传动齿轮工艺设计
传动齿轮轴的加工工艺设计说明书

摘要齿轮轴零件的主要作用是支撑回转零件、实现回转运动并传递转矩和动力。
齿轮轴具备传动效率高、结构紧凑和使用寿命长等一系列优点,是通用机械特别是工程机械传动中的重要零件之一。
齿轮轴加工材料、热处理方式、机械加工工艺过程的优化,将对提高齿轮轴的加工质量及寿命有着重要借鉴意义。
本设计首先分析了齿轮轴零件的作用和零件的材料,之后把加工传动齿轮轴所用的材料和生产类型确定下来。
然后确定毛坯的种类,绘制铸件零件图。
接下来设计零件的加工工艺性,包括零件表面的加工方法及热处理方法等。
最后进行工艺规程设计,选定加工所用的机床,刀具,夹具等。
齿轮轴零件的机械综合性能要求较高,一般选择锻件作为毛坯。
合理安排工艺路线,划分加工阶段对保证零件加工质量至关重要.关键词: 齿轮轴;工艺分析;工艺规程设计AbstractThe main function of the gear shaft is to support rotating parts, achieve rotary mo tion and transfer torque and power. Gear shaft has a series of advantages, such as high transmission efficiency, compact structure, long service life and so on. It is one of the important parts in the general machinery, particularly the engineering machinery tran smission. The optimization of the gear shaft’s machining materials, thermal treatmen t method and machining process will have great significance on the machining quality of the gear shaft and the service life.The first design of the gear shaft parts and parts of the material, then fix the processing gear shaft of the materials used and the type of production. And then determine the blank type, drawing casting parts diagram. The processing of the next design of parts, including the components surface processing method and heat treatment method. Finally, technological process design ,selection of the machine tool, cutting tool, fixture etc…Comprehensive mechanical performance requirements higher gear shaft parts, as general forging blank. Reasonable arrangements for the process, dividing the processing stage is very important to ensure the machining quality of parts.Keywords gear shaft; process analysis; process planning design目录摘要 (I)ABSTRACT (II)第1章绪论............................................................................................................. - 1 -第2章零件的分析 (2)2.1零件的作用 (2)2.1.1零件的作用 (2)2.1.2零件的结构特点及技术要求 (2)2.2零件材料分析 (3)2.3确定生产类型 (3)2.4毛坯的确定 (4)2.5绘制铸件零件图 (4)2.6本章小节 (5)第3章加工工艺过程分析 (5)3.1加工工艺过程的组成 (6)3.2定位基准的选择原则 (6)3.2.1基准的概念 (6)3.2.2 定位基准的选择 (7)3.2.3 定位基准的确定 (8)3.3零件表面加工方法的选择 (10)3.4加工工序安排 (10)3.5热处理工序的安排 (11)3.6工序的划分 (11)3.7加工余量及工序尺寸的确定 (12)3.7.1 加工余量的概念 (12)3.7.2 加工余量的确定方法 (12)3.8本章小结 (13)第4章选择加工设备及工艺设备 (14)4.1各机床的作用 (14)4.1.1车床的作用 (14)4.1.2铣床的作用 (15)4.1.3 磨床的作用 (16)4.1.4 零件加工中各机床的确定 (17)4.2刀具的选择 (17)4.2.1 刀具材料的确定 (17)4.2.2 刀具的分类 (17)4.2.3 常用车刀刀具的用途 (18)4.2.4 铣刀 (19)4.2.5 磨削 (20)4.2.6 加工零件刀具的确定 (20)4.3夹具的确定 (20)4.3.1 夹具的组成及作用 (20)4.3.2 夹具的分类 (21)4.3.3 选择夹具 (22)4.4量具的选择 (22)4.5本章小结 (23)第5章齿轮轴的工艺卡拟定 (24)5.1工艺卡的拟定 (24)5.2问题的提出 (28)5.3本章小结 (29)总结 (30)参考文献 (31)致谢 (32)第1章绪论本文设计的主要是齿轮轴的加工工艺,通过总结零件的的加工,提高所加工工件的质量,完善产品,满足要求,提高经济效益和劳动生产率。
齿轮传动设计与计算

齿轮传动设计与计算
引言
齿轮传动是一种常见且重要的机械传动方式,广泛用于各种机
械设备中。
本文旨在介绍齿轮传动的基本原理、设计方法和计算过程。
齿轮传动基本原理
齿轮传动是通过齿轮之间的啮合来传递力和运动的机制。
主要
包括两个关键参数:模数和齿数。
模数是指齿轮齿廓的比例系数,
齿数是指齿轮上的齿的数量。
通过合理选择模数和齿数,可以满足
传动的要求。
齿轮传动设计步骤
齿轮传动的设计过程一般包括以下步骤:
1. 确定传动比:根据传动要求和输入输出的转速,确定传动比。
2. 选择齿轮类型:根据传动要求和空间限制,选择合适的齿轮
类型,如直齿轮、斜齿轮或蜗杆齿轮。
3. 计算齿轮参数:根据传动比、输入输出转速和齿轮类型,计
算齿轮的模数、齿数和齿轮直径等参数。
4. 验证设计:通过计算齿轮间的啮合角度、啮合强度和齿轮的
受载能力等指标,验证设计的合理性。
齿轮传动计算
齿轮传动的计算过程主要涉及以下几个方面:
1. 齿轮啮合角度计算:根据齿轮的齿数和模数,计算齿轮之间
的啮合角度。
2. 齿轮模数计算:根据传动比和齿轮的模数,计算齿轮的模数。
3. 齿轮齿数计算:根据传动比和齿轮的模数,计算齿轮的齿数。
4. 齿轮直径计算:根据齿轮的模数和齿数,计算齿轮的直径。
以上是齿轮传动设计与计算的基本内容。
齿轮传动的设计和计算过程需要充分考虑传动要求、材料强度和工艺要求等因素,以实现可靠的传动效果。
微型行星齿轮传动设计方案

微型行星齿轮传动设计方案:一、设计需求分析:1. 需要设计一个微型行星齿轮传动系统,用于实现高效率和紧凑结构的转动传动。
2. 传动系统需要具备较高的扭矩传递能力和稳定性,适用于微型机械设备。
3. 考虑到微型尺寸和工作环境的特殊性,设计应该注重轻量化、低噪音和长寿命等特点。
二、设计方案概述:1. 采用行星齿轮传动结构,包括太阳轮、行星轮、行星架等部件。
2. 选择合适的材料,如优质合金钢或不锈钢,以确保传动系统的强度和耐磨性。
3. 考虑到微型尺寸,可以采用微加工技术,如微铣削、微孔加工等,来实现精密加工。
4. 结合CAD软件进行三维建模和仿真分析,优化传动系统的结构设计。
三、具体设计步骤:1. 确定传动比和扭矩传递要求,根据实际应用场景确定齿轮参数。
2. 设计太阳轮、行星轮和行星架的结构,保证它们之间的啮合正常,并考虑润滑和散热问题。
3. 进行齿轮参数的计算和优化设计,确保传动效率和稳定性。
4. 结合CAD软件进行三维建模,进行装配模拟和运动仿真分析,验证传动系统设计的合理性。
5. 制定加工工艺方案,选择合适的加工工艺和设备进行加工制造。
6. 进行实验验证,测试传动系统的性能指标,如传动效率、噪音水平和扭矩传递能力等。
四、注意事项:1. 在设计过程中要考虑到传动系统的整体性能,如传动效率、噪音、寿命等。
2. 选择优质材料和精密加工工艺,确保传动系统的稳定性和可靠性。
3. 注意传动部件之间的匹配和啮合,避免因为设计不当导致传动失效或损坏。
4. 完成设计后,要进行严格的实验验证,确保设计方案的可行性和有效性。
以上是关于微型行星齿轮传动设计方案的基本内容,希望对您的设计工作有所帮助。
齿轮设计方案

齿轮设计方案一、设计背景齿轮作为一种重要的传动元件,广泛应用于各种机械设备中。
为了满足不同工况下的使用需求,我们需要对齿轮进行精心设计。
本方案旨在提出一套高效、可靠、经济的齿轮设计方案,以提高设备的整体性能。
二、设计目标1. 确保齿轮传动平稳,降低噪音;2. 提高齿轮的承载能力,延长使用寿命;3. 优化齿轮结构,减轻重量,降低成本;三、设计原则1. 符合国家和行业标准,确保设计合理、安全;2. 充分考虑生产实际,提高生产效率;3. 注重产品可靠性,降低故障率;4. 兼顾美观与实用性,提高产品竞争力。
四、齿轮设计要点1. 齿轮材料选择根据工作环境和载荷特点,选用合适的齿轮材料,如优质碳钢、合金钢或铸铁等,确保齿轮的耐磨性和强度。
考虑齿轮的热处理工艺,以提高其硬度和使用寿命。
2. 齿轮参数设计精确计算齿轮的模数、齿数、压力角等基本参数,确保齿轮的传动性能。
合理设计齿轮的齿宽和齿高,以平衡强度、刚度与重量。
3. 齿轮结构设计采用斜齿或人字齿等结构,提高齿轮的平稳性和承载能力。
考虑齿轮的润滑和散热需求,设计合适的油槽和油孔。
五、设计方案详细说明1. 齿轮啮合设计通过优化齿轮的啮合线,减少啮合冲击,降低噪音。
确保齿轮啮合时的侧隙,避免因热膨胀导致的卡滞。
2. 齿轮强度计算对齿轮进行详细的强度计算,包括接触强度、弯曲强度和齿根强度,确保齿轮在复杂工况下的可靠性。
采用有限元分析方法,对齿轮进行强度校核,优化设计。
3. 齿轮加工工艺制定合理的齿轮加工工艺流程,确保齿轮的加工精度。
选择合适的加工设备和刀具,提高齿轮的加工质量和效率。
六、设计验证与优化1. 模型分析利用三维建模软件,建立齿轮模型,进行干涉检查和运动仿真。
分析齿轮在实际工作中的受力情况,为优化设计提供依据。
2. 实验验证制作齿轮样件,进行台架试验,验证齿轮的传动性能和可靠性。
根据试验结果,对齿轮设计方案进行优化调整。
3. 用户反馈收集用户在使用过程中的意见和建议,不断改进齿轮设计。
齿轮设计过程
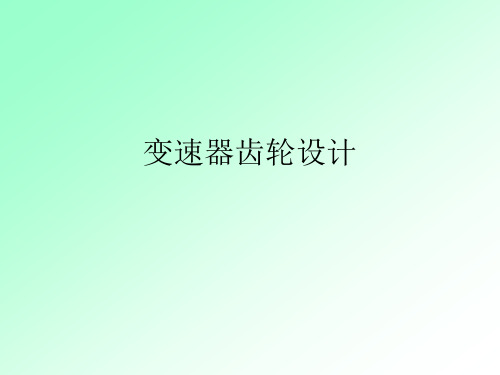
(二)根据接触强度计算确定中心距a或者小齿轮的直径d1, 根据弯曲强度计算确定模数。
1.渐开线圆柱齿轮受力分析及计算 (1)直齿受力分析
Fr Fn α
Ft
P
法向载荷Fn垂直于齿面,为计算方便Fn在节点P 处分解为两个互相垂直的分力,即圆周力Ft与Fr。
公式:
T1
9549
P n1
Ft
2T1 d1
T1——传递的转矩 d1——分度圆直径
α——啮合角
(2)斜齿受力分析
Fr Ft tan
Fn
Ft cos
Fr
αt
Ft
P
αn Fn Fr
F’ P
F’ Fa β
Ft P
如图所示:
圆周力 径向力
Ft
2T1 d1
,
F ' Ft ห้องสมุดไป่ตู้os
F'
F'
tan n
Ft tann cos
轴向力 Fa Ft tan
举例 名称:输出齿轮 材料:20CrMnTi 热处理技术条件:齿面渗碳淬火,渗碳层深度0.8~1.2mm,齿面硬度 HRC58~62,心部硬度HRC32~45。 加工工艺路线:下料→锻造→正火→加工齿形→局部镀铜(防渗)→渗 碳、淬火、低温回火→喷丸→磨齿。
热处理工艺:正火、渗碳、淬火及低温回火。
r1 r2
Fn1 FR1
β1
Fa1
1
2
Fa2
T
β2
FR2
Fn2
中间轴轴向力的平衡
由上图可知,欲使中间轴上两斜齿轮的轴向力平衡, 需满足下述条件: Fa1=Fn1tanβ1 Fa2=Fn2tanβ2
由于传递的转矩T=Fn1r1=Fn2r2,为使两轴向力平衡,必须满足
机床传动齿轮的工艺规程设计(大批量)
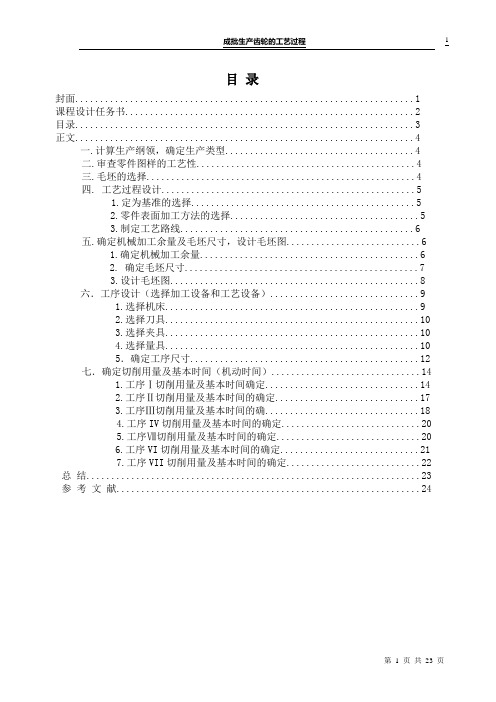
目录封面 (1)课程设计任务书 (2)目录 (3)正文 (4)一.计算生产纲领,确定生产类型 (4)二.审查零件图样的工艺性 (4)三.毛坯的选择 (4)四. 工艺过程设计 (5)1.定为基准的选择 (5)2.零件表面加工方法的选择 (5)3.制定工艺路线 (6)五.确定机械加工余量及毛坯尺寸,设计毛坯图 (6)1.确定机械加工余量 (6)2. 确定毛坯尺寸 (7)3.设计毛坯图 (8)六.工序设计(选择加工设备和工艺设备) (9)1.选择机床 (9)2.选择刀具 (10)3.选择夹具 (10)4.选择量具 (10)5.确定工序尺寸 (12)七.确定切削用量及基本时间(机动时间) (14)1.工序Ⅰ切削用量及基本时间确定 (14)2.工序Ⅱ切削用量及基本时间的确定 (17)3.工序Ⅲ切削用量及基本时间的确 (18)4.工序IV切削用量及基本时间的确定 (20)5.工序Ⅶ切削用量及基本时间的确定 (20)6.工序VI切削用量及基本时间的确定 (21)7.工序VII切削用量及基本时间的确定 (22)总结 (23)参考文献 (24)一.计算生产纲领,确定生产类型:某产品上的一个齿轮零件。
该产品产量为10000件,某生产备品率为10%,机械加工废品率为1%,现制定该齿轮零件的杰械加工工艺规程:N=Qn(1+a%+b%)=10000*1*(1+10%+1%)件/年=11100件/年式中:Q——产品的年产量;n——每台产品中该零件的数量;a,b——零件生产备品率(%),废品率(%)。
齿轮零件的年产量为11100件/年,现已知该产品属于轻型机械。
根据≤机械制造基础≥表1——1生产类型与生产纲领的关系,可确定其生产类型为大批生产。
二.审查零件图样的工艺性:齿轮零件图样的视图正确完整。
尺寸,公差及技术要求齐全。
本零件个表面的加工并不困难,只需要注意其基准孔 95.20其表面粗糙度要求为Ra=0.8µm,以及所需要加工的齿轮面的表面粗糙度要求也为Ra=0.8µm 。
斜齿圆柱齿轮传动与加工工艺

1斜齿圆柱齿轮传动1.1齿面形成研究直齿圆柱齿轮时知道,两轮的齿廓面沿一条平行于齿轮轴的直线KK ′相接触,KK ′与发生面在基圆柱上的切线NN ′平行。
当发生面沿基圆柱做纯滚动时,直线KK ′在空间形成的轨迹就是一个渐开面,即直齿轮的齿廓曲面,如图1示。
图1 直齿齿轮渐开线的形成斜齿圆柱齿轮齿面的形成原理和直齿圆柱齿轮的情况相似,所不同的是发生面上的直线KK ′与直线NN ′不平行,即与齿轮轴线不平行.面是与基圆杆母线NN ′成一夹角βb 。
故当发生面沿基圆柱作纯滚动时,直线KK ′上的每一点都依次从基圆柱面的接触点开始展成一条渐开线,而直线KK ′上各点所展成的渐开线的集合就是斜齿轮的齿面。
由此可知,斜齿轮齿廓曲面与齿轮瑞面(与基圆柱轴线垂直的平面)上的交线(即端面上的齿廓曲线)仍是渐开线。
而且由于这些渐开线有相同的基圆柱,所以它们的形状都是一样的,只是展成的起始点不同面己,即起始点依次处于螺旋线K 0K 0′上的各点。
所以其齿面为渐开螺旋面,如图2示。
由此可见.斜齿圆柱齿轮的端面齿廓曲线仍为渐开线。
可将直齿圆柱齿轮看成斜齿圆柱齿轮的一个特例。
从端面看,一对渐开线斜齿轮传动就相当于一对渐开线直齿轮传动,所以它也满足齿廓啮合基本定律。
图2 斜齿齿轮的渐开线形成斜齿圆柱齿轮传动和直齿圆柱齿轮传动一样,仅限于传递两平行轴之间的运动。
如果两斜齿轮分度圆上的螺旋角不是大小相等且方向相反,则这样的一对斜齿轮还可以用来传递既不平行又不相交的两轴之间的运动。
为了便于区别,把用于传递两平行轴之间的运动,称为斜齿圆柱齿轮传动;用于传递两交锗轴之间的运动,称为交错轴斜齿轮传动。
斜齿圆柱齿轮传动中的两轮齿啮合为线接触,而交错轴斜齿轮传动中的两轮齿啮合为点接触。
一对斜齿圆柱齿轮啮合时,齿面上的接触线是由一个齿轮的一端齿顶(或齿根)处开始逐渐由短变长,再由长变短,至另一端的齿根(或齿顶)处终止。
这样就减少了传动时的冲击和噪声,提高了传动的平稳性,故斜齿轮适用于重载、高速传动。
齿轮传动的设计步骤
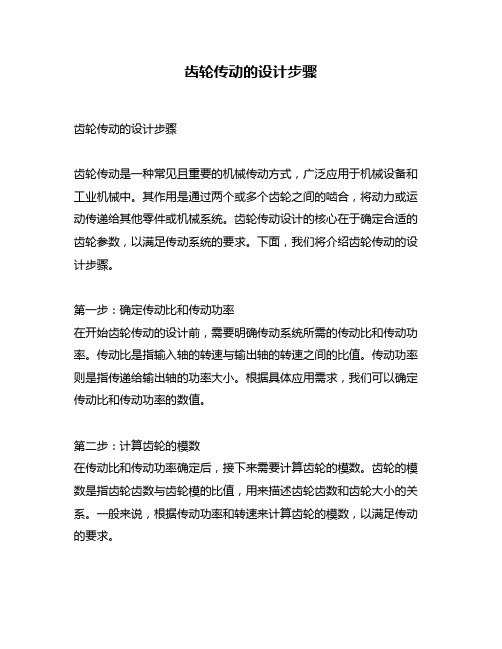
齿轮传动的设计步骤齿轮传动的设计步骤齿轮传动是一种常见且重要的机械传动方式,广泛应用于机械设备和工业机械中。
其作用是通过两个或多个齿轮之间的啮合,将动力或运动传递给其他零件或机械系统。
齿轮传动设计的核心在于确定合适的齿轮参数,以满足传动系统的要求。
下面,我们将介绍齿轮传动的设计步骤。
第一步:确定传动比和传动功率在开始齿轮传动的设计前,需要明确传动系统所需的传动比和传动功率。
传动比是指输入轴的转速与输出轴的转速之间的比值。
传动功率则是指传递给输出轴的功率大小。
根据具体应用需求,我们可以确定传动比和传动功率的数值。
第二步:计算齿轮的模数在传动比和传动功率确定后,接下来需要计算齿轮的模数。
齿轮的模数是指齿轮齿数与齿轮模的比值,用来描述齿轮齿数和齿轮大小的关系。
一般来说,根据传动功率和转速来计算齿轮的模数,以满足传动的要求。
第三步:选择合适的齿轮材料齿轮传动的设计过程中,选择合适的齿轮材料十分重要。
齿轮材料应具有良好的耐磨性、耐蚀性、强度和刚度,以确保传动系统的可靠性和寿命。
常用的齿轮材料包括钢、铸铁、铜合金等。
根据具体的应用需求和工作环境选择合适的齿轮材料。
第四步:确定齿轮的齿数和齿形根据传动比和齿轮模数,确定齿轮的齿数。
齿数的确定需要考虑到齿轮啮合条件的要求,如齿面接触、齿轮强度等。
齿形的设计也是十分重要的一步,合理的齿形设计可以提高齿轮传动的效率和传动能力。
常见的齿形有直齿、斜齿、渐开线齿等。
第五步:计算齿轮的几何参数在确定齿数和齿形后,需要计算齿轮的几何参数。
包括齿轮的分度圆直径、齿顶圆直径、齿根圆直径、齿隙等。
这些参数直接影响着齿轮的传动特性,如传动比、啮合条件等。
通过计算这些几何参数,可以确保齿轮传动的可靠性和稳定性。
第六步:计算齿轮的强度在齿轮传动设计的过程中,还需要计算齿轮的强度。
齿轮的强度是指齿轮在工作过程中能够承受的最大载荷。
通过计算齿轮的强度,可以判断齿轮是否能够满足工作条件下的要求。
- 1、下载文档前请自行甄别文档内容的完整性,平台不提供额外的编辑、内容补充、找答案等附加服务。
- 2、"仅部分预览"的文档,不可在线预览部分如存在完整性等问题,可反馈申请退款(可完整预览的文档不适用该条件!)。
- 3、如文档侵犯您的权益,请联系客服反馈,我们会尽快为您处理(人工客服工作时间:9:00-18:30)。
河南质量工程职业学院毕业设计(论文)题目传动齿轮工艺设计系别机电工程系专业机电一体化技术班级2011机电3班学生姓名杨艺楠学号0308110322指导教师王西建定稿日期2014 年 4 月 10 日河南质量工程职业学院毕业设计(论文)任务书班级设备三班学生姓名杨艺楠指导教师王西建设计(论文)题目传动齿轮工艺设计主要研究内容传动齿轮,它是齿轮的一个主要一种,其功用是传递运动和运动方向,以适应传动机构运动的需要。
主要技术指标或研究目标同轴孔φ35H7,φ49H7和同轴外圆φ92.55k7, φ66的同轴度、径向圆跳动公差等级为8~9级,表面粗糙度为Ra≤1.6μm.。
加工时最好在一次装夹下将两孔或两外圆同时加工。
(2)与基准孔有垂直度要求的端面,其端面圆跳动公差等级为7级,表面粗糙度为Ra≤3.2μm。
工艺过程安排时应注意保证其位置精度。
(3)距中心平面74.5mm的两侧面,表面粗糙度为Ra≤6.3μm。
(4)φ35孔的尺寸精度要保证,孔轴线的同轴度共差等级为9级及两孔公共轴线对基准孔(A1-A2)位置度公差值为0.06μm,应予以重视。
基本要求由各加工方法的经济精度及一般机床所能达到的精度可知,该零件没有很难加工的表面,各表面的技术要求采用常规加工工艺均可达到。
但是在加工过程中应注意齿轮端面的加工主要参考资料及文献[1] 吴雄彪.机械制造技术课程设计.杭州:浙江大学出版社,2005[2] 苏建修.机械制造基础.北京:机械工业出版社,2001[3]许德珠.工程材料.北京:高等教育出版社,2001[4] 东北重型机械学院、洛阳工学院、第一汽车制造厂职工大学编.机床夹具设计手册.上海:上海科学技术出版社,1990[5] 艾兴,肖诗纲.切削用量简明手册.北京:机械工业出版社,1993传动齿轮工艺设计摘要:随着科技技术的不断进步,生产都向着自动化、专业化和大批量化的方向发展。
这就要求企业的生产在体现人性化的基础上降低工人的生产强度和提高工人的生产效率,降低企业的生产成本。
现代的生产和应用设备多数都采用机电一体化、数字控制技术和自动化的控制模式。
在这种要求下齿轮零件越发体现出其广阔的应用领域和市场前景。
特别是近年来与微电子、计算机技术相结合后,使齿轮零件进入了一个新的发展阶段。
在齿轮零部件是最重要部分,因需求的增加,所以生产也步入大批量化和自动化。
为适应机械设备对齿轮加工的要求,对齿轮加工要求和技术领域的拓展还需要不断的更新与改进。
关键词:工艺设计齿轮零件齿轮传动Abstract:Preface technology with the progress toward the production of automation, specialization and a large number of quantization direction. This requires the production of the human embodiment of the workers on the basis of reducing the intensity of production and enhance worker productivity. lower their production costs. Modern production and application of the majority of equipment used electromechanical integration, digital control technology and automation control mode. In such a request Gear institutions increasingly reflects its broad application areas and market prospects. Especially in recent years and microelectronics, computer technology integration, make technology gear drive has entered a new stage of development. Gear drive gear parts is the most important part, Gear by the relative movement of the drive to promote change in direction. Gear result of the design requirements are relatively strict, in order to adapt to the type of gear increasing and updating. Because of the increase in demand, production has entered a large number of quantitative andautomation. To meet the mechanical equipment to gear machining requirements, Gear on the design requirements and technical fields is also expanding the need to constantly update and improve.Keywords: Gear start Gear Gear drive、目录1、基本任务和设计要求 (6)1.1、基本任务 (6)1.2、设计要求 (6)2、毕业设计工艺课程设计的方法和步骤 (7)2.1、生产纲领的计算与生产类型的确定 (7)2.2分析零件图 (7)2.3确定生产类型 (9)2.4确定毛坯 (9)2.5机械加工工艺过程设计 (9)2.6确定各工序切削用量 (12)2.7加工工序表 (12)3、夹具设计 (13)3.4、夹具设计图 (15)致谢 (16)1、基本任务和设计要求1.1、基本任务1.1.1、工艺设计的基本任务(1)绘制零件工作图一张(2)绘制毛坯-零件合图一张(3)编制机械加工工艺规程卡片一套(4)编写设计说明书一份1.1.2、夹具设计的基本任务(1)收集资料,为夹具设计做好准备(2)绘制草图,进行必要的理论计算和分析以及夹具的结构方案(3)绘制总图和主要非标准件零件图,编写设计说明书(4)编制夹具的使用说明或技术要求1.2、设计要求1.2.1、工艺设计的设计要求(1)保证零件加工质量,达到图纸的技术要求(2)在保证加工质量的前提下,尽可能提高生产效率(3)要尽量减轻工人的劳动强度,生产安全(4)在立足企业的前提下,尽可能采用国内技术和装备(5)工艺规程应正确.清晰,规范化,标准化的要求1.2.2、夹具设计的设计要求(1)保证工件的加工精度(2)提高生产效率(3)工艺性好(4)使用性好(5)经济性好2、毕业设计工艺课程设计的方法和步骤2.1、生产纲领的计算与生产类型的确定生产纲领的大小对生产组织和零件加工工艺过程起着重要的作用.它决定了各工序所需专业化和自动化的程度以及所选用的工艺方法和工艺装备.零件生产纲领可按下式计算.N=Qn(1+a%)(1+b%)式中:N-----零件的生产纲领(件/台)Q-----产品的年产量(台/年)n-----每台产品中,该零件的数量(件/台)a%----零件的备品率b% ---零件的平均废品率2.2分析零件图1、零件的作用传动齿轮,,它是齿轮的一个主要一种,其功用是传递运动和运动方向,以适应传动机构运动的需要。
2、零件的工艺分析传动齿轮零件如图所示,该零件主要加工表面及技术要求分析如下。
(1)同轴孔φ35H7,φ49H7和同轴外圆φ92.55k7, φ66的同轴度、径向圆跳动公差等级为8~9级,表面粗糙度为R≤1.6μm.。
加工时最好在一次装夹下将两孔或两a外圆同时加工。
(2)与基准孔有垂直度要求的端面,其端面圆跳动公差等级为7级,表面粗糙度为Ra≤3.2μm。
工艺过程安排时应注意保证其位置精度。
(3)距中心平面74.5mm的两侧面,表面粗糙度为Ra≤6.3μm。
(4)φ35孔的尺寸精度要保证,但孔轴线的同轴度共差等级为9级及两孔公共轴线对基准孔(A1-A2)位置度公差值为0.06μm,应予以重视。
(5)各外圆位置度公差为,齿轮轮齿轮的跳动公差要保证。
(6)该零件选用材料为20CrMnTi,这种材料具有低碳合金钢的特性,切削性能和工艺性均较好。
由各加工方法的经济精度及一般机床所能达到的精度可知,该零件没有很难加工的表面,各表面的技术要求采用常规加工工艺均可达到。
但是在加工过程中应注意齿轮端面的加工。
3、零件图4、热处理工序的安排热处理工序主要用来改善材料的性能及消除应力。
热处理的方法.次数和在工艺路线中的位置,应根据零件材料和热处理的目的而定。
热处理安排为毛坯→粗加工(粗车)→半精加工(半精)→精加工(精车)↑(去应力退火或者时效去应力)齿轮加工工艺过程:毛坯的选择---热处理1---齿坯加工---齿面加工---齿端的加工---热处理2---精基准的修正2.3确定生产类型已知零件的年生产纲领为10000件,零件质量约为3.6kg,查表1-1可知其生产类型为大批量生产,初步确定工艺安排的基本思路为:加工过程划分阶段;工序适当集中;加工设备以通用设备为主;大量采用专用工装。
这样安排,生产准备工作投资较少,生产效率较高,且转产容易。
2.4确定毛坯1、确定毛坯种类根据零件材料确定毛坯为锻件。
根据其桔构形状、尺寸大小、生产类型和材料性能,毛坯的铸造方法选用砂型机器造型。
2、确定锻件及形状根据表1-6取加工余量等级为MA-G级。
根据表1-7确定各表面的锻件机械加工余量(查表前必须先选择定位基准,以便确定基本尺寸)。
2.5机械加工工艺过程设计1、选择定位基准(1)选择粗基准选择内孔和端面定位元件.先加工外圆,按“基准先行”的原则,采用外圆及端面为粗基准先加工内孔。
(2)选择精基准为了保证圆跳动要求,各主要圆柱表面均互为基准加工,并尽量遵守“基准重合”的原则。
其余表面加工采用“一孔一端面的定位方式,即以端面及φ35H7内孔为精基准。
这样,基准统一,定位稳定,夹具结构及操作也较简单。
但必须提高这个内孔的精度,以保证定位精度。
2、拟定工艺过程(1)选择表面加工方法查表1-19~表1-21,根据各表面加工要求和各种加工方法所能达到的经济精度,选技零件主要表面的加工方法与方案如下:φ35H7内孔加工:粗车)—半精车—精车。