难处理金精矿3种预处理工艺分析
过氧化氢氧化预处理高硫高砷难选金精矿的试验研究

。
n e l o d t n,a d,c mp r d wi o v n in lmeh d ,i c n s o t n o i a in t . T e s d r vd s a d rmi c n i o d i n o ae t c n e t a t o s t a h r xd t i h o e o me h t y p o i e u
53. 4% r s e tv l e h u p c n e ta in wa 0 g L.Th s e vr nme tly fin l r te t n r c s s 9 e p ci ey wh n t e p l o c n r to s2 / i n io n al re d y p er ame t p o e s wa
Pr t e t e fH i h- u f r a d Hi h- r e i f a t r l n e t a e e r a m nto g - lu n g - s n c Re r c o y Go d Co c n r t s a 、 h d o e r x d n Ac d M e i m t Hy r g n Pe o i e i i d u
GUO iqn,LIDe g xn,MA e —u,ZHAO a - h n,ZHU iln Ka — i n —i Ch ng y Xi o c u Fe—o g
( o eeo n i n etl c ne n n i eig D n h a U i r t, h n h i 0 6 0 hn C lg l fE v o m na i c dE gn r , og u nv sy S ag a 12 ,C i r Se a e n ei 2 a) A s a t T epe et e t f ihsl ra dhg —re i rf c r o o cnrt R C i yrg nprxd b t c : h rt am n g — f n ihasnc er t ygl cn e t e( G )wt hdoe eoie r r oh uu ao d a h
我矿难处理金精矿焙烧氰化浸出试验

我矿难处理金精矿各处理方案对比分析历年来我矿通过外委和自已多次对难选冶金精矿进行焙烧氰化实验,目的是为了探索我矿难处理金精矿焙烧法预处理技术的可行性。
下面就历次实验情况介绍如下。
一、北京有色冶金设计研究总院所做的小型试验试验原料为选矿富集得到的高硫金精矿,化学分析结果如下(此试验为1999年完成):表1 主要化学组成(Au、Ag单位为g/t,其余为%)方案1 固硫、固砷焙烧氰化试验通过添加生石灰熟石灰添加剂,在焙烧过程中,使二氧化硫与砷固定,既保证金的浸出,又达到环保要求。
实验结果见表3 表3 固砷焙烧预处理及氰化试验固砷焙烧氰化的实验分析:通过加入固砷剂焙烧,砷的固定率约为95%,而金的浸出率在80~~85%之间。
由于精矿含砷、硫高,加入石灰量大,反应生成的砷酸钙造成的二次包裹,明显地降低了金的浸出率。
试验结果表明该方案不理想。
方案2 二段焙烧氰化试验:一段焙烧在低温、中性或弱还原性气氛下,使砷以三氧化二砷的形式挥发;二段在高温氧化性气氛下焙烧,使硫化物充分氧化。
保证金的浸出。
实验结果见表4表4 二段焙烧焙砂粒度与金浸出率的关系二段法焙烧氰化实验分析:随着焙砂粒度变细,金的浸出率逐渐提高。
一段的温度为500至550摄氏度,时间为60至90分钟,中性或弱氧化气氛下进行;二段的温度为700摄氏度,时间为120分钟,氧化气氛下进行。
金的浸出率大于92%。
其中砷的脱除率为80%左右,硫的脱除率可达96%,硫化物氧化比较彻底。
方案3 一段焙烧在一定温度下进行氧化焙烧,部分砷挥发,部分砷残留于焙砂中。
实验结果见表5表5 一段焙烧焙砂粒度与金浸出率的关系一段焙烧氰化实验焙浇温度为700摄氏度,时间为180分钟,金的浸出率约为95%,氧化渣含金5g/t左右。
其中砷的脱除率接近70%,硫的脱除率大于98%。
金的浸出率随焙砂的细度的增加有所提高。
对含砷硫化物难处理金矿,多倾向于两段焙烧,以利于砷的脱除,但这并不是绝对的。
难选冶金矿石的提金技术-黄金冶炼技术系列之二

难选冶金矿石的提金技术-黄金冶炼技术系列之二转载自谁?..轩难处理金矿石是指用常规的氰化提金方法,金的直接浸出率不高的金矿石,一般为80%以下,典型的难处理矿石直接浸出率仅为10%-30%。
造成难浸的原因主要是微细粒金和包裹金以及矿石中含砷、含碳等有害杂质。
此类矿石需进行预处理才能合理利用,并获得经济效益。
处理的方法较多,有焙烧法、加压氧化法、生物氧化法及其它化学氧化法等。
2.1 焙烧预处理技术焙烧氧化法是较古老的预处理方法,特别是对含硫、含砷较高的矿石,这种方法可以自热平衡,可以回收和,是一种比较理想的方法。
随着技术的进步和市场的需求,此法近年来得到新的发展。
早期使用的有多堂炉焙烧、回转窑焙烧、马弗炉焙烧。
沸腾炉氧化焙烧金矿石始于1947年,两段沸腾炉焙烧、原矿循环沸腾炉焙烧法是近十几年才得到商用。
两段焙烧、循环焙烧以及正在发展的热解--氧化焙烧法、闪速焙烧法、微波焙烧法都以解决环保、降低能耗、提高浸出率和增加焙烧强度为目的。
焙烧氧化法的特点是适应性强,但随着环保要求的提高,废气治理成本提高,此方法受到湿法预处理方法的挑战。
国外采用沸腾炉焙烧的主要厂家有11家,以原矿循环沸腾炉焙烧和两段沸腾炉焙烧为多。
如美国的IBM公司为处理部分包裹金和含有机炭的矿石采用了投资和操作成本最低的两段焙烧法。
我国的湖南某矿和新疆某矿为处理高砷金精矿也采用了焙烧法进行预处理。
2.2 加压氧化预处理技术这种方法是用加压氧化酸浸或用加压碱浸对矿石进行预处理。
先除去矿石中的S、As、Sb 等有害杂质,使金矿物充分暴露,然后用氰化法回收金。
环保的要求和金浸出率的要求,促进了加压氧化法的发展。
1984年此法首先应用于Homestake,Mclanlgh金矿,并从此得到快速发展。
目前国外有代表性的加压氧化厂有11家。
超细磨--低温低压氧化难处理金矿石技术是澳大利亚Dominion矿物公司发展的技术,通过超细磨,矿物表面活性提高,氧化温度、压力降低,反应釜材质、防腐问题变小,是比较有发展前途的。
三相流化床中预处理难浸金精矿冷模研究

Ab ta t t i e e s r O c n u t c l i lto f p e r ame t o e r c o y g l o c n r t sr c :I s n c s a y t o d c o d smu a in o r t e t n f r f a t r o d c n e t a e
eain c r to ondto hefo Cha a t s isw e e c n iinson t l w r c e itc r o duc e . ( ) a e a e g s h du nc e s d w ih g sve r td 1 v r g a ol p i r a e t a —
与气 速 的模 型 关 联 结 果 为 e一 0 1 U .2 。
关 键 词 : 相 流化 床 ; 处 理 ;金 精 矿 ; 模 三 预 冷 中 图 分 类 号 :T 9 D 8 文 献标 识 码 :B 文 章 编 号 : 0 4 0 I (0 1 4 0 5 0 1 0 —4 5 2 1 )0 —0 8 — 4
2 Co lg fEn io me t l ce c n g n e i g,Do g u i e st . l e o vr n n a S in ea d En i e r e n n h a Un v r i y,S a g a 2 1 2 h n h i 0 6 0,Ch n ) i a
第 2 o卷 第 4期
2 1 年 4月 01
中 国 矿 业
CH I NA I NG AG AZI M NI M NE
V o . 0。N o 12 .4
A pr .
2 1 01
i 盥蛰 菠 ຫໍສະໝຸດ 三相 流 化床 中预 处理 难 浸金 精矿 冷模 研 究
难处理金精矿焙烧预氧化工艺实践
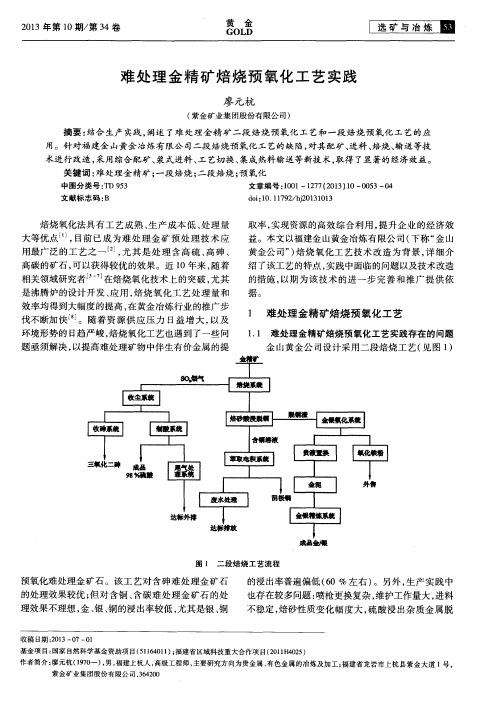
焙烧 氧 化法具 有 工 艺成 熟 、 生产 成本 低 、 处 理 量
果较好 , 对 含砷 矿 物 处 理 效 果 较差 。所 以 , 对 焙烧 工 艺进 行优 化改 良 , 扩 大工 艺 对 矿 物 的适 应性 , 是 焙烧 工艺 获得 竞争 优势 , 提 升企 业经 济效 益 的重要举 措 。
1 . 2 含砷 难 处理 金精 矿二 段焙 烧预 氧化 工艺 应用 对 含高砷 难 处 理 金 精 矿 进 行 二 段 焙 烧 j : 一 段
取率 , 实现 资 源的高 效 综 合 利用 , 提 升企 业 的经 济效 益 。本文 以福 建金 山黄金 冶炼 有 限公 司 ( 下称 “ 金 山
黄金公 司” ) 焙烧氧化工艺技术改造为背景 , 详 细 介
大等 优 点¨ , 目前 已成 为 难 处 理 金 矿 预 处 理 技 术 应 用最 广 泛 的工 艺 之 一 _ 2 J , 尤 其 是 处 理 含 高硫 、 高砷 、 高碳 的矿 石 , 可 以获得 较优 的效 果 。近 1 0年来 , 随 着 相关 领域 研 究者 在焙 烧氧 化技 术 上 的突 破 , 尤 其 是 沸腾 炉 的设 计 开 发 、 应用 , 焙 烧 氧 化 工 艺 处 理 量 和 效率 均得 到 大 幅度 的提高 , 在 黄金 冶炼 行业 的推广 步 伐 不 断加 快 。随 着 资 源 供 应 压 力 日益 增 大 , 以及 环境 形势 的 日趋严 峻 , 焙烧 氧化 工 艺也 遇 到 了一 些 问 题 亟 须解 决 , 以提 高难 处理 矿物 中伴 生有 价 金属 的 提
臭氧和三氯化铁氧化高硫高砷难浸金精矿的预处理试验研究
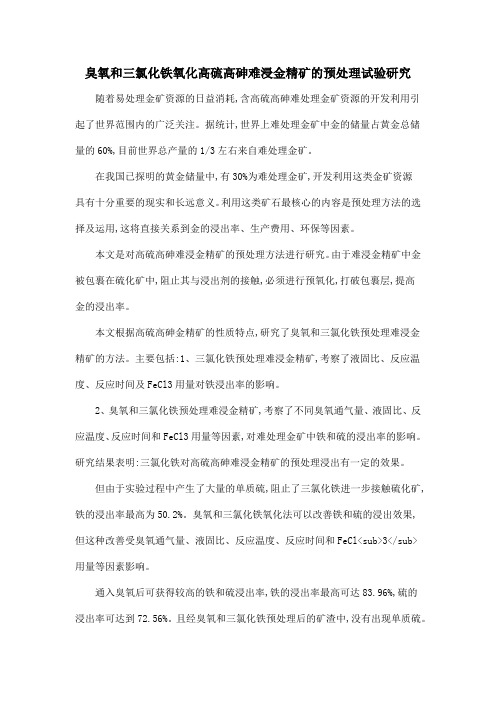
臭氧和三氯化铁氧化高硫高砷难浸金精矿的预处理试验研究随着易处理金矿资源的日益消耗,含高硫高砷难处理金矿资源的开发利用引起了世界范围内的广泛关注。
据统计,世界上难处理金矿中金的储量占黄金总储量的60%,目前世界总产量的1/3左右来自难处理金矿。
在我国已探明的黄金储量中,有30%为难处理金矿,开发利用这类金矿资源具有十分重要的现实和长远意义。
利用这类矿石最核心的内容是预处理方法的选择及运用,这将直接关系到金的浸出率、生产费用、环保等因素。
本文是对高硫高砷难浸金精矿的预处理方法进行研究。
由于难浸金精矿中金被包裹在硫化矿中,阻止其与浸出剂的接触,必须进行预氧化,打破包裹层,提高金的浸出率。
本文根据高硫高砷金精矿的性质特点,研究了臭氧和三氯化铁预处理难浸金精矿的方法。
主要包括:1、三氯化铁预处理难浸金精矿,考察了液固比、反应温度、反应时间及FeCl3用量对铁浸出率的影响。
2、臭氧和三氯化铁预处理难浸金精矿,考察了不同臭氧通气量、液固比、反应温度、反应时间和FeCl3用量等因素,对难处理金矿中铁和硫的浸出率的影响。
研究结果表明:三氯化铁对高硫高砷难浸金精矿的预处理浸出有一定的效果。
但由于实验过程中产生了大量的单质硫,阻止了三氯化铁进一步接触硫化矿,铁的浸出率最高为50.2%。
臭氧和三氯化铁氧化法可以改善铁和硫的浸出效果,但这种改善受臭氧通气量、液固比、反应温度、反应时间和FeCl<sub>3</sub>用量等因素影响。
通入臭氧后可获得较高的铁和硫浸出率,铁的浸出率最高可达83.96%,硫的浸出率可达到72.56%。
且经臭氧和三氯化铁预处理后的矿渣中,没有出现单质硫。
本论文研究的臭氧和三氯化铁法浸取难处理金矿,可有效提高铁和硫的浸出率,且反应后的产物无毒,符合当今环保的要求。
但黄铁矿和砷黄铁矿的浸出率还有提升的空间,实验装置和条件还需要进一步的技术研究和改进。
难处理金矿石预处理工艺
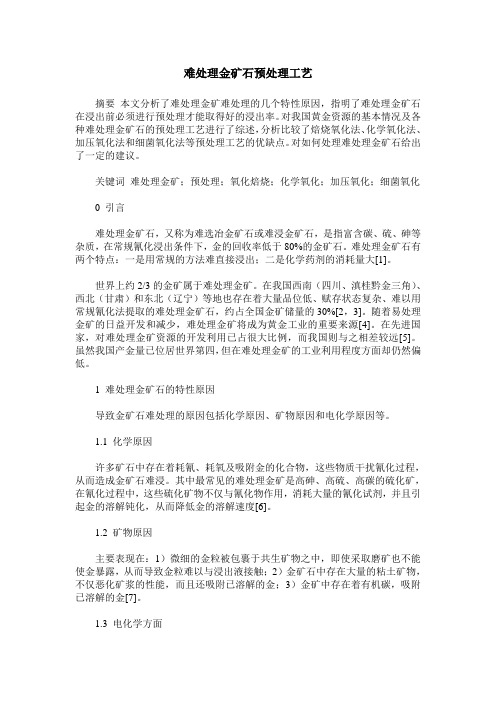
难处理金矿石预处理工艺摘要本文分析了难处理金矿难处理的几个特性原因,指明了难处理金矿石在浸出前必须进行预处理才能取得好的浸出率。
对我国黄金资源的基本情况及各种难处理金矿石的预处理工艺进行了综述,分析比较了焙烧氧化法、化学氧化法、加压氧化法和细菌氧化法等预处理工艺的优缺点。
对如何处理难处理金矿石给出了一定的建议。
关键词难处理金矿;预处理;氧化焙烧;化学氧化;加压氧化;细菌氧化0 引言难处理金矿石,又称为难选冶金矿石或难浸金矿石,是指富含碳、硫、砷等杂质,在常规氰化浸出条件下,金的回收率低于80%的金矿石。
难处理金矿石有两个特点:一是用常规的方法难直接浸出;二是化学药剂的消耗量大[1]。
世界上约2/3的金矿属于难处理金矿。
在我国西南(四川、滇桂黔金三角)、西北(甘肃)和东北(辽宁)等地也存在着大量品位低、赋存状态复杂、难以用常规氰化法提取的难处理金矿石,约占全国金矿储量的30%[2,3]。
随着易处理金矿的日益开发和减少,难处理金矿将成为黄金工业的重要来源[4]。
在先进国家,对难处理金矿资源的开发利用已占很大比例,而我国则与之相差较远[5]。
虽然我国产金量已位居世界第四,但在难处理金矿的工业利用程度方面却仍然偏低。
1 难处理金矿石的特性原因导致金矿石难处理的原因包括化学原因、矿物原因和电化学原因等。
1.1 化学原因许多矿石中存在着耗氰、耗氧及吸附金的化合物,这些物质干扰氰化过程,从而造成金矿石难浸。
其中最常见的难处理金矿是高砷、高硫、高碳的硫化矿,在氰化过程中,这些硫化矿物不仅与氰化物作用,消耗大量的氰化试剂,并且引起金的溶解钝化,从而降低金的溶解速度[6]。
1.2 矿物原因主要表现在:1)微细的金粒被包裹于共生矿物之中,即使采取磨矿也不能使金暴露,从而导致金粒难以与浸出液接触;2)金矿石中存在大量的粘土矿物,不仅恶化矿浆的性能,而且还吸附已溶解的金;3)金矿中存在着有机碳,吸附已溶解的金[7]。
1.3 电化学方面主要表现在金与锑、铋等一些导电物质形成的化合物导致金的阴极溶解被钝化[8]。
金精矿化学分析方法

金精矿化学分析方法
金精矿化学分析方法是在无条件下使用化学方法来分析金精矿中各元素含量的一种分析方法。
一般来讲,金精矿分析大致可分为两步:一是对矿物样品的精烬处理,二是分析样品中的元素含量。
具体的步骤如下:
1. 样品预处理。
包括样品抽取,物理分离和选定处理法。
2. 精烬处理。
根据样品的性质,以1000℃的温度,用电弧熔烧法或激光脱氧熔烧法进行样品处理。
3. 使用多种化学方法对精烬样品进行分析,包括电感耦合等离子体质谱法(ICP-MS)、原子荧光光谱法(AES)、X射线荧光光谱法(XRF)、串联质谱法(MS)以及波谱分析等。
4. 计算金精矿样品的各元素含量,形成化学分析报告。
5. 对结果进行准确性校核,确定金精矿的组成及成因。
- 1、下载文档前请自行甄别文档内容的完整性,平台不提供额外的编辑、内容补充、找答案等附加服务。
- 2、"仅部分预览"的文档,不可在线预览部分如存在完整性等问题,可反馈申请退款(可完整预览的文档不适用该条件!)。
- 3、如文档侵犯您的权益,请联系客服反馈,我们会尽快为您处理(人工客服工作时间:9:00-18:30)。
难处理金精矿3种预处理工艺分析
难处理金精矿是指金精矿中黄铁矿、毒砂等硫化物将金包裹起来,没有充分的外露表面,而且金呈微细粒状态嵌布,采用常规氰化法处理难以有效回收等有价金属。
根据金的按钮选冶程度,难处理金精矿划分为4级,即采用城规选冶方法时,金的侵出率小于50%的为难选冶金精矿,在50%-80%的为一般难选冶金精矿,在80%-90%的为较易选冶金精矿,90%以上的为易选冶金精矿。
荥阳矿机认为金精矿难侵原因是原因是因为含有碳等哪呢过吸附金的有机物,造成金属流失,或者金呈极微细粒嵌布于载体矿物的晶间及裂隙中,即使采用超细磨也难以使金粒有效解离,以及有害元素砷硫化矿物使之氧化分解,被包裹的金暴露出来,然后再用氯化法回收金。
预处理工艺主要有焙烧氧化法、生物氧化法、热压氧化法、硝酸催化氧化法、微波焙烧法以及其他预处理方法。
矿物进行预处理后经行氯化侵出,以便使金等有价元素得到最大限度的回收。
当前应用比较成熟的预处理工艺主要有焙烧氧化、生物氧化、热压氧化3种。
这3种工艺都有各自的优缺点,至于选用哪种工艺需要进行详细分析比较后确定。
焙烧氧化法
焙烧氧化法是在高温下,借助空气或氧气使包裹金的砷硫物氧化分解,使被包裹金暴露出来。
氧化焙烧工艺应用比较广泛,在国内外都有很好的应用。
国内工业生产应用的有山东招远国大冶炼厂、中原冶炼厂、海阳金澳冶炼厂等。
工艺特点及优缺点
氧化焙烧可使硫化物氧化生成二氧化硫,砷和锑以氧化态挥发,含碳物质被氧化从而失去活性,显微细粒状的金得到暴露及富集。
氧化焙烧法的优点为:1.矿石适应性强、操作费用低;2.可以实现副产品的综合回收,可产出硫酸、砒霜等作为化工原料,其他有价金属也可同时回收。
氧化焙烧法的缺点为:1.烟气中SO2会造成环境污染;2.副产品如硫酸、砒霜等的销售手制于市场;
3.对脉石型包裹金等的矿物回收率不高;
4.银回收率不
高;5.含砷不能高于5%。
生物氧化法
生物养护也称细菌氧化,氧化含硫矿物具有直接氧化、间接氧化以及电池作用的过程。
生物氧化法适用于矿物中铜含量低的,否则将增加氧化成本及中和成本,不适合含有劫金炭的金精矿,可处理含砷大于5%以上的矿物。
细菌氧化法的优点为:1.对周围环境产生的危害性很小,无烟气污染;2.没有副产品受制于市场的销售问题。
细菌氧化法的缺点为:1.细菌适应性差,特别是在高原地区,温差很大,含氧量低,比利于细菌的生长;2.产生大量的酸性液体,需要进行汇总和后才能复用;3.建造费用高,所有设备都要使用耐酸设备;
4.运行成本高;
5.矿物中的元素除了金银外,都不能综合回收;
6.预处理周期太长。
热压氧化法
热压氧化法是在高温高压下,矿石中的砷黄铁矿与氧发生化学反应,使包裹金暴露出来的方法,热压氧化法分为酸性热压氧化法和碱性热压氧化法。
热压氧化法使用性较广,原矿精矿都可以,也可处理含砷稍高的矿物。
热压氧化法的优点为:1.无烟气污染;2.对含碳金精矿有一定的处理效果;3.银回收率高。
热压氧化法的缺点为:1.产生大量的酸性液体;2.建造费用高,所有设备都要使用耐酸耐压设备;3.运行成本高;4.不能实现综合回收,热压氧化法一般的单位投资为4750/t,运行成本为1450元/t。
3种预处理工艺经济比较及方案比较
焙烧氧化法的单位投资一般为3200元/t,运行成本为700元/t。
细菌氧化法一般的单位投资为3100元/t,运行成本为1100元/t。
热压氧化法的单位投资一般为4750元/t,运行成本为1450元/t。
3种预处理工艺的主要技术指标及经济指标对比结果见下表。
工艺名称金回收率/% 运行成本/(元/t)单位投资/(元/t·矿)焙烧氧化≤90 700 3200
生物氧化92-95 1150 3100
热压氧化≥96 1450 4750 由上表可以看出,3种预处理工艺相比,采用热压氧化预处理工艺的金回收率最高,运行成本最高,投资也最大。
焙烧氧化金的回收率最低,有用成分综合利用高,中和渣少,投资与生物氧化进近,生物氧化的金回收率介于两者之间,运行成本略高于焙烧氧化,单投资最省。
焙烧氧化法、生物氧化法和热压氧化法3种预处理用以各有利弊。
因此,在选用何总处理方法时要有针对原料性质,结合拟建项目所处地理位置、交通、气候、环境等条件对原料进行预处理工艺详尽的试验研究,同时展开硫酸及砒霜销售市场调查,从技术和经济两方面进行比较后确定采用何种预处理工艺最适合。