回流焊接工艺
SMT加工之回流焊接工艺
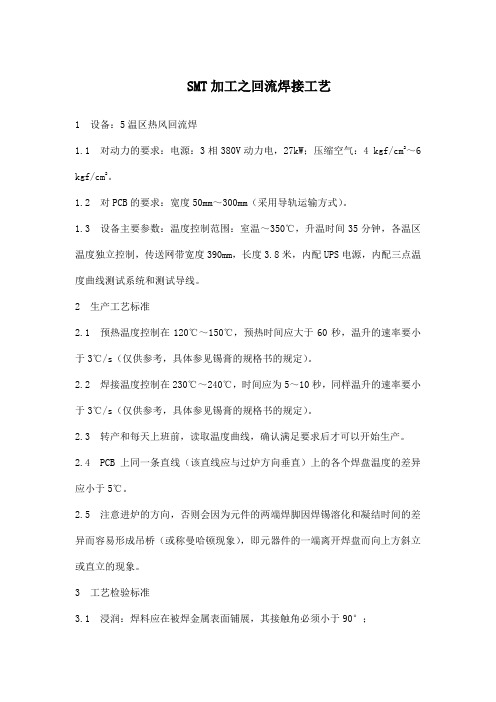
SMT加工之回流焊接工艺
1 设备:5温区热风回流焊
1.1 对动力的要求:电源:3相380V动力电,27kW;压缩空气:4 kgf/cm2~6 kgf/cm2。
1.2 对PCB的要求:宽度50mm~300mm(采用导轨运输方式)。
1.3 设备主要参数:温度控制范围:室温~350℃,升温时间35分钟,各温区温度独立控制,传送网带宽度390mm,长度3.8米,内配UPS电源,内配三点温度曲线测试系统和测试导线。
2 生产工艺标准
2.1 预热温度控制在120℃~150℃,预热时间应大于60秒,温升的速率要小于3℃/s(仅供参考,具体参见锡膏的规格书的规定)。
2.2 焊接温度控制在230℃~240℃,时间应为5~10秒,同样温升的速率要小于3℃/s(仅供参考,具体参见锡膏的规格书的规定)。
2.3 转产和每天上班前,读取温度曲线,确认满足要求后才可以开始生产。
2.4 PCB上同一条直线(该直线应与过炉方向垂直)上的各个焊盘温度的差异应小于5℃。
2.5 注意进炉的方向,否则会因为元件的两端焊脚因焊锡溶化和凝结时间的差异而容易形成吊桥(或称曼哈顿现象),即元器件的一端离开焊盘而向上方斜立或直立的现象。
3 工艺检验标准
3.1 浸润:焊料应在被焊金属表面铺展,其接触角必须小于90°;
3.2 焊料量:焊料量要适中,避免过多或过少;
3.3 焊点表面:应完整、连续和圆滑;
3.4 不允许有虚焊、脱焊、孔洞、桥接、拉尖、焊料球或吊桥的现象。
回流焊接工艺及无铅技术要求

回流焊接工艺及无铅技术要求回流焊接是一种常见的电子组装工艺,旨在通过在电路板上加热的同一区域内同时完成焊接和热残留的去除。
回流焊接工艺的目的是确保焊接质量,并尽量减少热应力对电子器件造成的损害。
无铅焊接是一种环保型的回流焊接工艺,旨在取代含铅焊料并减少对环境的污染。
下面将详细介绍回流焊接工艺和无铅技术要求。
回流焊接工艺通常包括以下几个步骤:预热、焊接、冷却和清洗。
首先是预热阶段,通过加热电路板上的焊盘和元件至预定温度,以准备焊接。
焊接阶段是回流焊接的关键步骤,焊盘和元件表面的焊膏会熔化并形成焊点。
在此过程中,需要控制好温度和焊接时间,以确保焊接的质量。
冷却阶段是将焊点迅速冷却至室温,以固化焊膏。
最后是清洗阶段,通过去除焊接过程中产生的流动剂和焊膏残留物,以使电路板达到可靠的电气和机械性能。
无铅焊接是对传统含铅焊接的替代方案,以减少对环境的污染和人体健康的影响。
无铅焊料通常使用锡和其他合金元素的组合,以替代传统含铅焊料。
由于无铅焊料的熔点较低和流动性相对较差,需要对回流焊接工艺进行调整。
以下是无铅焊接技术的一些要求:1.温度控制:无铅焊接的温度一般较高,通常在240-260摄氏度之间。
需要确保焊接区域的温度能够达到要求,并且在焊接过程中保持稳定。
2.施加力度:由于无铅焊料的流动性较差,需要增加施加于元件的重量,以确保焊盘和元件之间能够良好接触。
3.回流焊炉的设计:无铅焊接需要的温度较高,而焊炉的设计应考虑到这一点,以确保工艺的可行性。
4.元件的选择:无铅焊接对元件有一定的要求,不同的元件可能需要适用于无铅焊接的制造工艺。
5.环境和健康安全:无铅焊接强调环保和健康安全,需要遵守相关的法规和标准,并对焊接工艺进行有效的控制和监测。
总之,回流焊接是一种常见的电子组装工艺,无铅焊接是其环保型的变体。
为了确保焊接质量和减少环境污染,需要对回流焊接工艺进行调整,并且遵守无铅焊接技术的要求。
这些要求包括温度控制、施加力度、焊炉设计、元件选择以及环境和健康安全等方面。
回流焊工艺流程
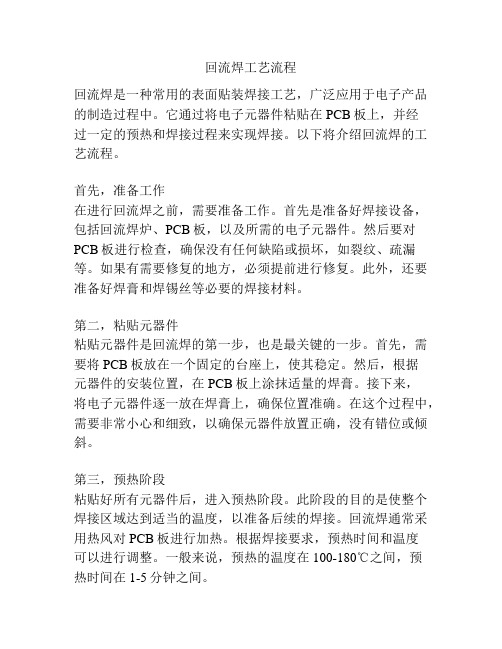
回流焊工艺流程回流焊是一种常用的表面贴装焊接工艺,广泛应用于电子产品的制造过程中。
它通过将电子元器件粘贴在PCB板上,并经过一定的预热和焊接过程来实现焊接。
以下将介绍回流焊的工艺流程。
首先,准备工作在进行回流焊之前,需要准备工作。
首先是准备好焊接设备,包括回流焊炉、PCB板,以及所需的电子元器件。
然后要对PCB板进行检查,确保没有任何缺陷或损坏,如裂纹、疏漏等。
如果有需要修复的地方,必须提前进行修复。
此外,还要准备好焊膏和焊锡丝等必要的焊接材料。
第二,粘贴元器件粘贴元器件是回流焊的第一步,也是最关键的一步。
首先,需要将PCB板放在一个固定的台座上,使其稳定。
然后,根据元器件的安装位置,在PCB板上涂抹适量的焊膏。
接下来,将电子元器件逐一放在焊膏上,确保位置准确。
在这个过程中,需要非常小心和细致,以确保元器件放置正确,没有错位或倾斜。
第三,预热阶段粘贴好所有元器件后,进入预热阶段。
此阶段的目的是使整个焊接区域达到适当的温度,以准备后续的焊接。
回流焊通常采用热风对PCB板进行加热。
根据焊接要求,预热时间和温度可以进行调整。
一般来说,预热的温度在100-180℃之间,预热时间在1-5分钟之间。
第四,焊接阶段预热完成后,进入焊接阶段。
焊接是回流焊的核心过程。
通过升温到适当的温度来烧结焊膏,并将焊膏中的焊锡熔化,使其与PCB板和元器件连接起来。
同时,焊锡中的助焊剂会起到去氧化和去污的作用,确保焊接质量。
焊接温度和时间取决于焊接质量要求和元器件的要求。
最后,冷却阶段焊接完成后,需要进行冷却。
冷却是回流焊过程中的最后一步,也是非常重要的一步。
它可以使焊接点冷却到室温,并使焊点与PCB板及元器件之间的连接得到巩固。
在冷却过程中,需要注意避免外力的干扰,以免焊接点受到损坏。
总结起来,回流焊工艺流程包括准备工作、粘贴元器件、预热阶段、焊接阶段和冷却阶段。
一次完整的回流焊过程需要注意每个环节的细节和要求,以确保焊接质量和稳定性。
回流焊原理以及工艺

回流焊机原理以及工艺1.什么是回流焊回流焊是英文Reflow是通过重新熔化预先分配到印制板焊盘上的膏装软钎焊料,实现表面组装元器件焊端或引脚与印制板焊盘之间机械与电气连接的软钎焊。
回流焊是将元器件焊接到PCB板材上,回流焊是对表面帖装器件的。
回流焊是靠热气流对焊点的作用,胶状的焊剂在一定的高温气流下进行物理反应达到SMD的焊接;之所以叫"回流焊"是因为气体在焊机内循环流动产生高温达到焊接目的。
回流焊机原理分为几个描述:(回流焊温度曲线图)A.当PCB进入升温区时,焊膏中的溶剂、气体蒸发掉,同时,焊膏中的助焊剂润湿焊盘、元器件端头和引脚,焊膏软化、塌落、覆盖了焊盘,将焊盘、元器件引脚与氧气隔离。
B.PCB进入保温区时,使PCB和元器件得到充分的预热,以防PCB突然进入焊接高温区而损坏PCB和元器件。
C.当PCB进入焊接区时,温度迅速上升使焊膏达到熔化状态,液态焊锡对PCB的焊盘、元器件端头和引脚润湿、扩散、漫流或回流混合形成焊锡接点。
D.PCB进入冷却区,使焊点凝固此;时完成了回流焊。
2.回流焊机流程介绍回流焊加工的为表面贴装的板,其流程比较复杂,可分为两种:单面贴装、双面贴装。
A,单面贴装:预涂锡膏→贴片(分为手工贴装和机器自动贴装)→回流焊→检查及电测试。
B,双面贴装:A面预涂锡膏→贴片(分为手工贴装和机器自动贴装)→回流焊→B面预涂锡膏→贴片(分为手工贴装和机器自动贴装)→回流焊→检查及电测试。
回流焊的最简单的流程是"丝印焊膏--贴片--回流焊,其核心是丝印的准确,对贴片是由机器的PPM来定良率,回流焊是要控制温度上升和最高温度及下降温度曲线。
"回流焊机工艺要求回流焊技术在电子制造领域并不陌生,我们电脑内使用的各种板卡上的元件都是通过这种工艺焊接到线路板上的。
这种工艺的优势是温度易于控制,焊接过程中还能避免氧化,制造成本也更容易控制。
这种设备的内部有一个加热电路,将氮气加热到足够高的温度后吹向已经贴好元件的线路板,让元件两侧的焊料融化后与主板粘结。
回流焊工艺简单介绍

回流焊工艺简单介绍1、回流焊流程介绍回流焊加工的为表面贴装的板,其流程比较复杂,可分为两种:单面贴装、双面贴装。
A,单面贴装:预涂锡膏→贴片(分为手工贴装和机器自动贴装) →回流焊→检查及电测试。
B,双面贴装:A面预涂锡膏→贴片(分为手工贴装和机器自动贴装) →回流焊→B面预涂锡膏→贴片(分为手工贴装和机器自动贴装)→回流焊→检查及电测试。
2、PCB质量对回流焊工艺的影响。
3、焊盘镀层厚度不够,导致焊接不良。
需贴装元件的焊盘表面镀层厚度不够,如锡厚不够,将导致高温下熔融时锡不够,元件与焊盘不能很好地焊接。
对于焊盘表面锡厚我们的经验是应大于100μm。
4、焊盘表面脏,造成锡层不浸润。
板面清洗不干净,如金板未过清洗线等,将造成焊盘表面杂质残留。
焊接不良。
5、湿膜偏位上焊盘,引起焊接不良。
湿膜偏位上需贴装元件的焊盘,也将引起焊接不良。
6、焊盘残缺,引起元件焊不上或焊不牢。
7、BGA焊盘显影不净,有湿膜或杂质残留,引起贴装时不上锡而发生虚焊。
8、BGA处塞孔突出,造成BGA元件与焊盘接触不充分,易开路。
9、BGA处阻焊套得过大,导致焊盘连接的线路露铜,BGA贴片的发生短路。
10、定位孔与图形间距不符合要求,造成印锡膏偏位而短路。
11、IC脚较密的IC焊盘间绿油桥断,造成印锡膏不良而短路。
12、IC旁的过孔塞孔突出,引起IC贴装不上。
13、单元之间的邮票孔断裂,无法印锡膏。
14、钻错打叉板对应的识别光点,自动贴件时贴错,造成浪费。
15、NPTH孔二次钻,引起定位孔偏差较大,导致印锡膏偏。
16、光点(IC或BGA旁),需平整、哑光、无缺口。
否则机器无法顺利识别,不能自动贴件。
17、手机板不允许返沉镍金,否则镍厚。
回流焊工艺流程

回流焊工艺流程一、概述回流焊是一种常用的电子元器件表面贴装工艺,它通过高温熔化焊锡膏,使其与电路板上的焊盘和元器件引脚相互连接。
本文将详细介绍回流焊的工艺流程。
二、准备工作1. 焊接设备:回流焊炉、印刷机等;2. 焊接材料:钢网板、焊锡膏等;3. 焊接工具:镊子、吸锡器等;4. 焊接环境:无尘室或洁净室。
三、印刷钢网板1. 准备好钢网板和印刷机;2. 在钢网板上涂抹适量的胶水,均匀分布在整个钢网板上;3. 将印刷机放置在钢网板上,通过压力将胶水压到印刷机孔洞中;4. 将印刷机移开,让钢网板完全干燥。
四、贴装元器件1. 准备好电路板和元器件;2. 在电路板上涂抹适量的焊锡膏,均匀分布在整个电路板上;3. 将元器件放置在电路板上,对齐焊盘和引脚;4. 使用镊子或吸锡器将元器件固定在电路板上。
五、回流焊1. 准备好回流焊炉;2. 将电路板放置在回流焊炉中;3. 开始加热,升温速度约为2-3℃/s,直到达到预设温度(通常为230-250℃);4. 维持温度一段时间(通常为60-120秒),使焊锡膏完全熔化并与焊盘和引脚相互连接;5. 冷却至室温,取出电路板。
六、检测1. 对焊点进行目视检查,确保没有明显的缺陷;2. 进行X射线检测和AOI检测,以确保所有的焊点都满足质量标准。
七、清洗1. 准备好清洗设备和清洗液;2. 将电路板放入清洗液中,轻轻搓揉几分钟;3. 取出电路板,用水冲洗干净;4. 用干净的气体吹干电路板。
八、包装1. 准备好包装材料和设备;2. 将电路板放入包装材料中,如泡沫盒或防静电袋中;3. 进行包装,标记相关信息。
九、总结回流焊是一种常用的表面贴装工艺,通过以上的步骤可以完成回流焊的工艺流程。
在实际操作中,需要严格控制温度、时间和环境等因素,以确保焊点的质量和稳定性。
回流焊接工艺的经典PCB温度曲线
回流焊接工艺的经典PCB温度曲线回流焊接工艺是目前电子制造中常用的连接电子元器件和印刷电路板(PCB)的工艺。
在这个工艺中,焊料在高温下融化,连接电子元器件和PCB,然后在一定时间内冷却固化。
经典PCB温度曲线是在回流焊接过程中记录温度变化的图表。
本文将介绍回流焊接工艺和经典PCB温度曲线的相关知识。
一、回流焊接工艺1. 回流焊接的分类回流焊接分为波峰焊接和气相焊接两种。
波峰焊接流程简单,加热过程和冷却条件单一,在单页双面电路板上应用较为广泛。
气相焊接由于温度和气流的可控性好,适用于多层电路板。
2. 回流焊接的基本步骤回流焊接过程包括物料准备、滞留、预热、焊接、冷却和检验六个步骤,每个步骤都有一定的要求。
a.物料准备确认PCB上元件的安装位置和方向是否正确。
b.滞留滞留指将焊接板在回流炉中升温前保持一定时间,以排除湿气,以免电路板和元器件受潮。
滞留时间不同,多因芯片型号、因素的耐受性以及实际情况。
在单页双面电路板和双面电路板中,常用的滞留时间为1-2小时但是在高层数的印刷电路板中滞留时间也可以达到2小时以上,需要根据实际情况判断滞留时间。
c.预热预热可以让PCB和元器件缓慢升温,以达到减少热应力和消除振动应力的目的。
预热时间通常为2-3分钟。
d.焊接焊接是回流焊接的主要步骤之一,只有在实现良好焊接后,电子产品才能保证稳定性和性能达到设计要求。
当确定每层焊点预热后,轮到钢板上。
生产厂商可以通过合理的方法来优化加热过程,大多数生产商将在PCB板上的贴有焊料的元器件表面涂上一只薄薄的层面包油,以防止软件软化后移位。
e.冷却冷却是回流焊接的一个关键步骤,在冷却过程中,焊料应该完全凝固,以避免导致PCB与元器件的热应力。
冷却时间一般为3-5分钟。
f.检验焊点完全冷却后,应对焊接点进行检查。
在这步检查过程,生产厂家会使用高清晰度成像系统,确保焊点品质符合标准。
二、经典PCB温度曲线经典PCB温度曲线是指在回流焊接过程中,PCB的温度变化曲线。
回流焊接工艺及可控制的手段
回流焊接工艺及可控制的手段作者:刘敏陈晓玲张强盛春玲来源:《硅谷》2008年第21期[摘要]回流焊炉的温度曲线对于回流焊接工艺及其关键指标具有显著的影响,对回流焊的温度曲线对回流工艺及其关键指标的影响进行全面的研究,并掌握焊接工艺的重要性。
[关键词]回流焊工艺回流温度曲线中图分类号:TM 文献标识码:A 文章编号:1671-7597(2008)1110122-01回流焊,也叫做再流焊,是伴随微型化电子产品的出现而发展起来的锡焊技术,主要应用于各类表面安装元器件的焊接。
这种焊接技术的焊料是焊锡膏。
预先在印刷电路板的焊接部位施放适量和适当的焊锡膏,然后贴放表面组装元器件,焊锡膏将元器件粘在PCB板上,利用外部热源加热,使焊料融化而再次流动浸润,将元器件焊接到印刷板上。
回流焊操作方法简单,效率高、质量好、一致性好,节省焊料,是一种适合自动化生产的电子产品装配技术。
回流焊技术目前已经成为SMT电路板安装技术的主流。
回流焊技术的一般工艺流程如下图所示。
下面进一步了解回流焊接工艺以及它可控制的手段技巧。
一、回流焊接工艺(一)回流焊接温度直线由于整个回流焊接的工艺要点在于控制PCBA上各点的温度和时间,温度曲线是个常用和重要的工艺管理工具。
从基本理论上来看,图二中的温度‘直线’是可以做到焊接效果的。
事实上这很难做到。
主要是实际产品存在不同的器件和布线,这意味着PCBA上不同点有热容量的差别。
所以可能出现以下图二中的情况。
从图二中可以看到板上有热点和冷点需要同时照顾到其各自的温度/时间需求。
当把冷点(B)的温度调到符合焊接要求时,板上的热点(A)有可能已经超出安全温度而造成损坏。
但如果把温度降低到A点符合要求时,则B点可能又出现冷焊故障。
另一个问题,是PCBA 设计一般牵涉到许多不同的器件材料和封装,因为目前采用的回流炉子以热风技术为多,其传热依靠对流效果,而空气流动的控制是个高难度的工艺,何况必须控制到SMT焊端这么微小的面积精度上,几乎是不可能做得很好。
回流焊操作工艺规程
回流焊操作工艺规程回流焊是一种常用的电子产品焊接工艺,它能够高效地完成PCB电路板上的焊接工作,并且能够保证焊接质量,因此在电子制造行业得到了广泛的应用。
为了保证回流焊质量和生产效率,制定回流焊操作工艺规程是非常重要的。
下面是一个1200字以上的回流焊操作工艺规程:一、回流焊工艺的基本要求:回流焊是一种通过传导和传导的热量来完成焊接的工艺,它要求焊接温度和时间的控制,以保证焊接质量。
回流焊操作工艺规程应遵循以下基本要求:1.确定正确的焊接温度曲线:回流焊需要在一个特定的温度区间内进行,过高或过低的温度都会影响焊接质量。
因此,应根据焊接器件和电路板材料的特性,确定合适的焊接温度曲线。
2.控制好焊接时间和速度:焊接时间和速度也会影响焊接质量。
焊接时间过长可能会导致电路板和焊接器件的损坏,而焊接时间过短则可能导致焊点不牢固。
因此,应根据实际情况,控制好焊接时间和速度。
3.保证焊接区域的平整度:焊接区域的平整度对焊接质量起着重要作用,可以通过调整传送带的速度、压力和焊接温度来保证焊接区域的平整度。
4.保证焊接点的一致性:焊接点的一致性是焊接质量的关键,要保证每个焊点的大小和形状一致。
可以通过控制焊接温度、焊接时间和焊接速度,以及选用合适的焊接剂来实现焊接点的一致性。
5.做好焊后检测和维护:焊后检测是确保焊接质量的关键,应定期对焊接点进行可视检查和电性测试,以发现焊接质量问题并及时解决。
同时,要定期对焊接设备进行维护,保持设备的良好状态。
二、回流焊操作工艺规程的制定:为了保证回流焊质量和生产效率,需要制定一套完整的回流焊操作工艺规程。
下面是一套可以参考的回流焊操作工艺规程:1.准备工作a.确定焊接温度曲线:根据焊接器件和电路板材料的特性,确定合适的焊接温度曲线。
b.设置传送带速度:根据焊接区域的大小和焊接时间要求,设置合适的传送带速度。
c.检查回流焊设备:确保焊接设备的工作状态良好,如传送带的运行平稳、加热区域的加热元件正常工作等。
回流焊原理及工艺流程
回流焊原理及工艺流程
回流焊(Reflow soldering)是一种将焊料(solder)涂在电子元器件和电路板表面,通过加热使其熔化并与电路板表面结合在一起的焊接技术。
回流焊的工艺流程如下:
1. 表面处理:电路板表面需要进行清洁、去毛刺、去污等处理,以便焊料可以充分润湿。
2. 贴装元器件:将元器件通过自动贴装机或手工贴装的方式粘贴在电路板上。
3. 印刷焊膏:将焊膏印刷到元器件和电路板的焊接区域上。
4. 预热:将电路板放置在预热区,温度逐渐升高,使得焊膏中的挥发性成分挥发,准备进入焊接区。
5. 焊接:在焊接区中,电路板通过运送带进入回流炉中,使得焊膏熔化,在高温下进行焊接,使得电路板表面和元器件连接在一起。
6. 冷却:将焊接区中的电路板冷却至室温,焊接完成。
回流焊技术的优点是焊接质量可靠,成本低,效率高,适用范围广。
但是焊接过
程中需要控制温度,不当的温度会造成元器件损坏或焊接质量不佳,因此对于不同种类的电路板和元器件,需要按照不同的工艺参数进行调整和优化。
- 1、下载文档前请自行甄别文档内容的完整性,平台不提供额外的编辑、内容补充、找答案等附加服务。
- 2、"仅部分预览"的文档,不可在线预览部分如存在完整性等问题,可反馈申请退款(可完整预览的文档不适用该条件!)。
- 3、如文档侵犯您的权益,请联系客服反馈,我们会尽快为您处理(人工客服工作时间:9:00-18:30)。
回流焊接工艺
回流焊接是表面贴装技术(SMT)特有的重要工艺,焊接工
艺质量的优劣不仅影响正常生产,也影响最终的质量和可靠性。
在使用表面贴装元件的印刷电路板(PCB)装配中,要得到优质的
焊点,一条优化的回流温度曲线是最重要的因素之一。
温度曲线是施加于电路装配上的温度对时间的函数,当在笛卡尔平面作图时,回流过程中在任何给定的时间上,代表 PCB 上一个特定点上的温度形成一条曲线。
几个参数影响曲线的形状,其中最关键的是传送带速度和每个温区的温度设定。
链速决定基板暴露在每个温区所设定的温度下的持续时间,增加持续时间可以允许更多时间使电路装配接近该温区的温度设定。
每个温区所花的持续时间总和决定总共的处理时间。
每个区的温度设定影响 PCB 的温度上升速度。
增加温区的设定温度允许基板更快地达到给定温度。
因此,必须作出一个较好的图形来决定 PCB 的温度曲线,理想的温度曲线由基本的四个区组成,前面三个区加热、最后一个区冷却。
回流炉的温区越多,越能使温度曲线的轮廓达到更准确和接近设定。
大多数锡膏都能用四个基本温区成功回流。
在回流焊接过程中,锡膏需经过溶剂挥发;焊剂清除焊件表面的氧化物;锡膏的熔融、再流动以及锡膏的冷却、凝固。
以下就对温度曲线图及四个区进行介绍:
1
Peak: 熔点 220℃以
上
210~220℃
180℃150℃
时间 S 250S 200S 150S 100S 50S 预热区:也叫斜坡区。
目的:使 PCB 和元器件预热,达到平衡,同时除去焊膏中的水份、溶剂,以防焊膏发生塌落和焊料飞溅。
要保
证升温比较缓慢,溶剂挥发。
较温和,对元器件的热冲击尽可能小,
在这个区,尽量将升温速度控制在 2~5℃/S,较理想的升温速度为
1~3 ℃/S,时间控制在 60~90S 之间。
升温过快会造成对元器件的
伤害,如会引起多层陶瓷电容器开裂。
同时还会造成焊料飞溅,使
在整个PCB的非焊接区域形成焊料球以及焊料不足的焊点。
而温度上
升太慢,锡膏会感温过度,没有足够的时间使 PCB 达到活性温度。
锡
炉的预热区一般占整个加热通道长度的 25~33%。
保温区:也称活性区、有时叫做干燥或浸润区。
目的:保证在达到回流温度之前焊料能完全干燥,同时还起着焊剂活化的作用,清除
元器件、焊盘、焊粉中的金属氧化物。
在这个阶段助焊剂开始挥发,
这个区一般占加热通道的 33~50%。
有两个功用:第一是将 PCB 在相当稳定的温度下感温,允许不同质量的元件在温度上同质,减少它们
的相当温差;第二个功能是允许助焊剂活性化,挥发性的物质从锡膏
中挥发。
一般温度范围在 150~180℃,时间范围在 60~120S,升温
速度控制在 0.3~0.5 ℃/S。
如果活性区的温度设定太高,助焊剂没
有足够的时间活性化,温度曲线的斜率是一个向上递增的斜率。
虽然
有的锡膏制造商允许活性化期间一些温度的增加,但是理想的曲线要
求相当平稳的温度,这样使得 PCB 的温度在活性区开始和结束时间是
相等的。
回流区:有时叫做峰值区或最后升温区。
目的:锡膏中的焊料使
合金属粉开始熔化,再次呈流动状态,替代液态焊剂润湿焊盘和元器
件,这种润湿作用导致焊料进一步扩展,对大多数焊料润湿时间为60~90 秒。
这个区的作用是将 PCB 装配的温度从活性温度提高到所推荐的峰值温度。
活性温度总是比合金的熔点温度低一点,而峰值温
度总是在熔点上。
再流焊的温度要高于锡膏的熔点温度,一般要超过
熔点温度 20 度才能保证再流焊的质量。
有时也将该区域分为两个区,即熔融区和再流区。
(有铅锡的熔点 183℃,无铅锡熔点 216~220℃)
其中温度在 210~220℃范围内的时间控制相当关键,一般控制在
10~20S 为最佳。
这个区的温度设定太高会使其温升斜率超过每秒
2~5℃,或达到回流峰值温度比推荐的高。
这种情况可能引起 PCB 的弯曲变形、脱层、烧损或烤黄,并损害元件的完整性,特别是一些耐热温度较低的元件。
冷却区:这一阶段锡膏开始凝固。
元件被固定在 PCB 上,同样的是降温的速度也不能够快,一般控制在 4℃/S以下,较理想的降温速度为 3℃/S。
由于过快的降温速度会造成 PCB 产生冷变形,会影响焊点的表面质量。
以下就对由于回流温度曲线设定不合适而造成不良分析:
1. 锡粒问题:
回流焊接中出的锡粒,常常藏于矩形片式元件两端之间的侧面或细距引脚之间。
在元件贴装过程中,锡膏被置于片式元件的引脚与焊
盘之间,随着印制板穿过回流焊炉,锡膏熔化变成液体,如果与焊盘
和器件引脚等润湿不良,液态焊锡会因收缩而使焊缝填充不充分,所
有焊料颗粒不能聚合成一个焊点。
部分液态焊锡会从焊缝流出,形成
锡粒。
因此,焊锡与焊盘和器件引脚润湿性差是导致锡球形成的根本
原因。
以下主要分析与相关工艺有关的原因及解决措施: a) 回流温度曲线设置不当。
锡膏的回流是温度与时间的函数,如果未到达足够的
温度或时间,锡膏就不会被回流。
预热区温度上升速度过快,达到平
顶温度的时间过短,使锡膏内部的水份、溶剂未完全挥发出来,到达
回流焊温区时,引起水份、溶剂沸腾,溅出焊锡粒。
实践证明,将
预热区温度的上升速度控制在 1~4°C/s 是较理想的。
b) 如果在贴片至回流焊的时间过长,则因锡膏中焊料粒子的氧化,焊剂变质、活
性降低,会导致锡膏不回流,焊球则会产生。
选用工作寿命长一些的
焊膏(至少 4 小时),则会减轻这种影响。
.锡珠(Solder Balls):
(1)、丝印孔与焊盘不对位,印刷不精确,使锡膏弄脏PCB。
2、锡膏
在氧化环境中暴露过多、吸空气中水份太多。
3、加热不精确,太慢并不
均匀。
4、加热速率太快并预热区间太长。
5、锡膏干得太快。
6、助焊剂活
性不够。
7、太多颗粒小的锡粉。
8、回流过程中助焊剂挥发性不适当。
锡球的工艺认可标准是:当焊盘或印制导线的之间距离为0.13mm时,锡珠
直径不能超过0.13mm,或者在600mm平方范围内不能出现超过五个锡珠。
2.竖立问题(曼哈顿现象)
矩形片式元件的一端焊接在焊盘上,而另一端则翘立,这种现象就称为曼哈顿现象。
引起该种现象主要原因是元件两端受热不均匀,
锡膏熔化有先后所致。
如何减少元件两端受热不均匀: a) 有缺陷
的元件排列方向设计。
我们设想在回流炉中有一条横跨锡炉宽度的回
流焊限线,一旦锡膏通过它就会立即熔化。
片式矩形元件的一个端头
先通过回流焊限线,锡膏先熔化,完全浸润元件的金属表面,具有液
态表面张力;而另一端未达到有铅与无铅的熔点的液相温度,锡膏未
熔化,只有焊剂的粘接力,该力远小于回流焊接的表面张力,因而,
使未熔化端的元件端头向上直立。
因此,保持元件两端同时进入回流
焊限线,使两端焊盘上的锡膏同时熔化,形成均衡的液态表面张力,
保持元件位置不变。
b) 在进行汽相焊接时 PCB 预热不充分(氮气回流)
汽相焊是利用惰性液体蒸汽冷凝在元件引脚和 PCB 焊盘上时,释放出热量而熔化锡膏。
汽相焊分平衡区和饱和蒸汽区,在饱和蒸汽区
焊接温度高达 217℃,在生产过程中我们发现,如果被焊组件预热不
充分,经受一百多度的温差变化,汽相焊的汽化力容易将小于 3216
封装尺寸的片式元件浮起,从而产生竖立现象。
我们通过将被焊组件
在烤箱内以 145 -150℃的温度预热 1-2 分钟,然后在汽相焊的平衡
区内再预热 1 分钟左右,最后缓慢进入饱和蒸汽区焊接消除了竖立现象。
3.吹孔
BLOWHOLES 焊点中(SOLDER JOINT)所出现的孔洞,大者称为吹孔,小者叫做针孔,皆由膏体中的溶剂或水分快速氧化所致。
对策;调整锡膏粘度。
调整预热温度,以赶走过多的溶剂。
提高锡膏
中金属含量百分比。
4.锡桥(Bridging):
一般来说,造成锡桥的因素就是由于锡膏太稀,包括锡膏内金属或固体
含量低、摇溶性低、锡膏容易榨开,锡膏颗粒太大、助焊剂表面张力太小。
焊
盘上太多锡膏,回流温度峰值太高等。
5.开路(Open):
原因:1、锡膏量不够。
2、元件引脚的共面性不够。
3、锡湿不够(不够熔化、流动性不好),锡膏太稀引起锡流失。
4、引脚吸锡(象灯芯草一样)或附近有
连线孔。
引脚的共面性对密间距和超密间距引脚元件特别重要,一个解决方法是
在焊盘上预先上锡。
引脚吸锡可以通过放慢加热速度和底面加热多、上面加热少
来防止。
也可以用一种浸湿速度较慢、活性温度高的助焊剂或者用一种Sn/Pb不同比例的阻滞熔化的锡膏来减少引脚吸锡。