基于三维应变渐进损伤准则的复合材料层合板大开孔压缩损伤研究
复合材料层合板渐进损伤分析与试验验证
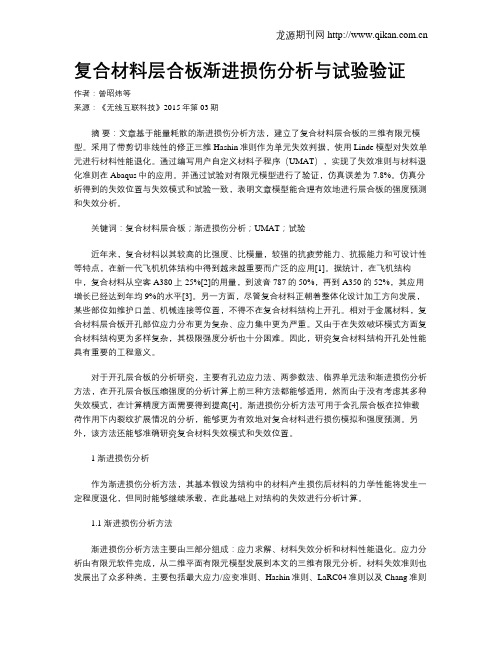
复合材料层合板渐进损伤分析与试验验证作者:曾昭炜等来源:《无线互联科技》2015年第03期摘要:文章基于能量耗散的渐进损伤分析方法,建立了复合材料层合板的三维有限元模型。
采用了带剪切非线性的修正三维Hashin准则作为单元失效判据,使用Linde模型对失效单元进行材料性能退化。
通过编写用户自定义材料子程序(UMAT),实现了失效准则与材料退化准则在Abaqus中的应用。
并通过试验对有限元模型进行了验证,仿真误差为7.8%。
仿真分析得到的失效位置与失效模式和试验一致,表明文章模型能合理有效地进行层合板的强度预测和失效分析。
关键词:复合材料层合板;渐进损伤分析;UMAT;试验近年来,复合材料以其较高的比强度、比模量,较强的抗疲劳能力、抗振能力和可设计性等特点,在新一代飞机机体结构中得到越来越重要而广泛的应用[1]。
据统计,在飞机结构中,复合材料从空客A380上25%[2]的用量,到波音787的50%,再到A350的52%,其应用增长已经达到年均9%的水平[3]。
另一方面,尽管复合材料正朝着整体化设计加工方向发展,某些部位如维护口盖、机械连接等位置,不得不在复合材料结构上开孔。
相对于金属材料,复合材料层合板开孔部位应力分布更为复杂、应力集中更为严重。
又由于在失效破坏模式方面复合材料结构更为多样复杂,其极限强度分析也十分困难。
因此,研究复合材料结构开孔处性能具有重要的工程意义。
对于开孔层合板的分析研究,主要有孔边应力法、两参数法、临界单元法和渐进损伤分析方法,在开孔层合板压缩强度的分析计算上前三种方法都能够适用,然而由于没有考虑其多种失效模式,在计算精度方面需要得到提高[4]。
渐进损伤分析方法可用于含孔层合板在拉伸载荷作用下内裂纹扩展情况的分析,能够更为有效地对复合材料进行损伤模拟和强度预测。
另外,该方法还能够准确研究复合材料失效模式和失效位置。
1 渐进损伤分析作为渐进损伤分析方法,其基本假设为结构中的材料产生损伤后材料的力学性能将发生一定程度退化,但同时能够继续承载,在此基础上对结构的失效进行分析计算。
基于修正Linde模型的复材层板的损伤模拟

收 稿 日期 : 2 0 1 2—0 9—2 7 ;修 回 日期 : 2 0 1 2—1 2— 0 4
基 金 项 目 :国 家 自然 科 学 基 金 ( 1 1 0 7 2 2 0 2 ) 和爆 炸 科 学 与 技术 国 家重 点 实验 室 基 金 ( K F J J 1 2—2 0 M) 资助项 目 作 者 简 介 :赵 士 洋 ( 1 9 8 6一) , 男, 西安 , 博士生 , 主要从事复合材料损伤研究 , E - ma i l : 8 4 0 2 0 8 9 2 7 @q q . c o n r
研究 带损 伤 的复合 材料 层合 板 的强 度 问题 , 目前 主要通 过 渐进损 伤 分析方 法 . 但多数 在 损伤模 拟 过程 中
依然 采用 材料 性能 突变 的模 型 , 在有 限元 隐式 求解 器 S t a n d a r d中导致 收敛 困难 . 本文 针对 这一数 值模 拟 过程 的典 型 问题 , 采用 连续 损伤 力学 思想 , 通过 L i n d e等 ¨ 引提 出 的应 变 失 效 准则 对 含 损 伤 的 复合 材 料 层 合板 进
的差 别 . C h a n g 等
结合 损 伤 机 理 , 通 过 有 限元 模 拟 二 维 复合 材 料 结 构 的损 伤 过 程. 采用 Y a ma d a — S u n准 , 并且 扩展 到模 拟编 织复 合材 料 的强度 问题 .
则 和 C h a n g . C h a n g准则 模 拟 了带孔 层合 板 的破 坏过 程 , 与试验 结果 较为 接 近. 对含 孔 的层合 板 的应 力集 中问题 , 研 究 人员 提 出了三 维数 值模 型 的材料 损 伤准 则
基于CDM的复合材料层合板三维非线性渐进损伤分析
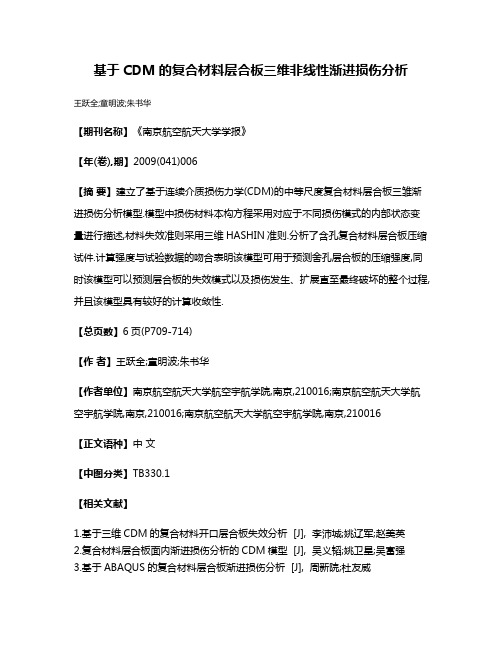
基于CDM的复合材料层合板三维非线性渐进损伤分析
王跃全;童明波;朱书华
【期刊名称】《南京航空航天大学学报》
【年(卷),期】2009(041)006
【摘要】建立了基于连续介质损伤力学(CDM)的中等尺度复合材料层合板三雏渐进损伤分析模型.模型中损伤材料本构方程采用对应于不同损伤模式的内部状态变量进行描述,材料失效准则采用三维HASHIN准则.分析了含孔复合材料层合板压缩试件.计算强度与试验数据的吻合表明该模型可用于预测舍孔层合板的压缩强度,同时该模型可以预测层合板的失效模式以及损伤发生、扩展直至最终破坏的整个过程,并且该模型具有较好的计算收敛性.
【总页数】6页(P709-714)
【作者】王跃全;童明波;朱书华
【作者单位】南京航空航天大学航空宇航学院,南京,210016;南京航空航天大学航空宇航学院,南京,210016;南京航空航天大学航空宇航学院,南京,210016
【正文语种】中文
【中图分类】TB330.1
【相关文献】
1.基于三维CDM的复合材料开口层合板失效分析 [J], 李沛城;姚辽军;赵美英
2.复合材料层合板面内渐进损伤分析的CDM模型 [J], 吴义韬;姚卫星;吴富强
3.基于ABAQUS的复合材料层合板渐进损伤分析 [J], 周新院;杜友威
4.复合材料层合板多尺度交互渐进损伤分析 [J], 田志强;李彦斌;张培伟;费庆国;钱意彦
5.复合材料层合板T型连接结构的渐进损伤分析 [J], 李家春;王德鑫
因版权原因,仅展示原文概要,查看原文内容请购买。
基于ABAQUS的复合材料结构渐进损伤方法研究_丁京龙
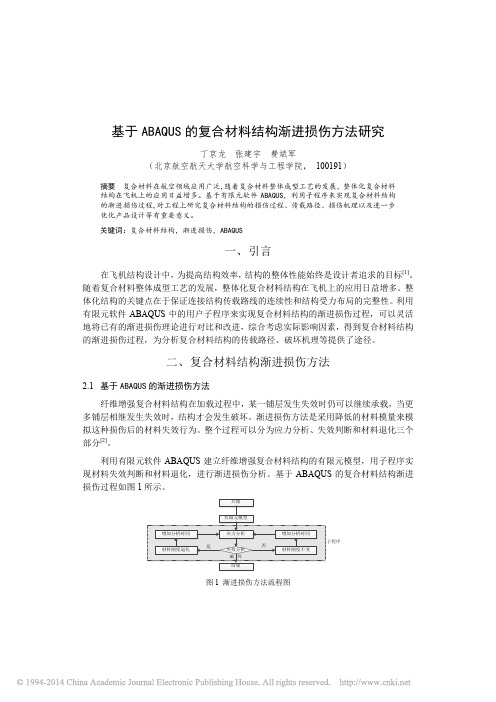
基于ABAQUS的复合材料结构渐进损伤方法研究丁京龙张建宇费斌军(北京航空航天大学航空科学与工程学院,100191)摘要复合材料在航空领域应用广泛,随着复合材料整体成型工艺的发展,整体化复合材料结构在飞机上的应用日益增多。
基于有限元软件ABAQUS,利用子程序来实现复合材料结构的渐进损伤过程,对工程上研究复合材料结构的损伤过程、传载路径、损伤机理以及进一步优化产品设计等有重要意义。
关键词:复合材料结构,渐进损伤,ABAQUS一、引言在飞机结构设计中,为提高结构效率,结构的整体性能始终是设计者追求的目标[1]。
随着复合材料整体成型工艺的发展,整体化复合材料结构在飞机上的应用日益增多。
整体化结构的关键点在于保证连接结构传载路线的连续性和结构受力布局的完整性。
利用有限元软件ABAQUS中的用户子程序来实现复合材料结构的渐进损伤过程,可以灵活地将已有的渐进损伤理论进行对比和改进,综合考虑实际影响因素,得到复合材料结构的渐进损伤过程,为分析复合材料结构的传载路径、破坏机理等提供了途径。
二、复合材料结构渐进损伤方法2.1 基于ABAQUS的渐进损伤方法纤维增强复合材料结构在加载过程中,某一铺层发生失效时仍可以继续承载,当更多铺层相继发生失效时,结构才会发生破坏。
渐进损伤方法是采用降低的材料模量来模拟这种损伤后的材料失效行为。
整个过程可以分为应力分析、失效判断和材料退化三个部分[2]。
利用有限元软件ABAQUS建立纤维增强复合材料结构的有限元模型,用子程序实现材料失效判断和材料退化,进行渐进损伤分析。
基于ABAQUS的复合材料结构渐进损伤过程如图1所示。
图1 渐进损伤方法流程图2.2 渐进损伤方法在分析复合材料π胶接接头中的应用本文对复合材料π胶接接头的拉伸渐进损伤过程进行了模拟,有限元模型如图2所示。
采用位移加载的形式,加载过程中位移载荷曲线如图3所示。
浅色部分表示π胶接接头的失效部位,可以看出π胶接接头的初始损伤发生在接头拐角处外侧铺层,然后由拐角处外侧铺层通过填料逐步向内部铺层扩展,随着损伤范围的逐渐扩大最终导致π胶接接头失效,π胶接接头的失效过程如图4所示。
基于三维应变渐进损伤准则的复合材料层合板大开孔压缩损伤研究
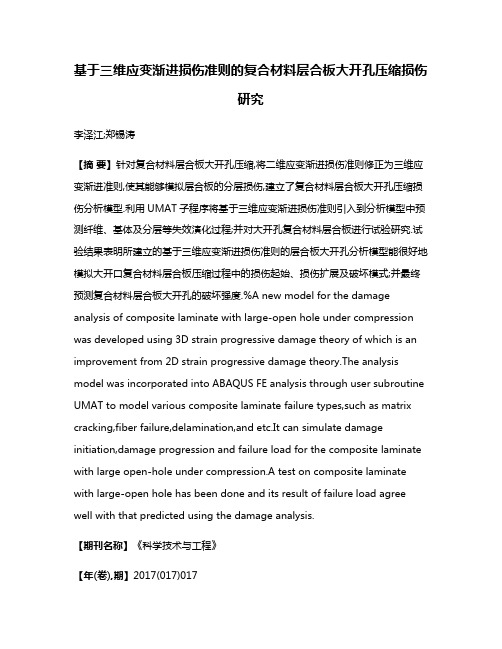
基于三维应变渐进损伤准则的复合材料层合板大开孔压缩损伤研究李泽江;郑锡涛【摘要】针对复合材料层合板大开孔压缩,将二维应变渐进损伤准则修正为三维应变渐进准则,使其能够模拟层合板的分层损伤,建立了复合材料层合板大开孔压缩损伤分析模型.利用UMAT子程序将基于三维应变渐进损伤准则引入到分析模型中预测纤维、基体及分层等失效演化过程;并对大开孔复合材料层合板进行试验研究.试验结果表明所建立的基于三维应变渐进损伤准则的层合板大开孔分析模型能很好地模拟大开口复合材料层合板压缩过程中的损伤起始、损伤扩展及破坏模式;并最终预测复合材料层合板大开孔的破坏强度.%A new model for the damage analysis of composite laminate with large-open hole under compression was developed using 3D strain progressive damage theory of which is an improvement from 2D strain progressive damage theory.The analysis model was incorporated into ABAQUS FE analysis through user subroutine UMAT to model various composite laminate failure types,such as matrix cracking,fiber failure,delamination,and etc.It can simulate damage initiation,damage progression and failure load for the composite laminate with large open-hole under compression.A test on composite laminate with large-open hole has been done and its result of failure load agree well with that predicted using the damage analysis.【期刊名称】《科学技术与工程》【年(卷),期】2017(017)017【总页数】6页(P66-71)【关键词】复合材料层合板;大开孔压缩;渐进损伤;UMAT;损伤分析【作者】李泽江;郑锡涛【作者单位】上海飞机设计研究院强度设计研究部,上海201210;西北工业大学航空学院,西安710072【正文语种】中文【中图分类】TB330.1;V257以碳纤维增强的先进复合材料因其高比模量、高比强度、耐腐蚀及热膨胀系数低等优点成为了航空航天领域广泛应用的材料之一,与传统金属材料相比,其结构减重可以达到20%~30%[1]。
基于损伤指数的三维编织复合材料结构损伤评估

基 于 损 伤 指 数 的 三 维 编 织 复 合 材 料 结 构 损 伤 评 估
万 振 凯 ,贡 丽 英 ,万 莉
( 1 .天 津 工 业 大 学 信 息 化 中心 ,天 津 3 0 0 3 8 7 ; 2 .天 津 科 技 大 学 计 算 机 科 学 与 信 息 ห้องสมุดไป่ตู้ 2 程学 院 , 天津 3 0 0 2 2 2 )
c o m p o s i t e m a t e r i a l w a s s t u d i e d b y u s i n g p r i n c i p a l c o m p o n e n t a n a l y s i s ( P C A) ,a n d s t a t i s t i c a l m e t h o d s o f a n d Q .T h e m e t h o d o f P C A w a s u s e d t o p r o c e s s t h e d a ma g e i n f o r m a t i o n o f i n t e l l i g e n t 3 - D b r a i d e d
中 图分 类 号 : T S 1 0 1 . 2 文献标志码 : A
S t r u c t ur a l da ma g e e v a l ua t i o n o f t h r e e - d i me ns i o n a l b r a i de d c o mp o s i t e b a s e d o n da ma g e i n de x
u s e d a s s t r e t c h s e n s o r s t o c o ns t r u c t i n t e l l i g e n t c o mp o s i t e s . Th e d a ma g e o f t h r e e — d i me n s i o n a l b r a i d e d
三维渐进损伤的复合材料层合板低速冲击模型

三维渐进损伤的复合材料层合板低速冲击模型郭卫【摘要】为了有效反映复合材料层合板面内和层间的非线性损伤,建立了一个新型的损伤模型,该模型基于三维实体单元和内聚力单元可以有效分析复合材料层合板在低速冲击作用下的层内和层间非线性失效行为。
对于复合材料层合板面内损伤,以改进的Hashin失效准则作为起始损伤准则,提出了一种基于能量释放率的损伤变量指数渐进演化模型,既描述了复合材料损伤的渐进失效过程,又避免了材料刚度突然下降导致刚度矩阵奇异的不足,同时引入特征长度来降低结果对网格的依赖性,最终建立了单层板的渐进损伤非线性分析模型;针对层合板的层间损伤,采用内聚力单元来模拟,通过结合传统的应力失效准则和断裂力学中的能量释放率准则定义了界面损伤演化规律。
该损伤模型通过商用有限元软件ABAQUS/Explicit 的用户子程序VUMAT实现,并使用该模型对碳纤维增强环氧树脂复合材料层合板在横向低速冲击作用下的损伤和变形行为进行预测分析。
数值仿真的结果与试验结果进行了比较,吻合良好,验证了该模型的有效性。
%In order to effectively describe the progressively intralaminar and interlaminar damage for composite laminates , a three dimensional progressive damage model for composite laminates used for low-velocity impact is presented in this paper .Being applied to three di-mensional solid elements and cohesive elements , this nonlinear damage model can be used to analyze the dynamic performance of composite structure and its failure behavior .For the in-tralaminar damage , as a function of energy release rate , this damage model in an exponential function can describe progressive development of the damage;for interlaminar damage , dam-age evolutionwas described by the framework of the continuum mechanics through cohesive elements.Through coding user subroutine VUMAT of finite element software ABAQUS /ex-plicit, and applied the model to an example ,carbon fiber reinforced epoxy composite lami-nates under low velocity impact , the prediction for damage and deformation were good agree-ment with the experimental results .【期刊名称】《哈尔滨商业大学学报(自然科学版)》【年(卷),期】2014(000)004【总页数】6页(P455-460)【关键词】复合材料层合板;渐进损伤;分层损伤;低速冲击【作者】郭卫【作者单位】上海飞机设计研究院,上海201210【正文语种】中文【中图分类】TB332复合材料是由两种或两种以上不同性质或不同形态的原材料,通过复合工艺组合而成的一种材料,它既保持了原组分材料的主要特点,又具备了原组分材料所没有的新的性能.但由于其沿厚度方向的性能不连续、层间强度较低,使得其低速冲击损伤成为工程实际中十分关切并得到广泛研究的问题.在冲击载荷作用下,损伤破坏模式主要表现为纤维断裂、基体开裂、层与层之间的分层损伤等,其过程很复杂,没有解析解, 因而使用有限元法求解越来越显示出其优势.为了预测复合材料层合板在低速冲击载荷下的损伤扩展情况,虽然很多学者都对其进行过探索性试验,并且提出了很多分析模型来预测层合板的损伤情况.但是因为冲击响应的分析过程比较复杂,因而采用何种损伤和演化准则仍然没有统一的认识.Tan[1] 等的渐进损伤分析模型中采用基于壳单元理论进行应力求解,但是却无法较好的反映层合板三维效应和铺层之间的相互作用.Chang[2-3]等在研究T300/976复合材料层合板强度时,根据不同的失效模式将相应的材料弹性常数退化为零,认为层合板一旦发生失效就不可以继续承载,明显与实际不符,因而预测的强度偏小.Camanho[4]等在分析T300/914复合材料层合板接头拉伸强度时,将Tan[1]的参数退化方式扩展到三维,认为材料发生损伤后,其弹性常数退化到一定程度,因此退化系数需要大量的试验进行测定,另外由于层合板的弹性系数突然降低同时会造成刚度矩阵的奇异,很容易发生计算无法进行.为了解决这些问题,张彦[5-6]等使用ABAQUS建立了以基于应变Hashin 失效准则基础上的层内损伤,并通过结合传统的应力失效准则定义了损伤演化规律,但是由于文中提出的损伤演化规律没有考虑到能量释放率和损伤力学对于网格的依赖影响,因而对于预测的分层面积和实验值相差很大.本文基于有限元软件ABAQUS对复合材料层合板低速冲击,建立了一个有效反映复合材料层合板面内和层间的非线性损伤模型,该模型基于三维实体单元和内聚力单元可以有效分析层合板层内和层间失效行为.对于复合材料层合板面内损伤, 以改进的Hashin失效准则作为起始损伤准则,提出了一种基于能量释放率的损伤变量指数渐进演化模型,既描述了复合材料损伤的渐进失效过程,又避免了材料刚度突然下降导致刚度矩阵奇异的不足,同时引入特征长度来降低网格的依赖性,最终建立了单层板的渐进损伤非线性分析模型.该损伤模型通过商用有限元软件ABAQUS/Explicit 的用户子程序VUMAT实现,并使用该模型对复合材料层合板在横向低速冲击作用下的损伤和变形行为进行预测分析,数值仿真的结果与试验结果进行了比较,吻合良好, 验证了该模型的有效性.1 复合材料三维渐进损伤模型1.1 层合板面内渐进损伤模型本文中考虑的失效模式包括纤维断裂、纤维挤压、基体开裂和基体挤裂4种模式,每种失效模式可以看作是在结构损伤过程中当一种特定的应力分量组合达到特定值时的一种明显状态,因此本文采用被众多研究人员普遍认可的三维Hashin失效准则[7],其具体形式:1) 纤维断裂(1)2) 纤维挤压(2)3) 基体开裂(3)4) 基体挤裂(4)其中:σi为单元的正应力,σij为单元的剪应力,Xt、Xc、Yt、Yc、S12、S23、S13分别为轴向拉伸、轴向压缩、横向拉伸、横向压缩和各方向剪切强度.只要单元内的各应力分量满足上述一个式子,即认为发生了该式子对应的破坏的模式.当复合材料积分点满足失效准则时,其材料积分点应力和刚度开始发生退化,进行应力更新.本文引入连续损伤变量来预测复合材料结构内部损伤的产生和演化,特征值dft表示纤维断裂,dfc表示纤维挤压,dmt表示基体开裂,dmc表示基体挤裂,这些损伤变量的定义域为[0,1],当d=0时,表示没有损伤产生,当d=1时,表示材料完全破坏失效了.使用上面四个损伤变量定义全局损伤,对于纤维损伤使用df来表征,对于基体损伤使用dm来表征:df=1-(1-dft)(1-dfc)(5)dm=1-(1-dmt)(1-dmc)(6)当材料积分点满足失效准则时,其刚度矩阵可以根据下面方程计算:(7)(8)(9)(10)(11)(12)(13)(14)(15)当复合材料发生损伤,对于纤维增强复合材料损伤累积引起的材料非线性,本文提出使用非线性指数函数定义损伤演化规律的方法,使材料性能逐渐下降,该方法可以避免刚度矩阵退化过程中矩阵的奇异性,又可以通过控制能量释放率保证材料刚度的迅速折减,达到积分点损伤破坏的目的,最终保证计算的顺利有效进行.(16)(17)(18)(19)其中:Gft、Gfc、Gmt和Gmc材料临界断裂能,Lc是单元的特征长度,本文参考ABAQUS,在损伤材料点的应变软化区域引入单元特征长度来降低其对于网格的敏感性,减小其对于网格的依赖特性.1.2 层合板层间渐进损伤模型大量试验表明,层合板的分层损伤在铺设角度不同的两相邻子层之间的界面处产生并扩展,因此把内聚力单元引入到可能发生分层的位置可以有效的预测分层损伤的产生、损伤扩展直至最后分层的发生.定义内聚力单元的应力分量为t1、t2、t3,ε为求的内聚力单元名义应变,可以得到本文所使用的内聚力单元本构关系如下:(20)其中:kn、ks、kt分别是内聚力单元法向刚度和切向刚度.Alfano[8]对双线性本构、梯形本构、指数本构、和线性抛物线内聚力模型做了分析比较,综合看在静态载荷作用下的中,双线性准则无论对于计算的经济行还是准确性以及收敛特征都是很好的选择,因此本文选择双线性本构模型来进行复合材料层合板的层间渐进损伤分析,其双线性本构模型典型的相对位移-牵引力曲线如图1.图1 双线性本构模型典型曲线根据图1,可以给出初始破坏点对应的界面相对位移,如下:(21)其中:N为界面的法向强度,S、T为界面的剪切强度.混合模式下的内聚力单元损伤扩展判据采用由Benzeggaph和Kenane[9]提出的B-K准则,该准则考虑了不同裂纹模式下应变能释放率直接的耦合关系,其表达式如下:(22)其中:2 复合材料层合板低速冲击分析算例验证2.1 模型参数试验中层合板尺寸150×100 mm,厚度5.8 mm,铺层方向[454/04/-454/904]s 对称铺层其基本力学性能见表1,层间性能见表2,通过四个刚性压头固支形成一个125×75 mm的冲击区域.刚性冲头为半球形,前端直径为16 mm,质量为5kg[10].表1 单层板材料基本力学性能E11/GPaE22/GPaG12/G Paυ11 υ23XT/MPaXC/MPaYT/MPaYC/MPaSL/MPa1287.64.40.350.452 300153126199.878.4表2 层间强度及层间韧性层间强度t0n=t0s=t0t=26.0MPa断裂韧性GIC=0.28N/mm;GⅡC=GⅢC=0.79N/mm2.2 有限元模型建立为了降低边界约束对试验结果的影响,本文在对复合材料层合板低速冲击部分建立有限元模型时,建立了试验中所有部件,即刚性底座、四个刚性压头、试验层合板、以及刚性冲头四部分,层合板子层选择沙漏增强的C3D8R单元;层间选择内聚力(CHO3D8)单元,其余全部选择离散刚体.为了保证接触区域分析精度,划分网格中部60×60区域内进行细化,其余部分按比例划分;四个刚性压头施加预紧位移0.015 mm,低速冲击的有限元模型如图2所示.图2 复合材料层合板低速冲击有限元模型2.3 数值仿真结果及讨论本文主要对冲击能量为19.3 J试验进行分析,图3中显示了数值计算和试验中冲击接触力随时间的变化曲线,从图3中可以看出冲击接触力峰值和试验值吻合的很好[11].图3 冲击能量为19.3 J下的接触力时间曲线图4为其各子层的基体损伤形状以及各层间分层,由图4可知,各层间的分层形状基本呈现对称的双叶形,即花生状,主轴方向沿着下层纤维的铺设方向,且靠近冲击背部的界面分层面积要大于靠近冲击点处的界面分层面积;基体损伤通常沿着该层纤维方向的带状分布,越是靠近冲击背部,基体开裂的长度越大,但发现靠近底层的铺层基体的方向沿着方向,其原因是因为其处在和之间,铺层角度变化最大,并且其下方有大面积分层出现,改变了该层的应力分布所致.图5所示冲击层合板后使用C扫描得到的分层面积,图6所示是使用绘图软件描边得到的数值计算和试验对比结果,从图5中可以看出分层面积在其沿长度和宽度的两方向上最大尺寸吻合的很好,但是整个投影面积有一定的误差,其试验投影面积最大值为4 000 mm2,图6是其数值计算的所有分层的投影面积,其值为4 450.9 mm2,其误差为11.3%.45°(45°/0°)45°(0°/-45°)-45°(-45°/90°)90°(90°)-45°(90°/-45°)0°(-45°/0°)45°(0°/-45°)图4 各子层的基体损伤形状以及各层间分层形状图5 试验分层面积图6 试验与数值计算分层投影面积对比3 结论本文基于损伤力学理论,建立了一个反映复合材料层合板面内和层间的三维渐进损伤的非线性损伤模型,研究了复合材料层合板在低速冲击作用下的层内和层间冲击响应下的非线性失效行为,可以得到如下结论:对于复合材料层合板面内损伤, 本文以改进的Hashin失效准则作为起始损伤准则,提出了一种基于能量释放率的损伤变量指数渐进演化模型,既描述了复合材料损伤的渐进失效过程,又避免了材料刚度突然下降导致刚度矩阵奇异的不足,同时引入特征长度来降低网格的依赖性,最终建立了单层板的渐进损伤非线性分析模型.针对层合板的层间损伤, 本文采用内聚力单元来模拟,通过结合传统的应力失效准则和断裂力学中的能量释放率准则定义了界面损伤演化规律.对试验结果进行对比分析,发现在冲击过程中,层合板最先产生的损伤形式是基体开裂和层间分层,并且是其能量消耗的主要表现形式,冲击造成的基体损伤,其方向一般沿纤维方向,并且越是靠近背部基体损伤较为严重,冲击造成的层间分层主要发生在不同铺层之间,一般呈现双叶形,即花生形,并且主轴沿着下子层的纤维方向,这与试验观察到的现象是一致的.参考文献:[1] TAN S C. A progressive failure model for composite laminates containing openings[J]. Journal of Composite Materials, 1991, 25: 556-577.[2] CHANG F C K. A progressive damage model for laminated composites containing stress concentrations[J]. Journal of Composite Materials, 1987, 21: 834-855.[3] CHANG K, LIU S, CHANG F. Damage tolerance of laminated composites containing an open hole and subjected to tensile loadings[J]. Journal of Composite Materials, 1991, 25: 274-301.[4] CAMANHO P P, DAVILA C G. Mixed-mode decohesion finite elements for the simulation of delamination in composite material[R]. NASA/TM-2002-211737, 2002: 1-37.[5] 张彦, 朱平, 来新民, 等. 低速冲击作用下碳纤维复合材料铺层板的损伤分析[J]. 复合材料学报, 2006, 23(2): 150-157.[6] 张彦, 来新民, 朱平, 等. 复合材料铺层板低速冲击作用下损伤的有限元分析[J]. 上海交通大学学报, 2006, 40(8): 1348-1353.[7] HASHIN Z. Failure criteria for unidirectional fiber composites[J]. Journal of Applied Mechanics, 1980, 47: 329-335.[8] ALFANO G. On the influence of the shape of the interface law on the application of cohesive-zone models[J]. Composites Science and Technology, 2006, 66(6): 723-730。
带孔复合材料层板动态拉伸破坏的应变率效应

带孔复合材料层板动态拉伸破坏的应变率效应荆臻;田常录;吴健;王纬波;赵军华;孙琎【摘要】采用三维Hashin准则作为纤维束损伤判据,根据材料不同损伤模式制定相应的材料性能退化方案,并考虑应变率效应对材料的强度性能进行修正,建立含孔复合材料层合板的渐进损伤分析模型,模拟材料在不同应变率下的损伤破坏过程.通过动态拉伸试验,获得材料在不同应变率下的载荷-位移关系及孔边不同位置的时间-应变关系,讨论了应变率对材料拉伸性能的影响及试件孔边的应力集中情况.有限元分析结果与试验数据相一致,证明了本文所提出分析模型的正确性和有效性.【期刊名称】《南京航空航天大学学报》【年(卷),期】2019(051)001【总页数】8页(P55-62)【关键词】带孔层合板;应变率效应;冲击拉伸;应力集中【作者】荆臻;田常录;吴健;王纬波;赵军华;孙琎【作者单位】江南大学机械工程学院江苏省食品先进制造装备技术重点实验室,无锡,214122;江南大学机械工程学院江苏省食品先进制造装备技术重点实验室,无锡,214122;中国船舶科学研究中心,无锡,214082;中国船舶科学研究中心,无锡,214082;江南大学机械工程学院江苏省食品先进制造装备技术重点实验室,无锡,214122;江南大学机械工程学院江苏省食品先进制造装备技术重点实验室,无锡,214122【正文语种】中文【中图分类】O385纤维增强树脂基复合材料凭借高比强度、高比模量、耐高温以及可设计性强等出色的综合性能,已被大量运用于航空航天、国防军工以及交通运输、化工和建筑等领域[1-4]。
在实际应用中,出于结构连接的需要,不可避免地对层合板进行开孔等操作,这破坏了材料自身的连续性,降低了结构强度[5-7]。
研究显示,开孔使某船用层合板的强度下降了40%~60%[8]。
而运用在航空航天、国防军工以及交通领域的结构,往往在很短的时间内承受极大的应力,由于复合材料存在应变率效应的问题,其破坏形式与应变率密切相关[9-10]。
- 1、下载文档前请自行甄别文档内容的完整性,平台不提供额外的编辑、内容补充、找答案等附加服务。
- 2、"仅部分预览"的文档,不可在线预览部分如存在完整性等问题,可反馈申请退款(可完整预览的文档不适用该条件!)。
- 3、如文档侵犯您的权益,请联系客服反馈,我们会尽快为您处理(人工客服工作时间:9:00-18:30)。
第17卷第17期2017年6月 1671—1815(2017)017-0066-06科学技术与工程Science Technology and EngineeringVol. 17 No. 17 Jun. 2017©2017 Sci. Tech. Engrg.一般工业技术基于三维应变渐进损伤准则的复合材料层合板大开孔压缩损伤研究李泽江1郑锡涛2(上海飞机设计研究院强度设计研究部1,上海201210;西北工业大学航空学院2,西安710072)摘要针对复合材料层合板大开孔压缩,将二维应变渐进损伤准则修正为三维应变渐进准则,使其能够模拟层合板的分层 损伤,建立了复合材料层合板大开孔压缩损伤分析模型。
利用UM AT子程序将基于三维应变渐进损伤准则引入到分析模型 中预测纤维、基体及分层等失效演化过程;并对大开孔复合材料层合板进行试验研究。
试验结果表明所建立的基于三维应变 渐进损伤准则的层合板大开孔分析模型能很好地模拟大开口复合材料层合板压缩过程中的损伤起始、损伤扩展及破坏模式;并最终预测复合材料层合板大开孔的破坏强度。
关键词复合材料层合板 大开孔压缩 渐进损伤 UMAT 损伤分析中图法分类号TB330. 1 V257;文献标志码A以碳纤维增强的先进复合材料因其高比模量、高 比强度、耐腐蚀及热膨胀系数低等优点成为了航空航 天领域广泛应用的材料之一,与传统金属材料相比,其 结构减重可以达到20% ~30% [1]。
在航空结构工程实 践中,为了维修等需要,常常需要对复合材料层合板进 行开孔,甚至进行大开孔;而复合材料层合板对缺口等 损伤极为敏感,致使压缩剩余强度可降低达60% M。
开孔复合材料层合板压缩性能研究是复合材料损伤容 限研究的重点之一,目前国内外学者对其进行了大量 试验和理论方法的研究,取得了很大的进展[2’3]〇近年来,国内外学者对复合材料层合板结构损 伤演化数值分析预测方法进行了不断的改进和优 化,从最初简单的二维受载,逐渐过渡到三维复杂受 载。
采用基于逐渐刚度退化的方法,形象地给出加 载过程中的损伤演变过程[4_14],能够较好地描述孔 口附近的层间应力集中等情况。
Tan[4]等在对含孔 复合材料层合板的剩余强度研究,将不同损伤模式 引起的材料性能下降通过参数折减的方式来表示。
Camanho 和 Soutis 等[5—7]在分析 T300/914 复合材 料层合板接头强度时,将T an的参数退化方式扩展2016年12月26日收到第一作者简介:李泽江。
E-mail: lizejiang@ comae, cc。
引用格式:李泽江,郑锡涛.基于三维应变渐进损伤准则的复合材 料层合板大开孔压缩损伤研究[J].科学技术与工程,2017, 17 (17) :66—71LI Zejiang, Zheng Xitao. Damage analysis of composite laminate with large open-hole under compression using 3D strain progressive damage theory [ J ]. Science Technology and Engineering, 2017 , 17 ( 17 ):66—71到三维;并对不同尺寸的开孔复合材料层合板进行 压缩性能的试验研究,得到了厚度增加会影响层合 板开孔压缩失效模式的变化的结论。
Wisn〇m等[8]通过研究缩放比例效应对复合材料开孔板的影响分 析;Sun等[9]则基于细观力学提出的非迭代失效单 元方法对复合材料渐进损伤进行研究。
关志东 等[1°,11]通过试验及数值分析方法对复合材料开孔 压缩过程中层内失效和层间失效都进行研究,结果 表明所建立的理论分析结果与试验结果吻合较好。
郑锡涛等[12,13]利用渐进损伤理论对低速冲击及含损 伤复合材料结构的等效性和损伤因素进行了研究,结 果表明利用渐进损伤方法可以有效的模拟损伤演化 过程。
崔海坡等[14]和李亚智等[15]采用三维和准三 维渐进损伤方法对复合材料开孔压缩和拉伸进行了 数值研究,结果表明与试验结果具有较好的一致性。
目前复合材料开孔压缩研究大多集中在孔径为 6 mm和12 mm等小开孔层合板结构;然而在实际 飞机结构中,由于管路及系统安装的要求,需要对复 合材料层合板进行大开孔。
本文通过对文献[16] 提出二维应变准则进行修正,建立起基于三维应变 渐进损伤准则,利用UMAT材料子程序,对复合材 料层合板大开口压缩强度进行预测并揭示其损伤演 化过程,最后通过与试验结果进行对比,验证修正准 则及模型的准确性。
1理论模型的建立1.1损伤判据准则大量的试验结果表明:复合材料结构在损伤过程17期李泽江,等:基于三维应变渐进损伤准则的复合材料层合板大开孔压缩损伤研究67中,基本包括有纤维损伤、基体损伤及界面的分层三种损伤形式,各种损伤形式都是相互关联的,在同一损伤区域可能同时存在多种损伤形式,一种损伤形式也可能诱发其他损伤形式。
对文献[16]提出的二维应变准则[式(1)和式(2)]进行修正,使其能模拟复合材料层间效应[式(3)],建立三维应变连续损伤准则,纤维损伤、基体损伤和分层损伤可相应的表示为:/fI s\\s\\(1)Ll i (s22)2 +(s2222})s22 +^(s12)2(2)S22 S Y1L l(s33)2+(4 C d:_(4)_4(1乂)^22式中,'和( & = 1=t,c )分别为该区域的工作应变和拉伸/压缩/剪切破坏应变;当A >&“ =f,m,s“= 1,2,3)时分另[J表示该区域出现纤维损伤、基体损伤和分层损伤。
1.2本构方程及损伤变量基于渐进损伤累积理论及连续介质损伤力学,本文采用一个二阶对称张量^来定义损伤状态,其特征值分别表示垂直于3个主方向有效承载比例。
特征值为〇时,表示该单元无损伤,特征值为1时,表示该单元已经完全失去承载能力。
设无损伤的刚度矩阵为C,当材料点发生损伤后,刚度矩阵为CD,本构方程可写为:(4)(^13)2+^(^23 )2^23(3)a= CB s式(4)中:(1-d{)(l~ds)C l3000(1~ds)C23000(1-ds)C33000(1-d{)(l-dm)C u00(1-d{)(l-ds)C550sym(1~ds)C6t目前复合材料结构损伤分析过程中的材料失效 退化模型,主要有以下3类[2]:①基于常数的刚度折 减法;②基于损伤状态变量的刚度折减法;③混合 法。
本文采用第2种方法,即基于损伤状态变量的 刚度折减法。
该方法能较好的预测层合板的破坏模 式,对于纤维增强复合材料损伤累积引起的材料非 线性,该损伤材料退化方法能很好地避免刚度矩阵 退化过程中的矩阵奇异性。
定义损伤变量[16]为:^= 1 _ J_e(-C n4l(/f-4l)/%)f{(5)" _ 1^_^(-C22s22(fm~s22)/G m)an i_ i _ eJ m(6)定义分层损伤变量为:— 1J_p(-C33£33(/s-^33)/G s)8L(V)式(4)〜式(7)各参数定义如下:E h(l -u TT)_ E T(1 - vL T v TL)以ABAQUS有限元软件为平台,采用用户材料 子程序UMAT嵌入材料本构方程及材料失效准则,应用Newton-Raphson方法进行求解。
本文计算中 米用的UMAT程序的流程图如图1所7K。
图1U M A T子程序图Fig. 1U M A T flow chat^12 ~ ^13E'rp (i;LT +i;LTi;T T)E t(v tt+v ltv t l):I5^23 = ""2分析实例^23E t(i;t t + vL T v TL)C44 = G l t;C55:^T L;^66:G t td一 1 一^^L T^T L 一^T T 一 ^^L T^T L^T TG,^m,^S分别为3个材料主万向的临界断裂目泛。
2.1有限元模型为了验证建立的基于三维应变的渐进损伤准则 有限元分析模型的有效性,分析计算了复合材料层合板大开口在压缩载荷下的损伤破坏过程。
本文研68科学技术与工程17卷0.20.40.6 0.8 1.(Displacement/mm1.2图3孔直径为50 m m 位移-载荷曲线Fig. 3 Displacement-load curve of 50 m m dia全破坏。
2.3损伤演化在压缩载荷作用下,层合板会发生纤维损伤、基 体损伤和分层损伤等损伤。
损伤累积图形和相应的演化过程如表2所示,其中SDV 3、SDV 4、SDV 5与损 伤状态变量 <、必、4相对应,分别用于表示纤维、 基体和分层损伤情况,数值为1表示单元发生完全 破坏,数值为〇表示元未发生损伤,数值在〇〜1 之间表示单元发生部分损伤。
从表2中可以看到,0°铺层的纤维在压缩载荷的作用下,损伤是从孔边的左右两侧(垂直载荷方 向)开始发生单元的损伤,当损伤长度扩展到1.5mm 左右时,此时到达层合板的极限载荷(b 点)。
此后,损伤迅速扩张到孔边,对比图3中b 和c 点的 位移可以得到。
这个过程是与实际试验现场是相符 合的,试验中,在即将到达极限载荷时,可以听到少 许纤维断裂的声音,接着|声巨响,试样件破坏。
45°铺层的基体损伤出现比0°铺层的基体损伤出现 的提早了一些,其基体损伤演化与〇°铺层的基体损 伤演化相似。
在达到极限载荷(b 点)之前,45°铺层 的分层损伤就已经出现了,说明分层损伤对压缩极 限载荷是有影响的。
90°铺层的基体损伤在压缩载 荷较小的时候就已经产生了,达到极限载荷时,其一 侧的孔边损伤面积约为80 mm 2,是影响压缩极限载 荷的一个重要因素。
综上所述,相比二维应变渐进损伤准则,本文 采用的三维损伤失效准则可以更真实的模拟和预 测复合材料层合板大开孔的压缩破坏过程和破坏 模式。
试验与计算结果表明:±45°和90°铺层分 层损伤对复合材料层合板大开孔的压缩强度有较 大的影响u对于开孔复合材料层合板iR 缩极限载荷的预 测,文献[18,19 ]认为当0°铺层的纤维损伤由孔边 扩展到边界时认为层合板发生破坏,本文通过后续 试验并结合有限元结果认为:〇°铺层的纤维损伤扩允尺寸为 150 mm X 100 mm x 5 mm 的 T 800/BA 9916复合材料层合板,铺层形式为[45/45/90/45/〇/45/0/45/45/0]2s,单层厚度为 0. 125 mm ◎采用H 维八节点减缩积分单元C 8D 3R 对各铺层进行模拟,该单元能有效的模拟压缩在作用下层合板的应 力状态。