管件液压成形技术在汽车制造中的应用研究
汽车车身设计及制造工艺新技术研究

汽车车身设计及制造工艺新技术研究随着汽车行业的快速发展和市场需求的不断增长,汽车车身设计及制造工艺也呈现出创新性和高效性的新趋势。
本文将重点探讨目前汽车车身设计及制造工艺新技术的应用研究。
1、数字化设计技术数字化设计技术将计算机辅助设计与三维实体建模相结合,能够更快速、精准地设计出符合市场需求的汽车车身。
数字化设计技术提供了丰富的工具和算法,使得设计师可以更加直观地理解和操作车身结构的细节。
该技术还可以快速进行多种方案的比较和优化,使其完全符合人体工程学和气动学的要求,从而提升汽车的舒适性和安全性。
2、仿真技术利用有限元分析、多体动力学等仿真技术,可以快速预测汽车车身的受力情况及其对车身整体结构的影响。
该技术能够大大降低试制成本和时间,同时有效降低车身设计中的失误和风险。
不仅如此,利用仿真技术还能够更好的优化车身结构和改进存在的问题,进一步提高车身的舒适性和安全性。
3、材料及工艺技术新材料和新工艺是现代汽车制造的基础和生命力所在。
特别是一些新型工程塑料和复合材料的出现,使得汽车车身设计师可以更加灵活地选择材料,精细调整车身结构和功能,提高汽车的抗冲击性、耐久性、耐腐蚀性和轻量化程度。
1、激光焊接技术传统车身焊接主要采用氩弧焊和点焊等方式,但是这些方法难以处理各种形态或变形较大的车身结构。
激光焊接技术则是将高能激光束聚焦在焊接点上,加热金属至融点以上,使其达到熔化状态从而连接在一起。
该技术的优点是:焊接速度快、焊接过程干净、焊缝质量高、效率高、能够适应复杂形状等口头。
随着激光技术和材料科学等领域的不断进步,激光焊接技术在汽车车身制造中的应用越来越普遍。
2、液压成形技术液压成形技术是一个先进的汽车车身成形工艺,主要是通过液压冲头对汽车板材进行快速成形。
拥有高转换率,提高了体积密度,能够生产出高性能的铝合金车身结构零件。
液压成形技术的应用不仅降低成本,大大缩短生产周期,而且能够在保证车身品质的前提下,实现小换组件的高速制造。
新型液压成形技术的研究进展

新型液压成形技术的研究进展徐勇;张士宏;马彦;陈大勇【摘要】Hydroforming processes have become popular in recent years, due to the increasing demands for forming lightweight or complicated components in the nuclear power, aerospace and automotive industries. This technology is almost new as compared with rolling, forging or stamping, therefore there is a lack of knowledge available for the product or process designers. Comparing to traditional manufacturing via stamping and welding, sheet and tube hydroforming tenders various ad-vantages, such as reducing the cost of workpiece, tools and product weight, improving product’s stability and increase of the stiffness and strength of the formed parts, more uniform thickness distribution, fewer secondary operations, etc. State-of-the-art and recent developments of sheet hydroforming and tube hydroforming are discussed in details especially tube pulsating hydro-forming and high-energy-rate impact hydroforming which are considered as novel processes in hydroforming technology. In ad-dition, applications, technical issues, deformation mechanisms, process parameters are explored in details. The research results indicated that the novel hydroforming processes can make full advantage of the idea of “simultaneously controlling the shape and performance”, avoid the material instability and defects during the hydroforming process and improve the formability on tube and sheet specimens. Therefore, pulsating hydroforming and high-energy-rate impact hydroforming will be expectedto be widely used in the field of automobile and aerospace in the future. The research results showed that, pulsating hydroforming and high-energy-rate impact hydroforming is expected to be used widely in different industrial sectors in near future.%针对我国航空航天、汽车及核电等关键领域对精密零部件的迫切需求,以及目前液压成形技术应用中遇到的常见问题和缺陷,提出研发针对异形空心零件的脉动液压成形技术,和适用于复杂曲面薄壁板类零件的高能率冲击液压成形技术。
大吨位管件液压成形设备液压系统的设计和研究

为塑性成形加工研究 的前沿和热点, 并在欧洲 、 美国、 日本 、 国等国家的科研机构和大型企业 中得到 了广 韩
泛 的应用 0 。 J
液压缸活塞下移 , 顶出零件 , 成形过程结束。该管件液 压成形设备 的主要工艺流程如图 1 所示 。
在国内, 对管 件液 压 成 形 技 术 的 研 究虽 然 起 步 较
晚, 但发展迅速 , 现已在成形机理 、 数值模拟 、 实验研 究等方面取得 了丰硕成果 , 为该技术的进一步发展奠 定 了基础。目前 , 国内对液压成形设备的研究 涉及较 少, 所建的实验台或经 旧液压机改造的成形设备 , 主要 是适应实验的需要而不是面向工业化的生产要求 。基 于这种 状况 , 学校 、 究 所 和企 业 三 方 共 同努 力 下 , 在 研 改变传统的思路 , 采用独特的专 利技术完成 了面向工 业化 生产 的较 低成本 的 大 吨位管 件液压 成形 设备 的研 制。针对该设备成形大型复杂管件的工艺流程特点及 要求 , 文中对液压系统进行了优化设计 , 并取得了较好
设备用于加工仪表梁副车架桥轴等这类大型构件管坯内腔容积较大注入高压乳化液时会占用较长时间因此设计时采用了高速大流量充液系统先快速充满管坯内腔之后借助增压缸补充乳化液和通过轴向进给补料使管坯内腔液压按给定压力曲线上升保证管件顺利成形
维普资讯
20 0 6年 第 8期
Z NG a xa g , A L— i , N nxu HE Z i i F N i a XI We .i2 — n x
(. 1南京理工大学 , 江苏 南京 2 0 9 ; .山西省机电设计研究院 ,山西 太原 10 4 2 000 ) 3 0 9
日本内高压翻译

介绍为防止全球变暖,减少排放二氧化碳气体的汽车是必要的。
汽车重量对排放二氧化碳影响非常大。
管件液压成形(四氢呋喃)可以制造轻质空心零件复杂截面。
许多汽车公司都采用了液压成形技术是因为它是一种有效的减少汽车的重量的技术。
在本文里,描述了液压成形技术在日本的最近的研究动态和发展,主要的是成形工艺方面。
1管件液压成形的成形技术1.1热膨胀成形铝合金管铝合金配件用于减少汽车重量,但因为铝合金的成形性很难在室温下形成复杂形状零件。
以实际应用为例,在高温地区,伸长率和金属材料的可成形性有了明显改善,但还有许多问题需要解决,如发热时间长,温度控制,氧化,润滑等。
最近,福田,在线等[ 1]报道,从2004年开始他们成功地使铝的分帧与热管胀形复杂截面安装在客车上。
管状零件热膨胀形成的内压和轴向进给是左右成员的前副车架,和前和后方成员的后副车架。
部分远比传统的更复杂的形状是由膨胀成形。
实现了减少零件数量和焊接过程中的长度,以及提高刚性。
也降低了重量和成本. 热胀管零件的截面形状如图1所示[2]。
原管是新开发的铝镁管。
这种管预热迅速,直接由电荷流和加热时间缩短。
然后管在模具内受激烈的轴向进给内部的压力隆起形成。
利用新思路预成形设计的零件的形状,从管两端的轴向进给控制,成形一步分几个阶段开发的产品具有壁厚均匀,精度高特点。
在室温下管最大的扩张速度(变动率周长)是90%复杂的截面形状不可能形成。
模具成型压力为3Mpa,以空气作为压力介质,是在正常室温下需要的成型压力的1%。
而且还能把模具夹紧力增加十分之一,也可以减小成型设备的规模。
这个新开发的管解决了在高温下晶粒粗化和腔核大变形问题。
这个热管膨出可塑性技术工艺的开发获得了日本学会“2006年阿依达奖”。
全文翻译请在百度空间联系。
管件液压成形技术及其在汽车零部件制造中的运用
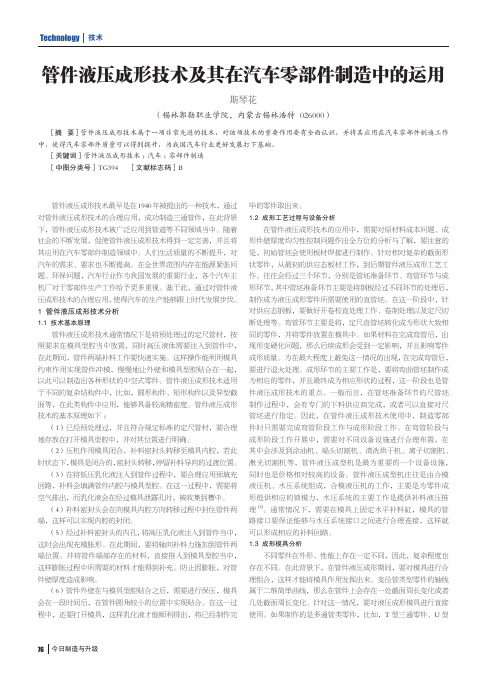
76 今日制造与升级Technology 技术管件液压成形技术最早是在1940年被提出的一种技术,通过对管件液压成形技术的合理应用,成功制造三通管件,在此背景下,管件液压成形技术被广泛应用到管道等不同领域当中。
随着社会的不断发展,促使管件液压成形技术得到一定完善,并且将其应用在汽车零部件制造领域中。
人们生活质量的不断提升,对汽车的需求、要求也不断提高。
在全世界范围内存在能源紧张问题、环保问题,汽车行业作为我国发展的重要行业,各个汽车主机厂对于零部件生产工作给予更多重视。
基于此,通过对管件液压成形技术的合理应用,使得汽车的生产能够跟上时代发展步伐。
1 管件液压成形技术分析1.1 技术基本原理管件液压成形技术通常情况下是将预处理过的定尺管材,按照要求在模具型腔当中放置,同时高压液体需要注入到管件中,在此期间,管件两端补料工作要快速实施。
这样操作能利用模具约束作用实现管件冲模,慢慢地让外壁和模具型腔贴合在一起,以此可以制造出各种形状的中空式零件。
管件液压成形技术适用于不同的复杂结构件中,比如,圆形构件、矩形构件以及异型截面等,在此类构件中应用,能够具备较高精密度。
管件液压成形技术的基本原理如下:(1)已经预处理过,并且符合规定标准的定尺管材,要合理地存放在打开模具型腔中,并对其位置进行明确。
(2)压机作用模具闭合,补料密封头转移至模具内腔,若此时状态下,模具是闭合的,密封头转移,停留补料导向的过渡位置。
(3)在将低压乳化液注入到管件过程中,要合理应用预填充回路,补料会填满管件内腔与模具型腔。
在这一过程中,需要将空气排出,而乳化液会在经过模具泄露孔时,被收集到槽中。
(4)补料密封头会在向模具内腔方向转移过程中封住管件两端,这样可以实现内腔的封闭。
(5)经过补料密封头的内孔,将高压乳化液注入到管件当中,这时会出现充模胀形。
在此期间,要将轴向补料力施加到管件两端位置。
并将管件端部存在的材料,直接推入到模具型腔当中,这样膨胀过程中所需要的材料才能得到补充。
液压胀形工艺

液压胀形工艺液压胀形工艺是一种利用液压力将金属件扩展成所需形状的加工方法。
它是一种常用的金属成形工艺,广泛应用于航空航天、汽车制造、船舶建造等领域。
液压胀形工艺具有成形快速、成本较低、加工精度高等优点,因此备受工业界的青睐。
液压胀形工艺的基本原理是利用液压力将金属件放入模具中,并施加高压液体,使金属件产生塑性变形,从而得到所需的形状。
在液压胀形过程中,液压油通过液压缸输出高压力,传递给液压缸内的活塞,使其向模具施加压力。
模具则对金属件进行约束,使其按照模具的形状进行胀形。
液压胀形工艺的关键是选择合适的液压油和控制系统。
液压油需要具有足够的粘度和压力传递能力,以确保胀形过程中能够提供足够的压力和流量。
控制系统需要能够精确控制液压缸的运动和施加的压力,以保证金属件的形状和尺寸符合要求。
液压胀形工艺可以实现对金属件的复杂形状加工,如圆形、椭圆形、异形等。
同时,液压胀形过程中不会对金属件造成变形或破坏,因此可以保证成品的质量和精度。
此外,液压胀形工艺还可以实现对薄壁金属件的加工,避免了传统加工方法中产生的残余应力和变形问题。
在实际应用中,液压胀形工艺可以用于制造各种金属管件、容器和壳体。
例如,航空航天领域中的燃气涡轮发动机和航空发动机中的涡轮叶片、汽车制造中的排气管和燃油管道,以及船舶建造中的船体结构等都可以使用液压胀形工艺进行加工。
液压胀形工艺虽然具有许多优点,但也存在一些限制。
首先,液压胀形工艺对模具的设计和制造要求较高,需要考虑金属材料的流动性和变形规律,以确保胀形过程中金属件的形状和尺寸的精度。
其次,液压胀形工艺在加工大型和复杂结构的金属件时,需要考虑液压缸的尺寸和力量的限制,以及加工过程中的变形和应力分布等问题。
液压胀形工艺是一种重要的金属成形工艺,具有广泛的应用前景。
随着科学技术的不断进步和工艺的不断改进,液压胀形工艺将在各个领域得到更加广泛的应用,为工业发展和产品制造提供更多的可能性。
管件液压成形技术及其在汽车零部件制造中的运用

管件液压成形技术及其在汽车零部件制造中的运用摘要:随着社会的发展,人们生活水平的不断提高,我国在汽车工业方面取得长足进步,目前已成为全球最大的汽车生产国和消费国之一。
但是我国汽车产业在技术研发、产品质量等方面仍然存在较大进步空间,特别是近年来频繁发生的交通事故引起社会对汽车安全性问题的广泛关注,使得人们对汽车产品的品质要求越来越高。
关键词:管件液压成形技术;汽车零部件制造;运用引言为了响应我国飞速发展的社会趋势,许多汽车零部件制造企业开始了大规模地生产制造以促进汽车产业的生产发展。
这对于汽车零部件制造企业是一个很大的机遇,也是一个很大的挑战,基于是能够让汽车零部件制造企业在这一时机能大量生产制造汽车零部件来促进自己企业的经济发展,挑战就是随着科学技术的不断进步,汽车零部件制造企业对于技术的要求有了更高的要求,对于汽车零部件的制造质量也有了更高的把控,需要汽车零部件制造企业能对自己的制造质量有严格的控制来满足现代化发展的需要。
1管件液压成形技术在汽车零部件中的应用分析1.1具体应用将管件液压成形技术应用在汽车零部件中之后,使得技术得到快速发展,并且已经成为韩国、日本、美国等先进国家,汽车零部件制造的主流技术。
在宝马、沃尔沃等主机厂推出的中高档车型当中,使用了管件液压成形技术,而国内的合资厂,比如,上海大众、一汽大众等,也能够对管件液压成形技术进行合理应用。
并逐渐推出自主品牌车型,比如,奔腾系列与荣威系列等。
从当前不同汽车车型应用中可以看出,管件液压成形技术通常情况下,会被应用在四大类中,分别是应用在底盘悬架系统零件制造中、应用在车身结构件制造中、应用在发动机零件制造中、应用在支撑框架类零件制造中。
在底盘悬架零件系统中应用,往往是横向稳定杆、转向管柱、控制臂等;在车身结构中的应用,是在A、B、C柱,车顶横梁、挡风玻璃支架等。
发动机系统零件中的应用,是在三元催化转化器、排气歧管等;支撑框架类零件中的应用,通常是在仪表板支架、座椅框架等。
液压成形
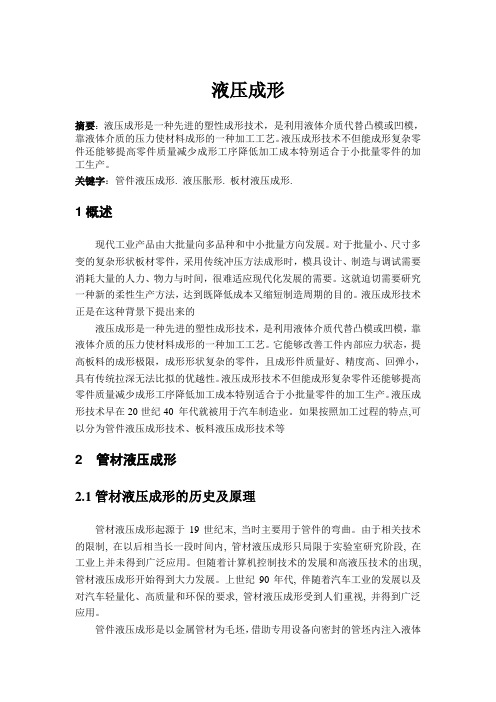
液压成形摘要:液压成形是一种先进的塑性成形技术,是利用液体介质代替凸模或凹模,靠液体介质的压力使材料成形的一种加工工艺。
液压成形技术不但能成形复杂零件还能够提高零件质量减少成形工序降低加工成本特别适合于小批量零件的加工生产。
关键字:管件液压成形. 液压胀形. 板材液压成形.1概述现代工业产品由大批量向多品种和中小批量方向发展。
对于批量小、尺寸多变的复杂形状板材零件,采用传统冲压方法成形时,模具设计、制造与调试需要消耗大量的人力、物力与时间,很难适应现代化发展的需要。
这就迫切需要研究一种新的柔性生产方法,达到既降低成本又缩短制造周期的目的。
液压成形技术正是在这种背景下提出来的液压成形是一种先进的塑性成形技术,是利用液体介质代替凸模或凹模,靠液体介质的压力使材料成形的一种加工工艺。
它能够改善工件内部应力状态,提高板料的成形极限,成形形状复杂的零件,且成形件质量好、精度高、回弹小,具有传统拉深无法比拟的优越性。
液压成形技术不但能成形复杂零件还能够提高零件质量减少成形工序降低加工成本特别适合于小批量零件的加工生产。
液压成形技术早在20世纪40 年代就被用于汽车制造业。
如果按照加工过程的特点,可以分为管件液压成形技术、板料液压成形技术等2 管材液压成形2.1管材液压成形的历史及原理管材液压成形起源于19世纪末, 当时主要用于管件的弯曲。
由于相关技术的限制, 在以后相当长一段时间内, 管材液压成形只局限于实验室研究阶段, 在工业上并未得到广泛应用。
但随着计算机控制技术的发展和高液压技术的出现,管材液压成形开始得到大力发展。
上世纪90年代, 伴随着汽车工业的发展以及对汽车轻量化、高质量和环保的要求, 管材液压成形受到人们重视, 并得到广泛应用。
管件液压成形是以金属管材为毛坯,借助专用设备向密封的管坯内注入液体介质,使其产生高压,同时还在管坯的两端施加轴向推力,进行补料,在两种外力的作用下,管坯材料塑性变形,并最终与模具型腔内壁贴合,得到形状与精度均符合技术要求的中空零件液压成形原理如图1 所示图1 管件液压成形原理示意图当零件轴线不是直线模腔分模面处截面小于管坯截面时,需进行弯管冲压等预工艺,以便管坯能顺利置入模腔中,如有必要,在液压成形之前还需进行退火处理2.2管材液压成形优点:与传统的冲压焊接工艺相比,管件液压成形工艺具有以下优点:(1 ) 减轻零件质量,节约材料; (2 ) 提高零件的强度和刚度,特别是疲劳强度; ( 3) 减少零件数量节约模具成本;(4) 零件整体成形,可减少后续机械加工和组装焊接量,简化生产流程,提高生产效率; (5) 提高加工精度,减少装配误差积累,可提高产品质量; (6)降低生产成本; (7) 结构形状设计更趋灵活优化。
- 1、下载文档前请自行甄别文档内容的完整性,平台不提供额外的编辑、内容补充、找答案等附加服务。
- 2、"仅部分预览"的文档,不可在线预览部分如存在完整性等问题,可反馈申请退款(可完整预览的文档不适用该条件!)。
- 3、如文档侵犯您的权益,请联系客服反馈,我们会尽快为您处理(人工客服工作时间:9:00-18:30)。
收稿日期:2004-04-05文章编号:100622343(2004)052065203管件液压成形技术在汽车制造中的应用研究杨 兵, 张卫刚, 林忠钦, 李淑慧(上海交通大学 机械与动力工程学院,上海 200030,E 2mail :yangbing @ ) 摘 要:阐述了管件液压成形的基本概念及其优点,介绍了在汽车制造领域中的应用,综述了管件液压成形技术的研究成果,重点介绍材料、塑性失稳、加载路径优化、预成形等问题;讨论了应用研究中进一步的发展方向。
关键词:管件;液压成形;加载路径中图分类号:TG 394 文献标识码:A 汽车轻量化是目前汽车设计制造的发展方向。
实现汽车轻量化一个重要方面是改进车身结构,采用轻型结构来达到减轻自重的目的。
一个有效途径是对满足力学要求情况下的构件采用空心结构,既可减轻重量节约材料又可充分利用材料的强度和刚度。
另一方面,传统车身零件制造常采用分离成形法,即利用不同压力机分别冲压成形单个零件,然后将各零件焊接组装成目标部件。
这种方法虽然选材、制造灵活,但由于零件数目多,存在装配精度低,焊接量大,车身刚度差,冲压、装配成本高等缺点。
因而,一种既能减轻车身自重,又能提高制造质量、降低生产成本的先进制造技术———管件液压成形技术(又称内高压成形技术)发展起来了。
1 成形原理 管件液压成形技术通常是用管坯作为原材,通过对管腔内施加液体压力、轴向施加负荷作用,使其在给定模具型腔内发生塑性变形,管壁与模具内表面贴合,从而得到所需形状零件的技术。
▲图1 管件液压成形原理图1.管坯 2.上模 3.液体介质4.冲头 5.下模 6.成形件 管件液压成形过程如图1所示。
先将管坯放入下模腔内;然后管件两端的柱塞冲头在液压缸的作用下压入,将管件腔密封,液体介质不断通过冲头内的液体通道流入管件腔;此时上模向下移动,与下模共同形成封闭的模腔,最后高压泵与阀门控制液体压力不断增大,冲头向内推动管件,管壁变形并逐渐贴模,最终得到所需形状的零件。
当零件轴线不是直线、零件局部最小截面小于管坯截面时,需进行预弯曲、预冲压等预成形工艺,以便管坯能放入模具中,并使管坯接近零件形状,再充液胀形成形。
2 优点与应用 在汽车制造业中,与传统的冲压焊接工艺相比,管件液压成形有着巨大的优势[1]:①减轻零件重量,不再需要多个零件焊接成部件,因而也改善了结构的紧凑性。
以副车架为例,管件液压成形件比冲压焊接件减轻20%~40%的重量。
②提高零件的强度、刚度和耐撞性。
③减少零件数量、节约模具成本。
④减少后续焊接装配过程,简化生产流程,提高生产效率。
以散热器支架为例:焊点数由174个减少到20个,装配工序由13道减少到6道。
⑤减少装配误差积累,提高产品质量。
由于上述的诸多优点,德国在20世纪70年代末就开始了管件液压成形技术的基础研究工作,90年代率先在汽车工业中实现了批量化生产应用。
之后,管件液压成形技术在欧洲其它国家、北美、日本、韩国等国迅速得到推广应用。
美国的三大汽车公司和十大钢铁公司还专门联合成立了“汽车/钢铁液压成形工业资源组织(Auto/Steel Partnership HydroformingIndustry Res ource G rou p )”。
在由世界18个国家35家钢铁企业联合实施的超轻钢车身计划(ULSAB )中,管件液压成形技术被作为完成该计划的重要技术手段之一。
国内哈尔滨工业大学等单位最近几年也开始了这方面的研究工作。
▲图2 液压成形汽车零件 奔驰汽车公司在1993年就建立了管件液压成形车间,目前通用、福特、欧宝等汽车公司都建立了液压成形生产基地。
采用液压成形技术制造汽车零部件典型的应用实例如:BMW500系列后桥,Mercedes Benz 排气岐管、Buick Park Avenue车顶纵梁、发动机支架等。
宝马、奥迪、奔驰、大众、克莱斯勒、沃尔沃等车型也都已采用了管件液压成形的零件。
采用管件液压成形技术可以制造各种沿轴线变化的圆形、矩形或异型截面的管状零件,零件轴线可以是直或弯曲的。
目前国外已第20卷第5期2004年10月机械设计与研究Machine Design and Research Vol.20No.5Oct.,2004经成功制造的液压成形汽车零件主要有排气系统异型管件、车身框架结构件、驱动轴以及安全构件等。
如排气岐管、排气管、车顶横梁、仪表盘支架、散热器支架、副车架、车顶纵梁、车身纵梁、座椅架、发动机支架、车门柱、后延臂、车桥、转向柱以及保险杠等。
图2是典型的管件液压成形汽车零件。
3 关键技术问题 管件液压成形技术涉及管坯材料、工艺参数控制、模具条件、设备系统等。
各国研究者通过理论或试验研究,探索这些因素的影响,以期获得无成形缺陷,成形零件与模具型腔内表面贴合程度好,壁厚分布均匀的零件。
3.1 材料性能与成形性管件液压成形性与材料密切相关,通常用于冲压成形的材料均可以用于管件液压成形。
适用于汽车的液压成形管坯材料有低碳钢、不锈钢、铝合金、低碳高强度钢等。
准确的管材力学性能参数是管材塑性成形工艺规划的基础。
管材的力学性能参数通常沿用的是同种材料平板试件的单向拉伸试验数据结果。
由于平板试件不能反映出滚弯、焊接等制管工序对板材力学性能的影响和成形性能的消耗,也无法精确反映管材在实际塑性成形中所处的复杂应力状态,从而影响数值模拟结果和工艺规划。
田仲可[2]基于各向同性硬化假设,提出一种轴压胀形、单向压缩试验与数据拟合技术相结合的估计管材硬化模型参数的方法。
美国的T.S okolowski[3]设计的液压胀形试验,更能反映管件液压成形过程的塑性变形行为。
该试验中变形区管件承受双向载荷,在试验中连续记录内压力、胀形高度、管壁厚度,通过试验数据和理论分析来确定给定管材的应力应变关系。
通过在不同压力等级下对材料进行试验,并利用所确定的材料参数进行数值模拟,模拟成形高度与试验非常接近。
用该试验方法也可以求得管材的FLD曲线。
Fuchizawa[4]也采用类似试验来确定管材的应力应变关系,结果都表明这种受双向载荷的液压胀形试验可以用于液压成形管材性能参数的确定。
通常管坯几何直径越小、壁厚越厚,管件液压成形所需内压力也越高。
管材各向异性系数r、硬化指数n值都影响管件的液压成形性能。
B.Carleer[5]通过管件自由胀形试验和理论分析认为材料r值、n值越大,摩擦系数越低,则管件自由胀形高度越高,轴向自由缩进量越大。
K en2ichi Manabe[6]对内压力和轴向压力同时作用成形矩形截面零件进行研究,表明r值变化明显影响成形高度、轴向缩进量和壁厚分布,是管件液压成形中重要的材料参数。
T.Y oshida[7]的研究认为材料轴向r值影响成形极限,值越大成形高度越高;周向r值影响成形所需最大内压力;随着n值增大,成形相同零件所需的内压力越低,零件壁厚分布也越均匀。
G.T.K ridli[8]考察n值对成形零件壁厚分布的影响,发现成形零件壁厚分布是材料n值的函数,n值越小,零件壁厚分布越不均匀;n值越大能够填充的模具圆角半径越小。
这些研究结果表明管材的r 值、n值越大,管件液压成形的成形性越好。
3.2 成形缺陷与加载路径管件液压成形过程中由于材料、模具、工艺条件不合理等因素会导致成形过程中出现起皱、破裂、屈曲、折叠等成形缺陷,如图3所示。
▲图3 典型成形缺陷 起皱(图3a)主要是因为内压力不足、轴向进给量过大而引起的。
起皱的数量、高度与加载路径、管坯几何尺寸等有关。
郎利辉[9]将皱纹分为有益和有害两种,有害的起皱将形成死皱;并提出成形初期形成合理几何形状的皱纹是必要的,而后采用提高内压进行整形消除皱纹的方法有利于零件的成形。
破裂(图3b)是因内压力过高、轴向进给量不足,使管壁迅速变薄产生局部缩颈而引起的。
若成形前后管件直径分别为d0、d1,通常平均变形量d1/d0>1.4时,易发生破裂[10]。
屈图(图3c)是因为在成形过程初始阶段轴向载荷高、内压力低,模具中的管坯自由段l f长、导向段短而引起管坯的整体屈服。
l f允许长度与管径d0、壁厚t0比值(d0/t0)有关:当d0/t0<20,l f<2d0时,不易发生屈曲;当20≤d0/t0≤45时,要求l f<2d0;当d0/t0>45时,易发生屈曲[10]。
折叠(图3d)是由于轴向压力过大,管壁被压入已发生胀形的管内而形成。
折叠的产生与模具几何尺寸、管坯形状有很大关系。
通常折叠的形式和管坯的壁厚有关。
壁厚与管径比t0/d0<0.05,d1/d0>1.8时,容易产生折叠缺陷[10]。
对于确定的零件材料和零件形状,管坯材料和模具结构即被确定,各种缺陷的产生通常是由于加载路径不合理所致。
所谓加载路径是成形过程中所施加的内压力、轴向压力(或轴向进给量)的大小及彼此间的匹配关系。
确定合理加载路径、避免产生成形缺陷,获得壁厚分布均匀的零件是管件液压成形中研究的一个重要问题。
▲图4 成形极限与工作区间 加载路径的确定与管坯材料、几何尺寸、模具尺寸等相关。
对形状规则的简单零件,可根据材料参数、零件形状和摩擦条件,计算出密封所需的轴向压力,成形最大内压力,最小、最大轴向进给量,管坯塑性失稳的临界载荷、屈服载荷等。
从而获得图4所示的加载区间图,减少工艺设计中凭经验设计时产生的试错次数[10~11]。
W. Rimkus[12]根据管件液压成形特有的充液、成形、整形阶段,利用内压力、轴向力、摩擦力所做功之间的联系,几何尺寸关系,分别求得各阶段开始结束时的内压力和轴向载荷,从而获得分段线性的加载路径。
数值模拟与优化策略相结合来确定加载路径的方法是近年来的研究热点。
根据优化方法的不同有自适应法、响应面法和灵敏度分析法等。
T.Altan[13]采用自适应法确定加载路66机械设计与研究 第20卷径,其原理是在有限元计算的每个增量步检查管件是否起皱,若没有就增加一个轴向进给增量,否则就增加一个内压力增量,从而在一次仿真过程中确定认为最优的加载路径。
Jae2 Bong Y ang[14]采用基于响应面和灵敏度分析法的优化方法来确定最优加载路径,以成形零件壁厚变化波动最小为优化目标,成形零件与模具内表面贴合程度为约束条件,通过多次模拟确定加载路径。
通过对副车架液压成形的加载路径进行优化设计,结果表明在优化加载路径下成形的副车架零件关键截面壁厚最大减薄量由原来的56%下降到30%,壁厚分布均匀度更好。
通过有限元数值模拟、试验方法和优化策略相结合,在虚拟环境下确定最优的管件液压成形加载路径,并通过少量的实验来验证是新产品开发中的重要手段。
3.3 预成形模具设计、加载路径等工艺设计都应考虑预弯曲、预冲压等预成形过程。