精益管理讲义版 - 第二部分
合集下载
精益管理讲义版
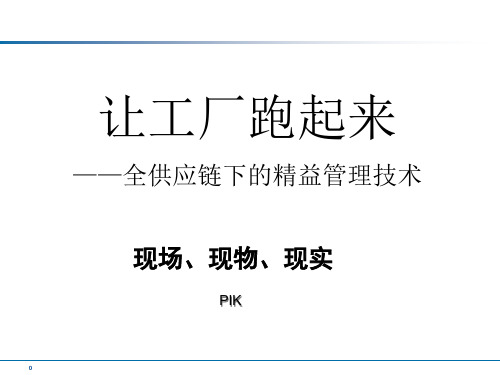
29
14、各部门、工序之间不协调 15、设备故障率高 16、质量过程控制不完善 17、车间管理没有实现有效的数据化管理 18、现场管理乱 19、一线主管的管理技能弱 20、信息反馈渠道缺乏,只有中高层决策, 没有有效的监督、反馈、改善、提高过程 21、员工管理过程激励太少 22、员工培训体系不完善,没有发展规划 23、采购周期急 24、管理者的主管意识大,流程难以执行
21
案例:江苏常州豪乐机械的改善方法
5人 6500
毛 坯
2人 4100
铣基 准平 面
4人 5400
镗 三 孔
3人 5200
铣其 它平 面
8人 6400
2人 4人 2人 4800 4300 6800
钻
攻 铣去
孔
丝 槽毛
平均每天 3907
落
车外
料
圆
滚 磨外
丝
圆
压 焊 喷 检验 配 接 涂 包装
入 库
5人 6人 4人 18人 4800 6300 7300 18000
19、一线主管的管理技能弱 22、员工培训体系不完善
10、计划管理体系无
30
5、岗位职责不明确
6、绩效考核不完善
整体观
整体观—速度: 控制利润的关键
如何衡量公司推动改善的成果可以充分反应在公司整体的绩效上? 例如: 1)投资200万改善生产设备,得到更好的生产效率,是否也等同于帮公司多赚200
万? 2)投资300万提升生产效率,节省5个人力,是否也等同于帮公司节省300万的营运
Lean Production TP
5S
JTI TPM
TQM
2
我们要达成的共识:企业的目标是什么?
赚钱
14、各部门、工序之间不协调 15、设备故障率高 16、质量过程控制不完善 17、车间管理没有实现有效的数据化管理 18、现场管理乱 19、一线主管的管理技能弱 20、信息反馈渠道缺乏,只有中高层决策, 没有有效的监督、反馈、改善、提高过程 21、员工管理过程激励太少 22、员工培训体系不完善,没有发展规划 23、采购周期急 24、管理者的主管意识大,流程难以执行
21
案例:江苏常州豪乐机械的改善方法
5人 6500
毛 坯
2人 4100
铣基 准平 面
4人 5400
镗 三 孔
3人 5200
铣其 它平 面
8人 6400
2人 4人 2人 4800 4300 6800
钻
攻 铣去
孔
丝 槽毛
平均每天 3907
落
车外
料
圆
滚 磨外
丝
圆
压 焊 喷 检验 配 接 涂 包装
入 库
5人 6人 4人 18人 4800 6300 7300 18000
19、一线主管的管理技能弱 22、员工培训体系不完善
10、计划管理体系无
30
5、岗位职责不明确
6、绩效考核不完善
整体观
整体观—速度: 控制利润的关键
如何衡量公司推动改善的成果可以充分反应在公司整体的绩效上? 例如: 1)投资200万改善生产设备,得到更好的生产效率,是否也等同于帮公司多赚200
万? 2)投资300万提升生产效率,节省5个人力,是否也等同于帮公司节省300万的营运
Lean Production TP
5S
JTI TPM
TQM
2
我们要达成的共识:企业的目标是什么?
赚钱
精益管理讲义版 - 第二部分

第二部分 精益管理技术介绍
Lean Production TP SS
JTI
TPM TQM
0
本节课程目的
• 精益的核心思想:关注流动性,持续改善、改善永无止境 • 精益的技术体系:应用工具介绍 • 精益的管理原则:精益生产的十四项原则
1
生产方式发展的历史
精益生产
福特流水 线 泰勒管理思 想
敏捷生产
供应商
500t卷材
蓝天车业
18400件/月 12400“左置“ 6400“右置“ 周转箱=20件 两班工作
每周传真
每周计划
周二 +周四
每日发运 计划
每日 一次
冲压 5d 卷材 200t 加工周期=1s 换模时间=1h 使用率=85% 准备量二周 1s 4600(左) 2400(右)
点焊Ⅰ 1
换模时间=10Min
价
值
流
过
下料
程
过
焊接
程
过
程
总装单元
原材料
成品
16
价值流的定义
供应链状态下的价值流包含的是特定产品从进公司到发货至客户的所有要素 括增值的和非增值的)。 (包
需求
设计 采购
原材料
生产制造
入库
发货
客户
也可以用价值流的方法来绘制全产业链的过程。
17
识别价值流
价值流是使一个特定产品通过任何一项商务活动的三项关 键性管理任务时所必须的一组特定活动。此三项关键性管理 任务为: 1、从接受订单到执行生产计划发货的信息流; 2、从原材料到转化为产成品的物流; 3、从概念到正式发布的产品设计流程。
加工周期=39s
有效时间27600s
Lean Production TP SS
JTI
TPM TQM
0
本节课程目的
• 精益的核心思想:关注流动性,持续改善、改善永无止境 • 精益的技术体系:应用工具介绍 • 精益的管理原则:精益生产的十四项原则
1
生产方式发展的历史
精益生产
福特流水 线 泰勒管理思 想
敏捷生产
供应商
500t卷材
蓝天车业
18400件/月 12400“左置“ 6400“右置“ 周转箱=20件 两班工作
每周传真
每周计划
周二 +周四
每日发运 计划
每日 一次
冲压 5d 卷材 200t 加工周期=1s 换模时间=1h 使用率=85% 准备量二周 1s 4600(左) 2400(右)
点焊Ⅰ 1
换模时间=10Min
价
值
流
过
下料
程
过
焊接
程
过
程
总装单元
原材料
成品
16
价值流的定义
供应链状态下的价值流包含的是特定产品从进公司到发货至客户的所有要素 括增值的和非增值的)。 (包
需求
设计 采购
原材料
生产制造
入库
发货
客户
也可以用价值流的方法来绘制全产业链的过程。
17
识别价值流
价值流是使一个特定产品通过任何一项商务活动的三项关 键性管理任务时所必须的一组特定活动。此三项关键性管理 任务为: 1、从接受订单到执行生产计划发货的信息流; 2、从原材料到转化为产成品的物流; 3、从概念到正式发布的产品设计流程。
加工周期=39s
有效时间27600s
精益生产全讲义
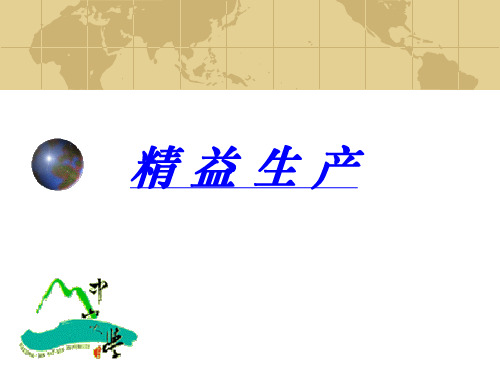
要求 库存水平 制造成本 产品质量 所适应的 市场时代
手工生产方式 完全按顾客要求 通用、灵活、便宜
粗略、丰富
懂设计制造 有较高操作技能
高 高 低 极少量需求
大批量生产方式
精益生产方式
标准化,品种单一 品种多样化、系列化
专用、高效、昂贵 柔性高、效率高
细致、简单、重复 不需要专业技能
较粗略、 多技能、丰富
待
8
管理的浪费
管理本身成为一种专 职的工作发生的浪费
事后管理的浪费
41
1、不良、修理的浪费
材料的损失; 设备、人员、工时的损失; 额外的修复、选别、追加检查; 额外的检查预防人员; 降价处理; 出货延误取消定单; 信誉下降; ……
42
2、加工的浪费
△
●
○
自动 插件
●
焊接 组装1 组装2 检测
○
◎
◎
●
包装 ●
徐小凤 ●
○
◎
○
◎
○
△
多技能员工 金 庸 ○
△
●
△
◎
◎
韦小宝 ◎
○
○
●
F4
○
◎
●
○
◎
拉登 ◎
●
△
●
○
萨达姆 △
●
◎
●
○
◎
吕不韦 ●
○
△
○
●
备注:△—计划学习,○—基本掌握,◎—完全掌握,●精通
27
案例
QC小组活动
Q C C uality ontrol ycle
多技能
高
低 高 物资缺乏、供不应 求
低 更低 更高 买方市场
手工生产方式 完全按顾客要求 通用、灵活、便宜
粗略、丰富
懂设计制造 有较高操作技能
高 高 低 极少量需求
大批量生产方式
精益生产方式
标准化,品种单一 品种多样化、系列化
专用、高效、昂贵 柔性高、效率高
细致、简单、重复 不需要专业技能
较粗略、 多技能、丰富
待
8
管理的浪费
管理本身成为一种专 职的工作发生的浪费
事后管理的浪费
41
1、不良、修理的浪费
材料的损失; 设备、人员、工时的损失; 额外的修复、选别、追加检查; 额外的检查预防人员; 降价处理; 出货延误取消定单; 信誉下降; ……
42
2、加工的浪费
△
●
○
自动 插件
●
焊接 组装1 组装2 检测
○
◎
◎
●
包装 ●
徐小凤 ●
○
◎
○
◎
○
△
多技能员工 金 庸 ○
△
●
△
◎
◎
韦小宝 ◎
○
○
●
F4
○
◎
●
○
◎
拉登 ◎
●
△
●
○
萨达姆 △
●
◎
●
○
◎
吕不韦 ●
○
△
○
●
备注:△—计划学习,○—基本掌握,◎—完全掌握,●精通
27
案例
QC小组活动
Q C C uality ontrol ycle
多技能
高
低 高 物资缺乏、供不应 求
低 更低 更高 买方市场
精益管理培训讲义

• 简化(Simple)——经过取消、合并、重排后 的必要工作,就可考虑能否采用最简单的方法 及设备,以节省人力、时间及费用。
2020/2/28
35
改善前的价值流程图
Product Current State Value Chain Map
Customer Location
Type
Film
- White Bluff, TN
2020/2/28
6
1、杜绝浪费
精益生产要求杜绝的8大浪费: 生产过剩、在现场等候的时间、不必要的运输、
过度处理、存货过剩、不必要的移动和搬运、瑕疵、 未使用的员工创造力。
2020/2/28
7
2、“JIT”及“零库存”
(1) “JIT” —— JUST IN TIME(准时化生产) 指的是适时、适量地生产适当的产品。
B、只有识别出顾客以后,才能定义出流程中创造价值的工 作和活动;
C、流程服务的顾客可能不只一个。
举例说明:
2020/2/28
18
(2)分析现状
A、绘制价值流程图 • 改善参与者须亲历整个流程; • 详细记录流程各步骤的内容、所花费的时间、移
动的距离等; • 将流程用价值流程图表现出来。
2020/2/28
(3)订立改善愿景
A、订立改善愿景时要注意纳入精益的概念,如: “一个流”、“视觉管理”、“工作均衡化”、 “减少浪费”等;
B、要画出改善后的价值流程图; C、要对改善后流程所花费的时间、前置期、成本
等进行方面进行估算。
2020/2/28
22
(4)实施流程改造
具体实施方法有: A、创造“一个流”,重新安排工作区域,尽可能地使信息
2020/2/28
2020/2/28
35
改善前的价值流程图
Product Current State Value Chain Map
Customer Location
Type
Film
- White Bluff, TN
2020/2/28
6
1、杜绝浪费
精益生产要求杜绝的8大浪费: 生产过剩、在现场等候的时间、不必要的运输、
过度处理、存货过剩、不必要的移动和搬运、瑕疵、 未使用的员工创造力。
2020/2/28
7
2、“JIT”及“零库存”
(1) “JIT” —— JUST IN TIME(准时化生产) 指的是适时、适量地生产适当的产品。
B、只有识别出顾客以后,才能定义出流程中创造价值的工 作和活动;
C、流程服务的顾客可能不只一个。
举例说明:
2020/2/28
18
(2)分析现状
A、绘制价值流程图 • 改善参与者须亲历整个流程; • 详细记录流程各步骤的内容、所花费的时间、移
动的距离等; • 将流程用价值流程图表现出来。
2020/2/28
(3)订立改善愿景
A、订立改善愿景时要注意纳入精益的概念,如: “一个流”、“视觉管理”、“工作均衡化”、 “减少浪费”等;
B、要画出改善后的价值流程图; C、要对改善后流程所花费的时间、前置期、成本
等进行方面进行估算。
2020/2/28
22
(4)实施流程改造
具体实施方法有: A、创造“一个流”,重新安排工作区域,尽可能地使信息
2020/2/28
精益生产2讲课文档

C15
066
077
FA-BC15/16
01
022
033
044
FA – L02
10
B16
第三十三页,共56页。
09
088
055
066
077
C16
33 33
4、现场5S
³ * 通过对现场人物分析,起码我们要做到:
精益生产PPT
第一页,共56页。
什么是精益生产? 为什么要精益生产?
和我们有什么关系?
如何做到?
如何保持?
2
第二页,共56页。
一、历史
两个故事
1. “搬运生铁块试验 ” 2. 丰田汽车(Toyota)
/日本
3
第三页,共56页。
1.“搬运生铁块试验”
1898年, 泰 勒 在伯利恒钢铁公司进行了著名的“搬运生铁 块试验”,搬运生铁块试验,是在这家公司的五座高炉的 产品搬运班组大约75名工人中进行的。这一 研 究 改进了 操作方法,训练了工人。这一研究的结果是非常杰出的,
1. 动作太大
2. 单手空闲 3. 转身动作过大
4. 操作动作不流畅 5. 重复/不必要的动作 6. 不必要的弯腰动作
动作经济原则
21 21
第二十一页,共56页。
7. 不平衡浪费
1. 人员工作分配不合理 2. 计划对人员需求不均匀 3. 设备产能搭配不合理
4. 设备故障
5. 物料短缺
6. 信息流与物流不同步
浪费
关于浪费
浪费和我们密切相关
浪费是指那些导致成本增加的因素
虽然增加价值,但耗用资源过高
• 一种浪费通常能够导致另外一种浪费
发现浪费和认识浪费的能力很重要
精益管理培训课件ppt精品模板分享(带动画)
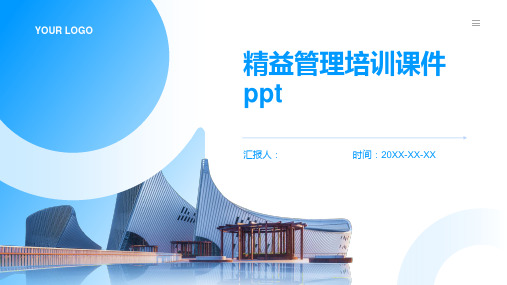
YOUR LOGO
精益管理培训课件 ppt
汇报人:
时间:20XX-XX-XX
目录
01
02
03
04
05
06
添加标题
精益管理 概述
精益管理 工具与方 法
精益管理 与企业实 践
精益管理 案例分析
精益管理 未来趋势 与挑战
PART 1
单击添加章节标题
PART 2
精益管理概述
什么是精益管理
定义:精益管理是一种以客户需求为导向,以消除浪费、提高效率为目标的管理理念。 起源:起源于日本丰田汽车公司,旨在通过消除生产过程中的浪费现象,提高生产效率 和产品质量。
明确企业愿景与使命
制定具体的战略目标和计划
建立精益管理团队,明确职责 分工
制定实施计划,明确时间节点立跨部门精益 管理团队
明确职责和目标
制定实施计划和 时间表
定期评估进展和 成果
培训与知识转移
定义培训目 标
实施培训计 划
制定培训计 划
评估培训效 果
持续改进与优化
流程优化
识别流程瓶颈: 分析流程中存在 的问题和瓶颈
优化流程:调整 流程,提高效率 和效益
制定流程规范: 制定流程规范, 明确职责和流程 标准
持续改进:不断 优化流程,提高 企业整体运营效 率
5S管理
定义:整理、整顿、清洁、清洁检查、素养 目的:提高工作效率,减少浪费 实施步骤:制定5S计划,实施5S活动,检查5S效果 应用范围:生产现场、办公室等
核心原则:包括以客户为中心、关注价值流、持续改进、以人为本、透明度和诚实。
应用领域:精益管理广泛应用于制造业、服务业、医疗保健业等多个领域,是企业实现 转型升级、提高竞争力的重要途径。
精益管理培训课件 ppt
汇报人:
时间:20XX-XX-XX
目录
01
02
03
04
05
06
添加标题
精益管理 概述
精益管理 工具与方 法
精益管理 与企业实 践
精益管理 案例分析
精益管理 未来趋势 与挑战
PART 1
单击添加章节标题
PART 2
精益管理概述
什么是精益管理
定义:精益管理是一种以客户需求为导向,以消除浪费、提高效率为目标的管理理念。 起源:起源于日本丰田汽车公司,旨在通过消除生产过程中的浪费现象,提高生产效率 和产品质量。
明确企业愿景与使命
制定具体的战略目标和计划
建立精益管理团队,明确职责 分工
制定实施计划,明确时间节点立跨部门精益 管理团队
明确职责和目标
制定实施计划和 时间表
定期评估进展和 成果
培训与知识转移
定义培训目 标
实施培训计 划
制定培训计 划
评估培训效 果
持续改进与优化
流程优化
识别流程瓶颈: 分析流程中存在 的问题和瓶颈
优化流程:调整 流程,提高效率 和效益
制定流程规范: 制定流程规范, 明确职责和流程 标准
持续改进:不断 优化流程,提高 企业整体运营效 率
5S管理
定义:整理、整顿、清洁、清洁检查、素养 目的:提高工作效率,减少浪费 实施步骤:制定5S计划,实施5S活动,检查5S效果 应用范围:生产现场、办公室等
核心原则:包括以客户为中心、关注价值流、持续改进、以人为本、透明度和诚实。
应用领域:精益管理广泛应用于制造业、服务业、医疗保健业等多个领域,是企业实现 转型升级、提高竞争力的重要途径。
精益管理培训精品课件ppt

企业文化传承发展路径规划
制定企业文化传承计划
加强企业文化的培训和教育
明确企业文化的传承目标、传承内容、传 承方式和传承时间等;
通过定期开展企业文化培训和教育活动, 提高员工对企业文化的认知和认同;
建立完善的企业文化传承机制
加强企业文化的宣传和推广
通过制定规章制度和行为规范,明确企业 文化的具体要求;
精益生产体系构建与实施
02
精益生产体系构成要素
价值流分析
识别产品或服务从原材料到最终 客户过程中的所有活动,并确定 哪些活动是增值的,哪些是不增
值的。
流程改进
通过消除浪费、简化流程、提高效 率等方式,不断优化生产流程。
持续改进
建立持续改进的企业文化,鼓励员 工提出改进意见,不断优化生产过 程。
精益生产流程优化与改进方法
01
02
03
5S管理
整理、整顿、清洁、清洁 检查、素养,提高现场管 理水平,减少浪费。
目视化管理
通过图表、看板等方式, 将生产过程中的信息直观 地展示出来,便于员工了 解和掌握。
快速换模
通过改进模具更换流程, 减少换模时间,提高生产 效率。
精益生产在生产现场的应用实践
现场布局优化
通过合理的现场布局,减 少物料搬运距离,提高工 作效率。
企业文化建设策略与方法探讨
企业文化建设策略
制定企业文化战略,明确企业文化的核心价值观和使命愿景;建立完善的企业文化体系,包括制度文 化、行为文化、物质文化和精神文化等方面;加强企业文化的宣传和推广,提高员工对企业文化的认 知和认同。
企业文化建设方法
通过培训和教育,提高员工对企业文化的认识和理解;通过制定规章制度和行为规范,明确企业文化 的具体要求;通过开展各种文化活动,增强企业文化的凝聚力和向心力;通过加强企业形象的塑造和 宣传,提升企业文化的知名度和美誉度。
精益管理培训课件ppt

拉动是指根据客户需求进行生 产,目标是消除过量生产和浪 费。
通过实现流动与拉动的原则, 企业可以更好地满足客户需求 ,提高生产效率和减少浪费。
追求完美
追求完美是精益管理的一个重要 原则,它鼓励企业不断改进和优
化其流程和产品。
追求完美的目标是消除浪费,提 高效率和质量,同时满足客户需
求。
企业应该不断寻求改进的机会, 并采取行动来实现持续改进。
企业可以通过采用环保材料、优化生产工艺、提高能源利 用效率等方式,实现环境可持续性融入精益管理,提高企 业的社会责任感和品牌形象。
人工智能在精益管理中的应用
人工智能技术在精益管理中具有广阔的应用前 景,可以提高生产过程的自动化和智能化水平 ,降低人工成本和提高生产效率。
人工智能技术可以通过机器学习、深度学习等 技术手段,实现对生产数据的自动分析和预测 ,帮助企业快速发现问题和优化生产过程。
意见和建议。
企业应该建立一种文化,鼓励员 工积极参与并承担责任,同时为
他们提供必要的培训和支持。
通过以员工为中心的管理方式, 企业可以提高员工的满意度和忠 诚度,同时促进企业的持续改进
和发展。
03
精益管理工具与技术
5S管理
5S管理是精益管理的基础,包括整理 (Sort)、整顿(Straighten)、清扫 (Sweep)、清洁(Sanitize)和素养
TPM强调设备的全面维护和保养,包括日常检查、定期维护、故障修复等方面。
TPM的实施可以提高设备的运行效率、减少故障停机时间、降低维修成本,从而提高企业 的生产效益和市场竞争力。
持续改进(Kaizen)
01
持续改进是一种追求卓越的管理理念,通过不断改进生产、服 务和管理的过程,提高企业的竞争力和盈利能力。
- 1、下载文档前请自行甄别文档内容的完整性,平台不提供额外的编辑、内容补充、找答案等附加服务。
- 2、"仅部分预览"的文档,不可在线预览部分如存在完整性等问题,可反馈申请退款(可完整预览的文档不适用该条件!)。
- 3、如文档侵犯您的权益,请联系客服反馈,我们会尽快为您处理(人工客服工作时间:9:00-18:30)。
2、请根据您上节课列举出来的困惑, 看看哪些方面是与精益思想矛盾的 3、根据精益生产的工具,您认为您的岗位上哪些工具 可以应用
14
第二部分 精益管理技术的实际运用
——运用价值流图发现问题
Lean Production TP SS TQM JTI
TPM
15
价值流的定义
传统思维中,我们总是从工厂内部来考虑,从原材料开始一直追踪到 产品的完成来检查价值流。
Final
27
价值流图的类型(公司级)
公司级价值流图的描述: 产品生产周期时间. 物料接收和完成品交付点. 总体的过程、物料、信息流 一个数据栏描述一个车间 产品生产周期计算 > 接收订单到交付订单 其他……
Supplier X
Customer Y
Press
Body
Paint
Assembly
工艺流 信息流 开展最大价值化行动
过程/时间/资源/ 控制 过程和信息的流向 可能改进的方向
3
24
价值流图的类型
产品簇
当前状态图
改进计划 (通向未来状态之路)
未来状态图
理想状态图
25
价值流图的类型(层级分类)
全公司的价值流图
部门的价值流图
由下向上 由上向下
区 / 分装线
工作小组
26
价值流图的类型(层级分类)
生产 可运行性
精益生产 的基础
9
精益管理的集成观:现场中心主义
任何制造型的企业中,【现场】是可以直接创造附加价值(利润)的 唯一场所,被称之为企业的核心。现场管理的成功与否已成为了企业 生存和发展的关键。围绕着现场的有效管理以提升竞争力,是现场管 理的职责,也是提升企业【核心竞争力】的关键。
供应商
4
精益方式结构
持续改善,尽善尽美
自动化是当 生产有问题 时,设备或 生产线具有 自动停止或 作业员主动 使之停止的 能力。 表现为: 自动检测 自动停止 自动报警
自 动 化 ( 傻 瓜 式 )
产 品 开 发 设 计 系 统
生 产 与 物 流 规 划
TPM 全 面 设 备 维 护
柔 性 生 产 系 统
永远站在客户的立场
价值 尽善尽美
持续改善,追求完美
价值流
从接单到客户接收过程的一切活动
精益生产 流动
象河流一样顺畅流动
需求拉动
按需求生产
降低浪费、改善质量、缩短制造周期、永远满足客户需求
8
精益生产的六个要素
流畅生 产
目标
利 润 和 效 益
质量
工作场地 组织
物料 移动
流畅生产 的保证
员工环境 和参与
价
值
流
过
下料
ห้องสมุดไป่ตู้
程
过
焊接
程
过
程
总装单元
原材料
成品
16
价值流的定义
供应链状态下的价值流包含的是特定产品从进公司到发货至客户的所有要素 括增值的和非增值的)。 (包
需求
设计 采购
原材料
生产制造
入库
发货
客户
也可以用价值流的方法来绘制全产业链的过程。
17
识别价值流
价值流是使一个特定产品通过任何一项商务活动的三项关 键性管理任务时所必须的一组特定活动。此三项关键性管理 任务为: 1、从接受订单到执行生产计划发货的信息流; 2、从原材料到转化为产成品的物流; 3、从概念到正式发布的产品设计流程。
高层级和低层级价值流图关系
一个高层级图通常是一个工厂或一个车间的范围,表现的单元较大
Supplier X Customer Y
Press
Body
Paint
Assembly
一个低层级图通常是一个工厂或车间的细节,表现的单元较小(最 小),通常它包含在高层级图中。
Body
Off Track
T1
T2
T3
T4
先进先出通道 外协厂
Supplier X
Customer Y
Press
Body
Paint
Assembly
30
价值流图需要的典型数据:
产品的生产周期时间:从下订单到交付给客户的整个时间
加工时间:实际产生价值的作业时间
等待时间:产品在现场等待制造或者储存的时间 生产线速率Line Rate (L/R)
设备综合运行效率OEE
生 产 的 快 速 与 维 护
精 益 品 质 保 证 与 自 动 化
柔 性 生 产 系 统
均 衡 化 同 步 化
现 场 IE 作 业 研 究
生 产 设 计 与 物 流 系 统
产 品 开 发 设 计 系 统
意识改革*5S
6
精益生产的技术体系
经济性 不 断 暴 露 问 题, 看板管理 JIT生产方式 尊 重 人 性 , 发 挥 人 的 作 用 公司整体性利润增加 适应性
12
系统解决问题的“七步法”
步骤2 分析 问题
步骤4 选择解 决方法
步骤6 效果 确认
步骤1 确定问题 设定目标
步骤3 提出潜在 解决方法
步骤5 实施 计划
步骤7 巩固 标准化
13
到目前为止我们学习到了什么?
谁完成 任务清单
估计 总的时间: 10分钟
1、通过本节课程,您认为精益生产的核心思想是什么?
28
价值流图的类型(车间级)
车间级价值流图的描述:
用数据栏来描述生产的各个区或工作小组。
工艺流、物流和信息流
表示 顾客-下一部门(车间)
供应商- 上一部门(车间)
计算前置时间 整个车间的生产周期 其他……
Supplier X
Customer Y
Press
Body
Paint
Assembly
为焦点。
进在生产价值流中的物料
流程; 流程改善的结果减少库
存,降低前置时间。
23
绘制价值流图的目的
价值流图是精益制造的工具,完整的绘制出价值流图后,引入目视化 能看到整个制造系统;
1
问题的解决 过程的了解与培训 减少缺陷
最终目标是降低DTD (也就是前置时间) 识别出浪费 改进流程 物流
2
目的
4
供应商
500t卷材
蓝天车业
18400件/月 12400“左置“ 6400“右置“ 周转箱=20件 两班工作
每周传真
每周计划
周二 +周四
每日发运 计划
每日 一次
冲压 5d 卷材 200t 加工周期=1s 换模时间=1h 使用率=85% 准备量二周 1s 4600(左) 2400(右)
点焊Ⅰ 1
换模时间=10Min
第二部分 精益管理技术介绍
Lean Production TP SS
JTI
TPM TQM
0
本节课程目的
• 精益的核心思想:关注流动性,持续改善、改善永无止境 • 精益的技术体系:应用工具介绍 • 精益的管理原则:精益生产的十四项原则
1
生产方式发展的历史
精益生产
福特流水 线 泰勒管理思 想
敏捷生产
加工周期=39s
有效时间27600s
加工周期=46s
换模时间=10Min 有效时间27600s
有效时间27600s
使用率=100% 7.6d 两班工作 39s 1.8d
使用率=80% 两班工作 46s
5d
2.7d
两班工作 62s
2d
两班工作 40s
4.5d
制造周期=23.6d
增值时间=188s
21
价值流图的作用
11
精益生产的十四项基本原则
原则8:使用可靠的、经过充分测试的技术以协助员工及生产流程。 原则9:把彻底了解且遵循公司理念的员工培养成领导者, 使他们能教导其他员工,通过长期关系发展和激励员工与事业伙伴。 原则10:培养与发展信奉公司理念的杰出人才与团队。 持续解决根本问题是企业不断学习的动力 原则11:重视事业伙伴与供货商网络,激励并协助其改善。 原则12:亲临现场察看以彻底了解情况(现实、现地、现物) 原则13:不急于作决策,以共识为基础,彻底考虑所有可能的选择, 并快速执行决策。 原则14:通过不断省思与持续改善以变成一个学习型组织。
现 代 IE 运 用
均 衡 化 同 步 化
TQM 精 益 质 量 保 证
准 时 化 ( ) )
在正确的时间以 正确的方式,按 正确的路线,把 正确的物料,送 到正确的地点, 每次都刚好及时
JIT
意识改革*5S
5
精益生产方式追求的目标
“零”
追求7个“零”极限目标
库存 切换浪费 浪费 停滞 灾害 故障 不良
集中分类
• 质量稳定
• 生产效率高 • 注重员工技能
工匠 单件生产
• 低产量 • 高技术工人
2
• 零缺陷
丰田汽车
现代制造业面临的问题
交货速度——从客户下订单到完成产品交付需要多少时间? 客户能否都对企业承诺的交货期保持信任?
质量要求——建立适当的产品质量标准,目的在于集中全力满足客户要求。
对需求变化的应变能力——在市场需求增长时,企业是否能充分满?
原材料
组 装
技术、品控
成 品
订 单
分销渠道
现场决不是狭义意义上的“车间”! 现场管理的内涵:制造型企业全部门、全过程管理 现场管理常常被忽略,而过度注重研发、营销、财务 分清企业中的2种人:赚钱的人、花钱的人
10
客 户
精益生产的十四项基本原则
原则1:管理活动决策以长期理念为基础,即使因此牺牲短期财务目标。 精益流程:正确的流程方能产生优异成果 原则2:致力于追求建立无间断的操作流程以使问题浮现。 原则3:实施拉动式生产制度以避免生产过剩。 原则4:使工作负荷水平稳定(生产均衡化)。 原则5:建立立即暂停以解决问题、一开始就重视质量管理的文化。 原则6:工作的标准化是持续改进与授权员工的基础。 原则7:运用可视化管理使问题无处隐藏。