运筹学---案例分析
管理运筹学的部分案例分析

精品课件
管理运筹学
12
案例分析—如何合理使用技术培训
因培训而产生的增加值
精品课件
管理运筹学
13
案例分析—光明制造厂经营报告书
Y2=10X0+(0.08X1+0.085X2+0.09X3+0.105X5)×700
精品课件
管理运筹学
14
案例分析—光明制造厂经营报告书
精品课件
管理运筹学
2
案例分析—北方化工厂月生产计划
精品课件
管理运筹学
3
案例分析—北方化工厂月生产计划
X2≦0.05∑xi
X3+X4 ≦X1
Y3 ≦4000
Xi≧0
精品课件
管理运筹学
4
案例分析—监理工程师配置问题
• 目标函数 • 约束条件 • 决案例分析—监理工程师配置问题
精品课件
15
案例分析—北方食品公司投资方案规划
精品课件
管理运筹学
16
案例分析—北方食品公司投资方案规划
精品课件
管理运筹学
17
案例分析—北方食品公司投资方案规划
精品课件
管理运筹学
18
案例分析—北方食品公司投资方案规划
精品课件
管理运筹学
19
案例分析
• 1、北方化工厂月生产计划 • 2、石华建设监理公司监理工程师配置
问题
• 3、北方印染公司就如何合理使用技术 培训费
• 4、光明制造厂经营报告书 • 5、北方食品公司投资方案规划
精品课件
管理运筹学
1
案例分析—北方化工厂月生产计划
1、目标函数 2、成品率问题如何处理 3、约束条件
精品课件
运筹学实例 含解析

案例1. 工程项目选择问题某承包企业在同一时期内有八项工程可供选择投标。
其中有五项住宅工程,三项工业车间。
由于这些工程要求同时施工,而企业又没有能力同时承担,企业应根据自身的能力,分析这两类工程的盈利水平,作出正确的投标方案。
有关数据见下表:表1 可供选择投标工程的有关数据统计工程类型 预期利润/元 抹灰量/m 2混凝土量/ m 3砌筑量/ m 3住宅每项 50011 25 000 280 4 200 工业车间每项 80 000480 880 1 800 企业尚有能力108 0003 68013 800试建立此问题的数学模型。
解:设承包商承包X 1项住宅工程,X 2项工业车间工程可获利最高,依题意可建立如下整数模型:目标是获利最高,故得目标函数为21X 80000X 50011z Max +=根据企业工程量能力限制与项目本身特性,有约束:利用WinSQB 建立模型求解:1080002X 4801X 25000≤+3680X 880X 28021≤+13800X 1800X 420021≤+为整数,;,2121X X 3X 5X ≤≤综上,承包商对2项住宅工程,3项车间工程进行投标,可获利最大,目标函数Max z=340022 元。
案例2. 生产计划问题某厂生产四种产品。
每种产品要经过A,B两道工序加工。
设该厂有两种规格的设备能完成A工序,以A1 ,A2表示;有三种规格的设备能完成B工序,以B1 ,B2,B3 表示。
产品D可在A,B任何一种规格的设备上加工。
产品E可在任何规格的A设备上加工,但完成B工序时只能在B1设备上加工。
产品F可在A2及B2 ,B3上加工。
产品G可在任何一种规格的A设备上加工,但完成B工序时只能在B1 ,B2设备上加工。
已知生产单件产品的设备工时,原材料费,及产品单价,各种设备有效台时如下表,要求安排最优的生产计划,使该厂利润最大?设设产品设备有效台时1 2 3 4A1 A2 B1 B2 B357647109812111068108601110000400070004000原料费(元/件)单价(元/件)0.251.250.352.000.502.800.42.4解:设Xia(b)j为i产品在a(b)j设备上的加工数量,i=1,2,3,4;j=1,2,3,得变量列表设备产品设备有效台时Ta(b)j1 2 3 4A1 A2 B1 B2 B3X1a1X1a2X1b1X1b2X1b3X2a1X2a2X2b1X3b2X3b3X3a1X3a2X3b1X3b2X3b3X4a1X4a2X4b1X4b2X4b3601110000400070004000原料费Ci (元/件) 单价Pi (元/件) 0.25 1.25 0.352.00 0.50 2.80 0.4 2.4其中,令X 3a 1,X 3b 1,X 3b 2,X 3b 3,X 4b 3=0 可建立数学模型如下: 目标函数: ∑∑==-=4121)](*[Maxi j iaj Ci Pi X z=1.00*(X 1a 1+X 1a 2)+1.65*(X 2a 1+X 2a 2)+2.30* X 3a 2+2.00*( X 4a 1+X 4a 2)约束条件:利用WinSQB 求解(X1~X4,X5~X8,X9~X12,X13~X17,X18~X20分别表示各行变量):4,3,2,1X21j 31==∑∑==i X j ibjiaj2,1T X 41iaj=<=∑=j Taj i iaj 3,2,141=<=∑=j TbjT Xi ibj ibj2,1;4,3,2,10X iaj ==>=j i 且为整数32,1;4,3,2,10X ibj ,且为整数==>=j i 0X X X X X 4b33b33b23b13a1=====综上,最优生产计划如下:设备产品1 2 3 4A1 A2 B1 B2 B3774235004004008732875目标函数zMax=3495,即最大利润为3495案例3. 高校教职工聘任问题 (建摸)由校方确定的各级决策目标为:P 1 要求教师有一定的学术水平。
运筹学在物流管理中的应用 案例解析
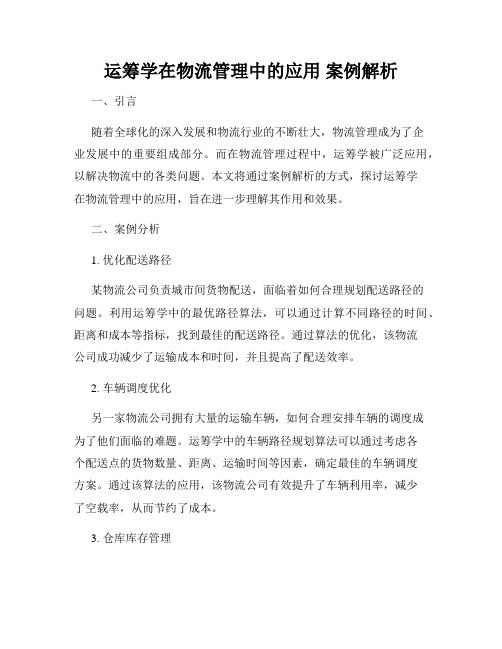
运筹学在物流管理中的应用案例解析一、引言随着全球化的深入发展和物流行业的不断壮大,物流管理成为了企业发展中的重要组成部分。
而在物流管理过程中,运筹学被广泛应用,以解决物流中的各类问题。
本文将通过案例解析的方式,探讨运筹学在物流管理中的应用,旨在进一步理解其作用和效果。
二、案例分析1. 优化配送路径某物流公司负责城市间货物配送,面临着如何合理规划配送路径的问题。
利用运筹学中的最优路径算法,可以通过计算不同路径的时间、距离和成本等指标,找到最佳的配送路径。
通过算法的优化,该物流公司成功减少了运输成本和时间,并且提高了配送效率。
2. 车辆调度优化另一家物流公司拥有大量的运输车辆,如何合理安排车辆的调度成为了他们面临的难题。
运筹学中的车辆路径规划算法可以通过考虑各个配送点的货物数量、距离、运输时间等因素,确定最佳的车辆调度方案。
通过该算法的应用,该物流公司有效提升了车辆利用率,减少了空载率,从而节约了成本。
3. 仓库库存管理某电商企业拥有多个仓库,需要根据订单情况合理规划仓库之间的货物调拨,以最大程度地减少库存和仓储成本。
运筹学中的库存模型可以通过统计订单需求和仓库存量,实现供需的匹配,避免库存过多或过少的问题。
该电商企业成功应用了库存模型,减少了库存积压,提高了物流配送效率。
4. 运输网络规划一家物流公司计划扩大业务范围,需要合理布局运输网络。
运筹学中的网络设计模型可以通过综合考虑各个节点的运输距离、成本、需求量等因素,确定最佳的网络布局方案。
利用该模型,该物流公司成功打造了高效的运输网络,实现了物流资源的合理配置,提升了服务水平。
三、结论通过以上案例的解析,我们可以清楚地看到运筹学在物流管理中的重要作用。
无论是优化配送路径、车辆调度优化、仓库库存管理还是运输网络规划,运筹学都可以通过建立数学模型、运用优化算法等方式,帮助物流企业降低成本、提高效率、实现优质服务。
因此,运筹学在物流管理中的应用是不可忽视的,并且在未来的发展中将会发挥更大的作用。
运筹学案例分析

案例五炼油厂生产计划优化炼油厂购买两种原油(原油1和原油2),这些原油经过四道工序处理:分馏、重整、裂化和调和,得到各种汽油、煤油和润滑油产品。
1、分馏分馏将每一种原油根据沸点不同分解为轻石脑油、中石脑油、重石脑油、轻油、重油和残油。
轻、中、重石脑油的辛烷值分别是90、80和70,每桶原油可以产生的各种油分如下表:表8 原油分馏得到的油分(桶/桶)轻石脑油中石脑油重石脑油轻油重油残油合计原油1 0.10 0.20 0.20 0.12 0.20 0.13 0.95原油2 0.15 0.25 0.18 0.08 0.19 0.12 0.97从上表可以看出,在分馏过程中有少量损耗。
2、重整各类石脑油可以用于调合成不同等级的汽油,也可以进入重整过程。
重整过程产生辛烷值为115的重整汽油,不同的石脑油经过重整可以得到的重整汽油为:表9 石脑油经过重整后提到的重整汽油(桶/桶)轻石脑油中石脑油重石脑油重整汽油0.6 0.52 0.45从表中可以看出,重整汽油的损耗量是非常大的。
重整汽油的主要目的是提高辛烷值。
3、裂化轻油和重油可以用于调合产生航空煤油和煤油,也可以经过催化裂化过程而同时产生裂化油和裂化汽油,裂化汽油的辛烷值为105,轻油和重油裂化产生的产品如下:表10 轻油重油裂化产生的产品(桶/桶)裂化油裂化汽油轻油0.68 0.28重油0.75 0.20裂化过程中同样有少量损耗。
裂化油可以用于调合成煤油和航空煤油,裂化汽油可用于调合汽油。
残油可以用来生产润滑油或者用于调合航空煤油或煤油,一桶残油可以产生0.5桶润滑油。
4、调合(1)汽油(发动机燃料)有两种类型的汽油,普通汽油和高级汽油。
这两种汽油都可以用石脑油、重整汽油和裂化汽油调合得到,且调合过程中没有重量损失。
要求:普通汽油的辛烷值必须不低于84,而高级汽油的辛烷值必须不低于94,我们假定,调合成的汽油的辛烷值与各成份的辛烷值及含量成线性关系。
(2)航空煤油航空煤油同样可以用汽油、重油、裂化油和残油调合而成,且调合过程中重量没有损失。
运筹学在实际问题中的应用案例分析
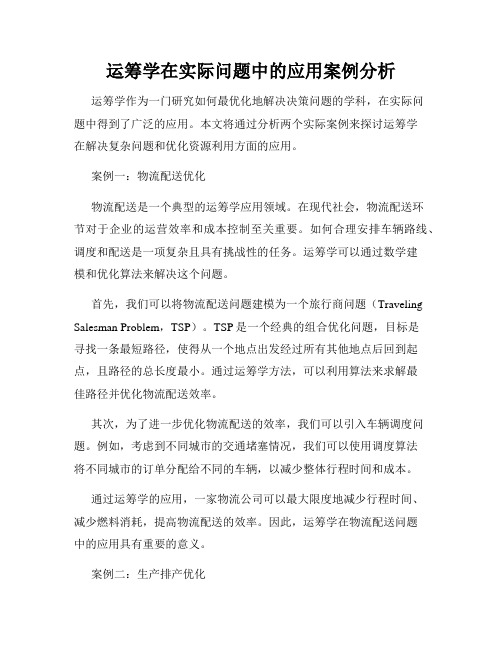
运筹学在实际问题中的应用案例分析运筹学作为一门研究如何最优化地解决决策问题的学科,在实际问题中得到了广泛的应用。
本文将通过分析两个实际案例来探讨运筹学在解决复杂问题和优化资源利用方面的应用。
案例一:物流配送优化物流配送是一个典型的运筹学应用领域。
在现代社会,物流配送环节对于企业的运营效率和成本控制至关重要。
如何合理安排车辆路线、调度和配送是一项复杂且具有挑战性的任务。
运筹学可以通过数学建模和优化算法来解决这个问题。
首先,我们可以将物流配送问题建模为一个旅行商问题(Traveling Salesman Problem,TSP)。
TSP是一个经典的组合优化问题,目标是寻找一条最短路径,使得从一个地点出发经过所有其他地点后回到起点,且路径的总长度最小。
通过运筹学方法,可以利用算法来求解最佳路径并优化物流配送效率。
其次,为了进一步优化物流配送的效率,我们可以引入车辆调度问题。
例如,考虑到不同城市的交通堵塞情况,我们可以使用调度算法将不同城市的订单分配给不同的车辆,以减少整体行程时间和成本。
通过运筹学的应用,一家物流公司可以最大限度地减少行程时间、减少燃料消耗,提高物流配送的效率。
因此,运筹学在物流配送问题中的应用具有重要的意义。
案例二:生产排产优化生产排产是制造业中的一个重要环节,它关系到企业的生产效率、生产能力和订单交付时间。
运筹学在生产排产中的应用可以帮助企业提高生产效率,降低成本并及时交付产品。
在生产排产中,我们通常需要考虑到多个因素,如机器的利用率、工人的工作时间和任务的优先级等。
通过运筹学的方法,可以构建一个数学模型,通过数学规划算法来优化生产排产方案。
例如,假设一个工厂有多个机器和多个订单需要排产,每个订单有不同的完成时间和优先级。
我们可以通过运筹学的方法,将这个问题建模为一个调度问题。
然后,利用调度算法来确定每个订单的完成时间和最优的生产顺序,从而实现生产排产的优化。
通过运筹学的应用,企业可以有效地优化生产排产计划,提高生产效率,减少资源浪费,并保证订单能够及时交付。
运筹学在流程优化中的应用案例分析
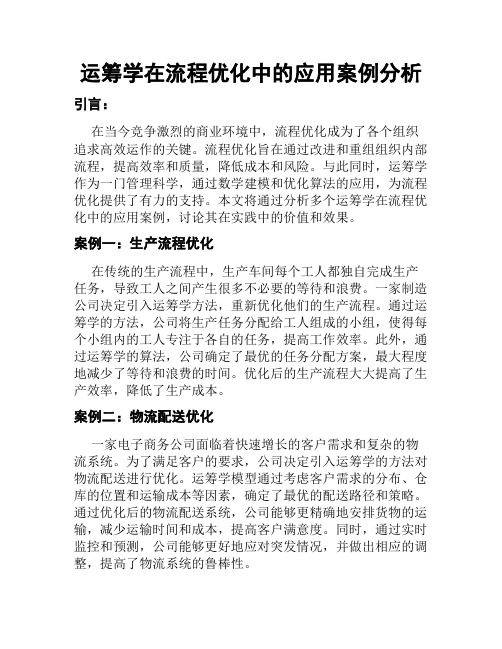
运筹学在流程优化中的应用案例分析引言:在当今竞争激烈的商业环境中,流程优化成为了各个组织追求高效运作的关键。
流程优化旨在通过改进和重组组织内部流程,提高效率和质量,降低成本和风险。
与此同时,运筹学作为一门管理科学,通过数学建模和优化算法的应用,为流程优化提供了有力的支持。
本文将通过分析多个运筹学在流程优化中的应用案例,讨论其在实践中的价值和效果。
案例一:生产流程优化在传统的生产流程中,生产车间每个工人都独自完成生产任务,导致工人之间产生很多不必要的等待和浪费。
一家制造公司决定引入运筹学方法,重新优化他们的生产流程。
通过运筹学的方法,公司将生产任务分配给工人组成的小组,使得每个小组内的工人专注于各自的任务,提高工作效率。
此外,通过运筹学的算法,公司确定了最优的任务分配方案,最大程度地减少了等待和浪费的时间。
优化后的生产流程大大提高了生产效率,降低了生产成本。
案例二:物流配送优化一家电子商务公司面临着快速增长的客户需求和复杂的物流系统。
为了满足客户的要求,公司决定引入运筹学的方法对物流配送进行优化。
运筹学模型通过考虑客户需求的分布、仓库的位置和运输成本等因素,确定了最优的配送路径和策略。
通过优化后的物流配送系统,公司能够更精确地安排货物的运输,减少运输时间和成本,提高客户满意度。
同时,通过实时监控和预测,公司能够更好地应对突发情况,并做出相应的调整,提高了物流系统的鲁棒性。
案例三:人力资源调度优化在一个大型医院中,不同科室之间的人力资源分配存在瓶颈和浪费。
为了解决这个问题,医院决定应用运筹学模型来优化人力资源的调度。
通过运筹学的方法,医院能够根据就诊人数的预测和就诊科室的需求来合理安排医生和护士的工作。
通过优化后的人力资源调度,医院能够提高科室的工作效率,减少等待时间,并提供更好的医疗服务。
此外,通过运筹学的优化算法,医院还能够合理安排员工的休假和轮班,提高员工的满意度和工作积极性。
案例四:供应链优化一家零售公司面临着供应链管理的挑战,包括供货商管理、库存管理和订单管理等。
运筹学案例分析1
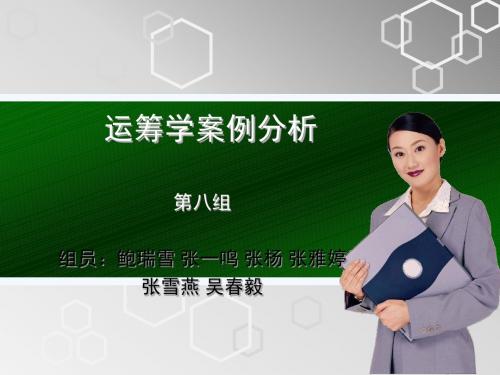
四、模型求解
1、求解工具 Excel线性规划求解模板 2、求解结果 本题为多解问题,由线性规划模板可求解出不同的最优 解,但最优值确定。现列举几种结果如下:
四、模型求解
2、求解结果(1)
四、求解模型
2、求解结果(2) ()
四、模型求解
2、求解结果(3)
五、结论
1、决策绩效评价 该模型有效解决了两辆车的分配运输问题,使得浪费的 空间最小,提高了资源的利用率。但是因为最优解为多解, 所以在最优方案的选择上又面临着难题。
2、目标函数的确定 •本问题的目标是使把全部包装箱装在两辆平板车上而使所浪 费的的空间最小,全部包装箱所占的空间为: 48.7x1+25.0x2+36.1x3+54.0x4+36.7x5+32.0x6+46.5x7+48.7x8 +25.0x9+36.1x10+54.0x11+36.7x12+32.0x13+46.5x14; •所以本题的目标函数为: minf=48.7x1+25.0x2+36.1x3+54.0x4+36.7x5+32.0x6+46.5x7+ 48.7x8+25.0x9+36.1x10+54.0x11+36.7x12+32.0x13+46.5x14;
三、模型构建
3、约束条件的确定 ⑴由包装箱的数量确定可得:x1+x8=8 x2+x9=7 x3+x10=9 x4+x11=6 x5+x12=6 x6+x13=4 x7+x14=8
三、模型构建
3、约束条件的确定 ⑵由每辆平板车有10.2米长的地方可用来装包装箱可得: 48.7x1+25x2+36.1x3+54x4+36.7x5+32x6+46.5x7≤1020; 48.7x8+25x9+36.1x10+54x11+36.7x12+32x13+46.5x14≤1020. ⑶每辆平板车的载重为50吨可得:
运筹学实例分析及lingo求解讲解

运筹学实例分析及lingo 求解一、线性规划某公司有6个仓库,库存货物总数分别为60、55、51、43、41、52,现有8个客户各要一批货,数量分别为35,37,22,32,41,32,43,38。
各供货仓库到8个客户处的单位货物运输价见表试确定各仓库到各客户处的货物调运数量,使总的运输费用最小。
解:设ijx 表示从第i 个仓库到第j 个客户的货物运量。
ij c表示从第i 个仓库到第j 个客户的单位货物运价,i a 表示第i 个仓库的最大供货量,j d 表示第j 个客户的订货量。
目标函数是使总运输费用最少,约束条件有三个:1、各仓库运出的货物总量不超过其库存数2、各客户收到的货物总量等于其订货数量3、非负约束数学模型为:∑∑===6181)(min i j ijij x c x f⎪⎪⎪⎪⎩⎪⎪⎪⎪⎨⎧≥===≤∑∑==08,,2,1,6,2,1,,..6181ij j i ij i j ij x j d x i a x t s 编程如下:model : Sets :Wh/w1..w6/:ai; Vd/v1..v8/:dj;links(wh,vd):c,x;endsetsData:ai=60,55,51,43,41,52;dj=35,37,22,32,41,32,43,38;c=6,2,6,7,4,2,5,94,9,5,3,8,5,8,25,2,1,9,7,4,3,37,6,7,3,9,2,7,12,3,9,5,7,2,6,55,5,2,2,8,1,4,3;EnddataMin=@sum(links(i,j):c(i,j)*x(i,j));@for(wh(i):@sum(vd(j):x(i,j))<=ai(i));@for(vd(j):@sum(wh(i):x(i,j))=dj(j));endGlobal optimal solution found.Objective value: 664.0000Total solver iterations: 0Variable Value Reduced Cost AI( W1) 60.00000 0.000000 AI( W2) 55.00000 0.000000 AI( W3) 51.00000 0.000000 AI( W4) 43.00000 0.000000 AI( W5) 41.00000 0.000000 AI( W6) 52.00000 0.000000 DJ( V1) 35.00000 0.000000 DJ( V2) 37.00000 0.000000 DJ( V3) 22.00000 0.000000 DJ( V4) 32.00000 0.000000 DJ( V5) 41.00000 0.000000 DJ( V6) 32.00000 0.000000 DJ( V7) 43.00000 0.000000 DJ( V8) 38.00000 0.000000 C( W1, V1) 6.000000 0.000000 C( W1, V2) 2.000000 0.000000 C( W1, V3) 6.000000 0.000000 C( W1, V4) 7.000000 0.000000 C( W1, V5) 4.000000 0.000000 C( W1, V6) 2.000000 0.000000 C( W1, V7) 5.000000 0.000000C( W2, V1) 4.000000 0.000000 C( W2, V2) 9.000000 0.000000 C( W2, V3) 5.000000 0.000000 C( W2, V4) 3.000000 0.000000 C( W2, V5) 8.000000 0.000000 C( W2, V6) 5.000000 0.000000 C( W2, V7) 8.000000 0.000000 C( W2, V8) 2.000000 0.000000 C( W3, V1) 5.000000 0.000000 C( W3, V2) 2.000000 0.000000 C( W3, V3) 1.000000 0.000000 C( W3, V4) 9.000000 0.000000 C( W3, V5) 7.000000 0.000000 C( W3, V6) 4.000000 0.000000 C( W3, V7) 3.000000 0.000000 C( W3, V8) 3.000000 0.000000 C( W4, V1) 7.000000 0.000000 C( W4, V2) 6.000000 0.000000 C( W4, V3) 7.000000 0.000000 C( W4, V4) 3.000000 0.000000 C( W4, V5) 9.000000 0.000000 C( W4, V6) 2.000000 0.000000 C( W4, V7) 7.000000 0.000000 C( W4, V8) 1.000000 0.000000 C( W5, V1) 2.000000 0.000000 C( W5, V2) 3.000000 0.000000 C( W5, V3) 9.000000 0.000000 C( W5, V4) 5.000000 0.000000 C( W5, V5) 7.000000 0.000000 C( W5, V6) 2.000000 0.000000 C( W5, V7) 6.000000 0.000000 C( W5, V8) 5.000000 0.000000 C( W6, V1) 5.000000 0.000000 C( W6, V2) 5.000000 0.000000 C( W6, V3) 2.000000 0.000000 C( W6, V4) 2.000000 0.000000 C( W6, V5) 8.000000 0.000000 C( W6, V6) 1.000000 0.000000 C( W6, V7) 4.000000 0.000000 C( W6, V8) 3.000000 0.000000 X( W1, V1) 0.000000 5.000000 X( W1, V2) 19.00000 0.000000 X( W1, V3) 0.000000 5.000000X( W1, V5) 41.00000 0.000000 X( W1, V6) 0.000000 2.000000 X( W1, V7) 0.000000 2.000000 X( W1, V8) 0.000000 10.00000 X( W2, V1) 1.000000 0.000000 X( W2, V2) 0.000000 4.000000 X( W2, V3) 0.000000 1.000000 X( W2, V4) 32.00000 0.000000 X( W2, V5) 0.000000 1.000000 X( W2, V6) 0.000000 2.000000 X( W2, V7) 0.000000 2.000000 X( W2, V8) 0.000000 0.000000 X( W3, V1) 0.000000 4.000000 X( W3, V2) 11.00000 0.000000 X( W3, V3) 0.000000 0.000000 X( W3, V4) 0.000000 9.000000 X( W3, V5) 0.000000 3.000000 X( W3, V6) 0.000000 4.000000 X( W3, V7) 40.00000 0.000000 X( W3, V8) 0.000000 4.000000 X( W4, V1) 0.000000 4.000000 X( W4, V2) 0.000000 2.000000 X( W4, V3) 0.000000 4.000000 X( W4, V4) 0.000000 1.000000 X( W4, V5) 0.000000 3.000000 X( W4, V6) 5.000000 0.000000 X( W4, V7) 0.000000 2.000000 X( W4, V8) 38.00000 0.000000 X( W5, V1) 34.00000 0.000000 X( W5, V2) 7.000000 0.000000 X( W5, V3) 0.000000 7.000000 X( W5, V4) 0.000000 4.000000 X( W5, V5) 0.000000 2.000000 X( W5, V6) 0.000000 1.000000 X( W5, V7) 0.000000 2.000000 X( W5, V8) 0.000000 5.000000 X( W6, V1) 0.000000 3.000000 X( W6, V2) 0.000000 2.000000 X( W6, V3) 22.00000 0.000000 X( W6, V4) 0.000000 1.000000 X( W6, V5) 0.000000 3.000000 X( W6, V6) 27.00000 0.000000 X( W6, V7) 3.000000 0.000000Row Slack or Surplus Dual Price 1 664.0000 -1.000000 2 0.000000 3.000000 3 22.00000 0.000000 4 0.000000 3.000000 5 0.000000 1.000000 6 0.000000 2.000000 7 0.000000 2.000000 8 0.000000 -4.000000 9 0.000000 -5.000000 10 0.000000 -4.000000 11 0.000000 -3.000000 12 0.000000 -7.000000 13 0.000000 -3.000000 14 0.000000 -6.000000 15 0.000000 -2.000000由以上结果可以清楚的看到由各仓库到各客户处的货物调运数量,由此得出的符合条件的最佳运货方案,而使运费最低,最低为664。
- 1、下载文档前请自行甄别文档内容的完整性,平台不提供额外的编辑、内容补充、找答案等附加服务。
- 2、"仅部分预览"的文档,不可在线预览部分如存在完整性等问题,可反馈申请退款(可完整预览的文档不适用该条件!)。
- 3、如文档侵犯您的权益,请联系客服反馈,我们会尽快为您处理(人工客服工作时间:9:00-18:30)。
管理运筹学案例分析
产品产量预测
一、问题的提出
2007年,山西潞安矿业集团与哈密煤业集团进行重组,成立了潞安新疆煤化工(集团)有限公司。
潞安新疆公司成立后,大力加快新项目建设。
通过技术改造和加强管理,使煤炭产量、销售收入、利润、职工收入等得到了大幅提高,2007年生产煤炭506万吨,2008年煤炭产量726万吨,2009年煤炭产量956万吨。
三年每月产量见下表,请预测2010年每月产量。
表1 2007—2009年每月产量表单位:万吨
二、分析与建立模型
1、根据2007—2009年的煤炭产量数据,可做出下图:
表2 2007—2009年每月产量折线图
由上图可看出,2007—2009年的煤炭产量数据具有明显的季节性因素和总体上升趋势。
因此,我们采取用体现时间序列的趋势和季节因素的预测方法。
(一)、用移动平均法来消除季节因素和不规则因素影响
1、取n=12;
2、将12个月的平均值作为消除季节和不规则因素影响后受趋势因素影响的数值;
3、计算“中心移动平均值”;
4、计算每月与不规则因素的指标值。
表3 平均值表
5、计算月份指数;
6、调整月份指数。
表4 调整(后)的月份指数
(二)、去掉时间序列中的月份因素
将原来的时间序列的每一个数据值除以相应的月份指数。
表5 消除月份因素后的时间序列表
三、计算结果及分析
确定消除季节因素后的时间序列的趋势。
求解趋势直线方程。
设直线方程为:
T t =b0+b1 t
T t为求每t 时期煤炭产量;b0为趋势直线纵轴上的截距;b1为趋势直线的斜率。
求得:
四、一点思考
新疆的煤矿生产企业产能只是企业要考虑的部分因素,因国家产业政策以及新疆距离内地需经河西走廊,因此,企业不仅要考虑产能,更多的要考虑运输问题,从某种意义上来说,东疆地区煤炭生产企业不是“以销定产”,而是“以运定产”,也就是说,物流运输方案是企业管理人员要认真思考的问题。
本案例可以结合物流运输远近及运输工具的选择作进一步的
运筹分析,以使得煤炭生产企业真正实现科学合理决策。
配矿计划编制(MBA10秋3班4组)
一、问题的提出
某大型冶金矿山公司共有14个出矿点,年产量及各矿点矿石的平均品位(含铁量的百分比)均为已知(见表1)。
表1 矿点出矿石量及矿石平均品位表
按照冶金生产,具体说这里指炼铁生产的要求,在矿石采出后,需按要求指定的品位值T Fe进行不同品位矿石的混合配料,然后进入烧结工序,最后,将小球状的烧结球团矿送入高炉进行高温冶炼,生产出生铁。
该企业要求:将这14个矿点的矿石进行混合配矿。
依据现有生产设备及生产工艺的要求,混合矿石的平均品位T Fe规定为45%。
问:如何配矿才能获得最佳的效益?
二、分析与建立模型
负责此项目研究的运筹学工作者,很快判定此项目属于运筹学中最成熟的分支之一——线性规划的范畴。
而且是一个小规模问题。
1.设计变量:记Xj(j=1,2,*,14)分别表示出矿点1 14所产矿石中参与配矿的数量(单位:万吨)。
2.约束条件:包括三部分:
(1)供给(资源)约束:由表1,有
X1≤70 ,X2≤ 7 ,…,X14 ≤ 7.2
(2)品位约束:
0.3716X1+0.5125X2+…+0.5020X14=0.4500∑X j
(3)非负约束:
Xj≥0 j=1,2,…,14
3.目标函数:
此项目所要求的“效益最佳”。
作为决策准则有一定的模糊性。
由于配矿后混合矿石将作为后面工序的原料而产生利润,故在初始阶段,可将目标函数选作配矿总量,并追求其极大化。
于是,可得出基本(LP)模型如下:
(LP) Max Z=∑X j
s.t. 0≤ X1≤70
0≤ X2≤ 7
……
0≤ X14 ≤ 7.2
0.3716X1+0.5125X2+…+0.5020X14=0.4500∑X j
三、计算结果及分析
(一)计算结果
使用单纯形算法,极易求出此模型的最优解:
X*=(X*1,X*2,…,X*14)T,它们是:
X*1 =31.121 X*2 = 7 X*3 =17
X*4 =23 X*5 = 3 X*6 = 9.5
X*7 = 1 X*8 =15.4 X*9 = 2.7
X*10= 7.6 X*11=13.5 X*12= 2.7
X*13=1.2 X*14= 7.2 (单位:万吨)
目标函数的最优值为:
Z*= ∑X*j =141.921(万吨)
(二)分析与讨论
按照运筹学教材中所讲述的方法及过程,此项目到此似乎应该结束了。
但是,这是企业管理中的一个真实的问题。
因此,对这个优化计算结果需要得到多方面的检验。
这个结果是否能立即为公司所接受呢?回答是否定的!
注意!在最优解X*中,除第1个矿点有富余外,其余13个矿点的出矿量全部参与了配矿。
而矿点1在配矿后尚有富余量:70-31.121=38.879(万吨),但矿点1的矿石平均品位仅为37.16%,属贫矿。
作为该公司的负责人或决策层绝难接受这个事实:花费大量的人力、物力、财力后,在矿点1生产的贫矿中却有近39万吨被闲置,而且在大量积压的同时,会产生环境的破坏,也是难以容忍的。
原因何在?出路何在?
经过分析后可知:在矿石品位及出矿量都不可变更的情况下,只能把注意力集中在混合矿的品位要求T Fe上。
不难看出,降低的T Fe值。
可以使更多的低品位矿石参与配矿。
T Fe有可能降低吗?在因T Fe的降低而使更多贫矿石入选的同时,会产生什么样的影响?必须加以考虑。
就线性规划模型建立、求解等方面来说,降低T Fe及其相关影响已不属于运筹学的范围,它已涉及该公司的技术与管理。
但是,从事此项目研究的运筹学工作者却打破了这个界限,深入到现场操作人员、工程技术人员及管理人员中去,请教、学习、调查,然后按照T Fe的三个新值:44%、43%、42%,重新计算
(三)变动参数值及再计算
将参数T Fe的三个变动值0.44、0.43、0.42分别代入基本模型(LP),重新计算,相应的最优解分别记作X*(0.44)、X*(0.43)及X*(0.42)。
下表给出详细的数据比较:
表2 不同T Fe值的配矿数据
11 52.71 13.5 13.5 0 13.5 0 13.5 0 0 13.5
12 56.92 2.7 2.7 0 2.7 0 0 2.7 0 2.7
13 40.73 1.2 1.2 0 1.2 0 1.2 0 1.2 0
14 50.20 7.2 7.2 0 7.2 0 4.53 2.67 0.77 6.43 配用总量、富余总量(万
141.921 38.879 162.67 18.13 175.43 5.37 158.17 22.63 吨)
(四)综合评判及结果
对表2所列结果,请公司有关技术人员、管理人员(包括财务人员)进行综合评判,评判意见是:
1.T Fe取45%及44%的两个方案,均不能解决贫矿石大量积压的问题,且造成环境的破坏,故不能考虑。
2.T Fe取43%及42%的两个方案,可使贫矿石全部入选;配矿总量在150万吨以上;且富余的矿石皆为品位超过50%的富矿,可以用于生产高附加值的产品:精矿粉,大大提高经济效益;因而,这两个方案对资源利用应属合理。
3.经测算,按T Fe取42%的方案配矿,其混合矿石经选矿烧结后,混合铁精矿品位仅达51%,不能满足冶炼要求,即从技术上看缺乏可行性,故也不能采用。
4.T Fe=43%的方案,在工艺操作上只需作不大的改进即可正常生产,即技术上可行。
5.经会计师测算,按T Fe=43%的方案得出的配矿总量最多,高达175万吨,且可生产数量可观的精矿粉,两项合计,按当时的价格计算,比T Fe=45%的方案同比增加产值931.86万元。
结论: T Fe=43%时的方案为最佳方案。
四、一点思考
由基本模型(LP)的目标函数及决策准则来看,它具有单一性,即追求总量最大。
而从企业的要求来看,还需考虑资金周转、环境保护、资源合理利用以及企业生存等多方面的因素,因此,企业所指的“效益最佳”具有系统性。
这两者之间的差异,甚至冲突,应属运筹学工作者在应用研究中经常遇到的问题,也是需要合理解决的问题。
而解决这个问题的关键之一是:运筹学工作者在理念与工作方式只具有开放性,也就是说,不能只拘泥于运筹学书本及文献资料,而应进入实际,与相关人员、相关学科相结合、交叉、渗透、互补,从而达到技术可行、经济合理以及系统优化的目的。
经验表明:在运筹学实际应用的项目中,很少遇到运筹学“独步天下”的情况。
如在此案例中,它属于线性规划的一个典型应用领域,即使如此,运筹学在其中也不能包揽一切,它可以起着骨架及核心作用,但若无其他方面的配合,也不能达到圆满成功。