柱、导套要始终配合,绝不能脱出。
(3)在装配时,凸模与凹模应保证良好的同轴度等级。
(4)在设计卸料和顶件装置时,其顶出器与凹模、卸料板与凸凹模应设计成Ⅱ级精度间隙(H7/h6)。
由于冲裁的板料很薄,冲出的制品零件容易粘附在顶出器上,在顶出器应设计有脱料器,零件在冲出后借助于脱料器排除。
为了保证薄板料冲模刃口的配合精度,模具的有关部件如底座、固定板、导套、导柱等的加工精度及平行度、垂直度及同轴度,加工时必须得到保证。
各部件的钢性要好。
底座及固定板在加工前要进行时效处理,以免在使用期间产生形变,影响冲裁件的质量与精度。
4.3常规技术规范:4.3.1重量超过50kg的模具应设置起吊环或起吊装置,并考虑模具叉吊方便性。
4.3.2对于下漏料的冲裁模模具冲裁范围大于500X400,下模应加装固定框架结构的垫块,以方便安装和废料排出方便。
大型模具框架允许采用铸件结构,但压装部分必须有方便装夹面。
4.3.3模具主要零件的材料选择必须符合附表所列的最低材料选择要求,所选择的材料技术指标应符合GB1298《碳素工具钢技术条件》,GB1299《合金工具钢技术条件》,GB699《优质碳素结构钢号和一般技术条件》,允许材料代料使用,但代用材料的机械性能不得低于原定材料,否则必须征得模具部认可.表1:零件名称 凸模 凹模 卸料模 垫板冲裁类模具 Cr12MoV,Cr12,SKD1145钢 45钢硬度 HRC58-64 HRC35-45 HRC35-45成形类模具 Cr12MoV,Cr12,SKD1145钢 45钢硬度 HRC55-60 HRC35-45 HRC35-454.3.4模具主要件的热处理硬度必须符合上表所指定的要求,其各零件的热处理硬度应满足于结构和使用寿命的要求,并符合于国家有关行业标准。
4.3.5对于冲裁模具原则上要求凸模与卸料板成导向的间隙配合H7/g6,对于凸模直径小于φ5的应考虑导向保护,对于孔冲裁和导向刚度不足的卸料板需增设足够数量的小导柱导向。
4.3.6对于需漏料的冲裁模具其凹模的刃口长度为:冲裁料厚小于1mm的刃口长度为5-8mm,冲裁料厚大于1mm的刃口长度为8-10mm,对于刃口与卸料板配合的结构应考虑全刃口长度。
4.3.7冲裁模具的冲裁刃口应达到Ra0.4的粗糙度要求,对于成形模具其工作面应达到Ra0.8的粗糙度要求。
冲裁模的凸模,凹模与凸凹模的冲裁轮廓尖角,除特别指明外,一律按R1制造。
4.3.8条料上冲孔时,板厚与搭边的关系见下表弧边边距直边边距 板厚 t(mm) A min(mm) 板厚 t(mm) B min(mm)1.55以下 3.12.3以下 4.61.55以上 2t2.3以上 2t4.3.9对于直径面积在φ4mm以下的小孔冲裁,其模架面积大于700X600的模具,在结构设计上尽可能考虑易损件的快速更换结构,并考虑不少于2次~3次的易损件的更换备件。
4.3.10卸料板的连接螺钉必须采用GB2867.5《冷冲模卸料装置,园柱头卸料螺钉》,GB2867.6《冷冲模卸料装置,园柱头内六角卸螺钉》所规定的卸料螺钉,或类似此结构的其它吊连方式,卸料螺钉的吊止面应考虑在一个连续平面上,所有螺钉必须拧紧,严防松动;模具精度要求较高时,采用等高套筒加螺钉结构。
4.3.11模具所用的弹性材料应选用重载弹簧,经协商后可采用指定性的聚氨脂橡胶,杜绝使用普通黑橡胶作弹性件。
4.3.12模具的设计制造寿命应保证:冲裁类模具每次刃磨寿命不少于八千次,冲裁(毛刺高度0.15mm),总寿命不低于50万次。
成型类模具其磨损面应保证总使用寿命不少于50万次的使用。
模具交付时冲裁毛刺的极限高度须小于下表所列要求。
表2:冲裁轮廓材料厚度(t)δs>200Mpa范围 0-0.5 >0.5-1 >1-1.6 >1.6-3 <240×2400.06 0.1 0.12 0.18>240×2400.08 0.12 0.16 0.2注:此毛刺要求适用于材料屈服极限δs<200Mpa对于δs>200Mpa的按此对应值放大30%4.3.13对于线性长度大于400mm的模具应在结构设计上注意加强其凹模的整体刚度,对于拼合结构其受力方向的支撑刚度必须足够,结构用定位销钉数量应足够多,要求两销钉间隔不大于200mm.4.3.14冷冲压模所有经磨削的零件在装配前均应退磁.模具交付时应保证无磁性。
4.3.15装配后的冲裁凸模、凹模凸凹模的工件端面应磨平,保证粗糙度Ra0.4。
4.3.16由模具部确定的重要或关键工序的模具其结构必须经过模具部的技术确认。
4.3.17模具通用技术要求应符合GB2870《冷冲模零件技术条件》规定。
4.4模具试模规范4.4.1模具试模所选用设备的精度必须达到机床说明书规定的最低工作精度要求。
试模所用材料必须符合模具设计制造时所给定的材料标准。
若一时无规定材料,则代料试模必须经开发部工程师认可。
4.4.2模具试模前应在上、下模具周边涂刷规定色彩的油漆,其余部位应涂油防锈,在正面的标记处打上标记,内容包括:产品名称、产品编号、工序数/总工序数、工序名称及制成日期。
标记示例:锅体 DF12-23/001 1/6 冲孔/落料 03/08/08。